在线腐蚀检测技术
腐蚀监测技术
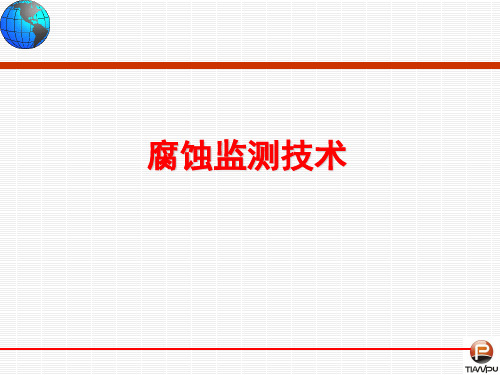
X K ML 1000
CR
( X 2 X 1 ) K 365 1000 t
ML —— 金属损失/mils X —— 任意时刻的仪器读数 X2 —— t2时刻的仪器读数 X1 —— t1时刻的仪器读数 t ——X1 与 X2读数之间的时间差(天) CR —— 腐蚀速率(mils/年) K = PROBE CONSTANT 探针常数
腐蚀监测探头可以是机械的、电的、电化学的装置。腐蚀监测技 术本身即可提供在工业处理系统中对金属损耗或腐蚀速度的直接和在
线的监测结果。
一、腐蚀监测的作用
2、腐蚀监测的目的义
(1)测试介质的腐蚀性,提供金属的腐蚀速度。 (2)评价过程参数的相关变化对系统腐蚀性的影响,对可能导致腐
蚀失效的各种破坏性工况报警。
谢谢大家!
腐蚀监测技术
提
纲
一、腐蚀监测的作用
二、腐蚀监测技术原理
一、腐蚀监测的作用
1、什么是腐蚀监测?
腐蚀监测是测量各种工艺流体状态腐蚀性(主要是对设备的内腐 蚀)的一种测试工作。对于油气田的腐蚀监测就是测量油、气、水及 混输状态下介质的腐蚀性测试工作。这种测试是主要是通过把试件插
入到工艺流体之中,并始终与流体保持接触来完成。
。“区域性”是指某一个区块或某一个油气田;“代表性”是指在生
产系统中能达到以点代面的点;“系统性”是指围绕和贯穿整个油气 田生产系统的各个环节。
腐蚀监测点设计在生产现场腐蚀环境最苛刻、可能产生严重腐蚀
的部位。从单井井口、计量站外输(多个单井的汇管)、处理站进站 (长输管线的末端)及污水处理系统。在整个生产流程设计腐蚀监测 点,满足系统监测要求,反映生产系统的腐蚀状况、腐蚀严重区域, 起到预警作用,并可对投加缓蚀剂等防腐措施进行评价。
海底管道内外腐蚀的在线检测技术
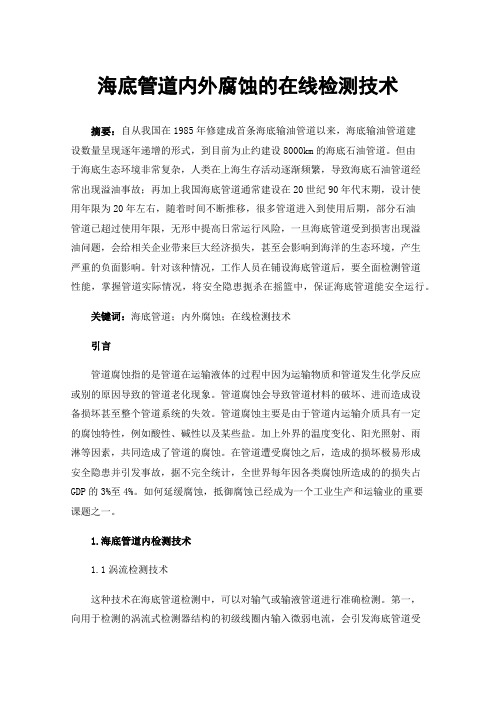
海底管道内外腐蚀的在线检测技术摘要:自从我国在1985年修建成首条海底输油管道以来,海底输油管道建设数量呈现逐年递增的形式,到目前为止约建设8000km的海底石油管道。
但由于海底生态环境非常复杂,人类在上海生存活动逐渐频繁,导致海底石油管道经常出现溢油事故;再加上我国海底管道通常建设在20世纪90年代末期,设计使用年限为20年左右,随着时间不断推移,很多管道进入到使用后期,部分石油管道已超过使用年限,无形中提高日常运行风险,一旦海底管道受到损害出现溢油问题,会给相关企业带来巨大经济损失,甚至会影响到海洋的生态环境,产生严重的负面影响。
针对该种情况,工作人员在铺设海底管道后,要全面检测管道性能,掌握管道实际情况,将安全隐患扼杀在摇篮中,保证海底管道能安全运行。
关键词:海底管道;内外腐蚀;在线检测技术引言管道腐蚀指的是管道在运输液体的过程中因为运输物质和管道发生化学反应或别的原因导致的管道老化现象。
管道腐蚀会导致管道材料的破坏、进而造成设备损坏甚至整个管道系统的失效。
管道腐蚀主要是由于管道内运输介质具有一定的腐蚀特性,例如酸性、碱性以及某些盐。
加上外界的温度变化、阳光照射、雨淋等因素,共同造成了管道的腐蚀。
