组装检验标准
组装件检验标准
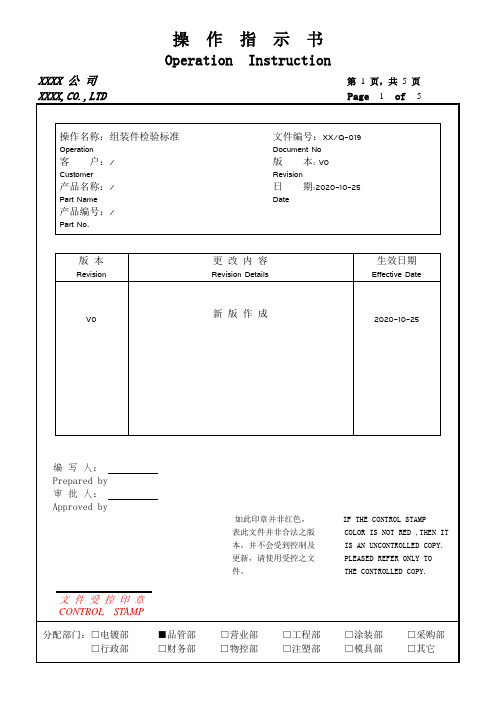
V0
新版作成
2020-10-25
编 写 人:
Prepared by
审 批 人:
Approved by
如此印章并非红色,IF THE CONTROL STAMP
表此文件并非合法之版COLOR IS NOTRED,THENIT
本,并不会受到控制及IS AN UNCONTROLLEDCOPY.
操作名称:组装件检验标准
Operation
客户:/
Customer
产品名称:/
Part Name
产品编号:/
Part No.
文件编号:XX/Q-019
Document No
版本:V0
Revision
日期:2020-10-25
Date
版本
Revision
更改内容
Revision Details
生效日期
3.任何位置的尘埃、杂粒不可有明显的刮手感
目视
●
●
●
●
●
15.毛刺、
毛边
1.A面长度≤0.15 mm²*1,高度≤0.05mm.两者间距>10mm
2.B面长度≤0.20 mm²*1,高度≤0.05mm.两者间距>10mm
3.任何位置的毛刺/毛边不可有明显的刮手感(以不影响装配为准)
目视游标卡尺
●
●
●
游标卡尺
●
●
●
13.沙眼
1.面壳、翻盖、电池面盖A面≤0.15mm²*1,深度≤0.05mm*1
2.面壳、翻盖、底壳B面、电池面壳≤0.25mm²,深度≤0.05mm*1,正面目视视距30cm处不可视
3.任何位置的沙眼不能影响表面喷涂
组装质检标准
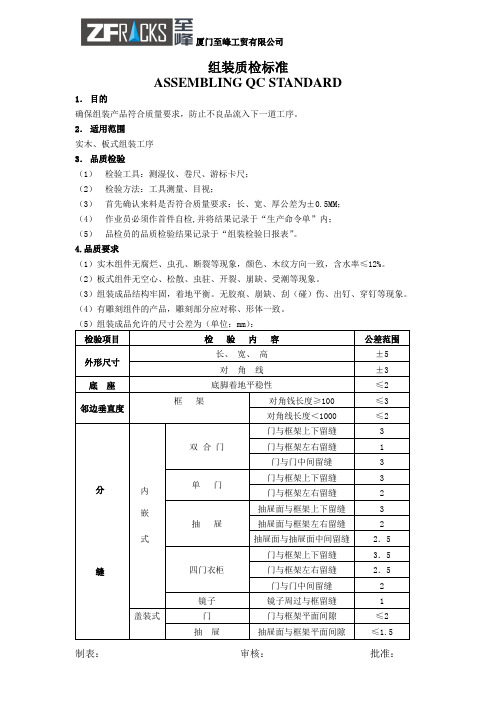
组装质检标准ASSEMBLING QC STANDARD1.目的确保组装产品符合质量要求,防止不良品流入下一道工序。
2.适用范围实木、板式组装工序3.品质检验(1)检验工具:测湿仪、卷尺、游标卡尺;(2)检验方法:工具测量、目视;(3)首先确认来料是否符合质量要求:长、宽、厚公差为±0.5MM;(4)作业员必须作首件自检,并将结果记录于“生产命令单”内;(5)品检员的品质检验结果记录于“组装检验日报表”。
4.品质要求(1)实木组件无腐烂、虫孔、断裂等现象,颜色、木纹方向一致,含水率≤12%。
(2)板式组件无空心、松散、虫驻、开裂、崩缺、受潮等现象。
(3)组装成品结构牢固,着地平衡。
无胶痕、崩缺、刮(碰)伤、出钉、穿钉等现象。
(4)有雕刻组件的产品,雕刻部分应对称、形体一致。
(5)组装成品允许的尺寸公差为(单位:mm):检验项目检验内容公差范围外形尺寸长、宽、高±5 对角线±3底座底脚着地平稳性≤2邻边垂直度框架对角钱长度≥100 ≤3对角线长度<1000 ≤2分缝内嵌式双合门门与框架上下留缝 3门与框架左右留缝 1门与门中间留缝 3单门门与框架上下留缝 3门与框架左右留缝 2抽屉抽屉面与框架上下留缝 3抽屉面与框架左右留缝 2抽屉面与抽屉面中间留缝2.5 四门衣柜门与框架上下留缝3.5门与框架左右留缝2.5门与门中间留缝 2镜子镜子周过与框留缝 1 盖装式门门与框架平面间隙≤2 抽屉抽屉面与框架平面间隙≤1.5。
装配检验规范
