2拉伸试验
拉伸试验步骤细则 gbt 228.1-2010
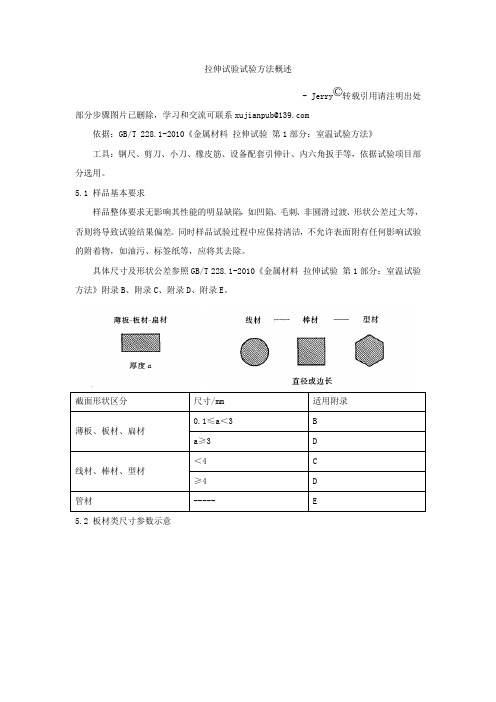
拉伸试验试验方法概述- Jerry©转载引用请注明出处部分步骤图片已删除,学习和交流可联系*****************依据:GB/T 228.1-2010《金属材料拉伸试验第1部分:室温试验方法》工具:钢尺、剪刀、小刀、橡皮筋、设备配套引伸计、内六角扳手等,依据试验项目部分选用。
5.1 样品基本要求样品整体要求无影响其性能的明显缺陷,如凹陷、毛刺、非圆滑过渡、形状公差过大等,否则将导致试验结果偏差。
同时样品试验过程中应保持清洁,不允许表面附有任何影响试验的附着物,如油污、标签纸等,应将其去除。
具体尺寸及形状公差参照GB/T 228.1-2010《金属材料拉伸试验第1部分:室温试验方法》附录B、附录C、附录D、附录E。
截面形状区分尺寸/mm 适用附录0.1≤a<3 B薄板、板材、扁材a≥3 D<4 C线材、棒材、型材≥4 D管材----- E5.2 板材类尺寸参数示意备注:尺寸参数对于不同截面形状会有变化,详细参考GB/T 228.1-2010第22页至第25页。
6.检测步骤6.2试验准备6.2.1 样品准备观察样品类型与形状,是否符合步骤5中所需要求。
若样品不符合要求,则需要对样品进行加工,使其尺寸要求满足步骤5。
加工方式一般有车削、线切割等,对于薄铝板等可用剪刀裁剪至规定尺寸,加工需注意避免缺陷、弯折。
对于同一样品,切割方向可能会影响材料的拉伸性能,需要参考具体标准规定,若无相应规定,一般切割方向为纵向。
6.2.2 尺寸测量对满足步骤5的样品,测量每个样本尺寸参数,一般在不同位置测量3次,精确到小数点后两位,并在原始记录中记录平均值。
对于板材,测量其平行长度的厚度和宽度;对于棒材,测量其平行长度的直径;对于管材,测量其外径和壁厚;对于管材的纵向切割弧形试样,测量其宽度、外径和壁厚;对于异形试样,测量并计算其横截面积。
6.2.3 原始标距刻画判断拉伸试验检测项目,对于需要检测断后伸长率的项目,需要对样品标识出原始标距L0。
拉伸试验方法1和方法2
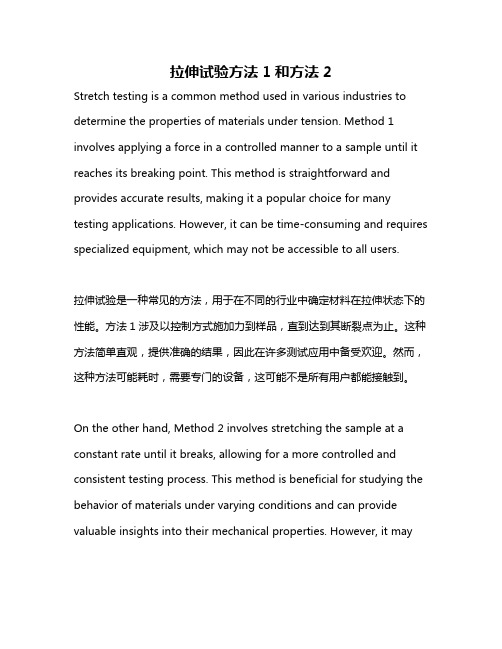
