现代加工技术期末复习题
2021年度现代数控技术期末模拟考试题及参考答案(试卷C)
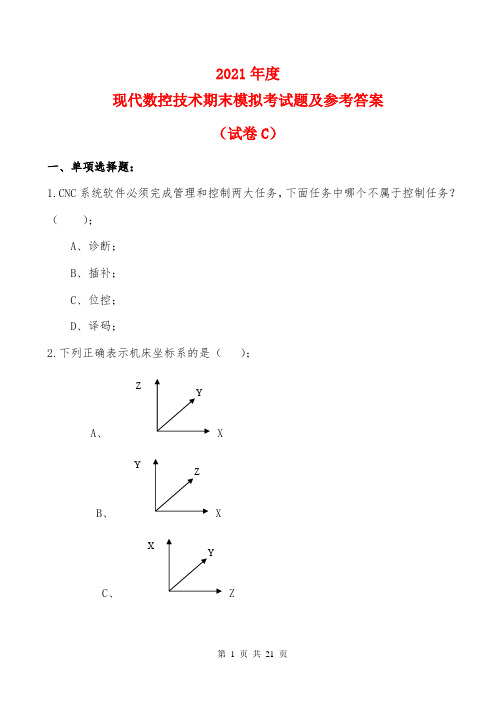
2021年度现代数控技术期末模拟考试题及参考答案(试卷C )一、单项选择题:C 系统软件必须完成管理和控制两大任务,下面任务中哪个不属于控制任务?( );A 、诊断;B 、插补;C 、位控;D 、译码;2.下列正确表示机床坐标系的是( );A 、XB 、XC 、 ZZYYZXYD 、 Y3.脉冲当量的大小决定了加工精度,下面哪种脉冲当量对应的加工精度最高? ( );A 、1um/脉冲;B 、5um/脉冲;C 、10um/脉冲;D 、0.01mm/脉冲;4.设编程原点在工件的上表面,执行下列程序后,钻孔深度是( )。
G90 G01 G43 Z-50 H01 F100 (H01补偿值-2.00mm )。
A .48mm ; B. 52mm ; C. 50mm 。
5.直线的起点坐标在坐标原点,终点坐标为A (x a 、y a ),刀具的坐标为P (x 、y )。
用逐点比较法对该直线进行插补时的偏差函数是( )。
A. F =x ·y -x a ·y a ;B. F =x a ·y -y a ·x ;C. F =x a ·x -y a ·y ;D. F =x a +y a -x -y ;6. 加工中心与其他数控机床的主要区别是( )。
A.有刀库和自动换刀装置;ZXB.机床转速高;C.机床刚性好;D.进刀速度高7. 数控机床的数控装置包括( )。
A.光电读带机和输入程序载体;B.步进电机和伺服系统C.输入、信息处理和输出单元;D.位移、速度传感器和反馈系统8. G00的指令移动速度值是()。
A.机床参数指定;B 数控程序指定;C 操作面板指定。
9.编程坐标系一般指的是()。
A.机床坐标系;B. 工件坐标系;10.下面哪项任务不是数据预处理(预计算)要完成的工作?()。
A、位置控制;B、刀具半径补偿计算;C、刀具长度补偿计算;D、象限及进给方向判断;11. A步进电机的转速是否通过改变电机的()而实现。
现代石油加工题
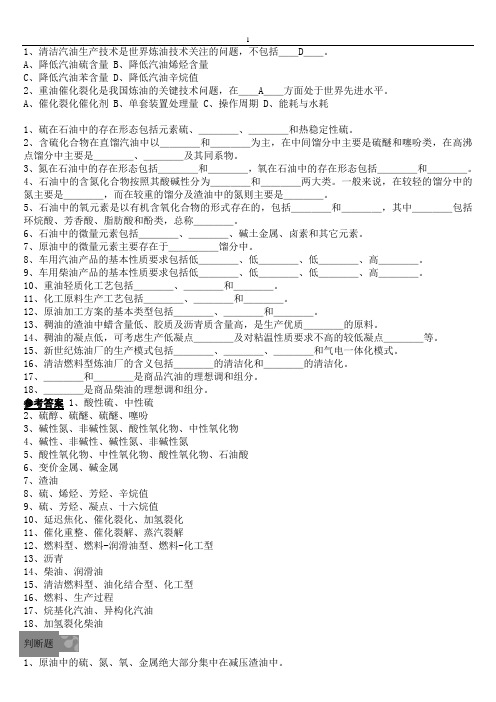
1、清洁汽油生产技术是世界炼油技术关注的问题,不包括__D__。
A、降低汽油硫含量B、降低汽油烯烃含量C、降低汽油苯含量D、降低汽油辛烷值2、重油催化裂化是我国炼油的关键技术问题,在__A__方面处于世界先进水平。
A、催化裂化催化剂B、单套装置处理量C、操作周期D、能耗与水耗1、硫在石油中的存在形态包括元素硫、____、____和热稳定性硫。
2、含硫化合物在直馏汽油中以____和____为主,在中间馏分中主要是硫醚和噻吩类,在高沸点馏分中主要是____、____及其同系物。
3、氮在石油中的存在形态包括____和____,氧在石油中的存在形态包括____和____。
4、石油中的含氮化合物按照其酸碱性分为____和____两大类。
一般来说,在较轻的馏分中的氮主要是____,而在较重的馏分及渣油中的氮则主要是____。
5、石油中的氧元素是以有机含氧化合物的形式存在的,包括____和____,其中____包括环烷酸、芳香酸、脂肪酸和酚类,总称____。
6、石油中的微量元素包括____、____、碱土金属、卤素和其它元素。
7、原油中的微量元素主要存在于_____馏分中。
8、车用汽油产品的基本性质要求包括低____、低____、低____、高____。
9、车用柴油产品的基本性质要求包括低____、低____、低____、高____。
10、重油轻质化工艺包括____、____和____。
11、化工原料生产工艺包括____、____和____。
12、原油加工方案的基本类型包括____、____和____。
13、稠油的渣油中蜡含量低、胶质及沥青质含量高,是生产优质____的原料。
14、稠油的凝点低,可考虑生产低凝点____及对粘温性质要求不高的较低凝点____等。
15、新世纪炼油厂的生产模式包括____、____、____和气电一体化模式。
16、清洁燃料型炼油厂的含义包括____的清洁化和____的清洁化。