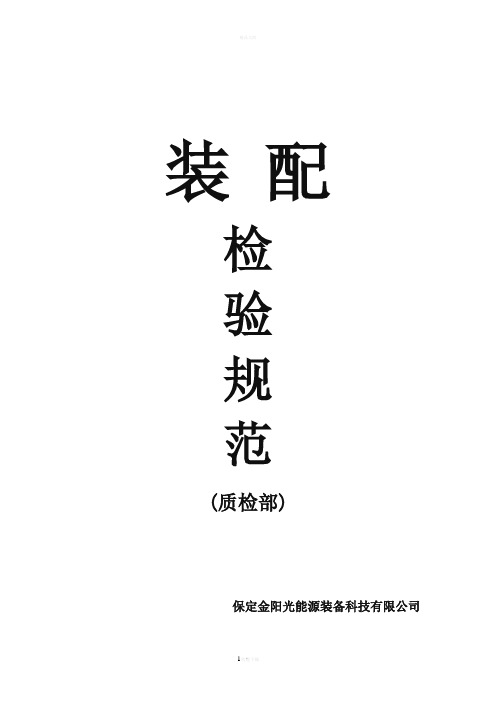
装配检验规范(质检部)保定金阳光能源装备科技有限公司一、表面检验1、严格按照图纸要求进行检验,尺寸是否符合要求,转动和传动部位是否灵活准确,面漆涂层表面应均匀平整,无流痕、不堆积、漆膜光亮、色泽鲜艳、无缺漆、不起泡、不开裂、不起皱、无划伤,不见明显的砂纸痕迹,不混色,装饰线条平、直、界线分明。
2、进行部件化生产的零部件在总装前严格按照上述要求进行涂装。
3、凡待装配的零部件,必须有检验人员检验合格标记,外购件、协作件须有证明合格的文件,方可进行装配。
4、凡已涂漆的零部件在油漆干透之前不得进行装配,凡不要求涂装的零部件,应涂上油脂。
5、电镀件、镀铬件、法兰件,不允许有锈蚀划痕和碰伤,配合面应清洗,干后涂适量的润滑油(脂)零部件的油孔要畅通注油。
6、箱体、阀体等零件与其他零件连接处,必须紧密不得漏油(水)。
二、紧固件装配检验1、紧固件螺纹不应有碰伤,螺栓、螺钉头部,与被紧固的零件平面均匀接触。
不应倾斜,螺栓不应有锈蚀划伤,表面应镀铬或法兰。
2、螺钉、螺母紧固时严禁使用不合适的搬手,必须对称交叉轮番逐次拧紧。
按图纸力矩要求进行。
3、各种止动垫圈在螺母拧紧后,应弯转舌耳,螺栓头部防松保险丝应按螺纹旋向穿装。
三、滚动轴承的装配检验1、轴承用温差法热装时,应将轴承用油加热至140-160度后进行装配。
但带防尘盖或密封圈的轴承不能用温差法加热。
2、轴承用压入法装配时,应用压力机压入,不允许用通过滚动体传递压力。
如用手锤敲打,则中间垫以铜棒或其它不损坏装配件表面的物体。
3、安装轴承时应将带标记端面朝外。
4、轴承空腔内应注入空腔容积65%-80%的黄油。
5、可拆卸的轴承在清洗后必须用原装位置组装不准颠倒。
四、滑动轴承的装配1. 衬套及轴瓦上的油槽必须平整光滑,无毛刺。
衬套在装入轴轴承承座时,应用压力机压入,且不得歪斜。
须用手锤打入时,其中间必须垫以软金属。
2. 装配后轴必须能灵活运转,轴向间隙应符合表1之规定。
表1五、链轮和链条的装配检验1、链轮安装后不许有轴向串动。
木工组装质量标准及检验规范

木工组装质量标准及检验规范引言:木工组装是一门重要的手工技术,涉及到家具制作、建筑工程和室内装饰等领域。
为了确保木工组装的质量,需要制定相应的标准和规范来指导和检验。
本文将介绍木工组装的质量标准及检验规范,以帮助提高木工组装的质量和效率。
一、木工组装的质量标准1. 材料选择和处理:在进行木工组装前,需要仔细选择和处理木材。
优质的木材应具备以下特点:均匀的颜色和纹理、无明显的病虫害和腐朽痕迹、无裂纹和变形等。
材料选择合适并经过适当的处理可以降低木工组装的问题。
2. 安装精度和稳定性:木工组装的质量取决于安装的精度和稳定性。
安装前,需要进行准确的测量和标记,确保每个零件的位置和角度准确。
并且,在组装时需要使用合适的工具和方法,确保木材之间的连接牢固和稳定。
组装后需要进行稳定性检测,确保木工制品在使用中不易变形或松动。
3. 表面处理和装饰效果:木工组装完后,需要进行合适的表面处理和装饰,以提升整体质量和美观度。
表面处理包括打磨、涂漆等,需要确保表面光滑、无划痕和斑点。
装饰效果包括雕刻、镶嵌等,需要确保装饰的精度和一致性。
