半钢成型工序标准流程
半钢轮胎生产工艺流程简图
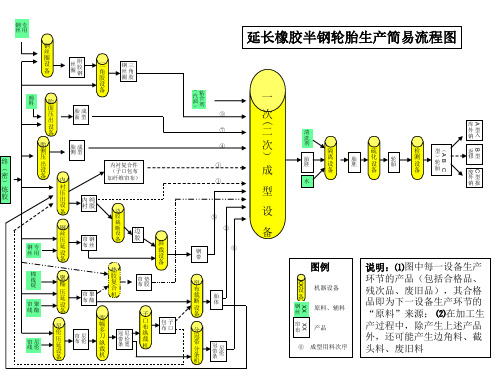
帘聚 布酯
垫 胶 复 合 机
图例
XX 帘 布 裁 断 设 备
胎 体
帘垫 布胶
设 备
XX
机器设备 原料、辅料 产品 成型用料次序
帘尼 线伦
帘尼 布伦
宽 幅 多 刀 纵 裁 机
冠尼 带伦 条宽
子 口 布 纵 裁 机
钢 丝 帘 布
包子 布口
分 冠 带 分 条 机
冠尼 带伦 条
⑥
说明:⑴图中每一设备生产 环节的产品(包括合格品、 残次品、废旧品),其合格 品即为下一设备生产环节的 “原料”来源; ⑵在加工生 产过程中,除产生上述产品 外,还可能产生边角料、截 头料、废旧料
④
终 ( 密 )备
轮 胎
检 测 设 备
返 修型 废 外型 销报 B C
内 衬 压 出 设 备 钢 丝 压 延 设 备 聚 酯 压 延 设 备 尼 伦 压 延 设 备
内纯 衬胶
钢专 丝用
帘钢 布丝
边 胶 裁 断 设 备
⑤
设
②
边 胶
备
⑥
斜 裁 设 备
钢 带
棉 线 锭 帘聚 线酯
钢专 丝用
钢 丝 圈 设 备
延长橡胶半钢轮胎生产简易流程图
丝附 圈胶 钢
三 角 胶 设 备
钢三 丝角 圈胶 ( 汽粘 油合 )剂 ③ ⑦
颜 料
胎 面 压 出 设 备 胎 侧 压 出 设 备
一 次 二 次 ) 成 型
清 洗 剂 胎 胚 水 库 外型 销入 A 型( ) 轮 胎 A B C
胎成 面型
(
胎成 侧型 内衬复合件 (子口包布 加纤维帘布)
XX
钢结构制作标准化施工流程

.钢结构制作标准化施工流程下料工艺流程:原材料采购、验收、进厂组装、焊接、预拼装除锈涂装成品保护、包装、运输至现场一、原材料采购、验收、进厂1、钢材、钢铸件的品种、规格、性能等应符合国家产品标准和设计要求。
进口钢材产品的质量应符合设计和合同规定标准要求。
2、焊接材料的品种、规格、性能等应符合国家产品标准和设计要求。
3、连接用紧固标准件其品种、规格、性能等应符合国家产品标准和设计要求。
4、钢材入库前必须办理入库交验手续,质检人员要核对材料牌号、规格、质量证明书、炉批号是否符合有关技术文件、标准相符、表面质量是否合格。
5、钢材要妥善堆放存储、堆放成形、成方、成垛,最底层上垫枕木,防止进水生锈。
6、材料凭证发放,领料时应该对材料品种、规格、牌号是否与单证一致,必要时质检员需要在场签证认可。
二、下料资料Word.2.1放样、号料、切割、制孔2.1.1按照施工图上几何尺寸,1:1比例在样台上放出实样以求出真实形状和尺寸,然后根据实样的形状和尺寸制成样板、样杆,作为下料、弯制、铣、刨、制孔等加工依据。
允许偏差表如下:项允许偏0.5平行线和分段线1.0对角0~0.5,宽度长度、宽度长度0~0.50.5 孔距±0.5 ±组孔中心距离±20°加工样板的角度2.1.2钢材下料前先对材料进行校正,矫正后的偏差不超过规范及设计规定的允许偏差值,保证下料的质量。
2.1.3根据工艺要求在放样和下料预留制作和安装时的焊接收缩余量及切割、刨边和铣平等加工余量。
2.1.3零件的切割与下料线的允许偏差符合下表规定执行。
资料Word.2.1.4、切割前应将钢材表面区域内的铁锈、污垢等清除干净;切割后清除断口边缘熔瘤、飞溅物,断口上不得有裂纹和大于1mm的缺棱并清除毛刺。
