1-1、我国近年水煤浆气化制合成氨、甲醇情况汇总
浅谈合成氨生产过程的危险性

浅谈合成氨生产过程的危险性摘要:近年来,煤气化技术得到了飞速发展,包括干粉煤、水煤浆以及碎煤加压气化技术均取得了很大的进展。
水煤浆气化法合成氨工艺也日益成熟,该工艺包括煤浆制备、气化、氨合成等多个工序,涉及了氢气、一氧化碳、氨等易燃易爆有毒有害的物质,并且部分工序的操作条件要求比较苛刻,识别水煤浆气化法各工序的危险性是保证合成氨安全生产的前提,生产企业应予以重视。
关键词:合成氨;生产过程;危险性引言在供给侧改革的基础上,综合实力和经济实力都有了长足的进步,推动了我国化工产品的发展。
当前,对化学制品的需求是市场经济发展的必然要求。
因此,在工业中发展合成氨生产技术显得尤为重要。
然而,目前我国合成氨生产过程中存在着许多问题,其中包括能耗问题最主要的就是安全问题。
如何改进现代化的合成氨生产技术,一直是人们普遍关心的问题。
在工业中,合成氨技术的进一步发展,要求进一步完善其技术指标,完善生产设备,完善生产工艺,强化安全管理,以实现合成氨生产工艺的安稳长满优运行。
我国合成氨的主要原材料来自原油,但由于我国原油资源日益枯竭,需要对上游的合成氨进行替代,以降低能耗,进而实现对社会生态的优化。
1我国合成氨工艺技术的现状水煤浆制气工艺采用先进的水煤浆气化、耐硫变换、低温甲醇洗、制酸。
多喷嘴对置式水煤浆气化分为煤浆制备、气化、渣水处理三个工序,煤浆制备送来的煤浆与高压氧气经烧嘴喷入气化炉,在1350℃下反应,产生的粗煤气经水洗塔洗涤后送净化系统。
气化来的粗煤气依次经宽温耐硫变换、低温甲醇洗、液氮洗精制的1:3氮氢气送往合成氨装置,经催化剂的催化作用,化学反应生成氨,经冷凝分离后得到产品液氨供尿素使用,甲醇洗产生纯度为98.5%的二氧化碳气供尿素使用。
硫回收采用上海科洋工艺包处理酸性气副产97.5%浓硫酸。
合成氨工业是我国化学工业的基础之一,也是生产尿素的原料,在如今耕地面积日益减少、恶劣天气日益增多的情况下,保证合成氨装置安全稳定运行,有序提供尿素生产所需原料,是保证粮食安全的一项重要举措。
加压水煤浆气化生产氨醇工艺中的酸性气处理

( )流程简单 ,且又 因压 力为 常压 ,所 以 1 整套设备投资较其他硫 回收装置低 。 ( )操作简单 ,较湿式 氧化泡沫硫磺 回收 2 工艺不但现场生产清洁,而且劳动强度小。 ( )设 计合 理 ,加之 良好 的催化 剂活性 , 3
制硫 反 应 较 好 ,正 常情 况 下 尾 气 ( H S+S 0)
第 1期
21 0 2年 1月
中 氮
肥
No .1
M— ie to e o s F riie o r s S z d Ni g n u e tl rPrg e s r z
Jn 2 1 a. 02
加 压 水煤 浆气 化 生产 氨 醇 工 艺 中的酸 性气 处 理
赵 华 。令狐 瓦奇
[ 山西 阳煤丰喜 ( 集团 )I 临猗分 公司 ,山西 临猗 0 4 O ] 4 10
[ 中图分类号 ]X 7 1 [ 8 文献标识码 ]B [ 文章编号 ]10 9 3 (0 2 0 — 0 6- 1 0 4— 92 2 1 ) 1 0 1 0
基 于 甲醇市 场长期 疲软且 价格波动 较大 , 20 09年我公 司提 出 对 40k a甲醇 装 置进 行 改 0 t / 造 ,新增 1 套合成氨及尿素生产系统。改造工程 于 21 0 0年 7月 完工 并 一 次 开 车 成 功 。新 系 统 对
