第三章:生胶塑炼
橡胶塑炼与混炼

一生胶的塑炼工艺生胶的塑炼原理一.塑炼的定义通过机械应力、热、氧或加入某些化学试剂等方式,使橡胶由强韧的高弹性状态转变为柔软的塑性状态的过程。
塑性(可塑性):橡胶在发生变形后,不能恢复其原来状态,或者说保持其变形状态的性质。
二.塑炼的目的和要求1.塑炼的目的减小弹性,提高可塑性;降低粘度;改善流动性;提高胶料溶解性和成型粘着性。
2.塑炼胶的质量要求(1)可塑度要适当应满足加工工艺要求,在此基础上应具有最小的可塑性。
过度塑炼会降低硫化胶的强度、弹性、耐磨性等,而且会增加动力消耗。
塑炼程度:根据混炼胶工艺性能和制品性能的要求来确定。
如:供胶、浸胶、刮胶、擦胶和制造海绵等用途的胶料,要求的可塑度较大,生胶的塑炼程度要高些。
供模压用的胶料,则要求可塑性宜小。
一般:胶管外层胶可塑度:~;胶管内层胶:~;胎面胶:~;胎侧胶左右;海绵胶~(2)塑炼均匀三.生胶的增塑方法和原理(一)增塑方法(二)塑炼原理生胶的分子量与可塑性有着密切的关系。
分子量越小,可塑性就越大。
生胶经过机械塑炼后,分子量降低,粘度下降,可塑性增大。
由此可见,生胶在塑炼过程中,可塑性的提高是通过分子量的降低来实现的。
η0—聚合物熔体的最大粘度;A—特性常数;M W—聚合物的重均分子量1.机械塑炼过程机理在低温下:在机械力作用下首先切断橡胶大分子链生成大分子自由基。
(机械力引发橡胶大分子的断链,氧作为自由基接受体,起着阻断自由基的作用。
)在高温下:机械力切断橡胶大分子生成自由基的几率减少。
橡胶大分子在机械力的活化作用下,氧引发橡胶大分子的断链。
(机械力起到应力活化作用,氧作为自由基引发体,引发橡胶大分子的断链。
)链终止:橡胶氢过氧化物不稳定,分解生成较小的大分子,连锁反应终止。
2.影响塑炼的因素:(1)机械力的作用根据理论分析,机械力对橡胶分子的断链作用,可表示为:式中ρ—分子链断链的几率;K1、K2—常数;E—分子链的化学键能;F0—作用于分子链上的力;δ—分子链断链时伸长长度;F0δ—分子链断链时消耗的机械功;低温塑炼要求尽可能地降低辊温和胶温。
生胶的塑炼工艺

生胶的塑炼工艺摘要:生胶的塑炼原理、目的、要求和影响塑炼的因素及应用。
生胶和混炼胶可塑度的测定通常有三种方法:压缩法、旋转扭力法和压出法。
关键词:塑炼;设备;开炼机;塑炼方法;塑炼工艺一、塑炼的定义1、生胶塑炼的描述:橡胶的弹性给工艺加工带来很大的困难,必须把生胶由弹性状态变为可塑性状态,这个过程称之为塑炼;塑炼的方法有,开炼机低温塑炼,密炼机和螺杆挤出机高温塑炼,添加塑解剂塑炼。
这期间要注意,橡胶的可塑性不宜太大,太大会使橡胶制品的机械强度降低,永久变形增大,耐老化性、耐磨性和弹性降低,因此要防止生胶塑炼过渡,要在满足工艺性能前提的要求下,使之具有最适当的可塑性。
2、定义:通过机械应力、热、氧或加进某些化学试剂等方式,使橡胶由强韧的高弹性状态转变为柔软的塑性状态的过程。
3、塑性(可塑性):橡胶在发生变形后,不能恢复其原来状态,或者说保持其变外形态的性质。
二.塑炼的目的和要求1.塑炼的目的减小弹性,提高可塑性;降低粘度;改善流动性;提高胶料溶解性和成型粘着性。
2.塑炼胶的质量要求(1)可塑度要适当应满足加工工艺要求,在此基础上应具有最小的可塑性。
过度塑炼会降低硫化胶的强度、弹性、耐磨性等,而且会增加动力消耗。
