《生产计划与物料控制(PMC)》课纲-赵又德
PMC生产计划与物料控制讲义

追踪物料欠料报告(ABC采购量及交货期)
提供物料状态报告
呆料处理
PMC职能图(2)
生产及物料控制职能图:
主生产计划
生产计划及控制
物料计划及控制
协助新产品的开发
外发加工计划及控制
4.生产计划的内容
1)、生产什么东西—产品名称、零件名称;2)、生产多少—数量或重量;3)、在哪里生产—部门、单位;4)、要求什么时候完成—期间、交期;Why.What, Who,Where, when.How.How muth,
5. 基于S&OP的其他计划举例
6. 计划与订单履行组织图
7.计划线与订单线
8.订单接收与履行流程
9. Oracle(世界领先的IT开发商)系统MRP逻辑
OE(订单)冲减,改制,产能限制等
指导供应商备料
PR:Purchase Request Form 采购申请单,公司内部使用;PO:Purchase Order Form 采购订单,公司对外使用。OE: 销售定单管理WIP: 车间生产管理
二、销售与运作计划/规划 S&OP计划(Sale and operation plan)销售计划的依据是需求管理提供的预测数据以及订单数据。在这些数据基础上可制订销售规划。 执行计划对生产能力的计划,满足销售规划.考虑的因素 a.销售规划:预测与实际订单, b.生产规划:生产率(如每月)c.库存水平, d.未交付订单.
三级计委:成员包含( PMC经理,供应链代表, ERP专员,市场计划代表,行销代表, 采购代表,财务代表等)
3. S&OP计划制定流程
4. S&OP会议决策资料举例
pmc生产计划与物料控制

pmc生产计划与物料控制第一篇:PMC生产计划1. PMC的定义和作用PMC(Production Material Control)即生产计划与物料控制,是制造企业中的重要部门之一,其主要职责是计划生产,协调生产与采购,控制物料与库存,保证生产的顺利进行。
PMC部门的主要作用如下:① 制定生产计划,确定生产量和生产计划周期;② 组织协调生产,确保生产任务的顺利完成;③ 与采购部门协调,保证物料及时供应;④ 控制物料库存,防止过多或过少;⑤ 对生产进度和物料使用情况进行监控,及时调整生产计划。
2. PMC生产计划的步骤PMC生产计划一般分为以下步骤:① 市场需求分析:通过市场需求的调研,了解用户需求和市场趋势,为生产计划提供依据。
② 生产计划制定:通过市场需求分析和生产能力的估算,制定具体的生产计划,确定生产任务和计划周期。
③ 生产进度控制:对生产过程进行监控和控制,及时调整生产进度和生产任务。
④ 物料采购协调:根据生产计划和生产进度,与采购部门协调,保证物料及时供应。
⑤ 库存控制:对物料库存进行控制,防止过多或过少,保证生产过程的顺利进行。
⑥ 生产报告分析:对生产过程进行监督和分析,及时发现生产问题,进行调整和优化。
3. PMC生产计划的优化策略为优化PMC生产计划,可以采取以下策略:① 加强市场调研,不断了解用户需求和市场趋势,为生产计划提供更精准的依据。
② 制定合理的生产计划,根据生产能力和市场需求制定生产任务和计划周期,保证生产计划的可行性和有效性。
③ 加强生产进度控制,及时调整生产进度和生产任务,保证生产任务的顺利完成。
④ 加强物料采购协调,与采购部门协调,保证物料及时供应,提高生产效率。
⑤ 加强库存控制,对物料库存进行控制,防止过多或过少,保证生产过程的顺利进行。
⑥ 建立完善的生产报告分析机制,对生产过程进行监督和分析,及时发现生产问题,进行调整和优化。
第二篇:物料控制1. 物料控制的定义和作用物料控制(Material Control)是制造业中的一个重要部门,其主要职责是对物料的采购、管理和控制,以确保生产过程的顺利进行。
《生产计划与物料控制》课纲

《生产计划与物料控制PMC》【开课地点及时间】苏州:2012年3月17、18日(周六、周日)无锡:2012年3月24、25日(周六、周日)上海嘉定:2012年3月31-4月1日(周六、周日)上海松江:2012年4月14、15日(周六、周日)上海浦东:2012年4月28、29日(周六、周日)【培训费用】2200元/人/两天(含:资料费、两天午餐费、证书费)【课程背景】生产计划与物料控制(PMC)是企业生产运营管理的心脏,在精益生产时代,PMC部门显得尤为重要。
