高炉卷料系统文档 (2)
高炉自动上料(配料)控制系统的设计与制作

课题:高炉自动上料(配料)控制系统的设计与制作系部:机电工程学院专业:电气自动化技术班级:姓名:李瑞学号:指导老师:2019.3.15目录摘要 (31)第一章序言 (31)1.1课题意义 (32)1.2课题来源 (33)1.3国内外高炉自动控制系统的研究现状和趋势 (33)1.3.1高炉计算机控制发展 (33)1.3.2炼铁自动化技术的现状 (34)1.3.3高炉自动化系统的发展趋势 (34)1.4毕业设计主要任务 (35)1.5本章小结 (35)第2章高炉上料生产工艺 (35)2.1高炉上料系统的组成与工作原理 (36)2.1.1高炉上料系统自动控制概述 (37)2.1.2高炉上料控制系统流程 (37)2.2高炉炼铁生产工艺简介 (39)第三章可编程控制器及PID控制 (39)3.1可编程控制器 (40)3.2PID控制 (41)第四章高炉上料系统的软件设计 (42)4.1PLC程序设计 (42)4.2槽下设备运转控制 (45)4.3主卷上料小车的连锁控制 (45)结束语 (47)谢辞 (47)参考文献 (48)在冶金企业中,高炉给料系统是一个非常重要的复杂的设备系统。
为了保证高炉进料的稳定、安全、高效工作,高炉进料计算机自动控制的设计与实现显得尤为重要。
在提高控制系统控制精度的基础上,进一步提高了高炉进给操作的可靠性、安全性和稳定性,为高炉的生产提供了可靠的保证。
本文结合实际科研项目——高炉进料系统自动改造,开发设计了一套高炉进料生产线自动控制系统。
本项目跟踪国内外先进技术,采用目前先进的无钟炉具设备,提高设备可靠性,降低备件消耗,节约成本。
在国内外生产过程控制技术发展的基础上,开发设计了可编程控制器控制系统。
在本系统中,PLC作为核心部件,对整个生产线起到监控作用,各种电磁阀等机械部件发出控制指令,并结合组态软件完成论文的要求。
根据PLC的输入和输出点进行硬件配置;根据PLC编程的特点,采用与工厂电路图最接近的方法——梯形图编制软件,并将软件划分为几个模块。
高炉槽下上料系统操作说明书
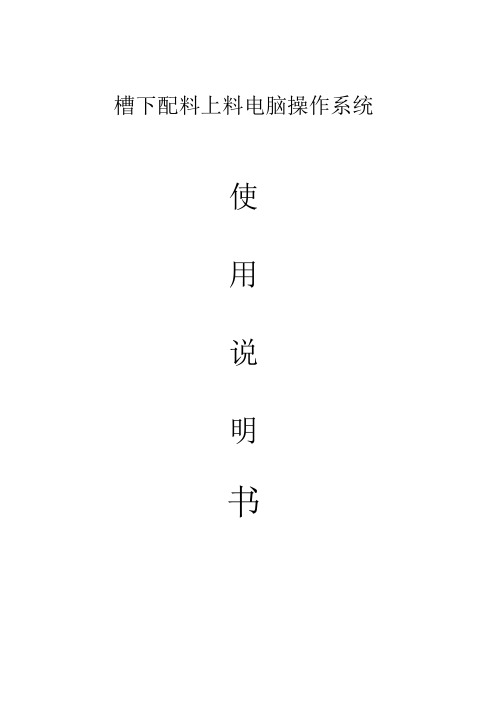
槽下配料上料电脑操作系统使用说明书1. 概述本系统实现了槽下14个振动筛、4个给料机、14个称量斗门、6条皮带、14个除尘闸门、1个上料卷扬的画面上的手自动操作。
具有手动时灵活、可靠和自动时运行稳定的特点。
槽下分为两部分进行控制,从给料机到中间斗为备料流程,从中间斗到炉顶为上料流程。
见下图。
2.基本操作2.1. 单台设备的操作2.1.1. 给料机和振动筛的操作▲自动状态时设备被程序所控制,按照连锁条件运行。
当切换到手动时设备由操作窗口内的“启动”,“停止”按钮来控制▲连锁状态选择,设备连锁时会对流程前后的设备的运行状态有影响,如振动筛不运行,给料机不能运行;皮带机不运行,振动筛不能运行;称量斗非空,振动筛不能运行;⏹手动状态下解锁时一定要考虑周全,以应对非正常情况。
⏹自动状态下不允许切换到解锁。
▲起停操作。
左键单击相应按钮,便可以在手动时操作设备。
自动时无效。
▲状态显示。
⏹PC控制方式。
方框显示绿色表示现场操作箱上切换到远程操作,否则为就地。
⏹自动状态。
方框显示绿色表示设备切换到远程且自动状态。
⏹故障状态。
方框显示黄色表示设备的电气回路出现故障且设备停机。
⏹电源状态。
方框显示绿色表示⏹运行状态。
方框显示红色表示设备处于停止状态,方框显示绿色表示设备处于运行状态。
2.1.2.称量斗门的操作▲自动状态选择⏹自动状态选择时设备被程序所控制,按照连锁条件运行。
当切换到手动时设备由操作窗口内的“启动”,“停止”按钮来控制▲连锁状态选择⏹设备连锁时会对流程前后的设备的运行状态有影响,如皮带机不运行,斗门不能关闭,称量斗非满,则斗门不能打开。
⏹手动状态下解锁时一定要考虑周全,以应对非正常情况。
⏹自动状态下不允许切换到解锁。
▲开关操作按钮⏹左键单击相应按钮,便可以在手动时操作设备。
自动时无效。
▲回路状态显示。
⏹PC控制方式。
方框显示绿色表示现场操作箱上切换到远程操作,否则为就地。