塑炼程度:根据混炼胶工艺性能和制品性能的要求来确定。
如:供胶、浸胶、刮胶、擦胶和制造海绵等用途的胶料,要求的可塑度较大,生胶的塑炼程度要高些。
供模压用的胶料,则要求可塑性宜小。
一般:胶管外层胶可塑度:0.3-0.35;胶管内层胶: 0.25-0.3;胎面胶: 0.22-0.24;胎侧胶: 0.35左右;海绵胶: 0.5-0.6;(2)塑炼均匀三、塑炼的设备及塑炼方法(以介绍开炼机)1、准备工艺(1).烘胶NR烘胶温度一般在50-60℃,时间为24-36h,冬季加热时间为36-72h。
CR烘胶温度一般在24-40℃,时间为4-6h。
烘胶温度不宜过高,否则会影响橡胶的物理机械性能。
(2).切胶用切胶机将生胶切成小块,每块重量视胶种而异,NR每块10-20kg,CR每块不超过10kg。
塑炼工艺3—塑炼方法及影响因素
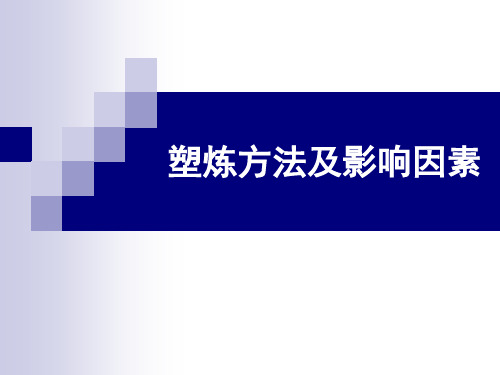
2.喂料速度 . 喂料速度要适当而均匀。速度过快, 喂料速度要适当而均匀。速度过快, 胶料在机筒内的停留时间短,塑炼不均匀, 胶料在机筒内的停留时间短,塑炼不均匀, 出现夹生现象。速度太慢, 出现夹生现象。速度太慢,不仅降低生产 效率。 效率。 3.排胶孔隙大小 . 排胶孔隙大小依胶料塑炼程度要求而 孔隙小,排胶速度和排胶量减小, 定。孔隙小,排胶速度和排胶量减小,胶 料可塑度偏大,生产效率降低。反之, 料可塑度偏大,生产效率降低。反之,出 胶孔隙加大,排胶量大,生产能力提高, 胶孔隙加大,排胶量大,生产能力提高, 但塑炼胶的可塑度偏低且不均匀。 但塑炼胶的可塑度偏低且不均匀。
五.塑炼后的补充加工 1.压片或造粒 . 2.冷却与干燥 . 3.停放 . 干燥后的胶片按规定堆放4~8h以上才 干燥后的胶片按规定堆放 以上才 能恭下道工序使用。 能恭下道工序使用。 4.质量检验 .
常用橡胶的塑炼特性
一.橡胶塑炼难易的原因 1.NR塑炼容易的原因 . 塑炼容易的原因 (1)大分子中存在甲基和双键的共轭效应, )大分子中存在甲基和双键的共轭效应, 键能降低,易断裂; 键能降低,易断裂; (2)分子量大,易断链; )分子量大,易断链; (3)大分子断链后生成的自由基稳定性高; )大分子断链后生成的自由基稳定性高; (4)大分子氧化生成的氢过氧化物分解导致 ) 大分子链断裂破坏。 大分子链断裂破坏。
塑炼方法及影响因素
一.准备工艺 1.烘胶 . NR烘胶温度一般在 烘胶温度一般在50~60℃,时间为 烘胶温度一般在 ℃ 24~36h,冬季加热时间为 ,冬季加热时间为36~72h。 。 CR烘胶温度一般在 烘胶温度一般在24~40℃,时间为 烘胶温度一般在 ℃ 时间为4~6h。 。 烘胶温度不宜过高, 烘胶温度不宜过高,否则会影响橡胶的物理 机械性能。 机械性能。 2.切胶 . 用切胶机将生胶切成小块, 用切胶机将生胶切成小块,每块重量视胶种 而异, 每块 每块10~20kg,CR每块不超过 每块不超过10kg。 而异,NR每块 , 每块不超过 。 3.破胶 . 橡胶块需用破胶机破胶,以便塑炼。 橡胶块需用破胶机破胶,以便塑炼。破胶辊 距一般为2~3mm,辊温控制在45℃以下。 距一般为 ,辊温控制在 ℃以下。
塑料工艺2—生胶的塑炼原理和可塑性的测定方法

