锡珠解决方法
回流焊产生锡珠的原因及解决方案

回流焊产生锡珠的原因及解决方案在SMT生产工艺里面,经常会碰到经过回流焊过出来的板有锡珠,锡珠的产生,让产品的质量没有保证,让外观看起来不光滑。
那产生锡珠的主要原因是什么,我们又如何去解决它,这就是我今天写这篇文章的目的。
产生锡珠的主要原因是锡膏的问题。
详细分析请看下面分析。
焊锡珠现象是表面贴装生产中主要缺陷之一,它的直径约为0.2-0.4mm,主要集中出现在片状阻容元件的某一侧面,不仅影响板级产品的外观,更为严重的是由于印刷板上元件密集,在使用过程中它会造成短路现象,从而影响电子产品的质量。
因此弄清它产生的原因,并力求对其进行最有效的控制就显得犹为重要了。
焊锡珠产生的原因是多种因素造成的,在回流焊中的温度时间,焊膏的印刷厚度,焊膏的组成成分,模板的制作,贴片机贴装压力,外界环境都会在生产过程中各个环节对焊锡珠形成产生影响。
焊锡珠是在负责制板通过回流焊炉时产生的。
回流焊曲线可以分为四个阶段,分别为:预热、保温、回流和冷却。
预热阶段的主要目的是为了使印制板和上面的表贴元件升温到120-150度之间,这样可以除去焊膏中易挥发的溶剂,减少对元件的热振动。
因此,在这一过程中焊膏内部会发生气化现象,这时如果焊膏中金属粉末之间的粘结力小于气化产生的力,就会有少量焊膏从焊盘上流离开,有的则躲到片状阻容元件下面,再流焊阶段,温度接近曲线的峰值时,这部分焊膏也会熔化,而后从片状阻容元件下面挤出,形成焊锡珠,由它的形成过程可见,预热温度越高,预热速度越快,就会加大气化现象中飞溅,也就越容易形成锡珠。
因此,我们可以采取较适中的预热温度和预热速度来控制焊锡珠的形成。
焊膏的选用也影响着焊接质量,焊膏中金属的含量,回流焊焊膏的氧化物含量,焊膏中金属粉末的粒度,及焊膏在印制板上的印刷厚度都不同程度影响着焊锡珠的形成。
1:焊膏中的金属含量:焊膏中金属含量的质量比约为90-91%,体积比约为50%左右。
当金属含量增加时,焊膏的粘度增加,就能更有效地抵抗预热过程中气化产生的力。
波峰焊锡珠产生的原因及解决方案

波峰焊锡珠产生的原因及解决方案大家好,今天咱们聊聊波峰焊锡珠的事儿。
要说波峰焊,真的是电子制造中一个非常关键的环节。
它像是给咱们的电路板披上了一层“金色铠甲”,保护它不受外界的侵害。
但是,有时候,这个看似完美的过程会出现一些小麻烦,比如焊锡珠。
那么,这些焊锡珠到底是怎么来的呢?又该如何解决呢?接下来,就让咱们一探究竟吧。
1. 焊锡珠的成因1.1 焊接温度过高首先,我们得知道,焊锡珠通常是在焊接过程中出现的。
第一个大头原因就是焊接温度太高。
想象一下,你在厨房里做菜,火开得太猛,油锅里就会冒油花儿,烫得你跳脚。
波峰焊的情况也是类似,如果焊接温度过高,焊锡在碰到电路板的时候就容易挥发,导致焊锡珠的产生。
过高的温度不仅让焊锡液体挥发,还可能影响到板子的质量,简直就是一场灾难!1.2 焊锡液体过多再有一个原因就是焊锡液体的量过多。
就像你做饭时加了过多的盐,结果整锅饭都咸了。
在波峰焊中,如果焊锡液体的量过多,也会导致焊锡珠的产生。
这是因为焊锡液体在焊接过程中不能完全被板子吸收,最终就会形成多余的小珠子,挂在电路板上,这看起来真是让人哭笑不得。
2. 焊锡珠的解决方案2.1 调整焊接温度知道了问题的根源,咱们也有解决的办法。
首先要做的就是调整焊接温度。
试着把焊接温度降低一点点,看看效果如何。
焊接温度一般在240°C到260°C之间比较合适,大家可以根据自己的实际情况微调一下。