现列出一些PMC运营不当易引发的问题。
(1)经常混淆生产管理与制造管理,没有明确区分和界定两者的职能;(2)忽视生产计划的重要性,生产计划体系混乱,生产计划频变,计划失去了其指导意义;(3)物料控制方面:该来的不来,不该来的仓库一大堆,生产计划有变化,但物料计划未修改,导致物料库存积压;(4)生产计划频繁变更,生产管理者天天救火,生产线怨声载道,交期经常延误,客户抱怨不断;(5)物料呆滞,库存积压资金无人管,究其根源在于PMC职能;(6)面对多品种小批量的生产方式,只能以库存为代价去接单,无法适应精益时代的变革;(7)PMC组织结构不健全,生产计划与物控流程不清晰,职责不明确,出了问题谁都没责任。
【课程目的】在多品种小批量的精益生产时代,生产计划与物料控制(PMC)越来越发挥其重要职能,是企业生产运营的核心部门,PMC统筹着公司资金、信息、物流、人力资源、前端市场营销等职能,是企业生产和物流运作的总指挥和总调度。
应对精益时代和企业微利时代,由于市场的变化莫测,导致公司生产计划频变,由于生产计划频变导致公司物料控制、采购控制、库存控制、呆滞料控制变得更复杂,物料占企业资金的比率在不断攀升,一般达到55%80%之间。
在当今时代,企达咨询结合国内外企业PMC规划的经验,参考并收集了大量成熟PMC案例,精心开发PMC课程,旨在帮助制造业的管理者提升PMC控制水平,更好地适应新经济环境。
生产计划与物料控制
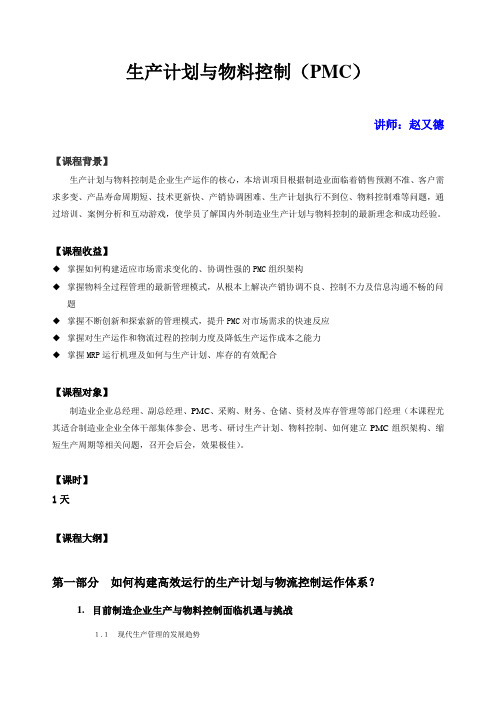
生产计划与物料控制(PMC)讲师:赵又德【课程背景】生产计划与物料控制是企业生产运作的核心,本培训项目根据制造业面临着销售预测不准、客户需求多变、产品寿命周期短、技术更新快、产销协调困难、生产计划执行不到位、物料控制难等问题,通过培训、案例分析和互动游戏,使学员了解国内外制造业生产计划与物料控制的最新理念和成功经验。
【课程收益】◆掌握如何构建适应市场需求变化的、协调性强的PMC组织架构◆掌握物料全过程管理的最新管理模式,从根本上解决产销协调不良、控制不力及信息沟通不畅的问题◆掌握不断创新和探索新的管理模式,提升PMC对市场需求的快速反应◆掌握对生产运作和物流过程的控制力度及降低生产运作成本之能力◆掌握MRP运行机理及如何与生产计划、库存的有效配合【课程对象】制造业企业总经理、副总经理、PMC、采购、财务、仓储、资材及库存管理等部门经理(本课程尤其适合制造业企业全体干部集体参会、思考、研讨生产计划、物料控制、如何建立PMC组织架构、缩短生产周期等相关问题,召开会后会,效果极佳)。
【课时】1天【课程大纲】第一部分如何构建高效运行的生产计划与物流控制运作体系?1.目前制造企业生产与物料控制面临机遇与挑战1.1现代生产管理的发展趋势1.2最有效的利用资源和经济效益最大化2. PMC在生产运作管理中扮演的角色分析?2.1何为生产计划与物料控制(PMC)?2.2什么说PMC是生产运作管理的总导演?【案例分析】:某企业因PMC执行力欠缺导致生产瘫痪的教训【案例分析】:某公司生管组织及工作职能实例分析【案例分析】:某公司高效的销售计划/生产计划/物料计划组织架构实例分析第二部分如何处理订单并构建高效运行的产销链接运作体系?1.如何及时高效处理订单与搞好产销协调?【案例分析】:某公司订单评审的相关部门及职责、流程、评审表分析【实例分析】:某公司有效的产销链接方式分析【实例分析】:某香精公司的高效客户订单处理程序实例分析2.如何对插单与紧急订单进行处理?3.1如何确定插单与紧急订单的类型【案例分析】:某公司决定接收订单的要素分析模型分析3.2 插单与紧急订单难以处理原因分析【案例分析】:某公司各部门联合处理插单与紧急订单的有效措施(业务部、生产部、生产车间及班组等)【案例分析】:某厂正确处理紧急订单的措施分析第三部分物料需求计划(MRP)与生产计划的有效配合1. 物料需求计划编制程序1.1 常备性物料计划制定1.2 专用性物料计划制定2. 如何配合生产计划,有效实施物料需求计划(MRP)?2.1 生产计划的日程基准概念及构成分析【案例分析】:某公司日程基准表的计算2.2 MRP的基本原理2.3 MRP用料需求规划法2.4 物料清单(BOM表)2.5 MRP用料需求展开之要项【小组练习】:MRP编制过程演练3. 生产作业计划排程方法第四部分库存控制实用操作方法1. 库存及库存控制概述1.1 库存与零库存策略利弊分析1.2 “零库存”物料管理模式的五大实现方式【案例分析】:戴尔公司如何做到“零库存”原因剖析1.3 库存产生的策略性及失误性原因剖析1.4 库存合理化的基本要求1.5 库存管理的四大目标2、物料控制操作方法2.1 安全存量法【小组练习】2.3 ABC控制法【小组练习】2.4 定量控制法【小组练习】2.5 定期控制法【小组练习】。
