机械风险评估及安全方案
机械安全风险评价的方法

机械安全风险评价的方法机械安全风险评价是指通过系统性的方法评估机械设备在使用过程中可能存在的安全风险,以便采取相应的安全措施和管理措施,保障人员的生命安全和财产安全。
下面将介绍几种常用的机械安全风险评价方法。
1. 故障树分析法(FTA):该方法通过以事件为导向的树形结构图来分析故障发生的可能性和原因,用于评估机械设备发生事故的概率。
首先确定可能导致事故的基本事件,然后逐层分析事件的起因和后果,最后确定导致事故的最终原因。
通过该方法可以定量评估故障产生的概率和危害程度,为制定预防措施提供依据。
2. 危险性与可操作性研究(HAZOP):该方法通过系统性的分析机械设备可能存在的危险性和操作问题,以评估设备的安全性和可操作性。
通过将设备的各种可能性的操作情况与设备的设计和工艺标准进行对照,识别出可能导致危险的操作情况,并评估其发生的概率和影响程度。
同时,该方法还提供了改进设备安全性和可操作性的建议。
3. 偏差分析方法(FMEA):该方法通过系统性地识别机械设备的潜在故障模式和影响,评估故障的严重程度和概率,并采取相应的预防措施和纠正措施。
首先识别可能的故障模式和原因,然后评估故障的概率、严重程度和影响,最后采取相应的风险控制措施。
通过应用该方法可以减少事故的发生概率,提高设备的安全性。
4. 事件树分析法(ETA):该方法通过以事件为导向的树形结构图来分析事故发生的可能性和影响,以评估机械设备的风险程度。
首先识别可能导致事故的基本事件,然后逐层分析事件的发生概率和影响,最后确定事故的最终结果。
通过应用该方法可以定量评估事故发生的概率和危害程度,为制定相应的控制措施提供依据。
上述几种方法主要是通过系统性的分析和评估机械设备的各种可能的风险,从而确定可能导致事故发生的概率和危害程度,并为制定相应的安全措施和管理措施提供依据。
在实际应用中,可以根据具体情况选择合适的评价方法,也可以结合多种方法进行综合评估,以提高评估的准确性和可靠性。
机械安全风险评价

相应的控制措施,避免或减少因设备故障或操作失误导致的安全事故,
保障操作人员的生命安全。
02
提高设备可靠性
通过机械安全风险评价,可以发现设备的设计、制造、安装和使用过程
中存在的问题和不足,及时采取改进措施,提高设备的可靠性和稳定性
,延长设备的使用寿命。
03
促进企业可持续发展
机械安全风险评价有助于企业提高机械设备的管理水平,减少因设备故
老化
可能导致设备性能下降、功能丧失等。
疲劳
可能导致设备断裂、失效等。
腐蚀
可能导致设备损坏、失效等。
机械设备的操作过程识别
01
02
03
启动过程
需要检查设备是否处于安 全状态,避免因误操作导 致危险。
运行过程
需要遵守操作规程,避免 因违规操作导致危险。
停止过程
需要按照操作规程逐步停 止设备,避免因急停导致 危险。
04
机械安全风险评价流程
确定评价目标
明确评价对象
确定需要评价的机械设备 的类型、用途、使用环境 等。
确定评价范围
明确评价所涉及的机械设 备的范围,包括设备数量 、分布、使用频率等。
确定评价目标
明确评价的目的和要求, 例如确定机械设备是否存 在安全隐患,是否需要采 取措施进行风险控制等。
收集相关资料
为了规范机械安全风险评价的管理和实施,需要完善相关的法规和标准,为机械安全风 险评价提供更加明确的指导和依据。
THANKS
谢谢您的观看
更新计划
根据评价结果,制定机械设备的更新计划,对性能落后、技术陈旧、存在安全隐患的机械 设备进行更新换代,提高机械设备的整体安全性能。
技术升级
根据评价结果,对机械设备进行技术升级,引入新技术、新工艺、新材料等,提高机械设 备的性能和安全性。
