SMT生产工艺中产生锡珠的原因分析及防控措施
回流焊产生锡珠的原因及解决方案

回流焊产生锡珠的原因及解决方案在SMT生产工艺里面,经常会碰到经过回流焊过出来的板有锡珠,锡珠的产生,让产品的质量没有保证,让外观看起来不光滑。
那产生锡珠的主要原因是什么,我们又如何去解决它,这就是我今天写这篇文章的目的。
产生锡珠的主要原因是锡膏的问题。
详细分析请看下面分析。
焊锡珠现象是表面贴装生产中主要缺陷之一,它的直径约为0.2-0.4mm,主要集中出现在片状阻容元件的某一侧面,不仅影响板级产品的外观,更为严重的是由于印刷板上元件密集,在使用过程中它会造成短路现象,从而影响电子产品的质量。
因此弄清它产生的原因,并力求对其进行最有效的控制就显得犹为重要了。
焊锡珠产生的原因是多种因素造成的,在回流焊中的温度时间,焊膏的印刷厚度,焊膏的组成成分,模板的制作,贴片机贴装压力,外界环境都会在生产过程中各个环节对焊锡珠形成产生影响。
焊锡珠是在负责制板通过回流焊炉时产生的。
回流焊曲线可以分为四个阶段,分别为:预热、保温、回流和冷却。
预热阶段的主要目的是为了使印制板和上面的表贴元件升温到120-150度之间,这样可以除去焊膏中易挥发的溶剂,减少对元件的热振动。
因此,在这一过程中焊膏内部会发生气化现象,这时如果焊膏中金属粉末之间的粘结力小于气化产生的力,就会有少量焊膏从焊盘上流离开,有的则躲到片状阻容元件下面,再流焊阶段,温度接近曲线的峰值时,这部分焊膏也会熔化,而后从片状阻容元件下面挤出,形成焊锡珠,由它的形成过程可见,预热温度越高,预热速度越快,就会加大气化现象中飞溅,也就越容易形成锡珠。
因此,我们可以采取较适中的预热温度和预热速度来控制焊锡珠的形成。
焊膏的选用也影响着焊接质量,焊膏中金属的含量,回流焊焊膏的氧化物含量,焊膏中金属粉末的粒度,及焊膏在印制板上的印刷厚度都不同程度影响着焊锡珠的形成。
1:焊膏中的金属含量:焊膏中金属含量的质量比约为90-91%,体积比约为50%左右。
当金属含量增加时,焊膏的粘度增加,就能更有效地抵抗预热过程中气化产生的力。
浅析SMT组装中锡珠的产生原理及预防措施

浅析SMT组装中锡珠的产生原理及预防措施焊锡珠(SOLDER BALL)现象是表面贴装(SMT)过程中的重要缺陷,主要发生在片式阻容组件(CHIP)的周围,由诸多因素引起。
焊锡珠的存在,不仅影响了电子产品的外观,也对产品的质量埋下了隐患。
本文为大家简单解析一下锡珠的形成原理及应对方法。
一、焊球的分类根据锡珠的发生个数和大小,可以分为4种情况。
单个焊粉的情况下,直径为10~40µm,如果大小有50µm以上,则认为是多个焊粉融合。
二、助焊剂内锡珠形成原理・加热时锡膏坍塌在加热时锡膏出现坍塌,但并不是完全连接两焊盘(见0.1m m位置),而是在绿油桥中形成薄薄的锡珠(见0.2m m位置)。
・助焊剂流出随着溶融时助焊剂流出,较迟溶解的焊粉流出。
三、常见锡珠形成原因①回流焊温度曲线设置不当;②助焊剂未能发挥作用;③模板的开孔过大或变形严重;④贴片时放置压力过大;⑤焊膏中含有水分;⑥印制板清洗不干净,使焊膏残留于印制板表面及通孔中;⑦采用非接触式印刷或印刷压力过大;⑧焊剂失效。