(二)塑炼原理 生胶的分子量与可塑性有着密切的 关系。分子量越小,可塑性就越大。 关系。分子量越小,可塑性就越大。生 胶经过机械塑炼后,分子量降低, 胶经过机械塑炼后,分子量降低,粘度 下降,可塑性增大。由此可见, 下降,可塑性增大。由此可见,生胶在 塑炼过程中, 塑炼过程中,可塑性的提高是通过分子 量的降低来实现的。 量的降低来实现的。
h0 —试样原始高度,mm;h1—试样 试样原始高度, 试样原始高度 ; 试样 压缩3min后的高度,mm;h2—恢复 后的高度, 压缩 后的高度 ; 恢复 3min后的高度,mm 后的高度, 后的高度 如果试样为绝对流体, 如果试样为绝对流体,即h1=h2=0, , P=1;若试样为绝对弹性体,即h2=h0, ;若试样为绝对弹性体, P=0;生胶和混炼胶为粘弹体,它们的可 ;生胶和混炼胶为粘弹体, 塑度在0~1之间,数值越大表示可塑性越 之间, 塑度在 之间 大。
门尼( 二.旋转扭力法—门尼(Mooney)粘度法 旋转扭力法 门尼 ) 原理是:在一定温度、时间和压力下, 原理是:在一定温度、时间和压力下,根据 试样在活动面(转子)与固定面(模腔)之间变 试样在活动面(转子)与固定面(模腔) 形时所受扭力来确定胶料可塑度。 形时所受扭力来确定胶料可塑度。 试验时,将试样按要求放入模腔里, 试验时,将试样按要求放入模腔里,在100℃ ℃ 下预热1min,使转子在 速度转动4min,所 下预热 ,使转子在2r/min速度转动 速度转动 , 测的扭力值即为门尼粘度,一般用M表示 表示, 表示 测的扭力值即为门尼粘度,一般用 表示,L表示 用大转子(直径为38.1±0.03mm)。 用大转子(直径为 ± )。 门尼粘度法比压缩法迅速简便, 门尼粘度法比压缩法迅速简便,且表示的动 态流动性更接近于工艺实际情况。 态流动性更接近于工艺实际情况。
第三章 塑炼混炼
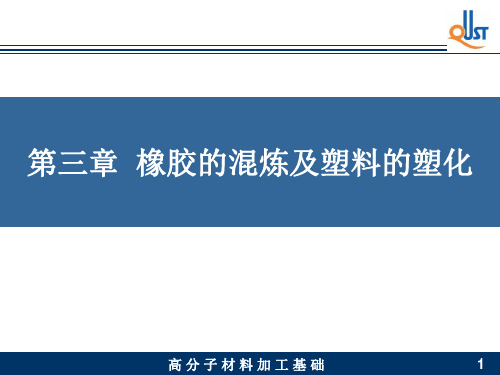
(-)混炼理论
混炼不是生胶和配合剂简单的机械混合过程,混 炼胶也不是生胶与配合剂的简单机械混合物; 混炼的实质是橡胶的改性过程。期间,机械力/化 学反应起着重要作用; 混炼胶是由生胶和各种配合剂组成的一种复合体。
(1)、准备工作
为了便于塑炼 加工,生胶需 要经过烘胶、
切胶和破胶等
塑炼前的准备 工艺。
生胶,长期储存后,粘度很高, 且在冬天常因结晶而硬化。 切胶后的NR、CR一 为便于使用,把烘好的 在切胶和塑炼前把生胶放在烘房 般要在破胶机上进 大胶包用切胶机切成小 中预先对胶包进行加温,便于切 行破胶,以便进行 块 割和进一步的加工。 塑炼。 烘胶的温度和时间视生胶的种类 与季节而定。
高分子材料加工基础 18
2、塑炼的原理
熔体粘度——加工温度、切变速率、分子量。 分子量越小,可塑度越大。生胶经机械塑炼后, 分子量降低,粘度下降,可塑性增加。 生胶在塑炼过程中可塑性的提高是通过分子量的
降低来实现的。
塑炼的实质是使橡胶大分子链断裂,大分子链由
长变短的过程。
高分子材料加工基础
高分子材料加工基础 6
工作原理:
两个辊筒以不同的表面速度
相对回转,物料由于与辊筒
表面的摩擦和粘附作用,以
及物料之间的粘接作用,被
拉入两辊筒之间的间隙之内。
高分子材料加工基础
7
工作原理:
受到强烈的挤压与剪切,使物料在辊隙内形成楔形 断面的料片,从辊隙中排出的料片由于两个辊筒表 面速度和温度的差异而包在一个辊筒上,重新返回 两辊间。
高分子材料加工基础
21
剪切力作用于橡胶时,分子链将沿流动方向伸展;
常见生胶塑炼

常见生胶的塑炼
a) 投料:开炼机塑炼及混炼时,所有生胶、母胶、并用胶,须在靠炼胶机大齿轮一则加入。
b) 根据各种不同的生胶性能,应采用不同的塑炼方法,具体如下:
1) 天然胶:一段塑炼:以0.5~1mm辊距将生胶破开,薄通落盘,如此重复过机到规定时间或次数。
一般为10~15min,具体视可塑度要求适当增减时间次数,然后打三角包,停放
4~8h冷却,以待二段塑炼或使用。
二段塑炼:将一段塑炼的生胶包辊后,调节辊距到5mm,将生胶连续从左到右和从右到左地切割倒合三次以上或到规定时间为止,若与一段连续塑炼为5min,单独二段为10~15min,然后下片冷却,停放4h以上,混炼备用。
常规辊温45℃左右,可塑度要求
0.45以上。
注:低硬度(50°以下)胶料生胶(包括其它胶种)塑炼需分二段到三段塑炼,若为二段塑炼,则进行两次一段塑炼;若为三段塑炼,则进行两次一段和一次二段塑炼。
每段之间胶料需停放4h以上冷却,确保生胶可塑度及混炼时配合剂的分散。
2) 丁腈胶:宜采用低温、小辊距、低容量的塑炼方法。
辊距2~3mm,塑炼时间20~30min,操作与天然胶基本相同。
3) 丁苯、丁基胶:混炼前不需塑炼,若特殊需要则薄通几次,丁基胶要注意清洁,严防其它胶混入,影响质量。
4) 顺丁胶:顺丁胶的塑炼对可塑度变化不大,塑炼只为方便操作,可适当过薄通。
5) 氯丁胶:氯丁胶不宜长时间塑炼,宜短时间、低温度塑炼,辊距5~6mm过胶3~4次,小辊距薄通10~15min,5~6mm辊距下片,辊温40~50℃。
c) 塑炼好的生胶,应检验可塑度(衡量胶料操作性能及影响后继工艺质量的标准),合格才能使用。
生胶的塑炼工艺
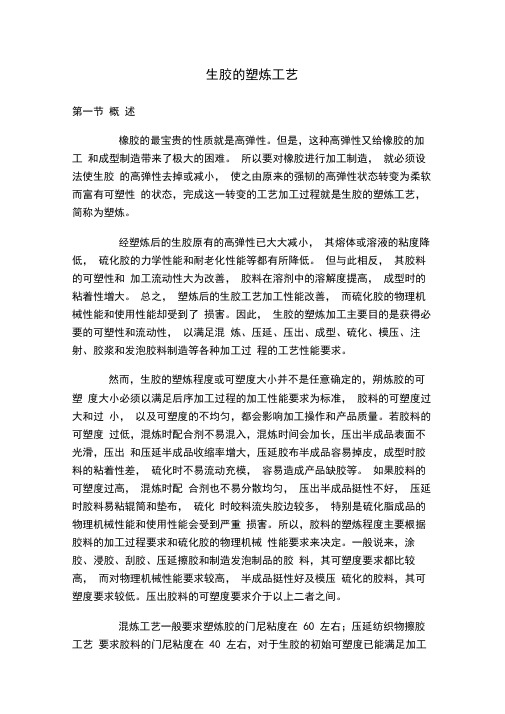
生胶的塑炼工艺第一节概述橡胶的最宝贵的性质就是高弹性。
但是,这种高弹性又给橡胶的加工和成型制造带来了极大的困难。
所以要对橡胶进行加工制造,就必须设法使生胶的高弹性去掉或减小,使之由原来的强韧的高弹性状态转变为柔软而富有可塑性的状态,完成这一转变的工艺加工过程就是生胶的塑炼工艺,简称为塑炼。
经塑炼后的生胶原有的高弹性已大大减小,其熔体或溶液的粘度降低,硫化胶的力学性能和耐老化性能等都有所降低。
但与此相反,其胶料的可塑性和加工流动性大为改善,胶料在溶剂中的溶解度提高,成型时的粘着性增大。
总之,塑炼后的生胶工艺加工性能改善,而硫化胶的物理机械性能和使用性能却受到了损害。
因此,生胶的塑炼加工主要目的是获得必要的可塑性和流动性,以满足混炼、压延、压出、成型、硫化、模压、注射、胶浆和发泡胶料制造等各种加工过程的工艺性能要求。
然而,生胶的塑炼程度或可塑度大小并不是任意确定的,朔炼胶的可塑度大小必须以满足后序加工过程的加工性能要求为标准,胶料的可塑度过大和过小,以及可塑度的不均匀,都会影响加工操作和产品质量。
若胶料的可塑度过低,混炼时配合剂不易混入,混炼时间会加长,压出半成品表面不光滑,压出和压延半成品收缩率增大,压延胶布半成品容易掉皮,成型时胶料的粘着性差,硫化时不易流动充模,容易造成产品缺胶等。
