无菌药品生产管理与质量控制
药品生产质量管理规范 药品生产质量管理规范附录:总则,无菌药品
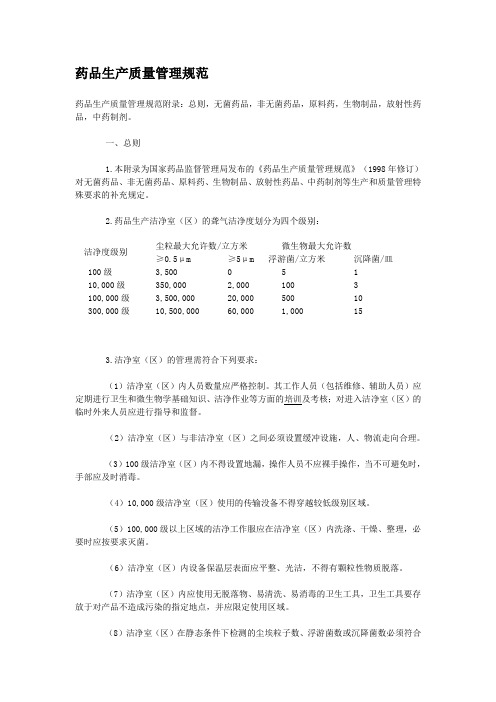
药品生产质量管理规范药品生产质量管理规范附录:总则,无菌药品,非无菌药品,原料药,生物制品,放射性药品,中药制剂。
一、总则1.本附录为国家药品监督管理局发布的《药品生产质量管理规范》(1998年修订)对无菌药品、非无菌药品、原料药、生物制品、放射性药品、中药制剂等生产和质量管理特殊要求的补充规定。
2.药品生产洁净室(区)的聋气洁净度划分为四个级别:洁净度级别尘粒最大允许数/立方米微生物最大允许数≥0.5μm ≥5μm 浮游菌/立方米沉降菌/皿100级 3,500 0 5 110,000级 350,000 2,000 100 3100,000级 3,500,000 20,000 500 10300,000级 10,500,000 60,000 1,000 153.洁净室(区)的管理需符合下列要求:(1)洁净室(区)内人员数量应严格控制。
其工作人员(包括维修、辅助人员)应定期进行卫生和微生物学基础知识、洁净作业等方面的培训及考核;对进入洁净室(区)的临时外来人员应进行指导和监督。
(2)洁净室(区)与非洁净室(区)之间必须设置缓冲设施,人、物流走向合理。
(3)100级洁净室(区)内不得设置地漏,操作人员不应裸手操作,当不可避免时,手部应及时消毒。
(4)10,000级洁净室(区)使用的传输没备不得穿越较低级别区域。
(5)100,000级以上区域的洁净工作服应在洁净室(区)内洗涤、干燥、整理,必要时应按要求灭菌。
(6)洁净室(区)内设备保温层表面应平整、光洁,不得有颗粒性物质脱落。
(7)洁净室(区)内应使用无脱落物、易清洗、易消毒的卫生工具,卫生工具要存放于对产品不造成污染的指定地点,并应限定使用区域。
(8)洁净室(区)在静态条件下检测的尘埃粒子数、浮游菌数或沉降菌数必须符合规定,应定期监控动态条件下的洁净状况。
(9)洁净室(区)的净化空气如可循环使用,应采取有效措施避免污染和交叉污染。
(10)空气净化系统应按规定清洁、维修、保养并作记录。
无菌药品质量管理
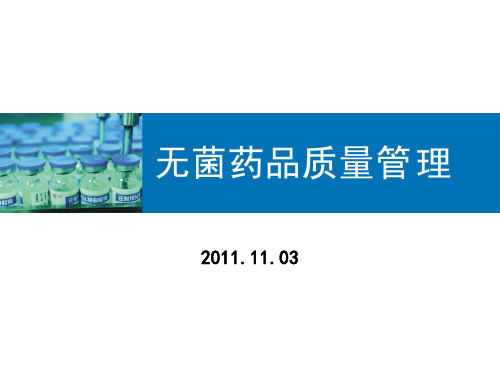
无菌生产影响因素控制
环境洁净度:
✓ 一定的换气次数和风速 ✓ 动态的粒子数和微生物数(在线监测装置的应用,检测时
间、采样量、频率、采样位置等) ✓ 高效的检漏(DOP或PAO) ✓ 环境的消毒(消毒效果确认、周期、消毒方式等),注意对