四、常见防止锡珠产生方法PC B线路板上的阻焊层是影响锡珠形成最重要的一个因素。
在大多数情况下,选择适当的阻焊层能避免锡珠的产生。
使用一些特殊设计的助焊剂能帮助避免锡珠的形成。
另外,要保证使用足够多的助焊剂,这样在PC B线路板离开波峰的时候,会有一些助焊剂残留在PC B线路板上,形成一层非常薄的膜,以防止锡珠附着在PC B线路板上。
同时,助焊剂必须和阻焊层相兼容,助焊剂的喷涂必须采用助焊剂喷雾系统严格控制。
1、尽可能地降低焊锡温度;2、使用更多的助焊剂可以减少锡珠,但将导致更多的助焊剂残留;3、尽可能提高预热温度,但要遵循助焊剂预热参数,否则助焊剂的活化期太短;4、更快的传送带速度也能减少锡珠。
锡珠产生的原因分析
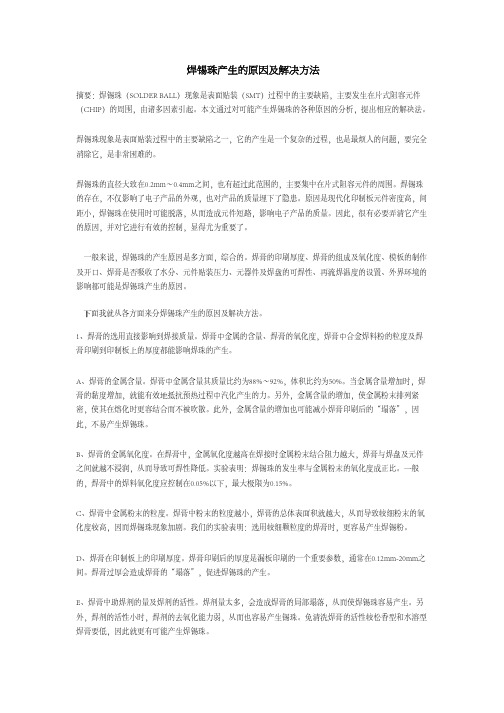
焊锡珠产生的原因及解决方法摘要:焊锡珠(SOLDER BALL)现象是表面贴装(SMT)过程中的主要缺陷,主要发生在片式阻容元件(CHIP)的周围,由诸多因素引起。
本文通过对可能产生焊锡珠的各种原因的分析,提出相应的解决法。
焊锡珠现象是表面贴装过程中的主要缺陷之一,它的产生是一个复杂的过程,也是最烦人的问题,要完全消除它,是非常困难的。
焊锡珠的直径大致在0.2mm~0.4mm之间,也有超过此范围的,主要集中在片式阻容元件的周围。
焊锡珠的存在,不仅影响了电子产品的外观,也对产品的质量埋下了隐患。
原因是现代化印制板元件密度高,间距小,焊锡珠在使用时可能脱落,从而造成元件短路,影响电子产品的质量。
因此,很有必要弄清它产生的原因,并对它进行有效的控制,显得尤为重要了。
一般来说,焊锡珠的产生原因是多方面,综合的。
焊膏的印刷厚度、焊膏的组成及氧化度、模板的制作及开口、焊膏是否吸收了水分、元件贴装压力、元器件及焊盘的可焊性、再流焊温度的设置、外界环境的影响都可能是焊锡珠产生的原因。
㆘面我就从各方面来分焊锡珠产生的原因及解决方法。
1、焊膏的选用直接影响到焊接质量。
焊膏中金属的含量、焊膏的氧化度,焊膏中合金焊料粉的粒度及焊膏印刷到印制板上的厚度都能影响焊珠的产生。
A、焊膏的金属含量。
焊膏中金属含量其质量比约为88%~92%,体积比约为50%。
当金属含量增加时,焊膏的黏度增加,就能有效地抵抗预热过程中汽化产生的力。
另外,金属含量的增加,使金属粉末排列紧密,使其在熔化时更容结合而不被吹散。
此外,金属含量的增加也可能减小焊膏印刷后的“塌落”,因此,不易产生焊锡珠。
B、焊膏的金属氧化度。
在焊膏中,金属氧化度越高在焊接时金属粉末结合阻力越大,焊膏与焊盘及元件之间就越不浸润,从而导致可焊性降低。
实验表明:焊锡珠的发生率与金属粉末的氧化度成正比。
一般的,焊膏中的焊料氧化度应控制在0.05%以下,最大极限为0.15%。
C、焊膏中金属粉末的粒度。
锡珠产生的原因及解决方法

锡珠产生的原因及解决方法(总2页)-CAL-FENGHAI.-(YICAI)-Company One1-CAL-本页仅作为文档封面,使用请直接删除焊锡珠产生的原因及解决方法摘要:焊锡珠(SOLDER BALL)现象是表面贴装(SMT)过程中的主要缺陷,主要发生在片式阻容组件(CHIP)的周围,由诸多因素引起。