拉伸试验方法1和方法2Stretch testing is a common method used in various industries to determine the properties of materials under tension. Method 1 involves applying a force in a controlled manner to a sample until it reaches its breaking point. This method is straightforward and provides accurate results, making it a popular choice for many testing applications. However, it can be time-consuming and requires specialized equipment, which may not be accessible to all users.拉伸试验是一种常见的方法,用于在不同的行业中确定材料在拉伸状态下的性能。
方法1涉及以控制方式施加力到样品,直到达到其断裂点为止。
这种方法简单直观,提供准确的结果,因此在许多测试应用中备受欢迎。
然而,这种方法可能耗时,需要专门的设备,这可能不是所有用户都能接触到。
On the other hand, Method 2 involves stretching the sample at a constant rate until it breaks, allowing for a more controlled and consistent testing process. This method is beneficial for studying the behavior of materials under varying conditions and can provide valuable insights into their mechanical properties. However, it maynot be as accurate as Method 1 in terms of determining the ultimate tensile strength of a material.另一方面,方法2涉及以恒定速率拉伸样品,直到其断裂,从而实现更为控制和一致的测试过程。
2拉伸试验
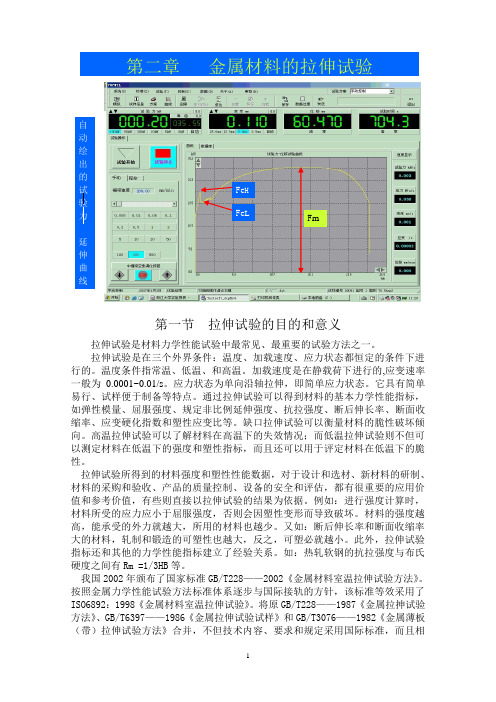
物体因外力作用产生变形,其内部各部分之间因相对位置的变化而引起的相互作用称为内力.众所周知,即使不受外力,物体各质点间也存在相互作用力.我们所称的内力,是在外力作用下,上述各作用力的变化量,随着该变化量的逐渐加大,物体内部发生一系列的物理变化,当到达某一极限时,物体就会被破坏,该极限与物体的强度有直接关系.
