硬齿面齿轮加工技术研究及应用
关于面齿轮磨齿加工技术研究

关于面齿轮磨齿加工技术研究摘要:为实现对硬齿面面齿轮的加工和提高面齿轮加工精度,对面齿轮磨齿加工进行了研究。
根据面齿轮的齿面方程,得到用空间曲线绘制的面齿轮齿面,确定了磨齿加工过程中接触点的运动轨迹和 3 个坐标方向的运动速度。
建立了磨齿机床的实体模型,分析了刀具与面齿轮的运动关系。
采用简单的碟片砂轮通过复杂的运动实现面齿轮的磨齿加工。
关键词:面齿轮;磨齿加工;碟片砂轮一、面齿轮磨齿的优势面齿轮传动是圆柱齿轮与锥齿轮之间啮合,实现传动轴空间相交或交错动力传动。
与锥齿轮传动相比,面齿轮传动主要有下面 5 方面的优点:(1)圆柱齿轮的轴向移动误差对传动性能影响很小。
(2)面齿轮传动重合度较大。
(3)圆柱齿轮无轴向力作用。
(4)同时啮合齿对的公法线相同。
(5)面齿轮传动的振动小、噪声低。
面齿轮传动具有上述优点,在直升机主传动系统中采用面齿轮传动可以简化支撑、减轻质量、降低噪声、减小振动,而且传动的重合度较大、动力分流效果好。
因此,面齿轮传动被西方发达国家称之为“21 世纪旋翼机传动之希望所在”。
面齿轮齿面是比较复杂的空间曲面,磨齿加工不能用成型法直接加工,利用范成法实现磨齿加工,主要有两条途径,一为简单刀具复杂运动,另一为复杂刀具简单运动。
目前对面齿轮磨齿加工的研究都集中在复杂刀具简单运动上,对基蜗杆刀具进行了理论基础研究,美国研制的面齿轮磨齿机床也是采用蜗杆砂轮刀具对面齿轮进行磨齿加工。
文中将对采用简单刀具复杂运动的面齿轮磨齿加工方法进行研究。
二、面齿轮磨齿原理文中研究采用简单的碟片砂轮通过复杂的运动对面齿轮进行磨齿,其关键在于碟片砂轮的运动轨迹的控制。
面齿轮齿面由工作面和过渡曲面两部分组成,面齿轮磨齿加工过程中,也将分步对两部分进行磨齿。
将面齿轮的工作面和过渡曲面视为由一系列空间曲线组成的空间曲面,在磨齿加工时,接触点沿曲线磨削,完成一条曲线后,再进行下一条曲线的磨削。
工作面上的空间曲线可由面齿轮的齿面方程确定。
面齿轮的发展及应用
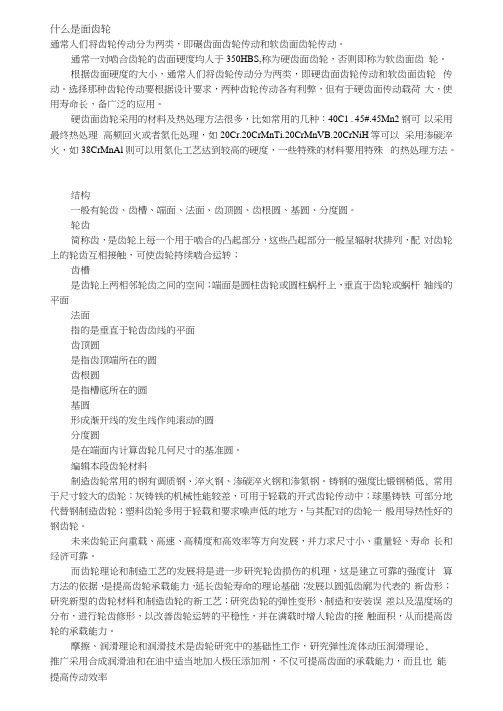
什么是面齿轮通常人们将齿轮传动分为两类,即碾齿面齿轮传动和软齿面齿轮传动。
通常一对啮合齿轮的齿面硬度均人于350HBS,称为硬齿面齿轮,否则即称为软齿面齿轮。
根据齿面硬度的大小,通常人们将齿轮传动分为两类,即硬齿面齿轮传动和软齿面齿轮传动。
选择那种齿轮传动要根据设计要求,两种齿轮传动各有利弊,但有于硬齿面传动载荷大,使用寿命长,备广泛的应用。
硬齿面齿轮采用的材料及热处理方法很多,比如常用的几种:40C1 . 45#.45Mn2钢可以采用最终热处理高频回火或者氮化处理,如20Cr.20CrMnTi.20CrMnVB.20CrNiH等可以采用渗碳淬火,如38CrMnAl则可以用氮化工艺达到较高的硬度,一些特殊的材料要用特殊的热处理方法。
结构一般有轮齿、齿槽、端面、法面、齿顶圆、齿根圆、基圆、分度圆。
轮齿简称齿,是齿轮上每一个用于啮合的凸起部分,这些凸起部分一般呈辐射状排列,配对齿轮上的轮齿互相接触,可使齿轮持续啮合运转;齿槽是齿轮上两相邻轮齿之间的空间;端面是圆柱齿轮或圆柱蜗杆上,垂直于齿轮或蜗杆轴线的平面法面指的是垂直于轮齿齿线的平面齿顶圆是指齿顶端所在的圆齿根圆是指槽底所在的圆基圆形成渐开线的发生线作纯滚动的圆分度圆是在端面内计算齿轮几何尺寸的基准圆。
