薄壁铝型材挤压有限体积分步模拟
薄壁铝合金型材稳态挤压模拟分析和实验验证
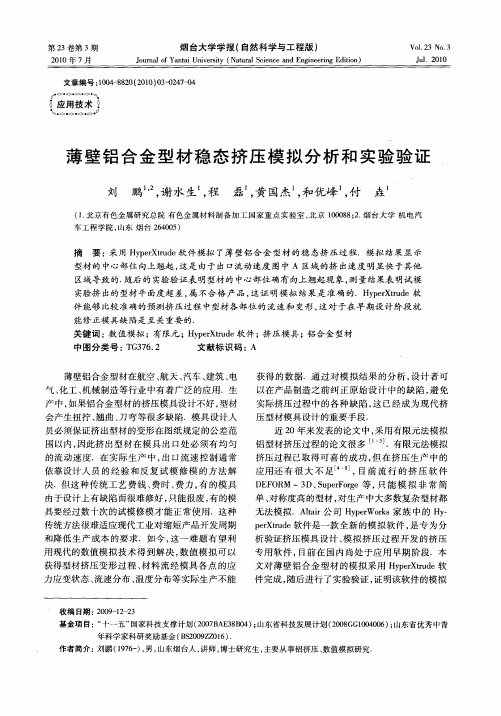
28 4
烟 台大 学学报 (自然 科学 与工 程版 )
第2 3卷
结果 准确 , 为模 拟 大 型 复杂 截 面 铝 合 金 型材 找 这
到 了切实 可行 的方 法.
擦 模 型为 C uo ol mb模 型 , 擦 系数 取 0 3 这一 模 摩 ., 型适用 于模 拟工 作带 处 的热 变形 过 程 .模 具 与型 材接 触 的前 端 面 、 流 室壁 面等 其 他 表 面 采用 粘 导 着模型, 即与模 具 表 面接 触 的铝 金 属 完 全粘 着 在 模 具表 面没 有相 对流 动 .型 材 工作 带处 的 网格 尺
型材 的 中心部位 向上 翘起 , 这是 由于 出 口流 动速 度 图 中 A 区域 的挤 出速度 明显 快 于其他
区域导致的. 随后 的实验验证表 明型材的中心部位确有 向上翘起现象, 测量结果表明试模 实验挤 出的型材 平 面度超 差 , 不 合格 产 品 , 证 明模 拟 结果 是 准确 的.H p r t d 属 这 y eX r e软 u 件 能 够比较 准确 的预 测挤 压过程 中型材 各部 位 的 流速 和 变 形 , 这对 于在 早期 设 计 阶段 就
无法 模 拟.A t r 司 H p r rs 族 中 的 H — li公 a y eWok 家 y pr t d eXr e软件是 一 款全 新 的模 拟 软 件 , 专 为分 u 是 析验证 挤 压模具 设 计 、 拟 挤 压 过 程 开发 的挤 压 模 专用 软 件 , 目前 在 国 内 尚处 于 应 用 早期 阶段 .本
能修 正 模 具 缺 陷是 至 关 重 要 的 .
关键 词 : 数值 模 拟 ;有 限元 ; yeXrd H pr t e软件 ; 压模 具 ; 合金 型材 u 挤 铝 中图分类 号 : G 7 . T 36 2 文献标 识码 : A
QForm extrusion铝型材挤压工艺模拟

模拟结果,中间的筋没有
实验结果照片,没有中间筋
模拟结果,中间的部分速度为零
第二十五页,共55页。
型材横截面上标记焊合线位置1
焊合线位置预测和验证
不同分流孔内的轨迹点用不同颜色显示
箭头显示焊合线的位置
焊合线位置用双线标记
1) With kind permission of Compes, Italy
第十二页,共55页。
实验结果 S. Abtahi (**)
模具角度及挤出速度对2mm厚铝型材滑动摩擦区域的影响
第十三页,共55页。
影响粘性摩擦的主要参数
程序中包含粘性摩擦条件
沿着工作带长度方向上的摩擦取决于:
•型材厚度
•挤压率 •工作带长度 •挤出速度 •模具角度
•型材温度
铝合金空心型材分流模挤压成形全过程温度场的数值模拟

铝合金空心型材分流模挤压成形全过程温度场的数值模拟侯文荣;张志豪;谢建新;陈蕴博【摘要】采用焊合区网格重构技术,解决包括分流与焊合过程的空心型材分流模挤压成形全过程温度场模拟问题,以一种典型大断面铝合金空心型材分流模挤压成形为实例,分析挤压速度和坯料温度对模孔出口处型材最高温度及型材横断面温度分布的影响,提出合理的坯料温度和挤压速度范围。
结果表明:挤压速度对模孔出口处型材横断面温度分布不均匀性的影响较大,而坯料温度的影响较小:当挤压速度由0.6 mm/s增大到3.0 mm/s,坯料温度为500℃时,模孔出口处型材横断面上最高与最低温度的差值(最大温差)由28℃增大到60℃;而当挤压速度一定,坯料温度在480~520℃变化时,型材横断面上最大温差的变化不超过3℃。
6005A 型材的合理挤压条件:坯料温度520℃时,挤压速度范围为0.63~0.93 mm/s;坯料温度500℃时,挤压速度范围为0.87~1.14 mm/s;坯料温度480℃时,挤压速度范围为1.10~1.34 mm/s。
%The precision simulation problem of the temperature field of hollow profile during the whole extrusion process, including the dividing and welding stages, was solved by mesh reconstruction technology of welding zone. Taking the porthole die extrusion of a typical aluminum hollow profile with large cross section as an example, the effects of billet temperature and extrusion speed on the maximum temperature of profile near the die exit and the temperature distribution on cross section were analyzed, and the reasonable billet temperature and extrusion speed were obtained. The results show that, the influence of the extrusion speed on the inhomogeneous temperature distribution of the cross section of the profile near the die exit is significant,while the influence of the billet temperature is not obvious. When the constant billet temperature is 500 ℃, the difference of the highest and lowest temperature (maximum temperature difference) on the profile cross-section increases from 28℃to 60℃with the extrusion speed increasing from 0.6 mm/s to 3.0 mm/s. The changes of maximum temperature difference on the profile cross section are not more than 3 ℃ with the billet temperature varying from 480℃to 520℃at constant extrusion speed. The extrusion conditions are that when the billet temperatures are 520, 500 and 480℃, the reasonable extrusion speed ranges are 0.63~0.93 mm/s, 0.87~1.14 mm/s and 1.10~1.34 mm/s, respectively.