轧机支撑辊与工作辊交叉产生轴向力分析(2)
万能轧机轧辊轴向窜动分析与控制
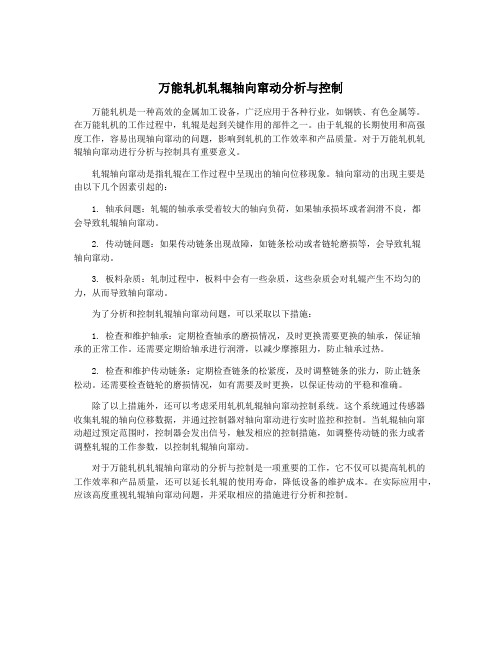
万能轧机轧辊轴向窜动分析与控制万能轧机是一种高效的金属加工设备,广泛应用于各种行业,如钢铁、有色金属等。
在万能轧机的工作过程中,轧辊是起到关键作用的部件之一。
由于轧辊的长期使用和高强度工作,容易出现轴向窜动的问题,影响到轧机的工作效率和产品质量。
对于万能轧机轧辊轴向窜动进行分析与控制具有重要意义。
轧辊轴向窜动是指轧辊在工作过程中呈现出的轴向位移现象。
轴向窜动的出现主要是由以下几个因素引起的:1. 轴承问题:轧辊的轴承承受着较大的轴向负荷,如果轴承损坏或者润滑不良,都会导致轧辊轴向窜动。
2. 传动链问题:如果传动链条出现故障,如链条松动或者链轮磨损等,会导致轧辊轴向窜动。
3. 板料杂质:轧制过程中,板料中会有一些杂质,这些杂质会对轧辊产生不均匀的力,从而导致轴向窜动。
为了分析和控制轧辊轴向窜动问题,可以采取以下措施:1. 检查和维护轴承:定期检查轴承的磨损情况,及时更换需要更换的轴承,保证轴承的正常工作。
还需要定期给轴承进行润滑,以减少摩擦阻力,防止轴承过热。
2. 检查和维护传动链条:定期检查链条的松紧度,及时调整链条的张力,防止链条松动。
还需要检查链轮的磨损情况,如有需要及时更换,以保证传动的平稳和准确。
除了以上措施外,还可以考虑采用轧机轧辊轴向窜动控制系统。
这个系统通过传感器收集轧辊的轴向位移数据,并通过控制器对轴向窜动进行实时监控和控制。
当轧辊轴向窜动超过预定范围时,控制器会发出信号,触发相应的控制措施,如调整传动链的张力或者调整轧辊的工作参数,以控制轧辊轴向窜动。
对于万能轧机轧辊轴向窜动的分析与控制是一项重要的工作,它不仅可以提高轧机的工作效率和产品质量,还可以延长轧辊的使用寿命,降低设备的维护成本。
在实际应用中,应该高度重视轧辊轴向窜动问题,并采取相应的措施进行分析和控制。
辊间轴向力分析

四辊可逆轧机轧辊轴向力分析由于工作辊是主动辊, 它带动支承辊转动。
因此若把工作辊表面的线速度沿支承辊的轴线和与轴线垂直的方向分解, 则所得的分量v b1必定等于支承辊表面的线速度v b, (假设两辊在沿着支承辊圆周的切线方向无滑动) 即:v b= v w cosa= v b1同时也得到了v w沿支承辊轴线的分量v wc 为v wc= v w sina。
上式表明, 两辊轴线的不平行使工作辊沿支承辊的轴线产生了相对滑动。
不难看出, 只要两辊的轴线不平行, 即a 角不为零, 相对滑动速度v wc就始终不为零。
尽管a 角很小,工作辊表面各质点与支承辊表面各质点沿轴向的相对滑动速度v wc仍不可忽视, 而这一滑动必将产生轴向滑动摩擦力, 换言之, 只要两辊的轴线不平行, 两辊间就有滑动摩擦力存在。
工作中, 辊系将受到轧制力P 的作用, 两辊的接触面是一条窄带,图1下辊系支撑辊和工作辊接触面速度分析在这条窄带上, 两辊沿支承辊的轴线有一个相对滑动速度v wc , 根据摩擦理论可知: 支承辊必定要给工作辊一个与v wc方向相反的滑动摩擦力的作用, 而它本身同时受到一个与v wc方向相同的滑动摩擦力的作用,两摩擦力在接触窄带上是以剪应力流的形式存在的。
当两辊轴线夹角不变而转动方向相反时则摩擦力反向,即随着轧件的往复轧制工作辊将做往复窜动,这种现象是与实际情况相符的。
轴向力及窜动距离大小计算。
假设轧制力为P,两辊夹角α,辊间压力为F,轧件长度l,锻钢与铸铁间摩擦系数f,工作辊轴向受力为X1,工作辊窜动距离为A。