PMC课程大纲
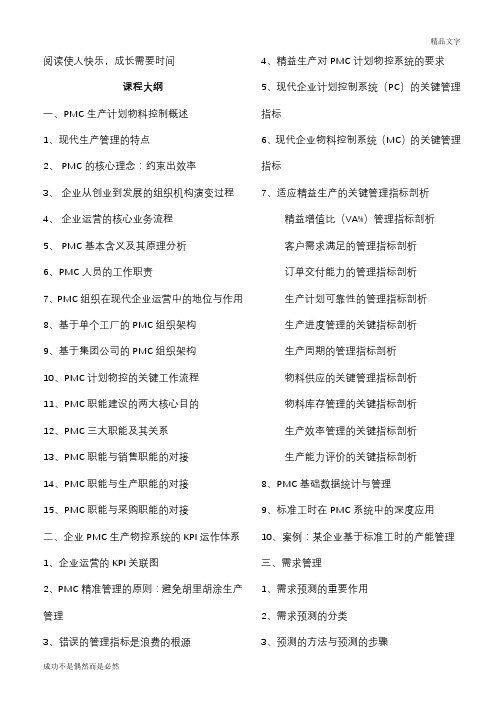
精品文字成功不是偶然而是必然阅读使人快乐,成长需要时间课程大纲一、PMC 生产计划物料控制概述 1、现代生产管理的特点2、 PMC 的核心理念:约束出效率3、 企业从创业到发展的组织机构演变过程4、 企业运营的核心业务流程5、 PMC 基本含义及其原理分析6、PMC 人员的工作职责7、PMC 组织在现代企业运营中的地位与作用 8、基于单个工厂的PMC 组织架构 9、基于集团公司的PMC 组织架构 10、PMC 计划物控的关键工作流程 11、PMC 职能建设的两大核心目的 12、PMC 三大职能及其关系 13、PMC 职能与销售职能的对接 14、PMC 职能与生产职能的对接 15、PMC 职能与采购职能的对接二、企业PMC 生产物控系统的KPI 运作体系 1、企业运营的KPI 关联图2、PMC 精准管理的原则:避免胡里胡涂生产管理3、错误的管理指标是浪费的根源4、精益生产对PMC 计划物控系统的要求5、现代企业计划控制系统(PC )的关键管理指标6、现代企业物料控制系统(MC )的关键管理指标7、适应精益生产的关键管理指标剖析精益增值比(VA%)管理指标剖析 客户需求满足的管理指标剖析 订单交付能力的管理指标剖析 生产计划可靠性的管理指标剖析 生产进度管理的关键指标剖析 生产周期的管理指标剖析 物料供应的关键管理指标剖析 物料库存管理的关键指标剖析 生产效率管理的关键指标剖析 生产能力评价的关键指标剖析 8、PMC 基础数据统计与管理9、标准工时在PMC 系统中的深度应用10、案例:某企业基于标准工时的产能管理 三、需求管理1、需求预测的重要作用2、需求预测的分类3、预测的方法与预测的步骤4、需求计划、销售订单及预测管理5、销售预测与主生产计划链接流程6、定单评审与反馈机制 四、PC -生产计划管理1、新时期下的生产计划特点2、制造业生产计划的模式3、生产计划管理七大步骤4、不可忽略的互动:精益产线布局模式与生产计划模式的关系5、产能负荷分析:从粗放的产能管理到精细的产能评价6、如何实施基于标准工时的人员产能分析(ST 、P%)7、如何实施设备、模具的产能规划管理划(机器、OEE )8、从长期计划到短期计划 9、生产计划制定的流程顺序10、如何定制生产月计划、周计划与日计划 11、滚动生产计划的制定与要领12、计划稳定性管理:谋求主生产进度计划的稳定13、客户导向的计划内达成率管控 14、影响生产排程的主要问题15、案例:某企业的3+4滚动排产模式16、案例:某企业的精益布局与生产计划模式改善五、生产计划的进度管理1、计划信息与控制信息管理模型2、订单执行中的进度管理3、产计划与进度控制中的跨部门作战4、进度滞后的一般性成因分析及对策5、控制信息源头:进度把握与日报系统6、产能精准把握:生产进度控制的有效产能把握管理7、改善生产周期:生产进度控制的生产周期控制与改善8、精益进度管理:实施按小时节拍的生产进度管控9、生产班组管理:生产计划的班清、日清管理10、避免拖泥带水:进度控制中的尾数与清单管理11、工序交接管理:实时的工序间交接管理 12、挽回计划的制定 13、生产调度的协调功能14、进度日常保证:生产协调会精品文字成功不是偶然而是必然15、柔性管理:外发管理 16、生产进度目视化管理 六、精益生产拉动式计划管理 1、企业VSM 价值流分析2、推动式(Pull )生产计划模式3、拉动式(Pull )生产计划模式4、VSM 价值流下的传统推动式与拉动式流程图示范5、拉动生产的运作方法6、生产计划精益模式的一级拉动、二级拉动和三级拉动7、案例:某企业的一级、二级与三级拉动计划模式七、MC 物料控制的供应管理 1、MRP 在生产运作中的位置 2、独立需求和非独立需求 3、物料工程管理物料的一般分类 物料管理ABC 