产品和设备内表面的保护,消毒残留的检测 ✓ 压差的控制(绝对压差的控制、压差流向的控制、压差报警) ✓ 恢复性试验(发烟材料) ✓ 流型测试(干冰、发烟笔,录像)
2011.11.03
2010版药品GMP定义
➢无菌药品是指法定药品标准中列有无菌检查 项目的制剂和原料药,包括无菌制剂和无菌原 料药。 ➢无菌药品按生产工艺可分为两类:采用最终 灭菌工艺的为最终灭菌产品;部分或全部工序 采用无菌生产工艺的为非最终灭菌产品。
无菌药品特性
无菌药品:一般指没有活体微生物存在的药品
无菌工艺模拟应考虑的关键
✓ 模拟不应提高或干扰生产工艺;不应人为提高或降低污 染的风险,除非设计中有此内容
(例配料反应时间等)
无菌生产影响因素控制
人员(包括维修人员):
➢ 培训(微生物、无菌操作、特殊防护 知识、卫生等)
➢ 体检(传染病、灯检人员视力等) ➢ 进入洁净区人员数量的控制(经验证) ➢ 进入洁净区人员资质的确认(关键人
员必须参加模拟灌装) ➢ 规范的无菌操作 ➢ 严格的更衣程序 ➢ 人员着装微生物检测(包括手套) ➢ 外来人员控制(官方或客户审计人员、
物和内毒素残留)
无菌药品质量检验
关注点:
取样程序SOP,取样方式、取样量、取样位置(前、中、后等) 生产异常偏差样品的标注和检验(样品单独检验,避免污染样品潜在
的稀释微生物、内毒素的检测结果) 取样包装(与市售包装一致或类似) 抽取样品在实验室贮存的条件(按照产品贮存条件或更好的贮存条件) 严格按照注册的质量标准检测,除非经过合理方法验证确认 实验室原始数据审计追踪系统的应用 无菌检验的数量(按照药典要求,必要时加严控制) 无菌方法验证(包括培养基灵敏度及无菌性检查),特别注意环境监 测菌的使用
无菌药品生产与质量控制
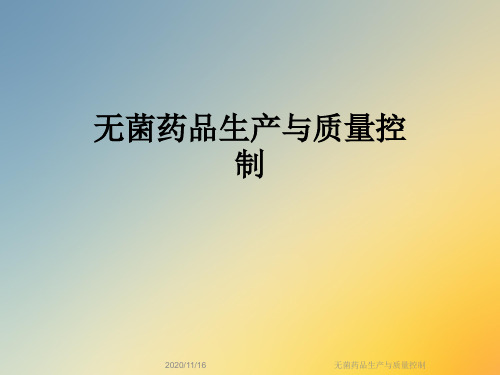
(3)、灭菌方法的选择: 1)灭菌条件121℃,15min湿热灭菌。 2)灭菌F0值≥8min,SAL ≤10-6的湿热灭菌。 3)采用微生物截留过滤器的除菌过滤工艺。 4)采用无菌原料和预先灭菌的包装材料进行无菌配制和 灌装工艺。
无菌药品生产与质量控制
灭菌工艺决策树
无菌药品生产与质量控制
所以,无菌保证水平必须有足够的F0值,控制产品灭菌前的 微生物。 例:假定灭菌开始时产品中的污染微生物总数(N0)为 100cfu/瓶,耐热参数(D)为1min,要达到无菌保证水 平不小于6的标准,灭菌 F0=SAL+lgNO*D=(6+lg100)*1=8min.