温度过高可不是好事,得适中才行。
你要记住,温度调得太高,锡珠飞溅,调得太低,又可能导致焊接不良,找准那个平衡点,才能让焊锡珠远离你的电路板。
2.2 控制焊锡液体量其次,焊锡液体的量也要控制好。
如果焊锡液体过多,就像是汤锅里的水太多,容易溢出来。
你可以通过调整焊锡槽的液面高度来控制焊锡的量。
合适的液体量不仅可以有效减少焊锡珠的产生,还能保证焊接的质量。
所以,控制好液体量也是非常关键的一个环节。
3. 板子的处理3.1 保持电路板干净除了以上两点,还得保证电路板的干净整洁。
锡珠的产生原因与解决措施

波峰焊接中溅锡珠的形成原因⑴ “小爆炸”理论波峰焊接中在 PCB 的焊接面及元件面上均可能产生锡珠飞溅现象。
普遍认为在 PCB 进入波峰之前有水汽滞留在PCB上的话,一旦与波峰钎料接触,在剧烈升温的过程中,就会在极短的时间内迅速汽化变成蒸汽,发生爆发性的排气过程。
正是这种剧烈的排气可能引发正处在熔融状态中的焊接点内部的小爆炸,从而促使钎料颗粒在脱离波峰时飞溅在PCB上形成锡珠。
在波峰焊接前PCB水汽的来源,杭州东方通信公司对此进行过专题研究和试验,归纳的结论如下:① 制造环境和PCB存放时间制造环境对电子装联的焊接质量有着很大的影响。
制造环境的湿度较重,或PCB包装开封较长时间后再进行贴片和波峰焊生产,或者PCB贴片、插装后放置一段时间后再进行波峰焊,这些因素都很有可能使PCB在波峰焊接过程中产生锡珠。
如果制造环境的湿度太大,在产品制造过程中空气浮动着水汽很容易会在PCB表面凝结,使PCB通孔中凝结有水珠,在过波峰焊时,通孔中的水珠经过预热温区后可能还没有完全挥发完,这些没有挥发完的水珠接触到波峰的焊锡时,经受了高温,就会在短时间内汽化变成蒸汽,而此时正是形成焊点的时候,水汽就会在焊料内产生空隙,或挤出焊料产生锡球。
严重的话就会形成一个爆点,并在它的周围分布有被吹开的细小的锡珠。
假如PCB在包装开封较长时间后再进行贴片和波峰焊,通孔中也会凝结有水珠;PCB完成贴片后或插装完成后放置了一段时间,也会凝结水珠。
同样的原因,这些水珠都有可能在波峰焊过程中导致锡珠产生。
因而,作为从事电子装联的企业,对制造环境的要求和对产品制造过程中的时间安排显得特别地重要。
贴片完成后的PCB应在24小时内完成插装并进行波峰焊,假如天气晴朗干燥,可以在48小时内完成。
② PCB阻焊材料和制作质量在PCB制造过程中所使用的阻焊膜也是波峰焊产生锡球的原因之一。
因为阻焊膜与助焊剂有一定的亲合性,阻焊膜加工不良常常会引起锡珠粘附,产生焊锡球。
锡珠产生的原因分析
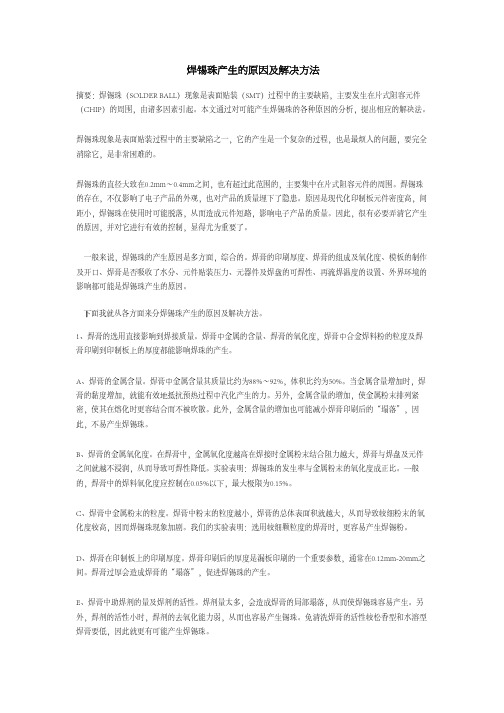
焊锡珠产生的原因及解决方法摘要:焊锡珠(SOLDER BALL)现象是表面贴装(SMT)过程中的主要缺陷,主要发生在片式阻容元件(CHIP)的周围,由诸多因素引起。
本文通过对可能产生焊锡珠的各种原因的分析,提出相应的解决法。
焊锡珠现象是表面贴装过程中的主要缺陷之一,它的产生是一个复杂的过程,也是最烦人的问题,要完全消除它,是非常困难的。
焊锡珠的直径大致在0.2mm~0.4mm之间,也有超过此范围的,主要集中在片式阻容元件的周围。
焊锡珠的存在,不仅影响了电子产品的外观,也对产品的质量埋下了隐患。
原因是现代化印制板元件密度高,间距小,焊锡珠在使用时可能脱落,从而造成元件短路,影响电子产品的质量。
因此,很有必要弄清它产生的原因,并对它进行有效的控制,显得尤为重要了。