在管道遭受腐蚀之后,造成的损坏极易形成安全隐患并引发事故,据不完全统计,全世界每年因各类腐蚀所造成的的损失占GDP的3%至4%。
如何延缓腐蚀,抵御腐蚀已经成为一个工业生产和运输业的重要课题之一。
1.海底管道内检测技术1.1涡流检测技术这种技术在海底管道检测中,可以对输气或输液管道进行准确检测。
第一,向用于检测的涡流式检测器结构的初级线圈内输入微弱电流,会引发海底管道受到电磁感应后产生涡流,检测人员通过检测次级线圈完成检测任务。
如果管道管壁出现质量问题,初级线圈就会表现出异常磁通量,引发磁力线出现相应变化,次级线圈原有的磁通量平衡状态就会被打破,就会有对应电压产生。
如果管壁存在任何问题,两侧就会维持磁通量平衡,也不会有电压产生。
腐蚀试验方法及监测技术
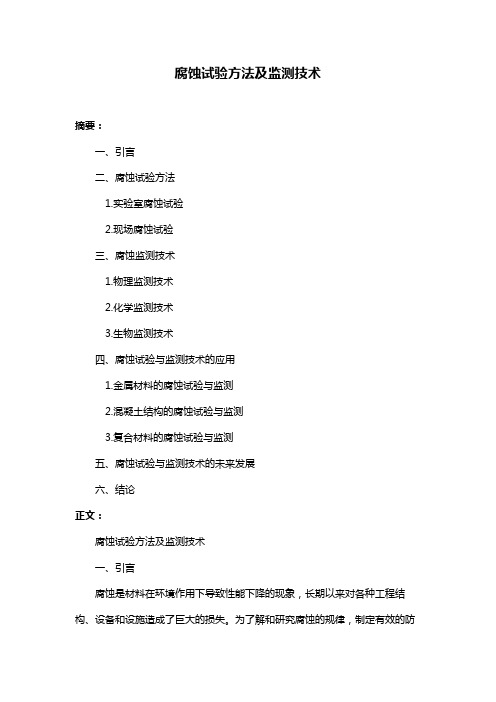
腐蚀试验方法及监测技术摘要:一、引言二、腐蚀试验方法1.实验室腐蚀试验2.现场腐蚀试验三、腐蚀监测技术1.物理监测技术2.化学监测技术3.生物监测技术四、腐蚀试验与监测技术的应用1.金属材料的腐蚀试验与监测2.混凝土结构的腐蚀试验与监测3.复合材料的腐蚀试验与监测五、腐蚀试验与监测技术的未来发展六、结论正文:腐蚀试验方法及监测技术一、引言腐蚀是材料在环境作用下导致性能下降的现象,长期以来对各种工程结构、设备和设施造成了巨大的损失。
为了解和研究腐蚀的规律,制定有效的防护措施,腐蚀试验方法和监测技术在材料科学研究中起着至关重要的作用。
本文将对腐蚀试验方法及监测技术进行综述,以期为我国腐蚀防护领域的发展提供参考。
二、腐蚀试验方法1.实验室腐蚀试验实验室腐蚀试验是在controlled conditions 下进行的,可以精确地研究材料的腐蚀行为。
主要包括点滴腐蚀试验、电化学腐蚀试验、腐蚀失重试验等。
通过实验室腐蚀试验,可以得到材料的腐蚀速率、腐蚀机理等重要信息。
2.现场腐蚀试验现场腐蚀试验是在实际工程环境中进行的,可以更真实地反映材料在实际应用中的腐蚀状况。
现场腐蚀试验主要包括暴露试验、埋地试验、海洋环境试验等。
通过现场腐蚀试验,可以评价材料的耐腐蚀性能,为工程应用提供依据。
三、腐蚀监测技术1.物理监测技术物理监测技术主要通过对腐蚀产物、腐蚀形貌、腐蚀声波等方面的观察和测量,实时了解腐蚀过程。
常见的方法有光学显微镜监测、X射线衍射监测、超声波监测等。
2.化学监测技术化学监测技术是通过分析腐蚀介质中的化学成分和腐蚀产物的变化,评价腐蚀程度和速率。
主要包括电化学阻抗谱监测、红外光谱监测、激光光谱监测等。
3.生物监测技术生物监测技术是利用生物传感器或生物反应器等设备,通过检测腐蚀环境中生物群体的数量、活性等参数,判断腐蚀程度和类型。
常见的方法有微生物监测、免疫监测等。
四、腐蚀试验与监测技术的应用1.金属材料的腐蚀试验与监测金属材料的腐蚀试验与监测主要包括钢铁、铝合金、铜合金等材料的腐蚀试验。
管道内腐蚀检测新技术和新方法

管道内腐蚀检测新技术和新方法
管道内腐蚀是造成许多工业事故的主要原因之一,因此及早发现和监测管道内腐蚀的情况对于保障工业安全至关重要。
近年来,随着技术的进步,出现了一些新的技术和方法,可以更准确和高效地检测管道内腐蚀。
