生产力改善手法稼动分析繁体
稼动分析
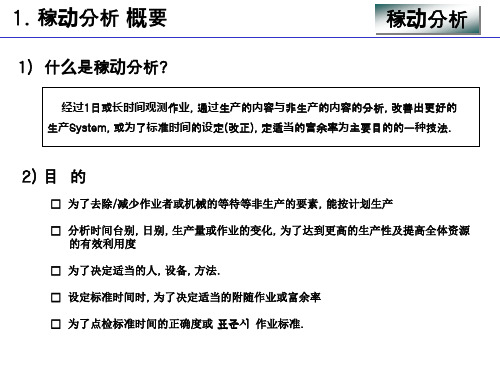
4
0:15 0:25 1:20 1:40 1:55 2:00 2:30 2:50 3:10 3:30 3:45 (19) (17) (23) (21) (20) (18)
5
0:05 0:25 0:45 1:05 1:50 2:10 2:20 2:30 2:35 2:50 3:00 (24) (21) (23)
(23)
6:20 6:45 6:50 7:25
4:35 5:40 6:45 7:35
(25)
7:00 7:55
8
(17)
(18) (15)
9
0:05
0:20 1:05 1:25 130 2:05 2:25 (18) (17) (24)
10
0:25
0:30 0:40 0:45 1:00 1:10 1:25 1:40 2:15 2:20 2:30 (22) (20) (15) (21)
• 为了减少不必要的步行的LAYOUT改善.
• 根据作业单调的生产量减少对策. • 准备作业的标准化. • 为了富余率减少的对策 • 为了振作现场的士气的对策. • 机械设备故障对策 • 为了监视.等待时间减少的对策 (工程的再编成)
• 自动计测, 自动调节, 自动化的检讨.
• 对突发性的事故, 应急措施,联络, 指使, 顺序的明确化.
= P-
P(1-P) n
< 1日的观测数为 200的 Work Sampling的 P管理图 >
□ 点检精密度 S = 4 (1-P) NP
※ 不满足时, 以观测后出现的概率为基础再算出观测分数, 把有差异的再观测.
2) 改善着重点
• 组 作业的情况, 谋求作业的分割及配分的适当化 • 作业 LOT的适当化 • 使作业者困惑的非正规作业或不必要作业的排除 • 检讨稼动率与变化推移, 决定休息时间 • 工具移动/损失, 材料/制品的搬运, 清扫等准备作业的分业化.
IE七大手法介绍
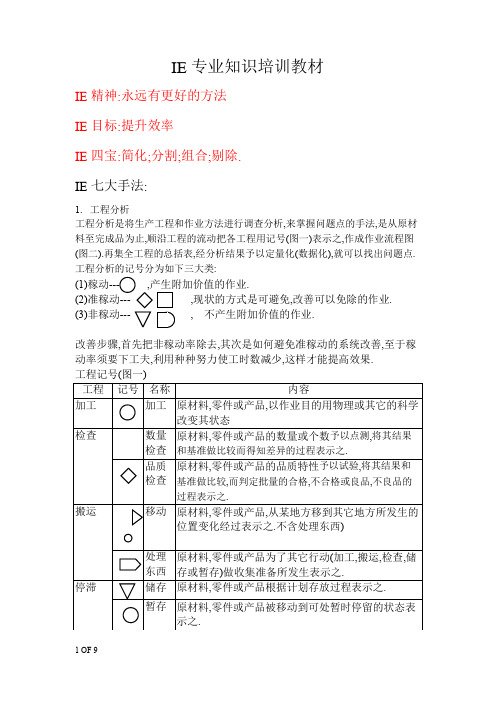
工程记号(图一)IE专业知识培训教材IE精神:永远有更好的方法IE目标:提升效率IE四宝:简化;分割;组合;剔除.IE七大手法:1.工程分析工程分析是将生产工程和作业方法进行调查分析,来掌握问题点的手法,是从原材料至完成品为止,顺沿工程的流动把各工程用记号(图一)表示之,作成作业流程图(图二).再集全工程的总括表,经分析结果予以定量化(数据化),就可以找出问题点.工程分析的记号分为如下三大类:(1)稼动.(2),现状的方式是可避免,改善可以免除的作业.(3),不产生附加价值的作业.改善步骤,首先把非稼动率除去,其次是如何避免准稼动的系统改善,至于稼动率须要下工夫,利用种种努力使工时数减少,这样才能提高效果.工程分析(图二)机种:2.稼动分析Working Sampling是人和机械的稼动状态,以瞬间观测(瞬时看到状况来观测,得到结果加以分类,记录)周而复始的采取抽样方式.列入对象的发生率作为实用上可以满足信赖度和精度,以统计来推定之方法.换模换线加班整理作业宽放现场宽放方便宽放疲劳宽放待待闲聊重修不在2.人的稼动观测分析项 稼动 非稼动 合计 目主作业 附带作业 准备作业 宽放 除外作业 观 测 (作业者不同内容也不一样)时 间 8:15 8:35 9:20 …… …… …… … 17:30 合计135 4030 10 72比率 45 13 10 7 2(%)58173. 生产线平衡分析依照流动生产的工程顺序,从生产目标算出周期时间,将作业分割或结合,使各 工站(工程)的负荷均匀,提高生产效率的技术,叫做生产线平衡(Line Balancing) 1. 生产线作业编成三种状况<案三> 12 121 1作 作 业 业公式:生产线编成损失率=(1-作业编成率)×100% 2. 生产线平衡的推行步骤(1) 将工程分为单位作业测定(2) 工程分析表(pitch diagram)的作成 (3) 计算 balance 效率和 balance loss(4) 实施 line balancing,则时间长的工程分配到时间短的工程 (5) 改善后的作成(pitch diagram)(6) 改善后 balance 效果和 balance loss 计算 (7) 结果比较3. pitch diagram(从减少式时数改变为减少工程数的范例) 将可分解的动作分至其它工位,使各工位时间平均.4. 