一般来说,焊锡珠的产生原因是多方面,综合的。
焊膏的印刷厚度、焊膏的组成及氧化度、模板的制作及开口、焊膏是否吸收了水分、元件贴装压力、元器件及焊盘的可焊性、再流焊温度的设置、外界环境的影响都可能是焊锡珠产生的原因。
㆘面我就从各方面来分焊锡珠产生的原因及解决方法。
1、焊膏的选用直接影响到焊接质量。
焊膏中金属的含量、焊膏的氧化度,焊膏中合金焊料粉的粒度及焊膏印刷到印制板上的厚度都能影响焊珠的产生。
A、焊膏的金属含量。
焊膏中金属含量其质量比约为88%~92%,体积比约为50%。
当金属含量增加时,焊膏的黏度增加,就能有效地抵抗预热过程中汽化产生的力。
另外,金属含量的增加,使金属粉末排列紧密,使其在熔化时更容结合而不被吹散。
此外,金属含量的增加也可能减小焊膏印刷后的“塌落”,因此,不易产生焊锡珠。
B、焊膏的金属氧化度。
在焊膏中,金属氧化度越高在焊接时金属粉末结合阻力越大,焊膏与焊盘及元件之间就越不浸润,从而导致可焊性降低。
实验表明:焊锡珠的发生率与金属粉末的氧化度成正比。
一般的,焊膏中的焊料氧化度应控制在0.05%以下,最大极限为0.15%。
C、焊膏中金属粉末的粒度。
锡珠的产生原因及解决方法

锡珠的产生原因及解决方法锡珠的产生原因及解决方法锡珠现象是smt过程中的主要缺陷,主要发生在片式阻容元件的周围,由诸多因素引起。
它的产生是一个复杂的过程,也是最烦人的问题,要完全消除它,是非常困难的。
锡珠的直径大致在0.2mm——0.4mm之间,也有超过此范围的。
锡珠的存在,不仅影响了电子产品的美观,对产品的质量也有极大的隐患。
我们都知道现在smt工艺中的元件间距小,密度高,若是锡珠在使用时脱落,就可能造成元件短路,影响电子产品的质量。
因此,弄清锡珠产生的原因,并对它进行有效的控制,显得尤为重要了。
锡珠的产生原因是多方面造成的。
锡膏的印刷厚度、其组成及氧化度、模板的制作及开口都有可能造成锡珠现象,同时锡膏是否吸收了水分、元件贴装压力、元器件及焊盘的可焊性、再流焊温度的设置、外界环境的影响都可能是锡珠产生的原因。
下面吉田店铺就从各方面来分锡珠产生的原因及解决方法。
1、锡膏的金属氧化度。
在锡膏中,金属氧化度越高在焊接时金属粉末结合阻力越大,锡膏与焊盘及元件之间就越不浸润,从而导致可焊性降低。
锡珠的发生率与金属粉末的氧化度成正比。
一般的,锡膏中的焊料氧化度应控制在0.05%以下,最大极限为0.15%。
2、锡膏在印制板上的印刷厚度。
锡膏印刷后的厚度是漏板印刷的一个重要参数,通常在0.12mm——0.20mm之间。
锡膏过厚会造成锡膏“塌边”,促进锡珠的产生。
3、锡膏中助焊剂的量及焊剂的活性。
焊剂量太多,会造成锡膏的局部塌落,从而使锡珠容易产生。
另外,焊剂的活性小时,焊剂的去氧化能力弱,从而也容易产生锡珠。
免清洗锡膏的活性较松香型和水溶型锡膏要低,因此就更有可能产生锡珠。
4、此外,锡膏在使用前,一般冷藏在冰箱中,取出来以后应该使其恢复到室温后打开使用,否则,锡膏容易吸收水分,在再流焊锡飞溅而产生锡珠。
58回流焊中锡珠形成的原因及解决方法介绍|南昌回流焊原理2017-03-22 12:44 | #2楼波峰焊第一品牌【精极科技】深圳市精极科技有限公司成立于2002年8月,是一家以设计、生产、销售等工业仓储设备及柔性生产线设备为主的专业生产厂家,同时分销配套的防静电周边产品。
SMT锡珠问题解决

SMT锡珠问题解决焊锡由各种金属合金组成。
由印刷电路板(PCB)装配商使用的锡/铅合金(Sn63/Pb37)是锡膏和用于波峰焊接的锡条或锡线的典型粉末。
