最全OEE计算方法共64页
OEE定义和计算方式
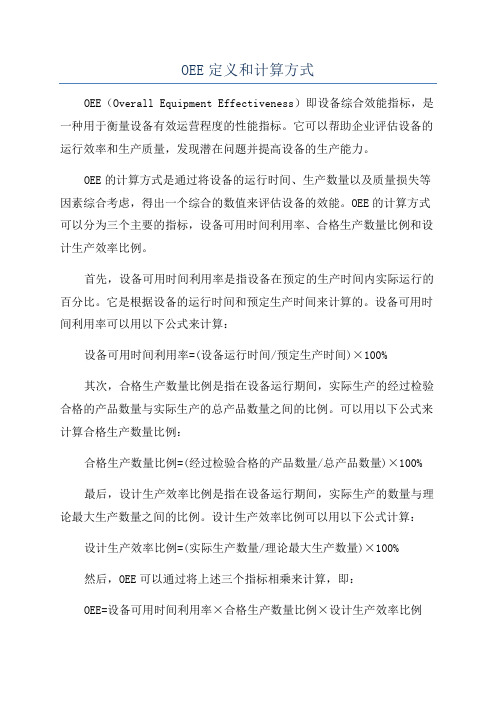
OEE定义和计算方式OEE(Overall Equipment Effectiveness)即设备综合效能指标,是一种用于衡量设备有效运营程度的性能指标。
它可以帮助企业评估设备的运行效率和生产质量,发现潜在问题并提高设备的生产能力。
OEE的计算方式是通过将设备的运行时间、生产数量以及质量损失等因素综合考虑,得出一个综合的数值来评估设备的效能。
OEE的计算方式可以分为三个主要的指标,设备可用时间利用率、合格生产数量比例和设计生产效率比例。
首先,设备可用时间利用率是指设备在预定的生产时间内实际运行的百分比。
它是根据设备的运行时间和预定生产时间来计算的。
设备可用时间利用率可以用以下公式来计算:设备可用时间利用率=(设备运行时间/预定生产时间)×100%其次,合格生产数量比例是指在设备运行期间,实际生产的经过检验合格的产品数量与实际生产的总产品数量之间的比例。
可以用以下公式来计算合格生产数量比例:合格生产数量比例=(经过检验合格的产品数量/总产品数量)×100%最后,设计生产效率比例是指在设备运行期间,实际生产的数量与理论最大生产数量之间的比例。
设计生产效率比例可以用以下公式计算:设计生产效率比例=(实际生产数量/理论最大生产数量)×100%然后,OEE可以通过将上述三个指标相乘来计算,即:OEE=设备可用时间利用率×合格生产数量比例×设计生产效率比例通过计算OEE,企业可以了解设备的实际运营情况,并找到提高设备效率和生产能力的方法。
OEE的最大值为100%,表示设备在预定生产时间内实现了理论最大生产能力,所有生产的产品均为合格产品。
实际上,大多数企业的OEE值往往远低于100%,因此,企业可以通过分析OEE和相关的损失原因来确定改善设备绩效的关键领域。
总之,OEE是一种重要的设备效能指标,可以帮助企业评估设备的有效运营程度。
通过计算设备可用时间利用率、合格生产数量比例和设计生产效率比例,并将它们相乘得出的OEE值来衡量设备的综合效益。
OEE怎么算看完这篇文章你就明白了~附OEE计算表格
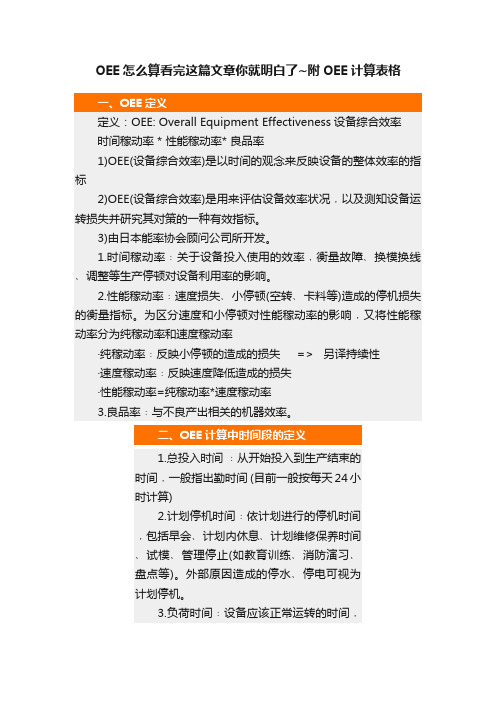
OEE怎么算看完这篇文章你就明白了~附OEE计算表格定义:OEE: Overall Equipment Effectiveness设备综合效率时间稼动率 * 性能稼动率* 良品率1)OEE(设备综合效率)是以时间的观念来反映设备的整体效率的指标2)OEE(设备综合效率)是用来评估设备效率状况﹐以及测知设备运转损失并研究其对策的一种有效指标。
3)由日本能率协会顾问公司所开发。
1.时间稼动率﹕关于设备投入使用的效率﹐衡量故障﹑换模换线﹑调整等生产停顿对设备利用率的影响。
2.性能稼动率﹕速度损失﹑小停顿(空转﹑卡料等)造成的停机损失的衡量指标。
为区分速度和小停顿对性能稼动率的影响﹐又将性能稼动率分为纯稼动率和速度稼动率·纯稼动率﹕反映小停顿的造成的损失 => 另译持续性·速度稼动率﹕反映速度降低造成的损失·性能稼动率=纯稼动率*速度稼动率3.良品率﹕与不良产出相关的机器效率。
1.总投入时间﹕从开始投入到生产结束的时间﹐一般指出勤时间 (目前一般按每天24小时计算)2.计划停机时间﹕依计划进行的停机时间﹐包括早会﹑计划内休息﹑计划维修保养时间﹑试模﹑管理停止(如教育训练﹑消防演习﹑盘点等)。