时间分析时间研究(time study)就是作业内容的时间经过,利用任何的测时机或记录设备抽 观测的方法,时间研究是泰勒创始的,制度为了将一天的公平工作量也就是作业任 务设定最合理最好的标准时间的手法.1. 观测器材 马表,摄影机2. 时间研究的实施步骤(1) 明确目的有改善现行的工作方法,设定标准时间,检讨现行标准时间的妥当性等 (2) 选定观测对象的作业通常选定反复性较高的作业,优其就重视在制造成本中比重较大的作业 (3) 选定观测对象的作业员通常依时间研究的目的不同,对选定对象作业员也有差异,如以改善工作 为目的时,应以熟练工为之,如以设定标准工时为目的时,则以普通或稍 高技术水准的作业员为之.(4) 获得有关人员(现场负责人,作业员)的理解与协助 (5) 检讨作业方法 (6) 预备调查(7)将作业分割为单位作业的单位(8)决定观测次数(9)实施马表观测(10)观测结果的整理与检讨(11)发表整理所得的结果标准工时的构成:作业时间+宽放时间=标准工时宽放种类:5.动作分析(Therblig)Therblig是动作研究,由吉伯莱夫妇(F.B GLIBRETH,1869-1924)开发的,有18种基本动作要素的分析方法,它是用目视观察,将各种动作要素组合,因此也称为目视动作分析.1.动作分析的意义从作业者的动作顺序来观察要素动作,不产生附加值的作业(不合理,不平衡,不需要=3不)或作业者周边的治工具配置等.作为改善检讨之眼点的手法,叫做动作分析2.动作分析的范围和IE手法区分工程单位作业要素动作手法工程分析单位作业的时间分动作分析PTS法观测手段探听到资料码表VRT目视例切断溶接刀具研磨材料安装手伸出刀具安装4点锁紧材料压住切断加工电源寻找电源操作3.动作分析的种类目视动作分析----------Therblig分析胶卷分析---------------Memo Motion StudyPTS法------------------WF法第一类:推行工作时必要的动作(要素)虽然不能免掉,唯看动作顺序,尽量在短时间内完成的改善.第二类:有此动作就会延迟第一类动作尽量考虑排除它.第三类:并没有推行工作的动作(要素)既没有执行工作的物体,应该要排除它.*第二类和第三类列为改善的对象.5.Therblig分析方法左手动作Therblig右手动作改善着眼点左眼睛右向容器伸手把容器移动靠向身边抓住螺丝左右同时拿过平抓住装配握住6.Therblig分析方法(1)首先使用准备好的纸张(2)左手的分析折写在左侧的纸张上,右手的分析写在右侧的纸张上,并记录记号和说明(3)分析之前务必要观察数次的动作作周期,并将顺序充分记在头脑里即可(4)分析的起点是从取拿新材料移动时算起(5)全周期先作要素作业予以分开(必要时将左手,右手的要素作业各别记述之(6)从右手(经常动的手)开始分析(7)左手同样的分析与右手之Therblig的时间关系要弄清楚(8)为了能够有良好的分析,其关键在于最初要素作业分开,务必切实去执行(9)时间的测定使用马表.6.动作经济的原则1.动作经济的概要动作经济的原则,并要为了排除人的无谓(浪费)动作,利用人工学使其动作最经济而获得正确,快速,轻松,安全的工作,提高效率的一种动作改善方法.此为美国有名的动作研究家吉伯莱慈(F.B GILBRETH)所创始的.2.动作经济的着眼睛点(1)尽量利用东西的力量(惯性,重力)(2)动作以最短距离为原则(3)工具和材料尽量靠近作业者前面的配置3.动作经济的四项基本想法●不必要的动作要减少(免掉)●动作时包含双手,双脚同时活用●动作必须采用最小范围和最短距离●动作就排除动作物和勉强的姿势而是轻轻松松4.动作经济原则的三项分类之原则除了基本之外●有关使用身体的原则●有关作业场所的原则●有关工具,设备设计的原则7.工厂布置的改善1.工厂布置(layout)改善的重要性工厂在推行生产活动时,务必考虑到厂房内的设备,机械,治工具,物料搬运等,如何有系统的安排与布置,期使达到最经济,安全,有效率的活用而提高生产力.1.