Dfmea案例
冲压模具dfmea案例
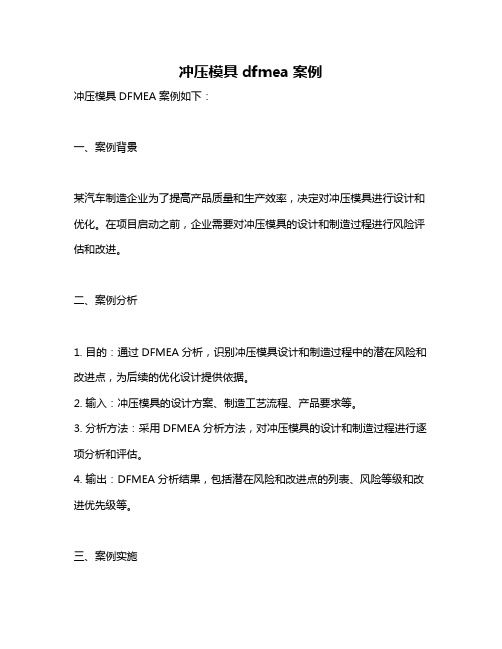
冲压模具dfmea案例
冲压模具DFMEA案例如下:
一、案例背景
某汽车制造企业为了提高产品质量和生产效率,决定对冲压模具进行设计和优化。
在项目启动之前,企业需要对冲压模具的设计和制造过程进行风险评估和改进。
二、案例分析
1. 目的:通过DFMEA分析,识别冲压模具设计和制造过程中的潜在风险和改进点,为后续的优化设计提供依据。
2. 输入:冲压模具的设计方案、制造工艺流程、产品要求等。
3. 分析方法:采用DFMEA分析方法,对冲压模具的设计和制造过程进行逐项分析和评估。
4. 输出:DFMEA分析结果,包括潜在风险和改进点的列表、风险等级和改进优先级等。
三、案例实施
1. 根据DFMEA分析结果,对冲压模具的设计和制造过程进行优化改进。
2. 针对潜在风险和改进点,制定相应的解决措施和优化方案。
3. 对优化后的冲压模具进行试验和验证,确保改进效果符合预期。
4. 将改进后的冲压模具应用于生产线上,观察其效果并进一步优化。
四、案例总结
通过DFMEA分析,企业成功地识别了冲压模具设计和制造过程中的潜在风险和改进点,并采取有效的措施进行了优化改进。
改进后的冲压模具在质量和生产效率方面都有了显著提升,为企业的可持续发展奠定了坚实基础。
DFMEA经典案例(4)

3
非凡的文化品位
体现不出高尚的 品位
不能增进好感
7
表达方式不当
6
295 第三方宣传造势 互动性交谈,以 245 对方为中心,灵 活进行。 162 父母搬出住 72 72 270 315 None None
展现的时机不当 没有足够住房 经济基础差 影响婚姻成败 9 没有一定数额存款 有保障的经济基础 经济没有保障 影响婚姻成败 9 没有丰厚的收入 工作没有保障 职业低下(清洁公 司) 油嘴滑舌,有“花 心”的迹象 举止轻浮,动手动 脚 有“前科”记录, 有暴力行为 不学上进,妒忌猜 疑心强 曾吃喝赌谝样样精 通 不良习气 影响婚姻成败 7 好吃懒做
270 克服坏习惯 504 克服坏习惯 36 54 None None
感觉不可靠 值得托付终身的品 质
影响婚姻成败
9
288 克服坏习惯 第三方赞扬其勤 快会做家务等
王老五/7月10 日前 帅哥/倩妹/王媒 婆7月10日前
4
解释“误会”
5
140
帅哥/倩妹/王媒 制定15套应 婆7月10日前 急方案 王老五/7月10 日前
7
1
4
28
谈吐幽默有品位
影响好感/第一印 俗气.乏味.无聊 象
展现失败
表达方式不当
约会D-FMEA
(1)项目名称 王老五的第999次约会
(4)过程责任部门
王媒婆 2015/7/18
(6)FMEA编号
FMEAWANG999 2 页 共 帅哥 修订日期 2
才学疏浅,肚里没 货
设计功能 (9) 要求
措施结果 (21)责任及 探 19风 (17)现行设计 测 险顺 (20)建议措施 目标 完成日 2 控制 26 (22) 采 23 24 度 序数 期 5 RPN 取的措施 S O D
太阳能逆变器设计DFMEA案例分析

太阳能逆变器设计DFMEA案例分析DFMEA(Design Failure Modes and Effects Analysis)是用于评估产品设计可能出现的故障、效应以及相应的预防措施的方法。
今天我们将运用DFMEA方法,对一款太阳能逆变器的设计进行案例分析。
一、产品描述该太阳能逆变器为一款出口型产品,主要用于太阳能发电系统中,将直流电转换为交流电。
产品工作电压范围为DC 200-600V,最大输出功率为3.5KW,具备防雷、过温、短路、过压、过流等保护功能。
产品尺寸为320 * 190 * 85mm,重量约为4KG。