同 样 的 产 品 , 在 110℃ 下 灭 菌 , 则 灭 菌 时 间 为 : t=F0/L110=8/0.08=100min。
N 产品内微生物的残留数 N0 灭菌开始时产品内的微生物数 t 累计灭菌时间 k 常数,与微生物的耐热性、灭菌温度有关
无菌药品生产与质量控制
4、微生物的耐热参数 微生物的耐热参数,简称D值,是指在特定灭菌 条件下,使微生物数量下降一个对数单位或杀灭 90%所用的时间(分钟)。
5、灭菌率:表示不同灭菌温度所对应的灭菌效果 的重要函数。 灭菌温度为T℃时的灭菌效果,与121℃下同样灭 菌时间的灭菌效果用下面公式表示 灭菌率L=10(T-121)/Z;
t 灭菌时间
例:110℃灭菌30minF0值计算:110℃的灭菌率为0.08, F0=0.08*30=2.4min,即110℃灭菌30min相当于121℃灭 菌2.4min。
F0值是衡量、区分无菌保证工艺属于最终灭菌工艺还是非 最终灭菌工艺。
无菌药品生产与质量控制
7、无菌保证水平:公式SAL=F0/D-lgN0 药典规定,最终灭菌工艺生产的药品SAL<=10-6,残存 微生物的概率越低,无菌保证的风险越低。
药品生产企业的无菌管理要求

药品生产企业的无菌管理要求
药品生产企业的无菌管理要求非常严格,主要是为了保证药品的质量和安全性。
以下是一些基本的要求:
1. 环境要求:药品生产的环境需要无菌,包括空气、水源、物料等。
这需要通过各种措施来控制,如空气净化系统、纯水处理系统等。
2. 设备要求:用于药品生产的设备也需要无菌,特别是直接接触药品的设备,如生产设备、运输工具等。
这些设备在使用前需要通过高温、高压、过滤等方式进行消毒。
3. 人员要求:药品生产的人员也需要无菌,包括服装、手套、鞋子等。
这些物品在使用前需要通过高温、高压、过滤等方式进行消毒。
4. 物料要求:用于药品生产的物料也需要无菌,特别是直接接触药品的物料,如原料、包装材料等。
这些物料在进入生产区前需要通过过滤、消毒等方式进行处理。
5. 操作要求:药品生产的过程也需要无菌,包括操作的方法、顺序、时间等。
这些操作需要通过标准操作程序(SOP)来进行。
以上就是药品生产企业的无菌管理要求。
这些要求需要通过严格的质量管理体系来进行管理和监控,如ISO 13485、GMP等。
药品生产质量管理规范附录无菌药品
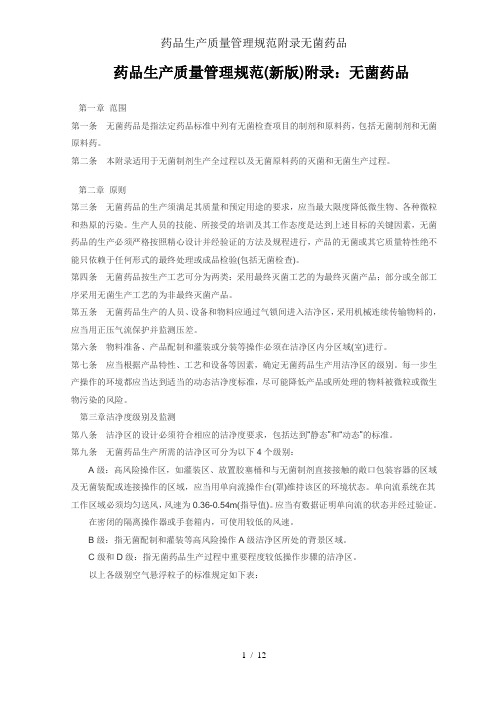
药品生产质量管理规范(新版)附录:无菌药品第一章范围第一条无菌药品是指法定药品标准中列有无菌检查项目的制剂和原料药,包括无菌制剂和无菌原料药。
第二条本附录适用于无菌制剂生产全过程以及无菌原料药的灭菌和无菌生产过程。
第二章原则第三条无菌药品的生产须满足其质量和预定用途的要求,应当最大限度降低微生物、各种微粒和热原的污染。
生产人员的技能、所接受的培训及其工作态度是达到上述目标的关键因素,无菌药品的生产必须严格按照精心设计并经验证的方法及规程进行,产品的无菌或其它质量特性绝不能只依赖于任何形式的最终处理或成品检验(包括无菌检查)。
第四条无菌药品按生产工艺可分为两类:采用最终灭菌工艺的为最终灭菌产品;部分或全部工序采用无菌生产工艺的为非最终灭菌产品。
第五条无菌药品生产的人员、设备和物料应通过气锁间进入洁净区,采用机械连续传输物料的,应当用正压气流保护并监测压差。
第六条物料准备、产品配制和灌装或分装等操作必须在洁净区内分区域(室)进行。
第七条应当根据产品特性、工艺和设备等因素,确定无菌药品生产用洁净区的级别。