4. 功能和耐久性:木工组装的质量标准还包括功能和耐久性。
根据不同的用途和需求,木工制品需要具备相应的功能,如承重能力、稳定性等。
耐久性是指木工制品在使用寿命内能够保持其功能和外观的能力,不易磨损或损坏。
二、木工组装的检验规范1. 外观检验:外观检验是对木工组装质量进行直观观察和评估。
包括检查木材的颜色和纹理是否一致、检查连接处是否牢固和稳定、检查表面有无划痕和缺陷等。
外观检验可以通过肉眼进行,需要细致地观察每个细节,并记录发现的问题。
2. 功能检验:功能检验是对木工制品的功能进行测试和评估。
例如,对椅子进行承重测试,对门进行开关测试等。
功能检验需要根据不同的用途和需求,确定相应的测试方法和标准。
测试时需要记录测试结果并与标准进行比较,判断是否合格。
3. 稳定性检验:稳定性是指木工制品在使用中是否能够保持其形状和结构的稳定性。
零部件检验标准及方法

零部件检验标准及方法零部件检验标准及方法1. 背景介绍在制造工业中,零部件的质量检验是确保产品品质的关键环节之一。
通过对零部件进行科学、严谨的检验,可以提高产品的可靠性和安全性。
本文将介绍常用的零部件检验标准及方法。
2. 外观检验•目的:检查零部件外观是否符合要求,包括表面光洁度、几何形状、尺寸精度等方面。
•方法:–直接目视检查:通过直接观察零部件外观,判断是否存在缺陷、损伤等问题。
–使用显微镜或放大镜进行检查:通过放大镜或显微镜观察细微的表面问题,如划痕、气孔等。
–使用测量工具进行尺寸检验:使用卡尺、量规等测量工具,对零部件的尺寸进行检查,确保其符合要求。
3. 功能性检验•目的:检查零部件的功能是否符合设计要求。
•方法:–运行测试:将零部件安装到相应的设备或系统中,进行正常工作状态下的运行测试,观察其功能是否正常。
–性能测试:使用专门的性能测试设备,对零部件进行负载测试、耐压测试、抗振动测试等,验证其性能是否达标。
4. 材料检验•目的:检查零部件所使用的材料是否符合要求,包括化学成分、物理性能等。
•方法:–化学分析:使用化学分析仪器,对材料进行成分分析,确保其成分符合要求。
–物理性能测试:使用拉力机、硬度计等测试材料的物理性能,如强度、硬度等。
5. 寿命检验•目的:检查零部件的使用寿命是否符合要求。
•方法:–疲劳测试:通过对零部件进行循环加载、循环使用等方式,检测其在长期使用过程中的寿命情况。
–加速老化测试:使用特定的老化设备,对零部件进行加速老化测试,模拟长期使用环境,检查其在短时间内的寿命表现。
6. 环境适应性检验•目的:检查零部件在特定环境条件下的适应性。
•方法:–温度适应性测试:将零部件暴露在不同温度条件下,观察其在不同温度下的性能变化。
–湿度适应性测试:将零部件暴露在高湿度或低湿度条件下,观察其在不同湿度条件下的性能表现。
–耐腐蚀性测试:将零部件暴露在化学腐蚀性环境中,观察其对腐蚀的抵抗能力。
组装检验作业指导书
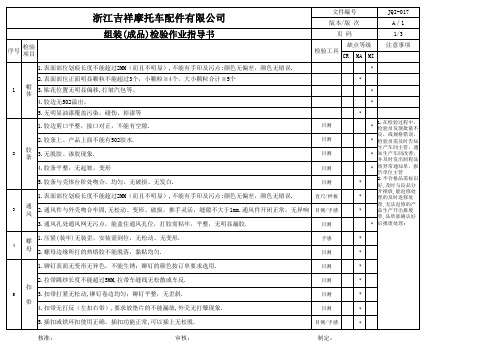
目测
﹡
良,或规格错误,
E 3.EPS看得见的部位划伤长度超过不3MM、宽度超过1MM;EPS无烧焦,无用错原料,EPS孔位不能被材料堵塞.
