复合材料孔隙率的测定
孔隙率测试方法
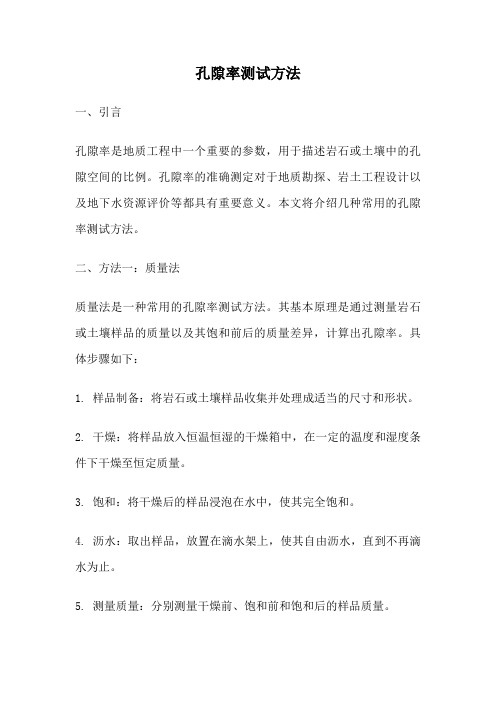
孔隙率测试方法一、引言孔隙率是地质工程中一个重要的参数,用于描述岩石或土壤中的孔隙空间的比例。
孔隙率的准确测定对于地质勘探、岩土工程设计以及地下水资源评价等都具有重要意义。
本文将介绍几种常用的孔隙率测试方法。
二、方法一:质量法质量法是一种常用的孔隙率测试方法。
其基本原理是通过测量岩石或土壤样品的质量以及其饱和前后的质量差异,计算出孔隙率。
具体步骤如下:1. 样品制备:将岩石或土壤样品收集并处理成适当的尺寸和形状。
2. 干燥:将样品放入恒温恒湿的干燥箱中,在一定的温度和湿度条件下干燥至恒定质量。
3. 饱和:将干燥后的样品浸泡在水中,使其完全饱和。
4. 沥水:取出样品,放置在滴水架上,使其自由沥水,直到不再滴水为止。
5. 测量质量:分别测量干燥前、饱和前和饱和后的样品质量。
6. 计算孔隙率:根据测量结果,使用以下公式计算孔隙率:孔隙率 = (饱和前质量 - 饱和后质量) / (饱和前质量 - 干燥前质量)方法一的优点是操作简单,仪器设备要求相对较低,适用于现场或实验室的快速测试。
但是,该方法忽略了孔隙结构的复杂性,对于高孔隙率或多孔介质的测试结果可能存在一定的误差。
三、方法二:气体法气体法是另一种常用的孔隙率测试方法。
其基本原理是通过测量孔隙中充满气体的体积,计算出孔隙率。
具体步骤如下:1. 样品制备:将岩石或土壤样品收集并处理成适当的尺寸和形状。
2. 体积测量:使用气体法测试仪器,将样品放入密闭的容器中,记录容器内气体的初始体积。
3. 充气:将一定压强的气体注入容器,使其充满样品中的孔隙。
4. 体积测量:记录容器内气体的最终体积。
5. 计算孔隙率:根据测量结果,使用以下公式计算孔隙率:孔隙率 = (初始体积 - 最终体积) / 初始体积方法二的优点是可以测量高孔隙率和多孔介质,适用于各种类型的岩石和土壤样品。
然而,该方法对于孔隙率较低的样品可能存在测试结果不准确的问题。
四、方法三:电阻率法电阻率法是一种基于电磁物理原理的孔隙率测试方法。
孔隙率的测定方法
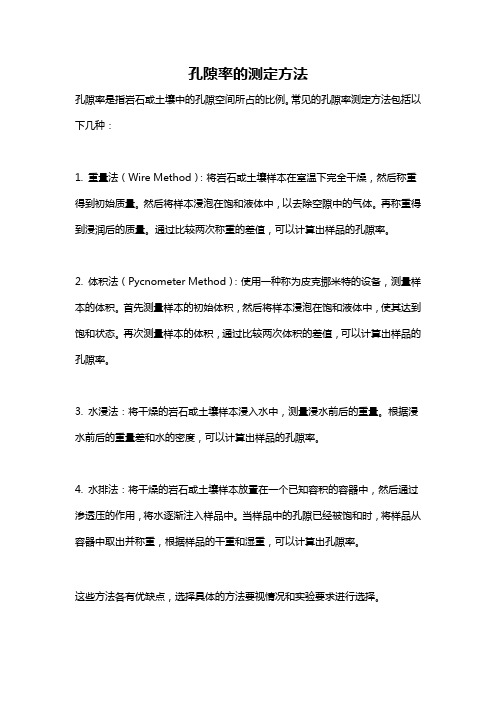
孔隙率的测定方法
孔隙率是指岩石或土壤中的孔隙空间所占的比例。
常见的孔隙率测定方法包括以下几种:
1. 重量法(Wire Method):将岩石或土壤样本在室温下完全干燥,然后称重得到初始质量。
然后将样本浸泡在饱和液体中,以去除空隙中的气体。
再称重得到浸润后的质量。
通过比较两次称重的差值,可以计算出样品的孔隙率。
2. 体积法(Pycnometer Method):使用一种称为皮克挪米特的设备,测量样本的体积。
首先测量样本的初始体积,然后将样本浸泡在饱和液体中,使其达到饱和状态。
再次测量样本的体积,通过比较两次体积的差值,可以计算出样品的孔隙率。
3. 水浸法:将干燥的岩石或土壤样本浸入水中,测量浸水前后的重量。
根据浸水前后的重量差和水的密度,可以计算出样品的孔隙率。
4. 水排法:将干燥的岩石或土壤样本放置在一个已知容积的容器中,然后通过渗透压的作用,将水逐渐注入样品中。
当样品中的孔隙已经被饱和时,将样品从容器中取出并称重,根据样品的干重和湿重,可以计算出孔隙率。
这些方法各有优缺点,选择具体的方法要视情况和实验要求进行选择。