本文通过对可能产生焊锡珠的各种原因的分析,提出相应的解决方法。
焊锡珠现象是表面贴装过程中的主要缺陷之一,它的产生是一个复杂的过程,也是最烦人的问题,要完全消除它,是非常困难的。
焊锡珠的直径大致在0.2mm~0.4mm 之间,也有超过此范围的,主要集中在片式阻容组件的周围。
焊锡珠的存在,不仅影响了电子产品的外观,也对产品的质量埋下了隐患。
原因是现代化印制板组件密度高,间距小,焊锡珠在使用时可能脱落,从而造成组件短路,影响电子产品的质量。
因此,很有必要弄清它产生的原因,并对它进行有效的控制,显得尤为重要了。
一般来说,焊锡珠的产生原因是多方面,综合的。
焊膏的印刷厚度、焊膏的组成及氧化度、模板的制作及开口、焊膏是否吸收了水分、组件贴装压力、元器件及焊盘的可焊性、再流焊温度的设置、外界环境的影响都可能是焊锡珠产生的原因。
下面我就从各方面来分焊锡珠产生的原因及解决方法。
1、焊膏的选用直接影响到焊接质量。
焊膏中金属的含量、焊膏的氧化度,焊膏中合金焊料粉的粒度及焊膏印刷到印制板上的厚度都能影响焊珠的产生。
A、焊膏的金属含量。
焊膏中金属含量其质量比约为88%~92%,体积比约为50%。
当金属含量增加时,焊膏的黏度增加,就能有效地抵抗预热过程中汽化产生的力。
另外,金属含量的增加,使金属粉末排列紧密,使其在熔化时更容结合而不被吹散。
此外,金属含量的增加也可能减小焊膏印刷后的“塌落”,因此,不易产生焊锡珠。
B、焊膏的金属氧化度。
在焊膏中,金属氧化度越高在焊接时金属粉末结合阻力越大,焊膏与焊盘及组件之间就越不浸润,从而导致可焊性降低。
锡珠的产生原因及解决方法

锡珠的产生原因及解决方法锡珠的产生原因及解决方法锡珠现象是smt过程中的主要缺陷,主要发生在片式阻容元件的周围,由诸多因素引起。
它的产生是一个复杂的过程,也是最烦人的问题,要完全消除它,是非常困难的。
锡珠的直径大致在0.2mm——0.4mm之间,也有超过此范围的。
锡珠的存在,不仅影响了电子产品的美观,对产品的质量也有极大的隐患。
我们都知道现在smt工艺中的元件间距小,密度高,若是锡珠在使用时脱落,就可能造成元件短路,影响电子产品的质量。
因此,弄清锡珠产生的原因,并对它进行有效的控制,显得尤为重要了。
锡珠的产生原因是多方面造成的。
锡膏的印刷厚度、其组成及氧化度、模板的制作及开口都有可能造成锡珠现象,同时锡膏是否吸收了水分、元件贴装压力、元器件及焊盘的可焊性、再流焊温度的设置、外界环境的影响都可能是锡珠产生的原因。
下面吉田店铺就从各方面来分锡珠产生的原因及解决方法。
1、锡膏的金属氧化度。
在锡膏中,金属氧化度越高在焊接时金属粉末结合阻力越大,锡膏与焊盘及元件之间就越不浸润,从而导致可焊性降低。
锡珠的发生率与金属粉末的氧化度成正比。
一般的,锡膏中的焊料氧化度应控制在0.05%以下,最大极限为0.15%。
2、锡膏在印制板上的印刷厚度。
锡膏印刷后的厚度是漏板印刷的一个重要参数,通常在0.12mm——0.20mm之间。
锡膏过厚会造成锡膏“塌边”,促进锡珠的产生。
3、锡膏中助焊剂的量及焊剂的活性。