第二阶段为屈服阶段(cd段),即试样屈服于外力产生较大塑性变形阶段。此时试样伸长急剧增加,但载荷却在很小的范围内波动,若忽略这一微小的波动,F- 曲线上该段可见一水平线段,该段对应的外力Fs以表示,这是由弹性变形阶段到塑性变形阶段的分界点。
第三阶段为强化阶段(de)(均匀塑性变形阶段)。试样屈服变形阶段结束后,要使之继续变形,就要继续施加外力,克服试样内部不断增加的抗变形力。因为材料本身在塑性变形中会产生强化,也称为加工硬化。该阶段的塑性变形比弹性变形大得多,所以曲线上可见 有很大增加。由d点开始,屈服结束,试样某部位产生塑性变形,截面变小,但加工硬化使该部位抗变形力增加,这样,下一步变形就转移到试样的其它部位。由此,在de段试样各部位产生较均匀的塑性变形之间近似遵循直线关系,且此直径gh与弹性现阶段内直线oa近似平行。由此可见,试样的变形包括了弹性变形 e和塑性变形 p。如卸载时的载荷,此后原则上遵循着原来的拉伸曲线。
Lo 试样原始标距。试验前,测量试样伸长所标记的标距长度。
Lu 试样断后标距。试样拉断后,将断口对接在一起时试样的标距长度。
Le 引伸计标距。用引伸计测量试样延伸所使用的试样部分的长度。
So 试样平行长度部分的原始横截面积
Su 试样拉断后缩颈处的最小横截面积
(一)圆截面试样
Lc≥Lo+d/2仲裁试验Lo+2d Lo=5d,10d或定标距 r≥0.75d粗糙度≤0.8µm
金属材料的拉伸与压缩试验2
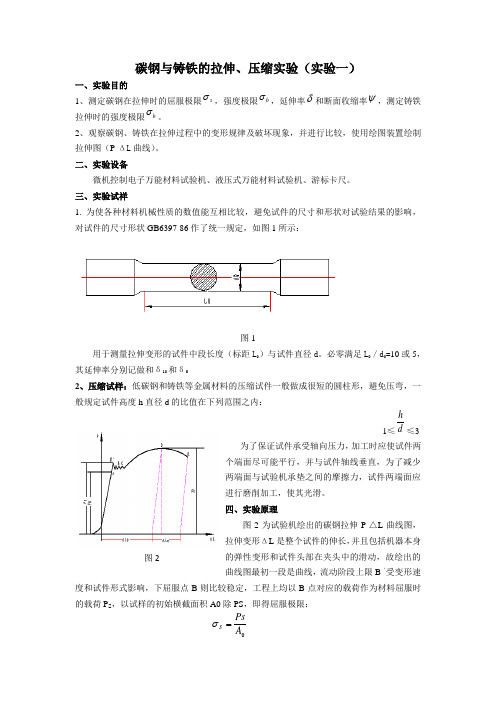
碳钢与铸铁的拉伸、压缩实验(实验一)一、实验目的1、测定碳钢在拉伸时的屈服极限s σ,强度极限b σ,延伸率δ和断面收缩率ψ,测定铸铁拉伸时的强度极限b σ。
2、观察碳钢、铸铁在拉伸过程中的变形规律及破坏现象,并进行比较,使用绘图装置绘制拉伸图(P-ΔL 曲线)。
二、实验设备微机控制电子万能材料试验机、液压式万能材料试验机、游标卡尺。
三、实验试祥1. 为使各种材料机械性质的数值能互相比较,避免试件的尺寸和形状对试验结果的影响,对试件的尺寸形状GB6397-86作了统一规定,如图1所示:图1用于测量拉伸变形的试件中段长度(标距L 0)与试件直径d 。
必零满足L 0/d 0=10或5,其延伸率分别记做和δ10和δ52、压缩试样:低碳钢和铸铁等金属材料的压缩试件一般做成很短的圆柱形,避免压弯,一般规定试件高度h 直径d 的比值在下列范围之内:1≤d h≤3为了保证试件承受轴向压力,加工时应使试件两个端面尽可能平行,并与试件轴线垂直,为了减少两端面与试验机承垫之间的摩擦力,试件两端面应进行磨削加工,使其光滑。
四、实验原理图2为试验机绘出的碳钢拉伸P-△L 曲线图,拉伸变形ΔL 是整个试件的伸长,并且包括机器本身的弹性变形和试件头部在夹头中的滑动,故绘出的曲线图最初一段是曲线,流动阶段上限B ‘受变形速度和试件形式影响,下屈服点B 则比较稳定,工程上均以B 点对应的载荷作为材料屈服时的载荷P S ,以试样的初始横截面积A0除PS ,即得屈服极限:0A Ps S =σ图2屈服阶段过后,进入强化阶段,试样又恢复了承载能力,载荷到达最大值P b ,时,试样某一局部的截面明显缩小,出现“颈缩”现象,这时示力盘的从动针停留在P b 不动,主动针则迅速倒退表明载荷迅速下降,试样即将被拉断。
以试样的初始横截面面积A 。
