异丙苯生产工艺
异丙苯生产工艺
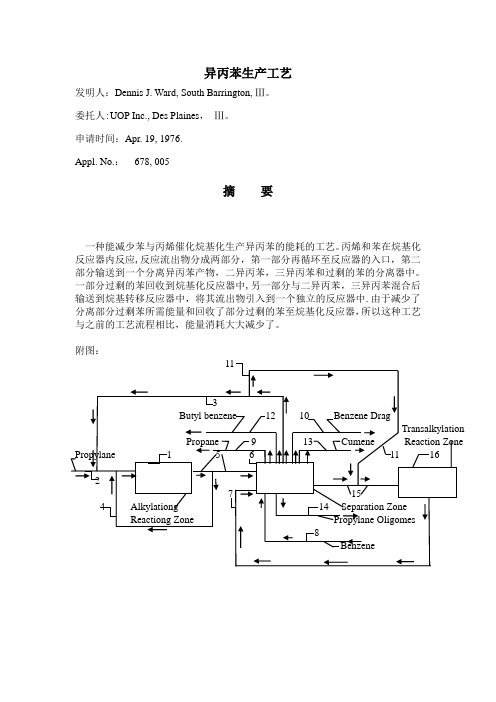
发明人:Dennis J. Ward, South Barrington, Ⅲ。
委托人:UOP Inc., Des Plaines,Ⅲ。
申请时间:Apr. 19, 1976.Appl. No.:678, 005摘要一种能减少苯与丙烯催化烷基化生产异丙苯的能耗的工艺。
丙烯和苯在烷基化反应器内反应,反应流出物分成两部分,第一部分再循环至反应器的入口,第二部分输送到一个分离异丙苯产物,二异丙苯,三异丙苯和过剩的苯的分离器中。
一部分过剩的苯回收到烷基化反应器中,另一部分与二异丙苯,三异丙苯混合后输送到烷基转移反应器中,将其流出物引入到一个独立的反应器中.由于减少了分离部分过剩苯所需能量和回收了部分过剩的苯至烷基化反应器,所以这种工艺与之前的工艺流程相比,能量消耗大大减少了。
附图:交叉引用相关的专利申请这篇专利申请在一定程度上是一篇正处于审理中的,编Ser。
No. 557010(在1975年3月10号提出,现已放弃)的专利申请的延续。
该项发明的背景该项发明提出了一种在烷基化催化剂的存在下由苯和丙烯生产异丙基苯的改进工艺,也涉及在转移烃化催化剂的存在下利用二异丙苯,三异丙苯和苯通过烷基转移生产异丙苯工艺。
本发明广泛适用于烷基化芳烃的生产,这些化合物是有用的在自己和更频繁地在后续其他化合物的化学合成。
本发明特别适用于生产异丙苯(异丙基苯),异丙苯是制备苯酚,丙酮、甲基苯乙烯、苯乙酮的重要反应物。
该项工艺发明的另一种用途是制备对异丙基甲苯,它能氧化生成对甲苯酚。
该工艺的进一步应用是在一类被取代的芳香族化合物的烷基化反应中,比如:苯酚,在它与异丁烯烷基化反应生成邻叔丁基苯酚和对叔丁基酚(两者在合成树脂领域都有重大用途)时,就能应用到该工艺。
综上所述,本发明在制备异丙苯工艺中有着特别的应用。
在一般商业生产异丙苯的过程中,将液态苯和液态丙烯投入反应器中,使之与烷基化催化剂接触下,在一个或多个反应器中发生相同的烷基化反应是一种惯例.为了减少苯的二烃基化合物的产生,通常我们将反应器中苯与丙烯的摩尔比由4:1提高至16:1,最好是8:1。
异丙苯工艺技术比较
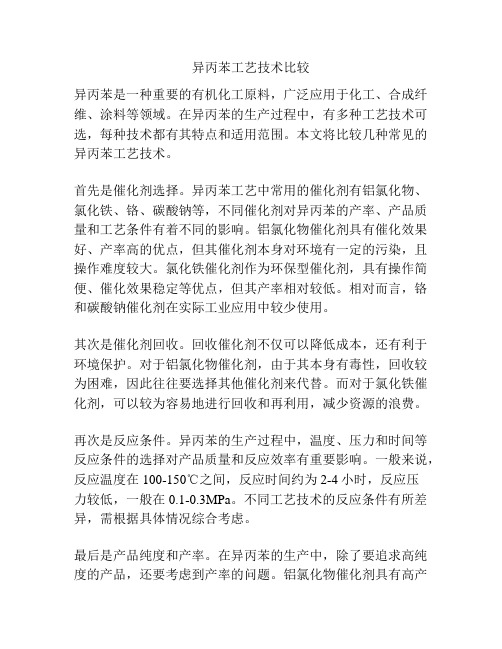
异丙苯工艺技术比较异丙苯是一种重要的有机化工原料,广泛应用于化工、合成纤维、涂料等领域。
在异丙苯的生产过程中,有多种工艺技术可选,每种技术都有其特点和适用范围。
本文将比较几种常见的异丙苯工艺技术。
首先是催化剂选择。
异丙苯工艺中常用的催化剂有铝氯化物、氯化铁、铬、碳酸钠等,不同催化剂对异丙苯的产率、产品质量和工艺条件有着不同的影响。
铝氯化物催化剂具有催化效果好、产率高的优点,但其催化剂本身对环境有一定的污染,且操作难度较大。
氯化铁催化剂作为环保型催化剂,具有操作简便、催化效果稳定等优点,但其产率相对较低。
相对而言,铬和碳酸钠催化剂在实际工业应用中较少使用。
其次是催化剂回收。
回收催化剂不仅可以降低成本,还有利于环境保护。
对于铝氯化物催化剂,由于其本身有毒性,回收较为困难,因此往往要选择其他催化剂来代替。
而对于氯化铁催化剂,可以较为容易地进行回收和再利用,减少资源的浪费。
再次是反应条件。
