PVC管材挤出工艺
PVC管材的生产工艺与设备操作介绍

PVC管材的生产工艺与设备操作介绍1.PVC管材生产工艺:(1)PVC树脂配料:根据PVC管材的要求,将PVC树脂、稳定剂、润滑剂、增塑剂等材料按一定比例配料。
其中,PVC树脂是PVC管材的主要成分,稳定剂用于防止PVC树脂分解、变色,润滑剂用于改善材料流动性,增塑剂用于提高PVC管材的柔韧性。
(2)PVC挤出:将混合好的PVC配料加入挤出机中,通过高温和高压条件下的挤出过程,将PVC材料推送至模具中,形成所需的管状形状。
(3)冷却和定径:经过挤出后的PVC管材通过喷淋冷却装置进行冷却,使其快速降温。
然后,通过定径装置对PVC管材进行定径,以确保管材尺寸的准确性和稳定性。
(4)切割和堆垛:定径后的PVC管材进入切割机,通过自动或手动操作进行切割,使其达到所需长度。
然后,切割好的管材经过堆垛装置进行堆垛,方便后续包装和运输。
2.PVC管材生产设备的操作:(1)PVC挤出机:操作人员需要将混合好的PVC配料加入挤出机的加料口,并通过控制挤出机的温度、压力、挤出速度等参数,确保PVC材料能够顺利挤出,并保持稳定的挤出速度和质量。
(2)喷淋冷却装置:操作人员需要调整喷淋冷却装置的水温和喷头位置,确保PVC管材可以均匀地冷却,避免管材热变形或产生其他质量问题。
(3)定径装置:操作人员需要根据所需的管材尺寸,调整定径装置的开口直径,以确保PVC管材能够准确地通过定径装置,并保持良好的尺寸一致性。
(4)切割机和堆垛装置:操作人员需要根据所需长度,调整切割机的切割速度和位置,确保切割好的管材长度准确。
然后,将切割好的管材通过堆垛装置进行堆垛,避免管材互相交叉,方便后续操作。
以上是PVC管材的生产工艺和设备操作的介绍。
操作人员在操作设备时需要严格遵守操作规程,确保安全生产。
此外,定期对设备进行维护保养,及时清理设备,更换磨损部件,可以提高设备的使用寿命和生产效率,保证产品质量。
pvc管道生产工艺流程及配方表
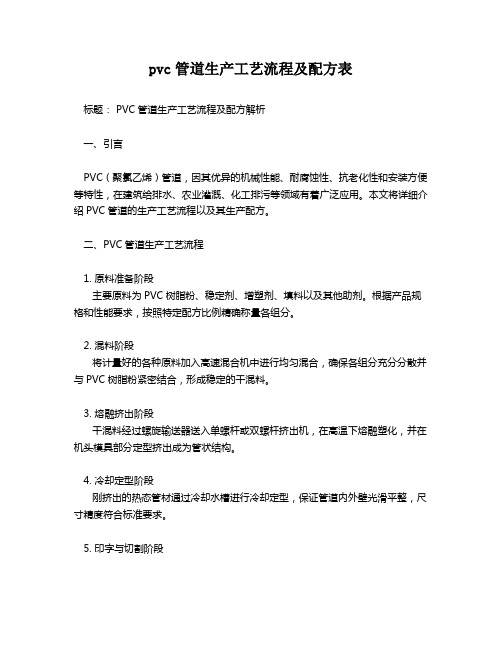
pvc管道生产工艺流程及配方表标题: PVC管道生产工艺流程及配方解析一、引言PVC(聚氯乙烯)管道,因其优异的机械性能、耐腐蚀性、抗老化性和安装方便等特性,在建筑给排水、农业灌溉、化工排污等领域有着广泛应用。
本文将详细介绍PVC管道的生产工艺流程以及其生产配方。
二、PVC管道生产工艺流程1. 原料准备阶段主要原料为PVC树脂粉、稳定剂、增塑剂、填料以及其他助剂。
根据产品规格和性能要求,按照特定配方比例精确称量各组分。
2. 混料阶段将计量好的各种原料加入高速混合机中进行均匀混合,确保各组分充分分散并与PVC树脂粉紧密结合,形成稳定的干混料。
3. 熔融挤出阶段干混料经过螺旋输送器送入单螺杆或双螺杆挤出机,在高温下熔融塑化,并在机头模具部分定型挤出成为管状结构。
4. 冷却定型阶段刚挤出的热态管材通过冷却水槽进行冷却定型,保证管道内外壁光滑平整,尺寸精度符合标准要求。
5. 印字与切割阶段定型后的管材表面可按需求印制相关标识信息,然后通过自动切割设备按设定长度进行切割。
6. 检验包装阶段对切割好的PVC管道进行严格的质量检验,包括外观质量、尺寸精度、力学性能等各项指标,合格产品进行包装入库。