17、____和____是商品汽油的理想调和组分。
现代切削加工技术试卷

得 分评分人 贵州大学考试试卷现代切削加工技术注意事项:1. 请考生按要求在试卷装订线内填写姓名、学号和专业年级。
2. 请仔细阅读各种题目的回答要求,在规定的位置填写答案。
3. 不要在试卷上乱写乱画,不要在装订线内填写无关的内容。
4. 满分100分,考试时间为120分钟。
题号一 二 三 四 五 总分 统分人 得分 一、填空题(每空1分,共20分)1. 切削不锈钢时,切屑的形状一般是 带状切屑 ,切削HT200时,切屑的形状一般是 崩碎切屑 。
2. 塑性材料变形程度的表示方法有 剪切角(φ) 、 相对滑移(ε) 和 变形系数(∧) 。
3. 精加工塑性金属材料时,为了避免积屑瘤,可采用的措施有: 增大切削速度、使用切削液 、 增大背吃刀量 。
(任选3种)4. 滚刀滚切齿轮时,常采用有一定粘度的切削油,其主要作用是:润滑和冷却;深孔加工时,采用大流量、高压力的切削液,其主要作用是:冷却和排屑 。
5. 在稳定切削时,刀具的六个基本角度中,影响已加工表面理论粗糙度最大的是:主偏角r κ和副偏角r κ' 。
6. 根据实际磨削深度与磨削径向进给量的关系,磨削过程一般分为初磨阶段、稳定阶段 、 清磨阶段 三个阶段。
7. 采用金刚石笔修整砂轮时采用的方法是 车削法 ,采用金刚石滚轮修整砂轮的方法是 磨削法 。
8. 整体三面刃铣刀刀齿磨钝后要刃磨 后刀面 ,铲齿铣刀齿刀磨钝后要刃磨 前刀面 ,才能保持其原来要求的廓形精度。
(前刀面 后刀面 前、后刀面)得 分评分人 9. 端铣有对称铣、不对称逆铣和不对称顺铣三种方式,铣削不锈钢和耐热合金时,为了减少硬质合金刀具的脱落,提高切削速度,宜采用 不对称顺铣 。
10. 28A·SOJT50·80-70——表示TMG28工具系统的 主柄 模块,符合ISO 标准,规格为50号锥柄7:24。
二、单项选择题(每小题2分,共20分)1. 关于金属的切削变形,下列说法正确的是 ( A )A. 金属切削过程是金属切削层在刀具前刀面的推挤作用下,发生以剪切滑移为主的塑性变形而形成切屑的过程;B. 金属切削过程是金属切削层在刀具后刀面的推挤作用下,发生以剪切滑移为主的塑性变形而形成切屑的过程;C. 车削45号钢棒时,作用在车刀前刀面上的摩擦主要以外摩擦为主,该外摩擦系数随工件的硬度、切削厚度、切削速度以及刀具的前角变化而变化;D. 根据切削第一定律(Lee and Shaffer 公式),前角增大时,剪切角减小,切屑变形增大。
现代加工技术考试重点

第一章3.现代加工技术的分类方法主要有哪些?各自有什么特点?答:按是否加热:冷加工,热加工。
至今仍有一定的使用意义,但是它远远未能反映出加工技术的全貌,过于粗糙,不够科学、严谨。
按照加工过程中所使用的能量形式:机械加工、电加工、光加工、声加工、热加工、化学加工、生物加工等。
这种分类方法有助于理解具体某种加工技术的加工机理,有助于创造新的加工技术。
按照加工对象的最终几何形状:平面加工;沟槽加工;圆柱面加工;光孔加工;螺纹加工;齿轮加工;非圆曲面(型腔)加工等。
这种分类方法对于实际生产中选择具体加工方式有指导意义。
但是,它主要适用于去除材料类加工技术的细分类,而不能适用于以变形或增加材料的方式进行加工的技术分类,也不能囊括主要以改变表面物理性能为目的的表面加工技术。
按照被加工工件加工前后材料的增减变化与否:去除(或减材)加工、增材加工、变形加工和表面加工。
该方法全面而形象,具有科学严谨性。
不过,它不像能量分类法那样能体现出加工过程的机理本质,而且比较粗略。
按广义和狭义:广义的加工概念包括去除(或减材)加工、接合加工、变形加工和表面处理等四大类,狭义的加工概念单指去除或减材加工。
这样分类基本符合习惯,但是它不能将快速成型技术、表面熔覆技术、气相沉积技术等涵盖进去,不够全面。
4.试列举十种以上去除加工方法的名称,并简述其用途答:车削、铣削、刨削、磨削、钻削、镗削、攻丝、滚齿、电解、光刻、激光加工等。
