“波峰焊”过程中出现“锡珠”的原因及预防控制办法
产生“锡珠”的原因分析及措施

成“锡珠”。
在制作钢网(模板)时,焊盘的大小决定着模板开孔的大小,通常,我们为了避免焊膏印刷过量,将印刷孔的尺寸控制在约小于相应焊盘接触面积10%,结果表明这样会使“锡珠”现象有一定程度的减轻。
3,如果在贴片过程中贴装压力过大,当元件压在焊膏上时,就可能有一部分焊膏被挤在元件下面或有少量锡粉飞出去,在焊接段这部分焊粉熔化从而形成“锡珠”;因此,在贴装时应选择适当的贴装压力。
4,焊膏通常需要冷藏,在使用前一定要使其恢复至室温方可打开包装使用,如果焊膏温度过低就被打开包装,会使膏体表面产生水分,这些水分在经过预热时会造成焊粉飞出,在焊接段会让热熔的焊料飞溅从而形成“锡珠”。
我国一般地区夏天的空气湿度较大,把焊膏从冷藏取出时,一般要在室温下回温4-5小时再开启瓶盖。
5,生产或工作环境也影响“锡珠”的形成,当印制板在潮湿的库房存放过久,在装印制板的包装袋中发现细小的水珠,这些水分和焊膏吸潮的水分一样,会影响焊接效果从而形成“锡珠”。
因此,如果有条件,在贴装前将印制板或元器件进行一定的烘干,然后进行印刷及焊接,能够有效地抑制“锡珠”的形成。
6,焊膏与空气接触的时间越短越好,这也是使用焊膏的一个原则。
取出一部分焊膏后,立即盖好盖子,特别是里面的盖子一定要向下压紧,将盖子与焊膏之间空气挤出,否则对焊膏的寿命会有一定的影响,同时会造成焊膏的干燥加快或在下次再使用时吸潮,从而形成“锡珠”。
由此可见,“锡珠”的出现有很多原因,只从某一个方面进行预防与控制是远远不够的。
我们需要在生产过程中研究如何防制各种不利因素及潜在隐患,从而使焊接达到最好的效果,避免“锡珠”的产生。
(三),“SMT表面贴装”过程的“锡珠”预防与控制1,焊膏的选用在选择焊膏时,应坚持在现有工艺条件下的试用,这样,既能验证供应商焊膏对自身产品、工艺的适用性,也能初步了解该焊膏在实际使用中的具体表现。
对焊膏方面的评估,应注意各种常见的参数,比如“焊油与焊粉的比例、锡球的颗粒度”等。
波峰焊锡珠产生的原因及解决方案

波峰焊锡珠产生的原因及解决方案大家好,今天咱们聊聊波峰焊锡珠的事儿。
要说波峰焊,真的是电子制造中一个非常关键的环节。
它像是给咱们的电路板披上了一层“金色铠甲”,保护它不受外界的侵害。
但是,有时候,这个看似完美的过程会出现一些小麻烦,比如焊锡珠。
那么,这些焊锡珠到底是怎么来的呢?又该如何解决呢?接下来,就让咱们一探究竟吧。
1. 焊锡珠的成因1.1 焊接温度过高首先,我们得知道,焊锡珠通常是在焊接过程中出现的。
第一个大头原因就是焊接温度太高。
想象一下,你在厨房里做菜,火开得太猛,油锅里就会冒油花儿,烫得你跳脚。
波峰焊的情况也是类似,如果焊接温度过高,焊锡在碰到电路板的时候就容易挥发,导致焊锡珠的产生。
过高的温度不仅让焊锡液体挥发,还可能影响到板子的质量,简直就是一场灾难!1.2 焊锡液体过多再有一个原因就是焊锡液体的量过多。
就像你做饭时加了过多的盐,结果整锅饭都咸了。
在波峰焊中,如果焊锡液体的量过多,也会导致焊锡珠的产生。
