实验烧结温度和烧结温度范围的测定——烧结炉法
实验 烧结温度和烧结温度范围的测定——烧结炉法

实验烧结温度和烧结温度范围的测定——烧结炉法一、实验目的(1)掌握烧结温度与烧结温度范围的测定原理和测定方法;(2)了解影响烧结温度与烧结温度范围的复杂因素;(3)明确烧结温度与烧结温度范围对陶瓷生产的实际意义。
二、实验原理烧成是陶瓷制品在生产中的重要环节。
为了制定最适宜的烧成条件,必须确切地了解各种陶瓷制品的烧结温度、烧结温度范围以及热过程中的重量变化、尺寸体积变化、吸水率、气孔率及处貌特征的变化,以便确定最适宜的烧成制度,选择适用的窑炉以及合理利用具有温度差的各个窑位。
对粘土类原料而言,在加热过程中坯体气孔率随温度升高而逐渐降低,当粘土坯体的密度达到最大值,吸水率不超过5%,此状态称为粘土的烧结,粘土达到此状态的温度为完全烧结温度,简称烧结温度。
自烧结温度继续升高温度,粘土坯体逐渐开始软化变形,此状态可依据过烧膨胀或坯体表面出现大的气孔或依目力观察有稠密的小气孔出现来确定,达到此状态时的温度称为软化温度(或称过烧膨胀温度),完全烧结温度和软化温度之间的温度范围称为烧结温度范围(简称烧结范围)。
中国科学院上海硅酸盐研究所在制瓷原料的研究中是:以被焙烧的粘土类原料的烧成线收缩曲线开始突然下降,即开始进行急剧收缩时的温度作为玻化温度范围的下限,当收缩进行到转向过烧膨胀的温度称为玻化温度范围的上限。
上限温度与下限温度的区间为玻化范围.该所对陶瓷坯料的研究是以坯料的烧成线收缩和显气孔率来确定的,当显气孔率开始减低到接近于零,即瓷胎密度达到最大,不再吸收水份,这个温度就是瓷胎烧成温度范围的下限,从收缩曲线开始“膨大”时的温度,为烧成温度范围的上限。
实际烧成温度不宜偏于烧成温度范围的上限,以避免有越过烧成范围而发生过烧的危险。
图1 坯体在加热过程中收缩与显气孔率的关系测定烧结温度与烧结范围是将试样于各种不同温度下进行焙烧,并对各种不同温度下焙烧的试样测定其外貌恃征、吸水、显气孔率体积密度,烧成线收缩等情况来确定。
烧结炉炉温校检作业指导书

编制
审核
批准
1.3每次校准前按热电偶编号套上相应号码管
热电偶按每使用10次内校一次。
号码管与热电偶编号要一一对应, 避免出现测试数据偏差。
2.1拆卸烧结炉法兰,将9支热电偶从法兰口穿入炉内,再将热电偶配套法兰紧固在 注意热电偶与法兰紧固处的密封性
烧结炉上。
是否完好。
2.2将9支热电偶按序号顺序固定在支架规定的位置,确保热电偶在支架的位置每次 注意支架位置(目视支架前后各空
反。 记录数据的时间点控制在保温时间
1h;第二点480℃ 保温1h;第一测试点测1050℃,测试、记录、调整之后再将炉温 段的第30-50分钟之间,如遇实测温
降至480℃,保温1H后测480℃时的数据。),开始升温,在各温度测试时间点手工记 度与设定温度偏差过大(超过±5
录“WJ-3热电偶自动检测系统”显示的电动势数据,将数据输入电脑自动转化程序 ℃)时,应立即通知材料分厂及设
中,将电动势数值转化为温度。
备课相关人员。 拆除热电偶时需检查热电偶处于炉
2.5校准结束待炉温降至80℃以下,打开炉门,将热电偶从支架上折下,拆除热电 偶法兰,将热电偶从炉内抽出,装好原有烧结炉法兰。
门位置处的表面有无压伤,热电偶 探头用200目以上细砂纸轻微打磨, 避免探头处因高温炭化影响测试准
确性。
相同,如图一;随后将支架推入炉膛内,确保支架位置处于炉膛中央,再关闭炉 余一根钼带)及热电偶不要被炉门
门,如图二。
夹伤
2.3将热电偶补偿导线一端插入冰点恒温器中,另一端按序号连接到“WJ-3热电偶 注意要将热电偶序号与“WJ-3热电