各自用途:(这个真的不好找,)第二章4.什么是积屑瘤?积屑瘤是如何形成的?在切削塑性材料时,往往在前刀面上紧靠切屑刃口处粘结着一小块很硬的金属楔块,这个楔块称为积屑瘤。
切削塑性材料时,由于前刀面与切屑底面之间的挤压与摩擦作用,使靠近前刀面的切屑底层流动速度减慢,产生一层很薄的滞留层,使切屑上层金属与滞留层之间产生相对滑移。
上下层之间的滑移阻力,称之为内摩擦力。
在一定切削条件下,由于切削时产生的温度和压力,使得刀具前刀面与切屑底部滞留层之间的摩擦力(称之为外摩擦力)大于内摩擦力,此时滞留层金属与切屑分离而粘结在前刀面上。
精密和超精密加工技术期末考试题及答案

1、八面体的单晶金刚石的晶体结构包括晶轴、晶面、面网密度和面网距。
晶面:通过原子中心的平面,即晶体中各种方位上的原子面。
晶轴:与晶面垂直的轴面网密度(致密度) :面网单位面积上的原子数面网距:晶体面网之间的距离用解理现象解释晶体的好磨难磨方向:解理现象是某些晶体特有的现象,晶体受到定向的机械力作用时,沿平行于某个平面平整的劈开的现象。
解理发生的原因主要是因为111)面的宽的面间距是金刚石晶体中所有晶面间距中的最大的一个,并且其中的连接共价键数最少,只需击破一个价键就可使其劈开。
金刚石的解理现象即沿解理面(111)平整的劈开两半,且金刚石的破碎和磨损都和解理现象直接有关。
金刚石的耐磨性可用相对磨削率来表示,对于金刚石研磨时,各晶面均有“好磨”和“难磨”方向。
高磨削率方向称为“好磨方向”,低磨削率方向称为“难磨方向”。
2、高速切削应用场合,由哪些特点决定的?应用场合:1)航空航天:由于有大量薄壁、细筋的大型轻合金整体构件加工,高速切削,随切削速度提高,切削力可减少30%以上,可以减少工件变形。
铝合金整体结构件的高速切削,不再铆接,省去了装配工作;薄壁件加工等。
2)模具业:高速切削可加工硬度HRC45~65的淬硬钢铁件,如高速切削加工淬硬后的模具可减少甚至取代放电加工和磨削加工,满足加工质量的要求,加快产品开发周期,大大降低制造成本。
3)汽车工业:采用高速数控机床和高速加工中心组成高速柔性生产线,实现多品种、中小批量的高效生产,高速切削使加工时间减少,切削效率提高3~5倍。
加工成本可降低20%-40%。
4)仪器仪表:精密光学零件加工。
转速的提高,使切削系统的工作频率远离机床的低阶固有频率,加工中鳞刺、积屑瘤、加工硬化、残余应力等也受到抑制。
因此,高速切削加工可大大降低加工表面粗糙度,加工表面质量可提高1~2等级。
有利于减少加工零件的内应力和热变形,也提高了加工精度。
这题有个简单的答案由于高速切削加工具有高生产效率,减少切削力,提高加工精度和表面质量,降低生产成本并且可加工高硬材料等许多优点,已在汽车和摩托车制造业、模具业、轴承业、航空航天业、机床业、工程机械、石墨电极等行业中广泛应用。
现代加工工艺理论及技术考题及答案_08级_
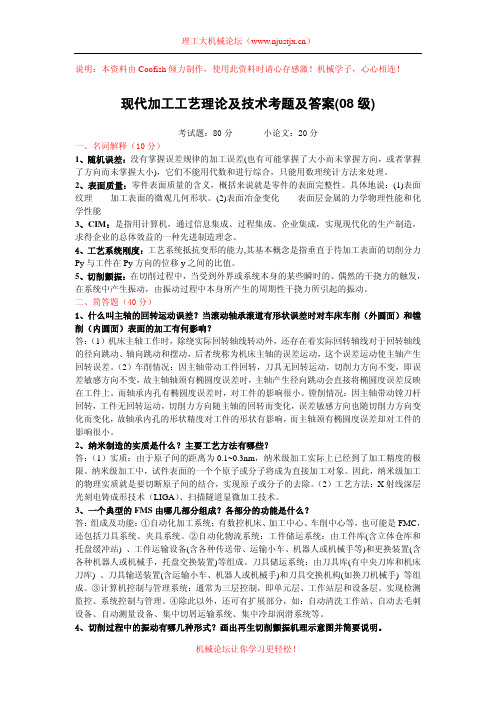
说明:本资料由Coofish倾力制作,使用此资料时请心存感激!机械学子,心心相连!现代加工工艺理论及技术考题及答案(08级)考试题:80分 小论文:20分一、名词解释(10分)1、随机误差:没有掌握误差规律的加工误差(也有可能掌握了大小而未掌握方向,或者掌握了方向而未掌握大小),它们不能用代数和进行综合,只能用数理统计方法来处理。
2、表面质量:零件表面质量的含义,概括来说就是零件的表面完整性。
具体地说:(1)表面纹理——加工表面的微观几何形状。
(2)表面冶金变化——表面层金属的力学物理性能和化学性能3、CIM:是指用计算机,通过信息集成、过程集成、企业集成,实现现代化的生产制造,求得企业的总体效益的一种先进制造理念。
4、工艺系统刚度:工艺系统抵抗变形的能力,其基本概念是指垂直于待加工表面的切削分力Py与工件在Py方向的位移y之间的比值。
5、切削颤振:在切削过程中,当受到外界或系统本身的某些瞬时的、偶然的干挠力的触发,在系统中产生振动,由振动过程中本身所产生的周期性干挠力所引起的振动。
