装配工艺的三个基本条件
装配工艺
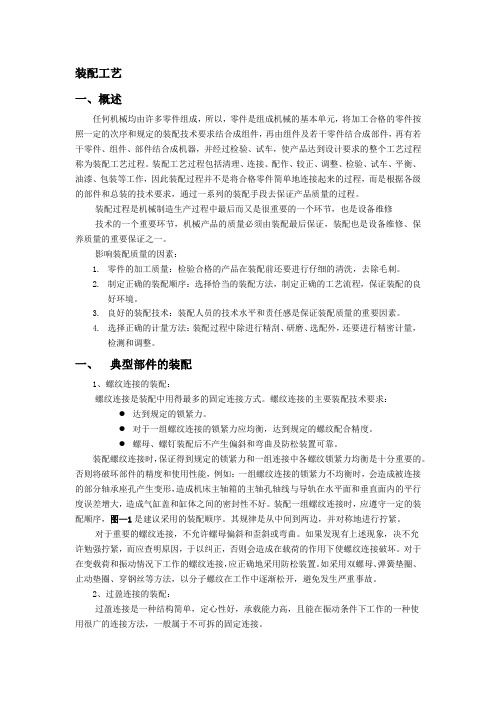
装配工艺一、概述任何机械均由许多零件组成,所以,零件是组成机械的基本单元,将加工合格的零件按照一定的次序和规定的装配技术要求结合成组件,再由组件及若干零件结合成部件,再有若干零件、组件、部件结合成机器,并经过检验、试车,使产品达到设计要求的整个工艺过程称为装配工艺过程。
装配工艺过程包括清理、连接、配作、较正、调整、检验、试车、平衡、油漆、包装等工作,因此装配过程并不是将合格零件简单地连接起来的过程,而是根据各级的部件和总装的技术要求,通过一系列的装配手段去保证产品质量的过程。
装配过程是机械制造生产过程中最后而又是很重要的一个环节,也是设备维修技术的一个重要环节,机械产品的质量必须由装配最后保证,装配也是设备维修、保养质量的重要保证之一。
影响装配质量的因素:1.零件的加工质量:检验合格的产品在装配前还要进行仔细的清洗,去除毛刺。
2.制定正确的装配顺序:选择恰当的装配方法,制定正确的工艺流程,保证装配的良好环境。
3.良好的装配技术:装配人员的技术水平和责任感是保证装配质量的重要因素。
4.选择正确的计量方法:装配过程中除进行精刮、研磨、选配外,还要进行精密计量,检测和调整。
一、典型部件的装配1、螺纹连接的装配:螺纹连接是装配中用得最多的固定连接方式。
螺纹连接的主要装配技术要求:●达到规定的锁紧力。
●对于一组螺纹连接的锁紧力应均衡,达到规定的螺纹配合精度。
●螺母、螺钉装配后不产生偏斜和弯曲及防松装置可靠。
装配螺纹连接时,保证得到规定的锁紧力和一组连接中各螺纹锁紧力均衡是十分重要的。
否则将破坏部件的精度和使用性能,例如:一组螺纹连接的锁紧力不均衡时,会造成被连接的部分轴承座孔产生变形,造成机床主轴箱的主轴孔轴线与导轨在水平面和垂直面内的平行度误差增大,造成气缸盖和缸体之间的密封性不好。
装配一组螺纹连接时,应遵守一定的装配顺序,图—1是建议采用的装配顺序。
其规律是从中间到两边,并对称地进行拧紧。
对于重要的螺纹连接,不允许螺母偏斜和歪斜或弯曲。
通用装配工艺及要求

通用装配工艺及要求一.装配基本规范装配工在装配之前,应首先熟悉本工位的工艺文件、图纸及技术要求;并在装配工作中,严格执行工艺及产品图纸等技术要求机械装配应严格按照设计部提供的装配图纸及工艺要求进行装配,严禁私自修改作业内容或以非正常的方式更改零件。
装配时,应检查零件与装配有关的形状和尺寸精度是否合格,检查有无变形、损坏等,并应注意零件上各种标记,防止错装。
,装配前应主动检查零部件的正确性和外观质量,发现不合格产品及零部件不应装配,应及时向质量人员报告外购件必须先经过试验检查合格后,才能投入装配。
装配时,零件、工具应有专门的摆放设施,原则上零件、工具不允许摆放在机器上或直接放在地上,如果需要的话,应在摆放处铺设防护垫或地毯。
装配过程中零件不得磕碰、切伤,不得损伤零件表面,或使零件明显弯、扭、变形,零件的配合表面不得有损伤。
各配钻孔应按装配图和工艺规定。
相配零件的配合尺寸要准确,不得偏斜需在整车上进行焊接作业时,应断开整车电源总开关,以及其它精密控制单元的插接器(如电控发动机ECU,自动变速箱ECU等),焊接用搭铁线应尽量远离整车线束,并且搭铁要牢固、可靠压入平键及装卸轴承时,不得用铁锤敲打,应用木锤、铅、铝、紫铜锤或用装配工具进行装配装配滑动零件,如花键轴和带花键孔的齿轮等,应保证能相对地灵活移动装配在同一位置的螺钉,应保证长短一致,松紧均匀部件上各外露件如螺钉、铆钉、销钉、标牌、轴头及发蓝、电镀等件均应整齐完好,不许有损伤或字迹不清等现象,否则应予以更换,以确保外观质量二.滚动轴承的装配工艺要点轴承的安装必须在干燥、清洁的环境条件下进行。
安装前应仔细检查轴和外壳的配合表面、凸肩的端面、沟槽和连接表面的加工质量。
所有配合连接表面必须仔细清洗并除去毛刺,铸件未加工表面必须除净型砂轴承装配前,轴承位不得有任何的污质存在轴承装配时应在配合件表面涂一层润滑油,轴承无型号的一端应朝里,即靠轴肩方向必须在套圈端面的圆周上施加均等的压力,将套圈压入,不得用鎯头等工具直接敲击轴承端面,以免损伤轴承。