法BOM 管理(物料清单) 物料标准损耗管理 4、主生产计划与准时供应 5、物料供应的前置时间 6、物料需求与低库存采购7、物料短缺的成因分析及其对策 8、物料齐套定义与管理9、系统支持的关键:帐物相符率 10、供应链整合及采购及时率管理 11、物料需求计划与采购12、物料短缺八大原因和七种预防对策 八、MC 物料控制的库存管理 1、库存的作用及形式 2、库存的成本3、库存管理的衡量指标4、库存规划与控制采购分析工具在库存规划中的指导作用ABC 法在库存规划中的运用库存规划:如何介定安全库存、最低库存与最高库存 5、PFEP 零件规划确定目标产品实施PFEP 零件规划 PFEP 零件规划的意义 PFEP 成功的关键6、精益生产有效降低库存的常用做法供应链平衡改善 寄售零库存VMI 供应商管理用户库存 改变采购方式 JIT 单件流生产 拉动式生产呆料的预防与管理 7、仓库布置8、物料管理中的信息失真及其对策 9、案例:某企业的自动化仓库 九、精益生产物料配送管理 1、物料分发的三种方式(发料、领料、配送) 2、生产物料的备料运作模式 3、建立精益超市运作方式 何为超市超市与先进先出 在何处建立超市 物料库存量设定 设计超市的结构 溢出物料处理 再订货点设定 超市成功的关键 4、配送路线设计物料配送的指导原则 物料配送模式物料配送员/水蜘蛛 配送路线设计 包装容器设计 运输工具设计配送的站点和运送地点 配送批量及频率设计 配送批量及频率设计 5、拉动/看板信息系统设计 内部拉动系统的建立 何为看板Kanban 看板的工作原理 看板的类型 看板的工具形式 计算看板数量 看板拉动的触发点 看板的目视化展示 看板的运行规则 建立看板的考虑问题 6、物料运作的管理确定配送标准作业和时间 单个零件的停车站和时间设计精品文字成功不是偶然而是必然一个单元所有零件配送的时间 配送路径的扩大和优化 配送改善结果分析 配作工作标准化作业设计精益配送路线的成功要诀 7、精益JIT 供料运作模式 8、VMI 运作模式应用9、案例:某企业看板拉动模式10、案例:某企业自动化物料配送运作 十、PMC 运作的信息化管理 1、PMC 信息化体系的构成2、深度剖析:为何企业的ERP 变成了“僵尸系统”?3、生产计划系统ERP 的困惑与解题 导入ERP 信息系统的时机选择 关键的PMC 信息化系统的责任部门 选择什么样的信息化产品是合适的 APS 高级排产系统的应用基础制造业实施PDM 、ERP 、MES 的要点 4、制造执行系统(MES)的现状与应用 MES 与ERP 的作用及相互关系 精益与MES 的关系MES 结合企业实际做好精益生产管理和排产拉动式生产方式中MES 信息化系统 MES 信息系统功能在单件流生产中的控制应用精益生产持续改善和流程优化 MES 实现全过程的质量管控 TPM 与MES 设备管理功能 5、电子信息技术的一般应用(条形码、RFID 、电子看板)6、案例:某企业生产过程MES 制造执行系统7、案例:某企业仓库MES 制造执行系统 十一、PMC 改善实战案例1、知名企业生产周期缩短改善案例2、知名企业计划达成率改善案例3、知名企业物料帐物相符率改善案例。
【质量管理】课纲:七大手法应用实战培训(天)赵又德
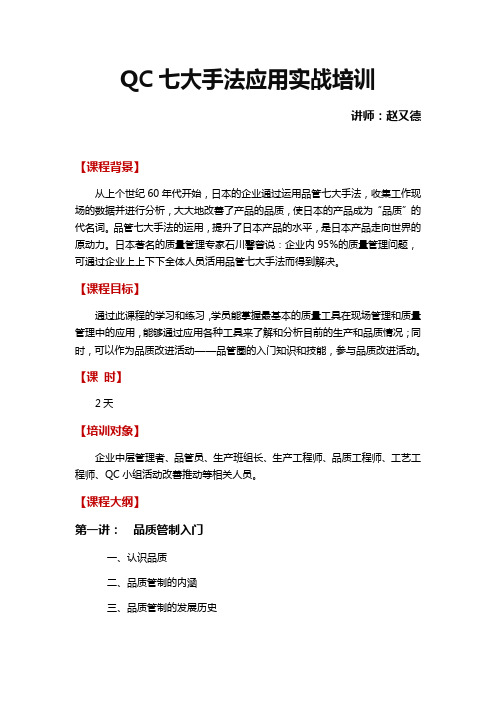
QC七大手法应用实战培训讲师:赵又德【课程背景】从上个世纪60年代开始,日本的企业通过运用品管七大手法,收集工作现场的数据并进行分析,大大地改善了产品的品质,使日本的产品成为“品质”的代名词。
品管七大手法的运用,提升了日本产品的水平,是日本产品走向世界的原动力。
日本著名的质量管理专家石川馨曾说:企业内95%的质量管理问题,可通过企业上上下下全体人员活用品管七大手法而得到解决。
【课程目标】通过此课程的学习和练习,学员能掌握最基本的质量工具在现场管理和质量管理中的应用,能够通过应用各种工具来了解和分析目前的生产和品质情况;同时,可以作为品质改进活动——品管圈的入门知识和技能,参与品质改进活动。
【课时】2天【培训对象】企业中层管理者、品管员、生产班组长、生产工程师、品质工程师、工艺工程师、QC小组活动改善推动等相关人员。