焊剂量太多,会造成锡膏的局部塌落,从而使锡珠容易产生。
另外,焊剂的活性小时,焊剂的去氧化能力弱,从而也容易产生锡珠。
免清洗锡膏的活性较松香型和水溶型锡膏要低,因此就更有可能产生锡珠。
4、此外,锡膏在使用前,一般冷藏在冰箱中,取出来以后应该使其恢复到室温后打开使用,否则,锡膏容易吸收水分,在再流焊锡飞溅而产生锡珠。
58回流焊中锡珠形成的原因及解决方法介绍|南昌回流焊原理2017-03-22 12:44 | #2楼波峰焊第一品牌【精极科技】深圳市精极科技有限公司成立于2002年8月,是一家以设计、生产、销售等工业仓储设备及柔性生产线设备为主的专业生产厂家,同时分销配套的防静电周边产品。
锡珠的形成及对策分析

7
而非锡珠(solder beads)
返回
锡珠形成的原因概述
锡珠
是怎样产生的
A 材料的原因
B 工艺的原因
I. 锡膏触变系数大
①
II. 锡膏冷坍塌或轻微热坍塌 ②
III. 焊剂过多或活性温度低
③
IV. 锡粉氧化率高或颗粒不均匀 ④
V. PCB的焊盘间距小
⑤
VI. 刮刀材质硬度小或变形
刮刀
锡膏
焊盘
钢版
9 PCB
返回
PCB 与钢版的间隔
在紧密印刷中不建议有间隔
!!
不建议
印刷钢板
PAD
PAD
线路板
10
不建议
脱模
返回
锡珠形成的原因(贴零件环节)锡膏印刷来自贴零件装 IC
回流焊接
检验
零件贴装部分
a) 贴片压力太大 b) 贴片精度太差 c) 其它因素
11
返回
贴片精度
线路板的精确度 ( PAD,校准点等)
共需要45分钟
介绍
锡珠 的形成和解决 SMT各工艺环节锡珠的预防措施和解决方法 根据鱼骨图逐项排除
3
大纲
相关词汇 (名词解释或定义)
SMT焊接中形成锡珠的现象
(正确的认识,错误的识别)
形成锡珠的原因(各工艺环节)
(印刷,贴件,回流焊接)
不停线调整减少锡珠的暂时对策
(暂时对策)
改良网版设计消除产生锡珠的隐患
14
Solder Beads
返回
其它的预防和改良措施
SMT各层工作人员的素质 SMT管理人员品质标准的培训 SMT 操作人员的相关操作的培训 明确各个工作岗位的权责(该做与不该做) 思想觉悟以及品质意识的提高
锡珠的形成及对策

温度曲线(Profile):用来监测零部件受热过程的走势图
焊盘(PAD): 电路板线路与零件引脚焊接的金属盘片
a) 印刷速度太快
b) 钢板底部不干净
c) 印刷环境温度过高(超过26摄氏度)
d) PCB定位不平整
e) 刮刀压力小(没刮干净锡)
f) 刮刀变形或硬度小(平直的钢刮刀)
g) 重复印刷次数多
h)
锡刮得太厚
i) 钢版太厚或开口太大
j)
PCB没处理干净
k) 及其它原因
当前您正浏览第9页,共29页。
回流焊接
当前您正浏览第7页,共29页。
返回
锡珠形成的原因概述
锡珠
是怎样产生的
A 材料的原因
B 工艺的原因
I. 锡膏触变系数小
II. 锡膏冷坍塌或轻微热坍塌
III. 焊剂过多或活性温度低
IV. 锡粉氧化率高或颗粒不均匀 V. PCB的焊盘间距小 VI. 刮刀材质硬度小或变形
VII. 钢版孔壁不平滑
VIII. 焊盘及料件可焊性差
8. 调整印刷参数减少减小锡珠(10分钟) 9. 调整回流温度曲线缓和锡珠的形成(10分钟)
