步进式加热炉设计计算模板
步进梁式加热炉炉底机械设计
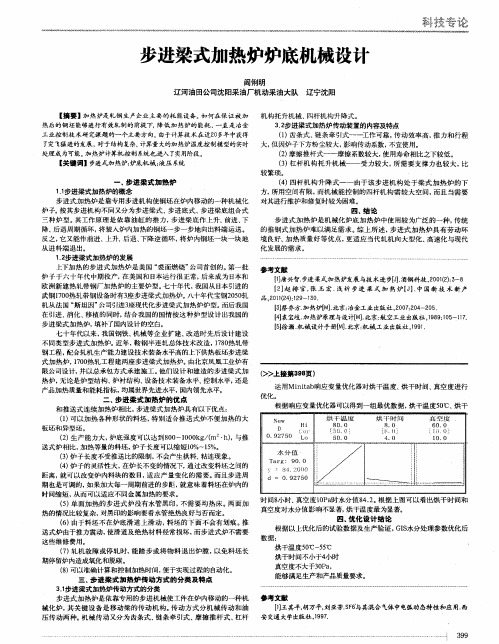
热后 的钢 坯能够进行 有效轧制的前提下, 降低加 热炉的能耗 —直是 台金 工业控制技 术研 究课题 的一个主要方向。由于计算技术在 近2 O 多年中Kg- 了突飞猛进 的发展 , 对于结构 复杂、 计算量大的加 热炉温度控制模型的实时 处理成 为可能。 加 热炉计算机控制 系统也进入了实用阶段。
反之它又能作前进上升后退下降逆循环将炉内钢坯一块一块地从进料端退12步进梁式加热炉的发展上下加热的步进式加热炉是美国裘面燃烧公司首创的
辩 镶专论
步进梁式加热炉炉底机械设计
阎俐 明 辽河油 田公司沈阳采 油厂机动采油大队 辽 宁沈阳
【 摘要 】加热炉是 轧钢 生产企业主要 的耗能设备。 如何 在保 证被 加 机构 托升机械 、四杆机 构升降式 。 3 . 2 步进梁式 加热炉传 动装置的内容及特点 ( 1 ) 齿条式 、 链 条牵引式一 唧= [ 作可 靠, 传 动效率 高, 推 力和 行程
1 . 2 步进 梁式加热炉 的发展 上下加 热 的步进式 加 热炉 是美 国 “ 裘 面燃烧” 公司首创的 。 第一批 参 考文献 炉 子于六 十年 代中期投产 , 在美 国和 日 本运 行很正常 , 后 来成 为 日 本和 【 1 ] 唐兴智. 步 进 梁式加热炉发展与技 术进步[ J 】 . 酒钢科技 , 2 o o 1 ( 2 ) : 5 - 8 欧 洲新建 热轧带钢厂加 热炉 的主要炉 型。 七十年 代, 我 国从 日 本 引进的 【 2 】 赵排 官, 张玉宏. 浅 析 步进 梁 式 加 热 炉【 J 】 . 中国新 技 术 新 产 武钢 1 7 0 0 热轧带 钢设备时 有3 座步进 梁式加 热炉 。 八十年 代宝 ̄2 o 5 o ¥ L 品, 2 0 1 1 ( 2 4 ) : 1 2 9 -1 5 0 .
加热炉课程设计说明书
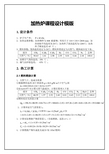
⑨计算金属热焓值
当t1均=610℃时,查表得cp= 0.5887 kJ/(kg.℃)
所以,i预=610×0.5887 = 359kJ/kg;Δi预=359-20×0.4773=349.6kJ/kg
注:与假设所得Δi预相差很小,故计算正确,不必重新校核,i预=610×0.5887 = 359kJ/kg。
4总加热时间
5单位加热时间
符合连续加热炉加热中碳钢时间要求。
2.4
1.炉子长度计算
①有效炉长:
②预热段长度:
③加热段双面加热长度:
④加热段单面加热长度:
⑤炉子总长:L总=L效+A=28517+1600=30117mm
2.炉门数量和尺寸确定
①进料炉门:炉门宽度B进= B=3.132m;炉门高度H进=3×0.11=0.330m;进料炉门数量:1个(炉尾端部)。
3.耐火材料和尺寸确定
本炉采用砌砖结构:拱顶(60度拱顶):加热段用一级硅砖300mm+硅藻土砖120mm;预热段用一级粘土砖300mm+硅藻土砖120mm;炉墙用一级粘土砖348mm+硅藻土砖120mm;
4.炉底水管布置及规格确定
①纵水管:最大中心距 ,取a实=1600mm;根数n=3132/1600=1.96,取n=2根;纵水管规格Ф121×20mm(横水管中心距b=2320mm条件下)。
②由k=0.977可计算天然气湿成分,计算结果列入下表
成分
CH4
C2H6
C3H8
H2
CO
CO2
N2
H2O
总和
天然气(%)
88.55
1.57
75T步进梁式加热炉技术方案书(用于钢锭轧制前的加热)

75T步进梁式加热炉用于钢锭轧制前的加热技术方案书目录第一篇商务文件(详细交流后提供)第一章报价表第二章供货清单一设备详细供货清单二备品备件清单三专用工器具清单第二篇方案书技术文件第一章原始设计条件一设计与环境条件二设备工艺要求第二章设备规格书一设备规格二产能计算三设备性能参数四设备介质、能源、动力消耗参数五设备组成及结构介绍(以下详细技术交流后提供)第三章投标设备质量控制计划一设计制造、检验、安装标准、规范二投标设备关键元器件选择及配套厂家三设备监造四质量保证承诺第四章工程进度、及交货计划(一双方工程范围二设计联络计划三制造进度计划四安装调试及人员派遣计划五考核测试及验收计划第五章包装、运输第六章资料交付一买方提供技术资料的内容及时间二卖方提供技术资料的内容及时间第七章培训及技术服务第二篇投标书技术文件第一章原始设计条件一设计与环境条件1 环境条件1.1 安装于室内1.2 海拔高度:1600m1.4周围空气温度所有户内电气/电子设备满足在室温40℃,没有空调的环境中长期安全可靠运行,且运行参数保2 公用介质条件2.1供电系统供电电源:三相四线制AC380V ±10% ;50HZ;频率及波动范围:50Hz±1Hz,或客户指定2.2水源条件工业水:悬浮物含量≤238毫克/升,悬浮物含量≤25毫克/升(经处理后一般)。
悬浮物颗直径不大于0.1mm,总硬度(德国度)8.8度,PH值:7.6。