外部原因造成的停水﹑停电可视为计划停机。
3.负荷时间﹕设备应该正常运转的时间﹐为总投入时间减去计划停机时间 (计算OEE 的分母)4.当机时间﹕指由于设备故障﹑模具故障﹑换模换线﹑暖机﹑换料等造成的生产停止时间。
1)设备故障时间﹕因设备故障造成机器停机的总时间。
包含维修时间和调试时间﹐直至可正常生产2)换线损失时间﹕机器因切换不同产品或为达成产品最终特性而进行调整的总时间﹐包括从前一个产品停止到新产品第一个良品产出所花费所有的时间3)模具故障时间﹕因模具原因造成的停机的总时间4)暖机时间﹕暖机时间是指﹐要开始生产时﹐启动﹑调整运转﹑直至加工条件安定前所需要的时间5.稼动时间﹕设备实际用于生产的时间﹐等于负荷时间减去当机时间6.净稼动时间﹕稼动时间中扣除速度损失﹑小停顿损失后的产出时间。
OEE计算公式范文

OEE计算公式范文OEE(Overall Equipment Effectiveness)是一种衡量设备综合效益的指标,常用于衡量生产线设备的运行效率和生产能力。
OEE的计算公式是:OEE = Availability × Performance × Quality其中,Availability(可用性)衡量设备在计划生产时间内真正可用的比例,Performance(性能率)衡量设备在可用时间内达到理论最高速度的比例,Quality(质量率)衡量设备生产出合格产品的比例。
具体计算公式如下:Availability = (计划生产时间 - 停机时间) / 计划生产时间Performance = (实际生产数量 / (计划生产时间 - 停机时间))/ 理论最高速度Quality = (合格产品数量 / 实际生产数量)OEE是一个综合指标,通过倍数相乘的方式,将设备的可用性、性能和质量三个方面综合考虑在内,从而得出设备的综合效益。
以下是对OEE计算公式的详细解释:1. Availability(可用性):可用性反映了设备是否按照计划进行生产的能力。
计算公式中的计划生产时间是指设备在一定周期内的累计时间,停机时间指设备由于故障、修理、更换等原因无法运行的时间。
可用性的计算结果通常为一个0到1之间的小数,1表示设备全天候稳定运行,0表示设备无法正常运行。
2. Performance(性能率):性能率反映了设备是否能够以最高速度进行生产。
实际生产数量指设备在可用时间内真实完成的产品数量,计划生产时间减去停机时间表示设备的可用时间。
理论最高速度是指设备在理想状态下的最高生产能力,通常以单位时间内的产品产量表示。
性能率的计算结果通常为一个0到1之间的小数,1表示设备以最高速度运行,0表示设备无法达到最高速度。
3. Quality(质量率):质量率反映了设备生产出合格产品的能力。
合格产品数量指设备在可用时间内生产的合格产品数量,实际生产数量是指设备在可用时间内真实完成的产品数量。
OEE算法及公式

OEE算法及公式OEE(Overall Equipment Effectiveness)是一种用于衡量生产设备综合效率的指标。
它通过综合考虑设备的可用性、性能和质量来评估设备的运行效率。
OEE可以帮助企业了解设备的运行状况,发现潜在的问题,并采取措施提高设备的工作效率。
下面将介绍OEE的计算公式和相关的算法。