10. 形成锡珠的其它原因(10分钟)
共需要45分钟
当前您正浏览第2页,共29页。
介绍
锡珠 的形成和解决 SMT各工艺环节锡珠的预防措施和解决方法
根据鱼骨图逐项排除
当前您正浏览第3页,共29页。
大纲
相关词汇(名词解释或定义)
一般是0.8mm(0603) ,如果贴片精度允许为防止 锡珠的产生可加大到0.82 mm
SMT产生锡珠的原因及对策

SMT产生锡珠的原因及对策前言在表面着装技术精密发达的时代中,常常发生扰人的问题,其中以在零件部品旁,所发生小锡珠为最常见。
本篇就探讨其发生原因与解决对策,提供使用人在制程上参考。
1.如图a.锡膏在印刷后,零件部品在植装时,置件压力过强,锡膏因此产生挤压。
当进入回焊炉加热时,部品零件温度上升通常比基板来得快,而零件部品下方温度上升较慢。
接着,零件部品的导体(极体)与锡膏接触地方,Flux因温度上升黏度降低,又因部品零件导体上方温度较高而爬升靠近。
所以锡膏是由温度最高Pad外侧开始溶融。
2.如图b.溶融焊锡开始向零件部品的导体处往上爬,溶融焊锡形成像墙壁一般, 接着未溶融焊锡中Flux动向,因溶融焊锡而阻断停止流动,所以Flux无法向外流。
当然所产生挥发溶剂(GAS)也因溶融焊锡而阻断包覆。
3.如图c.锡膏的溶融方向是向Pad的内部进行,Flux也向内部挤压,(GAS)也向内侧移动。
零件部品a.点的下方因力量而使溶融焊锡到达b.点,又因吃锡不良a.点停止下降,产生c.力量逆流,a.b.c.d.的力量,使得焊锡移动。
•零件部品氧化,在导体侧面吃锡是有界线的如图c.所示,结果反而焊锡受压析出形成锡珠。
•另一方面Pad温度较快上升,在Pad上的溶融焊锡先产生回塑效果,无法拉引零件部品,此时的力量使得未溶融焊锡受压析出溶融而形成小锡珠。
•锡膏内Flux易析出气泡,Flux流动力量加上挥发型溶剂的挥发,再加上零件部品在Pad上拉引的力量同时使得未溶融焊锡受挤压析出溶融而形成锡珠。
•锡膏量过多或Pad面积太小,溶融焊锡所保有空间过小也易形成锡珠。
对策零件部品旁发生锡珠的原因很多,需检讨与修正。
1.在设计上Pad的温度,能均匀上升,考虑受热平衡,来决定Pad大小及导体长宽。
2.在设计上考虑锡高的量,零件部品的高度与Pad面积,使得溶融焊锡保有舒展空间。
3.温度曲线不可急遽上升。
4.印刷精度及印刷量的控制,与印刷时的管理。
- 1、下载文档前请自行甄别文档内容的完整性,平台不提供额外的编辑、内容补充、找答案等附加服务。
- 2、"仅部分预览"的文档,不可在线预览部分如存在完整性等问题,可反馈申请退款(可完整预览的文档不适用该条件!)。
- 3、如文档侵犯您的权益,请联系客服反馈,我们会尽快为您处理(人工客服工作时间:9:00-18:30)。