⏹自动状态。
方框显示绿色表示设备切换到远程且自动状态。
第三章 高炉炼铁的上料系统

3.1.1 贮矿槽极其附属设备
3.1.1.2 闭锁装置
一般每个贮矿槽设有两个漏嘴,漏嘴上应装有闭 锁装置,即闭锁器。其作用是开关漏嘴,并调节 流量。
基本要求是:应有足够的供料能力;料流均匀连 续且稳定并可以调节;能正确锁住料流,不卡不 漏;结构简单,易于维修。
常用的闭锁装置:启闭器和给料机。
精选可编辑ppt
19
精选可编辑ppt
20
3.2.1 料车式上料设备
料车上料设备主要由料车、斜桥和卷扬机三部分组成。有两 种形式,一种为卷扬机安装在斜桥下面,另一种为卷扬机安 装在斜桥上面。
3.2.1.1 料车 一般高炉配备两个料车。容积一般为高炉有效容积的0.7 -
1.0%。大多以增加料车宽度和高度,并扩大开口的办法来扩 大料车容积,很少用加长料车的办法。料车由车体、车轮、 辕架三部分组成。 料车的车体一般由10~12mm钢板焊成,车体后部作成圆角以 防矿粉粘结,在尾部上方有一个小窗口,供撒在料车坑内的 料装回料车。 料车的前后两对车轮结构不同,前轮只能沿主轨道滚动,后 轮不仅沿主轨道,而且在炉顶曲轨段还要沿辅助轨道滚动。 所以,前轮只有一个踏面,轮缘在斜桥轨道的内侧;后轮做 成两个踏面,轮缘在两个踏面之间。 辕架是一个金属的门形框架,它与车体活动连接,便于辕架 与车体作相对转动。一般牵引料车是采用双钢丝绳结构。
5
3.1.1 贮矿槽极其附属设备
(2)贮矿槽贮存能力
是指贮矿槽的贮存量或者贮存可供生产的时间。
决定贮矿槽贮存能力的因素:
① 与原、燃料原始贮存能力有关 。 原、燃料生产能力大的, 贮矿槽贮存能力可少些;反之,贮矿槽贮存能力要大;
② 与外部运输方式有关 。 用火车运输装卸,调运环节多,贮 矿槽贮存能力要大些;用皮带输送到贮矿槽,贮矿槽贮存能力 可少些;
高炉装料系统安全技术(2篇)
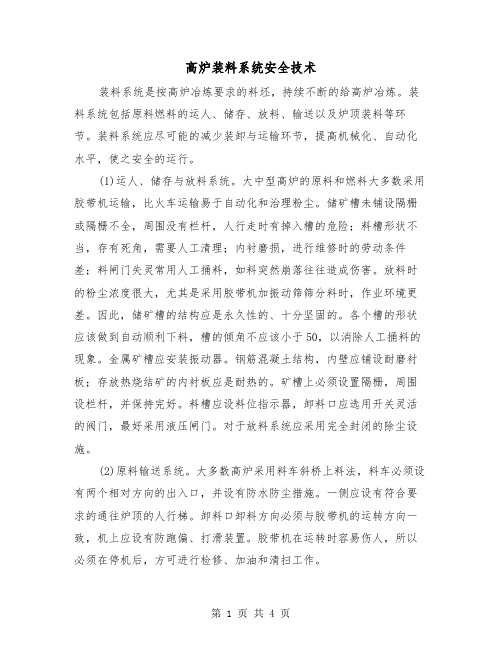
高炉装料系统安全技术装料系统是按高炉冶炼要求的料坯,持续不断的给高炉冶炼。
装料系统包括原料燃料的运人、储存、放料、输送以及炉顶装料等环节。
装料系统应尽可能的减少装卸与运输环节,提高机械化、自动化水平,使之安全的运行。
(1)运人、储存与放料系统。
大中型高炉的原料和燃料大多数采用胶带机运输,比火车运输易于自动化和治理粉尘。
储矿槽未铺设隔栅或隔栅不全,周围没有栏杆,人行走时有掉入槽的危险;料槽形状不当,存有死角,需要人工清理;内衬磨损,进行维修时的劳动条件差;料闸门失灵常用人工捅料,如料突然崩落往往造成伤害。
放料时的粉尘浓度很大,尤其是采用胶带机加振动筛筛分料时,作业环境更差。
因此,储矿槽的结构应是永久性的、十分坚固的。
各个槽的形状应该做到自动顺利下料,槽的倾角不应该小于50,以消除人工捅料的现象。
金属矿槽应安装振动器。
钢筋混凝土结构,内壁应铺设耐磨衬板;存放热烧结矿的内衬板应是耐热的。
矿槽上必须设置隔栅,周围设栏杆,并保持完好。
料槽应设料位指示器,卸料口应选用开关灵活的阀门,最好采用液压闸门。
对于放料系统应采用完全封闭的除尘设施。
(2)原料输送系统。
大多数高炉采用料车斜桥上料法,料车必须设有两个相对方向的出入口,并设有防水防尘措施。
一侧应设有符合要求的通往炉顶的人行梯。
卸料口卸料方向必须与胶带机的运转方向一致,机上应设有防跑偏、打滑装置。
胶带机在运转时容易伤人,所以必须在停机后,方可进行检修、加油和清扫工作。
(3)顶炉装料系统。
通常采用钟式向高炉装料。
钟式装料以大钟为中心,有大钟、料斗、大小钟开闭驱动设备、探尺、旋转布料等装置组成。
采用高压操作必须设置均压排压装置。
做好各装置之间的密封,特别是高压操作时,密封不良不仅使装置的部件受到煤气冲刷,缩短使用寿命,甚至会出现大钟掉到炉内的事故。
料钟的开闭必须遵守安全程序。
为此,有关设备之间必须连锁,以防止人为的失误。
高炉装料系统安全技术(2)高炉装料系统是高炉生产过程中至关重要的一个环节,其安全性对于高炉的正常运行和工人的安全至关重要。
高炉上车上料自动控制系统

高炉双车上料自动控制系统摘要:主卷扬控制系统是保证高炉正常连续生产的关键设备之一。