如果胶料的可塑度过高,混炼时配合剂也不易分散均匀,压出半成品挺性不好,压延时胶料易粘辊筒和垫布,硫化时皎料流失胶边较多,特别是硫化脂成品的物理机械性能和使用性能会受到严重损害。
所以,胶料的塑炼程度主要根据胶料的加工过程要求和硫化胶的物理机械性能要求来决定。
一般说来,涂胶、浸胶、刮胶、压延擦胶和制造发泡制品的胶料,其可塑度要求都比较高,而对物理机械性能要求较高,半成品挺性好及模压硫化的胶料,其可塑度要求较低。
压出胶料的可塑度要求介于以上二者之间。
混炼工艺一般要求塑炼胶的门尼粘度在60 左右;压延纺织物擦胶工艺要求胶料的门尼粘度在40 左右,对于生胶的初始可塑度已能满足加工性能要求的生胶,一般不需再行塑炼加:正,可以直接进行混炼。
生胶的塑炼工艺
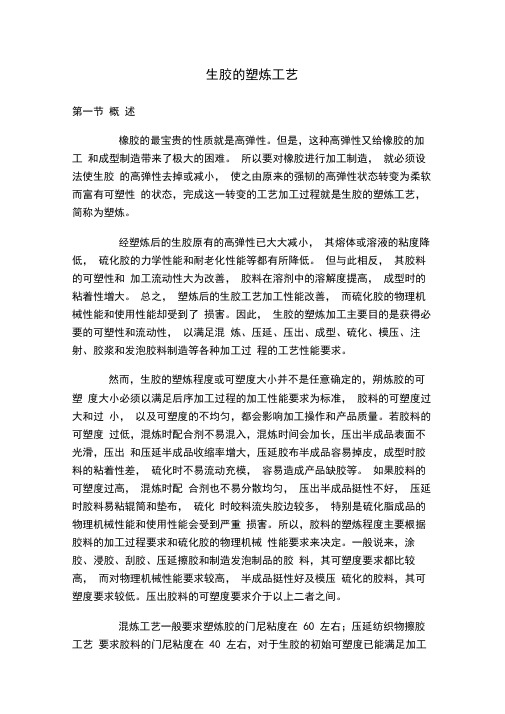
生胶的塑炼工艺第一节概述橡胶的最宝贵的性质就是高弹性。
但是,这种高弹性又给橡胶的加工和成型制造带来了极大的困难。
所以要对橡胶进行加工制造,就必须设法使生胶的高弹性去掉或减小,使之由原来的强韧的高弹性状态转变为柔软而富有可塑性的状态,完成这一转变的工艺加工过程就是生胶的塑炼工艺,简称为塑炼。
经塑炼后的生胶原有的高弹性已大大减小,其熔体或溶液的粘度降低,硫化胶的力学性能和耐老化性能等都有所降低。
但与此相反,其胶料的可塑性和加工流动性大为改善,胶料在溶剂中的溶解度提高,成型时的粘着性增大。
总之,塑炼后的生胶工艺加工性能改善,而硫化胶的物理机械性能和使用性能却受到了损害。
因此,生胶的塑炼加工主要目的是获得必要的可塑性和流动性,以满足混炼、压延、压出、成型、硫化、模压、注射、胶浆和发泡胶料制造等各种加工过程的工艺性能要求。
然而,生胶的塑炼程度或可塑度大小并不是任意确定的,朔炼胶的可塑度大小必须以满足后序加工过程的加工性能要求为标准,胶料的可塑度过大和过小,以及可塑度的不均匀,都会影响加工操作和产品质量。
若胶料的可塑度过低,混炼时配合剂不易混入,混炼时间会加长,压出半成品表面不光滑,压出和压延半成品收缩率增大,压延胶布半成品容易掉皮,成型时胶料的粘着性差,硫化时不易流动充模,容易造成产品缺胶等。
如果胶料的可塑度过高,混炼时配合剂也不易分散均匀,压出半成品挺性不好,压延时胶料易粘辊筒和垫布,硫化时皎料流失胶边较多,特别是硫化脂成品的物理机械性能和使用性能会受到严重损害。
所以,胶料的塑炼程度主要根据胶料的加工过程要求和硫化胶的物理机械性能要求来决定。
一般说来,涂胶、浸胶、刮胶、压延擦胶和制造发泡制品的胶料,其可塑度要求都比较高,而对物理机械性能要求较高,半成品挺性好及模压硫化的胶料,其可塑度要求较低。
压出胶料的可塑度要求介于以上二者之间。
混炼工艺一般要求塑炼胶的门尼粘度在60 左右;压延纺织物擦胶工艺要求胶料的门尼粘度在40 左右,对于生胶的初始可塑度已能满足加工性能要求的生胶,一般不需再行塑炼加:正,可以直接进行混炼。
- 1、下载文档前请自行甄别文档内容的完整性,平台不提供额外的编辑、内容补充、找答案等附加服务。
- 2、"仅部分预览"的文档,不可在线预览部分如存在完整性等问题,可反馈申请退款(可完整预览的文档不适用该条件!)。
- 3、如文档侵犯您的权益,请联系客服反馈,我们会尽快为您处理(人工客服工作时间:9:00-18:30)。