F≈1.04P,X1=Ffcosα=1.04Pfcosα[设f=0.1,P=3000吨,夹角为0.1度,则F=1.04×3000×0.1×cos(0.1×3.14159÷180)=312吨] A=lsinαcosα[设l=25000mm,α=0.1度,则A=25000×sin(0.1×3.14159÷180)×cos(0.1×3.14159÷180)=43.6mm]从以上各式可知,轧件越长则窜动距离越远,轧制力越大窜动力越大,这是与实际情况相符的。
探究冷轧支撑辊和工作辊剥落机理及有效预防措施

探究冷轧支撑辊和工作辊剥落机理及有效预防措施摘要:轧辊是轧钢厂主要的消耗性生产工具,轧辊的质量会对轧机产能和效率的发挥以及轧制产品质量产生直接的影响。
基于此,本文对冷轧支撑辊的进行力学分析以并对其剥落机理的进行研究。
关键词:冷轧支撑辊;剥落;控制措施引言轧辊是轧钢生产的重要工具,价格非常昂贵,尤其是冷轧板带用的锻钢支撑辊及工作辊。
近年来,各轧钢厂为提高产量和减少换辊周期, 广泛使用价格更贵、硬度更高及淬硬层更深的高合金辊。
因此,减少轧辊的早期失效及降低生产成本显得日益重要。
在冷轧板带生产过程中,轧辊处于复杂且不断变化的应力状态。
轧制负荷引起的支撑辊与工作辊间的接触应力、带钢跑偏断带以及肋浪粘钢造成的机械及热冲击容易使轧辊损坏。
轧辊损坏的形式主要为剥落,因此,探究轧辊剥落机理以便早期发现裂纹和预防剥落是延长轧辊使用寿命的有效途径。
1、冷轧技术概述钢材是国民经济的各个领域中的十分重要的材料,它被广泛应用于机械工程、电机工程、建筑、金属制品、汽车、运输、家用器具等各个行业。
2004年以来,全球对钢材的需求量除了在经受金融危机时出现负增长以外均保持持续增长状态。
2009年全球范围内粗钢产量11.65亿吨,中国达到5.68吨,中国在全球钢材市场上的产量及消费量表现出强劲的态势。
冷轧是指金属进行礼制变形时的温度在再结晶温度以下,实际一般是指带钢在室温下进行轧制加工而不加热。
利用冷轧技术生产的带材和钢板精确度高,而且性能优良,其主要特点为轧制温度低,可以获得精确的尺寸和均匀的厚度,可以获得很薄的带材,这是热轧技术无法做到的;冷轧产品具有很好的力学性能和工艺性能,可以获得优越的表面质量,可以避免热轧生产的带钢具有的缺陷,并且可以控制带钢的表面粗糙度,以满足不同的用户需求,也可以满足下一道工序的加工需求;并且可实现高速轧制,具有很高的生产效率。
2、冷轧支撑辊轴承的力学分析2.1、轴承的失效形式轴承的常火效形式命内的疲破坏命期外的失效,其中寿命内的疲劳点蚀、剥落、塑性变形、磨损与胶合。
中厚板轧机辊道受力情况模拟分析探讨

在模 型建 立 过程 中考虑 生 产实 际 ,辊道 、轧 件 均 作 为 弹性 体 ,采 用 八 节 点 六 面 体 实 体 单 元 Sl 6 进行 建模 ,分4 o d14 i 种情 况对 轧件 冲击 辊道 的 过程 进行 模 拟分 析 。第 1 情 况 :轧件 已经轧 出 , 种 无弯 曲 .轧 件支撑 在 工作 辊 与第 二机 架 辊上 ,与 辊 道接 触 。第 2 情 况 :轧件 已经 轧 出 ,头 部 向 种 下 弯 曲7 m,轧 件支 撑 在 工 作辊 与 第 二 机架 辊 0m
摘 要 :辊 道 是 中厚 板 生 产 中不 可 缺 少 的部 件 ,T作 环 境 恶 劣 ,尤 其 是 机 前机 后 辊 道 ,除热 辐 射 外 还有 氧 化铁 皮 及 油 水侵 蚀 ,并 且 承受 很 大 冲 击 。用 有 限元 软件 模 拟 计算 了辊 道 在 冲击 载 荷 作 用下 的等 效应
h a n ft e sa o b ol d a d t e c u e o e h a e d n .T e at l ie e e a rp s l t e d e d o h l b t e r l n h a s ft e d b n i g h ri e gv s s v r lp o o as o e h c
95 6 40 3 0 5 5 0 2 5 l 5 7l 20 40 07 .5 15 .