【期刊名称】《中国有色金属学报》【年(卷),期】2013(000)010【总页数】10页(P2769-2778)【关键词】空心型材;分流模挤压成形;网格重构;温度场【作者】侯文荣;张志豪;谢建新;陈蕴博【作者单位】北京科技大学材料先进制备技术教育部重点实验室,北京 100083;北京科技大学材料先进制备技术教育部重点实验室,北京 100083;北京科技大学材料先进制备技术教育部重点实验室,北京 100083;机械科学研究总院先进制造技术研究中心,北京 100083【正文语种】中文【中图分类】TG379在铝合金空心型材分流模挤压过程中,金属在分流和焊合过程中流动复杂,容易引起模具的局部温升和变形区金属温度的不均匀分布,显著影响挤压型材的质量和模具的强度。
挤压模具资料
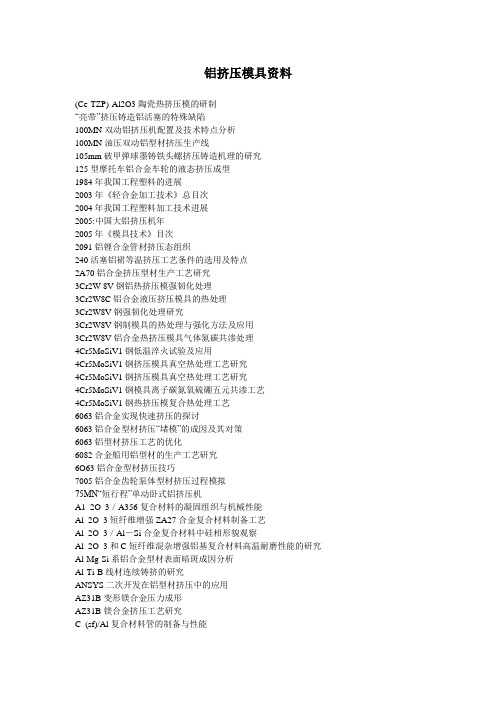
铝挤压模具资料(Ce-TZP)-Al2O3陶瓷热挤压模的研制“亮带”挤压铸造铝活塞的特殊缺陷100MN双动铝挤压机配置及技术特点分析100MN油压双动铝型材挤压生产线105mm破甲弹球墨铸铁头螺挤压铸造机理的研究125型摩托车铝合金车轮的液态挤压成型1984年我国工程塑料的进展2003年《轻合金加工技术》总目次2004年我国工程塑料加工技术进展2005:中国大铝挤压机年2005年《模具技术》目次2091铝锂合金管材挤压态组织240活塞铝裙等温挤压工艺条件的选用及特点2A70铝合金挤压型材生产工艺研究3Cr2W 8V钢铝热挤压模强韧化处理3Cr2W8C铝合金液压挤压模具的热处理3Cr2W8V钢强韧化处理研究3Cr2W8V钢制模具的热处理与强化方法及应用3Cr2W8V铝合金热挤压模具气体氮碳共渗处理4Cr5MoSiV1钢低温淬火试验及应用4Cr5MoSiV1钢挤压模具真空热处理工艺研究4Cr5MoSiV1钢挤压模具真空热处理工艺研究4Cr5MoSiV1钢模具离子碳氮氧硫硼五元共渗工艺4Cr5MoSiV1钢热挤压模复合热处理工艺6063铝合金实现快速挤压的探讨6063铝合金型材挤压“堵模”的成因及其对策6063铝型材挤压工艺的优化6082合金船用铝型材的生产工艺研究6O63铝合金型材挤压技巧7005铝合金齿轮泵体型材挤压过程模拟75MN“短行程”单动卧式铝挤压机A1_2O_3/A356复合材料的凝固组织与机械性能Al_2O_3 短纤维增强 ZA27 合金复合材料制备工艺Al_2O_3/Al-Si合金复合材料中硅相形貌观察Al_2O_3和C短纤维混杂增强铝基复合材料高温耐磨性能的研究Al-Mg-Si系铝合金型材表面暗斑成因分析Al-Ti-B线材连续铸挤的研究ANSYS二次开发在铝型材挤压中的应用AZ31B变形镁合金压力成形AZ31B镁合金挤压工艺研究C_(sf)/Al复合材料管的制备与性能C~+和Ti~+注入铝型材热挤压模表面改性研究CAD/CAM系统在挤压模具设计与制造中的应用CONFORM包覆机工模具调整提高铝包钢丝结合力Conform的扩展挤压及多孔管生产Conform机在生产多孔扁铝管产品上的应用CONFORM连续挤压变形过程的实验研究与数值模拟CONFORM连续挤压的模具Conform连续挤压内螺纹铝管工艺研究Conform连续挤压内螺旋翅片管模具研究CONFORM连续挤压生产线超高压(63MPa)液压系统分析与改进Conform连续挤压原理与铜线挤压加工的影响因素CVD技术在模具上的应用ECAP等径角挤压变形参数的研究ECAP工艺细化铁基形状记忆合金研究ECAP挤压L2纯铝的微观组织演化规律ECAP条件下纯铝的应变行为模拟研究ECAP细晶机制及对纯铝显微组织和力学性能的影响H13钢模具的表面强化技术H13钢热挤压模具自保护膏剂稀土硼碳氮共渗的应用研究H13钢散热器挤压模具失效分析H13铝型材挤压模具早期开裂失效分析H13模具钢的热加工工艺研究H13热挤压模具的开裂原因分析H13热挤压模具型腔变形原因分析及改进措施H13热作模具钢的表面热处理HPb59—1黄铜热挤压工艺及模具H形型材挤压模具的设计K87火车窗铝型材尺寸偏差的控制KBE技术在铝型材挤压模具设计中的应用LD31挤压型材缺陷和工艺优化LD8铝屑重熔—150活塞挤压铸造工艺LY12法兰盘液态模锻锻件及模具设计LY12法兰盘整体加压挤压铸造工艺试验LY12硬铝支架冷挤压工艺及模具设计Ni-Al系金属间化合物基复合材料的研究进展Ⅰ制备方法NiTi合金等径弯角挤压工艺及晶粒细化P/M制备SiC_p/Al复合材料的研究现状PAMOCVD工艺研究及在铝型材挤压模上的应用PCVD模具强化技术应用研究PLC在铝型材挤压机上的应用PSA氮气用于铝挤压保护SiC_p/A1复合材料挤压成形的实验研究SiC_P/Al复合材料搅拌熔炼—液态模锻成型工艺研究SiC_w/Al-Li-Cu-Mg-Zr复合材料压铸工艺的研究SiC_w/Al复合材料热挤压模具设计及其对挤压棒材组织和性能的影响SiC_W/LD2复合材料管材的包覆挤压SiC_w和纳米SiC_p混杂增强铝基复合材料的制备与评价SiCw/Al-Li复合材料热挤压变形及其对组织和性能的影响SiC颗粒增强铝基复合材料的挤压铸造工艺研究SiC颗粒增强铝基复合材料的热挤压工艺研究UGⅡ软件在铝型材挤压分流组合模具设计中的应用WCML-2热作模具钢的研究ZL201曲面薄壁件挤压铸造工艺及模具设计ZnAl_(22)的超塑成形及其装备阿尔福姆合金有限公司在挤压新工艺方面的成就半固态成形的工艺概况与模具材料选用半固态挤压SiC_p/2024复合材料的组织性能研究及缺陷分析半固态挤压变形体传热有限元模型及动态仿真半固态加工技术在机车车辆制造业中的应用前景半固态金属流变成形模具失效与选材半固态扩展挤压A2017合金过程中金属流动的有限元分析半固态模锻及其工业应用前景展望包装废弃物综合治理研究(续完)扁挤压筒的挤压力及应力场的光弹性分析扁挤压筒设计变断面铝型材挤压模平磨胎具的改进变断面型材模具加工工艺的改进变形铝合金均匀化热处理的应用现状与研究进展变形铝合金可