随着电子产品迅速朝小型化、便携式、网络化 和多媒体化方向发展,这种市场需求对电路组装技 术提出了更高的要求,其中主要包括高密度化、高 速化、高 性 能 、高 可 靠 性 、低 功 耗 、小 尺 寸 和 多 引脚等。SMT(SurfaceMounted Technology)技术作 为电子行业最流行和应用最广的工艺技术,因其具 备组装密度高、电子产品体积小、可靠性高和易于 实现自动化等特点,已成为电子组装行业里最重要 的一种工艺和技术。但在实际规模生产过程中,还 是有各种各样的问题发生,锡珠是最主要的缺陷。 另外,越来越多的电子焊接采用焊后“免清洗”工 艺,但是如果焊后板面有“锡珠”出现,则不可能 达到“免清洗”的要求,因此“锡珠”的预防与控 制在实施“免清洗”过程中就显得格外重要。“锡 珠”的出现不仅影响板级产品外观,更为严重的是 由于印制板上元件密集,在使用过程中有可能造成 短路等状况,从而影响产品的可靠性。
由此可见,锡膏的质量及选用也影响着锡珠产 生。锡膏中金属及其氧化物的含量、金属粉末的粒 度、锡膏抗热坍塌效果等都在不同程度地影响着 “锡珠”的形成。
2)设备角度——印刷机,贴片机,回流焊机 (1)锡膏在印制板上的印刷厚度及印刷量。锡膏 的印刷厚度是生产中一个主要参数,印刷厚度通常 在 0.15~0.20 mm 之间,过厚或过多都容易导致 “坍塌”从而形成“锡珠”,过少会影响焊接质量。 (2)如果在贴片过程中贴装压力过大,元件压在 锡膏上时就可能有一部分锡膏被挤在元件下面或有 少量锡粉飞出,在焊接段这部分焊粉熔化从而形成 “锡珠”。 (3)回流焊机如果温区较少或回流焊机的长度 不够,都会因升温较快而产生锡珠。 3)工艺角度 (1)印刷工艺 锡膏印刷时发生的塌陷使锡膏留在阻焊层上, 从而会在回流焊时产生焊锡珠。塌陷与锡膏特性、 模板、印刷参数设定有很大关系。锡膏的黏度较低、 保形性不好,使印刷后容易塌陷;如果模板内孔壁粗 糙不平,会造成锡膏从模板脱落,印出的锡膏也容易 发生塌陷。过大的刮刀压力会对锡膏产生比较大的 冲击力,使锡膏外形被破坏,发生塌陷的概率也会大 大增加。因此,相对应的解决方法是选择黏度较高的 锡膏,采用激光切割模板来提高孔壁光滑度以降低 刮刀压力参数。有时在生产过程中,印刷线路板印 错后需要将线路板上已经印制的锡膏清洗干净。若 清洗不干净,印制板表面和过孔内就会有残余的锡
1)物料角度——锡膏 锡膏是一种均质混合物,由合金焊料粉、糊状 焊剂和一些添加剂混合而成的具有一定黏性和良好 触变性的膏状体。当被加热到一定温度时(通常 183℃),随着溶剂和部分添加剂的挥发及合金粉的
51
精密制造与自动化
2014 年第 3 期
熔化,使被焊元器件和焊盘连在一起,冷却形成永 久连接的焊点。合金焊料粉是锡膏的主要成分,约 占锡膏重量的 85%~90%。常用的锡膏分以下几 种:锡铅(Sn – Pb)、锡铅银/铜(Sn – Pb – Ag/Cu)和 锡(铅)铋(Sn – Pb – Bi)。目前锡铋为低温锡膏,比 较容易出现“锡珠”,锡膏产生的原因主要是由锡膏 的配方及成分所引起。
(1)锡膏中的金属含量。锡膏中金属含量的质量 比约为 89%~91%,体积比约为 50%左右,如图 2(a) 所示。通常金属含量越多,锡膏中的金属粉末排列 越紧密,锡粉的颗料之间就有更多机会结合而不易 在气化时被吹散,因此不易形成“锡珠”; 如果金 属含量减少,则出现“锡珠”的机率增高。
0.6 焊
0.5
锡珠”,所用线路板在焊接后必须被清洗或将锡珠手 工去除。