三、PVC管道生产配方表以下是一个典型的PVC-U管道生产配方示例:- PVC树脂粉:100份- 稳定剂:3-5份- 增塑剂:10-20份(视管材硬度要求而定)- 钙锌复合稳定剂:1-3份- 内外润滑剂:1-2份- 填充剂(如碳酸钙):适量(以降低成本和提高刚性)- 抗冲改性剂:根据需要添加- 阻燃剂(如有防火要求时):适量请注意,以上配方仅为示例,实际生产过程中,各类助剂的种类和用量需根据具体的产品规格、性能要求以及生产环境条件等因素进行科学调整。
四、结语PVC管道的生产过程涵盖了从原料选择到成品检验的多个环节,每个环节都至关重要。
科学合理的配方设计和严谨精准的工艺控制是保证产品质量的关键,也是提升PVC管道市场竞争力的核心要素。
PVC挤出机操作工艺

二、挤出操作人员须熟悉所操作的挤出机的结构特性,加热和冷却的控制仪表特性、机头特性及装配情况等,以便正确地掌握挤出机工艺条件,正确的操作机器,挤出不同的产品型号及规格操作方法是不同的,生产过程中,应按工艺要求定期检查各种工艺参数是否正常。
※开机前准备1、模具准备及安装1.1 根据生产安排,找出生产该产品的模具,及相关的定径套、橡皮圈、夹具、加热片、加热圈及作业操作工具(活动扳手、内六角扳手、螺丝刀、砂纸、撬棒等)。
1.2 检查模具、定径套的各部位,并将其同料接触的部位打光;1.3 安装相应的模具、定径套、橡皮圈、夹具,加热片、加热圈等等;1.4 调整好模具的口模间隙、连接好加热片、加热圈的电源线;2、挤出机主机的检查2.1 检查挤出机的各水路、气路、油路是否畅通,有无漏水、漏气、漏油等情况;2.2 开启主机电源,打开各加热单元的电源开关,并设定相对较低的温度,用温度计检查各加热单元的升温是否正常、各温控仪表是否正常后,关闭加热单元的电源开关;2.3 检查主机真空泵的运转是否正常,及其管路是否畅通,有无漏气、漏水或堵塞现象;2.4 检查加料装置的运转是否正常。
2.5 待以上各步骤均显示正常后,开启模具各段的加热开关,并设定好初始工艺温度在120度左右;2.6 待模具各段的温度均达到初始设定值后,开始设定作业温度;以下是参考温度设定值:机筒一区(进料区)185度-192度机筒二区(加热区)188度-195度机筒三区(塑化区)175度-182度机筒四区(送料区)160度-172度合流芯160-172度模头175-185度口模188度-205度2.7以上温度值只作参考,实际设定应根据产品质量要求而定;待模具各段的温度均达到设定值后,需继续保温30分钟,使各加热单元受热均匀。
3、挤出机辅机的检查3.1 冷却水槽的检查1)打开冷却水槽的电源开关;2)按冷却水槽的前后移动开关,检查水槽的前后移动情况是否正常;3)开通冷却水槽冷却水的进水阀门,打开水泵运转开关,检查其进水及喷淋装置有无堵塞,开启水槽的出水阀门,检查其出水水路是否正常;4)打开水槽真空泵,检查真空泵的运转情况;5)检查冷却水槽的水平及其中心线同挤出机中心线是否在同一直线;3.2 牵引机1)启动牵引机,检查牵引机的牵引是否正常;2)按牵引机的下压、抬起开关,检查其气路是否正常;3)检查牵引机的履带位置是否可调整;3.3 检查切割机及排管架1)普通锯片式切割机a)调整好切割用夹具的高度,并做切割动作,检查其动作是否正常。
PVC管材生产工艺流程
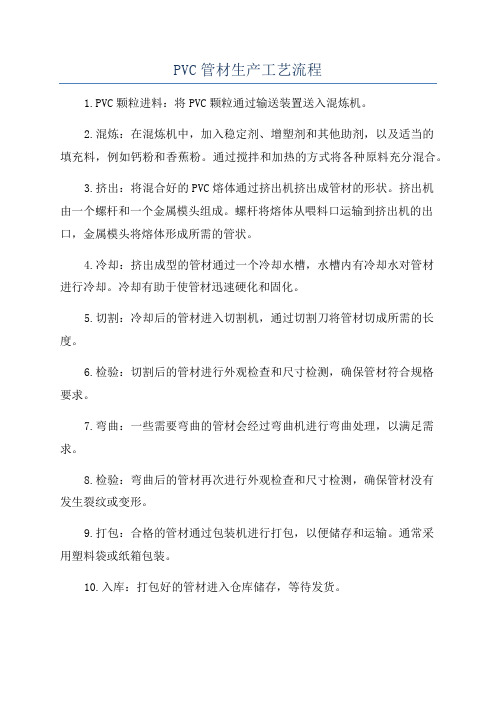
PVC管材生产工艺流程