工业ct孔隙率

工业CT孔隙率:原理、应用与优化策略一、引言在工业制造领域,孔隙率是一个关键的质量指标,尤其对于金属、陶瓷等材料的制品。
孔隙率过高可能导致制品的机械性能下降,甚至影响其功能性。
因此,准确、高效地检测孔隙率对于确保产品质量具有重要意义。
工业CT(Computed Tomography)技术作为一种无损检测方法,已被广泛应用于孔隙率的检测。
本文将详细介绍工业CT孔隙率的原理、应用以及优化策略。
二、工业CT孔隙率检测原理工业CT技术基于X射线穿透不同材料时的衰减差异,通过计算机重建物体的三维结构。
在孔隙率检测中,X射线穿过制品时,孔隙与实体材料对X射线的衰减程度不同,从而在重建的三维图像中形成明暗对比。
通过图像处理技术,可以定量计算制品中的孔隙率。
三、工业CT孔隙率检测应用1. 金属制品:在铸造、焊接等工艺过程中,金属制品可能出现气孔、缩孔等缺陷。
利用工业CT技术,可以无损地检测这些缺陷并计算孔隙率,为质量控制提供依据。
2. 陶瓷制品:陶瓷材料具有高硬度、高耐腐蚀性等特点,广泛应用于航空航天、电子等领域。
然而,陶瓷制品在制备过程中容易出现裂纹、气孔等缺陷。
工业CT技术可以检测这些缺陷并计算孔隙率,确保制品的质量。
3. 复合材料:复合材料由多种材料组成,其内部结构复杂。
工业CT技术可以检测复合材料中的孔隙、分层等缺陷,并计算孔隙率,为复合材料的制备工艺优化提供指导。
四、工业CT孔隙率检测优化策略1. 提高图像质量:图像质量是影响孔隙率检测精度的关键因素。
通过优化扫描参数(如X 射线管电压、电流等)、选择合适的重建算法以及降低图像噪声等方法,可以提高图像质量,从而提高孔隙率检测的精度。
2. 自动化检测:随着人工智能技术的发展,基于深度学习的自动化检测方法已被广泛应用于工业CT图像分析。
通过训练大量的标注数据,深度学习模型可以自动识别并分类孔隙,实现孔隙率的自动计算。
这不仅可以提高检测效率,还可以降低人为误差。
孔隙率超声检测技术在复合材料中的应用

递数据。以后就可直接采用US59校准仪器,
以便取得并建立与法宇航相一致的评定基准。并
按规定的检测技术规范实施孔隙率的测量。 从而达到检测结果能以法宇航的标准进行等效评 定的目的。 5.2但就目前的现状,由于还没有绘制出分贝衰减值与孔隙率的对应关系典线(或数据), 目前我们仅仅是根据标准中规定的用(中心频率lO~91z的宽频带)双探头超声穿透法检测时, 最大可接收孔隙率:2%,相当于-6分贝的衰减,这一要求对复合材料进行孔隙率的质量控制。 对于每一衰减分贝值所对应的孔隙率的含量,尚需做更多的试验。 5.3孔隙率的含量对超声波的衰减有着不同影响。此方法的建立对于其它类型的复合材料的 超声波衰减与孔隙率的相应关系也具有指导意义。
和
图2(a)可以看出当孔隙率较低时,孔隙的尺寸较小而且它们彼此之间相互分离;而当孔隙率 较大时,孔隙的长度均较大而且它们之间的距离也比较近,有时会连在一起,这些较大的孔 隙对孔隙率的大小起了决定性的作用。
4
孔隙率标准的建立
超声检测孔隙率的评定基准是个关键问题,即使是作为抽样破坏性检测孔隙率,也仍然