在PCB上不是设计所需的位置所找到的焊锡包括锡尘(solderfine)、锡球(solderball)和锡珠(solderbead)。
锡尘是细小的,尺寸接近原始锡膏粉末。
对于-325~+500的网目尺寸,粉末直径是25-45微米,或者大约0.0010-0.0018"。
锡尘是由颗粒的聚结而形成的,所以大于原始的粉末尺寸。
锡珠(solderbeading)是述语,用来区分一种对片状元件独特的锡球(solderballing)(图一)1。
锡珠是在锡膏塌落(slump)或在处理期间压出焊盘时发生的。
在回流期间,锡膏从主要的沉淀孤立出来,与来自其它焊盘的多余锡膏集结,或者从元件身体的侧面冒出形成大的锡珠,或者留在元件的下面。
图一、锡珠IPC-A-610C将0.13mm(0.00512")直径的锡球或每600mm2(0.9in2)面积上少于五颗分为第一类可接受的,并作为第二与第三类的工艺标记2。
IPC-A-610C允许“夹陷的”不干扰最小电气间隙的锡球。
可是,即使是“夹陷的”锡球都可能在运输、处理或在一个振动应用的最终使用中变成移动的。
锡球已经困扰表面贴装工业许多年。
对于只表面贴装和混合技术的PCB,锡珠在许多技术应用中都遇到。
查明相互影响和除掉锡珠的原因可以改善合格率、提供品质、提高长期的可靠性、和降低返工与修理成本。
锡珠的原因人们已经将锡珠归咎于各种原因,包括模板(stencil)开孔的设计、锡膏的成分、阻焊层的选择、模板清洁度、定位、锡膏的重印、焊盘的过分腐蚀、贴片压力、回流温度曲线、波峰焊锡的飞溅、和波峰焊锡的二次回流。
3-5模板开孔的设计模板开孔的形状是在免洗锡膏应用中的一个关键设计参数。
形成一个具有良好焊脚的高质量可靠的焊接点要求有足够的锡膏。
解决锡珠的办法
解决锡珠的办法
从业SMT工艺的朋友最困扰的不良问题估计就是锡珠了,绝大部份是因为"pad尺寸/钢板开窗/零件焊脚三者的不匹配所造成的.简而言之,就是鍚太多了,零件与pad不需要的就会变成鍚珠.尤其是零件底部的鍚膏,没必要的,不需要太多.
其次,就是鍚膏(吸湿,回温不足)或者pcb(HASL PTH内残鍚)所造成的问题,但是这种的现象与上面鍚太多的现象不同,鍚珠会以散布的方式呈现,上面pad尺寸/钢板开窗/零件焊脚三者的不匹配的鍚珠则者会在零件旁依偎式的躲在零件边,很容易分辨的.
造成锡珠的原因:
1.锡膏回温时温湿度不达标,锡膏回温时间不够
2.PCB拆封时间过长,导致PCB受潮,生産过炉时産生锡珠,
3.锡膏印刷厚度偏标准上限,印刷偏移,印刷的不良品,洗板后残留锡粉
4.钢板开口数据有误,人员擦拭钢板时,在湿擦的过程中未能待清洁水完全挥发即开始印锡,造成锡膏扩散
5.人员抹到已印好锡膏的PCB,造成锡膏扩散
6.元件PART DATA高度设定不对,置件速度过快,造成置件压力过大
7.手摆元件造成印锡扩散,元件PAD设置与元件类型不符合
8.回流炉升温斜率过高,恒温时间过长。
锡珠的形成及对策分析
7
而非锡珠(solder beads)
返回
锡珠形成的原因概述
锡珠
是怎样产生的
A 材料的原因
B 工艺的原因
I. 锡膏触变系数大
①
II. 锡膏冷坍塌或轻微热坍塌 ②
III. 焊剂过多或活性温度低
③
IV. 锡粉氧化率高或颗粒不均匀 ④
V. PCB的焊盘间距小
⑤
VI. 刮刀材质硬度小或变形
刮刀
锡膏
焊盘
钢版
9 PCB
返回
PCB 与钢版的间隔
在紧密印刷中不建议有间隔
!!