改善的必要性销售方式(受订生产,计划生产),品种和生产量(少品种多量,多品种少量),流程方法(连续生产,批量生产).1.2因应技术的进步和变化时作业的机械化,自动化以及材料,加工方法的技术进步和更新.1.3设计变更时随着设计变更而工程和作业方法必须变更1.4现状的工厂布置生产力不佳时8OF9依据稼动分析和工程分析,现场有很多浪费.1.5生产量常有增减时生产量常有巨大的增减,必须换装设备和工程变更.1.6现场有必要移动时全工厂门间变更.1.7新产品投入时新产品导入生产,必须增减机械,工程和加工方法的变更.2.七项改善的原则1.目的要明确化的原则2.考虑生产要素(4m)的原则3.提高水平的原则4.最短移动与流程的原则5.利用立体空间的原则6.安全与满足的原则7.具有弹性的原则3.工厂布置的关键性1.必须配合制程的需要(可行性)2.减少物料搬运(经济性)3.作业方式维持弹性调整性质(调整性)4.在制品保持高周转率(经济性)5.设备投资减少(经济性)6.充分利用空间(经济性)7.有效运用人力及设备产能(经济性)8.维持良好作业环境(安全性及舒适性)4.工厂布置改善的五项基本要素●P(Product):产品或材料要生产甚么产品●Q(Quantity):量以品目别,要生产多少●R(Route):(工程)经路如何做,使它生产●S(Service):补助服务可做为生产补助的动力,补助设备●T(Time or Timing):时间到底是下个月或是几年后。
IE改善与提高OEE、稼动率:提升生产效率和竞争力
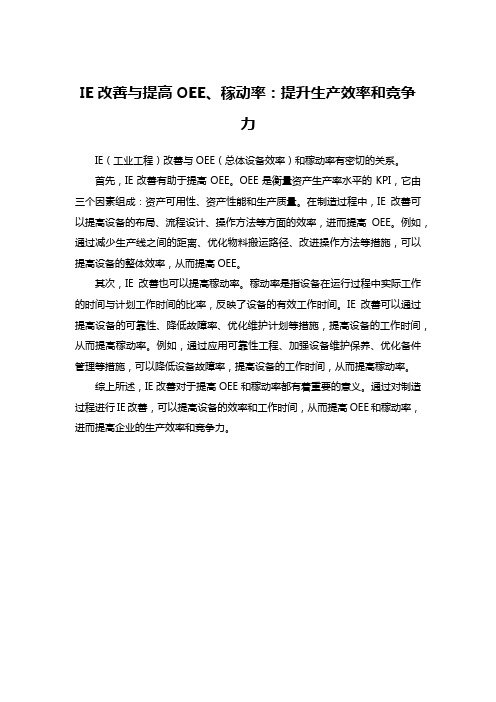
IE改善与提高OEE、稼动率:提升生产效率和竞争
力
IE(工业工程)改善与OEE(总体设备效率)和稼动率有密切的关系。
首先,IE改善有助于提高OEE。
OEE是衡量资产生产率水平的KPI,它由三个因素组成:资产可用性、资产性能和生产质量。
在制造过程中,IE改善可以提高设备的布局、流程设计、操作方法等方面的效率,进而提高OEE。
例如,通过减少生产线之间的距离、优化物料搬运路径、改进操作方法等措施,可以提高设备的整体效率,从而提高OEE。
其次,IE改善也可以提高稼动率。
稼动率是指设备在运行过程中实际工作的时间与计划工作时间的比率,反映了设备的有效工作时间。
IE改善可以通过提高设备的可靠性、降低故障率、优化维护计划等措施,提高设备的工作时间,从而提高稼动率。
例如,通过应用可靠性工程、加强设备维护保养、优化备件管理等措施,可以降低设备故障率,提高设备的工作时间,从而提高稼动率。
综上所述,IE改善对于提高OEE和稼动率都有着重要的意义。
通过对制造过程进行IE改善,可以提高设备的效率和工作时间,从而提高OEE和稼动率,进而提高企业的生产效率和竞争力。
稼动分析

■何谓稼动分析 稼动分析就是定量的掌握人或设备的稼动状态,及发现非稼动的原因 与存在的问题,并对其进行改善。
家用空调公司顺德工厂
■稼动分析的种类 连续观测法:全数检查 稼动分析 工作抽样法:抽样检查 ■连续观测法(时间分析法) 对作业员或设备的稼状态长时间并连续性地 进行调查分析的一种手法。 ■工作抽样法(次数分析法) 对作业员或设备的稼动状态根据行动分类,对其 状况多次抽样进行调查分析的一种手法。
工作抽样法可以在工厂、办公室、商店、医院、政府、机构等场所 获得广泛应用。如选举调查、顾客分布、电视收视率调查、购买意向调 查等应用工作抽样法都取得很好的效果。
家用空调公司顺德工厂
■工作抽样法实施步骤
一、定义问题 明确调查目的, 明确调查目的,测定内容 七、根据随机时刻表或乱数表决定观 测时刻
二、理解作业内容 详细了解作业内容, 详细了解作业内容,场地
居 宨
作 业 员
宼
孥 孽 対
宨
寅 宨 孷 中 层 居
宨
中 孷 孷 设 备
孷 孷 宨中 子 対
尟
居 寅 宨 宨
子
家用空调公司顺德工厂
■工作抽样法观测点数确定 观测数 的标准 100 600 2000 4000 10000以 上
NO 1 2 3 4 5
观测的目的 发现一般的问题点,找出线索的场合(确定故障所 在) 探寻机械停止作业,作业人员等待时间的原因 评价特定的状态(安排,产品的处理,延误等)的 场合 想了解人和机械的工作效率的场合 设定标准时间,确定余裕率,精确了解人和机械的 工作率的场合