1.PVC颗粒进料:将PVC颗粒通过输送装置送入混炼机。
2.混炼:在混炼机中,加入稳定剂、增塑剂和其他助剂,以及适当的
填充料,例如钙粉和香蕉粉。
通过搅拌和加热的方式将各种原料充分混合。
3.挤出:将混合好的PVC熔体通过挤出机挤出成管材的形状。
挤出机
由一个螺杆和一个金属模头组成。
螺杆将熔体从喂料口运输到挤出机的出口,金属模头将熔体形成所需的管状。
4.冷却:挤出成型的管材通过一个冷却水槽,水槽内有冷却水对管材
进行冷却。
冷却有助于使管材迅速硬化和固化。
5.切割:冷却后的管材进入切割机,通过切割刀将管材切成所需的长度。
6.检验:切割后的管材进行外观检查和尺寸检测,确保管材符合规格
要求。
7.弯曲:一些需要弯曲的管材会经过弯曲机进行弯曲处理,以满足需求。
8.检验:弯曲后的管材再次进行外观检查和尺寸检测,确保管材没有
发生裂纹或变形。
9.打包:合格的管材通过包装机进行打包,以便储存和运输。
通常采
用塑料袋或纸箱包装。
10.入库:打包好的管材进入仓库储存,等待发货。
以上是一种典型的PVC管材生产工艺流程,具体的工艺流程可能因厂家和管材产品的不同而有所变化。
但总体上,通过原料混炼、挤出成型、冷却、切割、检验、弯曲、检验、打包和入库等工艺步骤,可以得到高质量的PVC管材产品。
PVC管材生产工艺步骤
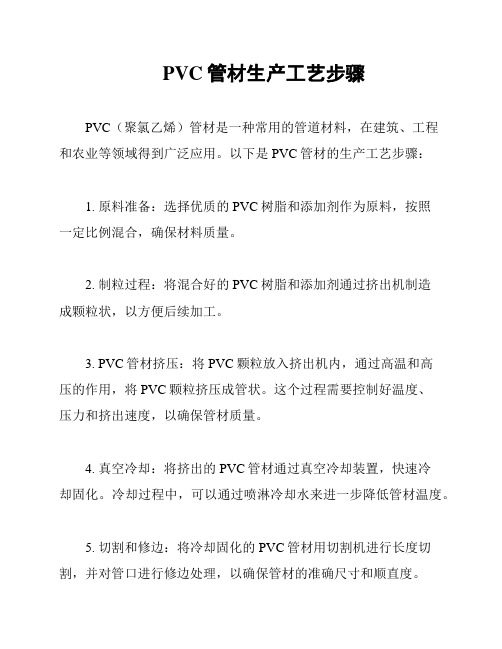
PVC管材生产工艺步骤
PVC(聚氯乙烯)管材是一种常用的管道材料,在建筑、工程
和农业等领域得到广泛应用。
以下是PVC管材的生产工艺步骤:
1. 原料准备:选择优质的PVC树脂和添加剂作为原料,按照
一定比例混合,确保材料质量。
2. 制粒过程:将混合好的PVC树脂和添加剂通过挤出机制造
成颗粒状,以方便后续加工。
3. PVC管材挤压:将PVC颗粒放入挤出机内,通过高温和高
压的作用,将PVC颗粒挤压成管状。
这个过程需要控制好温度、
压力和挤出速度,以确保管材质量。
4. 真空冷却:将挤出的PVC管材通过真空冷却装置,快速冷
却固化。
冷却过程中,可以通过喷淋冷却水来进一步降低管材温度。
5. 切割和修边:将冷却固化的PVC管材用切割机进行长度切割,并对管口进行修边处理,以确保管材的准确尺寸和顺直度。
6. 检测和质量控制:对切割好的PVC管材进行外观检测、尺
寸测量等操作,确保管材符合相关标准和要求。
如果出现不合格品,需要及时处理和修复。
7. 包装和存储:将合格的PVC管材进行包装,通常是用塑料
薄膜或纸箱包装,然后存放在干燥、通风的仓库中,以防止管材受
潮和变形。
以上是PVC管材的生产工艺步骤,每个步骤的操作和控制都
很关键,以确保最终生产出符合质量标准的PVC管材产品。
年产5000吨硬质聚氯乙烯管车间工艺设计

硬质聚氯乙烯(PVC-U)管是一种常用的管材,常用于给排水系统、化工管道等。
下面将对年产5000吨硬质聚氯乙烯管车间的工艺设计进行详细介绍。
1.原料准备:原料主要包括聚氯乙烯树脂、稳定剂、填充剂和其他助剂。
树脂是管材的主要成分,稳定剂用于防止聚合过程中的氧化反应,填充剂用于增加材料的硬度和冲击强度,助剂用于改善材料的流动性和加工性能。
原料按照一定比例称重,并进行混合搅拌,以确保材料均匀混合。
2.挤出工艺:经过原料准备后,将材料送入挤出机。
挤出机将材料加热到一定温度,使其熔化变成熔体。
