剩余物料退库操作程序
车间退料标准操作规程

车间退料标准操作规程1目的建立车间退料的工作程序,使退料行为规范化、标准化。
2范围车间退回物料。
3责任生产技术部、质量管理部、中药饮片车间、仓库。
4内容4.1退料原则:生产车间所退物料必须经质量管理部QA确认无污染、无混淆、数量准确、下次生产可继续使用。
已印有批号的包装材料不准退料。
4.2退料程序:4.2.1 生产结束后,进行结料时,车间班长根据批生产记录核对剩余物料名称、规格、数量、批号(进厂编号),并将结余物料报仓管员。
4.2.2 QA到现场核查,具体项目如下4.2.2.1尚未开包的物料是否完整,封口是否严密,数量、批号(进厂编号)与批生产记录所示是否相符。
4.2.2.2已开封的零散包装的物料,其开封、取料、结料是否在与生产空气洁净度级别要求相适应的洁净条件内操作,数量、批号(进厂编号)是否与批生产记录所示相符。
4.2.2.3如对申请退料的物料之质量产生怀疑,则应填写物料请检单进行检验。
4.2.2.4如对申请退料的物料之数量产生怀疑,则复称并查对批生产记录,查找原因。
4.2.3退料4.2.3.1车间班长清点退料,复原包装,严密封口,贴上标签。
标签上注明产品名称、批号(进厂编号)、退料量,并注明日期,送回仓库。
编码:SW06-01-003 车间退料标准操作规程第2页共2页4.2.3.2仓管员依据车间开出的退料单,核对退料物料上的退料标签,确认无误后双方签名。
4.2.3.3 退料入库,贴上“退料”标志,放置于该批物料货物前部,码齐,确保下次发料时,优先发放。
4.2.3.4 退库物料记录入帐。
————————————————。
生产过程中剩余物料处理标准操作规程

生产过程中剩余物料处理标准操作规程1 目的为了规范对生产过程中剩余物料的处理,避免差错和混淆,制定本标准操作规程。
2 范围适用于生产过程中所有剩余的原辅料、包装材料的处理。
3 责任中药饮片车间、生产技术部、质量管理部。
4 内容4.1 生产过程中剩余原辅料处理程序4.1.1 准备好盛装剩余物料的容器或自封袋。
4.1.2 用饮用水、干净抹布清洗干净容器,并晾干。
4.1.3 统计剩余原辅料品名、批号、来源、数量、规格并记录清楚,交车间材料员。
4.1.4 把剩余原辅料分品种、批号、规格来源装入容器或封口袋内密封,并用状态标签贴在容器或包装袋上醒目的地方,标签应标明所装物料的品名、规格批号、来源、数量,贴好标签后,将其存放在原辅料暂存间,下批生产时优先使用;如不连续生产则将原辅料退回仓库。
4.1.5 车间负责人不定期检查剩余原辅料处理情况。
4.1.6 本工序负责人对剩余原辅料的处理负管理和监督的责任。
4.2 生产过程中剩余包装材料处理程序4.2.1 准备干净包装袋。
4.2.2 统计剩余包装材料的名称、批号、来源、数量后记录清楚,交车间材料员。
4.2.3 把剩余包装材料按名称、批号、来源分类装入包装袋内包装完好,并用状态标签贴在包装袋醒目的地方,标签应标明名称、来源、批号、数量,贴好标签后退回包装材料暂存间,下批生产时优先使用。
如不连续生产,时间超过七天则将包装材料退回仓库。