在炼铁高炉的生产中,主令控制器是卷扬最为关键的核心控制设备,一旦上料的主卷扬发生故障维护及调整非常麻烦,将直接导致整个炼铁高炉生产的停滞,造成高炉上料中断,给炼铁生产带来重大经济损失。
高炉炼铁生产过程的自动控制程度的高低,直接制约着铁水的产量和质量。
因此高炉主卷扬是高炉炼铁的重要环节之一。
高炉上料卷扬系统是炼铁生产中的关键设备,主要作用是将炼铁所需的各种原料源源不断地送到高炉内,保证高炉炼铁的正常需要,考虑到上料的速度、设备的备用要求等诸多因素,目前普遍选用单筒双电机双料车的卷扬系统。
本文将对此进行分析和讨论。
介绍了在采用PLC和变频器实现高炉主卷扬料车常规控制的基础上,利用旋转编码器发出的脉冲信号构成位置反馈,实现料车的精确位移控制的智能主令控制器的应用情况。
改变了原有用LK系列的机械式有触点主令故障率高的缺点。
通过PLC程序设计实现料车加减速换速信号、到位信号的数字控制,提高了系统的可靠性和位置精度控制。
本设计是基于PLC控制、组态软件监控显示、变频器调速的高炉配料自动控制系统,而系统以PLC控制为核心。
本设计为4种原料的配料系统,PLC、变频器分别为西门子公司的S7-300和施耐德A TV71变频器。
PLC程序的开发以西门子公司的Step7作为软件平台,采用了面向对象的程序设计技术,模块化的设计,从而使系统具有良好的可移植性和可维护性。
关键词:主卷扬,料车,上料,可编程控制器,位移智能主令控制器AbstractHoist the main blast furnace control system is the guarantee forthe normal production of one of the key equipment. Blast furnace inthe production of the main winch controller is the core of the mostcritical control equipment, once the main winch on the expectedfailure of maintenance and adjustment is very troublesome, willlead directly to the blast furnace production of stagnation,resulting in BF Feeding disruption to the production ofiron-smelting result in major economic loss. Iron making blastfurnace production process of high and low degree of automation,molten iron directly restrict the quantity and quality. So the mainblast furnace blast furnace iron making winch is one of theimportant links. BF expected winch system is the key to theproduction of iron-smelting equipment, primary role is toiron-smelting of raw materials required to continue to blastfurnace, the blast furnace iron making guarantee the normal needs,taking into account the expected rate, Equipment reserverequirements and other factors, generally selected Dandongdouble-double motor vehicle winch system. This article will conductanalysis and