熔体经过螺杆的挤出和模具的挤压,形成连续的管状结构。
挤出机的温度、压力及机头设计的合理性对产品质量有着重要的影响。
3.冷却和定径:熔体经过挤出机后,将进入到冷却装置中进行冷却,通常采用水冷却的方式,以快速冷却管材并固化形成物理性能稳定的管材。
定径装置用于控制管材的直径,一般采用真空定径技术,通过控制真空度和压力差来调节管材的直径。
4.切割和包装:冷却凝固后的管材通过切割机进行定长切割,得到符合要求的管材长度。
切割后的管材经过目检和质量检验,将合格的管材送入包装机进行包装。
常见的包装方式包括塑料薄膜包装和纸箱包装。
5.质量控制:在整个生产过程中,需要进行严格的质量控制以确保产品质量。
可以在原料检验、挤出过程中的温度和压力控制、冷却定径过程中的各项参数监控以及最终产品的质量检验等环节进行质量控制。
总结:以上介绍了年产5000吨硬质聚氯乙烯管车间的工艺设计。
在实际生产中,需要根据具体情况进行设备的选择和工艺参数的优化,以确保产品质量和生产效率。
此外,还需要加强安全管理和环境保护,确保生产过程的安全和环境友好。
pvc管道生产工艺流程及配方表
pvc管道生产工艺流程及配方表
标题:PVC管道生产工艺流程及配方表详解
一、PVC管道生产工艺流程
1. 原材料准备:PVC管道的主要原料是聚氯乙烯(PVC)树脂,以及各种助剂如稳定剂、增塑剂、填充剂等。
这些原材料需要按照配方比例精确称量。
2. 混合:将称量好的原料放入混合机中进行混合,确保各种成分均匀分布。
3. 熔融挤出:混合后的物料进入挤出机,在高温和压力下熔融成液态,然后通过模具挤出形成管道雏形。
4. 冷却定型:挤出的管道雏形通过冷却水槽进行冷却,使其硬化并定型。
5. 切割:定型后的管道根据需要的长度进行切割。
6. 二次加工:如需要,可进行内外壁打磨、印刷标识等二次加工。
7. 检验包装:最后,对成品进行质量检验,合格后进行包装,准备出厂。
二、PVC管道基本配方表
以下是一个基本的PVC管道配方表,具体配方可能因生产商和产品需求有所不同:
- PVC树脂:100份
- 稳定剂:2-5份(常用有铅盐、钙锌复合稳定剂等)
- 增塑剂:10-30份(如DOP、DBP等)
- 填充剂:20-50份(如碳酸钙、滑石粉等)
- 润滑剂:0.5-2份(如硬脂酸、石蜡等)
- 加工助剂:0.1-1份(如抗氧剂、紫外线吸收剂等)
以上配方中的份量通常以树脂重量为基准,单位通常是“份”。
请注意,实际生产中,配方和工艺参数需要根据设备性能、产品要求、环境条件等因素进行调整。
同时,为了保证产品质量和环保要求,选择无毒、环保的助剂也是非常重要的。
pvc管材生产工艺流程
pvc管材生产工艺流程
PVC管材的生产工艺流程包括原料准备、混炼、挤出成型、冷却、切割和成品质检等环节。
首先是原料准备。
PVC材料是由聚氯乙烯树脂、稳定剂、助剂和填料组成。
这些原料需要事先量好并准备好,以保证生产过程的顺利进行。
接下来是混炼。
将事先准备好的PVC树脂和其他添加剂放入混炼机中进行混炼。
混炼的目的是将各种原料充分混合均匀,确保PVC管材的质量。
混炼完成后,将混炼好的PVC熔体通过喂料装置输送到挤出机中。
挤出机将PVC熔体加热并压缩,然后通过模头将熔体挤出成型。
挤出成型的PVC管材经过模头之后进入冷却装置,冷却装置通过水冷却的方式,迅速将PVC管材表面温度降低,使其硬化和固化。