编辑本段齿轮材料制造齿轮常用的钢有调质钢、淬火钢、渗碳淬火钢和渗氮钢。
铸钢的强度比锻钢稍低, 常用于尺寸较大的齿轮:灰铸铁的机械性能较差,可用于轻载的开式齿轮传动中;球墨铸铁可部分地代替钢制造齿轮;塑料齿轮多用于轻载和要求噪声低的地方,与其配对的齿轮一般用导热性好的钢齿轮。
未来齿轮正向重载、高速、高精度和高效率等方向发展,并力求尺寸小、重量轻、寿命长和经济可靠。
而齿轮理论和制造工艺的发展将是进一步研究轮齿损伤的机理,这是建立可靠的强度计算方法的依据,是提高齿轮承载能力,延长齿轮寿命的理论基础;发展以圆弧齿廓为代表的新齿形;研究新型的齿轮材料和制造齿轮的新工艺;研究齿轮的弹性变形、制造和安装误差以及温度场的分布,进行轮齿修形,以改善齿轮运转的平稳性,并在满载时增人轮齿的接触面积,从而提高齿轮的承载能力。
硬齿面齿轮的以研代磨新工艺构想

SHopSoLUTIoN生产现场剃齿刀主要参数对剃齿的影响及其选择剃齿刀作为齿轮的精加工刀具,在设计中它的参数选择显得尤为重要。
由于剃齿刀的受力状况E匕较复杂,因此对于其设计参数选择有一些较其他刀具不同的考虑和特殊要求。
1容屑槽槽型1.1对剃齿的影响盘形剃齿刀的主切削刃是剃齿刀容屑槽的侧面与渐开线齿面相交成的一条渐开线切削刃。
这条切削刃本身是平行于剃齿刀端面的。
剃■株洲齿轮有限责任公司卢新民文贵华齿刀的前角则是容屑槽的侧面与切削时所形成的基面的夹角《剃齿刀切削角度如图1)。
普通盘形剃齿刀的容屑槽一般有两种形式,即I型槽和|I型槽(如图2)。
因此.即使剃齿刀的螺旋角相同,由于容屑槽的槽型不同,剃齿刀的前角也不l司。
(1)剃齿缺陷——。
表面质量差”现象的分析剃齿时有一种重大的剃齿缺陷是齿面粗糙度大,一般情况下从节圆到齿顶,有时是全齿面出现一道道沟槽(俗称啃齿)。
啃齿”现象的__●-I__--●------_●I_●__--II----●●_---●_--_小,齿廓趋近渐开线,误差均化作用明显.长时间研齿齿形没有畸变。
齿圈径向跳动误差采用齿轮跳动检查仪测量。
对数据分析表明.互研法对齿圈径向跳动有一定修正能力,在径向跳动最高点齿轮研磨量较大,这是该点动态啮合力较大造成的。
试验数据如表1。
对齿距极限偏差和累计误差(采用相对测量法进行测量)也有一定的修正能力,绝对偏差值由0.027mm降为O.013mm.累积误差值由O.033mm降为0.023mm。
互研过程中,存在着广泛的误差均化作用.使各齿距偏差均匀一致。
这对齿轮传动十分有利。
其他如公法线长度变动误差以及齿面粗糙度均有不同程度的改善和提高.公法线长度变动有了明显的改善并趋近一致。
从齿形误差曲线上看出,研齿前齿面留有刀痕,反映出在齿形误差曲线上有杂奄专磺螽贰砥靠毛波,研齿后是一条光滑的曲线。
5.2工艺可行性公司生产的变速器圆柱齿轮中.其运转齿均为渐开线齿形,齿数一般为19~50.法向模数为3—5mm.齿轮精度等级为国标8级或DIN7级,所以把动态力研齿新工艺应用在变速器的圆柱齿轮上应该具有可行性.同时节省了磨齿工序.可以起到提高生产率、降低生产成本的作用。
硬齿面齿轮加工工艺及其在减速机中的应用

3 )压痕法。在硬面齿轮加工中利用压痕法进行齿轮测量能起 到很