自动检测系统”后部的接线端子上,并开启电源,后将“WJ-3热电偶自动检测系统 偶自动检测系统”的接线端子号对
烧结操作规程

烧结操作规程烧结操作规程一、烧结工艺概述烧结是一种将粉末颗粒在一定条件下通过加热使之相互融结并形成致密块体的工艺。
烧结操作规程是制定和规范烧结工艺的操作指南,通过严格执行操作规程,可以保证产品的质量稳定性和生产效率。
二、操作准备1. 烧结设备检查:检查烧结设备的各项参数和设备运行状态,确保设备正常工作。
2. 确定烧结工艺参数:根据产品要求和烧结设备的特性,确定烧结温度、时间、气氛和加热速率等工艺参数。
三、烧结操作步骤1. 入炉准备:将待烧结的物料按照工艺要求整理,清除表面杂质和水分。
然后将物料放入烧结炉,注意排列均匀,避免堆积过高或堆积不均匀。
2. 炉温升温:根据烧结工艺参数,将炉温逐渐升高至目标温度。
升温速率应控制在合理范围内,避免过快或过慢。
3. 保温烧结:当炉温升至目标温度后,保持一段时间进行保温烧结。
保持时间应根据具体产品的要求确定,一般在30分钟至2小时之间。
4. 炉温冷却:保温烧结完成后,将炉温逐渐降低至室温,冷却速率应适中,避免过快或过慢引起断裂或变形。
5. 取出产品:炉温冷却至室温后,打开烧结炉门,小心取出产品。
产品应进行质量检查,记录烧结参数和产品质量情况。
四、操作注意事项1. 操作人员应熟悉烧结工艺和设备操作规程,并佩戴相关的个人防护用品。
2. 物料应按照规定的品种、数量和质量进行装载和放置。
3. 炉温升降速率应根据具体物料和工艺要求合理确定,避免产生过快或过慢的冷却速度。
4. 在烧结过程中应定期监测和记录烧结设备和产品的温度、压力、气氛和形态等参数。
5. 若出现设备故障或异常情况,应及时停机检修或采取相应的应急措施,保证人员和设备安全。
6. 完成烧结后,应及时清理烧结炉和相关设备,做好设备维护和保养工作。
五、操作规程的执行和改进1. 烧结操作规程应由指定的技术人员编写,并明确操作人员的职责和权限。
2. 操作规程的执行应由质量管理部门进行监督和检查,确保操作的合规性和可靠性。
热压烧结的操作步骤及应用
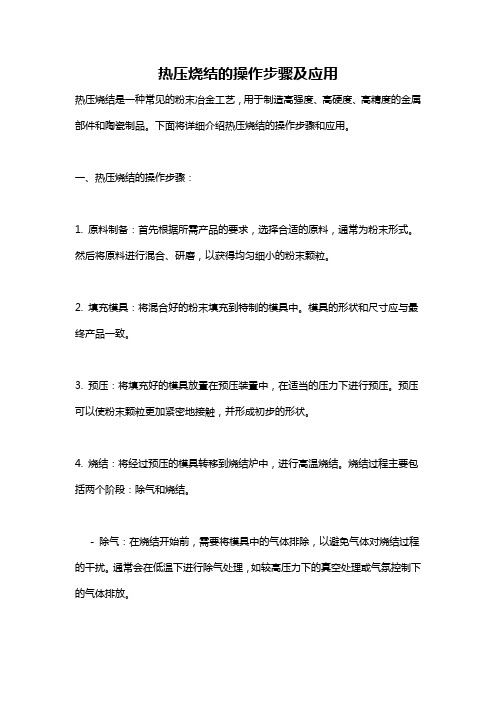
热压烧结的操作步骤及应用热压烧结是一种常见的粉末冶金工艺,用于制造高强度、高硬度、高精度的金属部件和陶瓷制品。
下面将详细介绍热压烧结的操作步骤和应用。
一、热压烧结的操作步骤:1. 原料制备:首先根据所需产品的要求,选择合适的原料,通常为粉末形式。
然后将原料进行混合、研磨,以获得均匀细小的粉末颗粒。
2. 填充模具:将混合好的粉末填充到特制的模具中。
模具的形状和尺寸应与最终产品一致。
3. 预压:将填充好的模具放置在预压装置中,在适当的压力下进行预压。
预压可以使粉末颗粒更加紧密地接触,并形成初步的形状。
4. 烧结:将经过预压的模具转移到烧结炉中,进行高温烧结。
烧结过程主要包括两个阶段:除气和烧结。
- 除气:在烧结开始前,需要将模具中的气体排除,以避免气体对烧结过程的干扰。
通常会在低温下进行除气处理,如较高压力下的真空处理或气氛控制下的气体排放。
- 烧结:将除气后的模具加热到适当的温度,使粉末颗粒发生相互结合和扩散,形成致密的固体。
烧结温度、时间和气氛的选择取决于所用材料和所需产品的特性。
5. 冷却:在烧结结束后,将模具从炉中取出,进行自然冷却或采用其他冷却方式。
冷却过程中,要注意避免产品出现热应力导致的开裂。
6. 除模:将烧结后的成品从模具中取出。
通常需要经过机械加工或其他后续处理步骤,以满足最终产品的要求。
二、热压烧结的应用:1. 金属制品:热压烧结可以用于制造各种金属制品,如钢制品、铝合金制品等。