PE编码:SW09-01-010 生产过程中剩余物料处理标准操作规程第2页共2页包装袋不进行退库处理。
4.2.4 车间负责人不定期检查剩余包装材料的处理情况。
4.2.5 本工序负责人对剩余包装材料的处理负管理和监督的责任。
————————————————。
结料、退料标准操作规程
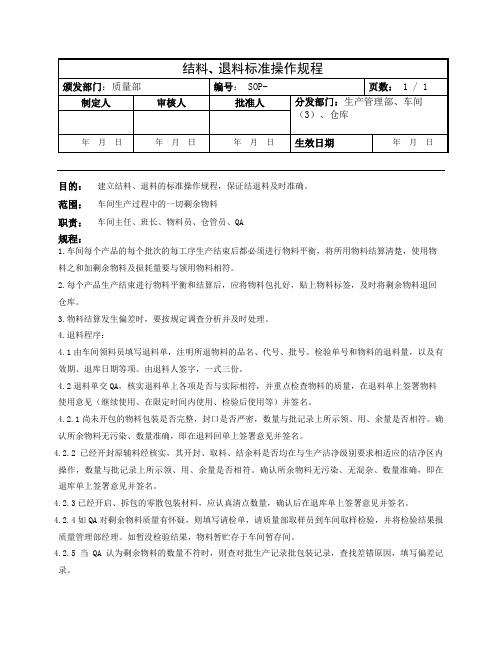
目的:建立结料、退料的标准操作规程,保证结退料及时准确。
范围:车间生产过程中的一切剩余物料职责:车间主任、班长、物料员、仓管员、QA规程:1.车间每个产品的每个批次的每工序生产结束后都必须进行物料平衡,将所用物料结算清楚,使用物料之和加剩余物料及损耗量要与领用物料相符。
2.每个产品生产结束进行物料平衡和结算后,应将物料包扎好,贴上物料标签,及时将剩余物料退回仓库。
3.物料结算发生偏差时,要按规定调查分析并及时处理。
4.退料程序:4.1由车间领料员填写退料单,注明所退物料的品名、代号、批号、检验单号和物料的退料量,以及有效期、退库日期等项。
由退料人签字,一式三份。
4.2退料单交QA,核实退料单上各项是否与实际相符,并重点检查物料的质量,在退料单上签署物料使用意见(继续使用、在限定时间内使用、检验后使用等)并签名。
4.2.1尚未开包的物料包装是否完整,封口是否严密,数量与批记录上所示领、用、余量是否相符。
确认所余物料无污染、数量准确,即在退料回单上签署意见并签名。
4.2.2已经开封原辅料经核实,其开封、取料、结余料是否均在与生产洁净级别要求相适应的洁净区内操作,数量与批记录上所示领、用、余量是否相符。
确认所余物料无污染、无混杂、数量准确,即在退库单上签署意见并签名。
4.2.3已经开启、拆包的零散包装材料,应认真清点数量,确认后在退库单上签署意见并签名。
4.2.4如QA对剩余物料质量有怀疑,则填写请检单,请质量部取样员到车间取样检验,并将检验结果报质量管理部经理。
如暂没检验结果,物料暂贮存于车间暂存间。
4.2.5当QA认为剩余物料的数量不符时,则查对批生产记录批包装记录,查找差错原因,填写偏差记录。
4.3由QA将退料单送回车间,并与车间物料员一起将退料单贴在退料外容器上。
4.4上述工作完成后,由仓管员收回退料,按退料单各项进行核对,确定无误后,由车间领料员和仓管员在退料单上签字,各留一份,并分别填写退料台帐。
退料管理规程完整版

退料管理规程HEN system office room 【HEN16H-HENS2AHENS8Q8-HENH1688】退料管理规程目的:建立一个退料管理规程,使退料工作规范化进行,保证退料质量。
范围:剩余生产物料。
责任:仓库保管员制定;仓储部部长审核;主管生产副经理批准;生产车间、质保部、仓储部执行。
内容:1.车间每个产品的每个批次生产结束后车间核算员都必须进行物料结算,将所用物料结算清楚,并将结算结果及时上报生产部。
使用物料与剩余物料之和要与领用物料相等或在限定范围之内。
若不符则在上报生产部时注明原因。
2.物料结算结果与“物料消耗定额”核对,超出消耗定额时,按《生产过程偏差处理规程》进行调查分析并及时处理。