入口压力为0.2-0.3Mpa。
水温:夏季温度:35℃,最热月平均27.5℃,冬季温度最低:3℃。
2.3 压缩空气供气条件:压缩空气0.4~0.6Mpa。
工作温度条件:环境温度在-20℃~40℃,湿度≤85%。
2.4 天燃气燃料类型:天然气煤气热值:8500~9000×4.18 kJ/m3压力范围:7~10k Pa二设备工艺要求1设备用途用于钢坯的轧制前加热。
第二章设备规格书一设备规格1炉型:炉子规格: 75T/炉钢锭加热炉炉子结构: 步进梁式进料方式侧面辊道快速自动进料至炉内工位出料方式侧面道快速自动出料至轧机辊道2组成3 设备规格炉型步进梁炉炉膛宽度9600 mm有效装料宽度: 9000 mm有效高度: 300 mm预热室长:7个步距,计:1400mm加热室长41个步距,计:8200mm装出料辊中心距9600mm步距200mm炉步数48步装出料辊中心高900mm炉底有效面积约100m2进料输送辊道长: 买方负责出料输送辊道: 买方负责(直接接辊机辊道)炉子总长: 约19000毫米以内(包括辅助设施安装空间)炉宽: 约12000毫米以内炉子总高: 约地面6000毫米、地下约3000mm炉子总重约150T加热室容积:约180m3二生产能力,产量计算三设备性能参数1生产能力:75T/h。
步进式加热炉炉温控制系统设计
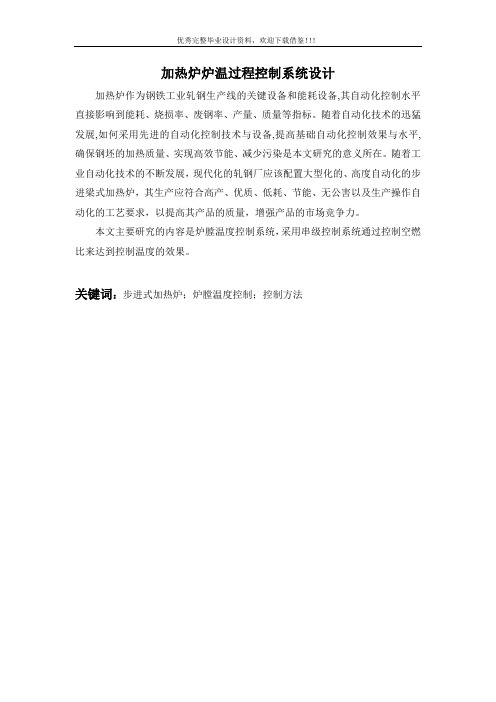
加热炉炉温过程控制系统设计加热炉作为钢铁工业轧钢生产线的关键设备和能耗设备,其自动化控制水平直接影响到能耗、烧损率、废钢率、产量、质量等指标。
随着自动化技术的迅猛发展,如何采用先进的自动化控制技术与设备,提高基础自动化控制效果与水平,确保钢坯的加热质量、实现高效节能、减少污染是本文研究的意义所在。
随着工业自动化技术的不断发展,现代化的轧钢厂应该配置大型化的、高度自动化的步进梁式加热炉,其生产应符合高产、优质、低耗、节能、无公害以及生产操作自动化的工艺要求,以提高其产品的质量,增强产品的市场竞争力。
本文主要研究的内容是炉膛温度控制系统,采用串级控制系统通过控制空燃比来达到控制温度的效果。
关键词:步进式加热炉;炉膛温度控制;控制方法第一章加热炉控制系统概述 ............................... 错误!未定义书签。
1.1步进式加热炉的发展和国内概况 ............. 错误!未定义书签。
1.2炉温控制基本原理 ..................................... 错误!未定义书签。
1.3 计算飞剪运行时间T ................................. 错误!未定义书签。
第二章控制系统具体方案设计 ........................... 错误!未定义书签。
2.1 飞剪的控制目标 ........................................ 错误!未定义书签。
2.2 飞剪计算 .................................................... 错误!未定义书签。
2.3 剪切过程存在问题 .................................... 错误!未定义书签。
第三章步进式加热炉过程控制方案的设计过程错误!未定义书签。
3.1 系统结构 .................................................... 错误!未定义书签。
毕业设计任务书(步进式加热炉)
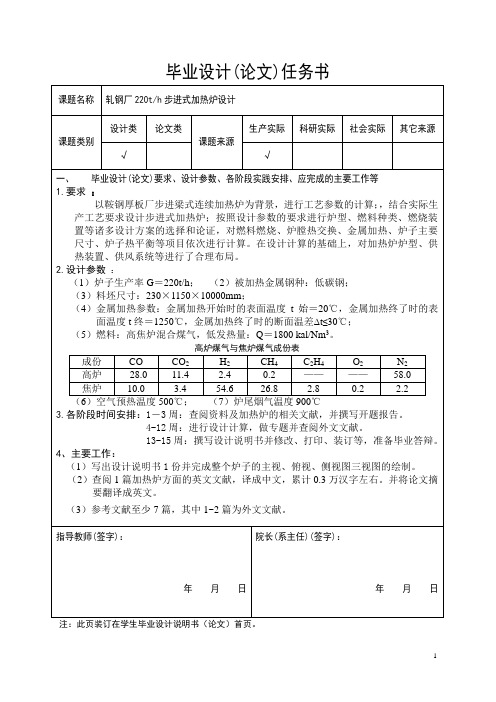
院长(系主任)(签字):
年月日
注:此页装订在学生毕业设计说明书(论文)首页。
13-15周:撰写设计说明书并修改、打印、装订等,准备毕业答辩。
4、主要工作:
(1)写出设计说明书1份并完成整个炉子的主视、俯视、侧视图三视图的绘制。
(2)查阅1篇加热炉方面的英文文献,译成中文,累计0.3万汉字左右。并将论文摘要翻译成英文。
(3)参考文献至少7篇,其中1~2篇为外文文献。
指导教师(签字):
毕业设计(论文)任务书
课题名称
轧钢厂220t/h步进式加热炉设计
课题类别
设计类
论文类
课题来源
生产实际
科研实际
社会实际
其它来源
√
√
一、毕业设计(论文)要求、设计参数、各阶段实践安排、应完成的主要工作等
1.要求:
以鞍钢厚板厂步进梁式连续加热炉为背景,进行工艺参数的计算;,结合实际生产工艺要求设计步进式加热炉;按照设计参数的要求进行炉型、燃料种类、燃烧装置等诸多设计方案的选择和论证,对燃料燃烧、炉膛热交换、金属加热、炉子主要尺寸、炉子热平衡等项目依次进行计算。在设计计算的基础上,对加热炉炉型、供热装置、供风系统等进行了合理布局。
2.设计参数:
(1)炉子生产率G=220t/h;(2)被加热金属钢种:低碳钢;
(3)料坯尺寸:230×1150×10000mm;
(4)金属加热参数:金属加热开始时的表面温度t始=20℃,金属加热终了时的表面温度t终=1250℃,金属加热终了时的断面温差∆t≤30℃;