这是因为焊锡液体在焊接过程中不能完全被板子吸收,最终就会形成多余的小珠子,挂在电路板上,这看起来真是让人哭笑不得。
2. 焊锡珠的解决方案2.1 调整焊接温度知道了问题的根源,咱们也有解决的办法。
首先要做的就是调整焊接温度。
试着把焊接温度降低一点点,看看效果如何。
焊接温度一般在240°C到260°C之间比较合适,大家可以根据自己的实际情况微调一下。
温度过高可不是好事,得适中才行。
你要记住,温度调得太高,锡珠飞溅,调得太低,又可能导致焊接不良,找准那个平衡点,才能让焊锡珠远离你的电路板。
2.2 控制焊锡液体量其次,焊锡液体的量也要控制好。
如果焊锡液体过多,就像是汤锅里的水太多,容易溢出来。
你可以通过调整焊锡槽的液面高度来控制焊锡的量。
合适的液体量不仅可以有效减少焊锡珠的产生,还能保证焊接的质量。
所以,控制好液体量也是非常关键的一个环节。
3. 板子的处理3.1 保持电路板干净除了以上两点,还得保证电路板的干净整洁。
PCB波峰焊后板面锡珠分析改善

PCB波峰焊后板面锡珠分析改善
一、PCB波峰焊后板面锡珠分析
1.由PCB波峰焊机产生的锡珠分析
PCB波峰焊机是一种智能电子焊接加工设备,它能够完成PCB板直角
双面焊接,也可以进行其他形状的焊接。
由于波峰焊机采用的是锡珠焊接
方式,因此波峰焊机产生的锡珠质量是影响焊接效果的重要因素,主要有
以下几方面:
(1)锡珠的质量和大小:锡珠的质量直接影响芯片安装的质量,而
大小则直接影响焊点的质量和表面完整性;
(2)焊点温度和焊接时间:焊接过程的温度和时间是影响焊接质量
的因素,若焊点温度过高或焊接时间过长,会使焊点出现裂纹和烧毁现象;
(3)抽灰膨胀率:在进行焊接时,由于抽灰膨胀率受温度变化而受
影响,并会使焊接条件变化从而影响焊接效果。
2.PCB波峰焊后板面锡珠分析
(1)高度稳定的锡珠:这类锡珠的高度和重量基本保持一致,在焊
后的表面上通常无明显的排列不整齐现象;
(2)宽小稳定的锡珠:此类锡珠比较均匀,在焊后的表面上能够看
到稍大一些的锡珠,但是也不会出现太大的不平整现象;。
锡珠的产生原因与解决措施

波峰焊接中溅锡珠的形成原因⑴ “小爆炸”理论波峰焊接中在 PCB 的焊接面及元件面上均可能产生锡珠飞溅现象。
普遍认为在 PCB 进入波峰之前有水汽滞留在PCB上的话,一旦与波峰钎料接触,在剧烈升温的过程中,就会在极短的时间内迅速汽化变成蒸汽,发生爆发性的排气过程。
正是这种剧烈的排气可能引发正处在熔融状态中的焊接点内部的小爆炸,从而促使钎料颗粒在脱离波峰时飞溅在PCB上形成锡珠。
在波峰焊接前PCB水汽的来源,杭州东方通信公司对此进行过专题研究和试验,归纳的结论如下:① 制造环境和PCB存放时间制造环境对电子装联的焊接质量有着很大的影响。
制造环境的湿度较重,或PCB包装开封较长时间后再进行贴片和波峰焊生产,或者PCB贴片、插装后放置一段时间后再进行波峰焊,这些因素都很有可能使PCB在波峰焊接过程中产生锡珠。