好的侧来哦效果,提高齿轮测量 的精确度。具体的测量方法是 :首先在 被测齿轮 的 齿顶涂上鲜艳的颜 色, 然后将齿轮在一张纸上滑滚一周,齿 顶滚过的陈迹就会留在纸上 , 然后按照压痕作出齿顶线的延伸线及匡助
2 )成本低 、寿命长。此加工工艺在进行大齿轮加工 时,承载 力和 中 击力都很强,所 以它工作时不需要高成本的磨齿机 ,就可以获得 高
机- 般用于低转速的传输 设备,把机械的电念头等高速运转的动力,通 过减速机上的齿轮转动达到减速的 目的, 而硬齿面齿轮在这个环节中起
着重要的作用。
质量 的表面要求,而 且延长了大齿轮的使用寿命,降低 了制造加 工成本
罐 词】 - 硬齿 面;齿轮加工 ; 减速杌
齿轮硬面是指采用特殊钢 材 , 利 用复合工艺技 术加工 使齿 轮表面 硬度达到一定的工艺要求 ,硬齿面齿轮加工工艺 的流程一般是滚齿一剃 齿一热处理工艺形式。传统 的硬齿轮磨削加工,不仅生产效率低下 ,而 且加工成本很 高。另 外所需的技术也很高 ,操作 复杂。随着技术 的进
线,然后再利用量角工具测量出齿向角度,这个角就是轮齿顶处的螺旋
行滚切加工 ,此种加工方法成本低、效率高,而且有很高的经济型 ,已
经被广泛应用与齿 轮m T中。 1 硬齿面刮削工艺特点分析
角。然后就可以结合齿轮的其他几何参量 , 计算出齿轮其他角 , 整个测
量结果就完成了。
3 硬齿面齿轮在减速机中的应用分析 1 ) 减速机在机械生产领域需要精密的加工,减速机的主要功能是 降低机械的转动速度 , 增加转动距离。减速机的种类很多,不同种类的 减速机有不同的用途。减速机的工作原理是降速的同时输 出扭矩,扭矩
论硬齿面齿轮的应用

3 齿 轮的热 处理 齿轮的表面硬化处理 主要是渗碳淬火 、渗氮及
感应 表面淬火 。渗 氮 由于硬 化层 薄 而 限 制 了齿 轮 的承载能力 ,高频淬火又很难得到理想的硬化层分 布,对大模数齿轮淬火时 ,齿轮淬硬深度 太浅或没 有 淬火造成应 力 分 布不均 而降低 了齿轮 弯 曲强度 。 气体渗碳淬火,可以得到所需要 的硬化层 ,热处理 后具有较理想的残余应力。用 最新技 术可准确地
交 换创 造 了条 件 。
(2) 混装 塔 配风 、配 水 较 点滴 塔 均匀 。因为
此混 装 塔 比点 滴 塔 的 冷却 能力 提 高 了 20% 一
40% 。
‘
(3) 采用 了混装技术 的横 流塔克服了点 滴
塔的关键性 毛病 ,充 分利用 了空气 动力 学 、热力 学 、 水力学 、结构力 学 及 材 料力 学 的 原理 ,尽 最 大 可能 促进 了冷 却塔 的热 工性 能 。
承钢 技术
维普资讯 com
2006年第 2—3期
论 硬 齿面 齿轮 的应 用
张欣 张耀 东 (维修 中心 )
摘 要 :齿轮的强度设计是从考虑润滑条件的齿面压力和齿根强度两个方面进行的。随着齿轮传 递 功率 的 日益增 大 ,世界各 国都在努力研究如何提高齿轮承载能力 的问题 。研究结果 和生产实践 都 已 证 明 ,采用硬齿面和提高加工精度是解决问题 的关键。热 轧带 钢厂底辊减 速机 由调质齿 轮改为硬齿 面 齿轮 ,收到了 良好 的经济效益 。
齿轮渗层表面碳 的质量分数、表层组织及心部 硬度的推荐数据见表 l。
深层渗碳、淬火磨 削的高精度硬齿 面齿 轮 ,精度 高 、表 面硬度 高 ,齿 面 硬化层 均匀 等多方 面