(5)燃料:高焦炉混合煤气,低发热量:Q=1800 kal/Nm3。
高炉煤气与焦炉煤气成份表
成份
CO
CO2
步进梁式加热炉-机械工程系毕业设计说明书.doc

目录第一章概述 (2)1.1 步进梁式加热炉的简单介绍 (2)1.2设计的目的及意义 (2)第二章设计原始资料 (3)2.1 加热炉的产量 (3)2.2 钢坯尺寸 (3)2.3 燃烧原料成分 (3)第三章不锈钢步进梁式加热炉的计算 (4)3.1燃烧计算 (4)3.2炉内各段综合辐射系数 (7)3.3炉子尺寸的确定 (11)3.4热平衡计算 (18)设计体会 (22)参考文献 (24)第一章概述加热炉是将物料或工件加热的设备。
在冶金工业中加热炉习惯上是指把金属加热到轧制成锻造温度的工业炉,包括有连续加热炉和室式加热炉等。
连续加热炉广义来说,包括推钢式炉、步进式炉、转底式炉、分室式炉等连续加热炉。
连续加热炉按炉温分布,炉膛沿长度方向分为预热段、加热段和均热段;进料端炉温较低为预热段,其作用在于利用炉气热量,以提高炉子的热效率。
加热段为主要供热段,炉气温度较高,以利于实现快速加热。
均热段位于出料端,炉气温度与金属料温度差别很小,保证出炉料坯的断面温度均匀。
由于本设计的内容是关于步进梁式加热炉,所以要对其做一些简单的介绍。
1.1 步进梁式加热炉的简单介绍步进式连续加热炉靠炉底或水冷金属梁的上升、前进、下降、后退的动作把料坯一步一步地移送前进的连续加热炉。
炉子有固定炉底和步进炉底,或者有固定梁和步进梁。
前者叫做步进底式炉,后者叫做步进梁式炉。
轧钢用加热炉的步进梁通常由水冷管组成。
步进梁式炉可对料坯实现上下双面加热。
70年代以来,由于轧机的大型化,步进梁式炉得到了广泛应用。
同推钢式炉相比,它的优点是:运料灵活,必要时可将炉料全部排出炉外;料坯在炉底或梁上有间隔地摆开,可较快地均匀加热;完全消除了推钢式炉的拱钢和粘钢故障,因而使炉的长度不受这些因素的限制。
1.2 设计的目的及意义通过课程设计,系统地总结巩固运用所学的加热炉及热工基础知识,掌握加热炉设计的基本方法、加热炉的基本结构。
培养理论联系实际,训练分析和解决问题的能力。
步进式加热炉汽化冷却系统设计说明-设计院
首钢迁钢2#热轧工程步进梁式加热炉汽化冷却系统设计说明1、汽化冷却系统的设计概述1.1汽化冷却系统的冷却效果取决于汽化水的热量吸收。
对于步进梁式加热炉,汽化冷却系统设计为强制循环系统。
系统产生的饱和蒸汽进入车间蒸汽管网,或者在紧急情况下排入大气。
1.2循环系统的主要设备如下:——炉底水梁及立柱——汽包——循环水泵(共3台)——旋转接头组给水供应系统主要设备如下:——电动给水泵——除氧器——除盐水箱——电动除盐水泵——柴油机给水泵——加药装置加热炉炉底水梁,其外表面包扎有耐高温的保温层。
活动梁:4根;固定梁:4根;每根固定梁分为3段;每根活动梁分为3段;另外,在均热段设两根单独固定梁,各自并联进相邻的固定梁;梁的编号为:活动梁(串联结构):2#、4#、5#、7#;固定梁(串联结构):1#、8#;固定梁(串并联结构):3#、6#。
每段梁均由一根双水平管和若干立柱组成,其中一根立柱为双管立柱,是支撑梁冷却水进水和出水的接管;其它为采用带有芯管的单管立柱。
1.3主要运行参数汽包设计工作压力:0.8—1.3MPa(g)工作温度:对应压力下的饱和温度蒸发量:13.0t/h(保温完好,10%排污率时)对应给水量:14.3 m3/h蒸发量:16t/h(10%保温脱落,10%排污率时)对应给水量:17.6 m3/h蒸发量:25t/h(40%保温脱落,10%排污率时)对应给水量:27.5m3/h给水温度:102~104℃系统总循环水量:700—600 m3/h以上参数参见X5212R1以及X5212ZK5。
2、汽化冷却系统的工作原理2.1.循环冷却回路内部冷却回路是指如下的回路:在正常工作时,汽包中的水位保持在汽包中心线以上100mm;由于本工程汽化冷却产汽送入厂区蒸汽管网,因此汽包运行压力根据管网压力确定,目前汽包工作压力确定为1.0—1.1MPa(g)。
冷却水通过汽包下降管、循环水泵、冷却水管总管,分配联箱,进入加热炉支撑水梁。
过程控制系统课程设计---步进式加热炉系统控制
课程设计课程设计名称:步进式加热炉系统控制 2013 年 12 月至2014 年 1 月目录一、实验任务二、实验要求三、步进式加热炉简介四、过程控制中仪表的选择五、步进式加热炉控制方案1、煤气/空气流量控制方案2、炉温控制方案3、炉压控制方案六、加热炉控制系统的硬件设计七、加热炉控制系统的PLC软件设计八、实验感受附录1(PLC梯形图)附录2(力控监控组态软件)我的任务:综合步进式加热炉的炉温、炉压控制系统的控制方案,以及PLC的编程和力控监控组态界面的设计。
正文一、实验任务以钢铁企业常见的“步进梁式加热炉”为对象,采用PLC为控制系统硬件,围绕工艺要求,完成控制系统方案设计。
二、实验要求(1)通过查阅文献,了解步进式加热炉工艺流程。
(2)了解对步进式加热炉的炉温控制、煤气/空气流量控制、炉压控制等功能,完成控制方案设计。