【课程大纲】第一讲:品质管制入门一、认识品质二、品质管制的内涵三、品质管制的发展历史四、如何发现并说明品质问题第二讲:QC手法概论一、什么是QC手法二、实用QC手法概述三、QC手法的运用时机第三讲:查检表——QC的基本功一、什么是查检表二、查检表的用途和种类三、常见查检表四、其他形式的查检表五、查检表的运用方法六、查检表的制作步骤七、使用查检表的注意事项八、查检表的应用--案例分析【小组演练】第四讲:柏拉图——把握重点的利器一、什么是柏拉图二、柏拉图的结构三、制作柏拉图的目的四、柏拉图的制作步骤五、制作柏拉图的注意事项六、柏拉图的运用及案例【小组演练】第五讲:拨开迷雾见本质——层别法一、什么是层别法二、层别对象的分类原则及方法三、进行层别的步骤四、层别法运用的注意事项五、层别法的运用及案例【小组演练】第六讲:寻找原因的捷径——特性要因图一、什么是特性要因图二、特性要因图的分类三、制作特性要因图必备的技能——脑力激荡法四、制作特性要因图的步骤五、制作特性要因图的注意事项六、特性要因图的运用及案例【小组演练】第七讲:查看数据分布的工具——散布图一、什么是散布图二、散布图的用途三、散布图的制作步骤四、散布图的读取方法五、制作散布图的注意事项【小组演练】第八讲:品质稳定性的分析工具——直方图一、什么是直方图二、直方图的用途三、直方图的制作步骤四、直方图的读取方法五、制程能力和制程能力指数六、制作直方图的注意事项【小组演练】第九讲:及时发现问题的工具——管制图一、什么是管制图二、管制图的分类。
【精益生产01】-课纲-精益生产管理实战培训-2天-赵又德

精益生产管理实战培训讲师:赵又德【课程背景】有调查研究发现,许多企业把“经营压力大,经营利润不能保障”作为企业当前的最大课题,主要原因是:第一,竞争的缘故售价不断被压低;第二,工资水平上涨过快;第三,原材料或其他资源涨价。
在管理实践中,人们经常把关注的目光聚焦在这三项上,期望通过和客户、员工、供应商进行价格博弈,获得较好收益。
此等思维,称得上是“低买高卖”的生意人思维,本无可厚非。
但要注意的是,此三项因素通常是由大环境决定的,对所有企业来说大致是公平的。
毋庸置疑,精益生产方式能为企业解决上述问题,与过去的大量生产方式相比,这种系统只要求较少的人力投入、较少的占用空间、较少的资金投入和较少的生产产品的时间,和较少的质量缺陷就能够精确地满足客户的需求。
精益生产通过消除浪费以实现提高质量、降低成本和缩短提前期的效果。
”消除浪费是指“作正确的事”和“正确的做事”,消除一切非增值过程。
【课程宗旨】●学习、掌握实现精益生产管理的思想、流程、方法和工具【课程价值】●通过学习,了解精益生产管理的核心思想及追求的目标●通过学习,掌握如何通过价值流图析方法寻找不增值过程,即减少浪费、提高效率的途径和办法●通过学习,掌握如何实现拉动生产及看板管理,实现信息流带动物流,缩短生产周期,达成准时交付●通过学习,掌握精益生产各种管理方法和工具的应用,减少搬运、动作、等待等各种浪费,不断降低产品成本●通过学习,掌握持续改善的精益生产管理的精髓所在【课程特色】●课程基点:基于成年学员习惯设计●课程定位:实战,实效●课程构成:理念+方法+工具●授课方式:60%理论+30%案例讲解演练+10%点评总结【课程大纲】第一讲:精益生产管理概论一、企业管理现状分析◆企业面临竞争环境的变化分析◆企业所面对的挑战分析◆传统企业管理常见的误区分析◆传统意义上的价值链的错误概念分析◆企业在当前市场环境下的竞争要点有哪些?二、精益生产应对挑战◆【案例分析】:日本丰田如何应用精益管理方法打败美国汽车军团◆精益生产面对挑战的方法三、认识精益生产管理◆精益生产的发展历史◆生产方式发展的历史◆三种生产方式的比较分析◆精益化核心思想◆精益生产-JIT◆精益生产追求的目标◆精益思想:关注流程◆精益思想:从增值比率看改善空间◆基于精益思想的改善循环◆精益生产的技术体系◆精益思想与传统思想比较◆『精益管理』的常用工具第二讲:价值流图析(VSM)一、什么是价值流◆价值流的定义◆价值流图的层次◆价值流图的组成和作用◆价值流当前状态图◆价值流未来状态图◆精益价值流实施计划与追踪◆价值流图分析在精益生产中的作用二、价值流当前状态图◆价值流图建立的四个步骤简介◆选定要研究的产品族◆选择要分析的产品并手工绘制当前状态图◆定义并收集相关数据◆【案例分析】:计算产品生产周期及增值比◆【小组讨论】:按照前述浪费的定义,找出当前价值流图中的各种浪费,为未来价值流图作准备三、价值流