3.每批产品生产结束要及时进行物料平衡和结算,若不连续生产同一品种,则要在三日内将剩余物料退回仓库。
4.退料程序一个批次的产品生产或包装操作结束后,生产工序负责人及时将剩余物料计数整理包装好,贴上《物料标签》,不允许有遗漏,转至中间站,与核算员办理交接手续。
质保部质监员对退库物料进行审核。
4.2.1尚未开包的物料包装是否完整,封口是否严密;已经开封的零散包件的物料,其开封、取样、接料是否均在生产洁净级别要求相适应的洁净区操作。
4.2.2确认剩余物料无污染、无混淆、数(重)量准确。
4.2.3质量不确定则由车间质检员填写《请验单》,取样员取样送检,由化验室检验判定物料是否存在质量问题。
若检验不合格则按《不合格物资管理规程》处理。
确认无质量问题后按以下程序进行。
核算员填写《退料通知单》(一式二份,车间自留一份、仓库留存一份),标明所退物料的名称、批号、数量、退料原因、退料单位等交仓库保管员。
仓库保管员通知搬运班组将所退物料搬至外清室(区),包上外包装,核算员贴上由质监员签字的《退料标签》。
由搬运员组负责将外清室中已包好外包装的退料送至仓库。
生产剩余物料应在清场结束后即进行退料处理,正常情况三日内完成,出现差错或不合格问题的处置不超过一周。
使用过的物料退库流程
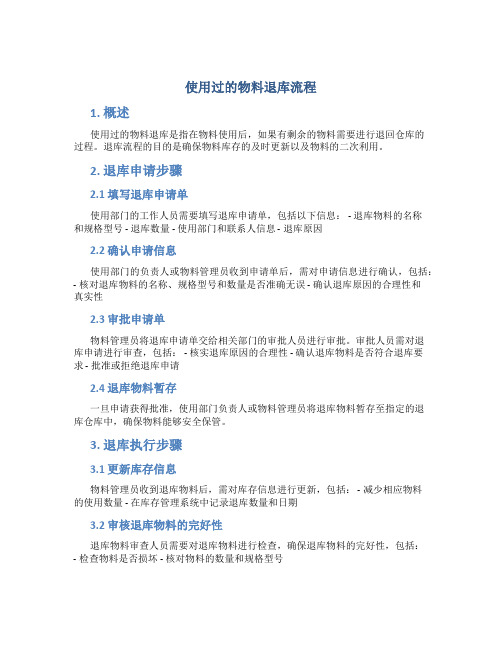
使用过的物料退库流程1. 概述使用过的物料退库是指在物料使用后,如果有剩余的物料需要进行退回仓库的过程。
退库流程的目的是确保物料库存的及时更新以及物料的二次利用。
2. 退库申请步骤2.1 填写退库申请单使用部门的工作人员需要填写退库申请单,包括以下信息: - 退库物料的名称和规格型号 - 退库数量 - 使用部门和联系人信息 - 退库原因2.2 确认申请信息使用部门的负责人或物料管理员收到申请单后,需对申请信息进行确认,包括:- 核对退库物料的名称、规格型号和数量是否准确无误 - 确认退库原因的合理性和真实性2.3 审批申请单物料管理员将退库申请单交给相关部门的审批人员进行审批。
审批人员需对退库申请进行审查,包括: - 核实退库原因的合理性 - 确认退库物料是否符合退库要求 - 批准或拒绝退库申请2.4 退库物料暂存一旦申请获得批准,使用部门负责人或物料管理员将退库物料暂存至指定的退库仓库中,确保物料能够安全保管。
3. 退库执行步骤3.1 更新库存信息物料管理员收到退库物料后,需对库存信息进行更新,包括: - 减少相应物料的使用数量 - 在库存管理系统中记录退库数量和日期3.2 审核退库物料的完好性退库物料审查人员需要对退库物料进行检查,确保退库物料的完好性,包括:- 检查物料是否损坏 - 核对物料的数量和规格型号3.3 生成退库单据物料管理员根据审核结果生成退库单据,包括以下信息: - 退库物料的名称、规格型号和数量 - 退库原因 - 退库日期 - 退库人员的签名3.4 退库单据审核退库单据需要经过相关人员的审核,包括: - 确认退库单据的准确性 - 确认退库物料的完好性和数量 - 批准退库3.5 再次更新库存信息经过审核的退库单据需要由物料管理员进行二次确认,并在库存管理系统中更新退库物料信息,包括: - 减少相应物料的库存数量 - 记录退库单据号和退库日期4. 退库流程结束一旦退库流程执行完毕,退库物料的库存信息将得到更新,并且物料库存数量将准确反映在库存管理系统中。