(3)了解常见的PLC系统的功能、系统软件及应用,完成加热炉自动控制系统架构设计、硬件选择设计及组态画面设计。
三、步进式加热炉简介1、步进式加热炉概述加热炉作为轧钢生产线上的主要能耗设备,其出炉钢坯的温度是钢铁生产工艺的首要指标,温度控制的好坏直接影响到下层产品的质量,并逐步影响到钢材的质量,还有可能会影响到生产线的其他相关行业,严重情况下可能会破坏整个轧钢生产线的正常运行。
因此,加热炉作为轧钢生产线上的重要环节,担负着为轧制工序提供质量合格钢坯的任务。
加热炉的作用是将钢坯加热后送往轧机进行轧制,其中加热炉能耗占冶金能耗的25%,因此,提高加热炉的热效率,对整个冶金行业的节能降耗具有重要意义。
为了保证钢坯在加热炉中均匀受热,必须调节钢坯的入炉参数、工艺指标及生产状况,因此要求的方面有:炉温、空气流量及压力、煤气流量及压力、空燃比、炉膛压力等。
通过控制上述量从而达到减少氧化损耗、降低能源损失。
步进式加热炉通过步进梁的“步进”运动,将钢坯从装料侧移至出料侧,通过钢坯在炉内的“步进”运动,从而完成从低温段到高温段,最后进入均热段的加热过程,从而达到轧钢所要求的轧制温度。
过程控制系统课程设计--步进式加热炉控制系统设计
步进式加热炉控制系统设计一、步进式加热炉工艺流程⒈步进式加热炉简介⑴步进式加热炉步进式加热炉是一种靠炉底或水冷金属梁的上升、前进、下降、后退的动作把料坯一步一步地移送前进的连续加热炉。
炉子有固定炉底和步进炉底,或者有固定梁和步进梁。
前者叫做步进底式炉,后者叫做步进梁式炉。
轧钢用加热炉的步进梁通常由水冷管组成。
步进梁式炉可对料坯实现上下双面加热。
(2)步进式炉的几种类型步进式炉从炉子构造上分目前有:单面供热步进式炉、两面供热步进式炉、钢料可以翻转的步进式炉、交替步进式炉、炉底分段的步进式炉等等。
单面供热步进式炉也称步进底式炉,钢料放置在耐火材料炉底或铺设在炉底上的钢枕上。
钢坯吸热主要来自上部炉膛,由于一面受热,这种炉子的炉底强度较低。
它适用于加热薄板坯、小断面方坯或有特殊要求的场合。
两面供热步进式炉也称步进梁式炉,活动梁和固定梁上都安设有能将钢坏架空的炉底水管。
在钢坯的上部炉膛和下部炉膛都设置烧嘴,因此炉底强度较高,适用于产量很高的板坯或带钢轧前加热。
钢坯可以翻转的步进式炉是每走一步炉内钢料可以翻转某一角度,步进梁和固定梁都带有锯齿形耐热钢钢枕,这是加热钢管的步进式炉,每走一步钢管可以在锯齿形钢枕上滚动一小段距离,使受热条件较差的底面逐步翻转到上面,以求加热均匀。
交替步进式炉则有两套步进机构交替动作。
运送过程中,钢坯不必上升和下降,振动较小,底面不会被划伤,表面质量较好。
炉底分段的步进式炉的加热段和预热段可以分开动作。
例如预热段每走一步,加热段可以走两步或两步以上。
这种构造是专门为易脱碳钢的加热而设计的。
钢坯在预热段放置较密,可以得到正常的预热作用,在加热段钢坯前进较快,达到快速加热,以减少脱碳。
(3)步进式炉的优缺点步进式炉是借机械将炉内钢坯托着一步一步前进,因此钢坯与钢坯还不必紧挨着,其间距可根据需要加以改变。
原始的步进式炉只用于加热推钢机无法推进的落板坯或异形坯,随着轧机的大型化和连续化,推钢式炉已不能满足轧机产量和质量的要求。
加热炉课程设计.doc
第一章设计原始条件及表格汇总1.1原始条件炉子产量140000kg G h =,钢坯规格为22022012000mm ⨯⨯,单重为4530㎏,加热温度201250C C ,许加热终了时钢坯断面温度差30C ,钢种为普碳钢。
用发热量为2150千卡/时的高焦炉煤气为燃料。
确定炉子的尺寸和燃料消耗量。
1.2计算结果表格汇总1. 燃烧计算kcal kcalkcal5.热平衡计算及燃料消耗量的决定第二章设计计算2.1炉子结构计算2.1.1空气量及燃烧生成量计算解:采用上下加热步进梁式加热炉,钢坯中心距取320mm ,炉宽定为12800mm 。
按三段式温度制度。
炉膛高度在预热段为1800mm ,加热段为2200mm ,均热锻为1500mm 。
用平焰烧嘴, 1.1α=。
高焦炉煤气的成分:完全燃烧时理论空气量 024 4.84(0.520.5 3.5)100m n L H CH CO C H =+++4.84(0.50.09297.10.50.01 3.50.54)100=⨯+⨯+⨯+⨯⨯ 2.12=过量空气系数 1.1α=实际供给空气量 0 1.1 2.02 1.122n L L α=⨯=⨯=烟气生成量 2221.9n c o N O V V V V =++=烟气中生成量 224(2)0.010.288CO m n V CO CO CH C H =+++⨯=烟气中生成量 22(78)0.012.183N n V N L =+⨯= 烟气中生成量烟气中生成量 24222(230.0128)0.010.484H O m n n V CH C H H H S H OL =+++++⨯=烟气中生成量 200.2067(1)0.2O V L α=-=由以上得: 20.048CO P = 