成 加热 炉 、轧制设 备 以及 其它 辅 助设 备之 间的 钢
板 传递 。中厚板 生产 线上 机前 机 后辊 道还 有 转 钢
功 能 ,用于 横轧 过程 的转 钢 。这 部分 辊道 有 三种 形 式 :圆柱形 、阶梯形 和 锥形 。 工作 环境 都 比较 恶 劣 ,需 要频 繁正 反转 ,又承 受很 大 冲击 、热辐 射 ,还有 氧化 铁皮 及 油水 侵蚀 。 当轧件 头 部有 向 下 的弯 曲时 ,辊道所 受冲击 载荷更 大 。
万能轧机轧辊轴向窜动分析与控制
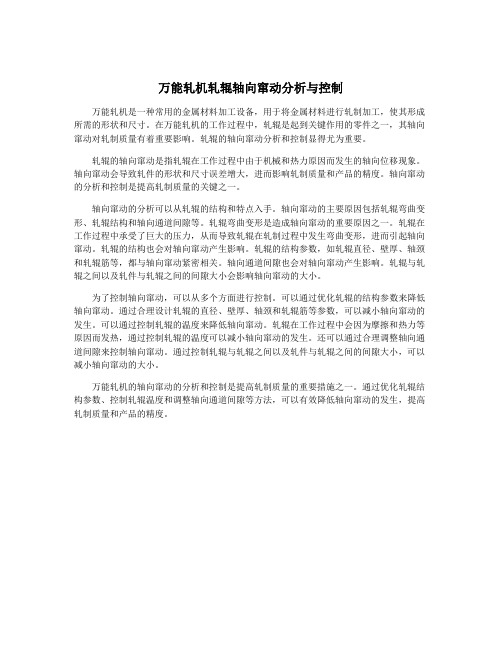
万能轧机轧辊轴向窜动分析与控制万能轧机是一种常用的金属材料加工设备,用于将金属材料进行轧制加工,使其形成所需的形状和尺寸。
在万能轧机的工作过程中,轧辊是起到关键作用的零件之一,其轴向窜动对轧制质量有着重要影响。
轧辊的轴向窜动分析和控制显得尤为重要。
轧辊的轴向窜动是指轧辊在工作过程中由于机械和热力原因而发生的轴向位移现象。
轴向窜动会导致轧件的形状和尺寸误差增大,进而影响轧制质量和产品的精度。
轴向窜动的分析和控制是提高轧制质量的关键之一。
轴向窜动的分析可以从轧辊的结构和特点入手。
轴向窜动的主要原因包括轧辊弯曲变形、轧辊结构和轴向通道间隙等。
轧辊弯曲变形是造成轴向窜动的重要原因之一。
轧辊在工作过程中承受了巨大的压力,从而导致轧辊在轧制过程中发生弯曲变形,进而引起轴向窜动。
轧辊的结构也会对轴向窜动产生影响。
轧辊的结构参数,如轧辊直径、壁厚、轴颈和轧辊筋等,都与轴向窜动紧密相关。
轴向通道间隙也会对轴向窜动产生影响。
轧辊与轧辊之间以及轧件与轧辊之间的间隙大小会影响轴向窜动的大小。
为了控制轴向窜动,可以从多个方面进行控制。
可以通过优化轧辊的结构参数来降低轴向窜动。
通过合理设计轧辊的直径、壁厚、轴颈和轧辊筋等参数,可以减小轴向窜动的发生。
可以通过控制轧辊的温度来降低轴向窜动。
轧辊在工作过程中会因为摩擦和热力等原因而发热,通过控制轧辊的温度可以减小轴向窜动的发生。
还可以通过合理调整轴向通道间隙来控制轴向窜动。
通过控制轧辊与轧辊之间以及轧件与轧辊之间的间隙大小,可以减小轴向窜动的大小。
万能轧机的轴向窜动的分析和控制是提高轧制质量的重要措施之一。
通过优化轧辊结构参数、控制轧辊温度和调整轴向通道间隙等方法,可以有效降低轴向窜动的发生,提高轧制质量和产品的精度。
正八工作辊的轴向力原因以及计算比较

工作辊轴承轴向力的原因分析以及计算比较一.轴向力产生的原因:1.跑偏当钢带跑偏时由于钢带与工作辊摩擦,导致工作辊往跑偏方向偏移,同时两侧水平受力不均,轧辊产生一定的水平方向交叉产生轴向力。
2. 轧机牌坊倾斜这其中包括机架牌坊相对中心线的不对称、下支承辊楔铁的不水平都会导致工作辊产生倾斜产生轴向力。
3.机架的震动由于轧机在工作时产生震动,导致轧辊在各个方向窜动。