探讨硬齿面齿轮的加工技术

解决热处理变形 、 降低精度 的问题采用生产 能力大 、 性能和质 量好 、 热处 理变形量小及 质量 稳定的热处理工 艺流程 , 该工艺 流
程具有连续碳氮共渗 的特点 , 工艺路线为 : 上料一脱脂 、 预氧化一 加热一碳氮共渗一 降温扩散一油淬一清洗一 回火一空冷一 卸料 。
统分 别控制加热炉 、 回火 炉 、 预处理 炉 、 火油和清洗机 的温度 , 淬
渗碳炉在 8 0 4 ℃和 9 0C 3 "时控制温差范围为± ℃,回火炉 在 2 0 5 0
的炉温均匀性也较好 , 温度范围为± ℃。 5 碳势控制系统控制加热炉 内的碳势, 碳势控制范 围为 : 0 5 ≤± . %C,轮齿表面渗碳层深度 为 0
一
般硬齿 面齿轮加二 制造有两种工艺 , r = 一种是剃齿工 艺; 另一
种磨齿工艺 。比较两种方法 , 磨齿工艺加工设备投入大 , 磨齿机价
格昂贵 , 机床结构和操作均较复杂 , 生产效率低 , 且要预 留一定 的
磨削余量供磨 齿磨削加工用 , 加大 了能源和材料消 耗 , 不适于 大 批量低成 本高质量齿轮制 造的需求 。剃齿 工艺具有 加工过程 灵
该工艺流程的热处理齿轮连续进入 由四个加热室组成的加热 无周期性变化 的传 动误差 , 传动 中不产生激 振频率 , 噪声较 传动 炉区 , 加热 和碳氮共渗 , 进行 碳势和温度控制系统控制精确 , 井 为柔和 , 至优 于同等精 度 的磨 齿 , 无 甚 齿轮 工作平 稳性好 、 接触精 式炉人为 的操作误差 , 零件 的热处理质量和批量 的同一性得 到保 度较高 。
民 营科技2 1 年第1 02 期
科 技 论 坛
探讨硬齿 面齿轮 的加工技术
硬化齿轮制造技术研究

硬化齿轮制造技术研究齿轮是传动机构中常用的一种零部件。
在很多机械传动中,齿轮的质量和性能起着至关重要的作用。
如何提高齿轮的耐磨性、抗疲劳性、噪音低等级以及准确度,一直是齿轮制造过程中的难点。
为了解决这些问题,许多制造技术不断地涌现出来。
其中,硬化齿轮制造技术就是一种重要的发展趋势。
一、硬化齿轮的特点硬化齿轮制造技术是一种将齿轮表面硬化的方法,通过提升齿轮表面的硬度,来提高齿轮的使用寿命和工作性能,同时减小了齿轮齿面的磨损和削减率,从而达到更好的使用效果。
硬化齿轮制造技术有很多的优点。
首先,硬化齿轮的硬度变高了,因此能够承受更大的负荷,抗疲劳性更好。
同时,硬化齿轮的表面光滑度也得到提高,摩擦和磨损都得到了很好的控制。
再者,硬化齿轮的噪音低等级也会有所提高,这对于一些噪音敏感的工业和机械设备来说尤为重要。
二、硬化齿轮的制造方法在制造硬化齿轮时,最主要的就是硬化过程。
硬化过程是借助高温、高压、高速等外力作用下,让齿轮表面经一定深度淬火而形成的。
在此过程中,要注意以下几点:1. 硬化时温度的控制。
普遍情况下硬化温度控制在800℃左右。
不过硬化温度也会根据不同材料的类型和厚度等因素不同而进行调整。
2. 硬化后的长期处理。
硬化后的齿轮需要再次回火。
在这个过程中,长时间的低温处理可以帮助保持齿轮表面硬度的同时,使得齿轮的耐腐蚀性变更好。
3. 清洁操作。
齿轮表面要保持清洁干净,无油无水,否则硬化效果会大打折扣。