20.17H O P = 2.1.2炉高的确定钢坯出炉的表面温度=1250C钢坯入炉的表面温度=20C经过预热段以后钢坯的表面温度=650C进入均热锻时钢坯的表面温度=1350C烟气出炉的温度=850C烟气进入预热段的温度=1400C烟气在均热中的最高温度=1350C烟气在均热锻中的平均温度=1275CH 效=3(0.05)10A B t +⨯气 H 效—炉子的有效长度B —炉宽t 气—炉气温度A —系数(1)预热段高度311(0.50.0512.8)14001015961796H H mm δ=+⨯⨯⨯=+=取 1800mm (2)加热段3322(0.05)10(0.680.0512.8)145010191419142002214H A B t mm H δ=+⨯=+⨯⨯⨯=+=+=气取 2200mm (3)均热锻333(0.05)10(0.50.0512.8)1275101453.5H A B t mm =+⨯=+⨯⨯⨯=气取1500mm2.1.3、炉内各段面积 1.炉膛的内表面积2()y F H B L =+(1)预热段2()2(1.812.8)29.2y y y y F H B L L L =+=⨯+=(2)加热段2()2(2.212.8)30.0j j j j F H B L L L =+=⨯+=(3)均热锻2()2(1.512.8)28.6jr jr jr jr F H B L L L =+=⨯+=2.气层的有效厚度1( 3.6)HBLS F = (1)预热段1.812.83.62.8429.2yy yL S m L ⨯==(2)加热段2.212.83.63.3830.0jj jL S m L ⨯==(3)均热锻1.512.83.62.4228.6jrjr jrL S m L ⨯==2.1.4炉气黑度 220CO H O e e e β=+ 预热段20.12 2.840.341CO y P S =⨯= 20.16 2.840.454H O y P S =⨯=加热段20.12 3.380.4056CO j P S =⨯= 20.16 3.380.5408H O j P S =⨯=均热锻20.12 2.420.2904CO jr P S =⨯= 20.16 2.420.3872H O jr P S =⨯=预热段温度800C 00.15 1.080.250.42e =+⨯=预热段温度1280C 00.141.080.1560.308e =+⨯= 加热段温度1280C 00.141.080.210.363e =+⨯= 加热段温度1330C 00.13 1.080.190.33e =+⨯=均热锻温度1330C 00.121.080.170.31e =+⨯= 均热锻温度1270C 00.141.080.180.336e =+⨯=2.1.5综合辐射系数()0201201204.881e e c e r e =+-砌体对钢坯的角度系数 预热段()1210.819F a r F +==金壁( 取0.45α=) 加热锻()1210.80F a r F +==金壁( 取 0.45α=) 均热锻()1210.837F a r F +==金壁( 取 0.45α=)钢坯黑度20.8e = 预热段温度800C()012 4.880.420.81.830.420.81910.42C ⨯⨯==+-预热段温度1280C()012 4.880.3080.81.370.3080.81910.308C ⨯⨯==+-加热段温度 1280C()012 4.880.3630.81.620.3630.8010.0.363C ⨯⨯==+-加热段温度 1330C()012 4.880.330.81.490.330.8010.33C ⨯⨯==+-均热锻温度 1330C()012 4.880.310.81.360.310.83710.31C ⨯⨯==+-均热锻温度 1270C()012 4.880.3360.81.430.3360.83710.336C ⨯⨯==+-预热段和加热段交界处取平均值0120.5(1.37 1.62) 1.49C =+=加热段和均热锻交界处取平均值0120.5(1.49 1.36) 1.43C =+=2.1.6炉长炉宽的确定 最大生产率: 220000kg G h = 预选炉底强度: 395P =2kg m h⋅加热面积:2220000557395xi G f m P ===又12.81xi xi f l =⨯⨯ 有55743.612.8xi f m == 有效长度44m =炉宽的确定:B =钢坯的长度2C + 即有1220.412.8B m =+⨯= 取 12.8m 求炉长及加热时间要求每小时加热的钢坯的钢坯数为30.9根,炉内放置的钢坯数为44000320137=根,则钢坯加热的时间131730.9 4.43t h == 2.1.7计算炉温制度和燃料消耗量将方坯看成截面积与之相等的圆坯,则圆坯的计算半径:0.1242r m ==在加热段完了时钢坯的温差为20C ,则加热段终了时钢坯的平均温度为:12500.5201240z jp t C =-⨯=。