药企车间剩余物料退库管理制度
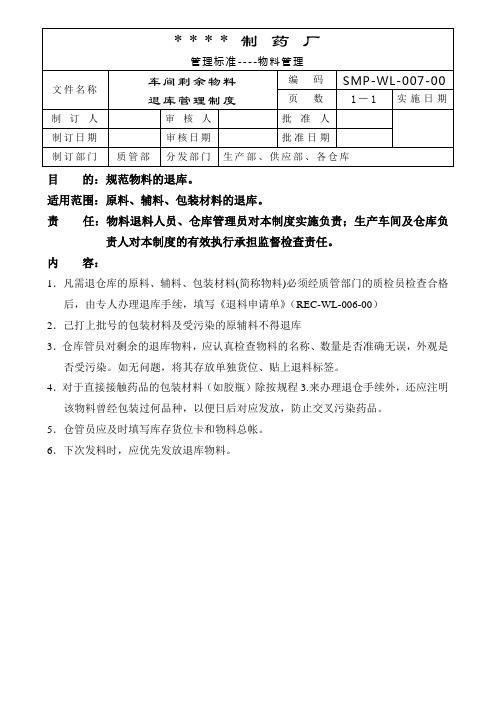
目的:规范物料的退库。
适用范围:原料、辅料、包装材料的退库。
责任:物料退料人员、仓库管理员对本制度实施负责;生产车间及仓库负责人对本制度的有效执行承担监督检查责任。
内容:
1.凡需退仓库的原料、辅料、包装材料(简称物料)必须经质管部门的质检员检查合格后,由专人办理退库手续,填写《退料申请单》(REC-WL-006-00)
2.己打上批号的包装材料及受污染的原辅料不得退库
3.仓库管员对剩余的退库物料,应认真检查物料的名称、数量是否准确无误,外观是否受污染。
如无问题,将其存放单独货位、贴上退料标签。
4.对于直接接触药品的包装材料(如胶瓶)除按规程3.来办理退仓手续外,还应注明该物料曾经包装过何品种,以便日后对应发放,防止交叉污染药品。
5.仓管员应及时填写库存货位卡和物料总帐。
6.下次发料时,应优先发放退库物料。
仓库退料管理流程

仓库退料管理流程仓库退料的流程是什么,办理退料有哪些相关的手续。
小编给大家整理了关于仓库退料流程,希望你们喜欢!产线退货流程1. 找到要退料的原限额领料单,点击领料;2. 在本次出库数量那一栏对应的子件(原材料)填上要退回仓库的数量(由于是退料,这里一定要填负数);3. 然后点击保存4.点击分单,就会生成一张红字的材料出库单温馨提示:红字的材料出库单相当于一张入库单5.参照订单生成一张红字到货单,然后保存6. 参照红字到货单生成红字采购入库单,保存,审核7.查询采购订单执行统计表,可查看对应的数量8.做采购发票时,要参照蓝字采购入库单和红字采购入库单生成同一张发票仓库退料管理规定1、目的为规范公司物品的退料工作,有效的对物料进行控管,降低不必要的损耗节约成本,特编制本规定2、适用范围本规定适用于公司指令性、号令性、技术、质量、生产、工程、销售、采购、综合等仓库领用物品的退库3、职责3.1《物料退库单》是物资退库的唯一凭证3.2 仓库保管根据审批后《物料退库单》内容做物料的退库3.3 无《物料退库单》,仓库保管拒绝物资退回仓库。
3.4退库工作由各职能部门配合仓库完成3.5企管部对退库过程进行管控4、过程4.1对于领用的物料在使用时遇有物料异常、用料变更、节余或因其它情况需要退回仓库时,相关部门安排人员进行退库。
4.2退库时退库单位填写《物料退库单》,物料退库凭单的填写要字迹清晰、页面整洁、项目齐全。
4.3退库方式4.3.1公司指令性退库公司指令性退库是指由公司层面发起的物料召回退库活动。
4.3.2技术性退库技术性退库是指因设计变更或设计错误来不及修正导致的领用物料退库。
4.3.3告知错误退库告知错误退库是指由销售、服务、生产任务、工程任务、研发认购指令下达错误导致的领用物料退库。