二、简答题(40分)1、什么叫主轴的回转运动误差?当滚动轴承滚道有形状误差时对车床车削(外圆面)和镗削(内圆面)表面的加工有何影响?答:(1)机床主轴工作时,除绕实际回转轴线转动外,还存在着实际回转轴线对于回转轴线的径向跳动、轴向跳动和摆动,后者统称为机床主轴的误差运动,这个误差运动使主轴产生回转误差。
(2)车削情况:因主轴带动工件回转,刀具无回转运动,切削力方向不变,即误差敏感方向不变,故主轴轴颈有椭圆度误差时,主轴产生径向跳动会直接将椭圆度误差反映在工件上。
而轴承内孔有椭圆度误差时,对工件的影响很小。
镗削情况:因主轴带动镗刀杆回转,工件无回转运动,切削力方向随主轴的回转而变化,误差敏感方向也随切削力方向变化而变化,故轴承内孔的形状精度对工件的形状有影响,而主轴颈有椭圆度误差却对工件的影响很小。
2、纳米制造的实质是什么?主要工艺方法有哪些?答:(1)实质:由于原子间的距离为0.1~0.3nm,纳米级加工实际上已经到了加工精度的极限。
现代数控技术及数控机床期末复习资料试卷答案浙工大
现代数控技术及数控机床试卷2标准答案学生姓名:,班级:,学号:,成绩:一.填空题(每题2分)1.数控机床是由控制介质、数控装置、伺服驱动装置、辅助控制装置、反馈装置、适应控制装置和机床等部分组成。
2.数控机床加工过程的加工路线是指刀具中心的运动轨迹和方向。
3.三相步进电机的转子上有40个齿,若采用三相六拍通电方式,则步进电机的步距角为 1.50。
4.数控机床的最小设定单位是数控机床能实现的最小位移量,标制着数控机床精度的分辨率,其值一般为0.0001~0.01mm,在编程时,所有的编程单位都应转换成与最小设定单位相应的数据。
5.通常把数控车床的床身导轨倾斜布置,可改善其排屑条件和受力状态。
提高机床的静刚度。
6.数控机床的工作台和刀架等部件的移动,是由交流或直流伺服电机驱动,经过滚珠丝杠传动,可减少进给系统所需要的驱动扭矩,提高定位精度、运动平稳性。
7.对步进电机施加一个电脉冲信号时,步进电机就回转一个固定的角度,叫做步距角,电机的总回转角和输入脉冲数成正比,而电机的转速则正比于输入脉冲的频率。
8.位置检测装置是数控机床的重要组成部分,在闭环系统中,它的主要作用是检测位移量,并发出反馈信号与数控装置发出的指令信号进行比较,如有偏差,经放大后控制执行部件,使其向着消除偏差方向运动,直至偏差等于零为止。
9.刀具半径补偿功能的作用就是要求数控系统根据工件轮廓程序和刀具中心偏移量,自动计算出刀具中心轨迹。
10.伺服系统的输入是插补器发出的指令脉冲,输出是直线或转角位移。
11.数控机床工作台和刀架等部件的移动,由交流或直流伺服电机驱动,经过滚珠丝杠传动,减少了进给系统所需要的驱动扭矩,提高了定位精度和运动平稳性。
12.光栅依不同制造方法有透射光栅和反射光栅两种。
数控机床中常用透射光栅做位置传感器。
二.选择题(每题2分)1.闭环伺服系统使用的执行元件是(1,2)(1)支流伺服电机(2)交流伺服电机(3)步进电机(4)电液脉冲马达2.步进电机的角位移与(4)成正比。
2024年机械制造技术期末考试复习题库(含答案)
2024年机械制造技术期末考试复习题库(含答案)一、单选题1.加工齿轮,成形法比展成法生产效率()。
A、低B、高C、接近D、相同参考答案:A2.刀具刀刃部分的失效形式的错误选项是()A、刀刃崩缺B、磨损C、塑性变形D、刀具折断参考答案:C3.进给运动通常是指()A、切削运动中消耗功率最多的运动B、切削运动中速度最高的运动C、不断地把切削层投入切削的运动D、使工件或刀具进入正确加工位置的运动参考答案:C4.在卧式铣床上铣台阶面时,一般用()铣刀A、端铣刀B、立铣刀C、三面刃铣刀D、两面刃铣刀参考答案:C5.普通机床床身的毛坯多采用()。
A、铸件B、锻件C、焊接件D、冲压件参考答案:A6.粒度是磨料颗粒尺寸的()A、刚性B、大小C、多少D、韧性参考答案:B7.根据《GBT3375-1994焊接术语》,将待焊处的母材金属熔化以形成焊缝的焊接方法,称为()。
A、熔焊B、压焊D、锻焊参考答案:A8.在进行车削加工时,有多种因素影响切削力的大小,其中,对切削抗力影响最大的是()A、工件材料B、切削深度C、刀具角度D、刀具材料参考答案:B9.一般轴类工件,在车铣磨等工序中,始终用中心孔作精基准,符合()的原则A、基准重合B、基准统一C、基准转换D、以上都不是参考答案:B10.()高速切削塑性金属材料时,若没有采取适当的断屑措施,则形成()切屑。