二、DFMEA分析2.1 确认可能出现的失效模式失效模式 | 效应 | 潜在原因 | 严重程度 | 发生频率 | 检测方法 | 措施---|---|---|---|---|---|---1. 输出电压不稳定 | 安全隐患、影响发电效率 | 元器件老化、电路设计不合理 | 10 | 5 | 防雷测试、故障监测 | 加强过电压、过流保护,采用优质元器件2. 输出电压、电流过大 | 电路烧毁、安全隐患 | 过流、过压等保护措施失效、元器件老化 | 10 | 5 | 防雷测试、故障监测 | 加强过电压、过流保护,采用优质元器件3. 输出电压有过大波动 | 影响发电效率 | 电容故障、电路设计不合理 | 8 | 3 | 产品测试 | 采用优质元器件,加强 PCB 线路电磁兼容性设计4. 输入电压不稳定 | 影响发电效率 | 电池老化、外界电压波动 | 7 | 4 | 故障监测、产品测试 | 采用输入电源波动范围更大的元件,加强电池保护5. 元器件老化 | 失效 | 元器件过度发热、使用寿命达到 | 9 | 7 | 测试、监测 | 采用易于更换的元器件,定期维护,加强散热设计2.2 计算风险优先等级风险优先等级 = 严重程度 ×发生频率 ×检测方法失效模式 | 风险优先等级 | 处理优先级---|---|---1. 输出电压不稳定 | 250 | 12. 输出电压、电流过大 | 250 | 23. 输出电压有过大波动 | 72 | 34. 输入电压不稳定 | 112 | 45. 元器件老化 | 441 | 52.3 制定预防措施- 对于风险优先等级为1、2的失效模式,我们将加强过电压、过流保护,并采用优质元器件,以降低失效的可能性。
dfmea潜在失效模式及后果分析案例

7
两侧导向筋强度不 足
CAE分析,导向筋 强度合理化 增加加强筋,提 高强度 连接处配合方式 选择合理
8
撞击导致结构破坏
8
连接处密封性差
密封性
手柄密封性 软管与软管连 不满足客户要 接管的密封性 求,影响手柄吸 差 尘效率 9 连接处密封性不足 增加密封件
裸机通过 重要部位断 需通过球 球击测试, 产品无法再使 裂(尤其是机 击测试 功能正常, 用 壳) 无断裂 电池包2000 电池包松脱或 次插拔寿命 电池使用效率 测试后挂靠 低 不牢 通过整机配 电池包撞墙 测试 机壳配合处断 裂
3
105
排除电池包倒扣位, 各暂定一个插拔力范 围。例3-5 kgf 1.参照样机考虑加弹 簧或弹片式减振结构
尺寸链分析计算保证尺 寸精度 尺寸链分析计算保证尺 寸精度 尺寸链分析计算保证尺 寸精度
检测插拔力 1.单边间隙 0.4mm以上 2.参照园林产 品
保证下盖与进 气口橡胶套翻 边配合无间隙 尘桶和下盖橡 胶密封圈尺寸 保证无间隙 分离管密封圈 翻边与尘桶之 间单边0.2mm过 盈 导流锥与橡胶 圈压装0.3mm过 盈 进气口与风机 橡胶套之间配 合单边过盈 过渡配合,IQC 尺寸全检 气阀密封圈喇 叭口做大,有 段直边配合 进气端两颗螺 丝柱保证高度 方向精度 密封圈与通风 盘内孔有单边 0.2mm过盈,检 测旋转力度 面接触部位开 槽加O型圈
8
A
1.塑件壳体加强筋 1.合理布设筋板 布设不合理 2.连接处强度薄 2.零件连接处强度 弱处加固 过于薄弱 1.机壳未做圆滑过 渡,磨损过大 2.电池包倒扣弹簧 疲劳 1.机壳参照园林 产品做圆滑过渡 2.选用成熟的电 池包 1.参照园林产品 机壳限位筋位强度 设计 2. 不够 配合尺寸计算累 积公差 1.参照园林产品 机壳与电池包卡扣 设计 2. 配合不当有干涉 配合尺寸计算累 积公差 机壳与电池包配合 配合尺寸计算累 间隙不当或无弹性 积公差 减震结构
新版dfmea系统分析案例