三、组装、焊接、预拼装1、在组装前,组装人员必须熟悉施工图、组装工艺及有关技术文件的要求,并检查组装零部件外观、材质、规格、数量,当无误后方可施工。
钢结构的制作工艺流程

钢结构的制作工艺流程
钢结构制作工艺流程通常包括以下几个步骤:
1. 设计和规划:根据需要确定钢结构的设计要求,包括结构类型、尺寸、承载能力等,制定详细的施工方案和图纸。
2. 钢材准备:根据设计要求选择合适的钢材,如钢板、钢管等,进行材料采购和加工,确保符合质量标准和要求。
3. 钢材加工:将钢材进行切割、钻孔、翻边等加工操作,以便于后续的组装和安装。
4. 钢构件制作:根据设计图纸和加工要求,将切割和加工好的钢材进行焊接、冷弯、锻造等工艺操作,制作成所需的钢构件。
5. 表面处理:对制作好的钢构件进行除锈、喷漆或镀锌等表面处理,提高防腐性能和美观度。
6. 钢构件组装:根据设计方案和图纸,将制作好的钢构件进行组装,通过螺栓连接或焊接等方式进行固定。
7. 安装调试:将组装好的钢结构进行安装调试,确保结构的稳定性和安全性。
8. 质量检验和验收:对安装完成的钢结构进行质量检验,包括材料质量、焊缝质量、尺寸精度等,完成验收手续。
以上是钢结构制作工艺流程的基本步骤,具体实施过程可能会因项目需求和规模而有所调整和变化。
钢结构加工流程

钢结构加工流程钢结构是一种重要的建筑结构形式,它具有高强度、轻质、抗震性能好等优点,因此在现代建筑中得到了广泛的应用。
而钢结构的加工流程则是保证钢结构质量的关键,下面将介绍钢结构的加工流程。
首先,钢材的选材十分重要。
合适的钢材能够保证钢结构的强度和稳定性。
在选材时,需要考虑到使用环境、承载力要求等因素,选择合适的钢材规格和品种。
其次,进行钢材的切割和成型。
在加工钢结构之前,需要对钢材进行切割和成型。
切割可以采用火焰切割、等离子切割、激光切割等方式,根据需要进行选择。
成型则需要根据设计要求进行冷弯或热弯等加工,使钢材达到设计要求的形状和尺寸。
接下来是焊接和连接。
焊接是钢结构加工中的重要环节,通过焊接将各个部件连接成整体。
在进行焊接时,需要严格按照焊接工艺规程进行操作,确保焊接质量。
连接则是将各个部件连接在一起,通常采用螺栓连接、焊接连接等方式。
然后是表面处理。
表面处理是为了提高钢结构的防腐蚀性能和美观度。
常见的表面处理方式包括喷涂防腐漆、热浸镀锌、喷丸除锈等,根据使用环境和要求进行选择。
最后是质量检验和包装。
在钢结构加工完成后,需要进行质量检验,包括外观质量、尺寸偏差、焊接质量等方面。
合格后进行包装,通常采用防水防潮的包装材料,以确保运输和使用过程中不受损坏。
综上所述,钢结构的加工流程包括选材、切割成型、焊接连接、表面处理、质量检验和包装等环节,每个环节都至关重要,需要严格按照工艺要求进行操作。
只有这样,才能保证钢结构的质量和安全性,为建筑工程提供坚实的支撑。
半成品工段标准操作法

纤维帘布裁断工序标准操作法1.检查设备是否正常,运输带是否跑偏,风源是否满足工艺要求(风压不低于0.7Mpa,风中不带水)。
2.检查裁刀小车是否运行平稳,刀片是否安装牢固。
3.检查吊滑子是否处于安全状态。
4.检查大小卡片与实物是否相符。
5.按施工标准调整好设备裁断角度和宽度。