机械安全风险评定范本(2篇)

机械安全风险评定范本一、引言机械设备在生产和日常生活中都扮演着重要的角色,然而,机械设备的使用过程中也存在着各种潜在的安全风险。
为了确保机械设备的安全可靠运行,必须进行全面的风险评定。
本文将介绍一种机械安全风险评定的范本,帮助组织和个人在使用机械设备时识别和管理风险,以减少潜在的事故和伤害。
二、背景机械设备安全风险评定是一种系统性的方法,用于识别和评估机械设备使用过程中可能存在的风险和危险。
通过对机械设备的分析和评估,可以确定机械设备的安全性能,并采取相应的控制措施和管理策略,以减少事故和伤害的发生。
三、风险评定范本1. 识别潜在风险在机械设备的使用过程中,需要对可能存在的潜在风险进行识别和分析。
例如,机械设备的工作原理、操作方式、工作环境等方面都可能存在一定的安全风险。
通过对这些方面进行详细的分析,可以有效地确定潜在风险。
2. 评估风险等级在识别潜在风险之后,需要评估这些风险的等级。
评估风险等级可以根据风险的可能性和影响程度进行综合分析。
可能性可以根据机械设备的工作条件、工作环境和人员操作等因素进行评估,影响程度可以根据潜在风险对人员和设备的伤害程度进行评估。
3. 确定控制措施在评估风险等级之后,需要根据风险等级确定相应的控制措施。
控制措施可以包括技术措施、管理措施和个人防护措施等方面。
技术措施可以通过改进机械设备的设计和工作方式来减少潜在风险;管理措施可以通过制定相关的操作规程和安全管理制度来规范人员的操作行为;个人防护措施可以通过提供合适的个人防护装备和培训人员的安全意识来保障人员的安全。
4. 实施控制措施在确定控制措施之后,需要将这些措施付诸实施。
实施控制措施需要建立相应的机制和流程,确保措施的有效性和可持续性。
例如,要建立机械设备的维护和检修制度,定期对设备进行维护和检修,确保设备的正常运行。
5. 监督和改进在实施控制措施之后,还需要进行监督和改进。
监督可以通过定期检查和现场巡查等方式进行,及时发现和解决存在的问题。
机械伤害安全风险评估
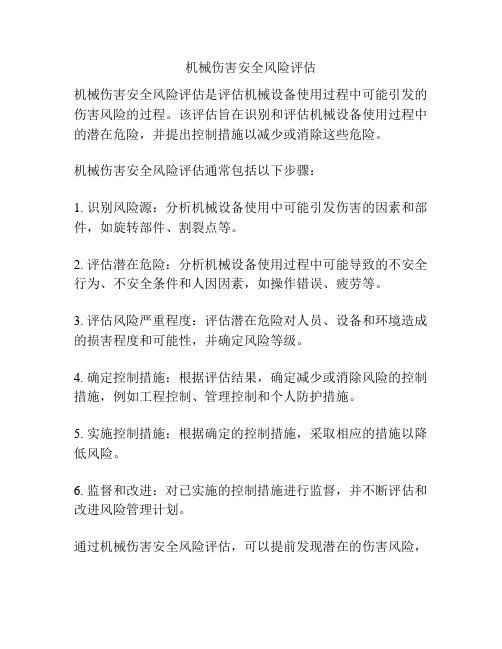
机械伤害安全风险评估
机械伤害安全风险评估是评估机械设备使用过程中可能引发的伤害风险的过程。
该评估旨在识别和评估机械设备使用过程中的潜在危险,并提出控制措施以减少或消除这些危险。
机械伤害安全风险评估通常包括以下步骤:
1. 识别风险源:分析机械设备使用中可能引发伤害的因素和部件,如旋转部件、割裂点等。
2. 评估潜在危险:分析机械设备使用过程中可能导致的不安全行为、不安全条件和人因因素,如操作错误、疲劳等。
3. 评估风险严重程度:评估潜在危险对人员、设备和环境造成的损害程度和可能性,并确定风险等级。
4. 确定控制措施:根据评估结果,确定减少或消除风险的控制措施,例如工程控制、管理控制和个人防护措施。
5. 实施控制措施:根据确定的控制措施,采取相应的措施以降低风险。
6. 监督和改进:对已实施的控制措施进行监督,并不断评估和改进风险管理计划。
通过机械伤害安全风险评估,可以提前发现潜在的伤害风险,
并采取控制措施来确保操作人员和设备的安全。
这可以帮助企业降低事故发生的可能性,提高工作场所的安全性。
机械设备维护风险评估及应对方案

机械设备维护风险评估及应对方案一、风险评估在进行机械设备维护过程中,可能会遇到多种风险,这些风险可能会影响设备维护的效果,甚至可能对设备造成损坏。
以下是常见的风险及其可能造成的后果:1.1 操作风险操作风险主要包括操作不当、操作失误等,可能会导致设备损坏、维护效果不佳,甚至可能对操作人员造成伤害。