新版DFMEA系统分析案例案例背景一家汽车制造公司正在推出一款全新的SUV车型,为了确保车辆的质量和可靠性,公司决定采用新版的DFMEA(设计失效模式和影响分析)系统进行系统分析。
DFMEA是一种在设计阶段评估和减少系统风险的方法,它能够识别潜在的失效模式、分析其影响和严重性,并提供相应的改进措施。
系统分析步骤步骤一:定义系统首先,团队需要明确系统边界、系统功能和设计要求。
在这个案例中,团队需要定义SUV车型的关键系统和子系统,例如发动机、悬挂系统、制动系统、安全气囊等。
步骤二:识别失效模式在这一步骤中,团队需要对每个系统和子系统逐一进行分析,识别潜在的失效模式。
以发动机系统为例,可能的失效模式包括发动机无法启动、发动机自动熄火等。
步骤三:分析影响和严重性对于每个失效模式,团队需要评估其对系统和用户的影响,并确定其严重性。
影响可以包括安全风险、性能降低、故障率增加等。
严重性通常可以按照某个评估标准进行定量评估,例如使用1-10的等级评定。
步骤四:确定改进措施针对每个失效模式和其严重性,团队需要制定相应的改进措施。
例如,在发动机无法启动的失效模式下,可能的改进措施包括增加备用电池、加强电路连接等。
步骤五:实施改进措施在这一步骤中,团队需要逐一实施确定的改进措施,并对其进行记录和追踪。
例如,在实施了增加备用电池的改进措施后,团队需要跟踪发动机启动失效模式的发生率,以评估该措施的有效性。
案例分析结果通过对SUV车型各个系统和子系统的分析,团队得出以下结论:•发动机系统中,发动机自动熄火失效模式对车辆安全性有较大影响,严重性评级为8,建议增加燃油供给系统的检测和报警机制。
•悬挂系统中,悬挂系统异常噪声失效模式对乘坐舒适度和驾驶体验有较大影响,严重性评级为7,建议改进悬挂系统的阻尼设计。
•制动系统中,制动距离过长失效模式对行车安全性有较大影响,严重性评级为9,建议优化刹车片材料和刹车系统的液压传动机制。
结论随着汽车制造业的快速发展,确保车辆质量和可靠性变得至关重要。
设计失效分析DFMEA经典案例剖析

五:DFMEA应用与表格制作实战第2步 ——DFMEA严重度(S)评价准则
五:DFMEA应用与表格制作实战第2步 ——找失效点之5-重要程度分级
级别(重要程度)
✓ 本栏目可用于对零件、子系统或系统的产品特性分级
(如关键、主要、重要、重点等),它们可能需要附加的
过程控制。
✓ 任何需要特殊过程控制的对象应用适当的字母或符号在
c)各系统、子系统、各部门 逻辑影响关系
1. 明确功能(预期功能) 考虑非预期功能,失效模式是针对功能而言: Ⅰ型失效模式:不能完成规定的功能 Ⅱ型失效模式:产生了非预期的、有害的 考虑后果:站在用户将来使用产品的立场:
2.严重度分级: a) 确定级别要根据经验、要小组讨论,大家
形成共识. b) 对整车的影响,假设零件(分析)装入整 体运行
•失效模式: 指设计(制造)过程无法达到预定或规 定的要求所表现出的特征;如:坏品、不良设备状 况等; •后果: 指失效模式对客户(包括下工序)所造成的影响;
三:DFMEA基本概念相关——定义
•FMEA 是一种用来确认风险的分析方法,它包含: •确认潜在的失效模式并评价其產生的效应; •确认失效模式对客户所產生的影响; •确认潜在的產品/过程失效原因; •确认现有控制產品/过程失效的方法; •确定排除或降低失效改善方这案里这是里;正是文正内文容内部容分部,分这,里
三:DFMEA基本概念相关
三:DFMEA基本概念相关-FMEA 的开发与发展
• 20世纪 60年代,美国宇航界首次研究开发 FMEA; • 1974年,美国海军建立第一个 FMEA 标准; • 1976年,美国国防部首次采用 FMEA 标准; • 70年代后期,美国汽车工业开始运用 FMEA; • 80年代中期,美国汽车工业将 FMEA 运用于生產过程中; • 90年代,美国汽车工业将 FMEA 纳入 QS9000 标准;在