不建议
印刷钢板
PAD
PAD
线路板
10
不建议
脱模
返回
锡珠形成的原因(贴零件环节)锡膏印刷来自贴零件装 IC
回流焊接
检验
零件贴装部分
a) 贴片压力太大 b) 贴片精度太差 c) 其它因素
11
返回
贴片精度
线路板的精确度 ( PAD,校准点等)
共需要45分钟
介绍
锡珠 的形成和解决 SMT各工艺环节锡珠的预防措施和解决方法 根据鱼骨图逐项排除
3
大纲
相关词汇 (名词解释或定义)
SMT焊接中形成锡珠的现象
(正确的认识,错误的识别)
形成锡珠的原因(各工艺环节)
(印刷,贴件,回流焊接)
不停线调整减少锡珠的暂时对策
(暂时对策)
改良网版设计消除产生锡珠的隐患
14
Solder Beads
返回
其它的预防和改良措施
SMT各层工作人员的素质 SMT管理人员品质标准的培训 SMT 操作人员的相关操作的培训 明确各个工作岗位的权责(该做与不该做) 思想觉悟以及品质意识的提高
SMT产生锡珠的原因及对策
SMT产生锡珠的原因及对策前言在表面着装技术精密发达的时代中,常常发生扰人的问题,其中以在零件部品旁,所发生小锡珠为最常见。
本篇就探讨其发生原因与解决对策,提供使用人在制程上参考。
1.如图a.锡膏在印刷后,零件部品在植装时,置件压力过强,锡膏因此产生挤压。
当进入回焊炉加热时,部品零件温度上升通常比基板来得快,而零件部品下方温度上升较慢。
接着,零件部品的导体(极体)与锡膏接触地方,Flux因温度上升黏度降低,又因部品零件导体上方温度较高而爬升靠近。
所以锡膏是由温度最高Pad外侧开始溶融。
2.如图b.溶融焊锡开始向零件部品的导体处往上爬,溶融焊锡形成像墙壁一般, 接着未溶融焊锡中Flux动向,因溶融焊锡而阻断停止流动,所以Flux无法向外流。
当然所产生挥发溶剂(GAS)也因溶融焊锡而阻断包覆。
3.如图c.锡膏的溶融方向是向Pad的内部进行,Flux也向内部挤压,(GAS)也向内侧移动。
零件部品a.点的下方因力量而使溶融焊锡到达b.点,又因吃锡不良a.点停止下降,产生c.力量逆流,a.b.c.d.的力量,使得焊锡移动。
•零件部品氧化,在导体侧面吃锡是有界线的如图c.所示,结果反而焊锡受压析出形成锡珠。
•另一方面Pad温度较快上升,在Pad上的溶融焊锡先产生回塑效果,无法拉引零件部品,此时的力量使得未溶融焊锡受压析出溶融而形成小锡珠。
•锡膏内Flux易析出气泡,Flux流动力量加上挥发型溶剂的挥发,再加上零件部品在Pad上拉引的力量同时使得未溶融焊锡受挤压析出溶融而形成锡珠。
•锡膏量过多或Pad面积太小,溶融焊锡所保有空间过小也易形成锡珠。
对策零件部品旁发生锡珠的原因很多,需检讨与修正。
1.在设计上Pad的温度,能均匀上升,考虑受热平衡,来决定Pad大小及导体长宽。
2.在设计上考虑锡高的量,零件部品的高度与Pad面积,使得溶融焊锡保有舒展空间。
3.温度曲线不可急遽上升。
4.印刷精度及印刷量的控制,与印刷时的管理。
焊锡珠产生的原因及解决方法
焊錫珠産生的原因及解決方法焊錫珠産生的原因及解決方法摘要: 焊錫珠(SOLDER BALL)現象是表面貼裝(SMT)過程㆗的主要缺陷,主要發生在片式阻容元件(CHIP)的周圍,由諸多因素引起。
本文通過對可能産生焊錫珠的各種原因的分析,提出相應的解決方法。
焊錫珠現象是表面貼裝過程㆗的主要缺陷之㆒,它的産生是㆒個複雜的過程,也是最煩㆟的問題,要完全消除它,是非常困難的。
焊錫珠的直徑大致在0.2mm〜0.4mm 之間,也有超過此範圍的,主要集㆗在片式阻容元件的周圍。
焊錫珠的存在,不僅影響了電子産品的外觀,也對産品的質量埋㆘了隱患。
原因是現代化印製板元件密度高,間距小,焊錫珠在使用時可能脫落,從而造成元件短路,影響電子産品的質量。