生产 中活 性 温 度控 制 得 较 低 (4 C左 右 ) 15o ,催 化剂 床 层热 点 温 度在 20—20℃ ,这 样 既可 以 3 5 延 长催 化 剂 的使 用 寿命 ,又 可 以控 制 较 少 量 的
S2 O 生成 。
从低温 甲醇洗热再生出来 300n / 0 l h的酸 性气 ( : H s质量浓度 7 m )在配人 6001 / 5 0 1 h 1 的脱碳 汽提 气后 ,气 体 中 H s质 量浓 度 降 至
煤制甲醇
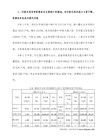
2、生产状况:
(1)国外生产状况:
从上世纪的20年代开发成功合成气生产甲醇以来,甲醇工业得到了飞速发展。近20年来,世界甲醇生产能力的地区分布及生产状况已发生了巨大变化,甲醇工业与天然气的开发是同步发展的,新建装置大多建在天然气资源丰富的地区。这些地区的需求有限,因此大量的甲醇出口到美国、西欧和日本,而美国、西欧和日本的装置则由于经济方面的原因,已逐步减产或关闭,转而进口甲醇,
煤气化制甲醇工艺技术介绍
第一篇:甲醇的主要用途及国内外生产状况:
1、甲醇的主要用途:
甲醇是一种重要的基本有机化工产品,在化工、医药、轻纺、国防等许多工业部门有着广泛用途。在化工生产中,甲醇主要用于制造甲醛、醋酸、氯甲烷、甲胺、甲基叔丁基醚(MTBE)、碳酸二甲酯、对苯二甲酸二甲酯(DMT)、丙烯酸甲酯、二甲基甲酰胺、甲基丙烯酸甲酯(MMA)等一系列有机产品。另外,近年开发成功的MTO工艺和MTP工艺,开辟了由甲醇生产烯烃的工艺路线,由甲醇替代石油生产石油化工产品的时代已经来临,其对甲醇的需求量将是非常巨大的。
SCOT法是一种还原吸收法硫磺回收尾气处理技术,它将Claus装置尾气中的SO2、有机硫、单质硫等所有硫化物经加氢还原转化为H2S,再采用溶剂吸收方法将H2S提浓后循环送回到Claus装置进行处理。
鲁奇(Lurgi)的Sulfreen工艺是最早工业化的一种低温Claus工艺,该工艺与传统的克劳斯工艺接近,对原料气中H2S浓度有要求(>25%)。如果原料气硫含量偏低,整个装置将低负荷运转。当负荷低于25%时,Sulfreen装置便不能正常运行,因而总硫回收率受到影响。
三、合成:
甲醇的合成按压力分为高压、中压和低压。高压法是在30 MPa以上,320℃一380℃的操作条件下通过催化剂来合成甲醇,其特点是技术成熟,但投资和生产成本较高,产品质臣差,设备制造难度大,已逐渐淘汰。中低压法的合成压力分别为10MPa和5MPa左右,操作温度为200℃一300℃,使用Cu — Zn — Al系作催化剂,中低压法比高压法优越,主要表现在能耗低,粗甲醇产品质量商,设备易制造,投资相对较低。
煤气化(甲醇)产业链

煤气化(甲醇)产业链一、煤气化(甲醇)产业发展现状煤气化生产合成气是煤化工的核心,煤气化技术始于20 世纪30 年代,煤气化的现有方法达70~80 种,目前还在不断研发新的煤气化技术。
按时代划分,煤气化技术包括第一代和第二代,由于第一代气化炉技术缺陷,70年代第二代煤气化技术逐渐取代了第一代煤气化技术。
第二代煤气化技术是六十年代末至70 年代初开发的,其代表炉型为德士古水煤浆气化炉、壳牌粉煤气化炉、GSP 气化炉、鲁奇MARK—IV 型气化炉、U-GAS 气化炉、PRENFLO 炉等。
第二代气化炉在各种煤的适应性、热效率的提高、单台炉能力的增加、环境污染的减少等方面均有很大进步。