存在评定基准的标准化的问题。采取“逐次逼近”法建立孔隙率为o%的评定基准的方法,即 按法宇航标准要求,在实施检测的产品上,于相同N层的区域内寻找对超声吸收最小的部位 作为基准。而每次对送检产品的检测都是取包括本次之前所有产品上所能得到的最小吸收界 限作为评定基准,这样经过多次、火量产晶检测的统计逼近,最终达到或趋近一个最小的吸 收极限,这个最小的吸收极限就定义为理论上的孔隙率为O%的基准。 我们是以制造出来的碳纤维复合材料层压板结构最好对比试块,且与US59对比试块进行 比较分析,并在理论上就把US59对比试块当作孔隙率为096的标准试样,用来校准系统灵敏度。 但这并不是一个很严密的定量条件,所谓孔隙率为O%实际上是不存在的,只不过将可忽略的 孔隙率(小于0.5%)在理论上看作为o%而已,以便建立基准波高值,从而解决校准检测系统 灵敏度与孔隙率评定的需要。在实际检测过程中我们是以一dB表示相对孔隙率含量值,并通过 A/D转换按2dB量化,分8级色彩记录C扫描图像来代表相应量化界限范围内的孔隙率。但 要想针对测试的衰减-dB值找出具体对应的孔隙率含量,则需通过人量的试验测定出以Pv/一dB 表示复合材料层压板的内部孔隙率值Pv的关系曲线。应当指出,随选定校准试块的质量不同, 其测试结果是会有差异的。
民用飞机复合材料结构孔隙率的影响及检测

民用飞机复合材料结构孔隙率的影响及检测廉 伟中国商用飞机有限责任公司上海飞机设计研究院上海201210摘要:本文从工程实践出发,总结了民用飞机复合材料结构中孔隙率产生的原因及相关工艺控制措施与孔隙率之间的内在关系,对比分析了目前航空工业界和主制造商可接受的孔隙率标准,探讨了孔隙率对复合材料理化特性及力学特性影响机理,对比了不同孔隙率的检测方法和孔隙率的控制方法,并给出了考虑结构安全和成本,在工程设计、制造和验证中统筹考虑可接受孔隙率的建议。
关键词:民用飞机复合材料结构孔隙率无损检测1 引言机体结构主要采用高性能复合材料的新型民机B787引领了复合材料在民机结构中应用的飞跃式发展和航空结构材料的应用变革,其复材用量重量占比接近50%;其竞争机型A350复材用量更高,达到52%;波音最近声明B777的改进型B777X的机身结构和此前宣布的机翼结构同样将采用复合材料;中俄即将联合研制的宽体客机中结构材料用量也将达同等水平。
由此可见,航空界已对复合材料在降低结构重量、油耗与排放、全寿命周期成本上达成共识。
航空复材结构的飞跃式发展是以材料进步、工艺发展、评价体系逐步成熟和大尺寸产品制造问题解决等为基础的,即便如此,复合材料领域还有诸多问题有待继续研究和解决,孔隙率便是其中之一。
对于孔隙,不同的手册、标准和规范给出了不同的定义,但其本质含义基本统一,即复合材料内部的、几何尺寸很小的、多点分布的孔洞(可能是空气、挥发物或空穴)。
孔隙是复合材料结构中常见缺陷的一种,通常用其体积占材料总体积的百分比来表征,也即孔隙率。
孔隙的尺寸跨度很大,线性尺寸可能从几个微米到几百个微米不等,在波音公司的规范中,甚至认为一簇密集孔穴缺陷中只要最大的直径小于6.35mm,该簇孔穴即被视为孔隙。
2 孔隙产生的原因及其影响目前航空工业领域,复合材料结构主要采用预浸料-热压罐固化工艺或液体成型工艺,虽然工艺形式和参数各不相同,但本质过程都是树脂基体与纤维增强材料之间的复合及树脂固化的过程,因此孔隙总存在于基体、树脂纤维界面或层间,典型的孔隙形貌如图1、2所示。
复合材料孔隙率的超声检测方法探讨