discussion.On the PLC in a blast furnace and converter to achieve the mainwinch control of conventional cars expected on the basis of arotating encoder pulse a position feedback, expected to achieve theprecise control of the displacement of the main controller of thesmart application. LK used to change the original series ofmechanical contact with the main shortcomings of the high failurerate. PLC program designed to achieve through the expected slowdownfor cars and speed signals, the digital control signals in placeand improve system reliability and location accuracy control. Thedesign is based on the PLC control, configuration softwaremonitoring display, Drives governor of BF ingredients automaticcontrol system, and PLC control system as the core. The four kindsof raw materials for the design of the batching system, PLC,Siemens converter for the S7-300, SchneiderA TV71.Feeding the ACdrive system using the Siemens 6 SE70 vector-type converter and PLCcombination to achieve. PLC program to the development of theSiemens Step7 as a software platform, using the object-orientedprogramming techniques, modular design, so that the system has goodportability and maintainability.Keywords:Master winch,Liu car,Feeding,PLC,The main displacementintelligent controller目录摘要 1 Abstract 20引言 41 主卷扬工艺简介 6 1.1 上料系统概况 6 1.2 上料系统在高炉的地位与作用7 1.3 基本工艺要求91.4 设计要求92 高炉卷扬控制系统13 2.1 卷扬系统简介及工艺描述13 2.2 控制方案16 2.3 料车定位202.4 高炉上料监视系统233 系统软/硬件说明28 3.1 变频器的简介及选型283.2 PLC程序设计334 设计图纸说明46 4.1 主回路说明46 4.2 控制回路及动作说明47 结束语49 谢辞50 参考文献51。
高炉上料系统施工方案

高炉上料系统施工方案1 引言高炉上料系统是高炉炼铁的关键环节之一,直接影响到生产效率和产品质量。
本文档旨在提供一个高炉上料系统施工方案,包括系统的设计、安装、调试等方面的内容。
2 系统设计2.1 系统功能高炉上料系统的主要功能包括原料的输送与配比、料斗的卸料、输送线的控制和监测等。
具体功能如下: - 原料配比:根据高炉冶炼工艺要求,将不同种类和比例的原料按照要求进行配比。
- 料斗卸料:将配制好的原料从料斗中卸下,并送入相应的输送线。