五、计算观测数 预测发生的比率求出观测的总数 六、决定每天观测点数 根据观测人数天数计算每天观测点数
十一、整理结果 检查精度 十一、整理结果,检查精度 整理观测结果舍弃异常观测值
关于生产稼动率计算公式的文章

关于生产稼动率计算公式的文章生产稼动率计算公式及其应用生产稼动率是一个衡量企业生产效率的重要指标,它反映了企业在一定时间内实际生产能力与理论最大生产能力之间的比例关系。
通过计算生产稼动率,企业可以评估自身的生产效率,并据此制定相应的改进措施,提高生产效益。
生产稼动率的计算公式如下:生产稼动率 = 实际产量 / 理论最大产量× 100%其中,实际产量是指企业在一定时间内真正完成的产品数量,理论最大产量是指在相同时间内,以最高效率运行时可以达到的产品数量。
通过这个公式,我们可以得到一个百分比数值,它表示了企业实际利用了多少潜在的生产能力。
如果稼动率接近100%,则说明企业已经充分利用了其可用资源,并且达到了最高效益。
相反,如果稼动率较低,则说明企业存在一定程度上的资源浪费或者运营不足。
那么,在实际应用中,我们如何使用这个公式呢?首先,我们需要确定实际产量和理论最大产量。
实际产量可以通过统计数据或者现场观察得到,而理论最大产量则需要根据企业的生产能力和生产线的运行效率进行估算。
这一步需要准确的数据和合理的假设,以确保计算结果的准确性。
其次,我们将实际产量和理论最大产量代入公式中进行计算。
计算结果将告诉我们企业当前的生产稼动率是多少。
如果稼动率较低,我们可以进一步分析原因,并采取相应的措施来提高生产效率。
例如,可以优化生产流程、提高设备利用率、加强人员培训等。
最后,我们需要定期进行稼动率的监测和评估。
通过长期观察稼动率的变化趋势,我们可以了解企业生产效率的整体发展情况,并及时调整管理策略以适应市场需求。
总之,生产稼动率是一个重要的指标,它可以帮助企业评估自身的生产效率,并据此制定相应的改进措施。
通过合理运用计算公式和监测方法,企业可以不断提高自身的竞争力,并实现可持续发展。
设备稼动率改善报告

设备稼动率改善报告设备稼动率改善报告概述本报告旨在分析和评估当前设备稼动率,并提出改善稼动率的相关建议。
通过采取有效的措施,公司可以提高设备的利用率和效率,从而实现生产成本的降低和生产能力的提升。
当前设备稼动率分析1.稼动率定义:设备稼动率是指设备实际运行时间与总可用运行时间的比例,通常以百分比表示。
2.稼动率计算公式:稼动率 = (设备实际运行时间 / 总可用运行时间) * 100。
3.目前公司设备稼动率:根据数据统计,公司设备稼动率为XX%。
4.稼动率低下的原因分析:通过详细调研和分析,我们发现以下几个主要原因导致了设备稼动率的低下:–设备故障频繁导致的停机时间增加;–生产计划不合理,导致设备长时间闲置;–操作人员技能不足,操作效率低下;–设备维护不当,导致频繁故障和维修时间增加。
改善设备稼动率的建议1.提高设备维护水平:–建立完善的设备维护计划,包括定期保养和预防性维修;–培训维护人员,提高其维修技能和知识水平;–定期检查设备,及时发现和解决潜在故障。
2.优化生产计划:–与生产部门密切合作,根据市场需求和设备能力,制定合理的生产计划;–减少产品切换时间,提高设备的连续生产能力;–引入先进的计划管理系统,实时跟踪设备状态和生产进度。
3.提升操作人员技能:–组织培训和知识分享会,提高操作人员的技术水平;–建立标准化的操作流程和作业指导书,降低操作错误率;–建立奖励机制,鼓励操作人员提高工作效率和稼动率。
4.引入设备监控系统:–安装设备监控系统,实时监测设备运行状态,快速发现异常情况;–建立设备维修记录和故障分析数据库,用于排查和修复设备问题。
结论通过以上建议的实施,我们相信公司的设备稼动率将会得到明显的改善。
提高设备稼动率不仅可以提高生产效率和产品质量,降低生产成本,还能够增加公司的竞争力和市场份额。
我们建议公司在改善设备稼动率方面持续投入资源和精力,确保改善措施的有效实施和成果的持续改进。
设备稼动率改善报告(续)改善措施的执行与监测1.设立设备稼动率改善团队:由相关部门的代表组成,负责制定、执行和监测改善计划;2.制定改善计划:根据以上建议,确定改善目标、具体措施和实施时间表;3.分配责任人:明确每项改善措施的责任人,并设立监测机制,确保改善进度的及时反馈和跟进;4.定期检查和评估:设立定期检查和评估机制,对改善措施的执行情况进行监测和评估,及时调整和改进措施。