复合材料孔隙率的超声检测方法探讨姓名:学号:摘要: 简单介绍了复合材料中孔隙的形成原因, 叙述了孔隙率对材料机械性能的影响, 综述了孔隙率测量的超声无损检测方法现状, 说明了目前各种检测方法的检测效果和优缺点, 并对将来孔隙率的检测方法作了展望。
关键词: 孔隙率; 复合材料; 超声检测孔隙是复合材料最常见的微小缺陷。
孔隙的出现会降低材料的性能, 如层间剪切强度, 纵向和横向的弯曲强度和拉伸强度、抗疲劳性以及高温下的抗氧化性能等。
即使孔隙含量很小, 也会对材料的寿命造成很大的影响[1- 4], 因此孔隙率的检测对复合材料的性能保证非常重要。
目前比较常用的无损检测方法是超声波检测, 国内外已对此种检测方法做了不少的研究, 并取得了一定的进展。
1 孔隙的形成及对材料的影响由于复合材料比较复杂的加工工艺, 完全没有孔隙的复合材料是没有的。
一般来说, 空隙的形成有两种原因[5]: 一是制作过程中树脂未完全浸润或叠层间空气未完全排除, 造成空气存留在其中, 这种原因形成的孔隙一般数量较多, 形状是扁圆形或拉长形; 二是由于工艺过程中产生挥发性物质, 这时形成的孔隙一般呈圆形, 孔隙数量较少, 孔隙的尺寸一般较小, 直径为几微米到几百微米。
评定孔隙对材料影响程度大小的定量指标是孔隙率, 有面积孔隙率和体积孔隙率两种定义。
面积孔隙率是单位面积所含孔隙的面积的百分比, 体积孔隙率是单位体积所含孔隙的体积百分比。
具体根据实际检测技术的不同采取不同的指标描述。
复合材料的机械性能对孔隙十分敏感。
ALmei2da[6]等人用实验证明, 即使孔隙的存在对材料的静态强度只有中等程度的影响, 它却可以使疲劳寿命显著下降。
研究指出, 孔隙率在0% ~ 5% , 每增加1%, 其层间剪切强度平均下降7% 左右, 其他性能如弯曲强度以10% 左右的比例下降, 弯曲模量则以5% 左右的比例下降。
不过孔隙的存在并不是对材料都具有有害的影响。
孔隙率的测试方法
孔隙率测试
材料的孔隙率是指材料内部孔隙的体积占材料总体积的百分率,以P表示。
孔隙率的测定是基于阿基米德原理,试验中采用水煮法测定电极的孔隙率。
首先称量需要的试样干重,记为m0;将称量完地试样放入干净的烧杯中,往杯中注入蒸馏水,直至淹没试样。
接着将烧杯置于电炉上加热至沸腾,并保持沸腾状态2h,使蒸馏水完全渗透至TiO2电极中的空隙内。
然后停止加热使其降至室温。
接着把试样快速取出放入事先准备好称重用的小吊蓝内,将其挂在天平的吊钩上,使试样继续浸没于水中,称取饱和试样在水中的悬浮重,记为m1;将饱和试样取出,用湿抹布小心地拭去饱和试样表面的水,快速称量饱和试样的质量,记为m2。
通过公式算出电极的孔隙率P。
P=(m2-m0)/(m2-m1)。
孔隙率测定——精选推荐
孔隙率测定
(开气孔率在80~90 vol %之间的多孔陶瓷铝合金过滤板)
本试验采用准确度较高的煮沸法测定制品的孔隙率。
(1)选取外观平整,表面不带有裂纹等破坏痕迹的试样,试验前刷去试样表面的灰尘和细碎颗粒,置于电热干燥箱中于110±5℃下烘干至恒重,即间隔一小时的两次连续称量之差小于0.1 wt %。
试样放置在干燥器中冷却至室温,称量精确至0.01g。
(2)将试样放在煮沸用器皿上,加入蒸馏水使试样完全被淹没,加热至沸腾后继续煮沸2 小时,之后冷却到室温。
(3)将上述饱和试样放入铜丝网篮,悬挂在带溢流管的注满蒸馏水的容器中,称量饱和试样在水中的重量,精确至0.01 g。