挤压性的分析与评价变形铝合金可挤压性的分析与评价表面镀铝及附着碳化硅微粒的高模碳纤维与铝的压铸复合特性表面强化技术与模具寿命冰箱后板成形模设计并行工程在铝型材产品开发中的应用研究玻璃钢拉挤模具设计薄壁铝型材挤压成形的一种有效模拟方法薄壁铝型材挤压有限体积分步模拟薄壁门窗型材挤压的有限体积分步模拟薄壁小铝管盘拉过程游动芯头稳定性的实验研究不连续碳纤维增强ZA-12合金基复合材料的制备工艺不同方式等通道转角挤压纯铝微结构分析不同路径等通道转角挤压镁合金的结构与力学性能不同压力下挤压铸造铝铜合金的组织与性能不锈钢棘轮的温热挤压模具材料加工·制造工程·冷压成形采用H13横向模块提高挤压模具寿命采用挤压铸造新工艺生产柴油机铝活塞试验采用径向挤压方法使废铝颗粒再生成材的试验研究侧向挤压陶瓷型芯模具设计与型芯质量评估超A级尺寸精度铝油堵的成形工艺超大型材生产经验超高分子量聚乙烯的成型技术现状及研究进展(Ⅱ)超高强铝合金强韧化的发展过程及方向超宽型材模具的几种设计方法超声振动压力加工的现状与展望超塑技术在模具制造中的应用超塑性挤压在金属塑性成形中的应用超塑性挤压在金属塑性成形中的应用超塑性锌铝共晶合金成形工艺的研究超塑性在压力加工中的应用超塑性增强合金及其注塑模具热挤压的应用探讨车辆铝合金大型材模具的设计与制造工艺研究车身覆盖件冲压成形动态仿真的研究进展衬套冷技工艺及模具尺寸驱动图元在挤压模具中的应用冲裁过程和冲裁间隙冲裁挤压成型模纯铝等径角挤技术(Ⅰ)——显微组织演化纯铝等径角挤技术(Ⅱ)——变形行为模拟纯铝和LY12铝合金微塑性成形性能评价试验研究纯铝铸件JB—1并沟线夹的挤压铸造工艺打火机壳挤压模具及工艺大壁厚铝型材分流模的设计大变形零件温挤压凹模型孔设计技巧大尺寸多层喷射沉积6066Al/SiC_p/Gr复合材料管坯的制备大间隙冲裁对模具寿命的影响大口径弹尾部零件挤压铸造工艺的研究大宽厚比薄壁异型材挤压多工艺参数优化研究大型工业铝合金型材的挤压生产工艺与关键技术(续)大型铝合金散热器挤压型材的模具设计大型双鼓形铝轮毂精密锻模设计与改进大悬臂半空心铝型材模具设计大悬臂挤压模变形机理分析大悬臂铝型材挤压模的设计与强度校核带翼内凸筋D形铝管连续挤压生产工艺的研究带翼内凸筋D形铝管连续挤压生产工艺的研究氮化硼粉末静电喷涂技术在铝型材挤压生产上的应用德国洪塞尔铝业公司44MM挤压机等截面侧挤压技术及其实验模具设计等截面通道角形挤压对高纯铝微观组织及力学性能的影响等径角挤压法制备超细晶的研究现状等径角挤压法制备块体超细晶材料的研究现状及展望等径角挤压模具对超细晶材料显微组织的影响等径角轧制AZ31镁合金板材的组织与性能等径通道挤压中晶粒细化影响因素的研究进展等径弯曲通道变形力的研究等离子体表面改性技术及其在模具中的应用等通道弯角多道次挤压工艺累积变形均匀性研究等通道弯角挤压变形机理模拟与工艺参数优化等通道转角挤压(ECAP)工艺的研究现状等通道转角挤压纯铝的组织结构等通道转角挤压对L2工业纯铝力学性能的影响等通道转角挤压对纯铝L2阻尼性能的影响等通道转角挤压工艺有限元分析等通道转角挤压过程有限元模拟等通道转角挤压铝硅合金组织的研究等通道转角挤压模具挤压力计算等通道转角挤压实验模具设计等温热反挤压工艺参数对SiCp/LY12复合材料超塑性的影响等效应变量对等径角挤压的2A12铝合金力学性能的影响低碳马氏体在模具中的应用低体积分数SiC_W/Al复合材料的制备低温渗硼提高模具的使用寿命地铁车辆铝型材用特种挤压模具制造技术分析地铁车辆用边梁型材GDX-14模具的设计地铁特宽空心型材模具设计与挤压工艺研究地铁型材模具的探讨地铁用铝合金型材挤压模具设计第八讲空心铝型材挤压模具优化设计(2)第二讲铝型材挤压模具的材料选择第二届全国液态模锻(挤压铸造)学术交流会论文摘要第九讲民用建筑铝型材挤压模具优化设计第六讲实心铝型材挤压模具优化设计(2)第七讲空心铝型材挤压模具优化设计(1)第三讲铝型材挤压模结构要素与设计原则第十讲工业铝型材模具优化设计(1)第十一讲工业铝型材模具优化设计(2)第四讲铝型材挤压模具的种类及组装形式第五讲挤压垫优化设计第五讲实心铝型材挤压摸具优化设计(1)第一讲挤压筒的优化设计(1)第一讲铝型材挤压模具概论电锤钻双键槽冷挤压成型新工艺电动机连接端盖拉伸精整模设计电加工技术在模具上的应用电解磨料喷射抛光工艺的试验研究电缆连续挤压包覆产品缺陷的分析电缆连续挤压包覆技术及设备电缆铝护套连续挤压包覆模具的设计电缆铝护套连续挤压包覆型腔设计的均压判定准则短碳纤维增强铝基复合材料的半固态加工短碳纤维增强铝基复合材料的挤压浸渗工艺短纤维氧化铝/铝复合材料液态浸渗后直接挤压的试验研究锻压模具的润滑对4Cr5MoSiV1热挤压模具钢加工工艺的研究对挤压模工作带的设计、加工、修正的研究对我国铝材挤压加工发展之管见对向式间接液态金属模锻对中国铝挤压工业若干问题的探讨对中国铝挤压工业若干问题的探讨多孔管、棒挤压模加工工艺的改进多坯料挤压及在铝/铝合金复合材料成形中的应用多腔室模具加热曲线及控制发射器用大型散热器挤压模设计反向挤压技术及挤压设备反向挤压模具设计探讨反向挤压时的挤压力变化规律反应烧结氮化硅陶瓷模具材料的研究非对称空心铝型材模具设计的重要原则非牛顿特性下冷挤压流体动力润滑模型的建立分流挤压镁合金管材工艺研究分流模挤压紫铜电脑散热片实验研究分流模在挤压生产中的应用分流组合模挤压的有限元模拟与模具设计评价粉末冶金法制造SiCp/LY12复合材料及SiCp/LY12复合材料超塑性研究粉末冶金制备颗粒增强5052铝基复合材料的压力加工工艺研究风机生产模具及工艺装备造价的对比研究氟塑料加工复杂断面空心型材挤压模具的制作技术复杂盒形零件挤压金属非均匀流动控制研究复杂铝型材挤压成形有限体积仿真改进重载铝活塞的技术改善挤压性能,提高6063合金挤压速度钢铝层叠复合材料固态复合技术及应用钢铝复合导电轨制造技术的探讨高表面质量铝管冷挤成形及挤光工艺高纯铝等通道转角挤压引起的微观组织变化高光洁度大铝管冷挤成形及挤光工艺高精度铝合金挤压型材生产的新发展高铝青铜Cu-14%Al-X合金的气孔及消除方法高铝锌基合金ZA27液态模锻工艺参数研究高铝锌基合金挤压铸造的组织和性能的研究高铝锌基合金直齿圆锥齿轮的挤压铸造工艺高强超高精度7A04超硬铝合金导轨型材的研制高强度铝及铝-锂合金大型壁板和型材的生产高强韧冷作模具钢——LD钢的性能和应用高热强性热作模具钢的开发研制及模具寿命的提高高热强性热作模具钢的研制开发及模具寿命的提高高速锤热挤压增压器涡轮叶片高速列车用大型挤压铝型材工业铝型材挤压模具的设计工艺参数对铝型材挤压变形规律的影响工艺润滑材料的发展评述骨架表面改性对SiC/Al复合材料性能的影响