煤浆多喷嘴对置气化炉推进了我国煤气化实现产业化进程,我国目前煤气化制甲醇多采用水煤浆多喷嘴对置气化炉。
由于国内甲醇市场发展较快,利润较高,使投资者对大型甲醇项目十分关注,特别是煤产地和天然气产地,在积极研究建设大型甲醇项目,部分已经开展开工建设。
《产业政策调整指导目录》(2011 年)指出限制建设110 万吨/年以下的甲醇生产装置。
二、煤气化(甲醇)产业发展趋势煤炭在我国能源生产与消费结构中一直占主导地位,近几年,我国大规模的煤化工项目相继开工建设并投产运行,作为煤化工的核心和关键技术的煤气化技术主要用于以下几个方面:(1)生产燃料煤气,通过选用不同的气化方法,可以制得低、中、高三种热值燃气,以满足钢铁工业、化学工业、联合循环发电(IGCC)和民用等不同对象的要求;(2)生产合成气,用作合成氨、合成甲醇和甲醚以及合成油的原料气;(3)生产氢,煤气化制氢将是未来氢能经济的主要技术路线。
德士古水煤浆加压气化工艺(TGP)、壳牌干粉煤加压气化工艺(SCGP)和新型(多喷嘴对置式)水煤浆加压气化技术在国内都已得到了规模化应用,其应用效果均已得到工业化验证,GSP技术在我国也已开始建设,神华宁煤和山西兰花煤化工集团将分别于2009年和2010年投料试车,其经济性和装置性能将得到有效验证。
浅述甲醇生产技术进展

1 引 言
2 1 甲醇原 料气 制造 和净化 技术 现状 .
然气为原料生产 , 国内甲醇生产企业主要是 以煤为 原料 。典型的流程包括原料气制造 、 原料气净化 、 甲 醇合成、 甲醇精馏等工序。其各单元技术的最新 粗 进展介 绍如下 。
熔聚气化) 气 流床气化炉 , 、 近几 年引进 的 T x c eao 水煤浆气化和 S e 粉煤气化, hl l 其中 Teao的气化 xc
成富氢成分 , 用作转化炉燃料 , 贫氢成分返回进人转 化炉转化管。这一设计使 甲醇合成反应器可比常规 反应器操作在较低压力下 , 从而允许反应器 和管道 使用 造价较 低 的材质 。 日 本东洋工程公司采用 MR - F Z甲醇合成反应 器设计 了 50 / 0 0td甲醇装置 。合成气 直接进入管 式反应器的管程 , 并径向透过催化剂进人多孔外管 。 该公司设计 的 1 0 / 00 0td的甲醇合成装置 , 采用 2 台专有的热交换器式转化器 ( APX )、 T - S 1台吹氧 二次转化器和 2台 MR . FZ反应器 。新工艺流程对 于 10 0/ 0 0td的装置可减少建造费用到 6 亿美元 。
引进较早 , 使用的经验较多 , 国产化率高 , 投资较省 。 S e 气化还没有使用经验。 hl l
3 0
四川化 工
第1 4卷
2 1 第ห้องสมุดไป่ตู้6期 0 1年
国内在德士古水煤浆造气技术的基础上开发了 多喷嘴对置式水煤浆气化技术 , 已在较多工业装 并 置上采用 , 几个主要运行指标 已超过德士古水煤浆 气化 技术 。由青 岛联 信 化 学有 限公 司、 西柳 州 化 广 学工业公司等共同开发的 Q B0 催化剂预示着我 D - 4 国自主开发的气化技术和耐硫变换技术将替代国外 技术, 打破了由国外公 司垄断气化 和高浓度耐硫变 换催化剂技术的局面。 甲醇粗煤气脱硫脱碳净化与合成氨是相 同的。 只是不需要液氮洗 。国内主要 的净化技术有低温甲 醇洗、 E N D, MD A、 H 对于中小厂也有脱硫用 A A、 D P S 脱碳用热钾碱 、C MD A技术L。 D , P、 E 7 ] 2 2 甲醇合成现状 .