稼动率分析与改善
三稼动率分析与改善从综合效率的计算公式(4-8)可以看出,要提升效率,可以从提升作业能率和提升稼动率入手。
首先来分析如何提升稼动率。
从表4-1中可以看出,提升稼动率,就是要减少损失时间,而损失时间又由除外时间与异常时间组成。
基中,除外时间只只能尽量缩短,但往往是必不可少的,因此提升稼动率的主要着眼点即为异常时间的降低。
1异常时间的种类拨所谓的异常时间(或称异常工时),是指造成制造部门停工或生产进度延迟的情形。
由此而产生的时间浪费。
由表面膜势得知,异常时间一般包括:①计划异常因生产计划临时变更或安排失误等导致的异常。
②物料异常因物料供应不及时(断料)、物料品质问题等导致的异常。
(3)设备异常因设备、工装不足或故障等原因而导致的异常。
(4)品质异常因制程中出现了品质问题而导致的异常,也称制程异常。
(5)机种异常因产品设计或其他技术性问题而导致的异常,也称产品异常或技术异常。
(6)水电异常因水、气、电等导致的异常。
2、异常的处理流程(1)异常发生时,发生部门的制造主管应立即与生技单位或相关责任单位联络,共同研拟对策加以处理。
(2)一般应先采取应急对策,并加以执行,以尽快恢复生产,降低异常时间的影响。
(3)在异常处理同时或异常排除之后,由制造部门填具生产异常报告单(如表4-7),并转责任单位。
(4)责任单位填写异常处理之根本对策,以防止异常重复发生。
(5)制造单位、责任单位依据该单作后续追踪工作、确认是否得到改善。
(6)财务部门依该异常单作为制造费用统计之凭证,并作为向厂商索赔之依据。
(7)生管部门依异常状况作为生产进度管制控制点,并作为生产计划调度之参考。
3、异常工时计算规定(1)当所发生的异常,导致生产现场部分或全部人员完全停工等待时,异常工时之影响以100%计算。
(2)当所发生的异常,导致生产现场需增加人力投入,采取临时应急对策处理该异常时,异常工时之影响以实际增加投入的工时为准。
(3)当所发生之异常,导致生产现场作业速度放慢(可能同时也增加人力投入)时,异常工时之影响度以实际影响比例计算。
稼动率简介
照X RAY 151 15.52% 69.27%
鑽測試 帶 105 10.79% 80.06%
放板子 84 8.63% 88.69%
叫測試帶 程式 34 3.49% 92.19%
叫測試帶程式
叫鑽頭 程式 28 2.88% 95.07%
鑽外圍孔 24 2.47% 97.53%
收板子 24 2.47% 100%
Productivity Management
170000 160000
Gap 1
150000 140000 130000
Gap 2
120000 110000 100000 90000 91年4月1日 4月1日 目標產量 實際產量 145390 130921 91年4月2日 4月2日 145390 111395 91年4月3日 4月3日 145390 97758 91年4月4日 4月4日 165390 151580 91年4月5日 4月5日 165390 161775 91年4月6日 4月6日 165390 161545
Effect Factors
The result of output (PD,PE,QA) Parameter & Operation Method (PE)
Cycle Time
PM, Shift Turnover, Break Down… (PD, ME, PP入每一action item所預期的改善比率 應加入每一 所預期的改善比率 *改善前 一般機台 理論稼動率:76.5 % 改善後 模範機台 理論稼動率:90 % 改善前(一般機台 理論稼動率: 改善後(模範機台 理論稼動率: 模範機台)理論稼動率 改善前 一般機台)理論稼動率
稼動管理
線別-機台 一、異常管理(by線別 機台 異常管理 線別 機台)
稼动率分析与改善
稼动率分析与改善稼动率是指设备或设施在单位时间内正常运转的时间比例,通常以百分比表示。
稼动率是衡量设备运行效率和产能利用率的重要指标之一、稼动率高,意味着设备运行效率高,生产能力得到充分利用;反之,稼动率低,意味着存在运行效率低下、停机时间过长等问题,需要进行改善。