异丙苯的生产过程中,温度、压力和时间等反应条件的选择对产品质量和反应效率有重要影响。
一般来说,反应温度在100-150℃之间,反应时间约为2-4小时,反应压力较低,一般在0.1-0.3MPa。
不同工艺技术的反应条件有所差异,需根据具体情况综合考虑。
最后是产品纯度和产率。
在异丙苯的生产中,除了要追求高纯度的产品,还要考虑到产率的问题。
铝氯化物催化剂具有高产率、高选择性的优点,可以得到较高纯度的异丙苯,但操作复杂。
氯化铁催化剂的产率相对较低,但可以得到较好的产品纯度。
综合比较来看,氯化铁催化剂工艺是一种操作简单、催化效果稳定且环保性较高的异丙苯生产技术。
在实际应用中,根据具体的生产需求和环境要求,可以选择适当的工艺技术,并结合催化剂选择、催化剂回收、反应条件等方面进行调整和优化,以获得最佳的异丙苯生产效果。
异丙苯的工艺

异丙苯的工艺异丙苯的工艺是通过对苯和丙烯进行反应制得的。
以下是异丙苯的工艺流程和详细步骤:1. 原料准备:苯和丙烯是异丙苯生产过程中的主要原料。
苯一般通过石化工艺从石油中提取,并经过脱氧、干燥等处理进行净化。
丙烯可通过烃类裂解、重整等工艺从石化原料中获得。
2. 反应器装置:反应器是进行异丙苯工艺反应的主要装置。
常见的反应器类型包括固定床反应器、流化床反应器等。
其设计要求包括能够提供合适的反应温度和压力,达到理想的反应条件。
3. 催化剂:催化剂在异丙苯生产过程中起到关键的作用,能够加速反应速率,提高产品收率和纯度。
常用的催化剂包括铝矽比为1的萤石型沸石类催化剂。
4. 反应过程:将净化后的苯和丙烯加入反应器中,利用催化剂的作用,进行转化反应。
反应一般在高温高压条件下进行,一般温度范围为200-450摄氏度,压力范围为1-3兆帕。
反应的产物包括异丙苯和副产品如甲苯等。
5. 分离纯化:反应结束后,通过分离纯化过程,将异丙苯和副产品分离开。
分离纯化的方法可以包括蒸馏、吸附、洗涤等多种工艺。
其中,蒸馏是基于异丙苯和副产品的沸点差异进行分离,是最常用的方法。
6. 产品处理:通过产品处理工艺,对异丙苯进行进一步的精制和改性处理。
这包括去除杂质、调整的产品组分等步骤。
产品处理的具体工艺根据产品的要求和应用不同而有所不同。
7. 副产物处理:副产品如甲苯等需要进行进一步的处理。
副产物处理工艺包括回收和再利用、分离和销售等步骤。
副产物的处理是生产过程中的一个重要环节,有助于提高产品收率和降低环境污染。
8. 管道和设备:生产过程中需要用到各种管道和设备来输送原料、产物和处理副产品。
这些管道和设备必须具备良好的耐高温、耐压性能,并符合工艺流程和安全要求。
9. 安全措施:在异丙苯工艺中,需采取各种安全措施,确保生产过程中的安全。
这包括良好的设备维护和检修工作、工艺操作的严格控制和操作规范、定期的安全培训和应急预案等。
以上是异丙苯的工艺流程和详细步骤。
催化精馏法生产异丙苯工艺的评述_胡一德
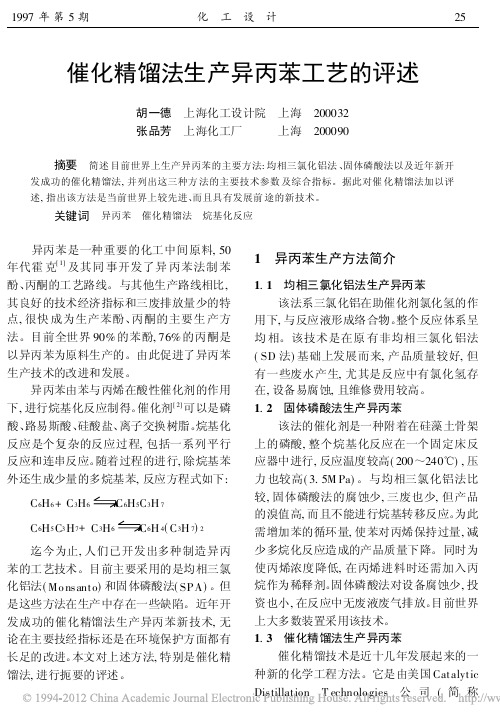
1997 年 第 5 期 化 工 设 计 1
ABSTRACTS
Speed up Reform and Aim at the International Market