装配工艺规程的制定

2、确定装配顺序的一般原则
1)预处理工序先行: 如零件的清洗、去毛刺与飞边、防绣和防腐处理、油漆和
干燥等。 2)先基准后其他:
先进行基准件的装配,以便保证装配过程的稳定性。 3)先下后上:
应用——固定式装配多用于单件小批生产;或装配时不便移动
的大型机械,或装配时移动会影响精度的产品。
2)移动式装配
将产品或部件置于装配线上,通过连续或间歇的移动使其 顺次经过各装配工作地,以完成全部装配工作。
移动式装配:连续移动、间歇移动、变节奏移动。 特点:较细划分装配工序,
广泛采用专用设备及工装, 生产率高, 对工人技术水平要求较低, 易于保证质量。
▪ 7)冲击性质的装配、压力装配和热装配或补充加工 的装配工序应尽量先行,以免破坏后续的装配质量。
▪ 8)使用相同设备及工艺装备的装配,有共同特殊装 配环境的装配,处于基准件同方位的装配应尽可能 连续安排。
大批大量生产中,要制订装配工序卡片,详细说明 该装配工序的工艺内容,以直接指导工人进行操作。
除了装配工艺过程卡片及装配工序卡片以外,还应 有装配检验卡片及试验卡片,有些产品还应附有测试报 告、修正(校正)曲线等。
(7)制定产品检测与试验规范
产品装配完毕,应按产品技术性能和验收技术条件制 定检测与试验规范。
单件小批生产中,装配精度要 求高且零件数较多的场合
中小型柴油机的活塞与缸套、 活塞与活塞销、滚动轴承的内 外圈与滚子
车床尾座垫板、滚齿机分度蜗 轮与工作台装配后精加工齿形
调整法
除必须采用分组法选配的精度 配件外,调整法可用于各种装 配场合
汽车装配工艺技术

3、装配的紧固性。凡是螺栓、螺母、螺钉等件必须 达到规定的扭矩要求。应交叉紧固的必须交叉紧 固,否则会造成螺母松动现象,带来安全隐患。 螺纹联接严禁松动现象,不过,过紧会造成螺纹 变形、螺母卸不下来。 4、装配的润滑性 按工艺要求,凡需润滑的部位必须加注定量的润 滑油或润滑脂。对发动机来说,如果润滑油过少 或漏加,发动机运转起来,很快会造成齿轮磨损 或拉缸现象,直到整机损坏;加注过多,发动机 运转时润滑油很容易窜到燃烧室、燃烧后产生积 碳;因此加油量必须按工艺要求执行。
13、加注油料。 给油箱加注柴油,中后桥减速器加注润滑油, 两边轮毂加注润滑油,注意加注油料是应按照工 艺要求加注,不能多加或者少加。最后,做好加 油标记,涂抹绿漆。 14、分装及安装翼子板。 根据工艺要求分装好翼子板,然后把翼子板安装 到翼子板支架上面,打紧螺栓。在安装过程中要 保护翼子板漆面不得有磕碰、划伤。牵引车安装 侧标志灯。
七、装配的注意事项 1、对于长圆孔连接件,一般要加平垫片,且 平垫片放于长圆孔一侧。 2、对于超过四个孔的连接件,需进行对角紧 固,最先紧固的螺母最后还应复紧。 3、对于圆孔与长圆孔同时存在的件,应先紧 圆孔端,后紧长圆孔端。 4、为保证整车美观性,管束与电线束应避免 交叉。 5、管线束过梁或者与梁接触时,必须用护套 和蛇形护套。
3、装贮电瓶箱 安装电瓶箱总成时 检查贮气筒油漆质量、不得 有漏漆、划漆、凸焊螺母焊缝平整、贮气筒不得有 明显缺陷。 4、连接传动轴于后桥减速器上。检查传动轴油漆无 划伤,将传动轴凸缘上的孔与后桥减速器凸缘上的 孔对准,从传动轴方向穿入螺栓、套上弹簧垫
圈、扭紧螺母。
5、翻转底盘 首先把吊链从后桥下面穿过去并固定在另一侧 的吊链上面;将翻转底盘夹具夹在车架前端,打紧 螺栓,操纵设备翻转底盘、翻转后取下夹具及吊链。
第三篇 过程装备制造工艺—— 装配工艺

3)查找组成环:从封闭环起
遵守最短路线原则:
组成环数等于相关零件数,即一件一环
2020/3/9
12.2 装配尺寸链—装配尺寸链的建立
1、方法和步骤 1、确定封闭环,是在装配后形成的,而且这一环是具有装 配精度要求; 2、确定各组成环,对装配精度有直接影响的零件尺寸或 位 置关系; 3、确定增减环
装配的运动精度有①主轴圆跳动;②轴向窜动;③ 转动精度;④传动精度。
装配的运动精度主要与主轴轴颈处的精度、轴承精 度、箱体轴孔精度及传动元件自身精度有关。
接触精度是指配合表面接触达到规定接触面积的大 小与接触点分布情况。