4.3.4质量问题退库质量问题退库是指由销售、生产、研发、工程过程中所用物料发现自身存在的外观、性能等质量问题而提出的物料退库。
剩余物料退库标准操作规程
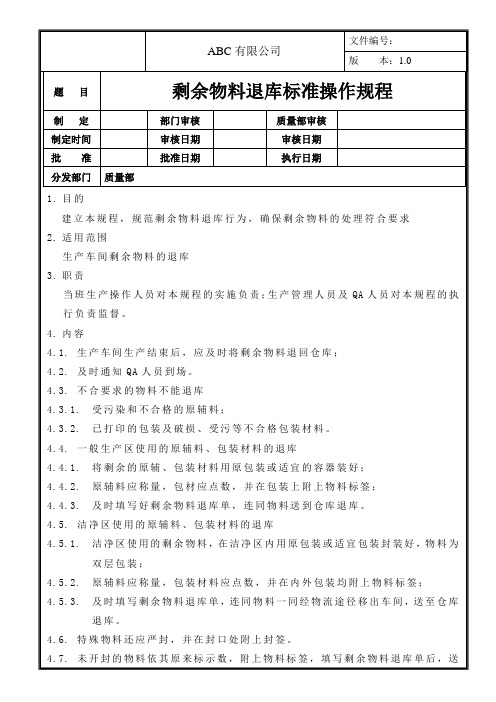
4.4.3.及时填写好剩余物料退库单,连同物料送到仓库退库。
4.5.洁净区使用的原辅料、包装材料的退库
4.5.1.洁净区使用的剩余物料,在洁净区内用原包装或适宜包装封装好,物料为双层包装;
4.5.2.原辅料应称量,包装材料应点数,并在内外包装均附上物料标签;
4.内容
4.1.生产车间生产结束后,应及时将剩余物料退回仓库;
4.2.及时通知QA人员到场。
4.3.不合要求的物料不能退库
4.3.1.受污染和不合格的原辅料;
4.3.2.已打印的包装及破损、受污等不合格包装材料。
4.4.一般生产区使用的原辅料、包装材料的退库
4.4.1.将剩余的原辅、包装材料用原包装或适宜的容器装好;
4.5.3.及时填写剩余物料退库单,连同物料一同经物流途径移出车间,送至仓库退库。
4.6.特殊物料还应严封,并在封口处附上封签。
4.7.未开封的物料依其原来标示数,附上物料标签,填写剩余物料退库单后,送至仓库退库。
题 目
剩余物料退库标准操作规程
制 定部Βιβλιοθήκη 审核质量部审核制定时间
审核日期
审核日期
批 准
批准日期
执行日期
分发部门
质量部
1.目的
建立本规程,规范剩余物料退库行为,确保剩余物料的处理符合要求
2.适用范围
生产车间剩余物料的退库
3.职责
当班生产操作人员对本规程的实施负责;生产管理人员及QA人员对本规程的执行负责监督。
- 1、下载文档前请自行甄别文档内容的完整性,平台不提供额外的编辑、内容补充、找答案等附加服务。
- 2、"仅部分预览"的文档,不可在线预览部分如存在完整性等问题,可反馈申请退款(可完整预览的文档不适用该条件!)。
- 3、如文档侵犯您的权益,请联系客服反馈,我们会尽快为您处理(人工客服工作时间:9:00-18:30)。
剩余物料退库操作程序
目的:规范剩余物料退库的操作程序。
范围:适用于生产车间剩余物料退库的操作。
责任:仓管员、生产车间领料员负责实施。
内容:
1.因为生产计划发生变化,使得剩余物料需退库时,应填写剩余物料退库单,
并由车间主任签字后,办理入库手续。
2.由于仓库不具备分装条件,仓库发料需发一件整包装时,车间领料员在车间
生产结束后,有车间主任签字后,对多领的物料办理退库手续。
3.退库单应写明退库日期、物料名称、批号、物料数量、重量、退库人及收件
人签字,送回仓库。
4.仓库对车间退回的物料应做好验收进库手续,做好剩余物料退库记录,并在
指定地点分类存放,对散装原辅料要检查是否包扎完好,是否有物料状态卡标明内容。
5.退库物料,由检查员现场检查,检查封口是否严密、有无破损及污染情况,
在退库记录上填写(继续使用、限期使用、检验后使用)的意见,仓管员根据此意见办理。
6.退库物料再次发放前,仓管员应重新检查,如其包装完好、标志明确、未经不妥当贮存,可按正常程序发料,但在领料单上注明“退库品”字样,否则重新检验。