三、规范化的生产流程硬化齿轮的生产流程比较复杂,需要细致认真的操作,遵循规范化、标准化的制造流程才能保证硬化齿轮的质量。
整个流程大致可以分为以下几个步骤:1. 理论分析。
在生产硬化齿轮之前,要先对涉及到的工业材料的性能进行详细的分析,并根据所选材料的特点设计方案。
2. 制造齿轮。
制造齿轮时,要根据设计要求进行制造,包括材料的选择、齿轮加工、刀具磨损情况等。
3. 检验工序。
检验工序是硬化齿轮制造中的重要工作,要对齿轮进行检查,保证无裂纹,无毛刺,无塌陷等缺点。
硬齿面齿轮加工技术现状分析

方案:工件热前所有制齿加工基准统一为左端B4中心孔与右端内孔30°外倒角,为保证热前热后基准统一,仍选用与热前相同的基准,保证了F、G齿的同轴度要求。加紧方案:采用拉杆胀套方式胀紧端头内孔,利用机床自动拉紧机构实现快速加紧工件。
4.3硬滚刀具的设计
目前,世界各国刀具厂家所设计的硬质合金滚刀,其结构主要有3种:整体式、机夹式、焊接式。整体式硬质合金滚刀刀齿和刀体用一整块硬质合金加工而成,其优点是刚性强,机械加工省时,可做到较高精度,目前技术可做到模数m=5mm以下,但损耗昂贵的硬质合金较多,成本高;机夹式硬质合金刀片用螺钉压至工具钢刀体上,机夹式结构比较复杂,夹紧可靠性也较差,适合大模数齿轮加工,但是在加工大模数淬硬齿轮时,齿面的挤压力较大,且交变作用显著,因此对刀片的夹紧要求较高;焊接式硬质合金滚刀刀片焊接至工具钢刀体上,其优点是结构简单,联接强度高,而且硬质合金刀片烧结容易,材料节省,应用较广泛。但由于焊接应力引起的裂纹一直是产品质量不稳定的因素,因此需要较高的焊接技术;并且此种滚刀实际加工中无法达到理想的切削速度。相比而言,整体式硬质合金滚刀其刚性强,精度高,覆涂后可达到较高的切削速度,更适合此零件的加工,所以选用进口整体式硬质合金滚刀。由于零件硬度高,而硬质合金材料的冲击韧性较差,因此,在硬齿面滚齿时,极易产生崩刃,崩刃是硬质合金滚刀要解决的主要问题。从理论上分析,随着硬质合金滚刀负前角的增大,滚刀侧刀刃倾角增大,使滚刀刀齿平稳地切入金属层,从而减小了冲击,保护硬质合金刀齿不致崩刃,耐用度明显提高。为此,设计滚刀时,采用大负前角的特殊形式,并覆涂TiN、TiALN和碳复合纳米材料,使滚刀的耐用度大幅度提高。由于此零件热后硬度58HRC~62HRC,结合刀具结构,采用厂家推荐的-20°前角。
- 1、下载文档前请自行甄别文档内容的完整性,平台不提供额外的编辑、内容补充、找答案等附加服务。
- 2、"仅部分预览"的文档,不可在线预览部分如存在完整性等问题,可反馈申请退款(可完整预览的文档不适用该条件!)。
- 3、如文档侵犯您的权益,请联系客服反馈,我们会尽快为您处理(人工客服工作时间:9:00-18:30)。
硬齿面齿轮加工技术研究及应用
摘要:随着我国现代社会中经济水平的进步和发展,硬齿面齿轮的市场需求量也开始逐渐加大,因此我国硬齿面齿轮的加工技术近年来也得到了相应的发展和完善。
同时根据相关的实践表示,硬齿面齿轮加工的过程中采用适当的技术,其精度能达到7级以上,不仅对材料做到了有效地节省,同时还减少了能耗的产生,大大地提升了整体的工作生产效率,取得的经济效果也比较明显。
为此,文章主要针对现代社会中硬齿面齿轮加工技术进行了相应的研究,同时开展了这项技术的应用分析,希望能对今后我国这项技术的应用和发展起到更有效的帮助作用[1]。