除P b 得强度极限为0A P b b =σ延伸率δ及断面收缩率φ的测定,试样的标距原长为L 0拉断后将两段试样紧密地对接在一起,量出拉断后的标距长为L 1延伸率应为 %100001⨯-=l l l δ断口附近塑性变形最大,所以L 1的量取与断口的部位有关,如断口发生于L ο的两端或在L ο之外,则试验无效,应重做,若断口距L 。
金属材料的拉伸与压缩实验_2

机械学基础实验指导书力学实验中心金属材料的拉伸与压缩实验1.1 金属材料的拉伸实验拉伸实验是材料力学实验中最重要的实验之一。
任何一种材料受力后都要产生变形,变形到一定程度就可能发生断裂破坏。
材料在受力——变形——断裂的这一破坏过程中,不仅有一定的变形能力,而且对变形和断裂有一定的抵抗能力,这些能力称为材料的力学机械性能。
通过拉伸实验,可以确定材料的许多重要而又最基本的力学机械性能。
例如:弹性模量E 、比例极限R p 、上和下屈服强度R eH 和R eL 、强度极限R m 、延伸率A 、收缩率Z 。
除此而外,通过拉伸实验的结果,往往还可以大致判定某种其它机械性能,如硬度等。
我们以两种材料——低碳钢,铸铁做拉伸试验,以便对于塑性材料和脆性材料的力学机械性能进行比较。
这个实验是研究材料在静载和常温条件下的拉断过程。
利用电子万能材料试验机自动绘出的载荷——变形图,及试验前后试件的尺寸来确定其机械性能。
试件的形式和尺寸对实验的结果有很大影响,就是同一材料由于试件的计算长度不同,其延伸率变动的范围就很大。
例如:对45#钢:当L 0=10d 0时(L 0为试件计算长度,d 0为直径),延伸率A 10=24~29%,当L 0=5d 0时,A 5=23~25%。
为了能够准确的比较材料的性质,对拉伸试件的尺寸有一定的标准规定。
按国标GB/T228-2002、GB/P7314-2005的要求,拉伸试件一般采用下面两种形式:图1-11. 10倍试件;圆形截面时,L 0=10d 0 矩形截面时,L 0=11.30S 2. 5倍试件圆形截面时,L 0=5d 矩形截面时, L 0=5.650S =45Sd 0——试验前试件计算部分的直径; S 0——试验前试件计算部分断面面积。
此外,试件的表面要求一定的光洁度。
光洁度对屈服点有影响。
因此,试件表面不应有刻痕、切口、翘曲及淬火裂纹痕迹等。
一、实验目的:1.研究低碳钢、铸铁的应力——应变曲线拉伸图。
2.实验二 铸铁拉伸实验
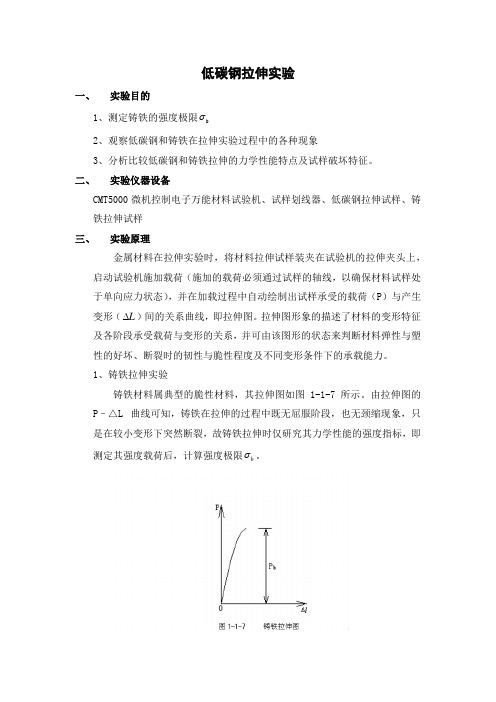
低碳钢拉伸实验一、实验目的σ1、测定铸铁的强度极限b2、观察低碳钢和铸铁在拉伸实验过程中的各种现象3、分析比较低碳钢和铸铁拉伸的力学性能特点及试样破坏特征。
二、实验仪器设备CMT5000微机控制电子万能材料试验机、试样划线器、低碳钢拉伸试样、铸铁拉伸试样三、实验原理金属材料在拉伸实验时,将材料拉伸试样装夹在试验机的拉伸夹头上,启动试验机施加载荷(施加的载荷必须通过试样的轴线,以确保材料试样处于单向应力状态),并在加载过程中自动绘制出试样承受的载荷(P)与产生∆)间的关系曲线,即拉伸图。
拉伸图形象的描述了材料的变形特征变形(L及各阶段承受载荷与变形的关系,并可由该图形的状态来判断材料弹性与塑性的好坏、断裂时的韧性与脆性程度及不同变形条件下的承载能力。
1、铸铁拉伸实验铸铁材料属典型的脆性材料,其拉伸图如图1-1-7所示。
由拉伸图的P–△L 曲线可知,铸铁在拉伸的过程中既无屈服阶段,也无颈缩现象,只是在较小变形下突然断裂,故铸铁拉伸时仅研究其力学性能的强度指标,即σ。
测定其强度载荷后,计算强度极限b2、拉伸试样破坏断口特征拉伸试样破坏断口如图1-1-8 所示,低碳钢试样拉伸破坏后,在试样的两个断面上各呈凸凹状,称为杯状断口。