水煤浆技术生产氨、醇过程中废液的处理

从 气 化炉 和碳洗 塔排 出 的高温黑 水进 人高 压 闪蒸器 ,闪蒸 出大部 分溶解 的合 成气 后进 入低 压 闪蒸器 进一 步 闪蒸 ,低压 闪蒸器 出 口黑水 与渣 池 送来 的黑水 一起 进入 真空 闪蒸 器 。真空 闪蒸器 出 口黑水 送 入澄清 槽 。 在澄 清槽 中 ,耙 料机将 沉 降下来 的细渣推 至 澄清槽 底部 出 口。澄清槽底 部 出来 的细渣 浆经 澄 清槽底 料泵 最终 送 至真空 过滤 机和压 滤机 。澄 清 槽上部 清 水 溢 流 至灰 水 槽 ,经 低 压 灰 水 泵 加 压 后 ,一部 分送 至锁 斗 冲洗 水 罐作 为锁 斗 冲 洗 水 ,
周 辉,李 灵 ,娄 伦 武 , 王启 延
( 贵 州 金 赤 化 工 有 限 责 任 公 司 ,贵 州 桐 梓 5 6 3 2 0 0 ) 摘 要 :我 公 司采 用 GE水 煤 浆 技 术 年 产 3 0 0 k t 合成 氨与 3 0 0 k t 甲醇 ,生 产 过 程 中 产 生 了 大 量 氮 、 硫
1 含 硫 、 含 氨 污 水 的 来 源
1 . 1 气 化 灰 水
硫磺 。但 经过 多级 反质硫 磺 、H S和 S O ,若 直 接 送 至氨法 脱硫 装置 会造 成一 系列不 利 影响 ,为此 在硫 回收尾气 排放 前设 置 了洗涤装 置 ,由此 产 生
化 工 设 计 通 讯
・
第4 O卷第 1期
2 0 1 4年 2 月
4 4 ・
Che mi c a l En gi n e e r i ng De s i gn Co m mun i c a t i o ns
水 煤 浆 技 术 生产 氨 、醇 过 程 中废 液 的处 理
合成氨工业现状及节能技术
化工工艺论文题目名称:合成氨的工业现状和节能技术系别:化学与化工学院专业:应用化学班级:学生:学号:指导教师:摘要本论文介绍了合成氨的一些生产方法,分别为煤制气合成法、固定床气化法、流化床气化法、气流床气化法、溶浴床气化法以及对现代典型合成氨工业生产流程详细介绍;节能技术分别从工艺改造和护手各项余热和余能进行研究。
关键字:合成氨,煤制气,固定床,节能,回收abstractThis paper introduces some methods of production of synthetic ammonia,for coal gas synthesis method, fixed bed gasification, fluidized bed gasification, entrained flow gasification method, melting bath bed gasification method and typical of modern synthetic ammonia industry production process in detail.Energy-saving technology from process improvement and hand the residual heat and energy research.key words: synthetic ammonia coal gas energy conservation reclaim目录第一章合成氨工艺现状 (1)1.1 国外传统型蒸汽转化制氨工艺阶段 (1)1.2 我国目前合成氨技术的基本状况 (2)第二章几种典型的合成氨工艺介绍 (3)2.1 煤制气合成氨工艺 (3)2.2 固定床气化法 (3)2.3 流化床气化 (4)2.4 气流床气化 (4)2.5 熔浴床气化 (5)第三章合成氨典型工业生产工艺流程 (6)3.1 造气工段 (6)3.2 脱硫工段 (6)3.3 变换工段 (7)3.4 变换气脱硫与脱碳 (8)3.5 碳化工段 (8)3.5.1 气体流程 (8)3.5.2 液体流程 (9)3.6 甲醇合成工段 (9)3.7 精炼工段 (10)3.8 压缩工段 (10)3.9 氨合成工段 (11)3.10 冷冻工段 (12)第四章合成氨的节能技术 (13)4.1 选择先进的节能工艺 (13)4.2 回收各项余热和余能进行热能综合利用 (14)参考文献 (16)第一章合成氨工艺现状合成氨工业在整个国民经济中占有重要的地位。