设计失效分析DFMEA经典案例剖析完整版.ppt

• 20世纪 60年代,美国宇航界首次研究开发 FMEA;
• 1974年,美国海军建立第一个 FMEA 标准;
• 1976年,美国国防部首次采用 FMEA 标准;
• 70年代后期,美国汽车工业开始运用 FMEA;
• 80年代中期,美国汽车工业将 FMEA 运用于生產过程中;
• 90年代,美国汽车工业将 FMEA 纳入 QS9000 标准;在 TQS9000体系中,是4.20统计技术这个要素中的首要审核项 目
•设计之前 是正文内容部分,这里是正文
预先进行风内险容这部分里分是,析正这文里,内是容正确部文分内保,容这部设分,计水平。
里是正文内容部分,这里是正 文内容部分,这里是正文内
容部分,这里是正文内 容部分,这里是正文
精心整理
14
四:DFMEA表格标准格式
精心整理
15
四:DFMEA标准格式
这里是正文内容部分, 这里是正文内容部分,这里 是正文内容部分,这里是正文 内容部分,这里是正文内容部分, 这里是正文内容部分,这 里是正文内容部分,这里是正 文内容部分,这里是正文内
• 09年8月,三合一外审正式提出对九阳的“DFMEA”应用要求
,对我们目前的FMEA状况较为不满;以后可能会作为一个主
要内容进行审核。
精心整理
11
三:DFMEA基本概念相关——FMEA的类型
DFMEA PFMEA SFMEA AFMEA PFMEA SFMEA MFMEA
设计失效模式及后果分析 过程失效模式及后果分析 服务失效模式及后果分析 应用失效模式及后果分析 采购失效模式及后果分析 子系统失效模式及后果分析 机器失效模式及后果分析
DFMEA理论与实战
——六步搞定DFMEA表格
嵌入式工控板卡DFMEA范例

芯片组本身实际抗高温与规格 书不符合(或策划采用筛选的 2 办法来过高温) PCB布局不合理导致散热器设 计受结构限制,主板上大热源 3 间距小互相影响。
MOS选取不满足要求
2
其他元器件选取不满足要求 2
PCB走线不当
3
内存时钟带负载能力不够
3
CF接口设计没有DMA功能
2
7
显示芯片电源纹波太大
3
显示
2
42 / 28 / 28 /
沈晖 沈晖
1.用测试开发板验证 2.根据实际样板结果更改
2
参与PCB布局和评审,合理解 决散热结构问题。
2
仔细计算所选MOS能否满足功 耗需求,参考以前成熟项目
3
选用规格符合温度范围的要 求的元件
2
1:PCB走线尽量按照design
guide的要求,实在不能满足
的参考其他成熟方案。
XXXX 版本:XX
行动结果 已采取的行动
S O D RP N
XXX 版本:XX
6
网络灯 电源IC 电源 CPU
网络灯接反
网络灯异常
5
TPS51116为新导入 IC,没有验证过
无法满足内存供电需 求
8
无法满足主板上电 时序要求
主板无法正常工作
9
纹波电流大
系统在运行过程中不
稳定,特别是跑大的 8
系统时,容易死机
网络变压器的电源与RTL8111C 冲突
3
设计规范和实际指示灯的连接 不一致,或线材连接反
2
IC供货来源
2
新导入的IC,设计中存在缺陷 4
全新chipset,没有验证
3
电源纹波控制没有满足芯片的 要求
- 1、下载文档前请自行甄别文档内容的完整性,平台不提供额外的编辑、内容补充、找答案等附加服务。
- 2、"仅部分预览"的文档,不可在线预览部分如存在完整性等问题,可反馈申请退款(可完整预览的文档不适用该条件!)。
- 3、如文档侵犯您的权益,请联系客服反馈,我们会尽快为您处理(人工客服工作时间:9:00-18:30)。
2
整体震动挤压试验
6
108
现场做防震处理
绝缘注塑件 电池壳体