- 1、下载文档前请自行甄别文档内容的完整性,平台不提供额外的编辑、内容补充、找答案等附加服务。
- 2、"仅部分预览"的文档,不可在线预览部分如存在完整性等问题,可反馈申请退款(可完整预览的文档不适用该条件!)。
- 3、如文档侵犯您的权益,请联系客服反馈,我们会尽快为您处理(人工客服工作时间:9:00-18:30)。
210步进式加热炉设计计算2.1 热工计算原始数据(1) 炉子生产率:p=245t/h (2) 被加热金属:1) 种类:优质碳素结构钢(20#钢)2) 尺寸:250 >2200 >3600 (mm )(板坯) 3) 金属开始加热(入炉)温度:t 始=20r 4) 金属加热终了(出炉)表面温度:t 终=1200C 5) 金属加热终了(出炉)断面温差:t < 15C (3) 燃料1) 种类:焦炉煤气2) 焦炉煤气低发热值:Q 低温=17000kJ/标m 3 3) 煤气不预热:t 煤气=20 °C表1-1焦炉煤气干成分(%)⑷ 出炉膛烟气温度:t 废膛=800C⑸空气预热温度(烧嘴前):t空=350 C2.2燃烧计算2.2.3 计算理论空气需要量L c1 1m L o 4.76 —CO -H 2 (n —)C n H m2 24把表2-1中焦炉煤气湿成分代入1 1333-H 2S O 2 2233)10 (m /m )L0 4.76 8.7939 険5741 2 24・8184 3 2・8336。
碍210 =4.3045m3/m3V n V CO 2 V H 2O V N 2 V O 2224计算实际空气需要量Ln查《燃料及燃烧》,取n=1.1代入L nnL o1.1 4.3045 4.7317 标 m 3/标 m 3实际湿空气消耗量L n 湿(10.00124g) nL o=(1 0.00124 18.9) 4.7317=6.0999 标 m 3/标 m 32.2.5计算燃烧产物成分及生成量V c°2(COnC n H m CO 2) 1001791.2702 丄 79 4.7317100 100=3.7507标m 3/标m 3V 02(L nL 0)标 m /标 m100 214.7317 4.3045 100=0.0897 标 m 3/标 m 3 燃烧产物生成总量(56.5741 2 1 24.8184 2 2.8336 2.2899) 1000.00124 18.9 4.7317标m 3/标m 3标m 3/标m 3(24.8184 8.7939 2 2.83363.0290)1 100=0.4231 标 m 3/标 m 3V H 2O (H 2m C Hn m2H 2S H 2O)1 1000.00124gL n 标 m 3/标 m 3V N 2N 2100 100 Ln 标说标m=1.25260.4231 1.2526 3.7507 0.0897 5.5161 标 m 3/标 m 3燃烧产物成分V Co i100% 6.145%V n 5.5161V H O 1 2526 上上空6100% 19.132% V n 5.5161 皿 37507100% 72.977% V n5.5161O 2 纟 00897100% 1.746%V n 5.5161100%将燃烧产物生成量及成分列于下表表2-2焦炉煤气燃烧产物生成量(标 m 3/标m 3)及成分(%)成 4名称7^CO 2 H 2O N 2 O 2 合计生成量(标m 3) 0.4231 1.2526 3.7507 0.0897 5.5161体积含量(%)7.6703 22.7081 67.99551.6261100按燃烧产物质量计算把表2-2中燃烧产物体积百分含量代入44CO 2 64SO 218H 2O 28N 232O 2100 22.444 7.6703 18 22.7081 28 67.9955 32 1.6261100 22.4=1.2063Kg/m 32.2.7计算燃料理论燃烧温度由t 空=350 C ,查《燃料与燃烧》表得 C 空=1.30kJ/标m 3,由《燃料与燃烧》P as ,Kg/m 3V n C 产Q 低L n C 空t 空C 燃 t 燃Q 分得燃烧室(或炉膛)内的气体平衡压力接近1个大气压(大多数工业炉如此),那么式中各组分的分压将在数值上与各组分的成分相等)即P CO2 CO2 %P CO CO %所以P CO2 7.6703% ,P H2O 22.7081%由《燃料与燃烧》附表8,附表9,得f co219.81% , f H2o 4.938%所以Q分12600 f co2(V co2)未10800 f H2o(V H2o)未10800 4.938% 0.227081 12600 0.076703% 0.1981140.2487KJ / Kg Kt 17790.4993 2152.9335 140.2487 所以理 5.5161 1.672149.7413 C2150误差% 2150 2100 100% 2.38% 5%2100在误差范围内,故不必再假设。
因此,可满足步进式加热炉加热工艺要求2.3 炉膛热交换计算2.4金属加热计算金属加热计算是连续加热炉全部热工计算的核心。