目测/直尺
检验员需及时告知
﹡
生产车间主管,通
P 4.EPS无断裂、凹陷、严重变形. 6S
主 5.EPS分大、小号的按订单要求选用,不能用错. 体 6.打胶位置正确.
1.在检验过程中, 检验员发现批量不
良,或规格错误,
﹡ 检验员需及时告知
生产车间主管,通
﹡ 知生产车间改善,
并及时发出制程品
﹡ 质异常通知单,报
告单位主管
﹡
2.不合格品需标识 好,及时与良品分
开摆放,能返修处
﹡
理的及时返修处
理,无法返修的产
﹡
品生产开出报废
单,品质部确认好
﹡ 后报废处理;
4
螺 1.压紧(装牢)无装歪,安装需到位,无松动、无变形. 母 2.螺母边缘所打的热熔胶不能脱落,黏贴均匀.
6.镜片上无披锋.
7.镜片关闭后,气密性要好,间隙不可太大
标 1.不可漏贴标签、贴纸,标签、贴纸内容需符合订单规格要求 签 2.标签不可有破损、打皱、脱落、或印刷不清楚等不良; 11 / 吊 3.贴放位置、方向正确,标贴不可太歪. 牌 4.尺码标与内衬上尺码一致(镜片上要贴则也要一致).
缺点等级 检验工具
目测/手感
﹡
核准:
审核:
制定:
浙江吉祥摩托车配件有限公司
组装(成品)检验作业指导书
文件编号 版本/版 次
页码
JQI-017 A∕1 2/3
序号
检验 项目
标准要求
检验工具 缺点等级 CR MA MI
柜子出厂组装检验标准
柜子出厂组装检验标准
序号 检验项目 检 验 标 准 检验依据/检验方法
预埋件:打入孔后与板面齐平或略低,不允许高出板面。 预埋件 连接杆:拧入预埋件中,拧到位,不准歪斜。 连接杆 锁扣:箭头向着连接杆方向装入相应孔内,安装到位与板面齐平或略低与板 锁扣 面,不允许高出板面。 板件安装连接件 二合一:塑料组合件打入板件相应的孔内,不准歪斜, 要到位。并用刀片 二合一 清理开口处毛刺。金属镙杆拧入板件相应孔位,不准歪斜。 PK2:塑料组合件打入板件相应孔内,不准歪斜,要到位。并用刀片清理开 PK2 口处毛刺。金属底座用螺丝拧到相应板件孔内,拧到位,不准歪斜。 各板件连接:符合图纸设计要求,连接紧密,各板件间隙不大于0.2mm。柜 体外形尺寸允许偏差:宽+2mm-1mm ,高+2mm-1mm ,深±2mm 。 后背板:四周嵌入槽内,无明显松动现象,不得对四周板件造成安装障碍。 不得出现脱槽现象。不准有严重变形情况。 层板:固定层板用要求的连接件连接,水平到位,要求牢固可靠,封边顺序 符合要求。 活动层板用要求的层板销放置,水平到位,平稳可靠,封边顺 序符合要求 顶底板:用要求的连接件进行连接,水平到位,要求牢固可靠,封边顺序符 合要求。顶底板外盖侧板的两端时,任何一端要与侧板平齐,误差允许± 0.2mm以内。 抽屉盒宽度与两侧间滑轨间距:三节滑轨为两面间距最小不小于25mm,最大 不大于27mm。隐藏滑轨两面间距17mm±1mm。抽屉盒进深推进去后堵板不能 抽屉、裤抽、领 碰到柜体后背板。抽屉面板四周与柜体间隙1.5mm最大不大于2mm.滑轨安装 抽安装 后推拉顺畅。避让平开门铰链进深退让最小不小于65mm,左右避让以不妨碍 抽屉抽出为准。
依据:图纸、工艺文件 方法:目测、测量、试装
钢箱梁制作质量检验项目及标准
11△
连
接
焊缝尺寸
符合设计要求
量规:检查全部
2
焊缝探伤
超声:检查全部
射线:按设计规定,设计无规定时按10%抽查
3
高强螺栓扭矩
±10%
测力扳手:检查5%,且不少于2个
注:①L以m计。
②s为加劲肋与加劲肋之间的距离。
2.钢梁防护涂装实测项目
项次
检查项目
规定值或允许偏差
检查方法和频率
权值
1△
除锈清洁度
符合设计规定,设计未规定时Sa2.5(St3)
比照板目测:100%
3
2△
粗糙度(µm)
外表面
70~100
按设计规定检查。设计未规定时,用粗糙度仪检查,每段检查6点,取平均值