由于热压烧结可以使金属颗粒充分结合,因此制造的金属制品具有高强度、高硬度和良好的耐磨性。
常见的应用包括汽车零部件、工具和模具、航空航天部件等。
2. 陶瓷制品:热压烧结是制造陶瓷制品的常用工艺之一。
热压烧结可以使陶瓷颗粒结合更紧密,从而获得高强度、高硬度和高密度的陶瓷制品。
常见的应用包括陶瓷刀具、陶瓷瓷砖、陶瓷合成材料等。
3. 硬质合金:热压烧结是制造硬质合金的主要工艺之一。
硬质合金通常由金属粉末和碳化物等非金属粉末混合而成。
【最新2018】烧结专题实验报告-范文模板 (7页)

本文部分内容来自网络整理,本司不为其真实性负责,如有异议或侵权请及时联系,本司将立即删除!== 本文为word格式,下载后可方便编辑和修改! ==烧结专题实验报告篇一:冷压烧结实验报告研究生课程实验报告《粉末冶金综合实验》课程名称超硬材料技术与应用姓名学号专业机械制造及其自动化任课教师教授开课时间 201X年3月课程实验提交时间:201X年 5月 20日一、实验目的通过本实验,对粉末冶金相关知识进行进一步学习,掌握粉末冶金的基本工艺,熟悉粉末成形和烧结过程研究方法及测试原理,培养粉末冶金相关研究的基本思路和初步能力,将课堂知识与实际试验联合起来。
二、实验仪器设备与材料(1)赛多利斯高精度天平(2)三维涡流混料机(3)YDH50T四柱液压机(4)真空热压烧结机(5)钴基粉末、铜基粉末图1 赛多利斯高精度天平图2 YDH50T四柱液压机图3 真空热压烧结机三、实验原理粉末冶金是由粉末成形和毛坯烧结这两道基本工序组成。
1、粉末成型粉末的冷压成型是将松散的粉末体加工成具有一定尺寸、形状,以及一定密度和强度的压坯。
冷压成型一般有普通模压法和特殊成型法。
前者是将金属粉末或其他混合粉末装在特定的压模内,通过压力机将其压制成型;而后者是指非模压成型,如静压成型,连续成型,无压成型等。
冷压前通常需经原材料的准备,如退火、各种元素粉末的混合、制粒及添加润滑剂等。
金属粉末的冷压成型过程:当对压模内的粉末施加一定压力后,粉末颗粒间将发生相对移动,粉末颗粒将充填空隙,使粉末体的体积减小,同时,粉末颗粒受压后,要经受不同程度的弹性变形和塑性变形,颗粒间产生一定的粘结,使压坯具有一定的强度;并且,由于压制过程中在压坯内聚集了较大内应力,当解除压力后,压坯会膨胀,也就是弹性后效,由于粉末体内应力的作用,需施加一定的压力把压坯从压模中取出,从而完成粉末冷压成型过程。
2、毛坯烧结粉末经过冷压成型后,粉末压坯虽然有了一定的机械强度,但是这种强度是粉末和粉末间的机械啮合,强度不高,不能满足实际使用要求,因此粉末经冷压成型后还需进行烧结。
烧结生产中的温度控制

烧结生产中的温度控制[摘要]:烧结是炼铁生产的重要环节,烧结生产的好坏对整个钢铁企业至关重要,本文主要介绍了烧结生产中温度控制的主要操作工艺。
[关键词]:烧结温度控制处理中图分类号:tq172.6+21.9 文献标识码:tq 文章编号:1009-914x(2012)32- 0100 -01烧结温度的调节简单的说就升降每个温区区的温度,但是关键的就是调节温区的选择,升降的选择以及升降幅度的选择,下面就根据经验发表一下对烧结温度调整的看法,希望能起到抛砖引玉的作用。
一.调节烧结温度时机的选择需要我们调节烧结温度的时候也就是电池的电性能和外观出现异常的时候,所以我首先要做的就是对测试结果的观测和分析。
其实我们主要观察的就是 ff的变化,ff的好坏在一定程度上反映了欧姆接触的好坏,如果此时填充因子不理想,看看串联电阻,并联电阻以及反向电流的情况,如果这些值不理想,那么有可能烧结温度调节不到位,此时我们可以考虑调节烧结温度来改善电池的电性能。