6.开车后,先手动操作裁1——3刀,测量角度、宽度是否符合质量标准,确认无误后,方可采用自动操作。
7.接头时,要求胶布应无劈缝、空白、帘线弯曲、疏密不均、自硫胶、胶疙瘩、杂物等缺陷。
帘布宽度公差:±2mm,裁断角度公差±0.5º,接头压线2——4根,接头出角≤2mm,帘布大头小尾≤2mm。
8.接头间距最小距离:单层胎体:150mm,2——3层胎体:100mm.9.接头数量:对于轮辋直径12〞——14〞规格,1220mm内最多有3个接头。
对于轮辋直径15〞——16〞规格,1450mm内最多有3个接头。
对于轮辋直径17〞以上规格,1600mm内最多有3个接头。
10.更换规格时,必须对第一刀进行测量,确认无误后方可接头。
11.卷取时,帘布应位于垫布中心,并且卷取平整无折子。
12.把卷好的小卷胶布拴上按规定填写的小卡片,吊挂在小卷车上推到规定位置存放。
13.按规定填写使用来源记录表和自检记录表(自检记录要求每规格不少于6次,包括首检记录)。
14.非三班连续生产,最后一班裁完后,应将大卷胶布卷回,防止胶布表面被污染。
编制:半钢分厂审核:批准:2009年10月28日钢丝圈成型工序标准操作法1.检查设备是否正常,水、电、风源(6 bar)是否满足工艺要求。
2.检查各项安全刹车和安全设施。
3.检查喂料口中有无杂物,检查钢丝的缠绕情况,避免交叉。
4.检查胶料大小卡片与实物是否相符,胶料有无杂物,自硫胶,喷霜等现象。
5.检查钢丝质量,打开钢丝前先检查钢丝盘在导开架上是否灵活,钢丝盘太宽应取下处理,钢丝不得锈蚀、油污、水分和杂物,上盘应牢固,避免散盘。
钣金成型工艺流程

钣金成型工艺流程钣金成型是一种金属加工技术,广泛应用于机械、电器、汽车等领域。
钣金成型工艺流程包括以下步骤:1.展开和下料在钣金成型前,需要对金属板材进行展开和下料。
展开是通过计算将二维的图纸转化为三维的立体展开图的过程,下料则是按照展开图将金属板材切割成所需形状和尺寸的过程。
2.弯曲和变形弯曲和变形是钣金成型的核心环节。
弯曲是将金属板材弯成所需形状的过程,包括压弯、滚弯、拉弯等。
变形则是通过机械、热等方式使金属板材发生形状改变的过程,如拉伸、压缩、扭曲等。
3.切割和连接在钣金成型过程中,需要对金属板材进行切割和连接。
剪板是将金属板材按照所需尺寸进行切割的过程,气割则是利用氧气和乙炔火焰将金属板材切割成所需形状和尺寸的过程。
激光切割是一种先进的切割技术,通过激光束将金属板材切割成所需形状和尺寸。
连接方式包括焊接、螺接等,需要根据实际情况选择合适的连接方式。
4.支架和镶嵌支架和镶嵌是钣金成型中的重要环节。
支架是在金属板材上打孔、折弯后制成的零件,用于支撑和固定其他零件。
镶嵌是将一个零件嵌入到另一个零件内部的过程,如轴套、轴承等。
设计时需要充分考虑支架和镶嵌的位置、大小、形状等因素,以保证钣金成型的稳定性和精度。
5.校正和修整校正和修整是钣金成型后的重要环节。
校正是指通过机械加工、热处理等方式将金属板材校正到正确的形状和尺寸。
修整则是为了提高金属板材表面的质量,去除毛刺、锐角等,使其达到所需精度和外观要求。
6.表面处理表面处理是钣金成型后为了提高金属板材的耐腐蚀性和美观程度而进行的处理过程。