A、挤裂B、崩碎C、带状参考答案:C11.刀具的寿命刀具的耐用度。
A、小于B、等于C、大于D、无关参考答案:C12.车削时切削热传出途径中所占比例最大的是()A、车刀B、工件C、切屑D、空气介质参考答案:C13.大批量生产的减速器输出轴毛坯应该选用()。
A、砂型铸造的铸件B、金属模砂型铸造的铸件C、自由锻造的锻件D、模锻的锻件参考答案:D14.磨削硬金属材料时,应选用的砂轮是。
A、硬度较低B、硬度较高C、中等硬度D、细粒度参考答案:A15.重要的轴类零件的毛坯通常应选择()A、铸件B、锻件C、棒料D、管材参考答案:B16.切削液的作用()、()、()等参考答案:冷却;润滑;排屑;17.四爪单动卡盘的每个卡爪都可以单独在卡盘范围内作()移动A、圆周B、轴向C、径向D、法向参考答案:C18.在碳素钢中加入适量的合金元素形成了()A、硬质合金B、高速钢C、合金工具钢D、碳素工具钢参考答案:C19.铣床主轴锥孔的空心轴是用来()A、安装铣刀B、安装工件C、安装轴套D、用来节省材料参考答案:A20.影响表面质量的最大因素是()A、切削速度B、进给量C、背吃刀量参考答案:B21.通过刀尖的运动轨迹来获得形状精度的方法称为()A、轨迹法B、仿形法C、成形法D、展成法参考答案:A22.精车时,为了提高表面质量,应选用的进给量,的切削速度。
现代制造技术期末题型总结
现代制造技术期末题型总结一、单项选择题单项选择题是期末考试中常见的一种题型,也是考察学生对现代制造技术基础知识掌握程度的一种方式。
该题型的特点是,每个题目给出若干个选项,只有一个正确答案。
例如:1. 现代制造技术的“数控机床技术设计及应用”专业实验室应配置的设备包括(A)、(B)、(C)。
(D)A. 数控机床B. 电脑C. 电焊机D. 示教器正确答案:A2. 真空注射模压是指将加热状的塑料(A)到配料仓后,(B)也配料速度通过上料上料锥来挤压出去,挤压后的材料在(C)流经螺杆,经(D)上预塑化后进入模腔,经过一定的制可得到所需的无线电器皿。
A. 沥青B. 塑料C. 金属D. 输液正确答案:B二、填空题填空题是一种要求考生根据题目给出的语境和条件,在空位置上填写适当的答案的题型。
该题型通常考察学生对现代制造技术的专业术语和概念的理解,以及对理论知识的掌握程度。
例如:1. 根据图示,请问以下哪种指示信号不适合用于数控机床?____________________正确答案:模拟信号2. 原子力显微镜(AFM)的测量原理是利用探针与样品的______作用力的改变来测量样品表面形貌。
正确答案:静电力三、简答题简答题是一种要求考生对某些概念、原理或现象进行简要阐述的题型。
该题型通常考察学生对现代制造技术的理论知识的掌握程度,以及对一些实际问题的分析和解决能力。
例如:1. 简要解释传统制造技术和现代制造技术的区别和联系。
传统制造技术是指在工艺过程中主要依靠人工操作,生产效率较低,产品质量难以保证的制造技术。
而现代制造技术是指利用先进的生产设备和自动化控制系统,提高生产效率和产品质量的制造技术。
它们的区别主要体现在以下几个方面:(1)物质形态:传统制造技术主要依靠人力,而现代制造技术主要依靠机器和设备(2)生产效率:现代制造技术生产效率较高,能够大大降低生产成本和提高生产效益(3)产品质量:传统制造技术产品质量难以保证,而现代制造技术能够通过自动化控制系统实现精密加工,提高产品质量(4)环保和可持续发展:现代制造技术更加注重环保和可持续发展,减少了对自然资源的消耗和污染等。
现代制造技术复习题
1、特种加工产生的原因是什么?特种加工产生的定义。