- 输送线控制:控制输送线的启停、速度调节等,确保原料的顺利输送。
- 监测:对原料的流量、温度、湿度等进行监测,以便及时调整系统参数。
2.2 系统组成高炉上料系统主要由以下几个部分组成: - 天车:用于将原料从存料仓库中取出,运送到指定的料斗。
- 料斗:用于存放原料,并通过卸料口将原料送入输送线。
- 输送线:用于将原料从料斗中输送到高炉的上料口。
- 控制系统:包括PLC控制、传感器监测和人机界面等,用于控制和监测整个系统的运行。
3 施工过程3.1 前期准备在施工之前,需要进行一系列的前期准备工作,包括: - 设计方案:根据高炉的工艺要求和现场情况,制定高炉上料系统的设计方案。
- 采购原材料和设备:根据设计方案,采购所需的原材料和设备。
- 组织人员:安排项目经理、施工人员和监理人员等,确保施工过程的顺利进行。
3.2 安装和调试安装和调试是高炉上料系统施工的关键环节,包括以下步骤: - 天车安装:将天车安装在指定位置,并进行调试,确保其正常运行。
- 料斗安装:将料斗安装在指定位置,并与天车和输送线连接,进行调试。
- 输送线安装:将输送线安装在指定位置,并与料斗和高炉上料口连接,进行调试。
- 控制系统安装:安装PLC控制器、传感器和人机界面,进行调试和联动测试。
3.3 系统验收在施工完成后,进行系统验收是必不可少的步骤。
验收过程中需要完成以下内容: - 系统功能测试:对高炉上料系统的各项功能进行测试,检查其是否满足设计要求。
高炉原燃料供应系统
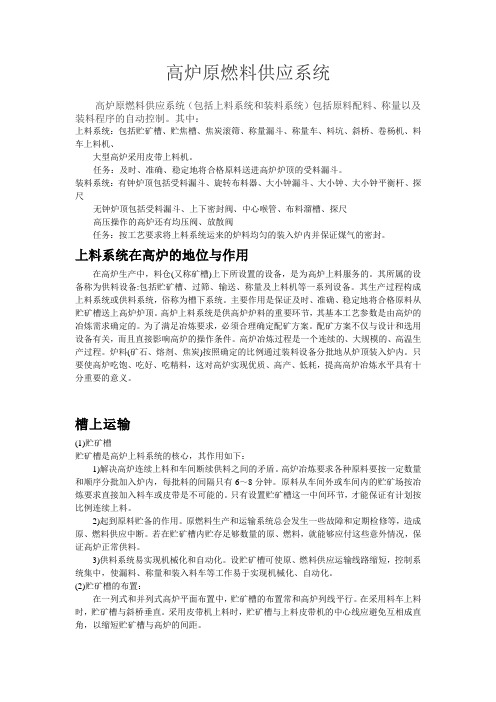
高炉原燃料供应系统高炉原燃料供应系统(包括上料系统和装料系统)包括原料配料、称量以及装料程序的自动控制。
其中:上料系统:包括贮矿槽、贮焦槽、焦炭滚筛、称量漏斗、称量车、料坑、斜桥、卷杨机、料车上料机、大型高炉采用皮带上料机。
任务:及时、准确、稳定地将合格原料送进高炉炉顶的受料漏斗。
装料系统:有钟炉顶包括受料漏斗、旋转布料器、大小钟漏斗、大小钟、大小钟平衡杆、探尺无钟炉顶包括受料漏斗、上下密封阀、中心喉管、布料溜槽、探尺高压操作的高炉还有均压阀、放散阀任务:按工艺要求将上料系统运来的炉料均匀的装入炉内并保证煤气的密封。
上料系统在高炉的地位与作用在高炉生产中,料仓(又称矿槽)上下所设置的设备,是为高炉上料服务的。
其所属的设备称为供料设备:包括贮矿槽、过筛、输送、称量及上料机等一系列设备。
其生产过程构成上料系统或供料系统,俗称为槽下系统。
主要作用是保证及时、准确、稳定地将合格原料从贮矿槽送上高炉炉顶。
高炉上料系统是供高炉炉料的重要环节,其基本工艺参数是由高炉的冶炼需求确定的。
为了满足冶炼要求,必须合理确定配矿方案。
配矿方案不仅与设计和选用设备有关,而且直接影响高炉的操作条件。
高炉冶炼过程是一个连续的、大规模的、高温生产过程。
炉料(矿石、熔剂、焦炭)按照确定的比例通过装料设备分批地从炉顶装入炉内。
只要使高炉吃饱、吃好、吃精料,这对高炉实现优质、高产、低耗,提高高炉冶炼水平具有十分重要的意义。
槽上运输(1)贮矿槽贮矿槽是高炉上料系统的核心,其作用如下:1)解决高炉连续上料和车间断续供料之间的矛盾。
高炉冶炼要求各种原料要按一定数量和顺序分批加入炉内,每批料的间隔只有6~8分钟。
原料从车间外或车间内的贮矿场按冶炼要求直接加入料车或皮带是不可能的。
只有设置贮矿槽这一中间环节,才能保证有计划按比例连续上料。
2)起到原料贮备的作用。
原燃料生产和运输系统总会发生一些故障和定期检修等,造成原、燃料供应中断。
若在贮矿槽内贮存足够数量的原、燃料,就能够应付这些意外情况,保证高炉正常供料。
高炉二级系统方案
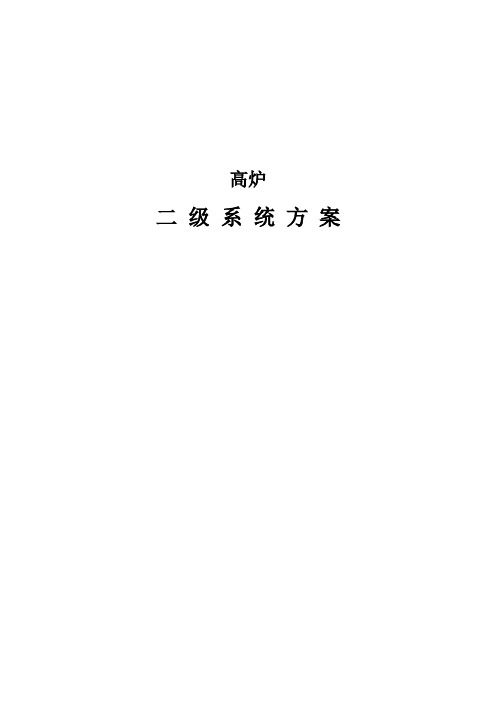
高炉二级系统方案“高炉二级系统”是基于高炉基础自动化系统之上的高炉管理系统,本系统通过OPC从一级自动化系统采集实时数据,存储于高炉二级系统的数据库,通过对这些数据的统计、计算、汇总、分析等一系列专业技术处理,完成实时数据显示、历史趋势显示、风口管理、出铁管理、物料成分管理、变料管理、报表管理等功能,为高炉的生产操作、管理和决策提供了有力的支持。