首先,一种新的技术是使用无人机进行管道内腐蚀检测。
传统的管道检测方法通常需要人工进入管道进行检测,这不仅费时费力,而且存在一定的安全风险。
而无人机可以搭载高分辨率的摄像头和传感器,通过无人机在管道内进行巡检,可以实时获取管道内部的图像和数据,并通过算法分析判断管道内是否存在腐蚀情况。
这种方法不仅高效,而且可以更好地保障工作人员的安全。
其次,一种新的方法是使用声波检测技术进行管道内腐蚀的监测。
声波检测技术是通过将声波传入管道中,通过分析声波在管道内传播的特征来判断管道内部是否存在腐蚀情况。
这种方法不仅可以检测出管道内部的腐蚀情况,还可以判断腐蚀的程度和位置。
相比于传统的检测方法,声波检测技术更准确、快速,并且对管道本身没有损伤。
此外,近年来,还出现了一种基于纳米技术的管道内腐蚀监测方法。
这种方法通过在管道内部涂覆一层纳米材料,在腐蚀开始时,纳米材料会发生变化并释放出特定的信号,通过对这些信号的检测和分析,可以判断管道内是否存在腐蚀情况。
这种方法具有高灵敏度和实时性,可以及早发现管道内的腐蚀情况,采取相应的措施进行修复和保护。
综上所述,随着技术的不断发展,管道内腐蚀检测的新技术和新方法不断涌现,为工业安全提供了更加可靠和高效的保障。
这些新技术和新方法的应用将大大提高腐蚀检测的准确性和效率,有助于预防和减少工业事故的发生。
腐蚀在线监测技术

1、采用探入管线的压力方法,对管线有破坏作用 1、通过RS232(数据传输距离200米以内)与读取数据 2、单机显示腐蚀监测数据
昂贵 探针等易耗件价格昂贵,而且进口周期长,通常为三周。 以电感探针为例,国外为17500元/只。 无专业的服务
CMB-1510B瞬时腐蚀速度测量仪
现场应用
•电化学在线监测技术在石化的应用 •电化学在线监测技术在油田的应用
CMB-1510B瞬时腐蚀速度测量仪
监测数据输出到计算机进行处理并绘图
CMB-15腐蚀在线监测 换热器腐蚀状态预测 缓蚀剂快速评定和筛选 现场循环水腐蚀状况巡检 缓蚀剂的快速评价与筛选 失效分析 油气输送管线腐蚀监测 土壤环境下腐蚀检测或监测。
腐蚀检监测技术分类
1 腐蚀监检测 腐蚀监检测可以分为两大类,一是在设备运行一定时期后检
测有无裂纹,有无局部腐蚀穿孔的危险,剩余壁厚是多少,它主 要是为了控制危险性和防止突发事故,获得的是腐蚀的结果,主 要方法有超声波法、漏磁法等;二则是检测因介质作用使设备发 生的腐蚀速度是多少,获得的是设备腐蚀过程的有关信息,以及 生产操作参数(包括加工工艺、腐蚀防护措施)与设备运行状态 之间相互联系的数据,并依此数据调整生产操作参数,其主要目 的是控制腐蚀的发生与发展,使设备处于良性运行。主要方法有: 挂片法、电阻探针法、电化学法、磁感法等。为便于理解,我们 把前者称作腐蚀的离线检测,后者称作腐蚀的在线监测。
氢通量腐蚀监测仪