每一步生产操作的环境都应当达到适当的动态洁净度标准,尽可能降低产品或所处理的物料被微粒或微生物污染的风险。
第三章洁净度级别及监测第八条洁净区的设计必须符合相应的洁净度要求,包括达到“静态”和“动态”的标准。
第九条无菌药品生产所需的洁净区可分为以下4个级别:A级:高风险操作区,如灌装区、放置胶塞桶和与无菌制剂直接接触的敞口包装容器的区域及无菌装配或连接操作的区域,应当用单向流操作台(罩)维持该区的环境状态。
单向流系统在其工作区域必须均匀送风,风速为0.36-0.54m(指导值)。
应当有数据证明单向流的状态并经过验证。
在密闭的隔离操作器或手套箱内,可使用较低的风速。
B级:指无菌配制和灌装等高风险操作A级洁净区所处的背景区域。
C级和D级:指无菌药品生产过程中重要程度较低操作步骤的洁净区。
以上各级别空气悬浮粒子的标准规定如下表:新版附录无菌药品注:(1)为确认A级洁净区的级别,每个采样点的采样量不得少于1立方米。
gmp无菌制剂的控制策略

gmp无菌制剂的控制策略在无菌药品的生产中,确保产品质量和安全性的关键在于对整个生产过程进行全面的控制。
以下是gmp无菌制剂的控制策略:1. 原辅料和包装材料的管理:原辅料和包装材料的质量直接影响产品的质量和安全性。
应对供应商进行严格的评估和审计,确保其符合质量要求。
同时,对物料的验收、存储、发放等环节进行严格控制,确保物料的质量和稳定性。
2. 工艺过程控制:无菌药品的生产过程中,应确保工艺参数的稳定性和一致性。
通过监控关键工艺参数,如温度、压力、时间等,确保工艺的一致性和可重复性。
同时,对生产过程中可能引入的微生物和微粒进行严格控制,确保产品的无菌性和安全性。
3. 环境监控:无菌药品的生产环境要求极高,应对生产环境进行严格监控。
通过定期对空气、表面和人员等进行微生物检测,以及时发现并控制污染源,确保生产环境的洁净度和无菌性。
4. 人员管理:人员是生产过程中的重要因素,也是最容易引入污染的环节之一。
应对人员进入无菌区的程序进行严格控制,确保人员符合规定要求。
同时,对人员进行严格的培训和资质管理,提高人员的操作技能和无菌意识,确保人员的行为符合无菌药品的生产要求。
5. 设备维护和清洗:设备是生产过程中的重要工具,其清洁度和维护状况直接影响产品的质量和安全性。
应定期对设备进行清洗和检查,确保其符合生产和质量要求。
同时,建立设备维修和保养制度,对设备进行全面的维护和管理,确保设备的正常运行和使用寿命。
6. 质量保证体系:建立完善的质量保证体系是确保无菌药品质量和安全性的关键。
应定期对生产过程进行审计和评估,及时发现并处理潜在的问题和风险。
同时,对生产过程和产品进行严格的检验和控制,确保产品符合质量标准要求。
生产管理-无菌药品
通过净化空调系统等手段,控制生产区域内的温湿度、压差等环 境参数,保证生产环境的稳定。
生产过程控制
工艺验证
对无菌药品的生产工艺进行验证,确保工艺的可靠性 和稳定性。
过程监控
通过自动化控制系统等手段,对生产过程中的各项参 数进行实时监控和记录。
批次管理
实施严格的批次管理,确保每个批次产品的可追溯性 和质量控制。
03
无菌药品生产的质量控制
质量控制标准与要求
01
药品生产质量管理规范(GMP)
确保无菌药品的生产过程符合法规要求,保证产品质量。
02
质量标准
制定无菌药品的质量标准,包括微生物限度、无菌保证水平等指标。
03
生产过程控制
对无菌药品的生产过程进行严格控制,确保生产环境、设备、物料等符