接触精度主要影响接触刚度和配合质量的稳定性。
2020/3/9
上述精度之间的关系: 接触精度和配合精度是距离精度的基础。 位置精度又是相对运动精度的基础。
2020/3/9
3、特点
除有一般尺寸链的特点外,还有: 封闭环十分明显,一定是机器产品或部件的某项装
配精度; 封闭环在装配后才能形成,不具有独立性(装配精
度只有装配后才能测量); 各组成环不是仅在一个零件上的尺寸,而是在几个
零件或部件间与装配精度有关的尺寸; 装配尺寸链形式较多,有线性尺寸链、角度尺寸链
B1
B2
A1
车床装配的尺寸
B0 B3
装配精度:产品装配后实际达到的精度,包括零部件间 的尺寸精度; 位置精度;相对运动精度和接触精度
位置精度反映各 零件有关相互位置与 装配相互位置的关系。
活塞 连杆 缸体
曲轴
0
1 2
3
2020/3/9
装配精度:产品装配后实际达到的精度,包括 距离精度; 位置精度;相对运动精度和接触精度
机械装配工艺详解
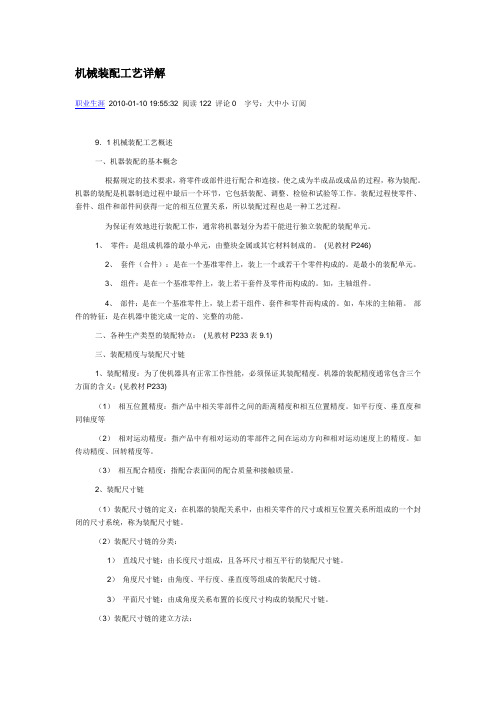
机械装配工艺详解职业生涯2010-01-10 19:55:32 阅读122 评论0 字号:大中小订阅9.1机械装配工艺概述一、机器装配的基本概念根据规定的技术要求,将零件或部件进行配合和连接,使之成为半成品或成品的过程,称为装配。
机器的装配是机器制造过程中最后一个环节,它包括装配、调整、检验和试验等工作。
装配过程使零件、套件、组件和部件间获得一定的相互位置关系,所以装配过程也是一种工艺过程。
为保证有效地进行装配工作,通常将机器划分为若干能进行独立装配的装配单元。
1、零件:是组成机器的最小单元,由整块金属或其它材料制成的。
(见教材P246)2、套件(合件):是在一个基准零件上,装上一个或若干个零件构成的。
是最小的装配单元。
3、组件:是在一个基准零件上,装上若干套件及零件而构成的。
如,主轴组件。
4、部件:是在一个基准零件上,装上若干组件、套件和零件而构成的。
如,车床的主轴箱。
部件的特征:是在机器中能完成一定的、完整的功能。
二、各种生产类型的装配特点:(见教材P233表9.1)三、装配精度与装配尺寸链1、装配精度:为了使机器具有正常工作性能,必须保证其装配精度。
机器的装配精度通常包含三个方面的含义:(见教材P233)(1)相互位置精度:指产品中相关零部件之间的距离精度和相互位置精度。
如平行度、垂直度和同轴度等(2)相对运动精度:指产品中有相对运动的零部件之间在运动方向和相对运动速度上的精度。
如传动精度、回转精度等。
(3)相互配合精度:指配合表面间的配合质量和接触质量。
2、装配尺寸链(1)装配尺寸链的定义:在机器的装配关系中,由相关零件的尺寸或相互位置关系所组成的一个封闭的尺寸系统,称为装配尺寸链。
(2)装配尺寸链的分类:1)直线尺寸链:由长度尺寸组成,且各环尺寸相互平行的装配尺寸链。
2)角度尺寸链:由角度、平行度、垂直度等组成的装配尺寸链。
3)平面尺寸链:由成角度关系布置的长度尺寸构成的装配尺寸链。
(3)装配尺寸链的建立方法:1)确定装配结构中的封闭环;2)确定组成环:从封闭环的的一端出发,按顺序逐步追踪有关零件的有关尺寸,直至封闭环的另一端为止,而形成一个封闭的尺寸系统,即构成一个装配尺寸链。
机械装配工艺规范标准

3.1.19 工艺准备 产品投产前所进行的一系列工艺工作的总称。其主要内容包括:对产品图 样进行工艺性分 析和审查;拟定工艺方案;编制各种工艺文件;设计、制造和调整工艺装
备;设计合理的生产 组织形式等。
3.1.20 工艺试验 为考查工艺方法、工艺参数的可行性或材料的可加工性等而进行的试验。
3.1.21 工艺验证 通过试生产,检验工艺设计的合理性。
3.4.2 安装 工件(或装配单元)经一次装夹后所完成的那一部分工序。 3.4.3 工步 在加工表面(或装配时的连接表面)和加工(或装配)工具不变的情况下,所连 续完成的那一部分工作。
3.4.4 辅助工作 由人和(或)设备连续完成的那一部分工序, 该部分工序不改变工件的形状、 尺寸和表面 粗糙度,但它是完成工步所必须的。如更换刀具等。