OEE的计算公式如下:OEE = Availability × Performance × Quality其中,Availability(可用性)表示设备在生产计划时间内实际可用的时间占总时间的比例。
可用性的计算公式如下:Availability = (总时间 - 故障时间) / 总时间Performance(性能)表示设备实际生产数量与理论生产数量之间的比例。
性能的计算公式如下:Performance = 实际生产数量 / 理论生产数量Quality(质量)表示合格产品的数量与总产量之间的比例。
质量的计算公式如下:Quality = 合格产品数量 / 总产量通过计算可用性、性能和质量的三个指标,可以得到OEE的值。
OEE 的取值范围在0到1之间,1表示设备运行效率达到了100%,0表示设备完全没有产出。
为了进一步了解设备运行的潜在问题,可以对OEE进行分解,得到可用性、性能和质量的具体数值。
通过这种分解,企业可以更加详细地了解设备运行的各个方面,并分析造成低OEE的原因。
在实际应用中,可以借助OEE软件来自动收集设备的运行数据,并计算OEE值。
这些软件通常会提供实时的设备运行状态监控、故障报警和生产情况分析等功能,帮助企业及时发现运行问题并采取相应的措施。
提高OEE的关键在于分析造成低OEE的原因,并采取相应的改进措施。
比如,如果可用性较低,可能是由于设备经常发生故障,可以采取预防性维护措施来减少故障次数。
如果性能较低,可能是由于设备的速度较慢或存在节拍不匹配等问题,可以优化设备的生产节拍或提高设备的运行速度。
OEE的计算公式

OEE是一个独立的测量工具,它用来表现实际的生产能力相对于理论产能的比率。
国际上对OEE的定义为:OEE是Overall Equipment Effectiveness(全局设备效率)的缩写,它由可用率(Availability time),表现性(Performance)以及质量指数(Quality)三个关键要素组成。
OEE的计算公式(不考虑设备加工周期的差异)=?OEE= 时间开动率×性能开动率×合格品率[1],[4]其中,时间开动率 = 开动时间/负荷时间而,负荷时间 = 日历工作时间-计划停机时间开动时间 = 负荷时间–故障停机时间–设备调整初始化时间(包括更换产品规格、更换工装模具、更换刀具等活动所用时间)性能开动率 = 净开动率×速度开动率而,净开动率 = 加工数量×实际加工周期/开动时间速度开动率 = 理论加工周期/实际加工周期合格品率 = 合格品数量/ 加工数量在OEE公式里,时间开动率反映了设备的时间利用情况;性能开动率反映了设备的性能发挥情况;而合格品率则反映了设备的有效工作情况。
反过来,时间开动率度量了设备的故障、调整等项停机损失,性能开动率度量了设备短暂停机、空转、速度降低等项性能损失;合格品率度量了设备加工废品损失。
例1: 设某设备1天工作时间为8h, 班前计划停机20min, 故障停机20min, 更换产品型号设备调整40min, 产品的理论加工周期为0.5min/件, 实际加工周期为0.8min/件, 一天共加工产品400件, 有8件废品, 求这台设备的OEE。
计算:负荷时间 = 480-20 = 460 min开动时间 = 460 – 20 – 40 = 400 min时间开动率 = 400/460 = 87%速度开动率 = 0.5/0.8 = 62.5%净开动率 = 400×0.8/400 = 80%性能开动率 = 62.5%×80% = 50%合格品率 = (400-8)/400 = 98%于是得到 OEE = 87%×50%×98% = 42.6%。