断口中间部分的材料成晶粒状,四周则呈纤维状。
铸铁试样拉伸破坏后,试样断口的两个断面基本平齐,断口上的材料呈晶粒状,材料呈晶粒状是脆性断裂的断口特征,纤维状是韧性的断口特征。
四、实验步骤本实验通过 CMT5000 微机控制电子万能材料实验机完成低碳钢、铸铁拉伸试样的加载、测量过程,实验操作前,必须详细了解实验机的使用操作方法,并仔细阅读实验中所用仪器设备的注意事项。
1、试样刻线使用试样刻线机,在低碳钢拉伸试样上划出标距线和十等分分格线,刻线过程中,线痕能分辨即可,过深易造成应力集中,影响实验测量结果。
2、原始数据测量测定低碳钢和铸铁拉伸试样原始工作直径d0及低碳钢拉伸试样的原始标距L0。
拉伸试验试验操作规程
目录一、金属材料室温拉伸试验方法 (2)二、试样的形状要求 (2)三、制样规范及弯曲要求 (3)四、拉伸试验操作 (4)五、弯曲试验原理 (5)六、弯曲试验操作 (5)七、冷弯试验结果的评定等级 (6)八、牌号和化学成份 (7)九、钢中的杂质元素及其影响 (8)十、钢号命名规则 (8)十一、弯曲试验原理 (10)十二、产品质量及标准 (11)十三、铁合金质量证明书 (13)一、拉伸试验操作1、试样准备(1)对试样进行外观检查,依照委托单顺序将试样排好,查对编号,并填写原始记录,如不符合制样规定者不列入试验,要求重新取样,对板状试样,挫掉试样所带毛刺。
(2)测量试样原始尺寸,圆试样直径d0用精度,0.01的千分尺测量,板坯试样和圆状试样都分别在标距长度的中部及两端处分三部分进行测量,圆形试样应在两个相互垂直方向上各测一次,取其平均值,选用三处测得横截面积中的最小值,计算试样的横截面积(保留四位有效数字)。
(3)试样的尺寸公差和形状公差应符合有关要求。
(4)根据横截面积,按要求打上相应长度的标距。
2、顺序开机运行软件,进入联机状态;3、进入试验窗口选择设置好的试验方案;4、设置好试验用户参数;5、装好合适的夹块,根据试样长度调整下横梁位置;6、启动油泵电机;7、先夹紧试样的一端,然后升降下横梁到合适的位置,力值清零,然后夹紧试样的别一端。
位移或变形值清零;8、点击试验窗口“运行”按钮,进入试验状态,顺时针旋转手动阀手轮进行加荷,直至试样断裂。
9、启动油泵,取下试样,再逆时针旋转手动阀手轮,使活塞退回到底,10、开、关机必须按照正确顺序进行:开机:显示器—打印机—计算机—DCS控制器—启动试验软件—液压源关机:液压源—退出试验软件—DCS控制器—计算机—显示器—打印机二、钢中的杂质元素及其影响在钢的冶炼过程中,不可能除尽所有的杂质,所以实际使用的碳钢中除碳以外,还含有少量的硅、磷、氧、氢、氮等元素,它们的存在,会影响钢的质量和性能。
实验一、二 拉伸和压缩实验
实验一 拉伸和压缩实验拉伸和压缩实验是测定材料在静载荷作用下力学性能的一个最基本的实验。
工矿企业、研究所一般都用此类方法对材料进行出厂检验或进厂复检,通过拉伸和压缩实验所测得的力学性能指标,可用于评定材质和进行强度、刚度计算,因此,对材料进行轴向拉伸和压缩试验具有工程实际意义。
不同材料在拉伸和压缩过程中表现出不同的力学性质和现象。
低碳钢和铸铁分别是典型的塑性材料和脆性材料,因此,本次实验将选用低碳钢和铸铁分别做拉伸实验和压缩实验。
低碳钢具有良好的塑性,在拉伸试验中弹性、屈服、强化和颈缩四个阶段尤为明显和清楚。
低碳钢在压缩试验中的弹性阶段、屈服阶段与拉伸试验基本相同,但最后只能被压扁而不能被压断,无法测定其压缩强度极限bc σ值。