稼动率的分析可以通过以下几个步骤进行:1.收集数据:首先,需要收集设备或设施运行状态的数据,包括开始运行时间、停机时间、故障时间等。
这些数据可以从设备控制系统中获取,也可以通过人工记录的方式获得。
2.计算稼动率:根据收集到的数据,计算稼动率。
稼动率的计算公式为:(运行时间/(运行时间+停机时间+故障时间))*100%。
计算得出的值即为稼动率。
3.分析稼动率:对计算得到的稼动率进行分析,找出存在的问题。
如稼动率低,说明设备存在运行效率低下、停机时间过长等问题;而稼动率高,但产量低,则说明存在其他问题,如工艺流程不合理、设备调试不当等。
4.确定改善措施:根据分析结果,确定改善措施。
对于稼动率低的问题,可以通过提高设备运行效率、减少停机时间和故障时间来改善。
可以采取的具体措施包括:加强设备维护保养、提高操作员技能、增加备品备件库存、优化生产计划等。
5.实施改善措施:将确定的改善措施付诸实施。
在实施改善措施的过程中,需要制定详细的实施计划、明确责任人、制定改善目标并进行监控。
6.持续监控:改善措施实施后,需要持续进行监控,以确保稼动率的改善效果。
可以通过定期进行稼动率分析,对改善效果进行评估,及时调整和优化改善措施。
稼动率的改善是一个持续的过程,需要全体员工的共同努力。
通过稼动率分析与改善,企业可以提高设备的运行效率和生产能力利用率,提高生产效益,降低生产成本,提高竞争力。
技术之稼动分析
技术之稼动分析简介技术之稼动分析是一种用于评估和分析技术设备或系统的有效性和可靠性的方法。
稼动率是一个指标,用于表示设备或系统在一定时间内的实际运行时间与总计划运行时间的比例。
通过分析技术之稼动率,可以了解设备或系统在运行过程中的稳定性和可靠性,从而优化生产过程,提高效率和质量。
稼动率计算方法稼动率是指设备或系统在运行时间内的可用时间和总计划运行时间的比例。
稼动率的计算方法如下:稼动率 = (实际运行时间 / 总计划运行时间) * 100%实际运行时间是指设备或系统在实际使用中的运行时间,总计划运行时间是指设备或系统在一段时间内的总计划运行时间。
稼动率的意义和应用稼动率是衡量设备或系统可靠性和效率的重要指标,具有以下意义和应用:评估设备或系统可靠性:稼动率可以用来评估设备或系统的可靠性,通过计算稼动率,可以了解设备或系统的稳定性和可靠性,从而采取措施提高设备或系统的可靠性,减少停机时间,降低维修成本。
优化生产过程:通过分析稼动率,可以了解设备或系统在生产过程中的表现,从而找出生产过程中的瓶颈和问题,并采取相应的措施优化生产过程,提高生产效率和质量。
制定生产计划:稼动率可以帮助制定生产计划,根据设备或系统的稼动率,合理安排生产时间和资源,提高生产效率,减少生产成本。
评估设备投资价值:稼动率可以用来评估设备的投资价值,通过计算设备的稼动率,可以了解设备的使用频率和使用效果,从而判断设备是否值得投资。
提高技术之稼动率的方法为了提高技术之稼动率,可以采取以下方法:定期维护和检修:定期对设备或系统进行维护和检修,预防故障和停机时间,提高设备或系统的可靠性和稳定性。
优化生产过程:分析生产过程中的瓶颈和问题,采取相应的措施优化生产过程,提高生产效率和质量。
培训和提升员工技能:培训和提升员工的技能水平,使其能够熟练操作设备或系统,减少操作错误和故障,提高设备或系统的稼动率。
引入先进技术和设备:引入先进的技术和设备,提高设备或系统的性能和可靠性,降低故障率和停机时间,提高技术之稼动率。
- 1、下载文档前请自行甄别文档内容的完整性,平台不提供额外的编辑、内容补充、找答案等附加服务。
- 2、"仅部分预览"的文档,不可在线预览部分如存在完整性等问题,可反馈申请退款(可完整预览的文档不适用该条件!)。
- 3、如文档侵犯您的权益,请联系客服反馈,我们会尽快为您处理(人工客服工作时间:9:00-18:30)。
如何進行稼動分析(五)
三、稼動損失分析 1、稼動率之計算及損失計算類表示。 (1)觀測期間內之稼動率,如何計算。
•最小瓶頸工程作業時間(CT)*良品數
稼動率=
•勞動時間
* 100%
例:
觀測時間 良品數 CYCLE TIME
部品A 部品B 290分 190分 100個 80個 2.05分 1.50分