4.弯辊力不均弯辊力是作用在轴承座上,操作侧与传动侧的弯辊力产生差值时,轧辊两侧受力不同产生倾斜,观察对比发现,轧机在工作时1、2、3架的弯辊力两侧差值一般小于5KN,4、5架差值差值一般在20KN左右,有的甚至达到80KN 以上。
5. 轧辊的弧度和轧辊的应力变形以及轧辊轴向的硬度不均轧辊有一定的弧度,在轧制过程中轧辊也可能会向两边产生一定的倾斜产生轴向力,当轴向的硬度不均时,轧辊在轧制过程中产生的变形量不同,轧辊也会出现倾斜。
6.轧制中两边的张力不均在轧制过程中机架与机架之间存在张力,当操作侧与传动侧的张力产生偏差时由于摩擦会使工作辊在水平方向产生一定的交叉产生轴向力。
观察发现在轧制时1、2、3架之间的张力差值几乎为0,而4、5架之间的张力差达到30KN。
7.轧制过程中的边浪、镰刀弯当轧制过程中产生边浪时,说明轧辊两侧的间隙量产生了差值,这就说明轧辊有了一定的倾斜,这也会产生轴向力。
8. 轧制力的偏差轧制过程中轧制出现偏差时由于轧辊受力不均也会产生倾斜,实际观察发现4、5架的轧制力偏差可以达到2t。
9.轧辊扁头与接轴器扁头配合间隙大导致轧机在运转时甩动量大产生的轴向力。
10.轧辊与接轴架的中心不同轴中间辊产生偏心转动,产生轴向力。
11.十字万向传动轴的十字头轴承间隙过大在轧制过程中使万向轴跳动过大产生轴向力。
对于以上轴向力产生的原因,其中轧辊交叉产生的轴向力最大,同时又会导致轴承座中的轴承内外圈产生不同轴,导致轴承产生局部磨损严重,游隙增大,滚动体局部受力,大大降低了推力轴承的寿命。
轧机轴向力产生的原因及减少轴承在线损坏的改进方法
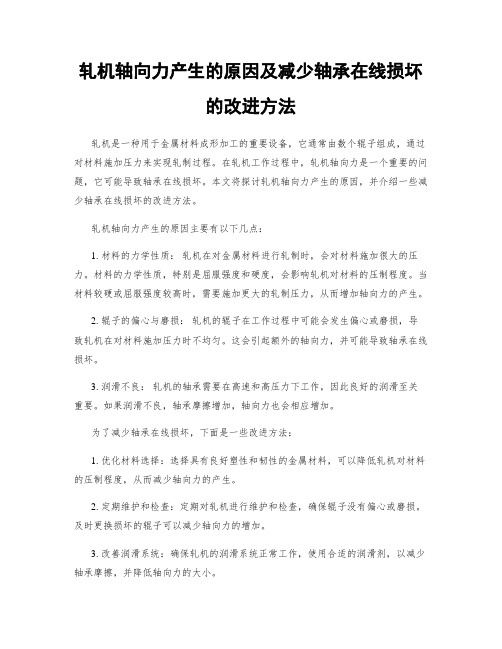
轧机轴向力产生的原因及减少轴承在线损坏的改进方法轧机是一种用于金属材料成形加工的重要设备,它通常由数个辊子组成,通过对材料施加压力来实现轧制过程。
在轧机工作过程中,轧机轴向力是一个重要的问题,它可能导致轴承在线损坏。
本文将探讨轧机轴向力产生的原因,并介绍一些减少轴承在线损坏的改进方法。
轧机轴向力产生的原因主要有以下几点:1. 材料的力学性质:轧机在对金属材料进行轧制时,会对材料施加很大的压力。
材料的力学性质,特别是屈服强度和硬度,会影响轧机对材料的压制程度。
当材料较硬或屈服强度较高时,需要施加更大的轧制压力,从而增加轴向力的产生。
2. 辊子的偏心与磨损:轧机的辊子在工作过程中可能会发生偏心或磨损,导致轧机在对材料施加压力时不均匀。
这会引起额外的轴向力,并可能导致轴承在线损坏。
3. 润滑不良:轧机的轴承需要在高速和高压力下工作,因此良好的润滑至关重要。
如果润滑不良,轴承摩擦增加,轴向力也会相应增加。
为了减少轴承在线损坏,下面是一些改进方法:1. 优化材料选择:选择具有良好塑性和韧性的金属材料,可以降低轧机对材料的压制程度,从而减少轴向力的产生。