2、特种加工的特点是什么?3、特种加工分为哪七大类?分别是消耗哪些能量?(课本)4、电火花加工的加工原理是什么?(课本)电火花加工的电蚀过程分为哪三个阶段?5.电火花就具备哪三个条件?6、共轭回转加工原理是什么?11、电火花加工表面变质层包括哪三个部分?12、什么是极性效应?如何使用极性效应?什么是覆盖效应?如何使用覆盖效应?13、铜、石墨、钼材料作为电极时分别在什么时候使用?14、如何清除孔加工中折断中钻头、丝锥?15、线切割加工的原理是什么?线切割加工机床由哪几部分组成?18、孔的加工:盲孔、台阶孔、上下异形孔分别可以采用哪种特种加工方法?22、电化学加工中的电解加工方法,工件接阳极还是阴极?为什么?24、从加工原理上看,电子束加工与离子束加工有何异同?25、从加工原理上看,离子束加工可以分为哪四类?电子束与离子束加工的工件材料必须导电吗?26、激光的产生有哪三个过程?27、激光打孔加工中,孔的加工精度与哪五个因素有关?会不会出现偏心孔的现象?试解释其原因。
30、什么是空化效应?试举出应用实例?31、高速加工的机理是什么?32、高速加工刀具不平衡消除有哪些方法?36、快速制造技术的定义:基于离散-堆积成形原理,由零件数字模型(CAD模型)直接驱动,可完成仼意复杂形状三维实体零件的技术总称38、选择性液体固化法(SLA)所用的材料是什么?该方法成形的产品有什么特点?有什么缺点?39、选择性层片粘接(LOM)所用的材料是什么?该方法成形的产品有什么特点?有什么缺点?40、选择性激光烧结(SLS)所用的材料是什么?该方法成形的产品有什么特点?有什么缺点?41、熔融沉积成形(FDM)所用的材料是什么?该方法成形的产品有什么特点?有什么缺点?42、试描述新产品快速开发制造系统的组成和过程。
43、真空注塑成形的原理。
48、试描述逆向工程的工作流程。
53、与接触式相比,非接触式测量有什么优点?3、简答与与分析两题,来自下面内容。
- 1、下载文档前请自行甄别文档内容的完整性,平台不提供额外的编辑、内容补充、找答案等附加服务。
- 2、"仅部分预览"的文档,不可在线预览部分如存在完整性等问题,可反馈申请退款(可完整预览的文档不适用该条件!)。
- 3、如文档侵犯您的权益,请联系客服反馈,我们会尽快为您处理(人工客服工作时间:9:00-18:30)。
《现代加工技术》复习题1.现代加工技术则是指满足“(高速)、(高效)、(精密)、微细、自动化、(绿色化)”特征中一种以上特征的加工技术。
2.20世纪末出现了一种新的加工技术分类方法,将加工技术分为四大类,即:(去除(或减材)加工)、(增材加工)、变形加工和表面加工。
3.切削用量三要素包括(切削速度)、(进给量)和(切削深度)。
4.单个磨粒的磨削过程大致分为(滑擦)、(刻划)和(切削)三个阶段.。
5.磨料在基带上的涂敷方法一般有重力作用法和(静电植砂法)。
6.研磨工艺参数有(研磨压力)、(研磨速度)、研磨时间、(研磨运动轨迹)。
7.珩磨加工时,珩磨头有三个运动,即(旋转运动)、(往复运动)和垂直于加工表面的径向加压运动。
8.电火花加工按工具电极和工件相对运动的方式和用途的不同,可分为(电火花穿孔成形加工)、(电火花线切割)、电火花磨削和镗磨、电火花同步共轭回转加工等。
9.(电火花高速小孔加工)工艺是近年来新发展起来的。
这种加工方法最适合加工~3mm左右的小孔且深径比可超过100。
10.激光切割的工艺参数为(切割速度)、(焦点位置)、(辅助气体)和(激光功率)。
11.绿色加工具有以下基本特征(技术先进性)、(绿色性)、(经济性)。
12.加工参数优化的方法有(解析优化方法)和(试验优化方法)两种。
13.塑性材料的切屑形成过程,就其本质来说,是被切削材料在刀具切削刃和前刀面作用下,经受挤压产生(剪切滑移)的过程。
14.默钱特剪切角理论公式中的剪切角是根据(最小切削功原理)确定的。
15.高速切削加工的刀具材料主要有(超硬刀具材料)、陶瓷刀具、TiC(N)基硬质合金和涂层刀具。
16.对(淬硬钢)材料进行高速车削加工叫高速硬车削,可以采用硬车削替代磨削加工的场合很多,如汽车曲轴加工、轴承加工、淬硬螺纹加工等。
17.在线电解修整ELID是专门应用于(金属结合剂)砂轮的修整方法,与普通的电解修整方法相比,具有修整效率高、工艺过程简单、修整质量好等特点。
18.以砂轮高速、(高进给速度)和大切深为主要特征的高效深磨HEDG技术是高速磨削在高效加工方面的最新应用。