( Cheng da Chemical Eng ineer ing Corp orati on of China Chengdu 610041)
( 3) 操作条件较为温和, 加上无腐蚀性, 设备可用碳钢制造。反应和分离在同一个设 备内进行, 设备的台数也较少, 因此投资较其 他方法低。
( 4) 在反 应同时进 行精馏, 无需苯的 回 流, 从而减少重组份在循环液中的积累, 有利 于延长催化剂的寿命。
( 5) 传统的工艺为了使丙烯保持低浓度, 通常用反应液循环的方法, 这增加了设备的 投资和操作费用。而催化精馏工艺中丙烯先 在气相被苯蒸汽稀释, 然后再溶于液相扩散 至分子筛表面, 在反应界面上丙烯与苯的浓 度比可达 1∶10, 从而减少多异丙苯的生成。
1997 年 第 5 期 化 工 设 计 2 5
催化精馏法生产异丙苯工艺的评述
胡 一德 上 海化 工设 计院 上 海 2000 32 张 品芳 上 海化 工厂 上 海 2000 90
摘要 简述 目前世界上生产异丙苯的主要方法: 均相三氯化铝法 、固体磷酸法以及近年新开
图 1 催化精馏法生产异丙苯流程
1. 烷基化反应器 2. 反烃化反应器 3. 异丙苯塔 4. 多异丙苯塔
原料分别从烷基化反应器中、上部加入。 在反应器上部为反应段, 下部为提馏段, 反应 段中采 用 CDT ECH 公司开 发的催化剂, 并 将其进行特殊包装和排列作为填料。液相苯 与气相丙烯一起渗入催化剂表面, 在反应界 面丙烯和苯的浓度比可以达到 1∶10( 采用 固体磷酸法丙烯与苯的浓度比为 1∶2~3) , 这样就可以保证苯对丙烯的过量, 从而减少 多异丙苯的产生, 提高主反应的转化率。反应 热由苯蒸发导出。
异丙苯生产工艺设计
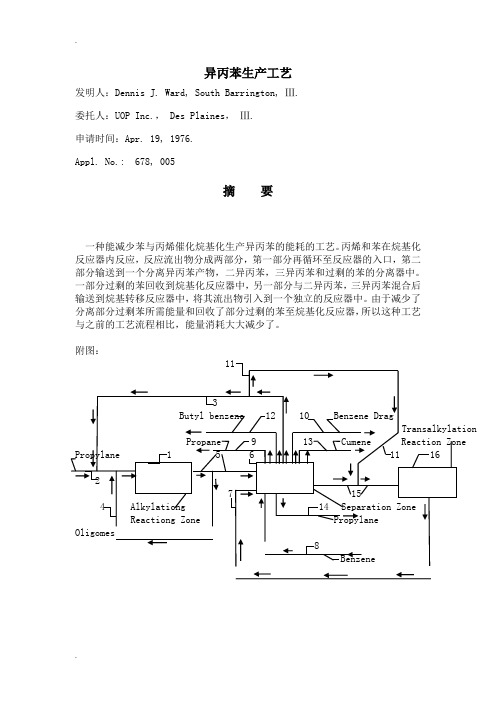
异丙苯生产工艺发明人:Dennis J. Ward, South Barrington, Ⅲ.委托人:UOP Inc., Des Plaines,Ⅲ.申请时间:Apr. 19, 1976.Appl. No.: 678, 005摘要一种能减少苯与丙烯催化烷基化生产异丙苯的能耗的工艺。
丙烯和苯在烷基化反应器内反应,反应流出物分成两部分,第一部分再循环至反应器的入口,第二部分输送到一个分离异丙苯产物,二异丙苯,三异丙苯和过剩的苯的分离器中。
一部分过剩的苯回收到烷基化反应器中,另一部分与二异丙苯,三异丙苯混合后输送到烷基转移反应器中,将其流出物引入到一个独立的反应器中。
由于减少了分离部分过剩苯所需能量和回收了部分过剩的苯至烷基化反应器,所以这种工艺与之前的工艺流程相比,能量消耗大大减少了。
附图:113Butyl benzene 12 10 Benzene DragTransalkylationPropane 9 13 Cumene Reaction Zone Propylane 1 5 6 11 1627 154 Alkylationg 14 Separation ZoneReactiong Zone PropylaneOligomes8Benzene异丙基苯的生产交叉引用相关的专利申请这篇专利申请在一定程度上是一篇正处于审理中的,编Ser. No. 557010(在1975年3月10号提出,现已放弃)的专利申请的延续。