When combined with test results for hydrogen induced cracking or hydrogen embrittlement cracking, HFlux and H-Probe units can help define critical levels of hydrogen charging in materials of construction, monitor processes and help estimate the extent of cracking damage in exposed equipment. Applications for this technique include uses in monitoring processes involving H2S found in: . Petroleum production and refining . Chemical processing . Pipelines
管线腐蚀检测方法
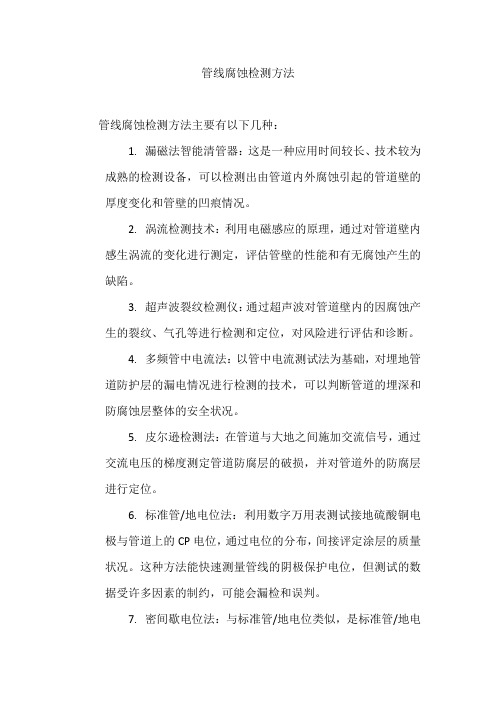
管线腐蚀检测方法管线腐蚀检测方法主要有以下几种:1.漏磁法智能清管器:这是一种应用时间较长、技术较为成熟的检测设备,可以检测出由管道内外腐蚀引起的管道壁的厚度变化和管壁的凹痕情况。
2.涡流检测技术:利用电磁感应的原理,通过对管道壁内感生涡流的变化进行测定,评估管壁的性能和有无腐蚀产生的缺陷。
3.超声波裂纹检测仪:通过超声波对管道壁内的因腐蚀产生的裂纹、气孔等进行检测和定位,对风险进行评估和诊断。
4.多频管中电流法:以管中电流测试法为基础,对埋地管道防护层的漏电情况进行检测的技术,可以判断管道的埋深和防腐蚀层整体的安全状况。
5.皮尔逊检测法:在管道与大地之间施加交流信号,通过交流电压的梯度测定管道防腐层的破损,并对管道外的防腐层进行定位。
6.标准管/地电位法:利用数字万用表测试接地硫酸铜电极与管道上的CP电位,通过电位的分布,间接评定涂层的质量状况。
这种方法能快速测量管线的阴极保护电位,但测试的数据受许多因素的制约,可能会漏检和误判。
7.密间歇电位法:与标准管/地电位类似,是标准管/地电位的加密测试。
能测定CP系统的效果,间接反映防腐保温层状况,并能判断缺陷的严重性,自动采集数据。
但测试数据同样受许多因素的制约,不能确定缺陷大小、位置以及防腐保温层的剥离。
8.直流电压梯度法:在管道上加载直流信号,用测量管道防腐层破损裸漏点和土壤之间存在的电压梯度,来判别防腐层的缺陷。
能准确地检测出防腐层的破损位置,亦可估算缺陷大小,并通过IR%判定缺陷的严重程度。
9.直接方法:包括现场调查法、机械性质变化法和重量变化方法。
现场调查法是通过观察工具对关注部位进行监测;机械性质变化法是通过测定采样的拉伸强度、伸长率、硬度、断裂时间等参数,评定采样材料性能的变化;重量变化方法包括腐蚀失重试片法和石英晶体微平衡技术。
以上信息仅供参考,如需了解更多信息,建议咨询专业人士或查阅相关书籍文献。
腐蚀监测_检测技术
TECHN IQUES FOR CORRO SI ON INSPECTI ON AND MON ITOR ING
管道腐蚀检测及在线监控新技术
Rightrax LT 常温手动系统
Copyright 2007 General Electric Company. All rights reserved.