如果制造环境的湿度太大,在产品制造过程中空气浮动着水汽很容易会在PCB表面凝结,使PCB通孔中凝结有水珠,在过波峰焊时,通孔中的水珠经过预热温区后可能还没有完全挥发完,这些没有挥发完的水珠接触到波峰的焊锡时,经受了高温,就会在短时间内汽化变成蒸汽,而此时正是形成焊点的时候,水汽就会在焊料内产生空隙,或挤出焊料产生锡球。
严重的话就会形成一个爆点,并在它的周围分布有被吹开的细小的锡珠。
假如PCB在包装开封较长时间后再进行贴片和波峰焊,通孔中也会凝结有水珠;PCB完成贴片后或插装完成后放置了一段时间,也会凝结水珠。
同样的原因,这些水珠都有可能在波峰焊过程中导致锡珠产生。
因而,作为从事电子装联的企业,对制造环境的要求和对产品制造过程中的时间安排显得特别地重要。
贴片完成后的PCB应在24小时内完成插装并进行波峰焊,假如天气晴朗干燥,可以在48小时内完成。
② PCB阻焊材料和制作质量在PCB制造过程中所使用的阻焊膜也是波峰焊产生锡球的原因之一。
因为阻焊膜与助焊剂有一定的亲合性,阻焊膜加工不良常常会引起锡珠粘附,产生焊锡球。
波峰焊和回流焊典型焊接缺陷及解决措施

波峰焊和回流焊典型焊接缺陷及解决措施1、波峰焊和回流焊中的锡球锡球的存在表明工艺不完全正确,而且电子产品存在短路的危险,因此需要排除。
国际上对锡球存在认可标准是:印刷电路组件在600范围内不能出现超过5个锡球。
产生锡球的原因有多种,需要找到问题根源。
1、1 波峰焊中锡球波峰焊中常常出现锡球主要原因有两方面:第一,由于焊接印刷板时,印刷板上的通孔附近的水分受热而变成蒸汽。
如果孔壁金属镀层较薄或有空隙,水汽就会通过孔壁排除,如果孔内有焊料,当焊料凝固时水汽就会在焊料内产生空隙(针眼),或挤出焊料在印制板正面产生锡球。
第二。
在印制板反面(即接触波峰的一面)产生的锡球是由于波峰焊接中一些工艺参数设置不当而造成的。
如果助焊剂涂覆量增加或预热温度设置过低,就可能影响焊剂内组成成分的蒸发,在印制板进入波峰时,多余的焊剂受高温蒸发,将焊料从锡槽中溅出来,在印制板面上产生不规则的焊料球。
针对上述两面原因,我们采取以下相应的解决措施:第一,通孔内适当厚度的金属镀层是很关键的,孔壁上的铜镀层最小应为25um,面且无空隙。
第二,使用喷雾或发泡式涂覆助焊剂。
发泡方式中,在调节助焊剂的空气含量时,应保持尽可能产生最小的气泡,泡沫与PCB 接触面相对减小。
第三,波峰焊机预热区温度的设置应使线路板顶面的温度达到至少100摄氏度。
适当的预热温度不仅可消除焊料球,面且避免线路板受到热冲击面变形。
1、2 回流焊中的锡球1、2、1回流焊中锡球形成的机理回流焊接中出的锡球,常常藏于矩形片式组件两端之间的侧面或细距引脚之间。
在组件贴装过程中,焊膏被置于片式组件的引脚与焊盘这间,随着印制板穿过回流焊炉,焊膏熔化变成液体,如果与焊盘和器件引脚等润湿不良,液态焊锡会因收缩面使焊缝充不充分,所有焊料颗粒不能合成一个焊点。
部分液态焊锡会从焊缝流出,形成锡球。
因此,焊锡与焊盘和器件引脚润湿性差是导致锡球形成的根本原因。
1、2、2 原因分析与控制方法造成焊锡润湿性差的原因很多,以下主要分析与相关的原因及解决措施:a)回流温度曲线设置不当。
4-3-波峰焊接中产生锡珠(球)、短路问题分析和正确的工艺方法