该项发明的背景该项发明提出了一种在烷基化催化剂的存在下由苯和丙烯生产异丙基苯的改进工艺,也涉及在转移烃化催化剂的存在下利用二异丙苯,三异丙苯和苯通过烷基转移生产异丙苯工艺。
本发明广泛适用于烷基化芳烃的生产,这些化合物是有用的在自己和更频繁地在后续其他化合物的化学合成。
本发明特别适用于生产异丙苯(异丙基苯),异丙苯是制备苯酚,丙酮、甲基苯乙烯、苯乙酮的重要反应物。
该项工艺发明的另一种用途是制备对异丙基甲苯,它能氧化生成对甲苯酚。
苯和丙烯反应生成异丙苯工艺流程

苯和丙烯反应生成异丙苯工艺流程1.首先,在反应釜中加入苯和丙烯。
First, add benzene and propylene into the reactor.2.然后加入催化剂,促使苯和丙烯发生反应。
Then add catalyst to facilitate the reaction between benzene and propylene.3.反应产生的异丙苯被收集和提纯。
The produced isopropylbenzene is collected and purified.4.通过精馏等工艺,获得高纯度的异丙苯。
High-purity isopropylbenzene is obtained through processes such as distillation.5.最后,产品经过包装和储存,准备出售。
Finally, the product is packaged, stored, and ready for sale.6.工艺流程中需要严格控制温度和压力。
The temperature and pressure need to be strictly controlled in the process.7.生产过程中要注意安全防护措施,防止意外发生。
Safety precautions should be taken during the production process to prevent accidents.8.合理设计反应釜和设备布局,以提高生产效率。
Reasonable design of the reactor and equipment layout to improve production efficiency.9.通过优化反应条件,提高异丙苯的产率和纯度。
By optimizing reaction conditions, the yield and purity of isopropylbenzene are increased.10.在生产过程中要进行原料和产品的在线监测。
异丙苯氧化法

异丙苯回收
• 本工段的主要目的是将异丙苯氧化、丙烯 环氧化工段中生成的aSM、DMPC等液相低 温加氢生成异丙苯。加氢反应进料由DMPC 塔塔顶来,加氢后产品回到异丙苯塔,aSM 、DMPC等加氢单程转化率大于90%。
优点
• 与共氧化法的主要区别在于使用异丙苯替代 了乙苯,并且异丙苯循环使用,不产生联产 品。 • 由于该工艺无需联产苯乙烯所需的辅加设备 ,装置投资费用比共氧化法约低1/3。 • 无需使用氯气的氯醇法工艺所需的防腐设备 。 缺点:生产过程中产生大量α-甲基苯乙烯
环氧化反应的主反应式如下:
C6H5C(CH3)2OOH+CH3CH=CH2===== C6H5C(CH3)2OH 二甲基苄醇+CH3CH(O)CH2
主要副反应:
C6H5C(CH3)2OOH====C6H5OH +CH3COCH3
• 该步骤是使CHP 溶液与丙烯在填充有催化剂 的固定床反应器中反应生成PO 和CMA,然 后供应给丙烯和P O 回收工艺。为此采用的 主要工艺方法是丙烯过量。CHP分多段进料 ,为防止CHP过热分解,段间采用换热器冷 却维持反应温度,采用钛硅分子筛催化剂 固定床反应工艺。
• 1. 氧化液;2 . 碱水溶液;3 、4 、6 、7 、8 . 水层 ;5 、9.油层;10.新鲜水;11.产品CHP 溶液
图1 CHP 溶液精制工艺流程示意图
异苯氧化过程工艺流程图
1-氧化塔;2、3-第一、第二提浓塔;4-贮槽;5-冷凝器; 6-气液分离器;7-降膜蒸发器
流程图
CHP氧化丙烯制环氧丙烷
异丙苯cm氧化法由日本住友sumitomo化学公司开发采用钛基催化剂的固定床反应器以过氧化氢异丙苯chp为氧化剂chp使丙烯环氧化得到环氧丙烷和二甲基苄醇后者脱水为甲基苯乙烯然后再加氢生成异丙苯异丙苯氧化成chp后循环使用
年产5万吨sd法制异丙苯工艺计算
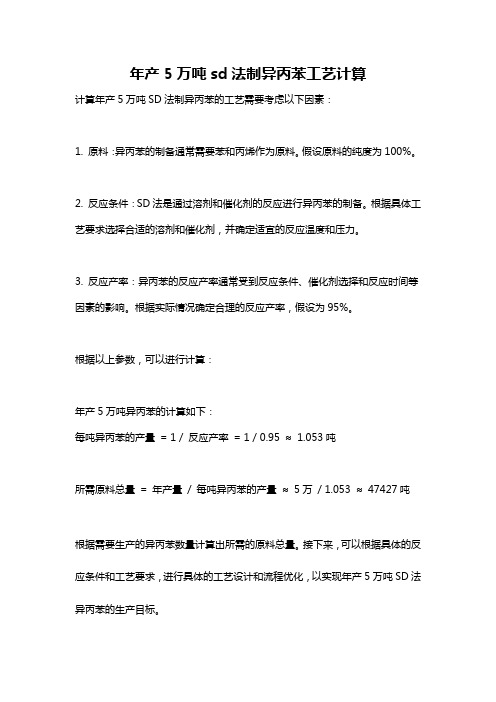
年产5万吨sd法制异丙苯工艺计算
计算年产5万吨SD法制异丙苯的工艺需要考虑以下因素:
1. 原料:异丙苯的制备通常需要苯和丙烯作为原料。
假设原料的纯度为100%。
2. 反应条件:SD法是通过溶剂和催化剂的反应进行异丙苯的制备。
根据具体工艺要求选择合适的溶剂和催化剂,并确定适宜的反应温度和压力。
3. 反应产率:异丙苯的反应产率通常受到反应条件、催化剂选择和反应时间等因素的影响。
根据实际情况确定合理的反应产率,假设为95%。
根据以上参数,可以进行计算:
年产5万吨异丙苯的计算如下:
每吨异丙苯的产量= 1 / 反应产率= 1 / 0.95 ≈1.053吨
所需原料总量= 年产量/ 每吨异丙苯的产量≈5万/ 1.053 ≈47427吨
根据需要生产的异丙苯数量计算出所需的原料总量。
接下来,可以根据具体的反应条件和工艺要求,进行具体的工艺设计和流程优化,以实现年产5万吨SD法异丙苯的生产目标。
- 1、下载文档前请自行甄别文档内容的完整性,平台不提供额外的编辑、内容补充、找答案等附加服务。
- 2、"仅部分预览"的文档,不可在线预览部分如存在完整性等问题,可反馈申请退款(可完整预览的文档不适用该条件!)。
- 3、如文档侵犯您的权益,请联系客服反馈,我们会尽快为您处理(人工客服工作时间:9:00-18:30)。
发明人:Dennis J. Ward, South Barrington, Ⅲ.委托人:UOP Inc.,Des Plaines,Ⅲ.申请时间:Apr. 19, 1976.Appl. No.: 678, 005摘要一种能减少苯与丙烯催化烷基化生产异丙苯的能耗的工艺。
丙烯和苯在烷基化反应器内反应,反应流出物分成两部分,第一部分再循环至反应器的入口,第二部分输送到一个分离异丙苯产物,二异丙苯,三异丙苯和过剩的苯的分离器中。
一部分过剩的苯回收到烷基化反应器中,另一部分与二异丙苯,三异丙苯混合后输送到烷基转移反应器中,将其流出物引入到一个独立的反应器中。