因此,很有必要弄清它産生的原因,並對它進行有效的控制,顯得尤爲重要了。
㆒般來說,焊錫珠的産生原因是多方面,綜合的。
焊膏的印刷厚度、焊膏的組成及氧化度、模板的製作及開口、焊膏是否吸收了水分、元件貼裝壓力、元器件及焊盤的可焊性、再流焊溫度的設置、外界環境的影響都可能是焊錫珠産生的原因。
㆘面我就從各方面來分焊錫珠産生的原因及解決方法。
1、焊膏的選用直接影響到焊接質量。
焊膏㆗金屬的含量、焊膏的氧化度,焊膏㆗合金焊料粉的粒度及焊膏印刷到印製板㆖的厚度都能影響焊珠的産生。
A、焊膏的金屬含量。
焊膏㆗金屬含量其質量比約爲88%〜92%,體積比約爲50%。
當金屬含量增加時,焊膏的黏度增加,就能有效㆞抵抗預熱過程㆗汽化産生的力另外,金屬含量的增加,使金屬粉末排列緊密,使其在熔化時更容結合而不被吹散。
- 1、下载文档前请自行甄别文档内容的完整性,平台不提供额外的编辑、内容补充、找答案等附加服务。
- 2、"仅部分预览"的文档,不可在线预览部分如存在完整性等问题,可反馈申请退款(可完整预览的文档不适用该条件!)。
- 3、如文档侵犯您的权益,请联系客服反馈,我们会尽快为您处理(人工客服工作时间:9:00-18:30)。
几种SMT焊接缺陷及其解决措施2002-5-30 13:48:54 阅读427次双击鼠标自动滚屏,单击停止 1 引言表面组装技术在减小电子产品体积重量和提高可靠性方面的突出优点,迎合了未来战略武器洲际射程、机动发射、安全可靠、技术先进的特点对制造技术的要求。
但是,要制定和选择适合于具体产品的表面组装工艺不是简单的事情,因为SMT 技术是涉及了多项技术的复杂的系统工程,其中任何一项因素的改变均会影响电子产品的焊接质量。
元器件焊点的焊接质量是直接影响印制电路组件(PWA)乃至整机质量的关键因素。
它受许多参数的影响,如焊膏、基板、元器件可焊性、丝印、贴装精度以及焊接工艺等。
我们在进行SMT工艺研究和生产中,深知合理的表面组装工艺技术在控制和提高SMT生产质量中起到至关重要的作作。
本文就针对所遇到的几种典型焊接缺陷产生机理进行分析,并提出相应的工艺方法来解决。
2 几种典型焊接缺陷及解决措施2.1 波峰焊和回流焊中的锡球锡球的存在表明工艺不完全正确,而且电子产品存在短路的危险,因此需要排除。
国际上对锡球存在认可标准是:印制电路组件在600范围内不能出现超过5个锡球。
产生锡球的原因有多种,需要找到问题根源。
2.1.1 波峰焊中的锡球波峰焊中常常出现锡球,主要原因有两方面:第一,由于焊接印制板时,印制板上的通孔附近的水分受热而变成蒸汽。
如果孔壁金属镀层较薄或有空隙,水汽就会通过孔壁排除,如果孔内有焊料,当焊料凝固时水汽就会在焊料内产生空隙(针眼),或挤出焊料在印制板正面产生锡球。
第二,在印制板反面(即接触波峰的一面)产生的锡球是由于波峰焊接中一些工艺参数设置不当而造成的。
如果助焊剂涂覆量增加或预热温度设置过低,就可能影响焊剂内组成成分的蒸发,在印制板进入波峰时,多余的焊剂受高温蒸发,将焊料从锡槽中溅出来,在印制板面上产生不规则的焊料球。
针对上述两面原因,我们采取以下相应的解决措施:第一,通孔内适当厚度的金属镀层是很关键的,孔壁上的铜镀层最小应为25um,而且无空隙。
第二,使用喷雾或发泡式涂覆助焊剂。
发泡方式中,在调节助焊剂的空气含量时,应保持尽可能产生最小的气泡,泡沫与PCB接触面相对减小。
第三,波峰焊机预热区温度的设置应使线路板顶面的温度达到至少100°C。
适当的预热温度不仅可消除焊料球,而且避免线路板受到热冲击而变形。
2.1.2 回流焊中的锡球2.1.2.1 回流焊中锡球形成的机理回流焊接中出的锡球,常常藏于矩形片式组件两端之间的侧面或细距引脚之间。