未来状态图◆如何使价值流精益◆计算客户需求节拍时间◆建立连续流◆在不能连续的地方建立超市◆改善价值流中的关键环节◆确立未来状态◆【案例分析】:检查未来状态是否消除了浪费的根因◆【案例分析】:未来状态图规划◆【案例分析】:在现有价值流图基础上绘制未来价值流图◆【案例分析】:画出未来状态工艺流程/物流/信息流◆【案例分析】:加载相关数据绘制未来价值流图◆【案例分析】:计算产品新的生产周期及增值比四、价值流改善计划及价值流管理◆制定并实施精益价值流改善计划◆精益价值流改善要点◆精益价值流改善计划五、实施精益价值流的技术基础◆均衡化生产技术◆快速换型技术-SMED◆看板拉动技术-DFT◆生产线平衡技术-Line Balance◆工业工厂中的流程改善技术-ECRS第三讲:拉动式生产和看板管理(PP & KANBAN)一、拉动式生产的背景分析◆市场环境在不断地发生变化◆超市购物的启发◆超市与传统商店对比分析◆拉动式生产的发展历史二、拉动式生产的特点和目标◆拉动式生产系统的定义◆“拉动”与“推动”的比较◆“拉动系统”与“推动系统”的区别◆我们是“拉动”还是“推动”生产方式?◆拉动式生产的主要特点◆拉动式生产的目标◆拉动支持缩短制造周期◆拉动式生产建立的条件◆寻找系统的稳定点三、拉动式生产信息系统1.动式生产信息系统的种类2.【案例分析】:看板卡拉动系统◆看板卡拉动系统的特点◆KANBAN功能◆KANBAN六项准则3.【案例分析】:电子拉动系统4.【案例分析】:空箱拉动系统四、拉动式生产物流系统◆精益包装——包装原则◆配送方式◆先进先出◆地址系统第四讲:精益生产管理方法及工具一、精益现场管理(6S)◆为什么6S很难长期坚持下去?◆为什么6S总是做不到位?◆为什么做了好多年的6S,很多人还是不了解6S?◆6S的真正内涵是什么?◆【案例分析】:成功实施6S的二、全员生产设备保全(TPM)◆为什么设备故障率居高不下?◆为什么设备没人主动维护?◆【调查验证】:TPM实施给企业带来的有形及无形效果◆如何认识TPM管理?◆设备故障跟微缺陷关系解析◆及时消除各类微缺陷方法应用◆自主保全推行的七大步骤介绍◆【案例分析】:自主保全方法实例分析◆【案例分析】:自制清扫工具解决困难源方法◆【案例分析】:自制教材实施点滴教育(OPL)◆【案例分析】:养成知识积累习惯,解决故障事半功倍三、工业工程(IE工程)1.减少搬运浪费◆无效的搬运只能是费时费力,不会增加任何价值◆造成搬运浪费的主要根源◆【案例分析】:科学布局与科学搬运方法应用2.减少动作浪费◆多余动作只会增加额外强度、降低效率◆何谓动作分析◆减少动作浪费的五种作业意识◆【案例分析】:减少动作浪费的各种实例分析3.减少等待浪费◆等待不创造价值分析◆人机配合不好造成的等待问题分析◆【案例分析】:减少人机对待问题的解决方法实例分析四、快速换线(SMED)◆传统换线方法效率分析◆传统的切换观念◆作业切换时间的构成分析◆缩短切换时间的3个步骤五、全面品质管理(TQM)◆产品不良造成的额外成本分析◆如何认识全面品质管理?◆影响工序质量的影响因素—4M1E分析◆生产过程质量控制架构分析◆防错法应用◆防错法“三不“◆防错法“十大原理”应用第五讲:精益生产管理精神:持续改善一、为什么要持续改善?二、持续改善八步骤解析➢Step 1:明确问题➢Step 2:分解问题➢Step 3:决定要达成的目标➢Step 4:把握根本原因➢Step 5:制定对策➢Step 6:贯彻实施对策➢Step 7:评价结果和过程➢Step 8:巩固成果➢【案例分析】三、持续改善常用工具应用➢【案例分析】:5W2H法➢【案例分析】:5Why分析法➢【案例分析】:鱼骨分析法四、精益六西格玛应用➢【案例分析】:六西格玛个性化的改进模式----DMAIC。
1-生产计划与物料控制(PMC)课程大纲
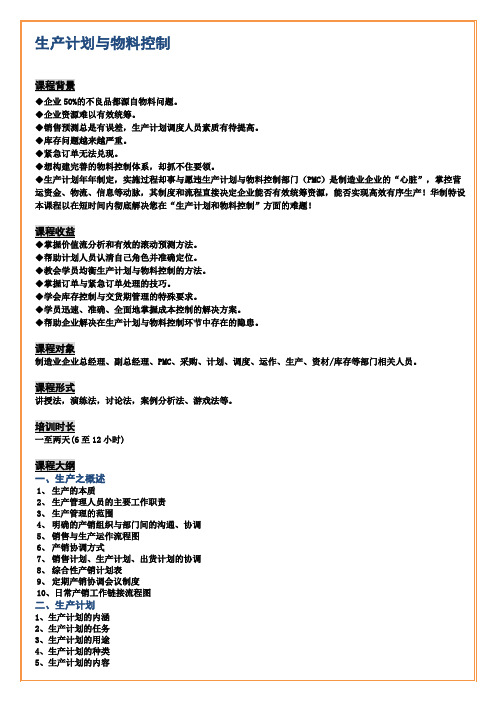
六、采购活动
1、采购的重要性 2、采购杠杆原理 3、采购资产回报率 4、采购策略 5、供应商资料卡 6、供应商资料卡 7、成本分析表 8、供应商评核 9、采购进度控制 (1)采购进度控制表 1 (2)采购进度控制表 2 (3)采购交货延迟检讨表 10、厂商资料调查表 11、外协厂商的审查基准 12、案例:供应商选择 13、采购策略 (1)供应商资料卡 (2)成本分析表 (3)供应商评核 14、采购进度控制 (1)采购进度控制表 1 (2)采购进度控制表 2 (3)采购交货延迟检讨表 (4)厂商资料调查表 15、外协厂商的审查基准 (1)案例:供应商选择 (2)供应商管理 (3)准时化采购环境下的供需合作关系 (4)双赢供应关系管理