因此,一般只对低碳钢材料进行拉伸试验而不进行压缩试验。
铸铁材料受拉时处于脆性状态,其破坏是拉应力拉断。
铸铁压缩时有明显的塑性变形,其破坏是由切应力引起的,破坏面是沿45︒~55︒的斜面。
铸铁材料的抗压强度bc σ远远大于抗拉强度b σ。
通过铸铁压缩试验观察脆性材料的变形过程和破坏方式,并与拉伸结果进行比较,可以分析不同应力状态对材料强度、塑性的影响。
一、 实验目的1.测定低碳钢的屈服极限s σ(包括sm σ、sl σ),强度极限b σ,断后伸长率δ和截面收缩率ψ;测定铸铁拉伸和压缩过程中的强度极限b σ和bc σ。
2.观察低碳纲的拉伸过程和铸铁的拉伸、压缩过程中所出现的各种变形现象,分析力与变形之间的关系,即P —L ∆曲线的特征。
3.掌握材料试验机等实验设备和工具的使用方法。
二、 实验设备和工具1. 液压摆式万能材料试验机。
2. 游标卡尺(0.02mm)。
三、 拉伸和压缩试件材料的力学性能sm s σσ(、sl σ)、b σ、δ和ψ是通过拉伸和压缩试验来确定的,因此,必须把所测试的材料加工成能被拉伸或压缩的试件。
试验表明,试件的尺寸和形状对试验结果有一定影响。
为了减少这种影响和便于使各种材料力学性能的测试结果可进行比较,国家标准对试件的尺寸和形状作了统一的规定,拉伸试件应按国标GB /T6397—1986《金属拉伸试验试样》进行加工,压缩试件应按国标GB /T7314—1987《金属压缩试验方法》进行加工。
JISK6251:2004
JIS K 6251 :2004JIS K 6251:2004 版本号:1硫化橡胶和热可塑性橡胶—拉伸特性的试验方法序文本标准是对翻译的1994年第3版发行的ISO 37:1994 ,Rubber, vulcanized or thermoplastic —Determination of tensile stress —strain propertics 进行技术性内容的修改而制定的日本工业标准。
说明: 本标准加有下划虚线的地方是修改了的原国际标准事项。
变更一览表及其说明见附件。
警告本标准的使用者必须是熟悉一般试验室作业的人员。
本标准并未就其使用的所有安全问题提出处理意见。
所以,使用本标准的人员必须按照各自的责任对安全和健康采取适宜的措施。
1. 适用范围本标准适用于硫化橡胶和热可塑性橡胶(下称硫化橡胶)的拉伸强度、断裂时的延伸率、屈服点延伸率和拉伸应力的证明方法。
备注本标准的采用国际标准如下:说明:采用程度的记号源自ISO/IEC Guide 21,IDT(等同)、MOD修改)、NEQ非等效)。
ISO 37:1994 ,Rubber,vulcanized or thermoplastic —Determinationof tensile stress-strain properties(MOD)2. 引用标准以下所列是本标准的引用标准,是构成本标准规定的一部分。
在这些引用标准中,注有发行年份的,表示只有这个年份的版本才是本标准的构成部分,其后所有的修订版和补充都不适用。
未注生效年份的引用标准,则表示适用其最新版(包括补充)。
JIS K 6200 橡胶术语JIS K 6250 橡胶—物理试验方法通则备注JIS K 6250 橡胶—物理试验方法通则的各个项目等同于以下国际标准的各个项目。