冷却完成后,PVC管材经过切割装置进行切割。
切割装置根据需要将PVC管材切割成不同长度,以满足客户的需求。
最后是成品质检。
对切割好的PVC管材进行质量检验,包括尺寸、外观和物理性能等方面。
只有通过检验的PVC管材才能被认定为合格品,可以包装和销售。
总结起来,PVC管材的生产工艺流程包括原料准备、混炼、挤出成型、冷却、切割和成品质检。
每个环节都需要严格控制和监测,以确保PVC管材的质量和生产效率。
这样才能生产出符合标准的优质PVC管材产品。
PVC管材生产工艺流程
PVC管材生产工艺流程
一、原料选择
二、搅拌混合
将所选的PVC树脂、辅助剂等按一定的配方放入高速混合机中进行搅拌混合,使各种原料均匀混合,形成塑料料浆。
三、挤出成型
将混合均匀的塑料料浆通过给料机输送至双螺杆挤出机,挤出机利用双螺杆的旋转和螺杆间的压力,将塑料料浆进行分散、塑化、熔融,并将熔融的塑料挤出成型,形成管材的初始形状。
四、真空冷却
经过挤出机挤出成型的管材会经过冷却水箱中的冷却水浸泡,同时利用真空系统对管材进行内外的冷却和固化,使其保持稳定的形状和尺寸。
五、牵引定径
冷却固化后的管材会经过牵引定径机构,利用牵引辊和定径模具对管材进行牵引和定径,使其达到所需的尺寸和形状要求。
六、切割检验
通过切割机将牵引定径好的管材进行切割,并进行必要的外观质量和尺寸检验。
合格的管材将进行下一步的处理,不合格的管材需进行返工或处理。
七、包装储存
经过质检合格的管材将进行包装,一般采用塑料薄膜包装,以保护管材的表面免受损坏。
包装好后的管材将进行储存,并标明型号、规格、生产日期等信息。
八、卸货装车
根据订单要求,将包装好的管材进行卸货装车,准备发往用户。
在装车过程中,需要注意对管材的搬运、装载等操作,以防止管材的损坏。
九、质量控制
在整个生产过程中,需要进行质量控制,对原料、中间产品和最终产品进行检验和测试,以确保产品的质量符合标准要求。
常见的检测项目包括外观检查、尺寸测量、力学性能测试等。
以上就是PVC管材的生产工艺流程,通过这一系列的生产工艺,可以制造出质量稳定、外观平整、尺寸精确的PVC管材产品。
PVC管材工艺流程
PVC管材工艺流程
1.原料准备:首先需要准备好PVC树脂、稳定剂、助剂、填充剂等原材料,并对它们进行仔细的检查和筛选,确保其质量符合生产要求。
2.混合:将预先配好的PVC树脂和不同的助剂、稳定剂等原材料放入混合设备中进行充分的混合搅拌,以使各种原材料充分融合,并确保材料的均匀性和稳定性。
3.制粒:将混合好的材料通过挤出机进一步加工,将其挤出成为一定规格和长度的颗粒状物料,这些颗粒即为制粒材料。
4.挤出:将制粒材料放入挤出机中,通过加热、熔融、塑化的工艺,将材料挤出成形出管材的形状。
挤出过程需要精确控制温度、挤出速度和压力等参数。
5.冷却:挤出成形的管材经过冷却处理,通常会使用水冷方式进行管材的快速冷却,以确保管材在形成中能够迅速固化。
6.拉伸:为使管材的物理性能能够满足要求,通常需要对管材进行拉伸处理。
拉伸的目的是增加管材的强度和硬度,并减少管材的管壁厚度。
7.切割:根据需要的长度要求,将拉伸好的管材进行切割。
通常采用锯切或者切割机进行切割,以确保切割的准确度和管材的整齐度。
8.检验和包装:对切割好的管材进行严格的质量检验,通常包括检查外观、尺寸、强度等指标是否符合要求。