OEE介绍
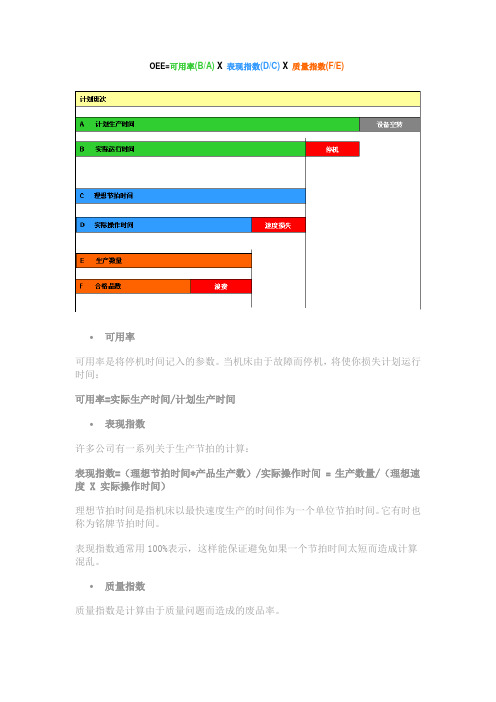
OEE=可用率(B/A) X 表现指数(D/C) X 质量指数(F/E)∙可用率可用率是将停机时间记入的参数。
当机床由于故障而停机,将使你损失计划运行时间:可用率=实际生产时间/计划生产时间∙表现指数许多公司有一系列关于生产节拍的计算:表现指数=(理想节拍时间*产品生产数)/实际操作时间= 生产数量/(理想速度 X 实际操作时间)理想节拍时间是指机床以最快速度生产的时间作为一个单位节拍时间。
它有时也称为铭牌节拍时间。
表现指数通常用100%表示,这样能保证避免如果一个节拍时间太短而造成计算混乱。
∙质量指数质量指数是计算由于质量问题而造成的废品率。
质量指数=合格品数/生产数量下面举一个例子来说明:假如下面是某车间一个班次的记录:从上面的数据,我们可以得出:计划生产时间=班次时间—计划中断=480—2 X 15=450(分钟)工作时间=计划时间—停工时间=420—47=373(分钟)良品=生产数量—次品=19271—423=18,848(件)从而:∙可用率=实际生产时间/计划生产时间=373/420=0.888(88.8%) ∙表现性=生产数量/(理想速度 X 工作时间)=19271/(60 X 373)=0.861(86.1%)∙质量指数=合格品数/生产数量= 18,848/19,271=0.978(97.8%)∙OEE=可用率 X 表现性 X 质量指数=0.888 X 0.861 X0.978=0.748(74.8%)根据OEE系统所提供的数据,你可以方便的知道自己工厂存在什么问题,例如,如果你的可用率在某一个时间段很低,说明在六大损失中和OEE可用率损失有关的故障太多,那么,显而易见,你应该把改善重点放在这些方面了!同样,如果质量指数或者表现性导致你的OEE水平降低,那么你就应该把目光放在和它们有关的问题点上。
在表一中,我们只列举了一些事件原因,其实它可以包括和生产有关的任何方面,因此,你可以对生产做到全面的管理和改善。
OEE计算公式
OEE计算公式OEE(Overall Equipment Effectiveness), 即设备综合效率,其本质就是设备负荷时间内实际产量与理论产量的比值。
企业在进行OEE计算时常常遇到很多迷惑的问题,如工厂停水、停电、停气、停汽使设备不能工作,等待定单、等待排产计划、等待检查、等待上一道工序造成的停机,不知如何计算。
本文引入非设备因素停机的概念,修改了OEE的算法,使计算得到的OEE更能够真实反映设备维护的实际状况,让设备完全利用的情况由完全有效生产率这个指标来反映。
同时介绍了在不同情况下如何分析设备损失的PM分析流程。
一、OEE表述和计算实例OEE= 时间开动率×性能开动率×合格品率[1],[4]其中,时间开动率= 开动时间/负荷时间而,负荷时间= 日历工作时间-计划停机时间开动时间= 负荷时间–故障停机时间–设备调整初始化时间(包括更换产品规格、更换工装模具、更换刀具等活动所用时间)性能开动率= 净开动率×速度开动率而,净开动率= 加工数量×实际加工周期/开动时间速度开动率= 理论加工周期/实际加工周期合格品率= 合格品数量/ 加工数量在OEE公式里,时间开动率反映了设备的时间利用情况;性能开动率反映了设备的性能发挥情况;而合格品率则反映了设备的有效工作情况。