19.精密磨削通过对砂轮的精细修整,使磨粒具有(微刃性)和等高性,可获得加工精度为1~0.1μm和表面粗糙度R a为~0.025μm的表面磨削方法。
20.缓进给磨削时,须采取特殊的工艺方式,如(连续修整)、(强化换热)、w(大气孔砂轮)等。
21.研磨的实质是用(游离的磨粒)通过研具对工件表面进行包括物理和化学综合作用的微量切削。
22.抛光加工方法有:(机械抛光)、(化学抛光)、(机械化学复合抛光)、(液体抛光)、(电解抛光)。
23.电规准是电火花加工过程中的一组电参数,如(电压)、(电流)、脉宽、脉间等,一般分为粗、中、精三种,每一种又可分几档,三种规准依次使用。
是在电火花加工基础上于50年代末最早在前苏联发展起来的一种新的工艺形式,是用(线状电极)靠火花放电对工件进行切割,故称为电火花线切割,有时简称线切割。
25.通常对加工过程进行优化的目标有:(最大生产率)、(最低加工成本)、(最大利润率)。
26.在动态优化过程中,为了建立瞬态优化模型,必须对加工过程的动态特征参数进行(实时检测)。
27.加工过程的动态优化一般需要通过机床、传感器、专用过程控制电路及电脑所组成的系统来实现,这样的系统称为加工过程(自适应控制系统)。
二、判断题1.剪切角φ与切屑变形系数ξ的关系:剪切角φ增大,切屑变形系数ξ增大。
(×)2.自然热电偶法测得的是切削区指定点的温度,人工热电偶法能够直接测得前刀面温度。
(×)3.在高速切削中,常规的7:24锥度刀柄系统已经不适用。
(√)4.工件表面的磨削温度是指磨粒磨削点的温度,它影响工件表面的烧伤、裂纹和加工硬化。
(×)5.硬磨料砂轮修整一般将整形和修锐分开(√)6.抛光和研磨所用的磨料及研具材料相同。
(×)7.电化学加工是利用阳极金属原子由于失去电子而成为正离子进入溶液的原理而进行的特种加工。
(×)8.干切削刀具多以月牙洼磨损为主要失效形式。
(√)9.由于CBN中的氮和硼可以溶入铁素体中(氮与硼易与铁素体反应),形成间隙固溶体,切削时产生的高温高压会使CBN颗粒产生扩散磨损,故不宜用于低硬度(HRC45以下)工件的加工。
(√)10.点磨削是利用超高线速度(120~250m/s)的多层CBN砂轮(宽度仅几毫米)来实现的。
(×)11.切削铸铁常常产生积屑瘤和鳞刺。
(× )12.刃倾角︒>0Sλ时,切屑流向已加工表面。
(× )13.低速切削时,刀具磨损的主要原因是扩散磨损。
(× )14.精密切削时背吃刀量对切削力的影响大于进给量对切削力的影响。
(× )15.双刃浮动镗刀不能消除由径向切削力对镗杆的作用而造成的加工误差。
(√ )16.高温切削的实质是加热后刀具材料和工件材料的硬度比增大了。
(√ )17.相同条件下同一砂轮磨削直径相同的内圆和外圆,前者比后者容易烧伤。
(√ )18.研磨过程可以用“纯切削说”来完全解释。
(× )19.为了环保,绿色切削不允许采用切削液。
(× )20.立方氮化硼砂轮磨削时一般采用油性液为磨削液,而不用水溶性液。
(√)三、名词解释1.积屑瘤答:在切削塑性材料时,往往在前刀面上紧靠刃口处粘结着一小块很硬的金属楔块,这个楔块称为积屑瘤。
2.超精密切削加工答:超精密切削加工是相对于精密切削加工而言的,其所能达到的加工精度和表面质量更高。
目前,将加工精度为μm以下,加工表面粗糙度R a小于μm的切削加工称为超精密切削加工。
3.磨削比答:单位时间内磨除工件材料的体积与砂轮磨耗体积之比称为磨削比。
4.电解加工答:电解加工时,工件接直流电源(10~20V)的正极(阳极),工具接电源的负极(阴极),工具向工件缓慢进给,使两极之间保持较小的间隙约~,具有一定压力(~2MPa)的氯化钠电解液从间隙中流过,这时阳极工件的金属逐渐电解腐蚀,电解产物被高速(5~50m/s)的电解液带走。
5.加工参数优化答:加工参数优化就是寻求一组最优的加工参数使得加工过程中某一指标达到最佳状态。
通常,首先选择一个优化目标,如最大利润率、最低成本或最大生产率。
6.刀具耐用度答:一把新刀具从开始切削直到磨损量达到磨钝标准为止总的切削时间,或者说刀具两次刃磨之间总的切削时间,被称为刀具耐用度,一般以T表示。