合格的管材会进行包装,然后交付给客户。
以上是PVC管材的工艺流程的一般步骤,通过这些步骤可以生产出质量优良的PVC管材产品。
在实际的生产过程中,可能还涉及到其他附加工
艺,如印字、压花等,这些工艺会根据具体产品的需求进行相应的调整和应用。
总之,PVC管材的生产工艺流程需要严格控制各个环节,以确保产品的质量和性能达到标准要求。
- 1、下载文档前请自行甄别文档内容的完整性,平台不提供额外的编辑、内容补充、找答案等附加服务。
- 2、"仅部分预览"的文档,不可在线预览部分如存在完整性等问题,可反馈申请退款(可完整预览的文档不适用该条件!)。
- 3、如文档侵犯您的权益,请联系客服反馈,我们会尽快为您处理(人工客服工作时间:9:00-18:30)。
3
管材表面有黑色条纹
机身或机头温度过高:
机头和多孔板未清理干净
4
管材外壁表面无光泽
口模温度过低
挤出速度太快或剪切速度太快,熔体破裂
口模温度过高,或内表面无光泽并毛糙
机身温度太低,塑化不良
5
管材表面有皱纹
口模四周温度不均匀,挤出速度不均匀
冷却水温度太高,冷却不够
牵引速度太慢
牵引或挤出速度不稳定
b、减少或不用高分子量加工助剂的用量(它提供橡胶弹性,增加膨胀)
通过修改模具来调整:a、增来自模具平直段长度,提供足够时间供分子链收缩
b、减小口模间隙
3
拉伸强度不合格
工艺条件:
f、加工温度太低,挤出速度太慢,塑化不良:
g、加工温度太高,挤出速度太快,过度塑化;
h、加料速度太慢,压实不良;
i、原料受潮、主机排气不良,混料温度太低,排气不良,导致管壁结构有气泡;
冷却水箱两孔不同轴线
12
管材冲击性能不好
加工温度低,塑化不良
原辅料质量差
混炼和压实不良,机头压力小,压缩比小
模具内有挂料或杂质,导致管壁有线条,引起性能不好
配方不当,如润滑剂过多,未正确使用抗冲击改性剂
配方中填料太多
1.3硬质PVC实壁管材生产中经常出现的几个性能指标的问题:
序号
性能
产生的可能原因
1
韧性的不良主要是:过度塑化所有能够引起过度塑化的因素都有影响;
另配方的影响:
a、配方中应用抗冲击改性剂不当;
a、填料太多;
b、使用了增塑剂;
c、使用的敷料质量有问题
d、使用的PVC树脂质量有问题
8
维卡温度太低
主要是原料和配方的影响:
a、PVC树脂的分子量太小;
b、增塑剂使用太多;
c、低分子量添加剂使用太多,如润滑剂;
冲击性能不合格
塑化不良,所有能够引起塑化不良的因素都有影响
工艺条件:
a、加工温度太低,挤出速度太慢,塑化不良:
b、加工温度太高,挤出速度太快,过度塑化;
c、加料速度太慢,压实不良;
d、原料受潮、主机排气不良,混料温度太低,排气不良,导致管壁结构有气泡
e、模具内有挂料或杂质,导致管壁有线条,引起缺口敏感。
1.硬质PVC实壁管材:
1.1配方的基本原则:必须兼顾制品的性能和加工性能;
1.2硬质PVC实壁管材生产中经常出现的问题:
序号
不正常现象
产生的可能原因
1
管坯强度差
塑化程度不够
2
管材表面有分解黑点、分解色点、焦点
机身或机头温度过高:
机头和多孔板未清理干净;
分流器设计不合理,有死角;
物料中有杂质;
原料热稳定性差,配方设计不合理;
机器、模具的影响:
a、机器太小,模具太大,小机生产大产品,不匹配,供料不足;
b、模具压缩比太小,压实不良;