二.烧结温度温区的选择烧结炉分为9个区,前三个区是烘干区,主要完成浆料中有机成分的挥发,后六个区主要完成背场和正面的烧结,背场主要是铝浆到铝金属的转变和硅铝合金的形成,也可以说有硅铝欧姆接触的形成,正面是银浆到银金属的转变和银硅合金的形成,我们烧结的关键是银硅的欧姆接触,因为银的功函数较高,和铝相比,较难以和硅形成欧姆接触,所以当我们选择温区的时候,如果出现弓片,铝珠和鼓包问题,首先可以选择降低8区和9区的温度,同时结合4,5和6区的温度,如果仅仅是电性能的异常,就主要选择调节8区和9区的温度,7区的温度配合着调节。
三.烧结温度升降的选择烧结温度调节最关键的,最难把握的就是升降的选择,该升温的时候就不能降温,何时升温何时降温需要一定的经验和技巧,两者要结合,这样才能更好的把握温度的调节,怎样判断升温还是降温主要还是根据测试的结果。
烧结是有欠烧和过烧的说法的,每一批片子都有一个最佳烧结点,当温度超过或者低于最佳烧结点的温度的时候,片子都是没有达到我们的理想烧结要求的,欠烧时欧姆接触没有完全形成,串联电阻会偏大,填充因子偏低,过烧时银硅合金消耗太多银金属,银硅合金层相当于隔离层,阻止了载流子的输出,也会增加接触电阻,降低填充因子。
陶瓷电阻实验报告总结(3篇)

第1篇一、实验目的本次实验旨在研究陶瓷电阻的物理特性,包括电阻值、温度系数、电阻率等,以及陶瓷电阻在电路中的应用。
通过实验,了解陶瓷电阻的基本原理和制作方法,为后续相关研究提供参考。
二、实验原理陶瓷电阻是利用陶瓷材料具有较高的电阻率和良好的稳定性而制成的电阻元件。
其主要特点是电阻温度系数小、耐高温、耐腐蚀、耐振动、耐冲击等。
陶瓷电阻的电阻值、温度系数、电阻率等参数可通过实验测量得到。
三、实验器材1. 陶瓷电阻:若干个不同规格的陶瓷电阻;2. 电阻测量仪:用于测量陶瓷电阻的电阻值;3. 温度计:用于测量陶瓷电阻的温度;4. 电源:提供实验所需的电压;5. 接线板:用于连接实验器材;6. 实验台:用于放置实验器材。
四、实验步骤1. 测量陶瓷电阻的电阻值:将陶瓷电阻接入电阻测量仪,读取电阻值;2. 测量陶瓷电阻的温度系数:将陶瓷电阻置于温度计附近,测量不同温度下的电阻值,计算温度系数;3. 测量陶瓷电阻的电阻率:将陶瓷电阻置于电阻测量仪,读取电阻值,计算电阻率;4. 陶瓷电阻在电路中的应用:将陶瓷电阻接入电路,观察其在电路中的性能。
五、实验结果与分析1. 陶瓷电阻的电阻值:实验结果显示,不同规格的陶瓷电阻具有不同的电阻值,符合预期;2. 陶瓷电阻的温度系数:实验结果显示,陶瓷电阻的温度系数较小,说明其在温度变化时电阻值变化不大,具有良好的稳定性;3. 陶瓷电阻的电阻率:实验结果显示,陶瓷电阻的电阻率较高,符合预期;4. 陶瓷电阻在电路中的应用:实验结果显示,陶瓷电阻在电路中表现出良好的性能,如耐高温、耐腐蚀、耐振动等。
六、实验结论1. 陶瓷电阻是一种具有良好物理特性的电阻元件,适用于电路中要求稳定性、耐高温、耐腐蚀等场合;2. 通过实验,掌握了陶瓷电阻的电阻值、温度系数、电阻率等参数的测量方法;3. 陶瓷电阻在电路中的应用表明,其在实际应用中具有良好的性能。
七、实验注意事项1. 实验过程中,注意安全,避免触电、烫伤等事故;2. 测量陶瓷电阻时,确保仪器准确可靠;3. 实验数据应准确记录,以便后续分析;4. 注意实验过程中的温度控制,避免对实验结果产生影响。
烧结温度和烧结温度范围与测定