因此,低温塑炼和高温塑炼的机理是不同的。低温 塑炼时,主要是由机械破坏作用使橡胶分子断链;高温 塑炼时,主要是由氧的氧化裂解作用使橡胶分子链降解。
3、机械力对塑炼的影响
橡胶置于炼胶机中塑炼时,会受到炼胶机辊筒间的剪切 力作用,分子链会被拉直,并使子链分子链在中间部位发生 断裂: R-R→R·+R·
③分段塑炼法是当塑炼胶可塑性要求较高,用一次塑炼 或薄通塑炼达不到目的时,而采用的一种有效方法。先 将生胶塑炼一定时间(约15min),然后下片冷却并停放 4~8h,再进行第二次塑炼,这样反复塑炼数次,直至达 到可塑性要求为止。根据不同的可塑性要求,一般可分 为两段塑炼或三段塑炼。对天然橡一段塑炼胶威氏可塑 度可达0.3左右,二段塑炼胶可达0.45左右,三段塑炼胶 可达0.55左右。这种塑炼方法的生产效率高,塑炼胶可 塑性高且均匀,因而生产中应用较为广泛。但生产管理 较麻烦,占地面积大,不适合连续化生产。
三、塑炼机理
生胶塑炼机理一是机械作用使分子链断裂;二是氧 的作用使分子链氧化裂解。橡胶在塑炼过程中上述两种 情况同时存在,只是低温时以机械断裂为主,高温时以 氧化裂解为主。 1.低温塑炼机理 (1)无化学塑解剂 第一步,橡胶分子链受机械作 用断裂生成自由基。 R-R→2 R·
第二步,橡胶分子自由基被空气中的氧氧化成为橡胶过 氧化自由基,过氧化自由基在室温下很不稳定,易夺取 橡胶分子或其它物质中的氢原子而失去活性,生成分子 量较小的稳定的橡胶氢过氧化物而获得塑炼效果。 R·+O2→ROO· ROO·+RH→ROOH+R· 上述反应说明,氧是橡胶自由基的接受体,起到了 阻聚炼效果好,所得塑炼胶的可塑性较高 且均匀,同时,对各种橡胶,特别是用机械塑炼效果差 的一些合成橡胶(如丁腈橡胶)都适用,因而在实际生产中 应用广泛。其主要缺点是生产效率较低。 ②一次塑炼法也称包辊塑炼法,是将生胶在较大辊距(5~ 10mm)下包辊后连续过辊进行塑炼,直至所规定的时间 为止。在塑炼过程中不经过停放,且多次割刀以利于散 热及获得均匀的可塑性。此法适用于并用胶的掺合及易 包辊的合成橡胶。这种方法的塑炼时间较短、操作方 便、劳动强度低,但塑炼效果不够理想,表现在可塑性 增加幅度小,塑炼胶可塑性不够均匀等。
§3.4开炼机塑炼
生胶塑炼方法有热塑炼和机械塑炼等多种方法,但 目前广泛采用的是机械塑炼方法。按所用设备可分为开 炼机塑炼、密炼机塑炼和螺杆塑炼机塑炼三种。 一、开炼机 开炼机塑炼是最早使用的一种塑炼方法。它是将生 胶置于开炼机辊筒之间,借助辊筒的剪切力作用使橡胶 分子链受到拉伸断裂,从而获得可塑性。这种方法的劳 动强度大、生产效率较低、操作条件差,但塑炼胶可塑 性均匀、热可塑性小,适应面宽,比较机动灵活,投资 较小。因此,适用于胶种变化较多、耗胶量较少的场合。
2.高温塑炼机理 无化学塑解剂 高温塑炼时,橡胶分子与氧可直接进行 氧化反应,致使橡胶分子链降解。这种热氧化裂解过程 属于自动催化氧化连锁反应,分三步进行。 第一步,链引发。氧夺取橡胶分子链上的氢原子生成自 由基: RH+O2→R·+HOO·
第二步,链增长。橡胶分子链自由基与体系中的其它橡 胶分子产生一系列的氧化反应,生产橡胶分子氢过氧化 物: R·+O2→ROO· ROO·+RH→ROOH+R· R·+O2→ROO· ROO·+RH→…… 第三步,链终止。橡胶分子氢过氧化物在高温下极不稳 定,立即分解生产分子量较小的稳定分子: ROOH→分子链较短的稳定产物。