反过来,时间开动率度量了设备的故障、调整等项停机损失,性能开动率度量了设备短暂停机、空转、速度降低等项性能损失;合格品率度量了设备加工废品损失。
例1: 设某设备1天工作时间为8h, 班前计划停机20min, 故障停机20min, 更换产品型号设备调整40min, 产品的理论加工周期为0.5min/件, 实际加工周期为0.8min/件, 一天共加工产品400件, 有8件废品, 求这台设备的OEE。
计算:负荷时间= 480-20 = 460 min开动时间= 460 – 20 – 40 = 400 min时间开动率= 400/460 = 87%速度开动率= 0.5/0.8 = 62.5%净开动率= 400×0.8/400 = 80%性能开动率= 62.5%×80% = 50%合格品率= (400-8)/400 = 98%于是得到OEE = 87%×50%×98% = 42.6%。
设备综合效率OEE的定义及计算示例
设备综合效率(OEE)的定义及计算示例1. 指标名称:综合设备效率OEE2. 指标定义:OEE即设备综合效率,其本质就是设备负荷时间内实际产量与理论产量的比值。
3. 计算公式:OEE=时间稼动率×性能稼动率×良品率公式注释:负荷时间--停止时间⑴时间稼动率=×100%负荷时间其中:a. 负荷时间=工作时间-计划损失时间b. 计划损失时间包括计划停机时间、教育、早会。
c. 停止时间包括停工时间、故障停机时间、工装更换调整时间、原材料中断供应等。
理论节拍×生产数量⑵性能稼动率=×100%稼动时间其中:稼动时间=负荷时间-停止时间加工数量-不良数量⑶良品率= ×100%加工数量4. 数据来源:生产线5. 计算示例:某工厂的一条生产线,计划工作时间8小时(即480分钟),员工休息30分钟,员工用餐30分钟,其它如换刀、设备保养、交接班等形成的停机时间50分钟,故障停机40分钟,原材料中断供应造成停机90分钟。
1)负荷时间=工作时间-计划损失时间=480-30―30―50=370(分钟)停止时间为:40分钟+90分钟=130分钟时间稼动率=(370-130)÷370=0.649(64.9%)2)性能稼动率理论节拍是0.85分钟/件,日产量(加工数量)为270件,其中不良品为30件性能稼动率=0.85×270÷240=0.956(95.6%)3)良品率良品率=(270-30)÷270=0.889(88.9%)由上,则:OEE=64.9%×95.6%×88.9% =55.2%6. 指标目的:1)利用OEE进行损失分析;2)OEE可以准确反映设备本身的问题,也能够客观评价企业的精益生产的实施水平,同时也不会使企业之间的OEE因理解与算法不同而不可比。
OEE定义和计算方式
OEE定义和计算方式OEE(Overall Equipment Effectiveness)是一个衡量设备综合效能的指标,它反映了设备在正常运行期间的生产能力、质量水平和设备利用率。
OEE的计算方式是通过将设备的可用时间、生产速度和生产质量三个因素相乘得到的。
OEE的计算方式如下:OEE=可利用时间×生产速度×生产质量1. 可利用时间(Availability):指设备在正常工作时间内处于可用状态的时间比例。