(4)从水中取出饱和试样,用饱含水的多层纱布,将试样表面的过剩水分轻轻擦掉(注意不应吸出试样孔隙内的水),迅速称量饱和试样在空气中的重量,精确到0.01 g。
ρ=(G2-G1)/(G2-G3)………………………………(2-1)
式中:ρ——试样的显气孔率(vol %);
G1——试样的干燥重量(g);
G2——饱和试样在空气中的重量(g);
G3——饱和试样在水中的重量(g)。
孔隙率测试方法
孔隙率测试方法一、引言孔隙率是指岩石或土壤中孔隙所占的比例,是岩石或土壤的一个重要物理性质参数。
了解孔隙率对于地质勘探、水文地质、土壤力学等领域具有重要意义。
本文将介绍几种常用的孔隙率测试方法。
二、密度法密度法是一种简单常用的孔隙率测试方法。
该方法通过测量岩石或土壤的干重和饱和重来计算孔隙率。
首先,将样品进行干燥,获得干重。
然后,将样品浸泡在水中,使其完全饱和,并测量饱和重。
最后,通过以下公式计算孔隙率:孔隙率 = (饱和重 - 干重)/ 饱和重× 100%三、气体法气体法是一种适用于孔隙率测试的非破坏性方法。
该方法利用气体在孔隙中的渗透性来计算孔隙率。
首先,在样品中施加一定的压力,使气体进入孔隙中。
然后,测量气体的压力变化,根据波伊尔定律计算孔隙率。
气体法对于岩石和土壤的孔隙率测试具有较高的精度和准确性。
四、电阻率法电阻率法是一种利用电流通过样品时的电阻变化来计算孔隙率的方法。
该方法基于样品的电导率与孔隙率之间的关系。
首先,将电极插入样品中,施加一定的电流,测量电阻变化。
然后,根据电阻率与孔隙率之间的关系,计算孔隙率。
电阻率法适用于不同类型的岩石和土壤,但在实际应用中需要考虑样品的电导率变化。
五、声速法声速法是一种利用声波在样品中传播的速度来计算孔隙率的方法。
该方法基于声速与孔隙率之间的关系。
首先,在样品上施加一定的压力,产生声波。
然后,测量声波在样品中传播的时间,并根据声速与孔隙率之间的关系计算孔隙率。
声速法适用于不同类型的岩石和土壤,但在实际应用中需要考虑样品的压缩性和饱和度等因素。
六、测井法测井法是一种利用地下测井仪器来测量孔隙率的方法。
该方法通过测量地下岩石或土壤的电磁、声波、核磁等物理性质来推断孔隙率。
测井法适用于地质勘探和水文地质等领域,具有较高的精度和准确性。
七、总结孔隙率是岩石或土壤的重要物理性质参数,对于地质勘探、水文地质和土壤力学等领域具有重要意义。
本文介绍了几种常用的孔隙率测试方法,包括密度法、气体法、电阻率法、声速法和测井法。
复合材料孔隙率的测定ppt课件
.
20
THE END!
.
21
.
22
.
23
.
24
.
25
.
26
.
9
复合材料在制造过程中容易产生的 缺陷可以分为宏观缺陷和微观缺陷 两大类。就微观孔隙缺陷而言,其 显著的特点是缺陷细微,甚至小到 微米级,分布在树脂或树脂基纤维 界面之间,呈明显体积分布。不仅 宏观缺陷的存在影响复合材料的性 能,微观缺陷的存在也会直接影响 复合材料力学性能和可靠性。
如孔隙,对于动态的力学性能来说
18
③显微照相法
该方法是一种常用的对孔隙率做 定量分析的方法。使用前先在所 测试件上选取几个截面,并进行 抛光处理,然后放在配有一定数 量方格参考物的显微镜下观察试 件的抛光截面,最后对落在方格 交叉点上的孔隙进行计数。如图 所示,得到面积孔隙率公式:
.