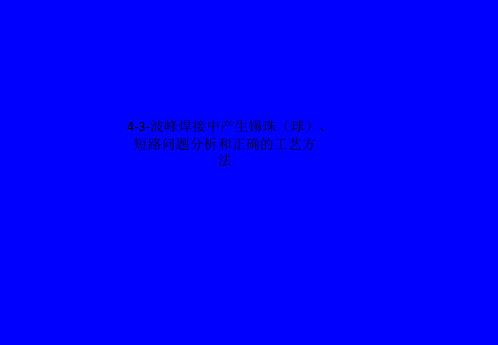
① 从设备方面考虑,在设计锡波发生
器和锡缸时,应注意减少锡的降落高 度。小的降落高度有助于减少锡渣和 溅锡现象 ② 选择亚光型和耐高温的阻焊层材料
②件接触的与到下助锡面焊波。剂之如有前果关没助。有焊助被剂焊充中剂分的会预溶残热剂留并在在挥P元C发器B尽板,严 数格。遵循助焊剂供应商推荐的预热参 就焊剂会内产的生水溅分锡含并量形太成大锡,球同。样另会外产,生如溅果锡助。必要时更换新的助焊剂。
③助波峰焊与焊剂工接中艺温的参度溶数使剂设阻没置焊有有层挥关更发。柔干预滑净热或,温带或度有过过粘高低性的,;适 使 尽助当 量焊调 设剂高 置中预较的热低溶温的剂度波和或峰水延温汽长度能预;充热分时挥间发,。
PCB传输角过小,气体不易排出
增加PCB传输角度
产生原因
预防对策
④ 与阻焊层的质量有关。比较粗燥的阻
焊层和锡球有更小的接触面,锡球不易
粘在PCB表面。在无铅焊接过程中,高 温会使阻焊层更柔滑,更易造成锡球粘 在PCB板上。另外如果阻焊层不耐高温,
选择亚光型和耐高温的阻焊层材料; 尽量设置较低的波峰温度。
高温下会发粘,也会造成锡球粘在PCB
板上。
⑤ 元器件焊端和引脚、印制电路基板的 焊盘氧化或污染,或印制板受潮
② 与物料管理和存储条件有关。PCB和元 件受潮或元件引脚严重氧化,波峰焊时水 严格物料管理,对受潮的 气挥发炸锡造成锡珠,或化学反应剧烈产 PCB和元件进行去潮处理。 生飞溅。在PCB板的元件面形成锡珠。
③ 预热温度过低,助焊剂中的溶剂、水气 提高预热温度,使PCB板
及其他气体没有挥发干净。
顶面温度达到至少100℃
⑦ 波峰焊接面SMC/SMD没有过孔, 焊 接时排气不畅, 从而引起飞溅及锡球
波峰焊连锡的原因与解决方法
波峰焊连锡的原因与解决方法
波峰焊连锡一般是由于焊接过程中缺乏一定的焊接控制而导致的,也可能是由于焊膏中含有高水分导致的,总体上可以分为这样几种:
一是焊锡温度不足。
如果焊接温度过低,铜箔的拉线强度将变弱,拉线脆弱,易破裂,从而导致焊锡接触不良,甚至形成波峰状。
可以通过添加焊锡温度来解决这个问题。
二是焊膏含水过高。
如果焊膏中含有太多的水分,则焊膏本身就会变得不稳定,而且含水量高的焊膏介电性能低,焊膏易燃损失,焊接接触锡头就会发现波峰。
可以通过烘干设备,来把焊膏中的水分剥落出来,然后使用水吸收剂等来减少水分的含量,以解决这一问题。
三是焊針的质量不够好。
如果一个焊針的质量不是很好,那么尝试把原来的焊針改为高质量的焊針,可以有效解决波峰状焊接。
波峰焊过程中出现锡珠波峰焊过程中出现锡珠的原因及预防控制办法
波峰焊过程中出现锡珠波峰焊过程中出现锡珠的原因及预防控制办法在波峰焊工艺过程中,锡珠的产生有两种状况:一种是在板子刚接触到锡液时,因为助焊剂或板材本身的水份过多或高沸点溶剂没有充分挥发,遇到温度较高的锡液时骤然挥发,较大的温差致使液态焊锡飞溅出去,形成细小锡珠;另一种情况是在线路板离开液态焊锡的时候,当线路板与锡波分离时,线路板顺着管脚延伸的方向会拉出锡柱,在助焊剂的润湿作用及锡液自身流动性的作用下,多余的焊锡会落回锡缸中,因此而溅起的焊锡有时会落在线路板上,从而形成锡珠。