2
内表面
40~80
3
总干膜厚度(Um)
符合设计要求
漆膜测厚仪检查
1
4
附着力(MPa)
符合设计要求
划格或拉力试验:按设计规定频率检查
1
注:项次3的检查频率按设计规定执行。无规定时,每10m2测3~5个点,每个点附近测3次,取平均值,每个点的量测值如小于设计值应加涂一层涂料。每涂完一层后,必须检测干膜总厚度。
2
5
盖板宽度(mm)
±4
尺量:检查两端断面
1
6
横断面对角线差(mm)
4
尺量:检查两端断面
1
7
旁弯(mm)
3+0.1L
拉线用尺量:检查跨中
1
8
拱度(mm)
+10,-5
拉线用尺量:检查跨中
1
9
腹板平面度(mm)
<s/250且≤8
光伏组装件检测标准
光伏组装件检测标准
1. 引言
该文档旨在制定光伏组装件检测的相关标准,以确保光伏组装件的质量和安全性,同时促进光伏行业的发展。
2. 检测标准
2.1 外观检测
- 检查组装件的外观是否正常,如有明显划痕、变形、污渍等缺陷,应予以记录和报告。
2.2 功能性检测
- 测试组装件的发电效率,确保其在光照条件下能够正常产生电能。
- 检测组装件的电压和电流输出,确保其符合设计要求。
- 确保组装件能够正常工作在预定的温度和湿度条件下。
2.3 安全性检测
- 检测组装件是否存在电气漏电和短路等安全隐患,并做出相应记录和报告。
- 检测组装件的抗风能力和抗压能力,确保其能够在恶劣环境下安全运行。
2.4 耐久性检测
- 通过暴露测试,确定组装件在不同气候条件下的耐久性和抗腐蚀性能。
3. 报告和记录
每次检测应生成相应的检测报告和记录,包括检测日期、检测结果以及任何不合格项的详细描述。
这些报告和记录应保存在合适的档案中,以便日后的参考和审核。
4. 遵守法规
在制定和执行光伏组装件检测标准时,应遵守国家和地区的相关法规和要求,确保检测工作的合法性和准确性。
5. 结论
制定光伏组装件检测标准对于确保光伏组装件的质量和安全性至关重要。
本文档所列的检测标准可以作为制定光伏组装件检测方案的参考,以促进光伏行业的健康发展和规范运营。
产品制造、安装、验收标准
产品制造、安装、验收标准1、木家具:木家具指班台、办公桌、书柜、衣柜、主席台、会议桌、茶几、会议椅等。
以上产品的制造、安装、验收标准要符合GB/T3324—2008《木家具通用技术条件》的规定。
2、材料基材:采用不低于E1级的刨花板或中纤板,基材材质应分别符合国家标准GB/T4897—2003《刨花板》和GB/T11718—2009《中密度纤维板》的规定,其环保指标应符合GB18580—2017《室内装饰装修材料人造板及其制品中甲醛释放量》国家标准的要求.饰面材料:优质装饰薄木(木皮)厚度0.6mm~0.8mm;防火板采用美国“富美家”或“富美家”产品,厚度0.8mm。
实木:对于同一单位产品采用单一树种硬质阔叶树树材,其材色和纹理与饰面材料相协调,材质符合GB/T3324—1995第4.3条规定,木材含水率在10%~12%之间,并经防腐、防虫处理,产品主要受力部位斜纹程度不超过20%。
工艺:木制品工艺要求要符合GB/T3324—2008第4.4条规定,要点列下:1.人造板部件要进行封边处理,包括隐蔽部位。
2.外表的倒棱、圆角、线形均匀一致,版面平整光滑。
3.各种配件安装严密、平整、端正、牢固,结合处无崩或松动;不得有少件、漏钉、钉透现象,启闭灵活顺畅,底角落地平稳。
4.涂饰部位的粗糙度要求精光,内部不涂饰3、外观:木制品外观质量要求符合GB/T3324—2008第4.4、4.5条规定。
要点列下:3.1整套产品或同批产品木材纹理,颜色要求一致,漆膜表面无尘粒、气泡、渣点,边缘及立面无流挂、开裂现象。
3.2正视面(包括面板)覆面层、涂层光滑平整、无皱皮、开裂现象,无明显加工划痕等缺陷。