我国合成氨生产工艺技术现状
我国合成氨生产工艺技术现状2009年07月10日09:271装置现状我国合成氨装置是大、中、小规模并存的格局,总生产能力为4260万t/a。
大型合成氨装置有30套,设计能力为900万t/a,实际生产能力为1000万t/a;中型合成氨装置有55套,生产能力为460万t/a;小型合成氨装置有700多套,生产能力为2800万t/a。
目前我国已投产的大型合成氨装置有30套,设计总能力为900万t/a,实际生产能力为1000万t/a,约占我国合成氨总生产能力的23%。
除上海吴泾化工厂为国产化装置外,其余均系国外引进,荟萃了当今世界上主要的合成氨工艺技术,如以天然气和石脑油为原料的凯洛格传统工艺(9套)、凯洛格-TEC工艺(2套)、托普索工艺(3套)、节能型的AMV工艺(2套)和布朗工艺(4套);以渣油为原料的德士古渣油气化工艺(4套)和谢尔气化工艺(3套);以煤为原料的鲁奇粉煤气化工工艺(1套)和德士古水煤浆气化工艺(1套)。
我国大型合成氨装置所用原料天然气(油田气)占50%,渣油和石脑油占43%,煤占7%,其下游产品除1套装置生产硝酸磷肥外,其余均生产尿素。
70年代引进的大型合成氨装置均进行了技术改造,生产能力提高了15%~22%,合成氨吨综合能耗由41.87GJ降到33.49GJ,有的以石油为原料的合成氨装置(如安庆、金陵、广石化)用炼油厂干气顶替一部分石脑油(每年大约5 万t)。
另外,我国还有3套大型合成氨装置在建,南化公司计划投料,吉化在设计中,卢天化公司购买的墨西哥二手设备在着手建设,届时,我国大型合成氨装置总生产能力将达1205万t/a。
我国中型合成氨装置有55套,生产能力为460万t/a;约占我国合成氨总生产能力的11%,下游产品主要是尿素和硝酸铵,其中以煤、焦为原料的装置有34套,占中型合成氨装置的62%;以渣油为原料的装置有9套,占中型合成氨装置的16%;,以气为原料的装置有12套,占中型合成氨装置的22%;我国小型合成氨装置有700多套,生产能力为2800万t/a,约占我国合成氨总生产能力的66%,原设计下游产品主要是碳酸氢铵,现有112套的装置经改造生产尿素。
我国合成氨工业的回顾与展望--纪念世界合成氨工业化100周年
我国合成氨工业的回顾与展望--纪念世界合成氨工业化100周年颜鑫【摘要】Author has briefly described the important influence of 100th anniversary of the world synthetic ammonia industrialization on human society development; has reviewed the developmental progress of ammonia synthsis industry in China since 80 years; has prospected the developmental tendency of synthetic ammonia industry in China:(1) Changing from oil to coal and oil to gas on aspect of raw materials ;(2) Developing large units and suppress-ing small ones, and displacing capacity on scale aspect;(3) Developing new type high efficiency catalyst, low pressure synthesis process and jointly pro-ducing process for a variety of products on aspect of production technology.%简述了世界合成氨工业化100周年对人类社会发展的重大影响;回顾了我国合成氨工业80年来的发展历程;展望了我国合成氨工业的发展趋势:①原料方面进行油改煤、油改气;②规模方面上大压小和产能置换;③生产技术方面发展新型高效催化剂、低压合成工艺和多联产工艺。