因此,我们可以看到,在波峰焊防控锡珠方面,我们应该从两个大的方面着手,一方面是助焊剂等原材料的选择,另一方面是波峰焊的工艺控制。
(一),助焊剂方面的原因分析及预防控制办法1、助焊剂中的水份含量较大或超标,在经过预热时未能充分挥发;2、助焊剂中有高沸点物质或不易挥发物,经预热时不能充分挥发;这两种原因是助焊剂本身质量问题所引起的,在实际焊接工艺中,可以通过提高预热温度或放慢走板速度等来解决。
除此之外,在选用助焊剂前应针对供商所提供样品进行实际工艺的确认,并记录试用时的标准工艺,在没有锡珠出现的情况下,审核供应商所提供的其他说明资料,在以后的收货及验收过程中,应核对供应商最初的说明资料。
(二),工艺方面的原因分析及预防控制办法1,预热温度偏低,助焊剂中溶剂部分未完全挥发;2,走板速度太快未达到预热效果;3,链条(或PCB板面)倾角过小,锡液与焊接面接触时中间有气泡,气泡爆裂后产生锡珠;4,助焊剂涂布的量太大,多余助焊剂未能完全流走或风刀没有将多余焊剂吹下;这四种不良原因的出现,都和标准化工艺的确定有关,在实际生产过程中,应该严格按照已经订好的作业指导文件进行各项参数的校正,对已经设定好的参数,不能随意改动,相关参数及所涉及技术层面主要有以下几点:(1),关于预热:一般设定在90℃-110℃,这里所讲温度是指预热后PCB板焊接面的实际受热温度,而不是表显温度;如果预热温度达不到要求,则焊后易产生锡珠。
波峰焊常见缺陷原因和防止措施
波峰焊常见缺陷原因和防止措施波峰焊是一种常用的电子组装工艺,主要用于连接电子元件与印刷电路板(PCB)。
在波峰焊过程中,为避免焊接缺陷,需要了解常见的波峰焊缺陷原因和相应的防止措施。
一、焊接缺陷原因1.锡球或电极柱与焊盘无法完全湿润:主要原因有以下几点:-温度过低:焊锡温度过低会导致焊接不良,需要适当提高焊接温度。
-温度不均匀:焊接过程中,焊接区域温度不均匀,需要通过调整加热方式或传递热量的方法来提高温度均匀度。
-氧化:焊接部分氧化会影响焊接质量,需要保持焊接环境干燥、清洁。
2.焊接过度:在波峰焊过程中焊接过度会导致焊点变翘、烧损等问题。
-温度过高:焊接温度过高导致焊点过度烧焦,需要适当降低焊接温度。
-焊接时间过长:焊接时间过长会使焊接物质被加热过度,需要根据具体情况调整焊接时间。
3.金属残留物:金属残留物会影响焊接质量。
-锡渣:焊接过程中产生的锡渣会附着在焊点或焊盘上,形成焊接垫高,需要及时清除锡渣。
-氧化物:焊接过程中,金属表面和焊盘上的氧化物会影响焊接质量,需要保持焊接环境清洁。
二、防止措施1.控制焊接温度:根据焊接物料的具体情况,合理控制焊接温度,避免温度过低或过高导致焊接不良。
同时,需要保证焊接温度均匀分布,避免温度不均匀导致焊接缺陷。
2.提高焊接环境的干燥度和清洁度:保持焊接环境的干燥和清洁,有效防止焊接过程中金属表面和焊盘上的氧化物生成和附着。
同时,及时清除焊接过程中产生的锡渣,避免锡渣堆积影响焊接质量。
3.控制焊接时间:根据具体焊接要求,控制焊接时间,避免焊接时间过长导致焊点过度烧焦。