3.3台面平整,平整度0.06mm,木皮及实木封边拼接紧密、细腻、线条均匀,外表结合处缝隙小于0.01mm,线条均匀、整齐,转角过度自然。
3.4封边条不允许有透胶、鼓泡等现象。
4、力学性能:4.1桌类稳定性、强度和耐久性分别按照国家标准GB10357·7—1995《家具力学性能试验桌类强度和耐久性》规定要求进行实验,实验结束后产品状态应是:(1)零、部件不得有断裂或豁裂。
- 1、下载文档前请自行甄别文档内容的完整性,平台不提供额外的编辑、内容补充、找答案等附加服务。
- 2、"仅部分预览"的文档,不可在线预览部分如存在完整性等问题,可反馈申请退款(可完整预览的文档不适用该条件!)。
- 3、如文档侵犯您的权益,请联系客服反馈,我们会尽快为您处理(人工客服工作时间:9:00-18:30)。
称(配)片工序1.本标准规定了称(配)片工序的检验项目、检验方法及质量标准。
本标准适用于电动助力车用密封铅酸蓄电池。
2.检验工具:电子天平(量程500g,最小分度值0.5g)3.检验项目及质量标准3.1操作手法:员工在极板包装箱里取出极板后,首先敲掉极板上的浮粉和铅粒。
3.2选片:剔除极板中的不合格品后再进行称片。
3.2.1极板外观检查:极板不允许有严重脱粉、穿孔、断筋、变形、飞皮毛刺、严重凹凸不平、极板弯曲、花板、环状裂纹。
极板不允许有大的铅膏脱落、极耳下部铅膏松动严重、边框断裂3.2.2正负极板颜色均匀一致。
正极板为棕褐色,负极板为青灰色或浅灰色.3.3标识标签:称片时先在标签上写好公司所规定的极板(群)重量,日期和员工工号,字迹要求清楚工整。
正极板用白色标签纸,负极板用黄色标签纸。
3.4极板(群)装箱:把合格的极板(群)板耳朝上,每组板耳交错放在干净相对应的周转箱里(正板极群用红色箱子,负板极群用其黑色箱子),每箱应有(3.3)标签纸。
相同型号、重量的周转箱中的极群数量应符合标准要求。
3.5 码放:将称好的极板群箱整齐码放,同规格同重量的极板摆放在一起,不同规格不同重量的塑料箱间保持一定的间距;码放层数不得高于6层。
禁止歪斜,禁止极板互相挤压。
4.极配组称重时允许的重量偏差中心值:±1g5.检验方法5.1全部目视检查5.2单格极板片数、装箱极板片数目视检验;极群重量按3%的比例用电子天平检验。
6.检验规则6.1 以上项目操作工人均要进行自检,自检率100%,合格率100%6.2 抽检工作由质检员进行,抽检合格率100%,抽检不合格由操作工人返工。
一次抽检不合格,第2次加倍抽样检验,还是不合格,整批次极群返工。
包片工序1.本标准规定了包片工序的检验项目、检验方法及质量标准。
本标准适用于电动助力车用密封铅酸蓄电池。
2.检验工具:电子天平(量程1000g,最小分度值1g)3.检验项目及质量标准3.1 工前准备:员工在操作前所用材料和工具的摆放应符合(.....)规定。
3.2 操作手法:员工在包片过程中应保持隔板的整洁度。
包正极板时要敲板,去除极板上的浮粉与铅粒。
3.3 选片:在包片的过程中发现有(.....)的不合格品极板,及时替换上相同型号同重量,相同厂家同批次的合格极板。
挑出隔板中的不合格品.3.4 填写流水作业单:包片操作前,按工艺标准,根据极群箱里的标签纸填写作业单:正、负极板的重量、日期、员工工号和极板批次。
不同规格的极板用的作业单颜色也不同。
3.5 极群质量:极板耳对齐,高度一致。
正、负板耳各自成一条线,而且极板板面相互对齐。
隔板左右侧超出极板尺寸一致,隔板上部超出极板上边框尺寸一致。
3.6 极群装盒:包片完成后,将极群立在工作台面上,用手指整理极群。
确保正极板底部无多余隔板,然后小心的插入极群盒,避免插入时极群变形或隔板破损。
3.7 极群装箱:将极群整齐的放入周转箱里,防止极群相互挤压,造成铅灰污染隔板或极群变型、损伤。