合要求。
质量检验与检测
05
无菌药品生产的未来发展
新技术与新工艺的应用
生物技术
利用基因工程、细胞工程等技术,开发新型无菌药品,提高药品 疗效和安全性。
纳米技术
将纳米技术应用于无菌药品的生产,提高药物的生物利用度和稳定 性。
连续制造技术
采用连续制造技术,提高生产效率,降低生产成本,确保产品质量。
智能化生产与管理
自动化生产线
的生产要求。
物料存储
02
建立严格的物料存储管理制度,确保物料在存储过程中不受污
染。
物料追溯
03
实施物料的追溯管理,确保物料来源清晰、质量可控。
卫生与环境管理
卫生制度
制定严格的卫生制度,规范生产区域的清洁卫生和消毒工作。
环境监测
定期对生产环境进行微生物和尘埃粒子等指标的监测,确保环境 符合无菌药品的生产要求。
无菌药品生产质量管理
无菌药品生产质量管理无菌系指经灭菌后产品中没有活的微生物存在的状态。
无菌药品系指不含任何活的微生物的药品。
要求药品是否必须是无菌,取决于药物应用的途径和微生物污染对人体的危害程度。
无菌药品往往在使用时直接注入血液循环、体内或直接用于创面、粘膜等,一旦药物受到微生物污染则会引起严重感染,直接危害病人的身体健康甚至危及生命。
无菌药品是药物制剂中的一大类,主要包括以下几个方面。
注射用药品如注射液、注射用无菌粉末和注射用浓溶液等。
眼用药品如滴眼剂、眼用膜剂、软膏剂和凝胶剂等。
植入性药品如植入片等。
创面用药品如溃疡、烧伤及外伤用溶液、软膏剂和气雾剂等。
手术用药品如止血海绵剂和骨蜡等。
注射剂按照其生产工艺可分为最终灭菌药品(小针剂、大输液)和非最终灭菌药品(无菌粉针剂、冻干制品)两大类。
非最终灭菌生产工艺又称作“无菌生产工艺”。
以下介绍的是注射用药品中的注射用无菌粉末管理体系是建立方针和目标并实现这些目标的体系。
一个组织的管理体系可包括若干个不同的管理体系,如质量管理体系、财务管理体系或环境管理体系等。
质量管理体系是在质量方面指挥和控制组织的管理体系,也是为保证产品、过程或服务质量满足规定的或潜在的要求,由组织机构、职责、程序、活动、能力和资源等要素构成的有机整体。
也就是说,为保证产品、过程或服务满足质量要求,把企业的组织机构、职责和权限、工作方法和程序、技术力量和业务活动、资金和资源、信息等协调统一起来,所形成的一个有机整体,称为企业的质量管理体系。
制药企业质量管理体系的核心是实施GMP。
在欧盟GMP(2005年版)质量管理一章中指出:药品生产企业必须确保所生产的产品适用于预定的用途,符合药品注册批准的要求,并且不让患者承担安全、质量和疗效的风险。
达到这一质量目标是高级管理层的责任,但是企业内部各部门不同层次的人员以及供应商、经销商应共同参与并承担各自的义务。
为切实实现这一目标,药品生产企业必须建立涵盖GMP以及质量控制(QC)在内的全面的质量保证(QA)系统。
无菌药品生产管理
消毒灭菌设备: 消毒柜、灭菌 器、消毒剂等
消毒灭菌效果 评价:微生物 检测、消毒剂 残留检测等
生产设备与设施
洁净室:无菌药品生产的核 心设施,需要达到一定的洁
净度要求
生产设备:包括灌装、包装、 灭菌等设备,需要满足无菌药
品生产的特殊要求
空气净化系统:用于控制洁 净室内的空气质量,包括过
滤、消毒等环节
风险
生产管理的主要内容
01
生产计划:制定生产计划,包 括生产时间、生产数量、生产 质量等
03
生产设备管理:对生产设备进 行维护和管理,确保生产设备 正常运行
05
生产环境管理:对生产环境进 行控制和管理,确保生产环境 符合要求