高炉二级系统已成为炼铁生产过程中不可或缺的组成部分。
1. 数据采集现代大型高炉检测和自动化系统的投入对高炉低能耗、提高生产效率以及稳定运行都起到了十分重要的作用,同时,大量的监测数据也为操作人员作出最佳决策提供了重要的依据。
因此,高炉相关数据采集应尽量全面和及时。
1.1. 定周期数据采集数据采集周期为1分钟。
定周期采集的数据有以下几部分:操作参数:风量、风温、热风压力、冷风压力、顶压、压差、富氧量、富氧率、顶温最高、顶温最低、顶温平均、喷煤量、大气湿度。
炉身部分:炉喉、炉基、炉衬温度测点。
炉顶十字测温数据。
冷却壁部分:铸铁冷却壁、铜冷却壁、高炉本体供水系统温度、流量、压力。
动力消耗:蒸汽流量、氧气流量、压缩空气流量。
布袋除尘:箱体和主管的温度、压力、压差、箱体及管道内粉尘检测值、箱体反吹时间等。
水温差及炉皮温度数据。
以上所有数据按小时、班、天进行统计、计算、汇总并保存到数据库中,用于形成报表、历史趋势图及查询。
1.2. 实时数据采集实时数据采集包括:焦炭称量数据、焦炭水分数据、矿称量数据、高炉布料数据。
以上所有数据按班、天进行统计、计算、汇总并保存到数据库中,用于形成报表及查询。
1.3. 定周期写回一级因高炉一级系统自身无法进行复杂化计算,本系统根据定周期采集的数据自动计算透气性、炉腹煤气量、透气阻力系数、标准风速、实际风速、鼓风动能、理论燃烧温度等高炉操作标参数并写回到一级,用于指导一级的操作。
回写周期为1分钟。
以上所有数据按小时、班、天进行统计、计算、汇总并保存到数据库中,用于形成报表、历史趋势图及查询。
- 1、下载文档前请自行甄别文档内容的完整性,平台不提供额外的编辑、内容补充、找答案等附加服务。
- 2、"仅部分预览"的文档,不可在线预览部分如存在完整性等问题,可反馈申请退款(可完整预览的文档不适用该条件!)。
- 3、如文档侵犯您的权益,请联系客服反馈,我们会尽快为您处理(人工客服工作时间:9:00-18:30)。
一、高炉卷扬上料及布料过程简介高炉上料的形式主要有两种:一是卷扬料车上料,二是皮带上料,由于料车上料占地面积小,在中小高炉中得到广泛的应用,如中型高炉卷扬系统采用双电机控制,小高炉采用单电机控制。
卷扬上料系统的主要过程是:各种原料经过槽下配料后放入中间料斗,料车到料坑后,中间斗把料放入料车,中间斗闸门关到位并且炉顶准备好后,料车启动,经过加速-匀速(高速)-减速1-减速2,到达炉顶。
二、控制系统方案(一)上料及炉顶系统主要电气设备1.卷扬机构交流电机功率160kW,三相交流380伏一台。
2.冷却风机电机3.7kW,三相交流380伏一台。
3.料车制动器1kW,两相交流380伏两台。
4.料车行程编码器,OMRON一台5.智能主令控制器一台6.料车切换柜一面、交流变频传动柜2面,一用一备,制动电阻柜一面7.料车变频器选西门子6SE70 200kW两台,配套制动单元(二)基本工艺要求1.料车卷扬机:料车卷扬机按料车行程曲线运行;2.在PLC及操作台手动方式下,满足高、中、低速调速要求;3.料车启动、停车及加、减速应平稳,速度控制受负载(空载或满载)影响较小;4.主卷扬有钢绳松弛保护和极限张力保护装置(过流保护);5.料车有行程极限,超极限保护装置,低速检查保护;6.料车尚未到达行程终点的卷筒反转保护;在卡车的状态下,可允许停车或有控下行。
(三)设计方案系统框图如图1所示:图1 系统框图1.主卷扬变频调速装置我们采用西门子公司的6SE70全数字交流变频调速供电装置。
系统配置了配套制动单元和独立的制动电阻柜,采用能耗制动方式实现卷扬系统的制动。
供电装置的工作方式选用一备一用方式,通过切换柜中的三刀双掷刀开关完成备用切换。
每个变频器的控制信号通过切换柜的电气设备来完成基本联锁及控制,在主PLC与切换柜之间、操作台与切换柜之间利用继电器相互隔离,使料车的控制可以由PLC或操作台分别控制系统,提高整个系统的可靠性。
抱闸由6SE70装置中的抱闸专用控制功能来实现料车运行中的抱闸控制及联锁控制。
调速装置的交流进线是通过交流进线电抗器解耦,并且进线电抗器设置在电源切换柜中,相当于两套变频器共用一台进线电抗器。
在切换开关后面分别接两台出线电抗器,消除出线高次谐波,保护电机。