2. 定期维护和检查:定期对轧机进行维护和检查,确保辊子没有偏心或磨损。
及时更换损坏的辊子可以减少轴向力的增加。
3. 改善润滑系统:确保轧机的润滑系统正常工作,使用合适的润滑剂,以减少轴承摩擦,并降低轴向力的大小。
4. 使用轴向力控制装置:安装轴向力控制装置可以实时监测轴向力的大小,并采取相应的措施来减少轴向力的产生。
综上所述,轧机轴向力的产生是由材料的力学性质、辊子的偏心与磨损以及润滑不良等因素引起的。
通过优化材料选择、定期维护和检查、改善润滑系统以及使用轴向力控制装置等改进方法,可以减少轴承在线损坏并提高轧机的工作效率。
18辊轧机工作辊轴向力导致止推轴承损坏因素分析及优化措施

Value Engineering———————————————————————作者简介:吴华(1992-),男,广西钦州人,本科(机械设计制造及其自动化),主要研究方向为冷轧机设备维护管理。
0引言止推轴承在18辊冷连轧机中起到了阻止工作辊持续轴向移动的主要作用,避免因不利因素移动超出工艺使用范围,造成断带、断辊或者其它设备的损坏,可以说没有止推轴承,18辊轧机组无法正常轧钢。
然而止推轴承在使用时存在受力大、使用环境差、损坏率高、损坏因素多、损坏时间不规律、生产过程中难以控制调整的缺点,因此降低止推轴承损坏率是具有紧迫性和难度的机组维护技术攻关工作,现在根据工艺原理和使用后效果作为参考依据,总结分析出相关的有利因素,用以指导止推轴承的使用。
1带钢板型影响因素分析带钢板型主要分两种情况易造成止推轴承损坏,横向切面呈楔形或者弯曲(镰刀弯、S 弯)。
为确保轧制的带钢厚度一致,同一组工作辊的中心高度位置要保持不变,改变的是带钢形变量。
当来料带钢存在横向厚度差,进入辊缝后轧制力必然会横向不对称分布,厚的一侧压下率大,轧制力大,工作辊单侧挠性变形,带钢从厚侧向薄侧跑偏[1],因工作辊与带钢表面接触存在摩擦力,使工作辊受到从厚侧趋向薄侧的轴向力而移动,止推轴承受力。
弯曲型带钢在前进方向受张力,带钢传动侧距离长,带钢往传动侧跑偏,反之则往操作侧跑偏,受工作辊与带钢之间受摩擦力的影响,工作辊产生轴向力向边部距离长的一侧移动,止推轴承受力[2]。
轧制时带钢板型不规则,以质点的形式在平面上按照各种不规则类型延展拉伸,提前检测出带钢楔形、弯曲,通过控制好速度,弯辊、串辊等控制工艺,降低因板型异常产生的轴向力,可以有效避免止推轴承损坏。
2中间辊影响因素分析中间辊是一对带有单边锥度的辊子,可以轴向移动起到调节带钢板型、松紧、跑偏的作用,在此过程中有两个重要的影响因素使工作辊产生轴向力致使止推轴承损坏。
上中间辊驱动侧带锥度,下中间辊操作侧带锥度,中间辊在压力状态下与工作辊完全贴合,以上中间辊与工作辊为分析对象,假设没有其它因素干扰的情况下压下力为F ,对其进行轴向力分析[3],见图1。
- 1、下载文档前请自行甄别文档内容的完整性,平台不提供额外的编辑、内容补充、找答案等附加服务。