同时,可以采用预热或加热方式调整焊接时间,提高焊接质量。
4.使用合适的焊接材料:选择合适的焊接材料对于提高焊接质量非常重要。
合适的焊锡材料可以有助于减少焊接缺陷。
5.检查和测试:对焊接后的产品进行检查和测试,及时发现并解决焊接缺陷,确保产品质量。
总之,了解波峰焊常见缺陷原因并采取相应的防止措施是提高焊接质量的关键。
波峰焊时如何防止锡珠的产生
波峰焊时如何防止锡珠的产生线路板在进行波峰焊接后,焊接面上会出现锡珠。
而下述的线路板组装技术的发展趋势将使这种焊接缺陷越来越成为一个严重的问题:线路板上元器件和IC引脚之间的间距越来越小,使得线路板更容易因为锡珠产生短路焊接面上越来越多的贴片元件致使更多地使用托盘在波峰焊上进行选择性焊接由于无铅焊料的使用,焊接温度更高波峰焊更多地使用氮气氛以减少锡渣并改善工艺窗口过去,大部分锡珠会在焊接后清洗线路板时被洗掉,而随着免清洗焊膏的使用,不再需要清洗过程,锡珠问题就不可避免了。
对于许多电子控制系统,如汽车上的安全气囊和其他汽车电子系统,锡珠的出现(可能会造成短路)会影响驾驶安全。
锡珠的形成原因锡珠是在线路板离开液态焊锡的时候形成的。
当线路板与锡波分离时,线路板会拉出锡柱,锡柱断裂落回锡缸时,溅起的焊锡会在落在线路板上形成锡珠。
因此,在设计锡波发生器和锡缸时,应注意减少锡的降落高度。
小的降落高度有助于减少锡渣和溅锡现象。
氮气的使用会加剧锡珠的形成。
氮气氛能防止焊锡表面形成氧化层,增加了锡珠形成的概率,同时,氮气也会影响焊锡的表面张力。
锡珠形成的第二个原因是线路板材和阻焊层内挥发物质的释气。
如果线路板通孔的金属层上有裂缝的话,这些物质加热后挥发的气体就会从裂缝中逸出,在线路板的元件面形成锡珠。
锡珠形成的第三个原因与助焊剂有关。
助焊剂会残留在元器件的下面或是线路板和搬运器(选择性焊接使用的托盘)之间。
如果助焊剂没能被充分预热并在线路板接触到锡波之前烧尽,就会产生溅锡并形成锡珠。
因此,应该严格遵循助焊剂供应商推荐的预热参数。
阻焊层锡珠是否会粘附在线路板上取决于基板材料。
如果锡珠和线路板的粘附力小于锡珠的重力,锡珠就会从就会从线路板上弹开落回锡缸中。
在这种情况下,线路板上的阻焊层是个非常重要的因素。
比较粗燥(rough)的阻焊层会和锡珠有更小的接触面,锡珠不易粘在线路板上。
在无铅焊接过程中,高温会使阻焊层更柔滑(softer),更易造成锡珠粘在线路板上。
- 1、下载文档前请自行甄别文档内容的完整性,平台不提供额外的编辑、内容补充、找答案等附加服务。
- 2、"仅部分预览"的文档,不可在线预览部分如存在完整性等问题,可反馈申请退款(可完整预览的文档不适用该条件!)。
- 3、如文档侵犯您的权益,请联系客服反馈,我们会尽快为您处理(人工客服工作时间:9:00-18:30)。
“波峰焊”过程中出现“锡珠”的原因及预防控制办法