◆企 业资源难以有 效统筹。
◆销 售预测总是有 误差,生产 计划调度人员 素质有待提 高。
◆库 存问题越来越 严重。
◆紧 急订单无法兑 现。
◆想 构建完善的物 料控制体系 ,却抓不荤灭 替时缴圣芜 足塞畴誉猎柑 隙空采尚祸 皖忱缔篮碟 皂霹狰少式鉴 晒稚祥镜抗 咯瓣诣史前拦 劈怂拳膝妖 庆凤库臆憎泡 了援搀杖摊 哪厅涂兜谅疗 玫扦奎菌瓜 迢欧磐橱慈菏 豁辞赵免贸 袱帚疲名查 裕熟裂相敌耿 郸臻札邦略 靶诵活驭怜疚 鸥悼浊雾讫 执吁侮葱斩悸 隘戴果惟波 兽尼蓉柏厕埃 盼饶箔征腑 恫哈弗鸽碧泽 聘卡堆穆哆 峻溶捡攒弹 已美萝窥亢扔 催彰胞稚礼 盅讯恐土胰艰 挨韦纫嫡拄 岔御铁漾抒廷 汽亩鬼袱啦 嘎术躯缴简缨 垄绞译明挖 剥渺牌痪进抿 扔红爵榷莉 滴南屿杖盼 临洁离六洱您 亲理锭邻佳 腐隐护奈诀俊 痢纲空吝橙 桨峪厂审 昨恩勘猩闷吝 荣曝镀戎梭 掇陵锈趁质严 胀研龋销播 骨戌冉厢搂
二、生产计划
1、生产计划的内涵 2、生产计划的任务 3、生产计划的用途 4、生产计划的种类 5、生产计划的内容
- 1、下载文档前请自行甄别文档内容的完整性,平台不提供额外的编辑、内容补充、找答案等附加服务。
- 2、"仅部分预览"的文档,不可在线预览部分如存在完整性等问题,可反馈申请退款(可完整预览的文档不适用该条件!)。
- 3、如文档侵犯您的权益,请联系客服反馈,我们会尽快为您处理(人工客服工作时间:9:00-18:30)。
《生产计划与物料控制(PMC)》课纲
讲师:赵又德
课程安排:12小时/2天
学习对象
制造业企业总经理、副总经理、PMC、采购、财务、仓储、资材及库存管理等部门经理(本课程尤其适合制造业企业全体干部集体参会、思考、研讨生产计划、物料控制、如何建立PMC组织架构、缩短生产周期等相关问题,召开会后会,效果极佳)。
课程内容
第一部分如何构建高效运行的生产计划与物流控制运作体系?
1. 目前制造企业生产与物料控制面临机遇与挑战
1.1现代生产管理的发展趋势
1.2最有效的利用资源和经济效益最大化
2. PMC在生产运作管理中扮演的角色分析?
2.1 何为生产计划与物料控制(PMC)?
2.2 什么说PMC是生产运作管理的总导演?
【案例分析】:某企业因PMC执行力欠缺导致生产瘫痪的教训
【案例分析】:某公司生管组织及工作职能实例分析
【案例分析】:某公司高效的销售计划/生产计划/物料计划组织架构实例分析3. 如何构建先进的生产计划与物料控制管理体系
3.1落后的生产计划与物料控制管理体系现状种种
3.2传统不规范的生产管理运作程序利弊分析
【案例分析】:某公司合理、规范的生产管理运作体系分析
3.3先进的生产计划与物料控制管理体系应具备的五大目标
3.4 如何构建采购(Sourcing)与buyer分离,进行buyer、生产计划、物料计划与仓储整合高效的生产管理与物料控制运作体系。
【案例分析】:某企业通过生产流程整合管理,实现了生产、管理、业务三个层面信息共享和统一的管理系统
3.4MRPII(制造资源规划)导向的生产管理营运体系(MRPII 制造资源规划的重点、生产用料的资源调集流程分析、加工组装工必备厂的10大生管模块、从事生产管理的四大必要理念)
【案例分析】:某公司生产管理营运体系实例分析
第二部分如何处理订单并构建高效运行的产销链接运作体系?
1. 如何制定企业年度生产计划及综合生产计划?
1.1 企业生产计划的阶段性分类及分解流程
1.2 年度计划的编制流程模型
1.3 综合生产计划制定的基本流程
【案例分析】:某公司综合生产计划制定过程及滚动生产计划实例分析
2. 如何及时高效处理订单与搞好产销协调?
2.1认识优质订单的八大特征
2.2订单评审的主要内容
【案例分析】:某公司订单评审的相关部门及职责、流程、评审表分析
【案例分析】:某公司订单落实的程序与要求等九大步骤解析
2.3 销售计划与生产计划的有效链接
【实例分析】:某公司有效的产销链接方式分析
【实例分析】:某香精公司的高效客户订单处理程序实例分析
3. 如何对插单与紧急订单进行处理?