关于挤压变形规律理论研究方法的一些探讨管材挤压工艺分析及实验研究管子钳铝合金钳柄体液态挤压工艺及模具罐用铝材的研究现状及存在的问题分析光塑性在连续挤压成形研究中的若干关键技术广东铝型材热挤压模具渗氮技术的发展广东热处理表面工程与市场经济广东省几家模具企业发展的启示硅酸铝短纤维增强铝硅合金复合材料热处理组织的研究硅线石/2024液态挤压成形件的摩擦学特性硅线石颗粒/LY12搅融混合后半固态挤压成形件组织与性能研究硅线石颗粒/铝搅融混合半固态挤压成材的试验研究硅线石颗粒与铝液混融后挤压下流动凝固的塑性变形特征轨道车辆大型铝合金型材模具的设计与制造技术轨道车辆用大型铝合金型材的开发评估及挤压工艺特点国内外挤压铸造技术发展概况国内外模具发展概况国外冲压与模具技术动向国外反应注塑成型技术的进展国外铝和铝合金挤压模具的发展国外铝挤压技术及其装备的进展国外铝加工技木新进展国外模具技术发展动态国外钛工业发展概况和加工工艺新发展(续)过共晶铝硅合金半固态挤压铸造近终成形技术研究过共晶铝硅合金活塞的挤压铸造过共晶铝合金汽缸体的挤压铸造航空用DQ3137型材舌型挤压模具的改进合理大间隙冲裁模的应用黑色压铸用铜合金模具材料活塞用碳纤维铝基复合材料的制备方案研究基于BP神经网络的铝型材挤压模具优化设计基于BP网络和遗传算法的铝型材挤压模工作带优化模型基于BP遗传算法的铝型材挤压模具优化设计基于UG平台构建三维铝型材挤压模具CAD系统基于VB6.0的轻合金带筋壁板挤压模具CAD系统开发基于多变性设计的回转体零件挤压模具结构智能设计方法研究基于多重优化设计的铝型材挤压工作带模型基于流函数法的铝型材挤压导流模合理设计基于热力耦合的热挤压模具结构参数优化设计基于数值模拟的铝型材挤压变形规律的研究(Ⅱ)基于数值模拟的铝型材挤压变形规律的研究(I)基于有限元分析的铝合金等温挤压工艺设计基于有限元技术的大型6061无缝管挤压温度变化规律研究基于有限元模拟的型材挤压专家系统基于知识的铝型材挤压模具集成设计系统极限变形程度下纯铝反挤压变形力的研究几种多腔工业铝型材挤压模具的设计几种具有优良性能的模具钢几种铝型材挤压模具的改良设计几种铝型材挤压模具的优化设计挤出吹塑模具设计挤出模损坏原因分析及改进办法挤压不锈钢用高铝青铜合金模具材料挤压成形技术在接插件端子模具设计中的应用挤压锭铸造新方法——气滑铸造挤压分流模CAD关键技术的研究挤压分流组合模的设计挤压工模具材料及其热处理与表面处理现状挤压工艺和模具对成品率的影响及措施挤压珩磨在模具研磨工艺上的应用挤压珩磨在模具制造中的应用挤压加工润滑剂的应用挤压加工新技术挤压浸渗法制备C_(sf)/Al复合材料的组织与性能挤压铝合金型材时牵引力的计算挤压铝型材表面“停止痕”缺陷的成因与对策挤压铝型材产品开发计算机辅助设计系统挤压铝型材出现“咬痕”的原因及预防措施挤压铝型材的悬臂模具设计挤压铝型材断面难度系数的探讨挤压模的寿命及提高实例挤压模具CAD应用程序开发技术挤压模具氮化工艺控制挤压模具电火花加工空刀新工艺挤压模具气体软氮化及废气处理新工艺挤压模具软氮化工艺实践挤压模具设计技术挤压模具设计综合数据库系统挤压模具使用寿命的主要影响因素挤压模具使用寿命影响因素的分析挤压模具早期失效起因与处理挤压模具制造工艺分析挤压模孔优化的CAD研究挤压渗流铸造泡沫铝合金的工艺因素探讨挤压式铝管外导体物理发泡射频同轴电缆的设计制造及铝管缺陷分析挤压筒锁紧面大帽的起因分析挤压温度对高硅铝合金材料组织与性能的影响挤压型材内腔加强筋的超声波探伤挤压硬铝时工艺条件对制品强度和粗晶环厚度的影响挤压铸件优质化技术进展挤压铸造CF/Al复合材料的工艺研究挤压铸造SiC_w/L3复合材料的热挤压挤压铸造SiC_w/L3复合材料液-固两相区包覆挤压挤压铸造代替锻铝的试验挤压铸造的应用与模具材料挤压铸造对过共晶铝硅合金活塞各部位含硅量分布的影响挤压铸造法制备(SiC/A1)/A1复合材料挤压铸造法制备可变形SiC_P/Al复合材料的组织与性能挤压铸造工艺参数对Al_2O_(3f)/Al-4.5%Cu复合材料凝固方式与组织的影响挤压铸造工艺参数对柱塞式大高径比ZA27合金铸件力学性能的影响挤压铸造技术的发展及应用挤压铸造铝合金车轮模具的结构与排气挤压铸造铝合金的材料研究挤压铸造铝基复合材料凝固偏析研究挤压铸造模具材料的选用及热处理挤压铸造模具三维运动仿真介绍挤压铸造模温对C/Mg复合材料组织和性能的影响挤压铸造硼酸铝晶须增强Al基复合材料浸渗过程理论分析挤压铸造汽车空压机铝连杆的试验研究挤压铸造汽车空压机铝连杆的研制与应用挤压铸造汽车制动主缸的研究与应用挤压铸造—烧结反应制备Al_2O_3/Ti_xAl_y复合材料新工艺挤压铸造碳纤维增强A356金属基复合材料凝固过程的研究挤压铸造条件下铝基复合材料铸造流动性研究挤压铸造条件下铝基复合材料铸造流动性研究挤压铸造无缩孔判据在有色金属中的验证挤压铸造用模具材料的选用技术改造推动了模具专业化发展加工过程对渗氮铝挤压模性能的影响加工制造过程对铝挤压模具寿命的影响加磷处理过共晶铝硅合金的挤压铸造夹头冷挤模设计间接挤压铸造模具编码系统研究减轻铝型材表面光泽条纹的措施检阅水平、交流技术、沟通渠道的一次盛会——参观“全国模具及模具加工机械展销会” 简易模具的制作及其应用(连载)——[Ⅰ]简易模具的基础知识角铝型材挤压过程的数值模拟接合型复合材料的成形界面对纤维增强铝硅合金复合材料耐磨性的影响金属表面的电火花强化法金属材料半固态挤压工艺的有限元分析金属材料的等通道转角挤压研究进展金属反向挤压技术的发展与应用前景金属复合线材成形工艺的研究开发概况金属挤压成形理论与技术发展的现状与趋势(1)金属挤压成形理论与技术发展的现状与趋势(2)金属挤压成形理论与技术发展的现状与趋势(3)金属连续铸挤包覆成型技术金属塑性成形模具的灵敏度分析金属微成形技术及其研究进展近代铝合金反向挤压技术近期国内液态模锻技术的一些研究进展九十年代模具技术的发展动向矩形钼管加工工艺研究具有较大舌比的半空心铝型材模具的设计聚苯乙烯泡沫塑料模的制造均匀流场在铝合金冷挤压中的应用(英文)颗粒增强金属基复合材料挤压性能的研究颗粒增强铝基复合材料的制备及应用颗粒增强铸造铝合金内燃机活塞材料的研究空调压缩机外壳的液态挤压成形空心铝铆钉冷挤压工艺及其模具的研究空心铝型材挤压成形过程的有限元数值模拟空心铝型材挤压过程计算机仿真系统空心铝型材挤压时金属流动的计算机辅助(CAD)分析空心型材分流组合挤压CAD/CAE模型的建立空心型材挤压模具模芯变形的有限元分析快速成型与快速模具制造技术快速模具制造技术的应用研究快速凝固/粉末冶金制备高硅铝合金材料的组织与力学性能快速凝固SiC_p/LY12复合材料的制造工艺