料车定位采用绝对值编码器来完成,信号是格雷码,以开关量的形式送给PLC;主令控制器采用增量式编码器,脉冲信号送给主令控制器的内部小PLC。
料车定位编码器器通过Profibus-DP与PLC联网。
2.料车定位高炉卷扬料车的传统定位方式是机械式的主令控制器,目前来看,使用起来有很多问题,定位精度差,现场环境恶劣,机械触点容易氧化,位置发生变化后,必须休风,跑几次空车,调整料车位置。
我们现在采用的方案是智能主令控制器与编码器(PLC)结合对料车进行定位,通过数字面板来调整料车位置,如料车位置发生变化,只需在数字面板上改变料车位置的数值即可完成对料车的定位。
同时,主令控制器所检测到的数据与主PLC中的数据相比较,误差小于允许值时认为定位准确。
3.料车运行简介料车在料坑底部(另一料车在顶部),备料装好后,地坑闸门关闭,炉顶受料斗料空,申请上料,由主PLC发出命令给变频器,6SE70在接到开车命令后系统解封。
通过6SE70系统中的抱闸控制功能,建立在抱闸状态下的转矩限幅给出的启车力矩电流后,6SE70系统发出打开抱闸命令,使抱闸打开,实现料车的平稳启动。
当料车启动运行后,所需的运行力矩电流大于启车力矩电流后,原来建立的转矩限幅将恢复到正常的限幅值。
启车后,料车将以启车加速度a1=0.25m/s2进行加速至V=2.36m/s。
待炉顶另一料车退出分歧轨后,当上行料车运行至接近炉顶时,由主令控制器发出减速1信号给切换柜,由切换柜发给6SE70使料车按a3=0.25m/s2减速至V=1.0m/s的中速运行。
当上行料车进入分歧轨前,主令控制器发出减速2的命令,使料车以a3=0.2m/s2减速,在此过程中主令控制器器还会发出低速检查命令,6SE70系统此时会根据料车在此点的实际运行速度作出比较判断,料车运行至炉顶时,主令控制器发出停车命令,由PLC控制6SE70完成停车,抱闸闭合,此时料车的停车位置应是工艺要求的角度,即能将车内的炉料倒净而又不撞极限弹簧。
4.料车运行保护所有使用卷扬上料的厂家,最担心的就是料车失控,产生飞车事故,一旦出现此类事故,那么所造成的停产时间和损失都无法估算,为避免这样的事故发生,我们重要采取的措施是松绳检测和低速检查保护。
有松绳现象出现时,松绳开关会立刻给PLC发出信号,PLC 收到松绳信号以后,立刻给供电装置发出停车命令,并同时给抱闸发出停车的命令。
作为卷扬上料无论是直流装置还是交流装置,都是用速度闭环的方式,在工艺要求低速的地方增加主令控制信号,该信号触发变频器的速度比较功能,一旦出现飞车失控的现象,比较值大于设定值测速装置就会向供电装置发出真实的速度信号,装置通过对速度信号鉴别,发现本给定所需要的反馈信号不符,那么装置就会自动关闭,并同时向控制它的PLC发出故障信号,接到信号以后,PLC马上发出停车抱闸的指令,并按程序设定进行断电等其它保护措施。
5、系统特点系统将PLC技术与变频器技术相结合,极大地提高系统性能,成为生产控制的坚实基础。
在此基础上开发出以下几个有特色的功能。
(1)设备故障检测报警:这一功能由两部分构成:PLC中的实时检测程序和计算机上的报警及记录程序。
(2)料车定位:采用主令控制器与编码器(PLC)结合对料车进行定位,定位准确,调整方便,在约60m长的轨道上定位精度可达0.6cm。
(3)料车启动控制:料车启动前,必须提前判断炉顶状态,防止在轨道中间停车。
目前为追求产量,都是大料批上料,料车如在轨道中间停车,再启动时较危险。
(4)安全独立操作方式:由主PLC和操作台分别独立控制主卷扬系统,并且与切换柜相互隔离,提高降低系统的故障率。
(5)开抱闸控制:开抱闸采用力矩电流的百分值由变频器BICO参数输出给抱闸接触器,来控制打开,通过现场调试测定合适的力矩值,在变频器建立起该力矩后,再打开抱闸,可有效的防止误动作及溜车故障。
(四)应用效果卷扬控制系统是实现了高炉生产全过程自动控制的基础,通过采用先进的传感器技术以及稳定的PLC控制技术大大提高了这个高炉生产最重要环节的准确性和稳定性。
系统自投入运行以来一直稳定运行,对高炉稳产、高产,降低成本,减轻工人劳动强度起着重要作用,取得了较好的经济效益和社会效益。