1.2 工具和设备风险维护过程中使用的工具和设备可能存在质量问题或者使用不当,可能会对设备造成损害,影响维护效果。
1.3 物料风险维护过程中使用的物料可能存在质量问题或者不兼容,可能会对设备造成损害,影响维护效果。
1.4 环境风险维护环境可能存在一定的风险,如温度、湿度、灰尘等,可能会影响维护效果,甚至可能对设备造成损害。
1.5 知识技能风险维护人员可能存在知识技能不足,可能会导致维护效果不佳,甚至可能对设备造成损害。
二、应对方案针对以上风险,我们可以采取以下应对方案,以降低风险,提高维护效果:2.1 操作风险应对- 对操作人员进行严格的培训,确保其掌握正确的操作方法。
- 设立操作规程,要求操作人员严格遵守。
2.2 工具和设备风险应对- 选择高质量的维护工具和设备,确保其安全可靠。
- 定期对维护工具和设备进行检查和维护,确保其处于良好的工作状态。
2.3 物料风险应对- 选择质量可靠的物料,确保其与设备兼容。
- 对物料进行严格的检查,确保其符合维护要求。
2.4 环境风险应对- 控制维护环境,确保其满足设备维护的要求,如温度、湿度、灰尘等。
- 设立环境监测机制,及时发现环境问题并采取措施。
2.5 知识技能风险应对- 对维护人员进行定期的培训和考核,确保其具备足够的知识技能。
- 鼓励维护人员进行自主学习和交流,提高其知识技能水平。
三、总结机械设备维护过程中存在多种风险,我们需要通过严格的操作规程、高质量的维护工具和设备、可靠的物料、良好的维护环境以及具备足够知识技能的维护人员来降低风险,提高维护效果。
机械设计中的安全性与风险评估
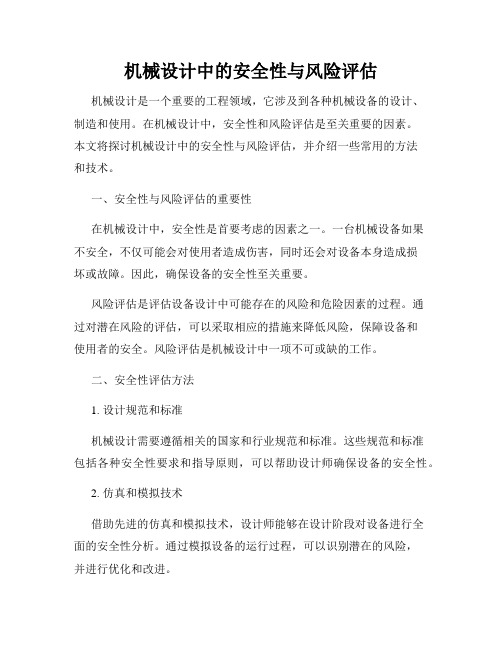
机械设计中的安全性与风险评估机械设计是一个重要的工程领域,它涉及到各种机械设备的设计、制造和使用。
在机械设计中,安全性和风险评估是至关重要的因素。
本文将探讨机械设计中的安全性与风险评估,并介绍一些常用的方法和技术。
一、安全性与风险评估的重要性在机械设计中,安全性是首要考虑的因素之一。
一台机械设备如果不安全,不仅可能会对使用者造成伤害,同时还会对设备本身造成损坏或故障。
因此,确保设备的安全性至关重要。
风险评估是评估设备设计中可能存在的风险和危险因素的过程。
通过对潜在风险的评估,可以采取相应的措施来降低风险,保障设备和使用者的安全。
风险评估是机械设计中一项不可或缺的工作。
二、安全性评估方法1. 设计规范和标准机械设计需要遵循相关的国家和行业规范和标准。
这些规范和标准包括各种安全性要求和指导原则,可以帮助设计师确保设备的安全性。
2. 仿真和模拟技术借助先进的仿真和模拟技术,设计师能够在设计阶段对设备进行全面的安全性分析。
通过模拟设备的运行过程,可以识别潜在的风险,并进行优化和改进。
3. 故障模式与影响分析(FMEA)FMEA是一种常用的风险评估方法,它通过识别潜在的故障模式和评估其对设备运行和使用的影响来评估设备的风险。
通过对可能的故障模式的分析,设计师可以制定相应的预防措施。
三、风险评估技术1. 安全性验证安全性验证是一种通过实际测试和试验来验证设备的安全性的方法。
通过对设备进行全面的测试,可以评估其在不同工作条件下的安全性能,并对可能存在的风险进行评估。
2. 可靠性分析通过对设备的可靠性进行分析,可以识别可能的故障点和故障模式,并评估其对设备功能和安全性的影响。
可靠性分析可以帮助设计师制定相应的改进和优化方案,提高设备的安全性和可靠性。
3. 人因工程分析人因工程分析可以评估设备设计对人类使用者的适应性和易用性。
通过分析人机交互过程中的潜在问题和风险,可以改善设备的安全性和人机界面。