6.每到取样温度点时,应保温15min,然后在电炉内取出样品,迅速 地埋在预先加热的石英粉或Al2O3粉内,以保证试样在冷却过程中不 炸裂。冷至接近室温后,再从石英粉或氧化铝粉中取出样品。并记好 每个取样温度点的温度及相应取出的样品编号。将焙烧过的试样,用 刷子刷去表面石英粉或Al2O3粉(低温烧后的试样用软毛刷),检查 试样有无开裂、粘砂等缺陷,然后放人105~110℃烘箱中烘至恒量, 放人干燥器内,冷却至室温。 7.将试样分成两批,900℃以下为第一批,测定其饱吸煤油后在煤油 中重及饱吸煤油后在空气中重;900℃以上的试样为第二批,测定其 饱吸水后在水中重及饱吸水后在空气中重。
式中 G0 ——干燥试样在空气中质量,g; G1——干燥试样饱吸煤油后在煤油中质量,g; G2——干燥试样饱吸煤油后在空气中质量,g; G3——烧后试样在空气中质量,g; G4 ——烧后试样饱吸煤油(水)在煤油(水)中质 量,g; G5——烧后试样饱吸煤油在空气中质量,g; γ水——水的密度(在室温下),g/ cm3; γ油——煤油的密度(在室温下),g/ cm3; V0——干燥试样体积,cm3; V ——烧后试样体积,cm3。
3.(1)吸水率的测定,由于样品表面不可能很光滑, 表面水膜不能完全擦净等原因,当样品实际无开 口孔隙,吸水率为零时,而测定的样品吸水率一 般不大于0.05%。因此,样品烧结温度范围的确 定,可根据测定的吸水率不大于0.05%,体积收 缩率和体积密度维持在最大的烧结温度至开始过 烧温度的温度范围,即样品的烧成温度范围。
(2)为了确定烧成温度范围准确,可将这部分样 品进行孔隙性试验,其结果均应不吸红。若有吸 红的样品,其对应的焙烧温度点应除外,或重新 进行试验。 (3)根据计算出的各温度点取出的样品测定结果, 以温度为横坐标,样品的孔隙率(吸水率)、体 收缩率和体积密度为纵坐标,绘制出样品孔隙率 吸水率一温度曲线、体积收缩率一温度曲线和体 积密度一温度曲线,以表示样品随着焙烧温度上 升的变化情况和烧成温度范围。
- 1、下载文档前请自行甄别文档内容的完整性,平台不提供额外的编辑、内容补充、找答案等附加服务。
- 2、"仅部分预览"的文档,不可在线预览部分如存在完整性等问题,可反馈申请退款(可完整预览的文档不适用该条件!)。
- 3、如文档侵犯您的权益,请联系客服反馈,我们会尽快为您处理(人工客服工作时间:9:00-18:30)。
实验烧结温度和烧结温度范围的测定——烧结炉法
一、实验目的
(1)掌握烧结温度与烧结温度范围的测定原理和测定方法;
(2)了解影响烧结温度与烧结温度范围的复杂因素;
(3)明确烧结温度与烧结温度范围对陶瓷生产的实际意义。
二、实验原理
烧成是陶瓷制品在生产中的重要环节。
为了制定最适宜的烧成条件,必须确切地了解各种陶瓷制品的烧结温度、烧结温度范围以及热过程中的重量变化、尺寸体积变化、吸水率、气孔率及处貌特征的变化,以便确定最适宜的烧成制度,选择
适用的窑炉以及合理利用具有温度差的各个窑位。
对粘土类原料而言,在加热过程中坯体气孔率随温度升高而逐渐降低,当粘土坯体的密度达到最大值,吸水率不超过5%,此状态称为粘土的烧结,粘土达到此状态的温度为完全烧结温度,简称烧结温度。
自烧结温度继续升高温度,粘土坯体逐渐开始软化变形,此状态可依据过烧膨胀或坯体表面出现大的气孔或依
目力观察有稠密的小气孔出现来确定,达到此状态时的温度称为软化温度(或称过烧膨胀温度),完全烧结温度和软化温度之间的温度范围称为烧结温度范围(简称烧结范围)。
中国科学院上海硅酸盐研究所在制瓷原料的研究中是:以被焙烧的粘土类原料的烧成线收缩曲线开始突然下降,即开始进行急剧收缩时的温度作为玻化温度
范围的下限,当收缩进行到转向过烧膨胀的温度称为玻化温度范围的上限。
上限温度与下限温度的区间为玻化范围.。