•BUT若慢慢地可以接 近0,不知道的改善對 策愈來愈少,而不需 要大投資的方法,會 愈來愈多。
生产力改善手法稼动分析繁体
稼動損失包含什麼(四)
四、稼動損失究竟有多大
Ex:有兩個生產形態、生產設備投資均相近的工廠,因生產設備使用效率不同, 其製造成本或公司的收益就不同。
1天的稼動損失 稼 動率
A社 105分 78%
什麼樣程度的停止,才要記錄呢?由於停止之頻度不同,記錄時間亦不同(花 費時間去記錄)。但假如決定了就應試作看看,然後再檢討之。一般來說,停 止時間超過10分鐘以上記錄的話就相當足夠了,畢竟花不了太多的時間嘛! 2、以連續觀測分析的方法
這個方法是對調查分析的物件、人或設備不間斷地觀測的方法。
從前面[稼動損失之一般的認識] [稼動損失之事例]中可很短,[非正常停止] 的停止時間很短,但是專案、頻率很高,總量在整個稼動損失中占最大的比率, 儘管[作業日報]沒有顯現出來,而且停止的量很小,在現場短暫的觀察,也不容 易發現,但為掌握[非正常停止]之事實,除到現場沈著地觀測外,別無他法。
•74.5%=
•稼動時間
•生產tact
•必要生產數量 •生產tact=0.69/0.745=0.92分/個
•STEP1 ••必勞要動生時產間數•量=•8時/•天15X40600個分/時X22天•=0.69分/
生产力改善手法稼动分析繁体
何謂稼動率(二)
三、稼動推移的相關表格 1、時間觀測用紙。 2、作業實績報告書[生產日報表] 3、日日稼動實績表。 4、實績稼動推移圖[生產管理表] 5、稼動狀況分析圖 6、改善對策一覽表
間接計算的停止 15.48分
生产力改善手法稼动分析繁体
稼動損失包含什麼(一)
一、稼動損失之分類: 分類之方式雖有許多,這裡僅就損失分析及排除(改善)等之考慮,分類之。
•發生的時間,可以 明確地預知的停止。
•換線作業 的停止
•稼動損失 •(停止)
•發生的時間,約略 可以預知的停止。
•發生的時間,不易 預見的停止。
•非正常的 停止
是均等的数量。 生产力要改牢善记手于心法。稼动分析繁体安全作为目标。
T P S(精益生產) 活 動
•TPS之二支柱
•基 本 原 則
•實現的道具 • 方策
•3.後工程引取和店面
•人的工作和機 •械的工作分離 •物/情報的-同期化 •人 ─ 多能工化 •設備─工程順序配置
•標準作業
•KANBAN方式
•段取短縮 • 小批量化
(6)MEMO欄內之異常內容應予以分類,合計停止時生产間力。改善手法稼动分析繁体
如何進行稼動分析(四)
方法二:作業時間短,製品完成時刻,不容易記錄時之情況 (1)一面詳細觀測每一個作業時間的人的動作,設備的作動狀況,若發生異常 狀況時,根據碼表記下時間,在MEMO欄內記入異常狀況。 (注)太過於細小的不容易測定的部分,並不一定要根據表,憑感覺亦可以。 (注)細小部分其頻度非常多時,也可以次數(正字)記錄之。 (注)異常發生時與碼表押下的時間不一致時,可憑感覺增加時間記入之。 (2)將MEMO欄內之內容分類之,並合計停止時間。 (3)記錄觀測期間之產量、良品、不良品等。
•稼動損失乃 是因設備故障
•YES那自然包含在內, 而每一次的量均很大且 非常明顯。
•BUT除此之外,不明 顯的項目,何止上百
•稼動損失之 排除非常困難
•雖知稼動損 失是不好的, 但除了接受它 之外,別無他 法
•YES要消除到0,是非 常困難的,且項目多, 很費時間(事)
•NO從現在起,改變想 法,努力排除,非建立 強的企業體制不可。
3、稼動率:在勞動時間內,將設備、人力運用在產品的產出上所表現出來的 指標。
公式:
稼動率(計畫)=LINE TACT /生產TACT
二、實績稼動率的計算:
公式:
稼動率(計畫)=NECK工程之作業時間*實際產出之良品/勞動時間
=稼動時間(分)/勞動時間
生产力改善手法稼动分析繁体
編成效率-3
•STEP2 •0.69分/個
作業慢 之遲延
E 非正常 清除切削屑、廢料(如塞滿、卡住無法自由落下等),因不順而需做檢查(品質),設備點檢,
的停止 因治具、模具、檢具、設備、輔助設備等不順而造成比標準作業慢之延遲,以及調整作業失誤 (如部品掉落、裝配失誤、設備操作失誤、治具、刀具、模具裝配失誤等),慢開工、早收工、 離開工作崗位、發生不良品時之對策研討、指示、等待指示、刀具破損、準備容器等