图 1 常见的锡珠形态及其尺寸标识照片
1.2 “锡珠”产生的原因 焊锡珠的存在不仅影响了电子产品的外观,也
对产品的质量埋下了隐患。现代化电子线路印制 板元件密度高、间距小,在使用时锡珠可能会脱 落。有的用户在使用端有二次回流的需要,锡珠 造成元器件或电路连接短路,影响电子产品的质 量。因此,很有必要弄清锡珠产生的原因,并进 行有效地控制及改进。在“SMT 表面贴装”焊接 工艺中,锡珠是在回流炉中产生,但回流焊的“温 度、时间、锡膏的质量、印刷厚度、钢网(模板)的 制作、装贴压力”等因素都有可能造成“锡珠”的 产生。锡珠其实就是由于锡膏受热太快,锡膏中的 水分爆裂而使得焊锡飞溅,从而在电路板上产生多 余的锡珠。所以原因主要从物料角度、设备角度和 工艺操作角度三个方面来分析。
2.3 工艺控制 1)模板的设计和制作 一般情况下,生产厂家往往根据印制板上的焊
(3)回流焊工艺 回流焊温度曲线是决定焊珠形成的一个重要参 数,温度曲线如图 3 所示。回流过程中不同阶段 的温度和升温速度会导致不同的问题产生。经典 的回流温度曲线将整个回流过程分为 5 个区域:预 热、保温、升温、焊接、冷却。每个区域的曲线斜 率不同,升温速率分别为 1.5℃/s、0.5℃/s、1.5℃/s、 2.5℃/s,冷却区域小于 4℃/s。特别是在焊接区,由 于升温速度较快,水分爆裂就容易形成锡珠。采 取较适中的预热温度和预热速度来控制锡珠的 产生。
(4)锡膏一般冷藏在冰箱中,使用前将其从冰 箱中拿出后不应立即开盖(立即开盖会使水汽凝结 在锡膏上),而应在使用环境下回温,待温度稳定 后再开盖使用。锡膏中助焊剂的量太多会造成锡膏 局部塌落,从而容易产生锡珠。另外,焊剂的活性 小导致焊剂的去氧化能力弱,也容易产生锡珠。免 清洗锡膏的活性较松香型和水溶型锡膏要低,因此 就更有可能产生焊锡珠。 2.2 设备选用
Paste C (Sn 63, -200/325)
0.4 珠
0.3
0.2 率
0.1
0.0 88
89
90
91
(a)
0.5 焊
0.4
Paste D (90% Sn 63, -200/325)
0.3 珠
0.2
0.1
率 0.0
0.00 0.05
0.10
0.15
0.20
0.25
(b) 图 2 锡膏成分与锡珠率对照曲线
1 “锡珠”产生主要因素分析 1.1 关于的“锡珠”形态及标准
根据电子产品生产现场质量检验标准及无铅的 验收标准(IPC-A-610C 标准)中规定“每平方英寸少 于 5 个”。最小绝缘间隙 0.13 mm,直径小于 0.13 mm 的锡珠被认为是合格的,常见的锡珠形态及其尺寸 照片如图 1 所示。而直径大于或等于 0.13 mm 的锡 珠是不合格的,制造商必须采取纠正措施,避免这 种现象的发生。在最新版 IPCA-610D 标准中没有对 无铅焊接中锡珠现象做更清楚的规定,另外 MIL-STD-2000 标准中规定“不允许有锡珠”,在有 关汽车和军用产品的标准中则是“不允许出现任何
52
戴建华 SMT 生产工艺中产生锡珠的原因分析及防控措施
膏,回流焊时就会形成锡珠,在这一过程中,人员 因素的影响显得尤为突出。因此要加强操作员在 生产过程中的责任心,严格按照工艺要求进行生 产,加强工艺过程的质量控制。