19
采用这种方法可以看出孔隙的种类、形状、大小 及分布。是目前孔隙率检测方法中精度最高的,但 由于其检测的是局部截面的孔隙率,只能按统计方 法来求出试件整体的孔隙率,因此要获得高的精确 度,必须对大量截面进行检测。因此其精度只比其 它方法相对来说略高一些。
等,现就其中几个比较常用的方法进行介绍
.
14
①密度测量法
.
15
.
16
由公式可知,该法得到的孔隙率是所测材料的 体积孔隙率,此方法的前提条件是树脂浇铸体 必须没有气泡,并且测定浇铸体密度时固化温 度、时间、压力等参数应与复合材料一致。
这种方法测得的孔隙率数值的精确度较低,一 般为 ±0.5%,这限制了低孔隙率情况下的应用。 该法相对来说操作简单,容易实现,不需要太 复杂仪器,因而得到广泛应用; 缺点是无法得 知孔隙尺寸、形状和分布,且一般精度不是很 高,可以与其它方法配合使用。
- 1、下载文档前请自行甄别文档内容的完整性,平台不提供额外的编辑、内容补充、找答案等附加服务。
- 2、"仅部分预览"的文档,不可在线预览部分如存在完整性等问题,可反馈申请退款(可完整预览的文档不适用该条件!)。
- 3、如文档侵犯您的权益,请联系客服反馈,我们会尽快为您处理(人工客服工作时间:9:00-18:30)。
本方法需要通过试验测得组分 树脂。复合材料在水中 300h 后吸收水的质量以及复合材料 中树脂质量含量,由公式可求 得体积孔隙率为:
②吸水测量 法
该方法得到的孔隙率也是 复合材料的体积孔隙率, 由于其它缺陷如裂纹、分 层等的存在对计算结果 的影响,该方法检测精度 与密度测量法差不多,但 是操作过程更为繁琐、耗 时,故其应用效果不及密 度法广泛。
碳纤维复合材料尽管有许多优良的特性,然而保 证材料质量,检测材料缺陷,是其得以正确、安 全应用的前提。碳纤复合材料的缺陷种类有很多, 孔隙是复合材料中最为常见、最为重要的缺陷之 一。
完全无孔隙的复合材料是没有的。
孔隙率对复合材料性能的影响
孔隙率对碳纤维复合材料性 能的影响主要体现在对复合 材料层间剪切性能和弯曲性 能的影响。 。
复合材料在制造过程中容易产生的 缺陷可以分为宏观缺陷和微观缺陷 两大类。就微观孔隙缺陷而言,其 显著的特点是缺陷细微,甚至小到 微米级,分布在树脂或树脂基纤维 界面之间,呈明显体积分布。不仅 宏观缺陷的存在影响复合材料的性 能,微观缺陷的存在也会直接影响 复合材料力学性能和可靠性。
如孔隙,对于动态的力学性能来说 就是一个应力集中点,在反复载荷 下会成为一个疲劳源,对于静态的 力学性能来说,孔隙会造成材料内 部疏松并使力学性能下降。
孔隙率对层间剪切性能的影响
研究表明,每含 1%的孔隙率,复合材料的层间剪切性能 下降 5%至 15% 不等,直到孔隙率达到4%时,这种规律 基本保持不变。通过试验得出复合材料孔隙率与层间剪切 性能的关系,当孔隙率小于 0.75% 时,剪切强度都在 76MPa 左右,孔隙率对剪切强度的影响不大,当孔隙率 大于1.5% 时,剪切强度迅速下降,只有 60%的保持率。 当孔隙率较低时( 尤其低于 4%时) ,剪切强度随孔隙率增 大而下降得比较快,当孔隙率大于 5%以后,强度损失己 经过大,并随孔隙率的增大下降得比较缓慢或稳定。 孔隙率0% 增大到 1%时,强度下降约 9%,当孔隙率 增大到 4% 时,强度己经下降32%.孔隙率在 0%-4%,每 增1%,剪切强度平均下降约 8%,基本成线性关系。
THE END!
如何测定孔隙率?