关键词:硬齿面齿轮;加工技术;研究;精度
在机械产品的生产和制造过程中,齿轮是一项重要的基础性零件,通常被广泛的应用在各种类型的机械传动装置上。
因此在一定程度上,齿轮制造水平的高低对机械产品的性能和质量能起到直接的影响作用,通过对加工技术进行研究和分析,对整体工艺流程进行优化和完善,将有效地提高齿轮的加工精度和工作生产效率,降低生产成本。
近年来,国内外都对硬齿面齿轮的加工都进行了大量的研究和分析,一直致力于全面提升硬齿面齿轮的加工程度,为此,文章就
将对硬齿面齿轮加工技术进行研究和分析,以期更好的提升这项技术的应用水平和产品的质量[2]。
一般情况下,硬齿面齿轮加工制造工艺一般主要分成两种:一是以齿轮、剃齿、热处理为主,我们通常将其称为剃齿工艺。
另一种则是以滚齿、磨齿和热处理为主,我们通常称之为磨齿工艺。
通过将两种方式进行对比,我们发现,磨齿工艺加工设备相对来讲投入比较大,不仅是因为磨齿的价格比较昂贵,同时也是因为磨齿机床的结构和工艺相对比较复杂,生产的效率不理想,因此我们要对其预留出相应的磨削余量以便磨齿磨削加工的时候进行使用,这种方式加大了能源和材料的消耗,不建议使用在大批量、低成本同时对质量要求较高的齿轮制造需求中。
剃齿工艺具备加工过程灵活、生产效率高,同时机械化自动程度高等优势,因此在在实际进行加工的过程中我们也经常对这项工艺进行使用。
但是在齿轮经过热处理以后淬火形成了硬齿面,因此将产生变形的情况,使得齿轮的整体精度大大地下降,通常会下降1到2级左右,另一方面,在剃齿的过程中也极易产生凹凸的想象。
通过实际的应用和时间证明,采用剃齿工艺的方法对高级齿轮进行制造,关键在对热处理问题进行解决,防止其精度降低情况的产生和出现,并且也要有效的将剃齿过程中产生凹凸齿形的难题进行合理的解决,保证工艺制造业的有效发展和进步[3]。
1 改进热处理工艺流程
通常情况下,硬齿面齿轮加工生产的工艺流程是齿胚――滚齿――剃齿刀凸形齿修形和抗热变形修形――剃齿――渗碳、淬火、回稳――检验――成品。
解决热处理变形和对精度进行降低的时候,我们可以采用生产能力相对比较强、性能稳定和质量好、热处理变形量相对较小的工艺流程进行操作,这个工艺流程主要具备连续碳氮共渗的特点,工艺路线是:上料――脱脂、预氧化――加热――碳氮共渗――降温扩散――清洗――回火――降温――卸料[4]。
整个流程的开展过程中电气控制部分氛围程序控制环节、温度控制环节、碳势控制环节和计算机控制环节。
整个程序控制环节控制整个流程的动作,实现了零件的清洗、加工等相关过程,可以对温度、火势等进行相应的设定和查询,同时这种方式也能对工作状态、记录情况进行实施监视,以这种方式对流程进行有效地控制和处理。
温度控制系统中我们要对控制加热炉、回火炉的温度进行有效地管理,渗碳炉在840摄氏度和930摄氏度控制温差时要将温差控制在上下不超过5摄氏度,回火炉的炉温在200摄氏度的时候均匀性也是最好的。
碳势控制系统对加热炉内的碳势要进行相应的控制和管理,一般情况下,碳势的控制范围内通常掌握在≤±0.05%C,齿轮的表面渗碳层深度一般在0.6到1.8毫米,
当层深的波动达到一定的范围时,同一批材料或是同一工件的数值一般是:层深≤1毫米的时候,偏差在≤±0.1毫米;当层的深度>1毫米的时候,偏差在≥±百分之十。