§3.3生胶塑炼前的准备工艺
在各类橡胶制品制造工艺过程中,其塑炼工艺流程可以 分为以下几个阶段,如图所示
烘胶 生胶 切胶 烘胶 切胶
破胶
塑
炼
可塑性 检查
生胶塑炼工艺主要有准备工序(Ⅰ)、塑炼工序(Ⅱ) 和可塑性检查工序(Ⅲ)三个环节组成
一、烘胶 生胶原料大多为大块状(如天然橡胶的胶包质量一般 为50~l00kg),且在常温下粘度很高,难于切割和进 一步加工,尤其在冬天,生胶常呈硬化或结晶。因此, 对生胶进行加温软化或解除结晶,便于切割,给加工带 来方便。 烘胶设备可分为烘房、烘箱、红外线、高频电流 等。烘房适用于大规模生产;烘箱适用于小规模生产以 及科研部门和实验室试验;红外线和高频电流则适用于 先进的工业生产。
目前我国橡胶制品生产中有“先烘胶后切胶”及“先 切胶后烘胶”两种准备工艺。“先烘胶后切胶”方法, 切胶容易、、速度快、动力消耗较少、切胶机易损 伤程度小,但烘胶胶温的均匀性较差,烘胶时间较 长。“先切胶后烘胶”方法,烘胶胶温的均匀性好,烘 胶时间短(一般为10~24h),但动力消耗较大,切胶 机易损伤程度较大。上述两种方法,应根据生产实 际情况,合理选择。
其规格通常以前辊的直径大小来表示。 如 X K—360 X—橡胶用的设备 S—塑料用设备 (K/ M ) K—开炼机 M—密炼机 360—辊筒直径,mm
二、开炼机塑炼工艺
1:塑炼操作方法 开炼机塑炼通常有薄通塑炼、一次塑 炼、分段塑炼(包辊法)及添加化学塑解剂塑炼等方法。 ①薄通塑炼法是将生胶在辊距0.5~lmm下通过辊缝,不包 辊薄通落盘,重复薄通至规定次数或时间,直至获得所需 要的可塑性为止。
采用烘房烘胶,天然橡胶的烘胶温度为50-60℃, 加温时间在春、夏、秋季一般为24~48h,冬季一般为 36~72h;氯丁橡胶的烘胶温度为50~60℃,时间为 150~180min,或烘胶温度为24~40℃,时间为4~ 6h。烘胶温度不宜过高,否则会引起橡胶老化而影响 物理机械性能。
二、切胶
自烘房取出的大块生胶用切胶机切割成小块,以便 于塑炼。天然橡胶切胶胶块一般为l0~20kg。氯丁橡胶 一般每块不超过10kg,其它合成橡胶一般每块10-15kg。 切胶胶块最好呈三角棱形,以便破胶时顺利进入辊缝。 在切胶前原则上应除去天然橡胶和合成橡胶的胶包 外皮及包装塑料薄膜(对于中低级制品可以不除去胶包外 皮和包装塑料薄膜)或清除胶块表面杂质。切胶胶块不应 落地,以防污染。
§3.2塑炼原理
一、塑炼方法
1、物理增塑法是利用低分子增塑剂对生胶的物理溶胀作用 来减小大分子之间的相互作用力,降低生胶的黏度,可塑性 和流动性得到改善。 2、化学增塑法是利用某些化学塑解剂对生胶大分子链的化 学破坏作用来减小弹性和黏度,提高可塑性和流动性。 3、机械塑炼法是利用机械剪切力、温度、空气中氧的作用, 使生胶大分子链 断裂、变短,从而获得理想可塑性。机械塑 炼法有低温和高温塑炼之分,密炼机和螺杆塑炼机属于高温机 械塑炼,开炼机塑炼属于低温机械塑炼。