和性能快速凝固高硅铝合金粉末的热挤压过程快速凝固过共晶铝硅合金材料的研究进展快速凝固铝锂合金粉末特性对其挤压村组织和性能的影响宽断面美格铝型材模具的设计宽截面铝型材挤压导流模应用研究宽展挤压模具正交试验研究扩音器话筒接头冷挤压模具设计冷冲模设计参考资料(三)冷挤工艺在圆形连接器中的应用冷挤铝手柄工艺及模具冷挤压凹模受力分析冷挤压锻铝的润滑剂冷挤压机载荷与缓冲参数关系的试验研究冷挤压技术的发展及模具冷挤压流体动力润滑模型的建立冷挤压散热片模具及工艺冷挤压通孔凹模受力分析与横向开裂冷挤压柱塞加工离子注入工模具材料表面改性及其展望力学分析在挤压模具调整方面的应用利用废旧模具生产优质电渣熔铸模具钢锭的新技术连续包覆(CONCLAD)模具优化的模拟实验连续变断面挤压成形方法的研究*连续变断面挤压工艺的开发连续挤压/包覆模具型腔CAD系统开发连续挤压D97多孔扁管组织性能的研究连续挤压包覆CATV同轴电缆芯线防灼伤系统研究连续挤压包覆技术在铝包钢丝生产上的应用连续挤压成形过程的计算机仿真连续挤压带翼内凸筋D型铝管模具研究连续挤压多通道铝扁管用硬质合金模具的研制连续挤压法介绍连续挤压工模具负载的计算机模拟连续挤压和连续包覆技术的理论研究与工程实践连续挤压铝管典型缺陷的原因分析及预防措施连续挤压模具的选材连续挤压模具型腔汇合室几何参数优化设计连续扩展挤压成形常见缺陷分析与预防连续铸挤成形技术的发展及应用连续铸挤成型技术及其发展连续铸挤生产铝管的力能计算与分析连续铸挤生产铝管的研究两种粒径颗粒混合增强铝基复合材料的导热性能流变法铸造石墨铝挤压铸造工艺参数的正交试验研究。
有限元作业-铝材挤压过程分析

铝材挤压过程分析(状态非线性问题)1、问题描述(1)问题的提出在用模具挤压型材的过程中,可能由于模具先天设计不合理导致挤压型材从模具口出来后产生一定程度的变形,如果变形超出许可程度,那么工作人员需要进行修模或者重新设计模具。
利用有限元分析软件可以预测型材和模具在挤压载荷的作用下产生的变形和应力,设计人员可以通过计算结果,分析原因,并对模具和挤压方式等进行改进。
(2)问题描述如图1-1所示为金属铝坯料和挤压模具结构示意图,铝的应力应变关系如图1-2所示,坯料与模具之间的摩擦因数为0.1,求挤压过程中坯料内部的应力场变化。
坯料材料参数:弹性模量:E1=69MPa;泊松比:v1=0.26。
模具材料参数:弹性模量:E1=360MPa;泊松比:v2=0.3。
图1-1 金属坯料和模具图1-2 铝的应力和应变关系2、整体规划该问题属于状态非线性大变形接触问题。
在分析过程中根据轴对称性,选择挤压式样和模具纵截面的1/2建立几何模型。
3、选择单元类型,定义材料性能因为该问题属于接触问题,所以选择CONTA172接触单元和TARGE169目标单元以及PLANE182结构单元进行求解。
坯料材料参数:弹性模量:E1=69MPa;泊松比:v1=0.26。
模具材料参数:弹性模量:E1=360MPa;泊松比:v2=0.3。
TARGE169单元实常数设置如图2-1所示:图3-1 TARGE169单元实常数设置4、创建几何模型(1)通过坐标值生成矩形面,选择Main Menu/Preprocessor/Modeling/Create/Ar eas/Rectangle/By Dimensions 命令,在出现的对话框中输入点的坐标值分别为:X1=0,Y1=0;X2=8E-3,Y2=0.05;X3=7E-3,Y3=-0.02;X4=0.025,Y4=-0.01。
得到如图4-1所示图形。
图4-1 两个矩形面(2)定义两个关键点,选择Main Menu/Preprocessor/Modeling/Create/Keypoints/In Active CS命令,在出现的对话框中输入关键点编号分别为9,10,坐标值分别为:(8E-3,0,0),(0.025,0,0)。
数值模拟铝型材挤

Company Logo
有限体积法模拟实例
上海交大的周飞等人利用有限体积法挤压成形过程中金属的流动情况,给出了 成形各阶段等效应变、温度和速度等物理场量的分布情况以及整个成形过程中 模具载荷/ 行程曲线的变化情况
门窗锁扣铝型材数值模拟
Company Logo
LOGO
数值模拟铝型材挤压过程
顾晨词
内容
1 2 3 4
介绍 数值模拟主要方法 数值模拟解决实际问题
结语
Company Logo
数值模拟的意义
铝合金型材在日常生活及生产领域应用越来越广泛, 用挤压的方法生产大型工业用铝型材,既节约金属又 具有很高的生产效率。由于挤压模具内部是封闭的, 因此材料的流动、应力与应变场的分布以及模具载荷 材料的整个求解 域离散为一系列相 互连接的单元体
求解各单元和节点 在每一加载步上的 物理场量
Company Logo
有限元法控制方程
1虚功率方程
Sijδ Eij dV0 = ∫ S0 Pi 0δ Vi dS 0 + ∫ V0 bi0δ Vi dV0 ∫ V0 &
有限元法
很好地处理变形 体与模具的接触 问题,又具有较 高的模拟精度
Company Logo
数值模拟软件
1应用有限体积法模拟的软件主要有 MSC/SUPERFORGE 2应用有限元法模拟的软件主要有 DEFORM,ANSYSLS等
Company Logo
2本构方程
& σ j = L[ D − D p ]
3有限元列式
[ K ]{∆v} = {∆F }
Company Logo
有限体积法
薄壁铝型材挤压成形的一种有效模拟方法
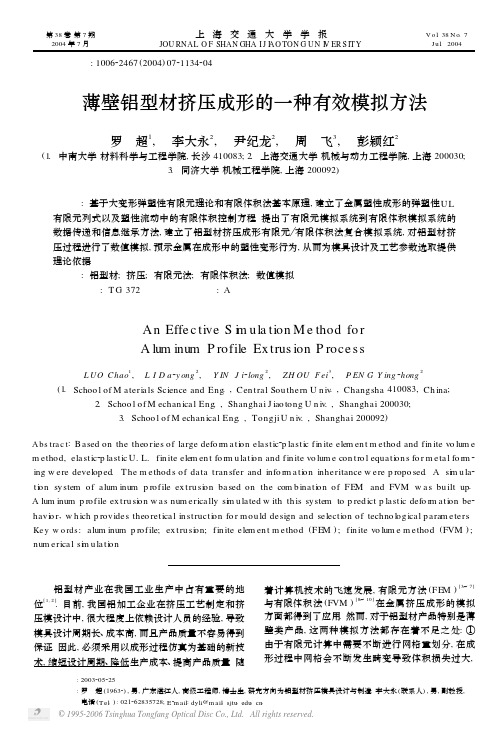
有限体积法将材料流动所要经历的空间采用
Eu ler 网格进行离散. Eu ler 网格是一个固定在空间 的参考框架, 物质从一个单元流到另一个单元, 材料 的质量、动量和能量也随之从一个单元流到另一个
基于taggeredid11方法对上述控制方程进三维弹塑性有限元理论弹塑性体发生温度耦合的塑性变形时行有限体积展开然后采用龙格2库塔法求解各微分方程从而得到有限体积内变形体的各种物理为变形率张量可表示em?fvm复合模拟方法为弹性变形温度以及塑性变形引起的变形率之在铝型材挤压过程中由于挤压比特别大很难由坯料直接挤出产品实际生产中往往采用导流模或分流模进行预成形
着计算机技术的飞速发展, 有限元方法 (F EM ) [3~ 7] 与有限体积法 (FVM ) [8~ 10] 在金属挤压成形的模拟 方面都得到了应用. 然而, 对于铝型材产品特别是薄 壁类产品, 这两种模拟方法都存在着不足之处: ① 由于有限元计算中需要不断进行网格重划分, 在成 形过程中网格会不断发生畸变导致体积损失过大,