表面处理一般包括清洗、防锈处理、涂层等步骤。
清洗是为了去除金属板材表面的污垢、氧化皮等杂质,以提高涂层的附着力。
防锈处理是为了提高金属板材的耐腐蚀性,一般采用喷漆、喷塑、镀锌等方式。
涂层是为了提高金属板材的美观程度和防护能力,一般采用涂料、油漆、镀铬等方式。
7.检查和组装检查和组装是钣金成型后的最后环节。
检查是为了验证钣金件是否符合设计要求,一般采用测量、外观检查等方式。
半钢子午胎成型工艺参数
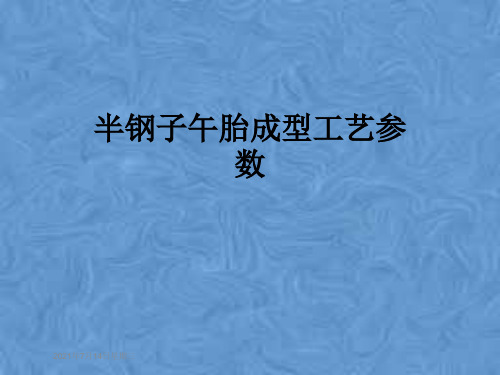
2±1
成型工艺
胎肩打压 脱空
成型工艺
• 材料接头定点。半钢子午胎有均匀
性的考虑,因材料接头处材料多出,
为此要考虑其位置的分布(施工表)。
主要接头点有内衬、钢丝圈、帘布、
胎侧、冠带层、胎面
三
帘
布
内
冠
衬
带
45
层
胎
帘
侧
布
5
二
帘 布
胎钢 冠圈
1
成型工艺
考试题
1.子午胎按机型成型方法?半钢成型时哪种方法? 2.子午胎按部件分成型方式?半钢成型目前是哪种成型方式? 3.画出生胎定点分布图?
1.6~2.0 kgf/cm2(三层胎体)
成型工艺
精元机胎面打压的工艺要求
CL A
B
C
位置
压力 kgf/cm2 停顿时间s
A
B
C
胎面中心
外层带束层 最宽带束层
端点
端点
1.5±0.5 2.5±0.5 2.5±0.5
1~2
2±1
2±2
D
E
过胎肩点 4±2mm
胎翼端点
2.5±0.5 2.0±0.5
2±2
胎面接头错位量≤2mm
a
成型工艺
胎面接头横向偏差 │a-b│≤2
a
b
成型工艺
三、成型工艺参数
RBF内压 • RBFⅠ一般≤0.5kgf/cm2, • RBFⅡ的宽度根据规格定,其作用是预定型,一般压力≤0.6kgf/cm2。 • RBFⅢ的宽度是个较重要的参数,充气压力在0.8~1.2 kgf/cm2(二层胎体)
下压 辊
横向对称性
≤1mm
径向位辊面超出 与鼓面相切 鼓距离0 ~ 1mm
钢结构制作工艺流程讲解

钢结构制作工艺流程讲解【范本1】钢结构制作工艺流程讲解本详细介绍了钢结构制作的工艺流程,通过细化的步骤,讲解了每一个环节的具体操作和注意事项。
一、工程准备阶段1.1 资料准备在工程准备阶段,需要采集并准备相关的资料,包括设计图纸、技术文件、施工方案等。
1.2 设备准备确定所需要的施工设备和工具,并进行检查、调试和保养。
二、钢材加工阶段2.1 钢材采购选择合适的钢材供应商,并进行采购。
要注意钢材的规格、质量和认证等方面的要求。
2.2 钢材切割根据设计图纸要求,采用切割设备对钢材进行切割,得到所需的各种尺寸和形状的构件。
2.3 钢材加工对切割好的钢材进行加工,如钻孔、焊接等。
确保构件的准确尺寸和质量。
三、构件预制阶段3.1 构件制作根据设计图纸和加工好的钢材,进行构件的预制。
包括焊接、磨光、喷漆等工序。
3.2 构件质量检验对预制好的构件进行质量检验,确保其符合设计和施工要求。
四、构件组装阶段4.1 搭设施工平台在施工现场搭设施工平台,为后续的构件组装提供便利条件。
4.2 构件组装将预制好的构件按照设计图纸要求进行组装。
包括焊接、螺栓连接等操作。
五、构件安装阶段5.1 构件运输将组装好的构件运输至施工现场,根据实际情况选择合适的搬运工具和设备。