3.3.21 装配 按规定的技术要求,将零件或部件进行配合和连接,使之成为半成品或成品的 工艺过程。
3.3.22 包装 对产品采取一定的包装措施,通过储存、运输等流通过程使产品完好无损地运 到用户手中。
//
3.4 工艺要素 3.4.1 工序 一个或一组工人, 在一个工作地对同一个或同时对几个工件所连续完成的那一部 分工艺过程。
3.1.11 工艺文件 指导工人操作和用于生产、工艺管理等和各种技术文件。
3.1.12 工艺方案 根据产品设计要求、生产类型和企业的生产能力,提出工艺技术准备工作 具体任务和措施 的指导性文件。
//
3.1.13 工艺路线 产品或零部件在生产过程中, 由毛坯准备到成品包装入库, 经过企业各有 关部门或工序的 先后顺序。
3.3.15 磨削 用磨具以较高的线速度对工件表面进行加工的方法。 3.3.16 冷作 在基本不改变材料断面特征的情况下,将金属板材、型材等加工成各种制品的 方法。
装配通用技术条件

装配通用技术条件(JB/ZQ4000.9-86) 1.外购材料与零部件应具有JB/ZQ4000.1-86<产品检验通用技术要求>中规定的检验报告与合格证.2.用于紧固机架,机座和压力容器压紧法兰的紧固件,在紧固后,螺钉或螺母的端面与被紧固零件间的倾斜不得大于1°.3.螺栓与螺母拧紧后,螺栓应露出螺母2-4扣,不许露出过长或过短.4.各种密封毡圈、毡垫、石棉绳、皮碗等密封件装配前必须浸透油.钢纸板用热水泡软,紫铜垫作退火处理(加热至600-650℃后在水中冷却).5.d>4mm圆锥销与孔应进行着色检查,其接触率不得低于50%.带螺尾圆锥销打入后,大端须沉入相关件2-3扣.6.钩头键与楔键装配后,工作面上的接触率应在70%以上,其不接触部分不得集中于一段. 装配后外露尺寸应为斜面长度的10-15%(不包括钩头).7.花键或齿形离合器的装配, 单齿分度加工的矩形花键或齿形离合器的工作面研合后,同时接触的齿数不得少于2/3;接触率在齿长和齿高方向上均不得低于50%,研合时可用0.05mm的塞尺检查齿侧隙,塞尺不得插入全齿长.8.锥轴伸与轴孔配合表面接触应均匀, 着色研合检验时其接触率不得低于70%.9.各类联轴器技术要求及轴向(△X)、径向(△Y)与角向(△α)的许用补偿量,应符合有关联轴器标准的规定.10.轴承外圈与开式箱体或轴承座的各半圆孔间不准有"夹帮"现象,各半圆孔的"修帮"尺寸,不准超过下表规定的最大值.滚动轴承装配修帮尺寸mm━━━━━━━━━━━━━━━━━━━━━━轴承外径D bmax hmax ──────────────────────≤1200.1010 120-2600.1515 260-4000.2020>4000.2530 ━━━━━━━━━━━━━━━━━━━━━━11.采用润滑脂的轴承,装配后在轴承空腔内注入相当空腔容积65-80%的清洁润滑脂.12.轴承装在轴上后应靠紧轴肩,轴承内圈在常温状态经打击没有串动现象的情况下,圆锥滚子轴承和向心推力球轴承与轴肩的间隙不得大于0.05mm.其它轴承不得大于0.10mm.13.装配滚动轴承允许采用机油加热进行热装,油的温度不得超过100℃.14.在轴两端采用了径向间隙不可调的向心轴承(或滚针轴承、螺旋滚子轴承等), 而且轴的轴向位移又是以两端端盖限定时,必须留出间隙 C.如果没规定C的数值,通常可按C=0.2-0.4mm规定,当温差变化较大或两轴承中心距较大时,间隙C的数值可按下式计算:C=Lα△t+0.15式中:C─轴承外座圈与端盖间的间隙,mm.L─两轴承中心距,mm.α─轴材料的线膨胀系数(取α=12×10^(-6)△t─轴工作时温度与环境温度之差,℃ .0.15─轴膨胀后剩余的间隙,mm.15.单列圆锥滚子轴承、向心推力球轴承、双向推力球轴承向游隙按(表1)调整.双列和四列圆锥滚子轴承在装配时均应检查其轴向游隙,并应符合(表2)的要求.表1 :mm━━━━━━━━━━━━━━━━━━━━━━━━━━━━━━━━━━━━━━━━━━━轴承内径向心推力球轴承向游隙单列圆锥滚子轴承向游隙双列推力球轴承向游隙轻系列中及重系列轻系列轻宽.