- 2、"仅部分预览"的文档,不可在线预览部分如存在完整性等问题,可反馈申请退款(可完整预览的文档不适用该条件!)。
- 3、如文档侵犯您的权益,请联系客服反馈,我们会尽快为您处理(人工客服工作时间:9:00-18:30)。
轧机支撑辊与工作辊交叉产生轴向力分析
在工作辊与支撑辊交叉的摩擦区域内,被动支撑辊接触点对的速度场如图所示:
图1-1
图1-2
图1-3
图1-4
如图所示,支撑辊辊面的线速度等于工作辊面线速度在支撑辊垂直方向上的投影,计算公式如下:
cos B W V V θ
=∙
式中B V 为支撑辊辊面的线速度;W V 为工作辊辊面线速度;θ为交叉角。
由于工作辊和支撑辊的交叉,辊面接触摩擦力使支撑辊相对于工作辊做螺旋运动,作用于支撑辊的轴向力与B W V 矢量同向。
不考虑其他因素,由两辊面平衡原理,获得支撑辊轴向力
||sin a BW F F P μθ
==
式中P 为轧制力,μ为摩擦系数;θ为交叉角。
工作辊的轴向力,由支撑辊的轴向力平衡力系求出,方向必然与支撑辊轴向力相反。
针对现场在入口往出口轧时辊子朝外窜动,出口往入口轧时辊子朝内走;结合图1-1,图1-2,图1-3,图1-4可看出,入口往出口轧时是图1-1所描述的情况,出口往入口轧时是图1-2所描述的情况。
而我们在现场也发现,当入口往出口轧时,轴向窜动力比较大,说明θ角比较大,当出口往入口轧是,轴向窜动力要小,说明θ角在减小。
再结合上次我们测量的间隙数据可知,刚好是和现场实际情况相吻合的。
假设支撑辊实际轴线与与理论轴线未发生交叉,那么结合上面的分析可知工作辊的轴线如图1-5所示:
图1-5
从现场轧制的板型以及现场窜动情况来看,这和实际是相符合的。
结合“偏心距理论”可知,本身我们的轧机设计是工作辊相对支撑辊轴线在出口方向偏移
10mm,理论上来说,当入口往出口轧制时,由于偏心距的存在,钢板对工作辊必然会产生一个沿轧制方向的力,使工作辊轴承座上的耐磨板5与耐磨板1贴合,耐磨板6与耐磨板2贴合。
如果两边耐磨板磨损量一样的话,仅仅是工作辊的轴线发生平移,并不会发生交叉。
但从现场的实际情况来看,确实发生了交叉,这说明耐磨板1远比耐磨3要磨损的剧烈一些,所以我们要对耐磨板1或者耐磨板5进行加垫,以补偿其磨损量。
同理分析出口往入口轧的情况,我们可得知耐磨板4要比耐磨板2磨损的剧烈一些,所以我们应对耐磨板4或者耐磨板8加垫。
根据分析可知,要想控制操作侧往传动侧的窜动量,需要控制入口这四块耐磨板之间的间隙;要控制传动侧往操作侧的窜动量,需要控制出口这四块耐磨板之间的间隙。
之前我们已经在耐磨板5及耐磨板8底下各加了1mm的垫片,发现传动侧往操作侧的窜动量比较小,但是操作侧往传动侧的窜动量比较大,最大达到15mm(轧8mm薄板的时候)。
下一步准备加大入口操作侧轴承座上垫的厚度,准备将其由原来的1mm加至1.5mm,观察工作辊道窜动情况。