水煤浆气化生产合成氨装置变换炉及变换工艺分析
水煤浆气化生产合成氨装置变换炉及变换工艺分析贺鑫平;余涛;王煊;黄垒;王延安【摘要】介绍了水煤浆气化生产合成氨装置中两种变换炉型:绝热变换炉和移热变换炉,根据不同的变换炉型,形成了两段绝热、两段移热和绝热+移热3种合成氨变换工艺.采用Aspen Plus模拟软件,计算了3种工艺下每台变换炉出口气体温度和CO含量,采用操作线分析的方法进行了比较,同时考察了3种工艺下的系统压降、副产蒸汽、催化剂装填量、运行和维护等,并对不同规模的合成氨装置变换工艺的选择给出了建议.%2 types of shift reactors,adiabatic shift reactor and heat-removal reactor,were introduced for ammonia plant based on coal water slurry gasification. According to different combinations of these 2 types,3 shift processes were formed, which were two-stage adiabatic process,two-stage heat-removal process,and adiabatic&heating-removal process. With the simulation of Aspen Plus,temperature and CO content of each shift reactor exit gas were calculated for these 3 shift processes and comparison was made based on the method of operating line analysis. Besides,shift section pressure drop,steam generated as a by-product,catalyst volume,operation and maintenance of the 3 different processes were investigated,and suggestions were given for the selection of shift process for the ammonia plant of different capacities.【期刊名称】《煤化工》【年(卷),期】2017(045)006【总页数】6页(P6-11)【关键词】水煤浆气化;合成氨;变换炉;变换工艺;绝热变换炉;移热变换炉;绝热+移热变换工艺【作者】贺鑫平;余涛;王煊;黄垒;王延安【作者单位】华陆工程科技有限责任公司,陕西西安 710065;华陆工程科技有限责任公司,陕西西安 710065;华陆工程科技有限责任公司,陕西西安 710065;华陆工程科技有限责任公司,陕西西安 710065;华陆工程科技有限责任公司,陕西西安710065【正文语种】中文【中图分类】TQ546变换炉是水煤浆气化生产合成氨装置变换单元的核心设备,粗水煤气中的CO与自身携带的水蒸气(H2O)在此发生变换反应。
- 1、下载文档前请自行甄别文档内容的完整性,平台不提供额外的编辑、内容补充、找答案等附加服务。