中及中宽系列轻系列中及重系列───────────────────────────────────────────≤300.02-0.060.03-0.090.03-0.100.04-0.110.03-0.080.05-0.1130-500.03-0.090.04-0.100.04-0.110.05-0.130.04-0.100.06-0.1250-800.04-0.100.05-0.120.05-0.130.06-0.150.05-0.120.07-0.1480-1200.05-0.120.06-0.150.06-0.150.07-0.180.06-0.150.10-0.18120-1500.06-0.150.07-0.180.07-0.180.08-0.20--150-1800.07-0.180.08-0.200.09-0.200.10-0.22--180-2000.09-0.200.10-0.220.12-0.220.14-0.24-->200-250--0.18-0.300.18-0.30-- ━━━━━━━━━━━━━━━━━━━━━━━━━━━━━━━━━━━━━━━━━━━表2: 双列、四列圆锥滚子轴承的轴向游隙mm━━━━━━━━━━━━━━━━━━━━━━━━━━━双列圆锥滚子轴向游隙轴承内径一般情况内圈比外圈温度高25-30℃───────────────────────────≤800.10-0.200.30-0.40 80-1800.15-0.250.40-0.50180-2250.20-0.300.50-0.60225-3150.30-0.400.70-0.80315-5600.40-0.500.90-1.00───────────────────────────四列圆锥滚子轴承内径轴向游隙───────────────────────────120-1800.15-0.25180-3150.20-0.30315-4000.25-0.35400-5000.30-0.40500-6300.30-0.40630-8000.35-0.45800-10000.35-0.451000-12500.40-0.50━━━━━━━━━━━━━━━━━━━━━━━━━━━16.滑动轴承上、下轴瓦的接合面要接触良好,无螺钉把紧的轴瓦接合面,用0.05mm和塞尺从外侧检查,在各处的塞入深度, 都不得大于接合面的1/3.17.上、下轴瓦装配后其外圆应与相关轴承孔良好接触,如果图样或相关设计文件对接触率未作具体规定时,应按下表的规定执行.上下轴瓦外圆与相关轴承孔的接触要求:━━━━━━━━━━━━━━━━━━━━━━━━━━━项目接触要求上瓦下瓦───────────────────────────接触角α:稀油润滑130°150°油脂润滑120°140°α角内接触率60%70%瓦侧间隙b,mm D≤200时,0.05mm塞尺不准塞入D>200时,0.10mm塞尺不准塞入━━━━━━━━━━━━━━━━━━━━━━━━━━━18.轴瓦内孔刮研后,应与相关轴颈接触良好, 如图样或相关设计文件未作具体规定时,则按下表的规定执行.上下轴瓦内孔与相关轴颈的接触要求:━━━━━━━━━━━━━━━━━━━━━━━━━━━接触角αα角范围内接触点,点数/25×25mm^2───────────────────────────稀油轴转速轴瓦内径,mm 油脂r/min≤180180-360360-500润润≤30043 2滑滑300-50054 3120°90°500-1000654>100086 5━━━━━━━━━━━━━━━━━━━━━━━━━━━注:受力较小的轴瓦、接触点可在25×25mm^2的面积上,按表中数值降低1个接触点.19.上、下轴瓦接触角α以外的部分均需刮出油楔(如下表所示C1),楔形从瓦口开始由最大逐步过渡到零,楔形最大值按下表中规定. 上、下轴瓦经刮研达要求并组装后,轴瓦内径与轴顶部处的间隙值C应达到图样配合公差的中间值或接近上限值.上下轴瓦油楔尺寸:(油楔最大值C1)━━━━━━━━━━━━━━━━━━━━━━━━━━━稀油润滑C1≈C油脂润滑距瓦两端面10-15mm范围内,C1≈C中间部位C1≈2C. ━━━━━━━━━━━━━━━━━━━━━━━━━━━注:C值为轴瓦的最大配合间隙.20.