5.2 构件安装按照施工方案,将构件进行安装,确保其位置、角度和水平度等要求。
六、施工完成阶段6.1 构件连接和加固完成构件的连接和加固工作,确保整体结构的稳定性和安全性。
6.2 检验和验收进行结构的检验和验收工作,确保施工质量符合设计和施工要求。
七、所涉及附件:1. 工程设计图纸2. 施工方案3. 钢材供应合同4. 技术文件八、所涉及法律名词及注释:1. 施工方案:指钢结构施工过程中所采取的具体行动和安排的规划和方案。
2. 结构稳定性:指结构在外力作用下能保持稳定的能力。
3. 施工质量:指施工过程中所达到的技术标准和要求。
【范本2】钢结构制作工艺流程讲解本详细介绍了钢结构制作的工艺流程以及相关的操作细节和注意事项,读者全面了解钢结构制作过程。
- 1、下载文档前请自行甄别文档内容的完整性,平台不提供额外的编辑、内容补充、找答案等附加服务。
- 2、"仅部分预览"的文档,不可在线预览部分如存在完整性等问题,可反馈申请退款(可完整预览的文档不适用该条件!)。
- 3、如文档侵犯您的权益,请联系客服反馈,我们会尽快为您处理(人工客服工作时间:9:00-18:30)。
步进第四步
海绵压辊下落 成型鼓旋转贴合
帘布裁刀压杆下落
裁刀裁断帘布
帘布接头贴合
海绵辊上升
帘布供料架退出
海绵压辊下落→成型鼓旋转→内衬层裁断压杆下落→裁刀裁料→内衬层供料架退 →海绵压辊上升→成型鼓位置调整→内衬层接头贴合
备注
1:帘布裁断时可用手按压帘布,防止裁刀将帘布卷起。 2:帘布接头贴合时按照标准贴合。帘布的长度可以设定定位角度来控制。
备注
带 束 鼓 传 递 环
带束层周长调整位置
传递环的作用有将带束鼓上 的组件取出送至涨缩机头的胎桶 上,并将压合完成后的成品胎胚 从涨缩机头取下。传递环的移动 采用左右两个气缸的动力。
传递环伸进距离由后方 联动螺丝来调控
4.3.二段设备结构介绍
二段操作主体
名称 图例 介绍 备注
夹 持 爪
涨 缩 机 头
换料时注意将材料和 衬布走向正确的位置, 位置错误会发生卷料现 象。
3.11.一段设备结构介绍
材料供料架
名称 内 衬 导 料 图例 介绍 备注
内衬层感应光电开关
帘 布 导 料 胎 侧 导 料
导料装置是依靠光电开关感 应的。原理是内衬层,帘布,胎 侧贴合后,材料收起,光电开关 感应不到,后方进行导开供料。
图例
介绍
备注
内衬层定中调整罗盘
帘布定中调整罗盘
帘布定中杆可直接松开 螺丝调整宽度。
3.10.一段设备结构介绍
材料供料架
名称
内 衬 送 料 车 帘 布 送 料 车 胎 侧 送 料 车
图例
介绍
备注
三种材料车各有两个卷轴, 附有材料的卷轴在导出材料的同 时将材料卷入另一个卷轴,导料 摩擦气缸,料车定位气缸和传动 电机气缸在更换材料时,全部打 到不接触状态。
备注
成 型 鼓
反 包 胶 囊
成型鼓的周长和宽度由 中间腰带的尺寸控制。
反包胶囊的作用是进行反包 动作,反包动作的形态为胶囊在 充气状态时,被推进罩推动进行 反包动作。
胶囊深入鼓的距离由后 方胶囊座的螺丝调控。
3.3.一段设备结构介绍
一段贴合主体
名称 图例 介绍
指形片的作用是在进行反包 动作前,对胎体进行正包,使子 口护胶伸展开,并且使胎圈顺利 进入,指形片动作采用气缸的动 力。
后压辊位置限位开关