注塑件起火 电解液挥发 电池漏液
安全事故 电池 容量降低 安全事 故
10
1
阻燃、绝缘试验
6
20
更换绝缘注塑件 更换电池 更换电池
7 9
2 2 单体震动挤压试验
6 6
84 108
高压箱
漏电 过电流 输出不受控制
安全事故 安全事故 安全事故
10 9 9
5
120
定期检查和更新BMS系统
4 10 8 4
6 1 5 5
更换SOC算法 BMS 控制系统升级 BMS 控制系统升级
充放电性能测试 充放电性能测试 充放电性能测试
6 6 6 6
144 60 240 120
定期检查和更新BMS系统 定期检查和更新BMS系统 定期检查和更新BMS系统 定期检查和更新BMS系统
电池组整体温度过高 影响电池工作 电池组整体温度过低 影响电池工作 噪音过大 影响乘车环境
电池间温度一致性差 影响电池工作 整体温度高,管理目 影响电池工作 标无法实现 连接片过热 安全事故
电池管理系
数据采样干扰性大和 影响用户使用 采样不准确 SOC异常 影响用户使用
4
6
BMS 控制系统升级
老化试验
现行探测性设计控制
现场电池组无输出电 电池组无法工作 压
探 测 度 数 3
R P N 63
临时采取的措施 现场更换损坏器件和改正 错误
单体电压过低
影响用户使用
7
4
设定标准值
万用表测量
6
168
更换电压过低电池
巡航里程低于额定值 影响用户使用
7
电池组单节容量降低或整 体过低 电池箱体密封不严
4
设定标准值
2 2 4
提高防护等级
漏电检测 过流保护
6 5 5
120 18 18
高压带电
安全事故
10 9 9 6 6 3 4 4 10
无有效保护措施 负载未断开、违规操作 充电时继电器未断开 风道设计不合理 加热系统未工作或设计达 不到要求 风扇固定不牢靠或功率过 高 通风方式不合理 环境温度过高 连接片氧化、未压紧防松 螺母连接电阻增加、截面 积小或材质不纯 电磁干扰,电路板虚焊或 保护电阻损坏 BMS SOC算法不合理 BMS 控制系统损坏 BMS 控制系统损坏 通信线断裂、线路连接错 误、受电磁干扰
2 2 2 4 4 5 5 3 3
提高防护等级 提高防护等级 提高防护等级
6 5 5 7 7 8 7 7 充放电性能测试 3
120 90 90 168 168 120 140 84 90 增加散热 更换加热系统 更换风扇 增加散热 外部环境降温 更换连接片或压紧防松螺 母
在负载连接的情况下 安全事故 意外开盖 充电时触电 热管理系统 安全事故
充放电性能测试
6
168
更换电压过低电池
电池组箱体
电池箱体进水
电池短路、电子器件失效 或损坏、箱体生锈 电子器件失效或损坏、影 响电池组散热 安全事故
7
3
提高防护等级
绝缘检测
6
126
现场做防水处理
电池箱体进灰尘
7
电池箱体密封不严
2
提高防护等级
绝缘检测
6
84
现场做防尘处理
电池组漏液
9
电池组间隙大电池受到挤 压碰撞震动 绝缘注塑件不阻燃 电池壳体密封不严 外力损伤;碰撞、安装不 规范造成密封结构破坏; 制造原因:焊接缺陷、封 合胶量不足造成密封性能 不好。 无有效保护措施 使用电流高于额定电流不 保护 元器件损坏
磷酸铁锂电池DFMEA分析
DFMEA
'01 PSW'!H6 '01 PSW'!F25
设计项目 动力电池
潜在的失效模式
潜在的失效后果
严 重 度 7
潜在的失效原因 /机理 1、电池组开路 2、未明确 区分正负极 3、主电缆未 连接、连接错误或器件损 坏 单节电池容量降低或损坏
频 度 数 3
现行预防性设计控制 用颜色和材料区分
电池组过充未报警和 安全事故 未保护 电池组过放未报警和 影响电池寿命或永久性损 未保护 坏 BMS通信异常 影响电池工作
'01 PSW'!H6 '01 PSW'!F25