一.引言随着我国现代化进程的不断加快,在各个领域的发展过程中对钢铁需求的数量与质量与日俱增。
我国的钢铁生产工艺正向数字化的高新技术方向发展。
作为整个钢铁生产中的重要环节,高炉炼铁工艺中高新技术的应用尤为重要。
其技术指标如何,对整个钢铁工艺流程有着直接和显著的影响。
其中又以高炉上料主卷扬系统为整个高炉的核心设备,负责原料的输送。
对卷扬系统采用高新技术进行合理控制与优化便成为现代钢铁工艺中的一个重要课题。
本次卷扬系统的设计是以MM440标准型变频器作为传动部分的核心控制部件,并与主控PLC自动化系统紧密结合使用,从而达到了系统的稳定性与操控灵活性的完善结合。
二.系统介绍接下来对此次工程的控制主体,卷扬上料主系统进行简要的介绍。
此次承接项目高炉容积为750m3,属于中小型高炉,采用斜桥式料车上料系统。
斜桥式料车上料机主要由斜桥、料车、卷扬电机三部分组成。
料车在斜桥上的运动分为起动、加速、稳定运行、减速、倾翻和制动六个阶段。
在整个过程中包括两次加速和两次减速,即第一次加速点、第二次加速点的高速给定值使料车加速;第一次减速点、第二次减速点的低速给定值使料车减速。
料车提升一次所需时间与料车的运动速度和加速度有关,其变化曲线为图2.1所示。
(1) t1时间内:料车起动,重料车开始上行,同时空料车自炉顶极限位置下行。
此时,钢绳自卷筒退出的加速度不应超过料车的加速度,以免产生钢绳松弛现象。
此段时间对应于斜桥的A区域,由于此处轨道较陡,在给定值相同的情况下加速度α1只为0.2~0.4m/s2,以较低的加速度加速运行。
(2) t2时间内:重料车继续上行,通过A区域,进入了斜桥的B区域,此处轨道倾角比A区域小,则加速度α2会变大升至0.4~0.8m/s2。
料车以较高加速度加速到最大速度υ。
(3) t3时间内:料车以最大速度υ稳定运行。
(4) t4时间内:重料车进入卸料曲轨道之前的第一次减速时间,加速度α4=-0.4~0.8m/s2。
如图2.5所示,在第一次减速点,取消之前的卷扬电机高速给定,转而给卷扬电机接入低速给定值,通过电机的回馈制动使料车减速至υp。
(5) t5为重料车在卸料曲轨段等速走行时间,速度υp=1m/s左右。
(6) t6为重料车第二次减速到停车的时间,一般加速度α6=-0.4~0.8m/s2。
如图2.5所示,在第二次减速点,要将此时的速度与预先的给定值进行比较。
如果速度降低到预期之内则可进行第二次减速;如果此时速度过大,超过了预期值则要通过调速器进行报警。
料车式上料机的工作特点为:工作过程中,两个料车交替上料,当装满炉料的料车上升时,空料车下行,空车重量相当于一个平衡锤,平衡了重料车的车箱自重。
这样,当上行或下行二个料车用一个卷扬机拖动时,不但节省了拖动电机功率,而且,电机运转时,总有一个重料车上行,没有空行程。
从而,使得电动机总是处于电动状态运行,免去了电动机处于发电运行状态所带来的种种问题。
三.控制系统构成根据厂家要求,主卷扬上料系统必须独立于主系统而自成一套独立系统,并通过以太网与主PLC 系统通讯,从而实现网络控制与数据时时传输。
电气传动装置选择的是西门子标准型变频器6SE64402UD420GA1两台,为一备一用状态,可以通过转换开关来时时切换两台装置,保证了运行的可靠性。
变频器电压等级为380V,功率为200KW。
由于考虑到卷扬系统为大惯量位能性负载特性,配置了制动单元与制动电阻,以保证料车停车过程中能量的回馈不会造成直流母线电压升高从而造成故障。
制动单元为6SE70327EB872DA0,制动电阻为6SE70327ES872DC0,配合使用峰值制动功率可达到255KW,可以满足传动系统的制动要求。
由于采用矢量控制方式需要速度反馈值,变频器选装了脉冲编码器模块6SE64000EN000AA0,将电机侧编码器反馈回的信号经由此模块转换传送给变频器。
传动逻辑控制的PLC 为西门子200系列PLC,主机为CPU226,配扩展I/O模块,及EM243-1以太网通讯模块与上级PLC系统通讯。
四.运行原理及功能我们采用了西门子MM440标准型变频调速装置,运用矢量控制方式,实现了精确的速度控制。