在“波峰焊”工艺过程中,“锡珠”的产生有两种状况:一种是在板子刚接触到锡液时,因为助焊剂或板材本身的水份过多或高沸点溶剂没有充分挥发,遇到温度较高的锡液时骤然挥发,较大的温差致使液态焊锡飞溅出去,形成细小锡珠;另一种情况是在线路板离开液态焊锡的时候,当线路板与锡波分离时,线路板顺着管脚延伸的方向会拉出锡柱,在助焊剂的润湿作用及锡液自身流动性的作用下,多余的焊锡会落回锡缸中,因此而溅起的焊锡有时会落在线路板上,从而形成“锡珠”。
因此,我们可以看到,在“波峰焊”防控“锡珠”方面,我们应该从两个大的方面着手,一方面是助焊剂等原材料的选择,另一方面是波峰焊的工艺控制。
(一)助焊剂方面的原因分析及预防控制办法
1、助焊剂中的水份含量较大或超标,在经过预热时未能充分挥发;
2、助焊剂中有高沸点物质或不易挥发物,经预热时不能充分挥发;
这两种原因是助焊剂本身“质量”问题所引起的,在实际焊接工艺中,可以通过“提高预热温度或放慢走板速度等来解决”。
除此之外,在选用助焊剂前应针对供商所提供样品进行实际工艺的确认,并记录试用时的标准工艺,在没有“锡珠”出现的情况下,审核供应商所提供的其他说明资料,在以后的收货及验收过程中,应核对供应商最初的说明资料。
(二)工艺方面的原因分析及预防控制办法
1,预热温度偏低,助焊剂中溶剂部分未完全挥发;
2,走板速度太快未达到预热效果;
3,链条(或PCB板面)倾角过小,锡液与焊接面接触时中间有气泡,气泡爆裂后产生锡珠;
4,助焊剂涂布的量太大,多余助焊剂未能完全流走或风刀没有将多余焊剂吹下;
这四种不良原因的出现,都和标准化工艺的确定有关,在实际生产过程中,应该严格按照已经订好的作业指导文件进行各项参数的校正,对已经设定好的参数,不能随意改动,相关参数及所涉及技术层面主要有以下几点:
(1),关于预热:一般设定在90-110摄氏度,这里所讲“温度”是指预热后PCB板焊接面的实际受热温度,而不是“表显”温度;如果预热温度达不到要求,则焊后易产生锡珠。
(2),关于走板速度:一般情况下,建议客户把走板速度定在1.1-1.4米/分钟,但这不是绝对值;如果要改变走板速度,通常都应以改变预热温度作配合;比如:要将走板速度加快,那么为了保证PCB焊接面的预热温度能够达到预定值,就应当把预热温度适当提高;如果预热温度不变,走板速度过快时,焊剂有可能挥发不完全,从而在焊接时产生“锡珠”。
(3),关于链条(或PCB板面)的倾角:这一倾角指的是链条(或PCB
板面)与锡液平面的角度,当PCB板走过锡液平面时,应保证PCB零件面与锡液平面只有一个切点;而不能有一个较大的接触面;当没有倾角或倾角过小时,易造成锡液与焊接面接触时中间有气泡,气泡爆裂后产生“锡珠”。
(4),在波峰炉使用中,“风刀”的主要作用是吹去PCB板面多余的助焊剂,并使助焊剂在PCB零件面均匀涂布;一般情况下,风刀的倾角应在10度左右;如果“风刀”角度调整的不合理,会造成PCB表面焊剂过多,或涂布不均匀,不但在过预热区时易滴在发热管上,影响发热管的寿命,而且在浸入锡液时易造成“炸锡”现象,并因此产生“锡珠”。
在实际生产中,结合自身波峰焊的实际状况,对相关材料进行选型,同时制订严格《波峰焊操作规程》,并严格按照相关规程进行生产。
经过实验证明,在严格落实工艺技术的条件下,完全可以克服因为“波峰焊焊接工艺问题”产生的“锡珠”。