在组件贴装过程中,焊膏被置于片式组件的引脚与焊盘之间,随着印制板穿过回流焊炉,焊膏熔化变成液体,如果与焊盘和器件引脚等润湿不良,液态焊锡会因收缩而使焊缝填充不充分,所有焊料颗粒不能聚合成一个焊点。
部分液态焊锡会从焊缝流出,形成锡球。
因此,焊锡与焊盘和器件引脚润湿性差是导致锡球形成的根本原因。
2.1.2.2 原因分析与控制方法造成焊锡润湿性差的原因很多,以下主要分析与相关工艺有关的原因及解决措施:a)回流温度曲线设置不当。
焊膏的回流是温度与时间的函数,如果未到达足够的温度或时间,焊膏就不会回流。
预热区温度上升速度过快,达到平顶温度的时间过短,使焊膏内部的水分、溶剂未完全挥发出来,到达回流焊温区时,引起水分、溶剂沸腾,溅出焊锡球。
实践证明,将预热区温度的上升速度控制在1~4°C/s是较理想的。
b)如果总在同一位置上出现焊球,就有必要检查金属板设计结构。
模板开口尺寸腐蚀精度达不到要求,对于焊盘大小偏大,以及表面材质较软(如铜模板),造成漏印焊膏的外形轮廓不清晰,互相桥连,这种情况多出现在对细间距器件的焊盘漏印时,回流焊后必然造成引脚间大量锡珠的产生。
因此,应针对焊盘图形的不同形状和中心距,选择适宜的模板材料及模板制作工艺来保证焊膏印刷质量。
c)如果在贴片至回流焊的时间过长,则因焊膏中焊料粒子的氧化,焊剂变质、活性降低,会导致焊膏不回流,焊球则会产生。
选用工作寿命长一些的焊膏(我们认为至少4小时),则会减轻这种影响。
d)另外,焊膏印错的印制板清洗不充分,使焊膏残留于印制板表面及通孔中。
回流焊之前,被贴放的元器件重新对准、贴放,使漏印焊膏变形。
这些也是造成焊球的原因。
因此应加强操作者和工艺人员在生产过程的责任心,严格遵照工艺要求和操作规程行生产,加强工艺过程的质量控制。
2.2立片问题(曼哈顿现象)矩形片式组件的一端焊接在焊盘上,而另一端则翘立,这种现象就称为曼哈顿现象。
引起该种现象主要原因是组件两端受热不均匀,焊膏熔化有先后所致。
在以下情况会造成组件两端热不均匀:a)有缺陷的组件排列方向设计。
我们设想在再流焊炉中有一条横跨炉子宽度的再流焊限线,一旦焊膏通过它就会立即熔化,如图1所示。
片式矩形组件的一个端头先通过再流焊限线,焊膏先熔化,完全浸润组件的金属表面,具有液态表面张力;而另一端未达到183°C液相温度,焊膏未熔化,只有焊剂的粘接力,该力远小于再流焊焊膏的表面张力,因而,使未熔化端的组件端头向上直立。
因此,保持组件两端同时进入再流焊限线,使两端焊盘上的焊膏同时熔化,形成均衡的液态表面张力,保持组件位置不变。
b)在进行汽相焊接时印制电路组件预热不充分。
汽相焊是利用惰性液体蒸汽冷凝在组件引脚和PCB焊盘上时,释放出热量而熔化焊膏。
汽相焊分平衡区和饱和蒸汽区,在饱和蒸汽区焊接温度高达217°C,在生产过程中我们发现,如果被焊组件预热不充分,经受一百多度的温差变化,汽相焊的汽化力容易将小于1206封装尺寸的片式组件浮起,从而产生立片现象。
我们通过将被焊组件在高低箱内以145°C-150°C的温度预热1-2分钟,然后在汽相焊的平衡区内再预热1分钟左右,最后缓慢进入饱和蒸汽区焊接消除了立片现象。
c)焊盘设计质量的影响。
若片式组件的一对焊盘大小不同或不对称,也会引起漏印的焊膏量不一致,小焊盘对温度响应快,其上的焊膏易熔化,大焊盘则相反,所以,当小焊盘上的焊膏熔化后,在焊膏表面张力作用下,将组件拉直竖起。
焊盘的宽度或间隙过大,也都可能出现立片现象。
严格按标准规范进行焊盘设计是解决该缺陷的先决条件。
2.3 细间距引脚桥接问题导致细间距元器件引脚桥接缺陷的主要因素有:a)漏印的焊膏成型不佳;b)印制板上有缺陷的细间距引线制作;c)不恰当的回流焊温度曲线设置等。