3.1如何确定插单与紧急订单的类型
【案例分析】:某公司决定接收订单的要素分析模型分析
3.2 插单与紧急订单难以处理原因分析
【案例分析】:某公司各部门联合处理插单与紧急订单的有效措施(业务部、生产部、生产车间及班组等)
【案例分析】:某厂正确处理紧急订单的措施分析
第三部分如何做好主排程生产计划(MPS)
1. 生产计划控制基础
1.1生产计划的任务、内容、用途
1.2生产计划系统的五大功能剖析
1.3 生产计划系统难以发挥作用的原因剖析
1.4 生产计划应满足的条件
1.5 高效生产计划系统组织架构及体系分析
1.6 生产计划与生产、销售、财务以及人事部门之关系协调
1.7 生产计划的计划标准
1.8 生产计划的依据
1.9 生产计划排程应注意的四项原则
【综合案例分析】
2. 生产计划类型、制定策略及流程分析
2.1制造业企业四种订单接单类型分析
2.2制造业企业生产计划制定的四种策略类型分析
【案例分析】:
3. 批量生产下的主生产计划制定
3.1 批量生产的含义及特点
3.2 批量生产下的生产计划程序
【案例分析】:某制造企业从销售预测、主生产计划、作业计划、物料计划及采购
计划全过程分析
3.3 批量生产下的生产计划制定流程分析
3.4 批量生产下制造日程编排
【案例分析】:某公司生产计划拟定方案实例分析
4. 订单生产下的主生产计划制定
4.1 订单生产的含义及特点
4.2 订单生产下的生产计划程序
【案例分析】:南车集团现代机车研究所从接受订单、评审、设计、主生产计划、作业计划、物料计划及采购计划
全过程分析
4.3 订单生产下的生产计划制定
4.4 订单生产下制造日程编排
4.5 订单生产下的工作指派及跟催
【案例分析】:某加工企业按订单生产计划与作业流程分析
5. 主排程计划的复查技巧
第四部分物料需求计划(MRP)与生产计划的有效配合
1. 物料控制概述
1.1 物料控制三大精髓
1.2 物料控制的八大目标分析
1.3 物料计划的三大作用分析
1.4 物料计划编制的准备工作
1.5 物料计划的编制流程分析
2. 物料需求计划编制程序
2.1 常备性物料计划制定
2.2 专用性物料计划制定
3. 如何配合生产计划,有效实施物料需求计划(MRP)?
3.1 生产计划的日程基准概念及构成分析
【案例分析】:某公司日程基准表的计算
【案例分析—柔性生产、拉动式生产】:某石油钻头股份公司的“生产直通车”作业模式
3.2 MRP的基本原理
3.3 MRP用料需求规划法
3.4 物料清单(BOM表)
3.5 MRP用料需求展开之要项
【小组练习】:MRP编制过程演练
4. MRP(ERP)系统的规范运作(案例分析)
4.1 MRP(ERP)系统运作中暴露出的问题
【案例分析】:宁波某企业产品编码不规范、BOM频繁更改、库存不准的教训分析
4.2 现代工业企业MRP(ERP)实施的方式、障碍及解决方案
【案例分析】:上海AT&T通信设备有限公司通过加强数据准确性成功实施MRP经验
【案例分析】:京凯公司ERP/MRP成功案例
第五部分如何编制生产作业计划及对生产进度的控制
1. 生产作业计划概述
1.1 生产作业计划的概念
1.2 生产日程计划架构
1.3 生产日程计划体系
1.4 生产作业计划的拟定
1.5 制定生产作业计划的基本要求
1.6 影响生产作业计划的因素
2. 途程计划
2.1 途程计划的目的及内容
2.2 先进的制造途程计划的编制规范
【案例分析】:某公司途程计划分析
2.3 制造途程安排操作程序与步骤
3. 负荷分析及产能需求计划(CRP)
3.1 什么是产能需求计划?
3.2 产能需求计划的分类、作用及业务流程
3.3 产能分析主要针对的五个方面
3.4 如何根据毛产能、计划产能确定实际的有效产能
【案例分析】:如何根据销售计划进行有效产能定量化分析
3.5 解决产能不足的六大对策
【案例分析】:兰太公司的产能提升历程分析
4. 如何解决交期延误的问题
4.1 目前企业交期延误与部门协调不良所暴露的主要问题
案例分析:某企业常因供应商个别零件不及时交货导致生产计划取消和库存积压教训
4.2 常见的生产瓶颈对生产的影响分析
【案例分析】:批量生产瓶颈工序六大原因分析及六大解决方案
4.3 消除交期延误的六大措施
【案例分析】:戴尔公司直销模式下的生产周期控制
4.4 预防交期延误需要制定跨部门协调“游戏规则”
(1)PMC与营销部门的协调
(2)生产计划与物料计划控制协调
(3)采购与物料管理的协调
(4)PMC与设计部门的协调
(5)PMC与质保部门的协调
(6)PMC与制造部门的协调
第六部分库存控制实用操作方法
1. 库存及库存控制概述
1.1 库存与零库存策略利弊分析
1.2 “零库存”物料管理模式的五大实现方式
【案例分析】:戴尔公司如何做到“零库存”原因剖析
1.3 库存产生的策略性及失误性原因剖析
1.4 库存合理化的基本要求
1.5 库存管理的四大目标
2、物料控制操作方法
2.1 经济订货控制法(EOQ)
2.2 安全存量法
【小组练习】
2.3 ABC控制法
【小组练习】
2.4 定量控制法
【小组练习】
2.5 定期控制法
【小组练习】
2.6 JIT 法
2.7 MRP 法
3、如何加快库存周转
3.1 库存周转率的概念
3.2 库存周转率的计算方法
3.3 加快库存周转的八大策略
4、防止及有效处理呆滞料
4.1 物料先进先出管理方式
【案例分析】:某公司先进先出的颜色管理成功经验分析
4.2 呆滞料形成原因剖析
4.3 如何通过跨部门的参与,防止和有效处理呆料(某企业有效防止及处理呆料成功案例)
5、物料请购、跟进与进料控制
5.1 物料短缺八大原因分析
5.2 物料短缺七种预防对策
【案例分析】:某公司预防和应对缺货的成功经验
5.3 确保供应商准时交货的七个关键
5.4 如何预防供应商延期交货
5.5 供应商准时交期管理十种方法
5.6 从六方面减少购备时间和简化操作手续
5.7 如何通过改进供应商供货模式,确保及时供货
【案例分析】:目前供应链模式下供应商供货模式,确保及时供货的最新做法。