02
生产过程控制:对生产过程进 行监控,确保生产质量符合要 求
04
生产人员管理:对生产人员进 行培训和管理,确保生产人员 具备相应的生产技能和素质
检测设备:用于检测无菌药 品的质量和稳定性,包括微 生物检测、理化检测等设备
无菌药品生产管 理法规与标准
4
法规要求
1
药品生产必须符合GMP (Good Manufacturing
Practice)标准
2
药品生产必须符合国家药品 监 督 管 理 局 ( N M PA ) 的 相
关法规
3
药品生产必须符合国际药品 生产规范(ICH)
法规依据: 《药品生产质 量管理规范》 (GMP)
标准依据: 《无菌药品生 产管理规范》 (GMP)
合规要求:生 产过程符合法 规和标准要求, 确保药品质量 和安全
合规检查:定 期进行合规检 查,确保生产 过程符合法规 和标准要求
谢谢
06
生产质量管理:对生产质量进 行控制和管理,确保生产质量 符合要求
无菌药品管理制度
无菌药品管理制度一、背景与意义无菌药品是指在生产和包装过程中严格遵循无菌操作规范,确保药品不受微生物污染的药品。
无菌药品具有很高的安全性和有效性,是临床治疗中不可或缺的重要药品之一。
但是,由于无菌药品本身的特殊性和易受外界污染的影响,要求药品生产、储存、运输过程中严格遵循无菌操作规范,以确保药品的质量和安全。
因此,建立科学、规范的无菌药品管理制度,可以有力地保障无菌药品的质量和安全性,促进医疗卫生事业的发展,也有利于提高药品企业的竞争力和市场占有率。
二、制度内容1.无菌药品生产管理制度(1)生产车间布局:生产车间应设置在干燥通风、无尘、无害的环境中,避免与高温、高湿、易受污染的环境相邻;(2)无菌药品生产设备:生产设备应具备GMP要求,定期维护、保养、清洁,确保设备处于正常使用状态;(3)人员管理:生产操作人员应具备相应的技术能力和专业知识,严格遵循无菌操作规程,保持良好的个人卫生习惯;(4)原辅材料管理:对进厂原辅材料应严格把关,避免潜在的污染源对产品质量的影响;(5)生产操作:严格遵循无菌操作规程,防止外界微生物对产品的污染;(6)清洁消毒:对生产设备、环境、人员进行定期的清洁和消毒,确保生产现场处于无菌状态。
2.无菌药品储存管理制度(1)储存环境:储存无菌药品的仓库应设置在干燥、通风、无尘、无害的环境中,避免与高温、高湿、易受污染的环境相邻;(2)温湿度管理:储存无菌药品的温湿度应符合药品的要求,避免药品因不合适的温湿度而失效或产生新的污染;(3)药品分类管理:根据储存条件和有效期对无菌药品进行分类管理,避免混杂使用导致药品质量下降;(4)货位管理:对每批次的无菌药品进行标识、记录,建立良好的货位管理制度,确保药品的检索、追溯和售后服务。
3.无菌药品运输管理制度(1)车辆卫生:货运车辆应保持清洁、整洁,避免与有害物质接触;(2)温湿度管理:运输时应采取合适的包装和温湿度控制措施,避免药品在运输过程中受到污染和损坏;(3)记录追踪:对每批次的无菌药品进行详细的记录和追踪,确保药品运输过程中的质量和安全。
- 1、下载文档前请自行甄别文档内容的完整性,平台不提供额外的编辑、内容补充、找答案等附加服务。
- 2、"仅部分预览"的文档,不可在线预览部分如存在完整性等问题,可反馈申请退款(可完整预览的文档不适用该条件!)。
- 3、如文档侵犯您的权益,请联系客服反馈,我们会尽快为您处理(人工客服工作时间:9:00-18:30)。
资料仅供参考,不当之处,请联系改正。
5、空气中的微生物污染:
(1)、空气中的微生物为革兰氏阳性菌,他们有可能形 成芽孢使其耐热性增大;严重的是,一旦被尘埃包裹,耐 热性比单独存在状态上升一个数量级。
(2)、为防止空气中耐热菌污染生产系统,需要将已清 洁/已灭菌的容器具等置于局部单向流之下。 无 菌 药 品 进 化空调系统的设置及洁净区环境的建立和维持,是的有效 控制微粒的同时,也在很大程度上自然的消除了尘埃粒子 包藏芽孢,造成难以灭菌的风险。
4、芽孢:当目些细菌遇到不良生存环境时,为保护自身 ,在细胞内形成一个壁厚而坚硬的休眠体,该休眠体及称 芽孢或者孢子。
由于其对不良环境的耐受性远高于生长态细胞,常被用于 挑战性灭菌工艺,以确认被灭菌物品无菌的可靠性。
芽孢的特点:
80℃以下长期存活;
100℃以下有相当高的存活率;
100℃以上死亡过程符合一级动力学方程
品的工艺。
资料仅供参考,不当之处,请联系改正。
(2)、最终灭菌工艺:将完成最终密封的产品进行灭菌 ,以杀灭产品种微生物的的工艺。由此生产的无菌制剂称 为最终灭菌。无菌药品。(SAL<10-6)
3、灭菌的基本原理:使细胞内的蛋白质或核酸发生不可 逆的凝固或破坏,使微生物死亡。符合一级动力学方程, 即:
资料仅供参考,不当之处,请联系改正。
6、工艺用水微生物的污染
(1)、水是注射剂的主要原料,水还是用于清洁与产品 相接触的容器、密封材料、药液过滤器和其他配液设备等 的清洁剂,因此,必须有效的控制水系统的微生物污染水 平,并同时控制细菌内毒素的水平。
(2)水源性的微生物多数为革兰氏阴性菌,不会形成芽 孢,不耐热。外壁的主要成分为脂多糖(细菌内毒素的主 要成分),其代谢产物及细胞的尸体均属细菌内毒素的污 染源,即使通过灭菌的方式将革兰氏阴性菌杀灭,但不能 消除细菌内毒素对无菌药品质量的影响。
F0值是衡量、区分无菌保证工艺属于最终灭菌工艺还是非 最终灭菌工艺。
资料仅供参考,不当之处,请联系改正。
7、无菌保证水平:公式SAL=F0/D-lgN0
药典规定,最终灭菌工艺生产的药品SAL<=10-6,残存 微生物的概率越低,无菌保证的风险越低。
所以,无菌保证水平必须有足够的F0值,控制产品灭菌前的 微生物。
通过清洗、灭菌降低微生物负荷,减少内毒素生成。
通过干热去除或者其他手段对已存在的内毒素进行破坏和 去除。
资料仅供参考,不当之处,请联系改正。
(4)、内毒素的去除方法: 加热法。 酸碱法(玻璃容器)。 蒸馏法(注射用水)。 活性炭吸附。 超滤(中药注射剂)。 离子交换法(缓冲液)。
资料仅供参考,不当之处,请联系改正。
lgN=lgN0-kt
N 产品内微生物的残留数
N0 灭菌开始时产品内的微生物数
t 累计灭菌时间
k 常数,与微生物的耐热性、灭菌温度有关
资料仅供参考,不当之处,请联系改正。
4、微生物的耐热参数
微生物的耐热参数,简称D值,是指在特定灭菌 条件下,使微生物数量下降一个对数单位或杀灭 90%所用的时间(分钟)。
(2)、污染热原的途径:
溶剂(注射用水)。
从原辅料中带入(胰岛素,葡萄糖等)。
资料仅供参考,不当之处,请联系改正。
从容器、用具、管道和装置带入。
制备过程中的污染(操作时间长,装备不密封,人员操作 不当)。
(3)内毒素控制的方法:
来源控制,控制物料、器具存放过程中的条件,减少微生 物滋生。
例:假定灭菌开始时产品中的污染微生物总数(N0)为 100cfu/瓶,耐热参数(D)为1min,要达到无菌保证水 平不小于6的标准,灭菌 F0=SAL+lgNO*D=(6+lg100)*1=8min.