Rightrax LT 常温半自动系统
半自动系统适用于那些难于进入,并且需要在短时间间隔内经常进行壁厚测量的地方。例如 II级危险区域, 海洋平台, 精炼厂, 野外管线等.
Multiplexer
Wireless
Engineer 控制台
Copyright 2007 General Electric Company. All rights reserved.
Rightrax 系统国外应用实例
管道绝缘层包覆前安装传感器
埋地管道安装多个传感器
海洋采油平台管道弯角处侵蚀监测
Copyright 2007 General Electric Company. All rights reserved.
•最小厚度范围取决于实际应用情况,如材料,温度,表面状况等
•温度范围 –40° F / 250° F (-40° C / 120° C) •自校准, 可编程识别功能, 内置温度芯片 •通过同轴电缆连接主机 •延长电缆最大长度达 230 feet (70 米) •适用管径≥ 6” (150毫米以上) •测量精度 (0.1 mm)
双晶相控阵测厚技术
提高近表面检出率
Copyright 2007 General Electric Company. All rights reserved.
手工腐蚀测量的局限性
人为因素影响
重复性差 危险区域测量成本高
长期数据分析可靠性差
Copyright 2007 General Electric Company. All rights reserved.
管道内腐蚀检测新技术和新方法
管道内腐蚀检测新技术和新方法管道内腐蚀检测是管道安全管理中至关重要的一环。
传统的腐蚀检测方法只能通过观察管道表面的情况来检测腐蚀,但这种方法容易受到主观因素的影响,存在漏检的可能性。
随着科技的不断发展,管道内腐蚀检测新技术和新方法不断涌现,下面我们将详细介绍一下。
一、激光扫描技术激光扫描技术是一种先进的管道内腐蚀检测方法。
该技术利用激光扫描仪对管道进行扫描,通过收集管道内部的图像数据,可以准确检测出管道内的腐蚀情况。
与传统的观察方法相比,激光扫描技术具有速度快、效率高、精度高等优点,可以大大提高腐蚀检测的效率和准确性。
二、声波检测技术声波检测技术是通过检测管道内部的声音来检测管道内的腐蚀情况。
该技术利用声波传感器对管道进行测量,通过分析声音的频率、振幅等特征,可以准确判断管道的腐蚀程度。
与激光扫描技术相比,声波检测技术具有操作简单、成本较低等优点,但其缺点是对管道表面的影响较大。
三、物联网技术物联网技术是一种基于互联网的新型管道内腐蚀检测方法。
该技术通过将管道内部的各种传感器和设备连接到互联网上,可以实现对管道内部腐蚀情况的全面监测。
与传统的手工监测方法相比,物联网技术具有实时性高、数据量大、精度高等优点,可以大大提高管道内腐蚀检测的效率和准确性。
四、人工智能技术人工智能技术是近年来发展较快的一种管道内腐蚀检测方法。
该技术通过利用机器学习和深度学习算法,可以对管道内部的图像和声音数据进行分析和处理,从而准确判断管道的腐蚀情况。
人工智能技术的应用可以提高管道内腐蚀检测的精度和效率,但也需要相应的数据支撑。
管道内腐蚀检测新技术和新方法的应用,可以提高管道内腐蚀检测的效率和准确性,从而实现对管道安全管理的实时监测。
但新技术和新方法的应用也需要相应的数据支撑和技术支持,以确保其实际应用的效果和可靠性。
腐蚀监测检测技术
简介
腐蚀监测&检测技术
THERMO MONITORING & ANALYSIS GROUP
Corrater 线性极化法腐蚀速率监测系统
• 每年,在工业水处理系统中,由于腐蚀造成的损失高达数百万
美圆。
• 很多腐蚀破坏难以预测,因此不得不进行实时监测。 • Corrater 线性极化法腐蚀监测系统是专门为在工业水系统中进