轴瓦中装固定销用的通孔,应在瓦口面与相关轴承孔的开合面保持平齐的情况下, 与其配钻铰. 固定销打入后,应与销孔紧密配合, 不得有松动现象,销子的端面应低于轴瓦内孔2-3mm.21.过盈配合零件在装配前必须对配合部位进行复检, 并做好记录.过盈量应符合图样或工艺文件的规定;与轴肩相靠的相头轮或环的端面,以及作为装配基准的轮缘端面,与孔的垂直度偏差应在图样规定的范围内.22.压装的轴和套允许在引入端制作导锥, 导锥的长度不准超过配合部位长度的15%,锥度各工厂自定.23.采用压力机压装时,应做好压力变化的记录,压力变化应当平稳,出现异常时就进行分析,不准有压坏零件配合表面的现象. 图样有最大压入力的要求时,应达到规定数值,不准过大或过小.24.压装完成后,在轴肩处必须靠紧,间隙不得大于0.10mm.25.热装薄环或轮缘时,在端面处应设置可靠的定位基准.热装后轴与环或轮毂与轮缘之间的中心不准出现互相偏斜现象.26.除铸铁轮毂与钢制轮缘在热装后可向轮毂内壁均匀浇冷水外,其余热装零件均应自然冷却,不准急冷.27.零件热装时,必须靠紧轴肩或其它相关端面.零件经过冷缩后, 零件与轴肩或其它相关端面的间隙在图样未做规定时, 不得大于配合长度尺寸的1/1000.28.主动链轮和被动链轮齿的中心线应当重合. 其偏移误码差不得大于两链轮中心距2/1000.29.链条非工作边的下垂度,在图样没有具体规定时,按两链轮中心距的1-4.5%的规定.30.相关的两个平面需要互研时, 只能在两个平面各自按平板或平尺刮研接近合格后,方准两件互研.被刮研表面接触点在图样或相关设计文件无具体规定或以精磨代替刮研时,应符合下表规定.一般情况下的平面刮研接触点━━━━━━━━━━━━━━━━━━━━━━━━━━━滑动速度接触面积,m^2≤0.20>0.20m/s点数/25×25mm^2 ───────────────────────────≤0.50340.50-1.5043━━━━━━━━━━━━━━━━━━━━━━━━━━━31.下列回转零件必须做静平衡试验:1).图样已给出不平衡力矩限值的零件;2).对于没有注明静平衡试验的回转零件,当Q.nmax>25时均需进行静平衡试验.式中Q为回转零件的质量,t;nmax为回转零件的最大转速,r/min.当nmax≤20r/min的以及锻造的全加工、全对称的回转零件不作静平衡试验.32.对于需要作平衡试验,但未规定平衡精度时,按JB/ZZ4-86<<刚体转动件的平衡>>规定的平衡精度G18执行. 33.所有铸造液压缸体等容器,如试压工序是安排在粗加工后进行的,而在精加工后表面又出现了气孔、裂纹、夹渣等缺陷时,则必须重新进行试压.34.所有钢板焊接的液压罐等容器,焊后应进行试压, 焊缝处经过切削加工时,则要重新试压.35.锻造或锻焊结构的液压缸等,要采用外观、超声波探伤、液压试验等方法,对承压的可靠性进行检验.36.探伤表面粗糙度应达到Ra3.2μm.37.承压母体试压与装配后的密封试压,如无特殊规定试验压力,一般为工作压力的1.5倍.38.零件母体承压可靠性的试压,保压15min(允许补压),母体各部不准有渗漏现象.39.装配件密封性试压,保压2min,不降压,且各密封处不准有渗漏现象.40.固定在机体上的管路,应按照JB/ZQ4000.8-86<<管道与容器焊接防锈通用技术要求>>的规定,进行清洗与防锈处理锻件通用技术要求(JB/ZQ4000.7-86)1.锻件上不应有白点,根据图样、工艺文件或订货技术要求的规定进行白点检查, 当发现有白点时,该批所有锻件必须经单个检查后,确定是否合格.2.锻件的力学性能试验,按图样、工艺文件或订货技术要求的规定可在纵向、切向和横向的试样上进行,试验的结果应符合JB/ZQ4287-86 (优质碳素结构钢)和JB/ZQ4288-86(合金结构钢)的规定.3.锻件根据其用途和工作条件,按试验种类分为:Ⅰ、Ⅱ、Ⅲ、Ⅳ和Ⅴ五组.每组锻件除Ⅰ组外,其必要的试验范围按下表规定.设计部门或订货单位对锻件力学性能有要求时,必须在图样或订货技术要求中注明.若未注明,则按Ⅰ组锻件处理.