按炉子有效长度分成三个区段(即预热段、加热段、均热段)分别进行计算。
计算方法简述如下:预热段和加热段采用热流等于常数的边界条件求解。
均热段计算有两种方法①根 据经验直接确定均热段实底段长度。
②选定均热度求均热时间。
后一种方法用于均热 床架空的时候,它与实际情况相差很大,应根据经验修正。
241 均热段该金属加热开始时,断面温度呈抛物线分布(《设计手册下》,P89),取出炉时, 钢的断面温差为10C ,采用抛物线的理想平均值求法。
加热终了时,钢坯的平均温度—— 2 2 t g1 & t 120010 1193.33o C33在此温度下,钢的导热系数29.73 3.6 107.04kJ/ m h °C前面假设温度为1250C ,误差为故不必再重新假设求热焓在 1193C 时,Cp=0.68716kJ/(kg 「C ) 热焓 i= Cp*t=1193.33*0.68716=820.0109 kJ/kg求热流密度2 t q S式中: s —钢材厚度(m ),对于双面加热,厚度取丄S , 2q 表12 t 2 107.°4 101712.64KJ/(m 2 h)1250 1201.4612503.88% V 5%均热段炉气温度273=1201.46 CgKM 均t g1 100242加热段设加热段加热终了时,金属断面温差 t =50C(1) 钢坯平均温度_ 2 2 t g2 t 表t 120050 1167o C3 3(2) 加热段末端钢坯表面热流查设计手册,在 1167C 时, 29.47 3.6 106.08kJ/t g2 1004yC gKM 加 “c 4 '84864 100 4----------V 10.20J 表终 273 )4273 1001261.64 C与前面假设炉气温度1300r 仅相差20 c1300 1261.64误差 %2.95% v 5%1300故不必再假设。
(4) 均热度式中: 一均热度t k —金属均热开始时的表面与中心温度差 t z —金属均热终了时的表面与中心温度差查《钢铁厂工业炉设计参考资料》 P288,图8—25,(3)2 t 2 106.08 50q表20.12584864 KJ /(m 2 h)加热段炉气温度对于大平板: =0.2时,a S 20.68m h o C(12°° 273)4273100 因为& 10 r t k 50c0.2立__t kS 2所以1S2a20.68 0.1252/0.021 0.506h(5)加热段内钢坯热焓加热段内钢坯平均温度1167C,查表Cp=0.6894 kJ/(kg 「C )i加1167 C 0.6894 804.497KJ/Kg2.4.3燃料利用系数及钢坯热焓分配(1)加热段燃料利用系数Q烧Q预Q废加Q低L n C空V n C废加T废加4加•Q烧Q预Q低L n C空T空式中:Q低17790.49993KJ /m3,L n 4.7317m3/m3,t空350°C,c空1.296kJ/m3,V n 5.5161m3/m3,t 废1300°C,c a1.61656kJ / m3gD 代入得Q低L n C空T空V n C废加T废加Q低L n C空T空17790.4993 4.7317 1.296 350 5.5161 1.61656 130017790.4993 4.7317 1.296 350=0.42(2)炉膛燃料利用系数Q烧Q预Q废膛Q烧Q预本设计中Q预只预热助燃空气,所以上式可以写为Q低L n C空T空V n C废膛T废膛Q低L n C空T空17790.4993 4。
317 1.296 350 5.5161 1.53356 80017790.4993 4.7317 1.296 350=0.6606(3)金属在炉膛中的总热焓增量i i终i始t均1 C p 1193 0.68716 820.0109kJ /kg(4)金属在预热段的热焓增量式中:Q 辐q F ,加热段向预热段辐射热量; q—辐射热流,一般q=10000旷130000千卡/m3,这里取q=110000千卡/m3; F —界面面积;式中: C gkM 加 加热段导来辐射系数,C gkM 加=10.20 kJ / m h k t g2 —加热段炉气温度,t g2 =1261.64 CF=B(H 预 2S )8.12 (1 0.25)6.075m 3i 3820.0109(1 0.42 )110000 6.0750.6606” 245000301.39kJ/kg(5)求金属平均温度设t 均3=550C ,查《火焰炉设计计算参考资料》表 3-3得,C P =0.5736 kJ/(kg「C )则t 均3i 预 301.39 C P0.5736% 550 525.4358550设计值与计算值相差很小,因此不必重算2.4.4预热段热流及加热时间(1)预热段始端热流(/t 废膛273、4 q 3C gkM 预g100/800 273、4 9.657 [ 4 100 127472.78kJ/(m 2(2)预热段末端热流(t表0273)4100(273)4100)q 