收稿日期: 2003205225 作者简介: 罗 超 (19632) , 男, 广东湛江人, 高级工程师, 博士生, 研究方向为铝型材挤压模具设计与制造. 李大永 (联系人) , 男, 副教授,
电话 (T el. ) : 021262835728; E2m ail: dyli@m ail. sjtu. edu. cn.
Байду номын сангаас
单元. 在材料流动的过程中, 必须满足质量守恒、动 量守恒、能量守恒等控制方程:
7644方管铝型材挤压过程仿真模拟及模具对比分析结果

3、模具部分的应力、压力、变形位移的数值模拟结果采用彩色云图方式表示,两种模具设计方案对比分析
小结具体内容如表9所示。
表9 模具部分的压力、应力、变形位移仿真模拟结果及分析表
对比内容
1#设计方案
2#设计方案
模具部分 压力分布 彩色云图 对比结果
模具部分 等效应力 彩色云图 对比结果
模具部分 变形位移 彩色云图 对比结果
3、模具设计方案三维立体模型对比内容
根据2个原始模具设计图(dwg格式),使用Solid works软件做三维造型, 获得初始设计三维模型,2套模 具共同内容和差异内容的对比表如表1所示。
表1 模具设计方案及三维模型结果对比表
对比内容
1#设计方案
2#设计方案
共同点
模具外径为Φ180mm,上模厚度:75mm,分流腔深度:75mm,模芯高出分流出口平面:8mm,模芯高
模具出口处 型材内表面
平均温度 (℃)
502.1
模具出口处 型材内表面
温度范围 (℃)
497.6 ~
505.1
模具出口处 型材内表面
平均温度 (℃)
499.5
模具出口处
型材内表面
温度范围
(℃)
494.9 ~
503.8
模具出口处 型材内表面 温度差异率
(%)
1.49
模具出口处 型材内表面 温度差异率
(%)
数值模拟分析模型的挤压过程数值模拟边界条件设置内容,如表5所示。 表5 挤压过程数值模拟边界条件
物理量
参数设置
铝合金坯料和工模具腔体内表面之间为粘性摩擦
Stick
铝合金坯料和工模具外表面之间为粘性摩擦
Stick
- 1、下载文档前请自行甄别文档内容的完整性,平台不提供额外的编辑、内容补充、找答案等附加服务。
- 2、"仅部分预览"的文档,不可在线预览部分如存在完整性等问题,可反馈申请退款(可完整预览的文档不适用该条件!)。
- 3、如文档侵犯您的权益,请联系客服反馈,我们会尽快为您处理(人工客服工作时间:9:00-18:30)。
第39卷第1期 2005年1月上海交通大学学报JOU RNAL O F SHAN GHA I J I AO TON G UN I V ER S IT YV o l .39N o.1 Jan .2005 收稿日期:2004202226基金项目:上海市启明星跟踪计划资助项目(01QM H 1411)作者简介:李大永(19732),河北唐山人,副教授,主要从事金属塑性成形CAD CA E KBE 研究.电话(T el.):021*********; 文章编号:100622467(2005)0120006204薄壁铝型材挤压有限体积分步模拟李大永1, 王洪俊2, 罗 超3, 彭颖红1, 周 飞4(1.上海交通大学机械与动力工程学院,上海200030;2.上海大众汽车有限公司,上海201805;3.中南大学材料科学与工程学院,长沙410083;4.同济大学机械工程学院,上海200092)摘 要:建立了铝型材挤压成形有限体积法分步模拟系统.研究了有限体积分步求解方法关键技术,实现了各分步有限体积模拟系统的数据传递和信息继承.在每一分步计算中,占用相对较少的计算机资源,可划分更为细致的有限体积网络.利用该方法成功地模拟了薄壁类铝型材挤压成形过程,并对成形中应力、应变及温度场分布的演化进行了分析.研究结果表明,有限体积分步法是模拟薄壁类铝型材挤压成形过程的有效方法.关键词:铝型材;挤压;有限体积法;分步模拟中图分类号:T G 316.92 文献标识码:AS i m ula tion of Thin 2W a lle d A lum inum P rofile Extrus ion P roce s sw ith M ulti 2s ta ge F inite V o lum e M e thodL I D a 2y ong 1, W A N G H ong 2jun 2, L UO Chao 3, P EN G Y ing 2hong 1, ZH OU F ei4(1.Schoo l of M echan ical Eng .,Shanghai J iao tong U n iv .,Shanghai 200030,Ch ina ;2.Shanghai V o lk s w agen A u tom ative Co .L td .,Shanghai 201805;3.Schoo l of M aterials Science and Eng .,Cen tral Sou thern U n iv .,Changsha 410083;4.Schoo l of M echan ical Eng .,Tongji U n iv .,Shanghai 200092)A bs tra c t :In the si m u lati on of th in 2w alled alum inum p rofile ex tru si on p rocess ,the fin ite elem en t m ethod(FE M )can resu lt in disto red p roduct shape due to frequen t m esh rezon ing ,w h ile the requ irem en t of fin ite vo lum e m ethod (FVM )on com p u ter resou rce is too h igh .T he key techno logy fo r m u lti 2state FVM si m u la 2ti on w as studied .D ata tran sfer and info r m ati on inheritance betw een successive stages w as fu lfilled .B e 2cau se less m em o ry is needed in every single stage ,m o re refined fin ite vo lum e m esh can be zoned .T he ex 2tru si on p rocess of a th in 2w alled