4.5.二段设备结构介绍
带 束 层 供 料 架
带束层供料架是由一层,二层带束层材料车,裁刀,导料装 置和送料架等部件构成。
4.6.二段设备结构介绍
带束层供料架
名称
带 束 层 送 料
1.5. 二次法成型机一段
步进第五步
指形片进入正包
扣圈盘进入
胶囊反包
成型鼓转动 下压辊升起压合
按光标贴合胎侧
后压辊进入
胎侧供料架进入
下压辊下降
成型鼓调整位置→平压辊下降→指形片进入→扣圈盘进入→胶囊充气→推进盘进入 →胶囊退出→下压辊升起→成型鼓转动→下压辊合拢→胎侧供料架进入→后压辊进入 →下压辊分离→平压辊上升→按光标线贴胎侧
帘布感应光电开关
胎侧感应光电开关
4.1. 二段设备结构介绍
二 段 操 作 主 体
二段操作主体是由带束鼓,传递环,涨缩机头,后压辊,平 压辊,旋转机头等部件构成。
4.2. 二段设备结构介绍
二段操作主体
名称 图例 介绍
带束鼓分收缩和张开两种状 态,带束鼓表面分布着磁铁,可 吸住带束层,方便带束层贴合, 有一处磁铁较多,此处为一层带 束层接头处。带束鼓手动使用时 踩脚踏板来控制正转和反转。
三种送料架的作用是将内衬 层,帘布,胎侧平整水平的送至 成型鼓前方供贴合,并由裁刀将 其裁断。裁断时有压板压下,防 止卷料。
图例
介绍
备注
内衬层宽度及调整旋钮
帘布宽度及调整旋钮
胎侧宽度及调整旋钮
3.9.一段设备结构介绍
材料供料架
名称
内 衬 定 中 帘 布 定 中 胎 侧 定 中
材料定中装置的作用是在内 衬层进入供料架前端之前将其的 位置进行定中,确保材料贴合的 水平精度。 内衬层和帘布定中装置可调 整罗盘来调整定中装置宽窄的大 小,内侧圆板可调整定中装置的 左右移动。
备注
1:贴合前先观察指形片形态,测量指形片到成型鼓的距离和扣圈盘到成型鼓的距离是否符合标准。 2:测量胎侧各项精度是否符合标准。按光标贴合胎侧。查看下压辊压合压力是否符合标准。
1.6.二次法成型机一段
步进第六步
海绵压辊下落 成型鼓旋转贴合
胎侧裁刀压杆下落
裁刀裁断胎侧
胎侧接头贴合
海绵辊上升
胎侧供料架退出
备注
1:贴合前先测量成型鼓宽度,成型鼓周长以及胶囊插入鼓里的距离是否符合标准。 2:测量内衬层各项精度是否符合标准。按光标贴合内衬层。
1.2.二次法成型机一段
步进第二步
海绵压辊下落 成型鼓旋转贴合
内衬裁刀压杆下落
裁刀裁断内衬层
内衬层接头贴合
海绵辊上升
内衬层供料架退出
海绵压辊下落→成型鼓旋转→内衬层裁断压杆下落→裁刀裁料→内衬层供料架退 →海绵压辊上升→成型鼓位置调整→内衬层接头贴合
海绵压辊下落→成型鼓旋转→胎侧裁断压杆下落→裁刀裁料→胎侧供料架退 →海绵压辊上升→成型鼓位置调整→胎侧接头贴合
备注
1:胎侧裁断时可用手按压裁料压板,防止裁刀将胎侧卷起。 2:胎侧接头贴合时按照标准贴合。胎侧的长度可以设定定位角度来控制。
1.7.二次法成型机一段
步进第七步
成型鼓旋转下压辊压合
尾座退出
涨缩机头的位置有预定 型位置,定性位置,拉 直位置和上胎位置,操 作前先与施工表确认。
4.4.二段设备结构介绍
二段操作主体
名称 图例 介绍 备注
平 压 辊
后 压 辊
二段平压辊的作用是将胎胚进 行压合,排出空气。后压合伸进 是采用气缸的动力。
平压压合两侧移动是采用电机 的动力,移动位置的宽度是通过 限位开关来控制的。