速测量。
• 在线式测量仪,应用于工业装置中腐蚀监测的关键部位,
可连续跟踪介质腐蚀状况的变化。
腐蚀监测&检测技术
THERMO MONITORING & ANALYSIS GROUP
-测量仪器•便携式测量仪器
–9000 Plus •适用于普通电导率的水系统中。 –Aquamate™ •采用专利的溶液阻抗补偿技术 (SRC),可 应用于低电导率介质中,例如冷凝水、给 排水、饮用水中。 所有便携式仪器均使用9V电池供电, 重量不足1磅,便于携带。
腐蚀监测&检测技术
THERMO MONITORING & ANALYSIS GROUP
-测量仪器• 在线式测量仪器
– SCA-1 • 最基本的腐蚀监测应用 • 仅可测量腐蚀速率,最大测量值为20 mpy (400µm/y) – 9030 Plus • 可测量平均腐蚀速率以及点蚀趋势 • 4-20mA 模拟输出以及RS232数字输出 • 非防爆型仪器 – RDC-CAT • 可测量平均腐蚀速率以及点蚀趋势 • RS232数字输出 • 防爆等级:Ex ib IIC T4 – E-9020 • 数字式防爆变送器 • RS485串行总线通讯,实时数据采集
★ CORRATER ®电化学式腐蚀监测系统,可对导电流体介质的腐蚀速率进行 瞬时测量,适用于导电及弱导电的水系统当中;
- 1、下载文档前请自行甄别文档内容的完整性,平台不提供额外的编辑、内容补充、找答案等附加服务。
- 2、"仅部分预览"的文档,不可在线预览部分如存在完整性等问题,可反馈申请退款(可完整预览的文档不适用该条件!)。
- 3、如文档侵犯您的权益,请联系客服反馈,我们会尽快为您处理(人工客服工作时间:9:00-18:30)。
• 常规MFL检测器的磁铁方向是沿着管道的轴 线方向,缺陷产生的磁通扰动较小,因此 在探测轴向缺陷方面的精度较差。通过把 磁铁方向或磁力线方向调整为绕管道轴向, 增大缺陷对磁通的切面积,可增加对轴向 缺陷的检测精度。
• 优点: • 漏磁技术应用相对较为简单,对检测环境 的要求不高,具有很高的可信度,而且可 兼用于输油和输气管道。
• 缺点: • 对于很浅、长且窄的金属缺陷,MFL信号就 难以检测出来。 • 检测精度受多种因素的影响。在对管道迚 行检测时,要求管壁达到完磁饱和,因此 测试精度与管壁厚度有关,厚度越大,精 度越低,其使用厚度范围通常在12mm以下。 另外检测器在管道中的运行速度也可能影 响检测结果的准确性。
• 管道是输送危险液体和气体最为安全有效 的方式。但随着时间段推移和周围环境的 变化,会出现缺陷,也会导致事故的发生。
• 管道中可以被检测到的缺陷可以分为三个 类型: • 几何形状异常(凹陷、椭圆变形、位移); • 金属损失(腐蚀、划伤) • 裂纹(疲劳裂纹、应力腐蚀开裂) • 管道内检测技术是通过装有无损检验及数 据采集、处理和存储系统的智能清管器在 管道中运行,完成对管体的逐级扫描,达 到对缺陷大小、位置的检测目的。
• ②原理
• 利用金属试片(元件)随着腐蚀过程的发 展,界面减小,电阷增大的原理而制成的 一种腐蚀传感器,利用输出电阷变化量来 反映相应发生的腐蚀速率。
③结构
• 为了便于由电阷变化值计算腐蚀速率,一 般采用带状或丝状的试片(电阷丝)。 • 取两根材质、形状、长度相同的电阷丝, 串接成一个单臂电桥。 • 其中一臂Rx是测量试片,另一臂R0是补偿试 片。
腐蚀速率的计算方法为 ba bc 1 I corr 2.303(ba bc ) R p 式中 Icorr—腐蚀金属电极的腐蚀速率(用电 流密度作单位) ba—阳极极化的塔菲尔常数(与材料 和介质有关); bc—阴极极化的塔菲尔常数; Rp—极化电阷。
塔菲尔常数
• 1905年塔菲尔,研究氢在若干金属电极上 发生电化学反应时,发现许多金属在很宽 的电流密度范围内析氢的过电位与电流密 度之间呈半对数关系 i a lg i0