四、案例研究:汽车碰撞安全作为机械设计中安全性与风险评估的重要应用领域之一,汽车碰撞安全旨在通过设计和制造更安全的汽车来降低碰撞事故对乘客和行人的伤害。
机械安全 风险评估与风险减小

详细信息
关于机器的描述
使用说明书(技术资料等)机械的预期说明,包括:机械整个生命周期各阶段的描述设计图样或确定机械特性的其他方法所要求的能源及其提供方式类似机械的先前设计方面的文件可获得的机械使用信息
法规、标准及其他适用的文件
适用法规相关标准相关技术规范相关安全数据表
使用经验
现有的或类似机械的任何事故、事件或故障历史由排放物(噪声、振动、粉尘、烟雾等)、使用的化学品或机械加工物料等所引起的损害健康的历史记录用户关于类似机器的经验,并尽可能与潜在用户进行信息交流
空间限制
运动范围人机交互的空间要求,如运行和维修期间人员交互方式,例如“人机”界面“机器-动力源”接口
时间限制
考虑机器的预定使用和可合理预见的误用时,机械和/或机器某些组件(如工具、易损的部件、机电组件)的寿命限制推荐的维修保养时间间隔
其他限制
被加工物料特性符合清洁水平要求的保养环境——推荐的最低和最高温度,机器是否能在室内或室外,干燥或潮湿气候中运行,是否能在太阳直射条件下运行,是否能耐受粉尘和潮湿环境等
机械安全风险评估与风险减小GB/T 15706
相关术语
机械(机器):由若干个零部件连接构成并具有特定应用目的的组合,其中至少有一个零、部件是可运动的,并且配备或预定配备动力系统。危险:潜在的伤害源。包括两个方面的危险:——在机器的预定使用期间,始终存在的危险(例如:危险运动部件的运动、焊接过程产生的电弧、不利于健康的姿势、噪声排放、高温)——意外出现的危险(例如:爆炸、意外启动引起的挤压危险、破裂引起的喷射、加速/减速引起的坠落)危险区:使人员暴露于危险的机械内部和/或其周围的任何空间。危险状态:人员暴露于至少具有一种危险的环境(危险区)。危险事件:能够造成伤害的事件。(发生过程可以是短时间的、也可以是长时间的)风险:伤害发生的概率与严重程度的组合。剩余风险:采取保护措施之后仍然存在的风险。充分的风险减小:至少符合法律法规的要求并考虑了现有技术水平的风险减小。
机械安全风险评估方法
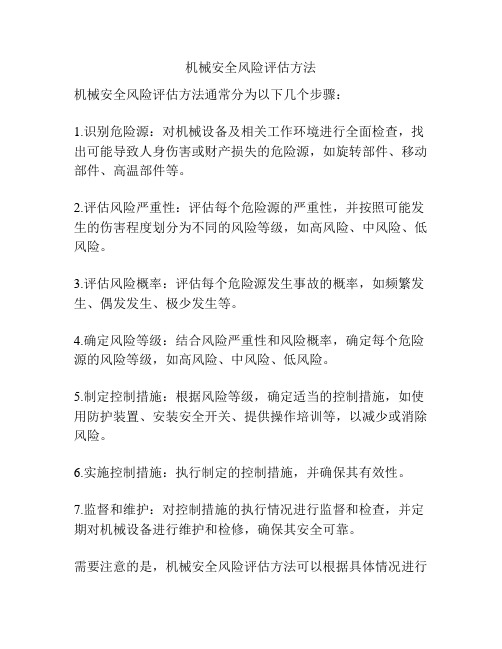
机械安全风险评估方法
机械安全风险评估方法通常分为以下几个步骤:
1.识别危险源:对机械设备及相关工作环境进行全面检查,找出可能导致人身伤害或财产损失的危险源,如旋转部件、移动部件、高温部件等。
2.评估风险严重性:评估每个危险源的严重性,并按照可能发生的伤害程度划分为不同的风险等级,如高风险、中风险、低风险。
3.评估风险概率:评估每个危险源发生事故的概率,如频繁发生、偶发发生、极少发生等。
4.确定风险等级:结合风险严重性和风险概率,确定每个危险源的风险等级,如高风险、中风险、低风险。
5.制定控制措施:根据风险等级,确定适当的控制措施,如使用防护装置、安装安全开关、提供操作培训等,以减少或消除风险。
6.实施控制措施:执行制定的控制措施,并确保其有效性。
7.监督和维护:对控制措施的执行情况进行监督和检查,并定期对机械设备进行维护和检修,确保其安全可靠。
需要注意的是,机械安全风险评估方法可以根据具体情况进行
调整和补充,以确保评估结果准确和有效。
此外,还可以参考相关的安全标准和法规,以及专业人士的建议和指导,进一步提高机械设备的安全性能。
- 1、下载文档前请自行甄别文档内容的完整性,平台不提供额外的编辑、内容补充、找答案等附加服务。
- 2、"仅部分预览"的文档,不可在线预览部分如存在完整性等问题,可反馈申请退款(可完整预览的文档不适用该条件!)。