7.高速切削加工答:通常把切削速度比常规高出5~10倍以上的切削加工叫做高速切削或超高速切削。
8.砂轮硬度答:砂轮硬度是指砂轮上的磨粒受力后自砂轮表面脱落的难易程度,也反映磨料与结合剂的粘结强度。
砂轮的硬度是由结合剂的粘结强度和砂轮的制造工艺决定的,与磨粒本身的硬度无关。
9.电火花加工答:电火花加工又称放电加工,是通过导电工件和工具电极之间脉冲性火花放电时的电腐蚀现象来蚀除多余材料,以达到对工件尺寸、形状及表面质量要求的加工技术。
10.绿色加工答:绿色加工是指在不牺牲产品的质量、成本、可靠性、功能和能量利用率的前提下,充分利用资源,尽量减轻加工过程对环境产生有害影响的加工过程,其内涵是指在加工过程中实现优质、低耗、高效及清洁化。
四、简答题1.现代加工技术的发展呈现哪些趋势?答:1.追求更高的加工精度2.以高速实现高品质高效加工3.微细与纳米加工快速发展4.追求加工智能化5.更加注重加工的绿色化主要特征表现为:节能、低耗、无废排放。
2.简述激光加工、电子束加工和离子束加工的原理。
答:激光加工是把具有足够能量的激光束聚焦后照射到所加工材料的适当部位,在极短的时间内,光能转变为热能,被照部位迅速升温,材料发生气化、熔化、金相组织变化以及产生相当大的热应力,从而实现工件材料被去除、连接、改性或分离等加工。
电子束加工是利用高能电子束流轰击材料,使其产生热效应或辐照化学和物理效应,以达到预定的工艺目的。
离子束加工是在真空条件下,将离子源产生的离子束经过加速聚焦,使之具有高的动能能量,轰击工件表面,利用离子的微观机械撞击实现对材料的加工。
3.磨削加工与切削加工方法相比,具有哪些特点?答:磨削加工从本质上来说属于随机形状、随机分布的多刃切削加工,但是与车、铣等具有规则形状刀具切削加工方法相比较,具有如下特点:(1)砂轮表面磨粒的分布及其刃口形状均处于随机状态。
(2)磨削速度很高,一般在30~50m/s,是车、铣速度的10~20倍。
因此,磨削层金属变形速度很快,磨削区在短时间内发热量大,瞬时可高达1000℃以上,将引起加工表面物理力学性能改变,甚至产生烧伤和裂纹。
(3)磨粒的切削刃和前(后)刀面的形状极不规则,顶角在100 以上,前角为很大负值,后角小,刃口半径r n却较大,会使工件表层材料经受强烈挤压变形。
特别是磨粒磨钝后和进给量很小时,金属变形更为严重,因而磨除单位工件体积时消耗的能量比一般切削加工高得多,约是其它加工方法的10~30倍。
(4)普通磨粒在磨削力作用下,会产生开裂和脱落,会形成新的锐利刃,这称为磨粒的自砺作用,对磨削加工是有利的。
(5)磨削时单个磨粒的切削厚度可小到几微米,故易于获得较高加工精度和较小表面粗糙度值。
(6)由于多数磨粒切削刃具有极大的负前角和较大的刃口半径,使径向磨削力F y远大于切向磨削力F z,加剧工艺系统变形,造成实际磨削深度常小于名义磨削深度。
4.试简要介绍水射流加工工艺的优点。
答:与其它高能束流加工技术相比,水射流切割技术具有独特的优越性:(1)切割品质优异。
水射流是一种冷加工方式,“水刀”不磨损且半径很小,能加工具有锐边轮廓的小圆弧。
加工无热量产生且加工力小,加工表面不会出现热影响区,自然切口处材料的组织结构不发生变化,几乎不存在机械应力与应变,切割缝隙及切割斜边都很小,无需二次加工,无裂缝、无毛边、无浮渣,切割品质优良。
(2)几乎没有材料和厚度的限制。
无论是金属类如普通钢板、不锈钢、铜、钛、铝合金等,或是非金属类如石材、陶瓷、玻璃、橡胶、纸张及复合材料,皆可适用。
(3)节约成本。
该技术不需二次加工,既可钻孔亦可切割,降低了切割时间及制造成本。
(4)清洁环保无污染。
在切割过程中不产生弧光、灰尘及有毒气体,操作环境整洁,符合环保要求。
5.你如何理解难加工材料和难加工结构,并举例说明。
答:难加工材料是指难以进行切削加工的材料,即切削加工性差的材料。
难加工材料有:钛合金、高温合金、不锈钢、高强度钢与超高强度钢、复合材料、硬脆性材料。
难加工结构是指在常规机床上加工时精度难以保证或必须采用多轴联动才能加工出的结构,如薄壁、深(长)径比大的结构、复杂型面、微小微细结构及其它用常规方法难以加工的孔、槽等结构。