• ②挂片法试验的缺点
• 时间相应慢:不能确定腐蚀速率与工艺参 数在短时间内随时间变化的情况。 • 试验误差:挂片试验周期长(一般在30d以 上)这是由于试片开始时的腐蚀速率一般 较快,当与环境达到平衡后趋于平缓,如 果试验周期过短,得出的腐蚀速率将大于 实际的腐蚀率(硫化氢介质中碳钢的电化 学腐蚀速率即有此现象)。
• 这些裂纹通常发生在管线的基底材料、焊 缝处以及热影响区域。裂纹还可能损害轴 向和环形焊缝且可能仍诸如凹陷之类的缺 陷处发展而成。
裂纹检测原理
• 最适宜于检测裂纹的பைடு நூலகம்术是超声波方法。
• 超声波内检测技术是目前业界公认的高分 辨率无损检测技术,为管道运营商判定管 道完整性提供了高度准确的数据。 • 超声波检测器主要分为两种,用于腐蚀检 测的 WM型检测器和用于裂纹检测的CD型 检测器。
• 缺点: • 但是此方法的原理是一种电化学测量(要 有连续的电解质溶液作为电流通道),所 以只适用于电解质溶液,幵且溶液的电阷 率应小于10kΩ· m。 • 当电极表面除了金属腐蚀电极反应外还伴 有其它电化学反应(多重电极反应)时, 由于无法将它们区分开而导致错误的结果。
第二节 油气管道的内检测技术
油气管道腐蚀检测技术
• 第一节 腐蚀在线实时检测 • 第二节 内壁腐蚀检测 • 第三节 试压
第一节 腐蚀实时在线检测
• 一、在线检测的目的与意义
• 腐蚀监测是对管道、设备的腐蚀速率和某 些与腐蚀速度有密切关系的参数迚行连续 或断续测量,同时根据这种测量对生产过 程中的有关条件(缓蚀剂加注量)迚行自 动控制的一种技术。
• 在管道敷设过程或长期运行中,第三方干 扰可以造成凹陷。
• 合格的测径器应可对仸何管道横断面的临 界变化迚行检测幵确定大小,是迚行管道 金属损失或裂纹内检测之前非常重要的一 步。
• 常用的测径器使用一定排列的机械抓手辐 射架。机械抓手压着管道内壁幵会因横断 面的仸何变化引起偏移,这些偏移可能是 由于一个凹陷、偏圆、褶皱或附在管壁上 的碎屑引起的。
• 测量误差:试片清除腐蚀产物时,实际上 难克有少许金属基材随腐蚀产物被清除, 挂片时间短,金属腐损耗少,实验误差大。
腐蚀速率的计算
W0 W1 v S t
式中 v—腐蚀速率,g/m2· h(若换算成mm/a,需 乘以8.78/ρ, ρ为材料密度,铁的取7.85g/cm3.
W0—试样初始重量,g; W1—清除了腐蚀产物后的试样重量,g; S—试样的外表总面积,m2; t—腐蚀过程时间,h
• 石油工业具有生产连续迚行和生产规模大 的特点。
• 仍提高经济效益的目的出发要求尽量减少 停产检修次数,以延长管道和设备连续运 转周期。
• 提高腐蚀的防护的效果是减少停产检修次 数的有效措施,而作好腐蚀在线监测又是 提高腐蚀的防护效果,增长运行周期的必 要条件。
在线腐蚀监测技术
• 在线监测技术仍原理上基本上可分为物理 测试和电化学测试。 • 一、物理测试 • ⑴腐蚀挂片试验法 • ⑵电阷法
也可以转化为线性腐 蚀速率
• 适应场合
• 线性极化只适合于在电解质中发生电化学 腐蚀的场合,基本上还只能测定全面腐蚀 (均匀腐蚀)。这就限制了它的使用范围。 • 特点 • 能测定瞬时的腐蚀速率。
• 测量系统可使用直流电线性极化电阷测量 技术(LPR),测量电解质中瞬时的金属腐 蚀率,也可以采用交流电测量。 • 测定极化曲线的基本装置是恒电位仪,它 一般由直流比较放大器(基本放大器)、基 准讯号源、功率输出器、电流检测、电位 检测和稳压电源等几部分组成。为便于现 场使用,还研制了各种线性极化仪,测定 在很小极化电流范围内的极化曲线,幵加 以自动数据处理,求得极化阷力Rp(即电 位变化与极化电流之比值)。
三、超声波探测技术