- 2、"仅部分预览"的文档,不可在线预览部分如存在完整性等问题,可反馈申请退款(可完整预览的文档不适用该条件!)。
- 3、如文档侵犯您的权益,请联系客服反馈,我们会尽快为您处理(人工客服工作时间:9:00-18:30)。
我国近年水煤浆气化制合成氨、甲醇情况汇总
原料结构调整取得积极进展。
随着一批先进煤气化技术开发成功和投入运行,氮肥行业的原料结构调整迈出新的步伐。
到2014年底,我国采用水煤浆加压气化、干煤粉加压气化、碎煤加压气化技术已建成合成氨装置生产能力达到1700万吨,占全国合成氨总产能的23%。
随着这些新技术的应用,采用非无烟煤为原料的产品比重明显提高,2014年以非无烟煤为原料的合成氨、尿素产能占比均达24%,相比2010年提高10个百分点以上。
以常压无烟煤为原料的合成氨、尿素产能相比2010年分别下降了16个百分点和9个百分点。
水煤浆气化合成氨生产装置情况
2014年底,我国共有27家企业的合成氨生产装置采用水煤浆气化技术制取原料气,合成氨生产能力957.5万吨/年。
(1)GE水煤浆气化合成氨生产装置
2014年底,共建成采用GE水煤浆气化技术的合成氨生产企业9家,应用了23台气化炉,合成氨生产能力236.5万吨/年。
(2)多喷嘴对置式水煤浆气化合成氨生产装置
2014年底,共建成采用多喷嘴对置式水煤浆气化技术的合成氨生产企业6家,应用了11台气化炉,合成氨生产能力204万吨/年。
(3)多元料浆气化合成氨生产装置
2014年底,共建成采用多元料浆气化技术的合成氨生产企业13家,应用了34台气化炉,合成氨生产能力469万吨/年。
(4)清华炉水煤浆气化合成氨生产装置
2014年底,共建成采用清华炉水煤浆气化技术的合成氨生产企业2家,应用了7台气化炉,合成氨生产能力48万吨/年。
水煤浆气化合成氨生产产品产量及产能利用情况
2014年,全国采用水煤浆气化技术制取原料气的合成氨产量751.3万吨。
2014年,共有27家企业采用水煤浆气化技术生产合成氨,除去3家2013年下半年和2014年建成投产的企业外的24家企业中,有14家占58.3%的企业合成氨产量达到设计能力的90%以上(其中9家超过设计能力),有5家占20.8%的企业合成氨产量达到设计能力的80%-90%;有3家占12.5%的企业合成氨产量达到设计能力的50%-80%;有2家占8.3%的企业合成氨产量不足设计能力的50%。
在所有的新型煤气化合成氨生产中,水煤浆气化合成氨装置的开车率最高。
水煤浆气化合成氨生产装置在建情况
2015年投产及在建(或设计)的采用水煤浆气化技术的合成氨生产企业14家,设计能力536.6万吨/年。
(1) GE水煤浆气化合成氨生产装置在建情况
2015年投产采用GE水煤浆技术的合成氨生产企业1家, 3台气化炉,设计能力30万吨/年。
(2)多喷嘴对置式水煤浆气化合成氨生产装置在建情况
2015年投产及在建采用多喷嘴对置式水煤浆技术的合成氨生产企业6家, 15台气化炉,设计能力271.6万吨/年。
(3)清华炉水煤浆气化合成氨工业生产装置在建情况
2015年投产及在建(或设计)采用清华炉水煤浆气化技术的合成氨生产企业7家, 11台气化炉,设计能力235万吨/年。
继续推进合成氨原料及动力结构调整,提高以非无烟煤为原料的产能比重,支持部分有条件的气头氮肥装置承担天然气调峰任务,并执行可中断气价政策。
到2020年,采用非无烟煤的合成氨产能占比从目前的23.9%提升至40%左右;以常压无烟煤为原料的合成氨产能占比从目前的51.3%下降至41%;以天然气为原料的合成氨产能占比从目前的22.2%下降至17%。
其余2%为以焦炉气为原料。
2020年氮肥原料结构调整目标
单位:万吨,折纯氮 合成氨产能占比 2014年 2020年
以煤为原料 75.2% 81%
其中 以无烟煤为原料 51.3% 41% 以非无烟煤为原
23.9% 40%
料
以气为原料 22.2% 17%
以焦炉气为原料 2.1% 2%
十二五”期间,我国甲醇产业集中度逐年提高。