alum inum p rofile w as si m u lated w ith the p ropo sed m ethod .T he evo lu ti on of stress ,strain and tem peratu re distribu ti on w as analyzed .T he si m u lati on resu lts show the m u lti 2stage FVM is an effective num erical si m u lati on m ethod fo r alum inum ex tru si on p rocess and can help the develop 2m en t of new alum inum ex tru si on p roducts .Ke y w o rds :alum inum p rofile ;ex tru si on ;fin ite vo lum e m ethod (FVM );m u lti 2stage si m u lati on 挤压成形是一个复杂的热力耦合过程,只依靠实验与经验并不能完全掌握其变形规律.金属塑性成形数值模拟技术不仅可以实时地描述成形过程中的塑性流动模式、各种物理场量的分布规律,而且还能预测成形过程中的缺陷,优化成形过程.目前,基于L agrange方法的有限元方法[1~5]与基于Eu ler方法的有限体积法(FVM)[6,7]在金属挤压成形的模拟中都得到了应用.然而,对于薄壁类铝型材产品挤压成形,这两种模拟方法都存在着缺陷.在FVM模拟中,有限体积网格需要事先占据材料所要经过的所有空间.对于薄壁类型材产品,需要将网格划分很细,因此采用FVM模拟会占用大量计算机内存,如果对成形进行一步模拟,往往会因为内存不足导致计算无法进行下去.如果采用较粗网格,虽然占用内存少,但是模拟精度又不能得到保证.针对这种情况,本文采用了有限体积分步模拟方法,将型材产品的挤压过程分为多个阶段进行模拟,每一步的模拟结果作为下一步的初始条件.这样,在每一步中可以采用比较细致的网格,而又不会占用很多的计算机资源.1 FV M基本理论及模拟方法1.1 FV M基本理论FVM将材料流动所要经历的空间采用Eu ler 网格进行离散.在材料流动的过程中,必须满足控制方程质量守恒方程、动量守恒方程、能量守恒方程、状态方程、塑性材料的应力2应变关系[7].基于Stag2 gered Grid[8]方法对控制方程进行有限体积展开,然后采用龙格2库塔法[9]求解各微分方程,从而得到有限体积内变形体的各种物理场量.1.2 FV M分步模拟方法1.2.1 方法流程 整个模拟过程按以下步骤进行:(1)建立型材挤压模具和坯料的几何模型,输入到第1步FVM数值模拟系统中.(2)根据坯料及模具数学模型建立有限体积网格体系,并输入材料、工艺参数和模拟控制参数.(3)施加力学和温度边界条件,采用FVM对第1步成形过程进行模拟.第1步成形结束,输出有限体积模拟结果到中间数据文件.(4)建立新的有限体积网格体系,并实现第1步有限体积模拟系统到第2步有限体积模拟系统的几何数据及各种场量的传递,将上一步的成形结果作为下一步的“坯料”.(5)输入模拟所需的控制参数.(6)采用FVM模拟第2步成形过程.(7)如达到预期的产品形状,则整个模拟过程结束,否则重复(4)~(7),直到达到预期产品形状. 1.2.2 各分步间的几何数据传递 对于三维变形体的几何外形,在有限元中采用四面体或六面体单元表面网格来表示.数据传递过程中,首先将上一步数值模拟系统中变形体的表面网格分解成一系列有序的三角形小平面,然后以STL格式输出到数据文件,再输入到下一步有限体积模拟系统中.1.2.3 各分步间物理场量数据传递 为了将上一步数值模拟系统中变形体的物理场量传递到下一步模拟系统中,必须首先计算有限体积网格体系的中心格点在原有的有限体积网格体系中的局部坐标.设i为新的有限体积网格体系的中心格点,它在上一步网格体系中的局部坐标为(Ν,Γ,Φ),则i点的物理场量可以通过下式插值得到f i(Ν,Γ,Φ)=∑pj=1N j(Ν,Γ,Φ)f0j其中:f i(Ν,Γ,Φ)为新的有限体积网格中心格点i的任意一个物理场量(如速度场、应变速率场、应变场、应力场和温度场等);f0j为j点所在的原有网格体系中各节点相应的物理场量;p为单元的节点个数; N j(Ν,Γ,Φ)为插值函数.对于不在原有限体积网格体系中的新的有限体积中心格点,其物理场量置零.这样便得到了用于下一步有限体积数值模拟的初始物理场量.2 应用实例 图1为深圳某铝业公司的型材产品,图2为零件尺寸图,最小壁厚为1.5mm.图3为工作带设计图.型材材料为6061铝合金,棒料直径为80mm.棒料预热温度为470°C,模具温度为450°C,摩擦系数取0.4.图1 型材产品图F ig.1 P ractical alum inum p rofile product图2 零件尺寸图(mm)F ig.2 Secti on configurati on7 第1期李大永,等:薄壁铝型材挤压有限体积分步模拟图3 3种方法模拟结果对比F ig .3 R esults comparison of si m ulati on m ethods 数值模拟在1.0GCPU 、1.0GB 内存的PC 计算机上进行.压下量S =5mm .由图3可见,有限元法模拟由于多次网格重划分而产生畸变,FVM 一步模拟受计算机资源所限,最小单元尺寸不能超过0.9mm ,模拟结果表面不够平整,FVM 分步模拟中,最小单元尺寸可以取到0.5mm ,得到了比较好的结果.图4 第1步模拟阶段的等效应力分布F ig .4 Effective stress distributi on during the first stage 图4为第1步模拟过程(S =3.5mm )的等效应力分布的演化过程,图5为经过与第1步模拟结果的数据传递后第2步模拟过程(S =5.0mm )的等效应力分布的演化情况.在预成形开始阶段,坯料和模具接触端面外缘环状区域内存在一个难变形区,这是由于受到挤压筒、模面和坯料3方挤压造成的,因而挤压刚刚开始时该区域应力较大.当金属充满导流模模腔,即完成材料终成形前的预先分配.在预成形阶段由于成形相对容易,大量金属流入导流模模腔,变形主要集中于坯料顶端与预成形模口相接触的边沿区域,因而该区域应力也相对较大.铝材经过预成形后开始进入到终成形平面模工作带部分,由于平面模模口狭长,金属的流动变得十分困难;同时在导流模口靠中心对称面区域也形成一个难变形区.因此金属在工作带和导流模口靠近对称面区域的应力最大.