资料仅供参考,不当之处,请联系改正。
目录
无菌保证与无菌生产 湿热灭菌工艺的管理 除菌过滤工艺 制药用水的管理 GMP检查中存在的问题
资料仅供参考,不当之处,请联系改正。
无菌保证与无菌生产
一、自然界常见的微生物
资料仅供参考,不当之处,请联系改正。
二、微生物分布特点
1、微生物无处不在。
5、灭菌率:表示不同灭菌温度所对应的灭菌效果 的重要函数。
灭菌温度为T℃时的灭菌效果,与121℃下同样灭 菌时间的灭菌效果用下面公式表示
灭菌率L=10(T-121)/Z;
资料仅供参考,不当之处,请联系改正。
右图给出湿热灭菌,以 121℃为标准灭菌时间, Z=10℃时灭菌率。 所以,121℃灭菌1min对 微生物的杀灭效果,相当 于110℃灭菌12.5min的 杀灭效果,100℃则需要 125min。
资料仅供参考,不当之处,请联系改正。
6、标准灭菌时间:标准灭菌时间,即F0值是指在121℃下的 灭菌时间,他的意义在于将不同灭菌温度下的灭菌工艺, 按照灭菌效果等效的原则,换算为121℃下灭菌所需要的 时间。即: F0 =L*t
F0 标准灭菌时间
L 特定灭菌温度下的灭菌率
t 灭菌时间
例:110℃灭菌30minF0值计算:110℃的灭菌率为0.08, F0=0.08*30=2.4min,即110℃灭菌30min相当于121℃灭 菌2.4min。
2、气源性微生物革兰氏阳性菌较多:它们可形成芽孢, 难以杀灭。因此,需要洁净的环境。可以通过氧化(消毒 )方法除去。
3、水源性的则革兰氏阴性菌多,不会形成孢子,但会形 成细菌内毒素,耐热性差。通过加热,让其凝固,从而除 掉。
资料仅供参考,不当之处,请联系改正。
(1)、细菌内毒素和热原的概念:热原的污染是注射用 原料及制剂生产普遍存在的问题,污染可能来源于原料、 水、试剂、车间环境、设备等。含有热原的药品进入人体 后,会使人体发冷、寒战、体温升高、出汗、恶心呕吐等 不良反应。严重着出现昏迷、虚脱甚至生命危险。引起热 原反应的主要是革兰氏阴性菌细胞壁中降解的脂多糖,也 称细菌内毒素。
资料仅供参考,不当之处,请联系改正。
三、无菌保证工艺
1、无菌的标准及概念:每批证值为6).
2、无菌保证工艺:使产品达到规定的无菌保证水平的工 艺过程。分为两类:最终灭菌工艺和非最终灭菌工艺。
(1)、非最终灭菌工艺:指在无菌环境下通过无菌操作 生产无菌产品的方法。具体就是将组成药品的原料和包装 材料分别灭菌或经除菌处理,在无菌条件下降其组装成成