業的停 檢查品質、設備定時清掃、點檢、定時加油、更換廢料容器、研磨、交換電極等、其他。 止
B 間接的 朝會、小集團會議、健康檢查、掃除、有支薪的休息。
計畫停 止
C 作出不 表面上雖沒有停止,但到上下工程時,製品被判不良。
良品, 被視為 之停止
D 較標準 作業值(RATE)(標準作業時間 / 觀測時間 *100%)
(3)觀測前後,可根據計數器,記錄觀測期間之產量、良品、不良品等之數量。 (4)觀測後(觀測中若有餘裕時間),算出[一個作業所要的時間] (5)根據觀測的作業時間,算出所決定的最小瓶頸作業時間(最順的作業)與 所要時間的差。
(注)沒有做[作業時間觀測]的時候,可將瓶頸工程之最小時間當作所要時間之 最小值。
意
善
动
识
的
生
改
基
产
4 平 准 化
5 标 准 作 业
及 时 生 产
革
础
•·
•
…….. S
•
品
保
看
质
全
5
板
保
安
证
全
•目 视
管理
•步骤1:意识改 革 •JIT
•旧意 识
•抛弃
•抛弃陈旧的意识,改 用JIT的想法.
•步骤2: 5S •基础
•5S •JIT改善的基础是整
理、整顿、清扫、清 洁、教养等5S.
•步骤3:流动生 产
•(2.05*100)+(1.50*80)•*100
•290+19
%
0
•=
67.7%
•100% • 稼 動 67.7%
稼動損失
生产力改善手法稼动分析繁体
如何進行稼動分析(六)
(2)觀測期間內之停止時間,依內容分類,其各占比率如何計算。 例:
觀測時間
480.00分
非正常停止
67.75分
換線作業的停止 64.77分
生产力改善手法稼动分 析繁体
2020/11/24
生产力改善手法稼动分析繁体
目錄
一、何謂“稼動損失” 二、何謂“稼動率” 三、稼動損失包含什麼? 四、如何進行稼動分析? 五、稼動損失的排除
生产力改善手法稼动分析繁体
TPS架構
•少
人
化
•
•
•
多
作
工 程
变 换 准
•自働
2
操
备
化
• •
•
•
现
•
•
1
场
3
改
流
這個方法對於觀測者而言,需要非常之體力,但對以後之真正原因之追求及改 善來說,卻是非常有用及必須的
觀測時之注意點
(1)勿偏重於某一特定的時間帶,應以1日為單位觀測之。如:1日、2日。 (2)假使無法全日觀測時,亦不可偏重某一特定時間,應予錯開之。如:第一
生产力改善手法稼动分析繁体
如何進行稼動分析(三)
日(8:00~10:00)、第二日(10:00~12:00)、第三日(13:00~15:00) (3)盡可能不要把作業者的意識要因納入,盡可能在遠的地方長時間的觀測, 1小時以上。 (4)對於泛用生產線,觀測時遇到相同產品之機會教多,因此遇到出現較多的 產品時,對其觀測的時間,應增長。
觀測分析的方法
•只是程度上的差別而已, 相似的現象不管在哪 里都會產生,而且,只要稍有猶豫就會馬上發生。
生产力改善手法稼动分析繁体
何謂稼動損失
在以標準作業方式進行的作業中,由時間觀測的一個作業時間(CYCLE TIME),經長時間為何無法獲得:
1個作業時間 * 產出數=工作總時間 這是什麼原因呢? 因為其中發生了許多的“停止”,這些停止的浪費就是所謂的稼動損失
生產TACT(計畫)=LINE的勞動時間(480分)/必要生產數 =LINE的勞動時間/計畫生產數量*(1+預測不良率)
2、LINE TACT:一天中有效的生產時間中,生產一個良品的時間。 公式:
LINE TACT(計畫)=計畫稼動時間/生產必要數
=勞動時間-計畫的停止時間/計畫生產數量*(1+預測不良率)
•突 發 的 停止
若再細分,即為:
A:換線作業之停止(段取替作業停止) B:間接的計畫停止
•換線作業的停止
C:做出不良品,被視為之停止:較標準作業慢之遲延
•非正常的停
E:非正常的停止
止 生产力改善手法稼动分析繁体
稼動損失包含什麼(二)
二、稼動損失之內容(例):
A 換線作 模具、治具、刀具之交換,供給材料、整理製品(如更換棧板、台車等)、定時(取下製品)
F
突發的 停止
設備、輔助設備、治具、模具故障、模具、刀具、治具破損、材料中斷、討論、缺水、缺油、 聽電、天災、不良品發生之處理。源自生产力改善手法稼动分析繁体