(2)贴片工艺 如果在贴装时压力太大,锡膏就容易被挤压到 元件下面的阻焊层上,在回流焊时焊锡熔化在元件 的周围形成锡珠。可以减小贴装时的压力,调整贴 装压力并设定包含元件本身厚度在内的贴装吸嘴的 下降位置,要注意元器件的物理尺寸,设置正确的 元件高度。
2 生产中“锡珠”的防控措施 2.1 锡膏选用
(1)锡膏中金属颗粒的含量、锡膏的氧化度、锡 膏中焊料球的粗细度、锡膏吸湿及锡膏中助焊剂的 量以及焊剂的活性都能影响锡珠的产生。锡膏中金 属含量的质量比约为 88%~92%,体积比约为 50%。 当金属含量增加时,锡膏的黏度增加,就能有效地 抵抗预热过程中汽化产生的力。另外,金属含量的 增加使焊料球排列紧密,使其在熔化时更容易结合 而不被吹散。此外,金属含量的增加也可以减小锡 膏印刷后的塌陷,因此,选用金属含量高的锡膏不
图 3 回流焊温度曲线图
(4)其他辅助工艺 湿度敏感的元器件及印制板长时间暴露在空 气中会吸收水分并发生焊盘氧化,导致可焊性变 差,极易引起焊锡珠现象。对这些湿度敏度元件和 印制板要进行湿度敏感度控制,控制的原则是在运 输、储存、备料及生产过程中一定要严格按照元器 件及印制板的湿度敏感等级进行控制,暴露时间超 标时必须及时用低温(40℃)或者高温(120℃) 在 干燥箱中进行 24 h 的烘烤,并且用湿度敏感指示卡 进行跟踪且要进行真空封装,这样可以有效地减少 锡珠产生。
(4)锡膏抗热坍塌效果。在回流焊预热段,如果 锡膏抗热坍塌效果不好,在焊接温度前(焊料开始熔 融前)已印刷成型的锡膏开始坍塌,并有些锡膏流到 焊盘以外。当进入焊接区时焊料开始熔融,由于内 应力的作用,锡膏收缩成焊点并开始浸润爬升至焊 接端头。有时因为焊剂缺失或其他原因导致锡膏应 力不足,有一少部分焊盘外的锡膏没有收缩回来, 当其完全熔化后就形成了“锡珠”。
(1)印刷机的选用。印刷机本身应选用压力适 中、控制精确的全自动印刷机。特别是与印刷机相 匹配的钢网。钢网的开孔和印刷的压力是印刷工艺 阶段主要控制因素。
(2)贴片机的选用。主要是贴片的压力和位置 精确度,一般选择全自动的贴片机。主流贴片机一 般都能达到使用要求。
(3)回流焊机的选用。回流焊机是引起锡珠的 主要原因,在实际生产加工一款遥控器电路板时出 现锡珠的可能性较多,选用的回流焊炉是 HW-8800 的 8 温区。开始一直以为是印刷工艺出现的问题,后 来发现回流焊机的温控曲线在低温时的控制不是很 好,回流焊机常用的温度是在 230℃,但由于这款遥 控器电路板的问题只能选用低温锡膏,在温度测试 时正常,但过板是温度有一点偏差;后选用另一条 生产线的回流焊炉,锡珠的出现率大大降低。
53
精密制造与自动化
2014 年第 3 期
易产生焊锡珠。 (2)锡膏接触空气后,金属颗粒表面可能产生
氧化。金属氧化度越高,在焊接时颗粒越不易结合, 锡膏与焊盘及元件之间就越不浸润,从而导致可焊 性降低。而试验证明锡珠的发生率与锡膏氧化物的 百分率成正比。一般锡膏的氧化物应控制在 0. 03% 左右,最大值不要超过 0. 15%,所以锡膏不宜长时 间暴露的空气中。