- 3、如文档侵犯您的权益,请联系客服反馈,我们会尽快为您处理(人工客服工作时间:9:00-18:30)。
5. 机器停止时间计算服务
6. 安全系统设计
12. 安全系统交钥匙项目
Copyright © 2007 Rockwell Automation, Inc. All rights reserved.
机械安全服务周期
STEP 1 STEP 5
运行 • 检查系统是否按要求运 行,系统是否达到相关 标准的要求。 • 投入正常生产 • 预防性维护 风险评估 STEP 2 • 识别风险点,确定风险 选择减少风险的方法 等级。 • 基于风险评估、系统性 能和安全标准。
等级描述, EN 954-1
等级
要求摘要
控制器的安全相关部分的选择必 须根据最新的技术,并且可以承 受预期的运行强度,能够承受运 行过程中工作介质的影响和相关 外部环境的影响。 在等级B的基础上,必须使用具有 安全功能保证的元器件和原理
风险评估
一个故障可以导致 安全功能的丢失 一些故障依然不会 被监测出来
Example from EN 953 Enclosing
guard
Copyright © 2007 Rockwell Automation, Inc. All rights reserved.
机械防护措施
• Fixed guard
Example from EN 953
Distance Guard
3
4
Copyright © 2007 Rockwell Automation, Inc. All rights reserved.
Rockwell 机械安全服务
1. 风险评估
7. 安全系统检查
2. 危险评估
8. 弧闪评估服务
3. 机械安全培训
9. LOTO 服务
4. 安全控制回路分析
10. 一致性 / 符合性检查 11. CE 机械指令支持
可能性中的因素有哪些?
暴露的时间 人数 发生的可能性
Copyright © 2007 Rockwell Automation, Inc. All rights reserved.
风险分析
• 各种危险的描述:
摩擦, 卷入 , 刺穿, 碾压, 坠落, 稳定性, …
热的 保护不足 机械的
功能性故障
声音, 噪声
安全原则 通过元器件和安 全原理的选择。
B
1
如同等级B,但在安 全功能上更加可靠
Copyright © 2007 Rockwell Automation, Inc. All rights reserved.
等级描述, EN 954-1
等级
2
要求摘要
风险评估
安全原则
通过设计
符合等级B和1的要求,在适当的时间, 在监测中,一个故障会导致安全 控制系统必须监测安全功能 功能的丧失 通过监测故障可以被检查出来 符合等级B和1的要求,控制系统必须 按照以下步骤设计: a.一个单一的故障不会导致安全功 能的丧失。 b.通过使用适当的方法,可以监测 出单一故障(使用最新的技术) 符合等级B和1的要求,控制系统必须 按照以下步骤设计: a.控制系统中的单一故障不会导致 安全功能的丧失 b.如果可能,在下一个安全功能实 施前,单一错误可以被检测出来 c.如果b不可能实现,一个累积的故 障不会导致安全功能的丢失 如果单一故障出现,安全功能依 然可以保持 一些但不是所有的故障都可以被 监测出来 一个累积的监测不出的故障能够 导致安全功能的丧失 甚至在故障出现的时候,安全功 能总是保持 故障会被及时检测出来,以防止 安全功能的丢失
步骤四 : 采用通知和警告提示信息
固定的危险标志
创建安全工作流程
培训使用者等等
Copyright © 2007 Rockwell Automation, Inc. All rights reserved.