由于减少了分离部分过剩苯所需能量和回收了部分过剩的苯至烷基化反应器,所以这种工艺与之前的工艺流程相比,能量消耗大大减少了。
附图:交叉引用相关的专利申请这篇专利申请在一定程度上是一篇正处于审理中的,编Ser. No. 557010(在1975年3月10号提出,现已放弃)的专利申请的延续。
该项发明的背景该项发明提出了一种在烷基化催化剂的存在下由苯和丙烯生产异丙基苯的改进工艺,也涉及在转移烃化催化剂的存在下利用二异丙苯,三异丙苯和苯通过烷基转移生产异丙苯工艺。
本发明广泛适用于烷基化芳烃的生产,这些化合物是有用的在自己和更频繁地在后续其他化合物的化学合成。
本发明特别适用于生产异丙苯(异丙基苯),异丙苯是制备苯酚,丙酮、甲基苯乙烯、苯乙酮的重要反应物。
该项工艺发明的另一种用途是制备对异丙基甲苯,它能氧化生成对甲苯酚。
该工艺的进一步应用是在一类被取代的芳香族化合物的烷基化反应中,比如:苯酚,在它与异丁烯烷基化反应生成邻叔丁基苯酚和对叔丁基酚(两者在合成树脂领域都有重大用途)时,就能应用到该工艺。
综上所述,本发明在制备异丙苯工艺中有着特别的应用。
在一般商业生产异丙苯的过程中,将液态苯和液态丙烯投入反应器中,使之与烷基化催化剂接触下,在一个或多个反应器中发生相同的烷基化反应是一种惯例。
为了减少苯的二烃基化合物的产生,通常我们将反应器中苯与丙烯的摩尔比由4:1提高至16:1,最好是8:1。
在之前的工业化生产中利用两个相抵触的反应生产异丙苯产生了一些问题,其中之一就是产生了上文所说的二烃基化合物,比如:二异丙苯、三异丙苯,而不是所需的单烷基化产物。
这种竞争反应通过采用如上所述的大摩尔量过剩的苯来控制。
其他的竞争反应导致了异丙苯产量的损失,因为一部分反应物丙烯形成丙烯的低聚物,如在一定程度上会出现丙烯二聚物和三聚物,即使有大量过剩的苯存在。
将丙烯三聚物和一些丙烯四聚物与异丙苯一起加热,由于这些烯烃的存在,这种产生低聚物的反应(异丙苯氧化制备苯酚的反应)必须控制到最小,这样才能获得高纯度的产品。
烷基化芳香族化合物的烷基化反应在自然条件下是放热的,反应器的温度会迅速增高。
放热反应导致温度的增高,同样也会导致副反应的产生,从而增加异丙苯的残留产物。
在过去已经习惯通过在多个单独的区域和使用骤冷剂之间的几个连续的烷基化区催化反应来控制温度上升。
这种骤冷剂是为了在反应混合物进入每个连续的区域时控制温度,因此在每一个区域内温度都会上升。
反应器从进口到出口温度的增加也通过控制苯的摩尔量的过量来控制,苯充当散热器吸收烷基化反应所释放的热量。
因此,向反应器增加苯的摩尔过剩量,与相应的稀释丙烯反应物,不仅提供了更多的芳香族化合物发生烷基化和减少低聚物的产生和烷基化的副产品,也减少了在一个或多个烷基化反应器中因过度温升造成不良副产物的形成。
为了获得装有所需高摩尔量过剩苯的反应器,通常将反应器流出物分离,来获得适合回收的富苯流。
因为反应器流出物的主要成分是苯和异丙苯,分离苯和异丙苯是很有必要的,后者是高沸点组分。
因此,要获得相对纯化的苯,且适合回收至反应器,苯需要蒸发分馏,从而需要消耗大量热量来蒸发苯,而且在苯分馏器中提供足够的回流,热量需求实质上与反应器中苯和丙烯的比例成正比。
目前,相对较高的燃料成本的工艺会导致高能量消费,所以,如果能量消耗减少的话,此前缺乏吸引力的处理方案变得越来越理想。