图5 第2步模拟阶段的等效应力分布F ig .5 Effective stress distributi on during the second stage 图6为第1步模拟过程的等效应变分布的演化过程,图7为经过与第1步模拟结果的数据传递后第2步模拟过程的等效应变分布的演化情况.可以看出,刚刚开始时,难变形区应变较大,随后在预成形阶段,变形主要发生在预成形导流模口边缘.终成形阶段,变形主要集中在平面模模孔工作带区域,最大等效应变达5.273.图6 第1步模拟阶段的等效应变化分布F ig .6 Effective strain distributi on during the firststage图7 第2步模拟阶段的等效应变分布F ig .7 Effective strain distributi on during the second stage 图8为第1步模拟过程的温度场分布的演化过程,图9为经过与第1步模拟结果的数据传递后第2步模拟过程的温度场分布的演化情况.由于模具预热温度与棒料初始温度接近,铝材和模具之间的热交换较少,成形过程中变形体的最高温度发生在工作带附近,并向四周递减.8 上 海 交 通 大 学 学 报第39卷 图8 第1步模拟阶段的温度场分布F ig .8 T emperature distributi on during the firststage图9 第2步模拟阶段的温度场分布F ig .9 T emperature distributi on during the second stage3 结 语采用有限体积分步模拟的手段来仿真铝型材的挤压成形过程,一方面可以避免网格再划分难题,另一方面可以很好地解决FVM 一步模拟方法所面临的计算机资源不足的问题,保障模拟过程顺利地完成并获得理想的模拟结果.因此,对于薄壁类铝型材挤压这类极度大变形塑性成形问题,FVM 分步法是一种行之有效的数值模拟方法.参考文献:[1] 彭颖红,周 飞,阮雪榆.汽车联轴节壳体挤压成形过程三维有限元数值模拟[J ].上海交通大学学报,1998,32(5):18-21.PEN G Y ing 2hong ,ZHOU Fei ,RUAN Xue 2yu .N u 2m erical si m ulati on of j o int shell extrusi on p rocess us 2ing 3D finite elem ent m ethod [J ].Journal of Shangha i J i aotong Un iversity ,1998,32(5):18-21.[2] 周 飞,彭颖红,阮雪榆.铝型材挤压过程有限元数值模拟[J ].中国有色金属学报,1998,8(4):637-642.ZHOU Fei ,PEN G Y ing 2hong ,RUAN Xue 2yu .N u 2m erical si m ulati on of alum inum m aterial extrusi on by finite elem ent m ethod [J ].The Ch i nese Journal ofNonferrousM et als ,1998,8(4):637-642.[3] Park Y B ,Yoon J H ,Yang D Y ,et al .F inite elem entanalysis of steady 2state th ree di m snsi onal helical ex 2trusi on of tw isted secti ons using recurrent boundary conditi on [J ].I n t J M ech Sc i ,1994,36(2):137-148.[4] Yang D Y ,L ee C M ,Yoon J H .F inite elem ent analy 2sis of steady 2state th ree di m ensi onal extrusi on of sec 2ti on th rough curved dies [J ].I n t J M ech Sc i ,1989,31(2):145-156.[5] 闫 洪,包忠诩,柳和生,等.角铝型材挤压过程的数值模拟[J ].中国有色金属学报,2001,11(2):202-205.YAN Hong ,BAO Zhong 2xu ,L I U H e 2sheng ,et al .N um erical ulati on of angle alum inum p rofile extru 2si on p rocesses [J ].The Ch i nese Journal of Nonferrous M et als ,2001,11(2):202-205.[6] 周 飞,苏 丹,彭颖红.有限体积法仿真金属塑性成形的基本理论[J ].上海交通大学学报,2002,36(7):915-919.ZHOU Fei ,SU D an ,PEN G Y ing 2hong .Basic theo ry fo r si m ulati on of m etal fo r m ing w ith finite vo lum e m ethod [J ].Journal of Shangha i J i aotong Un iversity ,2002,36(7):915-919.[7] 周 飞,苏 丹,彭颖红.铝型材挤压有限元和有限体积对比模拟[J ].上海交通大学学报,2003,37(7):1072-1076.ZHOU Fei ,SU D an ,PEN G Y ing 2hong .Contrastsi m ulati on of alum inum extrusi on p rocess w ith FE M and FVM [J ].Journal of Shangha i J i aotong Un iversi 2ty ,2003,37(7):1072-1076.[8] Slagter W J ,F lo rie C J L ,V enis A C J .A dvances in3D fo rging p rocess modeling [J ].Journal of Co m put a -tional Physics ,1991,92:82-105.[9] 沈永欢,梁在中,许履瑚,等.实用数学手册[M ].北京:科学出版社,2001.726-732.上海交通大学学报国家期刊奖百种重点期刊 百种中国杰出学术期刊欢迎投稿 欢迎订阅9 第1期李大永,等:薄壁铝型材挤压有限体积分步模拟。