3.8 数量:按工艺标准,相同型号的极群箱中的极群数量一样。
3.9 码放:将包好的极群周转箱整齐码放,同规格同重量同批次的极群周转箱摆放在一起,不同规格不同重量的塑料箱间保持一定的间距;码放层数不得高于6层,禁止歪斜。
4.同规格同重量同批次的极群重量差3g5.检验方法(3)全部目测检验。
5.2(4)极群重量按5%的比例用电子天平检验。
6.检验规则6.1 以上项目操作工人均要进行自检,自检率100%,合格率100%6.2 抽检工作由质检员进行,抽检合格率100%,抽检不合格由操作工人返工。
一次抽检不合格,第2次加倍抽样检验,结果仍不合格,则判该操作工所做的批次极群不合格,必须返工。
由车间主任监督执行。
焊接工序1.本标准规定了焊接工序的检验项目、检验方法及质量标准。
本标准适用于电动助力车用密封铅酸蓄电池。
2.检验工具:直尺(测量范围0-300mm);尖嘴钳。
3.检验项目及质量标准3.1 工器具检查:⑴每天操作工自检,焊接夹具上有无水分、锈蚀,若有及时进行清理。
⑵检查焊接夹具的高度是否符合要求,并检查夹具螺丝有无松动,出现异常及时进行调整。
⑶检查疏形板有无缺损变形。
注:1、焊片架高度为焊片架底板上平面到焊片架梳齿板上平面的距离。
2、未标出焊接高度的型号按照极群图纸调整焊接架高度。
3.2 质量检验:(1)正、负极汇流排焊条不允许混用。
(2)各规格极柱严格区分,不可混用。
(3)汇流排质量:宽度5-6mm,厚度为3.5-4mm.表面平整、光亮,无虚焊、假焊、气孔;无铅渣、铅瘤、飞皮、毛刺、裂纹;极耳熔接牢靠。
极柱烧伤程度<0.2mm.极群内应无铅渣、铅粒夹杂。
3.3 上下模员工应始终保持极群的整洁度。
对烧好的极群模,首先应使用铜刷小心的去除汇流排上的杂质,不许把极柱碰弯曲,否则应及时扶正。
接下来敲上钢印,字迹要清楚、工整、明显。
用双手以水平方向拿掉正极梳板,再用手捏住极群上部,轻轻的左右晃动取下极群(绝对不可以上下摇动,不然会使极柱变形,影响电池质量)。
如果有质量问题应及时修理好。
仔细检查每个极群,用剪刀修去飞边、毛刺、挂铅等。
确认合格后放入极群箱中,核对数量,填好流程卡,流入下道工序。
4.检验方法:[3.2.(3)、3.3]用目测和检验工具检验;其他全部目视检查。
5.检验规则:5.1 以上项目操作工人均要进行自检,自检率100%,合格率100%。
5.2 抽检工作由质检员进行,每小时一次,逐个工位进行巡检。
抽检合格率100%,抽检不合格由操作工人返工。
入槽、拼接、检测工序1.本标准规定了入槽、拼接、检测工序的检验项目、检验方法及质量标准。
本标准适用于电动助力车用密封铅酸蓄电池。
2.检验工具:极板短路检测仪3.检验项目及质量标准3.1 填写作业单:员工在操作前检查蓄电池槽有无裂纹、杂物等缺陷,再将流水作业单粘帖到蓄电池槽侧面,填上入槽工号。
流水作业单粘帖要求平整,工号字迹工整,清楚。
3.2 入槽手势:将极群从极群盒中取出,检查焊接质量,清除铅渣等杂物。
两手用力均匀捏紧极群,使极群压缩到小于单体厚度时,连同PVC薄膜一同水平插入电池单体槽内,插入深度为极群高度的2/3,动作用力均匀,防止损伤极板和隔板。
将专用工具置于正负极群汇流排上,将极群压到槽底,校正所有极柱。
将电池翻转(倒过来)用专用工具轻轻敲击电池低角,去掉残留铅灰和铅渣等。
极群无反极,隔板无破损、划伤、无明显污染,隔板之间无杂物。
3.3 拼接:过桥焊接无虚焊,厚度为2.5-3 mm,蓄电池槽口无烧损,极群内无铅渣、铅粒等。
3.4 测试:按检测仪提供的信息,极群内部有短路现象,应立即将该极群取出,准确找到短路位置并更换,确保极群无短路现象,整理极群后再插入电池槽内,重新检测。
4.检验方法4.1 3.1-3.3目视检查。
4.2 3.4按3%的比例用极板短路检测仪进行抽检。