该项发明的概要本发明的目标是为在烷基化催化剂的存在下通过苯与丙烯的烷基化生产异丙苯提供一个改进的工艺。
这项发明的一个特定目标是减少苯与丙烯烷基化生产异丙苯工艺的能耗。
更具体的目标是为该工艺提供一种固体磷酸催化剂,这一过新工艺与先前技术流程相比。
本发明提出的生产异丙苯的新工艺具体体现在:a)丙烯与过量的苯在烷基化催化剂存在下在烷基化反应器中发生烷基化反应;b)将反应器总液体流出物分离出至少两部分组成;c)将一部分分离物循环回反应器;d)将一部分以上流出物和烷基化反应器的流出物按以下规定引入一个分离器中;e)在分离器中将混合物分离出富苯流、异丙苯流、富二异丙苯和富三异丙流;f)在烷基转移催化剂存在下,在烷基转移反应器中。
使富二异丙苯和富三异丙流与苯发生烷基转移反应生成额外的异丙苯;g)将烷基转移反应器的流出物输送到分离器中;h)将一部分富苯流输送到烷基化反应器中;i)从分离器中收集异丙苯流。
在本发明的处理方案中,丙烯和过量的苯使用烷基化催化剂在烷基化反应器中反应,一部分生成物不经分离,直接循环至的反应器。
另一部分生成物,即净流出物,输送到一个分离器中,过量的苯、异丙基苯、二异丙苯和三异丙苯,和其他组分在其中分离。
正如在上文提到的,从净流出物中减少过剩苯的分离,以减少能量消耗是可取的,同时需要保持足够量的过剩苯进入反应区,以防止过度形成丙烯低聚物。
这将通过再循环一部分未经分离的反应器生成物来完成。
工艺流程的主要影响在上文所描述的方式包括:1)通过减少从净流出物中分离过剩苯与异丙苯的量来减少能量消耗;2)比之前技术形成相对更多的二或三烷基化苯产品。
在该工艺的分离器中,将二异丙苯和三异丙苯集中,然后与过剩苯混合后送入烷基转移反应器在使用烷基转移催化剂的情况下发生反应。
烷基转移反应器产生富异丙苯流将返回到分离器。
流程图的描述这项发明可以更清晰地参照附图进行描述和演示。
然而在这样一个示意图描述中必然会存在某些局限性,从而无意限制了大部分发明。
正如在上文提到的,该工艺的第一步包括将苯与丙烯在烷基化反应器内发生烷基化反应。
在附图中,第一步发生在烷基化反应器1内。
然而,苯和丙烯的混合物必须送入这个反应器内。
在图中,富丙烯进料流通过管道2进入反应器1中,从循环系统而来的苯通过管道3,与管道2并列进入烷基化反应器1中,烷基化反应器生成物的再循环流包括主要是苯,还有异丙苯通过管道4和2供应到反应器进口。
最后提到物流提供了额外的苯,目的是提高烷基化反应器中的苯/丙烯比。
丙烯反应物,循环苯和循环反应器流出物混合后通过管道2引入反应器1。
烷基化反应器的流出物通过管道5流出,一部分通过管道4提供在上文描述的再循环流,剩下的部分是通过管道5进入分离器6。
同样还引入分离器6的是在下文所述的烷基转移反应器的流出物,这股物料通过过管道7进入分离器。
在该工艺中苯的进料流也是通过管道8引入分离器6中。
富丙烯进料流通过管道2提供给烷基化反应器,是能是不同流程的流出物来准备的,如流化床催化裂解或热解,通常包括不反应的链烷烃,主要是丙烷,还有少量乙烷、丁烷。
烯烃除了丙烯会导致副产品的产生在烷基化反应生产异丙苯过程中,因此富丙烯进料流通常含有至少99%的丙烯。
经管道8进入反应器的苯进料流也是一股包含至少99.5%苯的高纯度物流,经常可以从一种芳烃抽提工艺的流出物得到。