表 3 C gkM 加4t g2 273100 h ) 273q 表3S100525.4358 C100% 4.47% 5%4S —热透深度,S=0.125m查《火焰炉设计计算参考资料》表 3-1得,t 均3=525.4358 C 时,3.6 38.5 138.6kJ/(m h C)(525.4358 273),1261.64 273,3 138 6 q 表 3 10.20()43 138.6100 100对上式采用顺序渐进法求解:K 1 —金属形状系数;平板K 1 1,圆柱K 1 2,球体K 1 30.125q表 30.1q 表 3首先令总1詁0,代入上式得0.125q 表 3 157.62138.6反复迭代,得q表3 1480533.82kJ/(m 2h ),0.125q 表3 1 144.463 138.60.125q 表3 2q表3 2 485129.91kJ/(m 2h )145.843 138.6q表3 3484656.88kJ / (m 2h )0.125q 表3 3 145.73 138.6这里取 q 表3 484656.88kJ/( m 2 h )q 表3S525.4358484656・88 °125671.14 C 3 138.6(4) 预热段内平均热流4q 均预qq 表312747278 464656.88248556.951kJ/(m 2 h )(5) 预热段内加热时间式中: 524298.77kJ/(m 2 h )3 计算金属表面温度(3) q表3i预i预i0714 C 0.63976 456.79kJ/kg42.4.5加热段内热流及加热时间(1) 加热段热流q 2平均热流的计算,通常预热段采用几何平均值,加热段采用对数平均值q 均加q 表3 q 表 2 484656.88 84864 229450.86KJ/(m 2 h).q 表3 Inq 表2,484656.88 In84864(2)加热时间i加i加i 预 804.497 525.4358 0.5673506.42KJ / Kgi 加S506.42 0.125 7863力口2.169hK 1q均加229450.86综上所述:预1.18h加2.169 h均0.506h总加热时间:总 均加预3.855h注:由于步进梁式加热炉料坯之间有间隙,受热面增大,加热时间有所缩短,但单位面积上料坯数量减少了,故它对生产率的影响 ,应综合考虑,修正加热时间:炉膛(既间隙开口)对间隙内炉底的角度系数式中:s —料坯厚度; a—间隙宽;取间隙a 约为料坯厚度的0.4〜0.5倍,a=0.4 250mm=100mmi 预 S 301.39 0.125 7863 K i q 均预248556951.18hq均加q 3 q 2所以:1 ( )2 —0.1926¥ a a因为,在假定金属黑度& =1的条件下,分析间隙内料坯侧面与炉膛及间隙内炉底 之间的辐射热交换,可以导出有间隙和无间隙两种条件下的金属获得热量比 ,它的倒数即为有间隙和无间隙的加热时间比;1t2a1 (1 2)-b式中: n t —相对加热时间,即有间隙和无间隙的加热时间之比; a,b, 分别为间隙宽,料坯宽度,料坯厚度;0.9582100 1 (1 0.1926 )1000各段加热时间为:2.5炉子主要尺寸确定2.5.1长度计算(1)有效长度L 效P b ng式中:P —炉子生产P=245t/h b —料坯宽度;b=2200mmg —料坯平均单重所以:均 0.506 0.958 0.4847h 加2.169 0.958 2.0779h 预1.180.958 1.1304h总均 加 预3.69hP b245000 3.69 2200(2) 预热段长度(3) 加热段长度L 加 L 效』63875216937546mm总3.69(4) 均热段长度L 均 L 效 —63875 0.48758439mm总3.692.5.2炉门数量和尺寸及炉膛各部分用耐火材料的确定(1)连续式加热炉炉门有进料炉门,出料炉门,操作炉门,窥视炉门,人孔等;这些炉门 数量和尺寸的确定总的原则是:在满足操作要求的条件下,炉门数量越少,开门尺寸越 小越好,这样可以减少炉门的散热损失,提高炉子的热效率.主要炉门的确定如下: (a) 装料门:炉门宽度B 进:连续步进梁式加热炉通常都是采用端进料,其宽度等于炉膛内宽 B,即 B 进=B=8.12m炉门高度H 进:是指步进炉固定梁上表面至炉门上沿下表面之间的距离 ,对于步进炉可取大于料坯(方坯或板坯)厚度与步进高度之和.这里取250mm+200mm=400mm; (b) 出料门:炉门宽度B:若采用侧出料时,则需很大炉门,且容易卡钢,结构和操作上都很困 难.从尺寸上考虑,因板坯教宽,故多用端出料.其宽度等于炉膛内宽 B=8.12m,由于出 料端温度很高,所以出料门带有水冷管.炉门高度H 进:同装料门一样. (c) 操作炉门:ng 2 (3.6 2.2 0.25 7863)63875mm1.13043.6919568mm63875P b 245000 3.69 2200用做操作之用,如进出返回钢坯,清除氧化铁皮等。