因此计算机控制系统通过对以上系统中的各项环节进行监控,我们在对数据进行记录的过程总,通过查询整个流程中的各项参数,对整体设备的运行状态能够进行更有效的控制[5]。
这项工艺流程的开展中的热处理齿轮连续进入了四个
加热室中的加热炉区,通过对其进行加热和碳氮共渗,碳势和温度在控制的过程中将更加准确,特别是无井式炉人为的操作误差将得到十分有利的控制,零件在经过热处理质量和批量的同一性将得到更有效的保证。
通过我们相关的实践证明:通过这种工艺热处理的齿轮齿面比较耐磨,不容易出现点蚀的情况,因此相对其他方式来讲平均的使用寿命相对较长,与井式变形量相对较少了20%到40%,这种方式共渗介质甲烷和氮气的价格相对较低,原材量的成本能得到有效地控制,生产环境也将得到十分有效地改善。
2 合适的剃齿加工方式
剃齿作为齿形加工过程中的一道重要的工序,不仅能对齿形的误差进行修正,同时对齿距的误差和齿向的误差都能起到一定的修正作用,因此在经过了剃齿加工的齿轮无周期性变化的传动误差,传动中不易产生激振频率,因此传动的
噪声相对比较温和,甚至在一定程度上要比同等精度的磨齿还要完善,由于齿轮工作的平稳性相对较强,因此精度也会相对比较准确。
这种工艺方式将传统的轴向剃齿法进行了彻底的摒弃,而是采用径向法对剃齿进行加工。
径向剃齿法在进行剃削工作的开展过程中,径向剃齿的齿形、齿向、修形都是在经过了剃齿刀齿部修磨之后进行完成的,因此这种方式比较容易对修形量进行控制和掌握,剃齿刀和齿轮之间通过线做基本的接触方式,剃齿的过程相对来讲对比较稳定,因此具有生产效率高、刀具耐用程度强、齿形精准度高和加工表面粗糙程度相对较低的优势,由于强制性的齿向修正能力较好,因此在经过修剃后零件的稳定性会更强[6]。
3 结束语
以上是对硬齿面齿轮的加工技术和相关工艺方式的改
进措施,成功在7级以上硬齿面齿轮大批量生产中进行应用。
由于我们不需要对磨削的余量进行保留,因此渗碳层可以相应的减少,这样不仅对渗碳的时间进行了相应的缩短,同时还大大的对工作效率进行了提高,很大程度上节省了材料和能耗问题。
另一方面上,由于我们采用的方式是径向法剃齿加工技术,因此对轴向剃齿法的走刀流程也进行了节约,对生产效率还能达到进一步的提升。
通过对这项技术的应用,能为相关产业带来十分明显的经济收益,因此我们应该加强
这项技术的使用和推广,使其能有效的对我国整体的经济水平和相关产业效益进行进一步提升和发展。
参考文献
[1]白城.硬齿面齿轮加工技术进展及展望[J].四川水泥,2016,35(7):133.
[2]郑喜朝.硬齿面齿轮精加工技术的现状与展望[J].新技术新工艺,2013,27(4):88-90.
[3]吕明,梁国星.硬齿面齿轮加工技术进展及展望[J].太原理工大学学报,2012,43(3):237-242.
[4]林阔,董福超.硬齿面齿轮加工技术研究及应用[J].企业文化(中旬刊),2016,11(1):276.
[5]钱利霞,李华,肖启明,等.硬齿面齿轮加工技术研究及应用[J].热加工工艺,2011,40(2):184-185+187.
[6]李涛涛,武永福,权中华,等.硬齿面齿轮加工技术展望[J].金属加工(冷加工),2013,32(4):18-19.
作者简介:高宇(1983-),男,山西省神池县人,2006年毕业于东北大学,工学学士。