其他芳烃是有害的,他们的存在会导致副产品的产生,而且不反应的芳烃也是一个问题,因为在分离器6中是不能分离苯和未反应芳烃的。
因此,在该工艺中,流入分离器6的物流包括主要是苯、异丙苯、丙烷、二异丙苯和三异丙苯,较少量的石蜡(乙烷和丁烷),芳烃(甲苯和二甲苯),丁苯和丙烯低聚物。
在分离器6中,通过合适的闪蒸、分馏、吸收、和提纯,就能从进口组成中分离出几股不同的物流。
富丙烷流包括其他轻组分芳烃通过管道9回收;富苯流包括未反应芳烃组分通过管道10回收;另一股富苯流通过管道3回收,一部分是通过管道3循环回烷基化反应器1,另一部分是通过管道1供给烷基转移反应器;富丁苯流通过管道12回收;异丙苯流通过管道13回收;丙烯低聚物产品通过管道14回收;二异丙苯和三异丙苯流是通过管道15回收。
通过管道15回收的二异丙苯和三异丙苯流与通过管道11回收的苯混合后送入烷基转移反应器16,其中包含了优选的固体磷酸催化剂。
从烷基转移反应器中得到的富异丙苯流通过管道7进入分离器6。
该发明的详细过程丙烯和苯是这项生产异丙苯工艺的反应物。
通常从流体催化裂化装置、热解装置、热裂化装置或其他炼油单元生成物中得到丙烯与丙烷的混合物。
所以其他轻质烷烃化合物,如乙烷、丁烷可能会有少量存在于富丙烯进料流中,除了丙烯以外的烯烃化合物会产生烷基化芳烃而不是异丙苯,因为掺杂了其他原料。
一个典型的丙烯原料流的摩尔百百分比如下:0.10%乙烷、24.80%丙烷、74.95%丙烯、0.11%异丁烷、0.01%正丁烷和0.03%丁烯。
该工艺需要超过99.5%的高纯度苯,以防止副反应,消除分离额外的苯的消耗和避免在该工艺中加热非芳香族组分。
一个典型的苯原料流是由芳烃抽提装置提供的,且含有以下摩尔百分数的组分:99.90%苯、0.05%甲苯、0.05%非芳香族化合物。
在附图中,该工艺的苯原料流引入分离器,当然这股物料也可引入烷基化反应器或烷基转移反应器。
在该工艺中烷基化反应器的进口物料由三股混合在一起的物料组成;新鲜富丙烯流,一部分如下文所描述的烷基化反应器流出物的循环流,和一股供给该工艺作为新鲜进料的富苯流,更好的是,利用如下文所描述的回收的富苯流。
烷基化反应器的操作条件包括入口温度约为150-260°C,首选温度约195-215°C;约20到60大气压力;每体积/小时的净流出物使用大约0.2到2.0体积的催化剂;每一摩尔丙烯进入烷基化反应器需要大约2到6摩尔从回收富苯流中得到的苯,在进料中苯与丙烯首选的摩尔比率大约是3;每一摩尔的丙烯进入烷基化反应器需要1到100摩尔循环物流中的苯,在进料中循环苯与丙烯的首选的摩尔比率是3到20。
本工艺可由一个或多个反应器串联或并联组成,流动方向可以是向下、向上、径向、或其他方向。
在本发明的构思中,反应器的配置设计没有任何限制。
本发明可使用任何常规或易得的烷基化催化剂。
这种催化剂通常描述为酸性催化剂,也可以是同构或异构催化剂品种。
因此,催化剂可以是一种负载型或非负载型酰基化反应的金属卤化物,例如无水氯化铝、氯化铁、氯化锡、氟化硼、氯化锌等。
某些无机酸,特别是硫酸、氢氟酸、磷酸,催化烷基化反应的能力很强,这些催化剂如包含少于10wt%水的硫酸,至少含有83%浓度的氢氟酸,或液态无水氟化氢都非常实用。