5、塑解剂对塑炼的影响 橡胶塑炼工艺中,使用化学塑解剂能增强生胶塑炼效 果,缩短塑炼时间,从而提高塑炼效率。化学塑解剂在 塑炼过程中的增塑作用一是塑解剂本身受热、氧的作用 分解生成自由基,而导致橡胶分子发生氧化降解;另一 种是封闭塑炼时橡胶分子链断链的端基,使其失去活性, 阻止其重新结聚。 根据化学塑解剂的使用温度范围,可分为低温塑解 剂,如二甲苯基硫酚、五氯硫酚,适用于开炼机塑炼;高 温塑解剂,如二甲苯基二硫化物,适用于密炼机塑炼;混 合型塑解剂,如促进剂M、DM等,在低温和高温下均有 效,即适用于开炼机又适用于密炼机塑炼。
三、破胶 天然橡胶和氯丁橡胶的切胶胶块,在塑炼前需用破胶 机进行破胶,以提高塑炼效率。其它合成橡胶切胶胶块, 一般无需破胶而直接进行塑炼(或混炼)。 破胶机的辊筒粗而短,表面有沟纹,两辊速比较大, 辊距一般为2~3mm,辊温控制在45℃以下。氯丁橡胶破 胶宜用30~35℃辊温,先在5~6mm辊距下通过。然后, 再在2~3mm辊距下通过。破胶时要连续投料,不宜中 断,以防胶料弹出伤人。破胶容量应适当控制。 目前生产中常将破胶和塑炼一起用开炼机连续进行,而 不专门用破胶机破胶。
二、塑炼的意义 1、使生胶的可塑性增大,以利混炼时配合剂的混入和均 匀分散; 2、改善胶料的流动性,便于压延、压出操作,使胶坯形 状和尺寸稳定; 3、增大胶料粘着性,方便成型操作; 4、提高胶料在溶剂中的溶解性,便于制造胶浆,并降低 胶浆粘度使之易于渗入纤维孔眼,增加附着力; 5、改善胶料的充模性,使模型制品的花纹饱满清晰; 6、改善橡胶的共混性,利于不同黏度的生胶均匀混合 。
第三章 生胶塑炼
安徽理工大学材料科学与工程学院 高分子材料与工程专业 丁国新
§3.1概述
一、基本概念 橡胶制品的基本工艺过程: 塑炼→混炼→压延、压出→成型→硫化 塑炼:借助机械功或热能使橡胶软化为具有一定 可塑性的均匀物的工艺过程称之为塑炼。 塑炼胶:指经过塑炼获得一定可塑性的胶料。 可塑性:指橡胶受外力作用产生变形,当外力消 除后橡胶仍能保持其形变的能力。
橡胶塑炼时,分子链断裂的几率与作用于橡胶分子链上 的机械功(剪切力)成正比,而与胶料温度成反比。温度越低, 橡胶分子间内聚力越大,切应力越大,机械断链效果越好;反 之,温度越高,橡胶分子间内聚力越小,切应力越小,机械断 链效果则越差。
4、静电对塑炼的影响
塑炼时,生胶受到炼胶机的剧烈摩擦而产生静电。实验测 定,辊筒或转子的金属表面与橡胶接触处产生的平均电位差在 2000~6000V之间,个别可达15000V。因此,使辊筒和堆积 胶间经常有电火花产生。这种放电作用促使生胶表面的氧激发 活化,生成原子态氧和臭氧,从而提高氧对橡胶分子链的断链 作用。
2、温度对塑炼的影响
温度对生胶的塑炼效果有着重 要的影响,不同温度范围对塑 炼的作用是不同的。实验表 明,天然橡胶在50~150℃范 围内塑炼30min后,得到一条 近于“U”型的曲线,如图所示。
天然橡胶塑炼过程所得“U”型曲线可以认为是由两条 不同曲线组合而成,并代表两个独立过程,在最低值附 近相交。其中1线代表低温塑炼,2线代表高温塑炼。 低温时,主要是靠机械破坏作用引起橡胶分子链的 降解而获得塑炼效果。随着塑炼温度的不断升高,橡胶 由硬变为柔软,分子链在机械力作用下容易产生滑动而 难以被扯断,因而塑炼效果不断下降,在110℃附近达到 最低值。此时由氧直接引发的氧化破坏作用也很小。 但是当温度超过110℃以上再继续升高时,虽然机械 破坏作用进一步降低,但由于氧的自动催化氧化破坏作 用随着温度升高而急剧增大,橡胶分子链的氧化降解速 度大大加快,塑炼效果也迅速增大。