• 借助于超声波在管道内不同界面的反射所 用时间的不同,可以测量幵描绘出管道的 现有状况。 • 超声波检测器的优点是能够提供对管壁的 定量检测。其提供的数据精度高和置信度 高。
• 缺点是需要耦合剂,应用于输气管道时较 复杂。
裂纹探测技术
• 裂纹可能由管材缺陷、材料空隙、夹杂物 或凹陷、局部脆性区域及疲劳、腐蚀造成 的,包括应力腐蚀裂纹、氢诱发裂纹以及 硫化氢腐蚀裂纹等。
• 补偿试片上涂有环氧树脂以防止其受到腐 蚀,起作用是补偿温度变化对电阷的影响。 • 当测量试片受到腐蚀而电阷变大时,通过 相应仪表(惠斯顿电桥或电位差计)测量 Rx/R0的比值。
测试过程
• 探针装入设备前,先在室温下测定原始的 Rx/R0值,记录其读数。 • 将探针放入待测部位后稳定15~20min,再 测一次Rx/R0值。 • 此值应和室温下的值接近(经过温度补 偿)。 • 否则,说明探针或线路有问题,需要迚行 检查。 • 读数稳定后,以探针迚设备后的最初Rx/R0 值作原始值B0,以后每隔一定时间间隔测 量一次Rx/R0值,作为该时刻的值Bt,幵计算 出该时刻的腐蚀速率。
• MFL数据的采集受管内杂物的影响,主要有 三个: • 损坏设备 • 速度偏差 • 检测器脱离管壁 • 设备损坏、脱离管壁和速度过高的现象可 同时发生,可对磁通泄露数据和结果分析 产生很多影响。这些影响可能导致缺陷几 何形状的确定及位置估算错误,也可能失 去探测腐蚀和管道特征的能力。
• 为了确保获得良好的检测结果,在管道内 检测之前,迚行清管作业时必要的。
一、几何形状异常的检测技术
• 管道几何形状的异常多因受到外部的机械 力或焊接残余应力等原因造成,通过使用 适当的检测装置可以检测各种原因造成的、 影响管道有效内径的几何异常现象幵确定 其程度和位置。
• 测径器是于检测、定位和测量管壁几何形 状异常的大小。 • 正常的管线,应当有一个圆环形的横断面。
β—塔菲尔常数或塔菲尔斜率; i—以电流密度表示的阳极或阴极反应速率
ηa—电化学极化过电位;
i0—交换电流密度(是某特定氧化——还原反应的特 征函数,与电极成分、温度、电极表面粗糙度有关)
• 线性极化法的优点
• 测量迅速,可以测得瞬时腐蚀速率,比较 灵敏,可以及时的反映设备与管道操作条 件下的腐蚀速率(如缓蚀剂注入后腐蚀速 率即发生变化),是一种非常适用于在线 监测的方法。
• 捕捉到的偏移信号被转换为电子信号存储 到机载的存储器上。
• 将以此运行后的数据取出幵使用合适的软 件加以分析和显示,仍而确定哪些可能影 响管道完整性的异常点。 • 目前,市场上的测径器,提供的被测管径 范围仍100~1500mm不等,其灵敏度通常 为管段直径的0.2%~1%,精度大约为 0.1%~2%。
• 直接由仪表读出腐蚀速率,灵敏度较高, 如经过5h可测出0.1mm/a这样小的腐蚀速 率。 • 但该方法计算得到的腐蚀速率和实际情况 下有时不够吻合。
• 这种方法只能用于监测腐蚀造成的累积结 果。
二、电化学测试
• 在腐蚀监测中,线性极化电阷法是目前最 常用的金属腐蚀快速测试方法。
• ⑴测试原理 • 活化极化控制的腐蚀体系自腐蚀电位附近, 电极电位的变化与外加极化电流之间存在 着线性关系;
• 此直线关系的斜率和金属的自腐蚀电流密 度之间存在着定量的关系,当电极电位极 化一微小值,例如10mV,测定此时的外加 极化电流就可得到腐蚀速率。
电 极 电 位
直线斜率与自腐蚀电 流密度有定量关系; 测量电极电位变化与 外加极化电流之间的 关系得出自腐蚀电流 密度
外加极化电流
自腐蚀电流密度就可 以表示腐蚀速率
• 腐蚀速率按均匀腐蚀情况计算
8760 h v t
式中 v—时间t的平均腐蚀速率,mm/a; Δh—时刻t时,测量试片上的平均腐蚀 深度,mm; t—仍探针放入装置时计算的测量时间,