截止2014年,年产能规模在30万吨以上的企业共81家,比2010年增加45家,这些企业合计产能4653.6万吨,比2010年同类规模增加108.3%,占总产能比重达67.5%,比2010年提高9.3个百分点。
其中,还形成了神华等16家百万吨级超大型规模的生产企业或企业集团。
与此同时,我国甲醇生产向资源地聚集的趋势也更加明显。
2014年,具有煤炭资源优势的西北地区甲醇产能达到2937万吨,比2010年增加143.8%,占全国产能的比重由2010年的31.4%提高到2014年的42.6%。
产业结构更趋合理。
从原料结构看,经过“十二五”的努力,我国以煤制甲醇为主的格局已经形成。
2011-2014年,全国总计新增甲醇产能3053万吨,其中煤头产能增加2184万吨,占总计新增产能的71.6%;煤制甲醇产能总量已达4706万吨,占总产能的68.3%,比2010年提高了2.6个百分点,年均增长15%。
同时,焦炉煤气制甲醇也得到较快发展。
2011-2014年,焦炉煤气制甲醇新增产能636万吨,占总计新增产能的20.8%;焦炉煤气制甲醇产能总量已达1073万吨,占总产能的15.5%,比2010年提高了1.1个百分点,年均增
长16.6%。
而同期天然气制甲醇所占的份额逐年降低,2014年天然气制甲醇产能总量为1114万吨,占总产能的16.2%,产能占比较2010年下降了6.7个百分点。
依托先进煤气化技术,以煤为甲醇生产的主要原料更加符合我国的能源资源条件。
再从工艺角度来看,单醇已占据我国甲醇生产的主体地位。
2014年,我国单醇产能已达到5462万吨,占总产能的79%,比2010年提高7个百分点;其中采用先进粉煤气化技术的产能达到3315万吨,占单醇产能的60%以上。
单醇产能总量的提高,反映了我国甲醇生产在规模和整体水平上均有较大程度的提高。
2014年,全国共建成采用新型煤气化技术的甲醇生产企业61家,甲醇生产能力3808万吨/年。
水煤浆气化甲醇生产装置情况
2014年底,我国共有40家企业的甲醇装置采用水煤浆气化技术制取原料气,甲醇生产能力2531万吨/年。
(1)GE水煤浆气化甲醇生产装置
2014年底,共建成采用GE水煤浆气化技术的甲醇生产企业16家,71台气化炉,甲醇生产能力1345万吨/年。
(2)多喷嘴对置式水煤浆气化甲醇生产装置
2014年底,共建成采用多喷嘴对置式水煤浆气化技术的甲醇生产企业9家,22台气化炉,甲醇生产能力496万吨/年。
(3)多元料浆煤气化甲醇生产装置
2014年底,共建成采用多元料浆气化技术的甲醇生产企业14家,31台气化炉,甲醇生产能力660万吨/年。
(4)清华炉水煤浆气化甲醇生产装置
2014年底,共建成采用清华炉水煤浆气化技术的甲醇生产企业1家,应用了3台清华炉,甲醇生产能力30万吨/年。
水煤浆气化甲醇产品产量及装置利用情况
2014年,全国采用水煤浆气化技术制取原料气的甲醇产量1759.4万吨。
2014年,共有37家采用水煤浆气化技术的甲醇生产企业,其中29家为2013年之前建成投产,其中的23家企业占2014年前投产企业总数79.1%的企业甲醇产量达到设计能力的80%以上;其中4家企业占2014年前投产企业总数13.4%的企业甲醇产量达到设计能力的50%-80%;2家企业占2014年前投产企业总数6.9%的企业甲醇产量低于设计能力的50%。
水煤浆气化甲醇生产装置在建情况
2015年投产及在建的采用水煤浆气化技术的甲醇生产企业17家,设计能力1178万吨/年。
(1)GE水煤浆气化甲醇生产装置在建情况
在建采用GE水煤浆气化技术的甲醇生产企业4家,新增22台气化炉,设计能力510万吨/年。
(2)多喷嘴对置式水煤浆气化甲醇生产装置在建情况
在建采用多喷嘴对置式水煤浆气化技术的甲醇生产企业7家,其中一家为后期,新增23台气化炉,设计能力522万吨/年。
(3)清华炉水煤浆气化甲醇生产装置在建情况
在建采用清华炉水煤浆气化技术的甲醇生产企业6家,新增8台气化炉,甲醇设计能力146万吨/年。