因而,应从模板的制作、丝印工艺、回流焊工艺等关键工序的质量控制入手,尽可能避免桥接隐患。
2.3.1模板材料的选择SMT工艺质量问题70%出至于印刷这到工序,而模板是必不可少的关键工装,直接影响印刷质量。
通常我们使用的模板材料是铜板和不锈钢板,不锈钢板与铜板相比有较小的摩擦系数和较高的弹性,因此在其它条件一定的情况下,更有利于焊膏脱模和焊膏成型效果好。
通过0.5mm引脚中心距QFP208器件组装试验统计,因铜模板漏印不合格而造成的疵点数占器件总焊点数(208个)的20%左右;在其它条件一定的情况下,利用不锈钢模板漏印,造成的疵点率平均为3%。
因此,对引脚中心距为0.635mm以下的细间距元器件的印刷,提出必须采用不锈钢板的要求,厚度优选0.15mm~0.2mm.。
2.3.2丝印过程工艺控制焊膏在进行回流焊之前,若出现坍塌,成型的焊膏图形边不清晰,在贴放元器件或进入回流焊预热区时,由于焊膏中的助焊剂软化,则会造成引脚桥接。
焊膏的坍塌是由于使用了不合适的焊膏材料和不宜的环境条件,如较高的室温会造成焊膏坍塌。
在丝印工序中,我们通过以下工艺的调整,小心地控制焊膏的流变特性,减少了坍塌。
a)丝印细间距引线,通常选用厚度较薄的模板,为避免漏印的焊膏量偏少,所需的焊膏黏度应较低,这样焊膏流动性好,易漏印,而且模板与PCB脱模时不易带走焊膏,保证焊膏涂覆量。
但同时为了保持焊膏印刷图形的理想形态,又需要较高的焊膏黏度。
我们解决这一矛盾的方法是选用45-75um的更小粒度和球形颗粒焊膏,如爱法公司的RMA390DH3型焊膏。
另外,在丝印时保持适宜的环境温度,焊膏黏度与环境温度的关系式表示如下:logu=A/T+B ---------------(1)式中:u —粘度系数;A,B—常数T—绝对温度。
通过上式可看出,温度越高,粘度越小。
因此,为获得较高的粘度,我们将环境温度控制20+3°C。
b)刮刀的速度和压力也影响焊膏的流变特性。
因为他们决定了焊膏所受的剪切速率和剪切力大小。
焊膏黏度与剪切速率的关系如图2所示。
在焊膏类型和环境温度较合适的情况下,在刮刀压力一定的情况下,将印刷速度调慢,可以保持焊膏黏度基本不变,这样供给焊膏的时间加长,焊膏量就增多,而且有好的成型。
另外,控制脱模速率的减慢和模板与PCB的最小间隙,也会在减少细间距引脚桥接方面起到良好的效果。
根据我们使用的SP200型丝印机,我们认为印刷细间距线较理想的工艺参数是:印刷速度保持在10mm/s-25mm/s;脱模速率控制在2s左右;模板与PCB的最小间隙小于等于0.2mm。
2.3.3 回流过程工艺控制细间距引线间的间距小、焊盘面积小、漏印的焊膏量较少,在焊接时,如果红外再流焊的预热区温度较高、时间较长,会将较多的活化剂在达到回流焊峰值温度区域前就被耗尽。
然而,只有当在峰值区域内有充足的活化剂释放被氧化的焊粒,使焊粒快速熔化,从而湿润金属引脚表面,形成良好的焊点。
免清洗焊膏,活化程比要清洗的焊膏低,所以如果预热温度和预热时间设置稍不恰当,便会出现焊接细间引线桥接现象。
我们通过降低热温度和缩短预热时间控制焊膏中活化剂的挥发,保证了免清冼焊膏在焊接温度区域的流动性和对金属引线表面的润湿性,减少了细间距线的桥接缺陷。
针对细间距器件和阻容器件,我们采用的回流温度焊接曲线典型例图如图3所示。
3 结束语随着表面组装技术更广泛、更深入的应用于各个领域,SMT焊接质量问题引起人们高度重视,SMT焊接质量与整个组装工艺流程各个环节密切相关,为了减少或避免上上述焊接缺陷的出现,不仅要提高工艺人员判断和解决这些问题能力,另外还要注重提高工艺质量控制技术、完善工艺管理,制定出有效的控制方法,才能提高SMT焊接质量,保证电子产品的最终质量。
本文若有不对之处,请予以指正。