备注
后 压 辊
后压辊旋转位置由限位 开关控制,左右移动由 编码器控制
下 压 辊
下压辊的作用是在反包动作 后,由外侧向内侧压合,将反包 内的空气压出,最后一步滚压的 时候,下压辊也提供压合的作用 下压辊伸出的动作采用气缸的动 力。
后压辊左右移动由编码 器控制
3.6. 一段设备结构介绍
一段贴合主体
名称 图例 介绍
备注
1:压合时查看平压辊和后压辊压合压力是否符合标准。
二次法成型机设备介绍
3.1.一段设备结构介绍
一 段 贴 合 主 体
一段贴合主体是由成型鼓,尾座,反包胶囊,推进罩,指形 片,扣圈盘,下压辊,平压辊,海绵压辊和后压辊等部件构成。
3.2.一段设备结构介绍
一段贴合主体
名称 图例 介绍
成型鼓分收缩和张开两种状 态,成型鼓表面分磨砂面和光滑 面,光滑面的位置是用来贴合内 衬层(内衬帘布符合件),手动 使用时踩脚踏板来控制成型鼓正 转和反转。
备注
平 压 辊
海 绵 压 辊
平压辊海绵应保持良好 状态,如发现损坏及时 更换。
海绵压辊高度调整是在 此处调整,两侧各一个
3.7. 一段设备结构介绍
材 料 供 料 架
材料供料架是由内衬层,帘布,胎侧分别的材料车,导料装 置,定中装置和送料架等部件构成。
3.8.一段设备结构介绍
材料供料架
名称
内 衬 送 料 架 帘 布 送 料 架 胎 侧 送 料 架
胎面供料架伸出
胎面接头贴合
胎面供料架伸出→胎面压辊下降→带束鼓旋转→胎面供料架收回→胎面接头贴合
备注
1:测量胎面各项精度是否符合标准。按光标贴合胎面。 2:胎面接头贴合时按照标准贴合。胎面的长度可以在设定中控制。
2.5.二次法成型机二段
步进第五步
传递环左移抓胎面
传递环右移至等待位
胎桶套入涨缩机头
带束鼓调整位置→传递环左移→抓片伸张→带束鼓收缩→传递环右移 →带束鼓侧循环第一步→一段胎桶套入涨缩机头
1:成型前先检测传递环抓片到带束鼓的距离,涨缩机头各项位置的数值是否符合标准。 2:胎桶放到涨缩机头的时候检查接头方式是否符合标准。
备注
2.6.二次法成型机二段
步进第六步
传递环右移放置胎面
机头充气缩至定型位
平压辊压合
传递环左移至等待位
传递环右移取胎胚
后压辊压合
PU环涨开传递环右移→传递环右移→涨缩机头缩至预定型位置→抓片收缩→传递环左移→涨缩机头缩至定型位置 →涨缩机头旋转→平压辊伸进→平压辊压合后缩回→后压辊伸进→后压辊分离 →后压合缩回后合拢→传递环右移→抓片张开→传递环右移→传递环左移→取下成品胎胚
备注
值形片应保持良好状态, 如有变形,损坏应及时 更换。
指 形 片 推 进 罩
推进罩的作用是当反包胶囊 充气后推进胶囊,从而完成反包 动作,推进罩的动作采用气缸的 动力。
推进罩伸进距离由后方 联动螺丝来调控
3.4.一段设备结构介绍
一段贴合主体
名称 图例 介绍 备注
扣 圈 盘
扣圈盘的作用是将胎圈固定, 在扣圈动作时将胎圈送至胎胚上。 扣圈盘未伸进时与成型 鼓的距离应保持在为 扣圈盘的动作采用气缸动力。 390±2MM
传递环上的夹持爪共同组成 一个圆周,抓片上有凸出的针头, 夹持爪高度是一定的, 根据不同规格的轮胎生 用来固定胎面,传递环传递胎面 产可更换夹持爪的高度。 时,要保持胎面的真圆,不能出 现掉冠等现象。