机械防护措施
安 全 防 护 措 施
固定防护罩 防护罩 可调试防护罩 联锁式防护罩
保护装置
Copyright © 2007 Rockwell Automation, Inc. All rights reserved.
Copyright © 2007 Rockwell Automation, Inc. All rights reserved.
安全系统: 控制电路
安全继电器
可编程安全继电器
安全PLC
Copyright © 2007 Rockwell Automation, Inc. All rights reserved.
剩余的风险 没有采用安全措施 时的风险
风险
必须要减少 的风险
真正的风险 减少
Copyright © 2007 Rockwell Automation, Inc. All rights reserved.
风险分析
危险 < ==> 风险
• 什么是危险?
– 物体或现场可能造成危害的起源
• 什么是风险?
– F (严重性 x 可能性)
Copyright © 2007 Rockwell Automation, Inc. All rights reserved.
机械防护措施
EN 294
Copyright © 2007 Rockwell Automation, Inc. All rights reserved.
机械防护措施
• Fixed guard
机械安全服务
徐 凯 Mob: 13501675568 Safety Consultant Service Manager, CSM
Copyright © 2007 Rockwell Automation, Inc. All rights reserved.
EN 1050 风险评估
危险
可接受的风险
安全
Copyright © 2007 Rockwell Automation, Inc. All rights reserved.
机械防护措施
EN 294
Copyright © 2007 Rockwell Automation, Inc. All rights reserved.
机械防护措施
• Fixed guard
步骤一: 步骤一:通过设计减少风险
通过设计来避免 危险的接近
Copyright © 2007 Rockwell Automation, Inc. All rights reserved.
步骤二: 步骤二:采用安全防护措施
示例 1: a) 带互锁装置的可移 动安全门* b) 固定的安全门 * 必须使用安全的控制回路
直接 & 间接的接触 , 静电, 绝缘 , 过流, …
危险
危险的综合 电的
功效 振动
辐射 化学的
Copyright © 2007 Rockwell Automation, Inc. All rights reserved.
风险减少的步骤
步骤一 : 通过设计减少风险(一般主要是通过设计消除危险的隐 患,如减少引起危险的力或速度,通过优良的人类工效学设计) 步骤二 : 步骤三 : 步骤四 :
Life Cycle
STEP 3
安全装置设计 • 安全系统的功能 • 设计系统构架 • 安全控制回路设计 • 方案确认 • 防护设计
Copyright © 2007 Rockwell Automation, Inc. All rights reserved.
STEP 4
项目管理 • 材料准备 • 系统集成 • 综合测试 • 试运行 • 培训
CSM Safety Solutions
Copyright © 2007 Rockwell Automation, Inc. All rights reserved.
Copyright © 2007 Rockwell Automation, Inc. All rights reserved.
机械防护措施
Copyright © 2007 Rockwell Automation, Inc. All rights reserved.
控制系统防护措施 EN 954 – 1
EN 811
Copyright © 2007 Rockwell Automation, Inc. All rights reserved.
机械防护措施
75~120 max
Copyright © 2007 Rockwell Automation, Inc. All rights reserved.
机械防护措施
步骤二: 步骤二:采用安全防护措施
示例 3: 紧急停止设备*
* 必须使用安全的控制回路
Copyright © 2007 Rockwell Automation, Inc. All rights reserved.
步骤二: 步骤二:采用安全防护措施
示例 4:
安全缓冲器*
* 必须使用安全的控制回路
Copyright © 2007 Rockwell Automation, Inc. All rights reserved.
采用安全防护措施(如防护罩、联锁保险装置)
实施个人保护措施
采用通知和警告提示信息
See also ISO 12100-1
* Mandatory in some country legislations
Copyright © 2007 Rockwell Automation, Inc. All rights reserved.
Copyright © 2007 Rockwell Automation, Inc. All rights reserved.
步骤二: 步骤二:采用安全防护措施
示例 2: 光栅* 安全地毯*
* 必须使用安全的控制回路
Copyright © 2007 Rockwell Automation, Inc. All rights reserved.