可利用时间可以通过以下公式计算:可利用时间=总运行时间-计划停机时间总运行时间是指除计划停机时间之外的设备运行时间,可以通过记录设备的实际运行时间来获得。
计划停机时间是指计划维护、更换模具或设备调整的时间。
可利用时间的百分比越高,设备的利用率就越高。
2. 生产速度(Performance):指设备实际生产与设备理论生产的比例。
生产速度可以通过以下公式计算:生产速度=实际产量/理论产量理论产量是指在设备理想运行状态下,单位时间内最大产量。
实际产量是指设备在实际运行状态下实际生产的产量。
生产速度的百分比越高,设备的生产能力越大。
3. 生产质量(Quality):指设备在生产过程中产生的合格产品的比例。
生产质量可以通过以下公式计算:生产质量=合格品数/总产量合格品数是指在设备运行期间通过质量检验合格的产品数量。
总产量是指设备在运行期间产生的产品的总数量。
生产质量的百分比越高,设备的质量水平越高。
将以上三项因素相乘即可得到OEE的值。
OEE的结果通常以百分比形式表示。
OEE的一个关键优势是它能够帮助企业快速识别和改善设备运行中的问题和瓶颈。
通过监测OEE的值,企业可以确定哪些方面需要改进,并采取相应的措施提高设备效能。
此外,OEE还可以用于设备之间的比较和竞争分析。
通过比较不同设备的OEE值,企业可以确定哪些设备在生产效能上最为出色,并对其他设备进行改进或优化,以提高整体生产效能。
oee计算简便方法
OEE(Overall Equipment Effectiveness,设备综合效率)是一个衡量设备性能的指标,它结合了设备的可用性、性能和质量。
OEE的计算公式通常包含三个部分:时间开动率、性能开动率和合格品率。
以下是一种简便的方法来计算OEE:1. 时间开动率(Availability):时间开动率衡量的是设备实际运行时间与计划运行时间之间的比例。
计算公式为:时间开动率= 实际运行时间/ 计划运行时间实际运行时间包括设备正常运行和进行维护的时间,计划运行时间是指设备的日历工作时间。
2. 性能开动率(Performance):性能开动率衡量的是设备在运行时的实际性能与理论性能之间的比例。
计算公式为:性能开动率= 实际产出/ 理论产出实际产出是指在设备运行时间内实际完成的产品数量,理论产出是指在理想情况下设备能够达到的最大产品数量。
3. 合格品率(Quality):合格品率衡量的是设备生产出的合格产品数量与总生产数量之间的比例。
计算公式为:合格品率= 合格品数量/ 总生产数量合格品数量是指在设备运行时间内生产出的符合质量标准的产品数量,总生产数量是指设备在这段时间内生产出的所有产品数量。
简便计算方法:如果你想要一个更简便的方法来估算OEE,可以只关注设备的运行时间和合格品率。
假设设备每天运行8小时,如果设备在这8小时内都在运行,那么时间开动率就是8小时/8小时,即100%。
接下来,如果你知道设备在运行时能够达到的理论产出,而实际产出稍微低于这个理论值,你可以假设性能开动率是95%(这是一个假设值,实际可能不同)。
最后,如果你知道合格品率是90%,那么OEE就可以用以下公式简便计算:OEE ≈ 时间开动率× 性能开动率× 合格品率OEE ≈ 100% × 95% × 90%OEE ≈ 85.5%这个简便计算方法提供了一个大致的OEE估算值,但实际的OEE计算可能需要更详细的数据和更精确的方法。