c、模具分流器结构不合理,如分流筋太大,导致融合不良;
d、主机螺杆和料筒磨损,塑化不良;
配方和原料的影响:
a、润滑剂太多,塑化不良;
b、润滑剂使用不当,主要是低分子量润滑剂用量太多,影响性能;
c、抗冲击改性剂用量太少或选材不当;
机器、模具的影响:
e、机器太小,模具太大,小机生产大产品,不匹配,供料不足;
f、模具压缩比太小,压实不良;
g、模具分流器结构不合理,如分流筋太大,导致融合不良;
h、主机螺杆和料筒磨损,塑化不良;
配方的影响:
f、润滑剂太多,塑化不良;
g、润滑剂使用不当,主要是低分子量润滑剂用量太多,影响性能;
h、抗冲击改性剂用量太多或选材不当;
d、使用抗冲改性剂不当,如CPE、EVA等
9
弯曲性能
主要原因:
a、塑化不良;
b、填料太多;
c、增韧剂太少
10
耐热性能
主要原因:
a、使用增塑剂太多;
b、抗冲击改性剂使用不当;
c、低分子量添加剂使用太多,如润滑剂
d、填料用量太多;
e、原辅料质量差。
2
纵向回缩率太大
模具口模间隙太大,与产品厚度不相符合,需要修改模具
在一定的设备和配方条件下,以下方法可减小其数值:
a、在标准范围内,尽量使产品厚度厚,可减小其数值
b、降低机出速度
c、提高机出温度
d、使冷却水箱远离口模,增加在空气中冷却时间
通过调整配方来调整:
a、配方中增加填料的用量
i、填料用量太多;
j、使用了增塑剂。
4
拉伸伸长率太小
主要是塑化不良,所有能够引起塑化不良的因素都有影响
配方的影响:
a、滑剂太多,塑化不良;
b、润滑剂使用不当,主要是低分子量润滑剂用量太多,影响性能;
c、抗冲击改性剂用量太少或选材不当;
d、填料用量太多;
5
扁平性能不合格
主要是塑化不良,所有能够引起塑化不良的因素都有影响
主要是塑化不良,所有能够引起塑化不良的因素都有影响
配方中填料太多
7
耐水压性能
分为脆性和韧性的不良
脆性不良主要是:
a、塑化不良引起,所有能够引起塑化不良的因素都有影响
b、机器太小,模具太大,小机生产大产品,不匹配,供料不足;
c、模具压缩比太小,压实不良;
d、模具分流器结构不合理,如分流筋太大,导致融合不良;
6
管材内壁毛糙,不光滑
芯模温度太低
机身温度太低,塑化不良
螺杆温度太高,粘模
7
管材内壁有裂纹
料内有杂质
芯模温度太低
机身温度太低
牵引速度太快
模具口模间隙太大
8
管壁有气泡
原料受潮,水分高
混合时温度低排气排湿不良
加工温度过低
配混料稳定性不够,少量分解产生气泡
主机排气管路堵塞或有其他不正常
9
管材壁厚不均匀
口模、芯模未同心,单边厚
配方中填料太多
管壁结构有线条,出现缺口应力集中
机器、模具的影响:
a、机器太小,模具太大,小机生产大产品,不匹配,供料不足;
b、模具压缩比太小,压实不良;
c、模具分流器结构不合理,如分流筋太大,导致融合不良;
d、主机螺杆和料筒磨损,塑化不良;
e、温度过低,挤出速率过小,螺杆或机筒磨损。
6
耐化学药品性能
机头温度不均匀,出料速度不均一
牵引或挤出速度不稳定
加料速度不均匀
管材四周冷却不均匀
配方中低分子量润滑剂太多,析出螺杆吃料不均匀
10
管材内壁凹凸不平
螺杆温度太高
螺杆转速太快
配方中润滑剂太多
模具压缩比太小
机台规格相对产品规格太小
11
管材弯曲
管材壁厚不均匀(见第9项)
机身、冷却装置、牵引装置轴线不在同一条线