━━━━━━━━━━━━━━━━━━━━━━━一、锻件组别:Ⅰ1.组别的基本标志1)检验特性: 不试验.2)组成批的条件: 同一钢号的锻件.1.组别的基本标志1)检验特性: 测定每批中锻件的硬度.2)组成批的条件:根据同一规范进行热处理的同一钢号的锻件.2.验收时的必要力学性能指标: HB3.试验方法1)力学性能: -2)硬度: 每批中试验5%,但不少于5件.三、锻件组别:Ⅲ1.组别的基本标志1)检验特性: 测定每一锻件的硬度.2)组成批的条件:共同进行热处理的同一钢号的锻件.2.验收时必要力学性能指标: HB3.试验方法:1)力学性能: -2)硬度: 每一锻件均受试验.1.组别的基本标志1)检验特性:测定每一锻件的硬度和每一批中的力学性能.2)组成批的条件:共同进行热处理的同一炉号的锻件.2.验收时的必要力学性能指标:σs或σb, δ5, ψ, αk3.试验方法1)力学性能: 试验数量.a.锻件重量在10kg以下,每批在300件以下者,试验2件;每批超过300件者,试验0.5%,但不少于2件.b.锻件重量超过10-20kg,每批在200件以下者,试验2件:每批超过200件者,试验1%,但不得少于2件.c.锻件重量超过20kg,每批超过150件以下者,试验2件;每批超过150者,试验1.5%,但不得少于3件.2)硬度:每一锻件均受试验,选择具有极限的毛坯作力学性能试验.五、锻件组别:Ⅴ1.组别的基本标志1)检验特性: 测定每一锻件的力学性能.2)组成批的条件: 每一锻件均单个验收.2.验收时的必要力学性能指标:σs或σb, δ5, ψ, αk3.试验方法1)力学性能: 每一锻件均受试验.2)硬度: 每一锻件均受试验.───────────────────────注:1.每批锻件由同一图号制造的锻件组成, 允许在同一批锻件中包括根据各种图号制造的外形尺寸近似的锻件.2.经订货单位同意, 允许把各种牌号钢制成的Ⅰ组锻件组成一批.3.对Ⅳ、Ⅴ组锻件验收时的必要力学性能指标σs和σb的选择,应在图样或订货技术要求中规定,如无规定,由制造厂工艺部门决定.━━━━━━━━━━━━━━━━━━━━━━━4.锻件的验收规则和试验方法按标准要求进行焊接件通用技术要求(JB/ZQ400.3-86)1.焊接结构件的长度尺寸公差见1-245c 尺寸和形位公差数值.plb,适用于焊接零件和焊接组件的长度尺寸. 焊接件的直线度.平面度和平行度公差见1-245c 尺寸和形位公差数.plb,焊接结构件的尺寸公差与形位公差等级选用见1-245b 尺寸和形位公差等级.plb2.标注和未标注角度的偏差见1-246a 角度偏差.plb,角度偏差的公称尺寸以短边为基准边, 其长度从图样标明的基准点算起.3.喷丸处理的焊接件,为了防止钢丸钻入焊缝, 必须焊接内焊缝,并尽量避免内室和内腔.如果结构上必须有内室和内腔, 则必须进行酸洗,以便达到表面除锈质量等级Be(见JB/ZQ4000.10-86附录A). 对此图样需作标注.4.由平炉钢制造的低碳钢结构件, 可在任何温度下进行焊接.但为了避免焊接过程产生裂纹及脆性断裂, 厚度较大的焊接件,焊削必须根据工艺要求,进行预热和缓冷. 板厚超过30mm的重要焊接结构,焊后应立即消除内应力,消除内应力采用550-600℃回火,或200℃局部低温回火.5.普通低合金结构钢制造的焊接件,必须按照焊接零件的碳当量和合金元素含量、零件的厚度、钢结构件的用途和要求进行焊前预热和焊后处理,见表1 .表1:━━━━━━━━━━━━━━━━━━━━━━━━━━钢号厚度mm焊前预热焊后热处理温度℃℃──────────────────────────09Mn2不预热不处理09Mn2Si不预热不处理09MnV不预热不处理12Mn不预热不处理16Mn≤40不处理或600-650回火16MnRE>40≥ 100不处理或600-650回火14MnNb>40 ≥ 100不处理或600-650回火15MnV≤32不预热不处理或560-590,630-650回火15MnTi>32≥ 100不处理或560-590,630-650回火14MnMoNb>32≥ 100不处理或560-590,630-650回火15MnVN≤3215MnVTiRE>32>10018MnMoVNb≥ 150600-650回火14MnMoV≥ 150600-650回火14MnMoVB≥ 150━━━━━━━━━━━━━━━━━━━━━━━━━━在气温较低、焊接件厚度较大的情况下焊接的普通低合金结构,应按表2的规定预热.