5.检验规则5.1 以上项目操作工人均要进行自检,自检率100%,合格率100%5.2 抽检工作由质检员进行,每小时一次,逐个工位进行巡检。
抽检合格率100%,抽检不合格由操作工人返工。
一次抽检不合格,第2次加倍抽样检验,结果仍不合格,则判该操作工所做的批次电池不合格,必须返工。
由车间主任监督执行。
封胶工序1.本标准规定了封胶工序的检验项目、检验方法及质量标准。
2.检验工具:气密性测试仪。
3.检验项目及质量标准3.1 槽盖配合上盖与底槽配合良好,槽盖密封线之间的间隙<2mm。
3.2 密封胶固化在配胶、浇密封胶、固化工艺规定的条件下,固化完全,强度良好。
3.3 “O”型密封圈“O”型密封圈不得有油污、灰尘和水份等缺陷,安装必须到位,与极柱配合紧密。
3.4 正、负极端子3.4.1将合格的接线端子对应安装到位,焊接点必须良好熔合,焊接牢固、无虚焊、假焊,焊接时不得损伤焊接以外的部位,不得有焊渣掉入电池内。
3.4.2打底胶应完全覆盖焊接部位。
3.4.3封色胶应填满极柱密封槽,不能外溢,固化后略低于密封槽表面0.1mm以内。
正极封红色胶,负极封蓝色胶。
3.5 电池外观电池槽盖无破裂、划痕,电池表面(包括正负极端子)清洁光亮,无残留胶污。
4.检验方法4.1 (3)抽检率为5%,均用目测。
4.2 密封胶按固化工艺要求取小样,用指甲刮其表面,观察是否有划痕。
4.3 气密性检测:由专人负责,用气密性测试仪测试每只电池。
4.4 质检员同时要监督检查操作工人是否严格按工艺规程操作。
5.检验规则5.1 以上项目,各操作人员均要进行自检,自检率为100%,合格率100%。
5.2 下工序操作工人对上工序的产品要进行互检,互检率为100%,合格率100%。
5.3 抽检由质检员进行,抽检合格率100%,抽检不合格需加倍抽样检验,如仍不合格,由操作工人将不合格品剔出并进行返修、返工。
加酸、充电、小包装工序1.本标准规定了加酸、充电、小包装工序的检验项目、检验方法及质量标准。
本标准适用于电动助力车用密封铅酸蓄电池。
2.检验工具:序号名称测量范围精度或分度值1比重计1.30-1.400.012温度计0-100℃1℃3量筒0-100ml1ml4数字万用表0-20v0.01v3.检验项目及质量标准3.1 加酸3.1.1 硫酸比重:1.340±0.002(25℃)。
3.1.2 每单格加硫酸量:符合工艺要求。
3.1.3 端子:灌酸前必须涂上防腐油。
3.1.4 外观:无漏酸现象,电池表面无残留酸液。
3.2 充放电3.2.1 充放电工艺:必须符合工艺规程要求。
3.2.2 电流表、电压表:必须校正,误差不大于0.1。
3.2.3 电池表面:无残余酸液。
3.2.4 充电时电解液:保持富液。
3.2.5 电池间距:保持10mm距离。
3.2.6 电池完全充电,2h率放电容量≥125min(25℃)。
3.3 小包装3.3.1 外观:经过完全充好的电池,整个电池外表面(包括注液孔、端子附近)清洁,无残留酸。
3.3.2 安全阀:安全阀无破损、变形,安装到位,配合良好。
3.3.3 盖片:安装到位,粘接牢固,配合良好。
3.4 配组3.4.1 开路电压:同组电池电压差不大于0.03v。
3.4.2 放电电压:同组电池电压差不大于0.4v。
3.4.3 2h率放电时间大于125min(25℃)4.检验方法4.1 加酸4.1.1 每天加酸前,质检员用比重计、量筒、温度计测试加酸比重和体积,符合工艺规程要求后,方能放行生产。
4.1.2 端子和外观抽查按百分之五的比例进行目测。
4.2 充放电4.2.1充放电工艺:检查充放电记录,查看电流表、电压表工作状态。
4.2.2 电流表、电压表校正检定按规定送检。
4.2.3 电池表面:逐只检查有无残余酸液。
4.2.4 用手提灯逐只观察电池内是否有缺液现象。