孔隙率的检测方法
鉴于孔隙是评价复合材料的重要指标,因此人 们对孔隙率的检测总结了大量的测量方法,总体来 说复合材料孔隙率的检测方法分为两类: .破坏性检测法
主要包括①密度测量法、②吸水法、③显微照相法
、④酸溶解法
.无损检测法 包括超声波检测法、射线检测法、热红外成像方法 等,现就其中几个比较常用的方法进行介绍
孔隙率对弯曲性能的影响
随着孔隙率的增加,弯曲强度逐渐下降,在孔隙 率小1%时,弯曲性能相差不大,弯曲强度的保持 率为 90%左右,当孔隙率大于 3%时,弯曲强度的下 降趋势趋于平缓,弯曲强度保持率大约只有 75%。 当孔隙率超过一定的数值时,复合材料就会由于强 度的急剧下降而失效“另外,复合材料的其它性能。 如纵、横向拉伸强度、弯曲强度、模量、抗压强度、 疲劳极限等均受到孔隙率的影响。
①密度测量法
由公式可知,该法得到的孔隙率是所测材料的 体积孔隙率,此方法的前提条件是树脂浇铸体 必须没有气泡,并且测定浇铸体密度时固化温 度、时间、压力等参数应与复合材料一致。 这种方法测得的孔隙率数值的精确度较低,一 般为 ±0.5%,这限制了低孔隙率情况下的应 用。该法相对来说操作简单,容易实现,不需 要太复杂仪器,因而得到广泛应用; 缺点是无 法得知孔隙尺寸、形状和分布,且一般精度不 是很高,可以与其它方法配合使用。
复合材料孔隙率的测定方法
碳纤维复合材料是指把碳纤维作为增强相,与基 体材料合理地进行复合而制得的一种材料。 其主要优点在于材料的轻质高强和轻质高模的特 性,这种特性通常用比强度和比刚度来表示的。 比强度是强度与密度的比值,比刚度是弹性模量 与密度的比值。这两个比值越大可以说明材料特 性越优良。例如碳纤维环氧树脂复合材料在比强 度、比刚度方面明显的优于传统的航空材料铝合 金,成为航空工业的新宠。 碳纤维复合材料的优良特性使其在航空、航天等 领域得到了广泛的应用。
孔隙率的定义
评价孔隙含量的定量指标是孔隙率。孔隙率有两种定义方法 .面积孔隙率 指单位面积所含孔隙的面积的百分比
.体积孔隙率 体积孔隙率是指单位体积所含孔隙的ቤተ መጻሕፍቲ ባይዱ积百分比
具体应根据工程实践中的检测技术而有所不同"通常指的 孔隙率为体积孔隙率"根据统计学原理,在某一体积内, 当面积孔隙率统计的次数达到一定数量后,所有面积孔隙 率之和的平均值可近似为体积孔隙率。
孔隙的形态对复合材料力学性能的 影响
多数研究者在研究孔隙问题时都只是考虑孔隙率,这种方 法虽然简单,但却忽略了孔隙的形状、尺寸和分布对复合 材料力学性能的影响"近年来,孔隙的形状、尺寸等越来 越受到人们的重视 研究了孔隙的形状、尺寸和分布对其 力学性能的影响,研究发现,当孔隙的纵横比从 1增加到 4 时,复合材料的层间剪切强度降低了20%。
③显微照相法
该方法是一种常用的对孔隙率做 定量分析的方法。使用前先在所 测试件上选取几个截面,并进行 抛光处理,然后放在配有一定数 量方格参考物的显微镜下观察试 件的抛光截面,最后对落在方格 交叉点上的孔隙进行计数。如图 所示,得到面积孔隙率公式:
采用这种方法可以看出孔隙的种类、形状、大小 及分布。是目前孔隙率检测方法中精度最高的,但 由于其检测的是局部截面的孔隙率,只能按统计方 法来求出试件整体的孔隙率,因此要获得高的精确 度,必须对大量截面进行检测。因此其精度只比其 它方法相对来说略高一些。
产生孔隙的原因
孔隙是复合材料成型过程中形成的空洞,是复合材料的主 要缺陷之一。一般分为:延单纤孔隙(包括纤维内孔隙)和层 板间孔隙。孔隙率小于1.5%时,孔隙为球形:孔隙率大于 1.5%时,一般为柱形,孔隙与纤维轴向平行。产生孔隙的原 因有: ①树脂与纤维浸润性差,空气难以挤压出去 ②树脂中的低分子组分在加工过程中的挥发 ③复合材料固化过程中树脂的化学反应中也存在挥发物 ④成型工艺不合理 ⑤孔隙含量和分布与树脂的类型、沾度、组分、固化温度、 压力及时间有关。