表2 :━━━━━━━━━━━━━━━━━━━━━━━━━━钢板厚度,mm焊接气温, ℃预热温度, ℃──────────────────────────≤16-10以下100-15016-24-5以下100-15024-400以下任何温度>400以下任何温度━━━━━━━━━━━━━━━━━━━━━━━━━━6.有密闭内腔的焊接件,在热处理之前,应在中间隔板上适当的位置加工Φ10mm孔,使其空腔与外界相通.需在外壁上钻孔的, 在热处理后要重新堵上.7.焊缝射线探伤应符合GB3323-82的规定.要进行力学性能试验的焊接,应在图样或订货技术要求中注明.焊缝的力学性能试验种类、试样尺寸按GB2649-81-GB2656-81的规定,试样板焊后与工件经过相同的热处理,并事选经过外观无损探伤检查. 8.焊件要进行密封性检验和耐压试验时,应按本标准要求进行.对耐压试验有要求时, 应在图样或订货要求中注明试验压力和试压时间.常用材料的相对加工性(JB/ZQ4011-84)━━━━━━━━━━━━━━━━━━钢种材料代号相对加工性──────────────────优质20170碳素35131钢451005577合35SiMn54金42SiMn54结38SiMnMo65构38CrMoAlA45钢60SiMnMo5437SiMn2MoV4420MnMo9718MnMoNb7420Cr10520CrMnMo2720CrMn2Mo3840Cr10050Cr8035CrMo7340CrSi5438CrSiMnMo5435Cr2MnMo44轧辊60CrMnMo44钢60CrMOV44弹65Mn50 簧60Cr2MoW33钢50CrVA44碳素T773工T873 具T1073 钢T1262合4CrW2Si73金Cr12MoV62 工CrWMn62 具5CrMnMo62 钢GCr1573GCr15SiMn73W18Cr4V47不2Cr13100 锈3Cr1377 钢1Cr18Ni9Ti62碳素ZG230-450144铸ZG270-500144钢ZG310-570118合ZG35SiMn100金ZG35CrMnSi100铸ZG35CrMo100 钢ZGMn13118ZGCr22Ni2N100灰HT15083 铸HT20065铁HT25052HT30045铸ZQSn6-6-3造ZQSn10-1181有ZQA19-4181色ZHA166-6-3-2 181合ZHMn58-2-2307金ZL104551ZL203551硬度換算公式:1.蕭氏硬度(HS)=勃式硬度(BHN)/10+122.蕭式硬度(HS)=洛式硬度(HRC)+153.勃式硬度(BHN)= 洛克式硬度(HV)4.洛式硬度(HRC)= 勃式硬度(BHN)/10-3硬度測定範圍:HS<100HB<500HRC<70HV<1300。
- 1、下载文档前请自行甄别文档内容的完整性,平台不提供额外的编辑、内容补充、找答案等附加服务。
- 2、"仅部分预览"的文档,不可在线预览部分如存在完整性等问题,可反馈申请退款(可完整预览的文档不适用该条件!)。
- 3、如文档侵犯您的权益,请联系客服反馈,我们会尽快为您处理(人工客服工作时间:9:00-18:30)。
装配工艺的三个基本条件
装配工艺的三个基本条件是:装配精度、配合精度和组装技术。
1.装配精度:指组件或产品在装配过程中需要达到的精度要求,
包括尺寸精度、形状精度、位置精度等。
装配精度直接影响着组件或产品的性能、稳定性和可靠性。
2.配合精度:指组件或产品中各个零部件之间的配合关系,包括
间隙、过盈、过渡配合等。
配合精度直接关系到组件或产品的稳定性、可靠性和性能。
3.组装技术:指将组件或产品中的各个零部件进行组装和连接的
技术,包括机械连接、焊接、胶接、压接等。
不同的组装技术对组件或产品的性能、稳定性和可靠性有着不同的影响。