1JIS K 6251:2004 版本号:1ISO 471:1995 Rubber —Temperatures, humidities and times forconditioning and testingISO 3383:1985 Rubber —General directions for achieving elevatedor subnormal temperatures for test purposesISO 4648:1991 Rubber,vulcanized or thermoplastic —Determinationof dimensions of test pieces and products for testpurposesISO 4661-1:1993 Rubber, vulcanized or thermoplastic —Preparationof samples and test pieces —Part 1: Physical tests JIS K 6272 橡胶—拉伸、弯曲及压缩试验机(定速) —规格要求备注ISO 5893:2002 Rubber and plastics test equipment —Tensileflexural and compression types (constant rate of traverse) —Description 引用的事项等同于本标准的相应事项。
拉伸实验报告
拉伸实验报告
实验目的,通过拉伸实验,了解材料在受力作用下的力学性能,掌握拉伸实验的基本操作技能。
实验仪器,拉伸试验机、标尺、试样。
实验原理,拉伸试验是通过对试样施加拉伸力,使其在拉伸过程中产生应力和应变,从而研究材料的力学性能。
拉伸试验的基本参数包括抗拉强度、屈服强度、断裂伸长率等。
实验步骤:
1. 准备试样,根据实验要求,选择合适的试样,对其尺寸进行测量,并在试样上标记好测量点。
2. 安装试样,将试样安装到拉伸试验机上,并调整好试验机的参数。
3. 进行拉伸实验,启动拉伸试验机,施加拉伸力,记录试验过程中的拉伸力和试样的变形情况。
4. 数据处理,根据实验记录的数据,计算出试样的抗拉强度、屈服强度等力学性能参数。
实验结果:
经过拉伸实验,我们得到了试样的拉伸力-应变曲线。
从曲线上可以看出,试样在拉伸过程中出现了线性阶段和非线性阶段。
在线性阶段,试样的应变随拉伸力的增加呈线性增长,而在非线性阶段,试样的应变增长速度加快,最终导致试样的断裂。
根据拉伸力-应变曲线,我们计算出了试样的抗拉强度为XXX,屈服强度为XXX,断裂伸长率为XXX。
这些数据反映了材料在拉伸过程中的力学性能,为材料的工程应用提供了重要参考。
实验总结:
通过本次拉伸实验,我们深入了解了材料在受力作用下的力学性能,掌握了拉伸实验的基本操作技能。
同时,我们也发现了材料在拉伸过程中的一些特点,对材料的工程应用具有重要的指导意义。
在今后的学习和工作中,我们将继续深入研究材料的力学性能,不断提高实验操作技能,为材料工程领域的发展做出更大的贡献。
拉伸实验报告到此结束。
- 1、下载文档前请自行甄别文档内容的完整性,平台不提供额外的编辑、内容补充、找答案等附加服务。
- 2、"仅部分预览"的文档,不可在线预览部分如存在完整性等问题,可反馈申请退款(可完整预览的文档不适用该条件!)。
- 3、如文档侵犯您的权益,请联系客服反馈,我们会尽快为您处理(人工客服工作时间:9:00-18:30)。
第一节拉伸试验的目的和意义
拉伸试验是材料力学性能试验中最常见、最重要的试验方法之一。
拉伸试验是在三个外界条件:温度、加载速度、应力状态都恒定的条件下进行的。温度条件指常温、低温、和高温。加载速度是在静载荷下进行的,应变速率一般为0.0001~0.01/s。应力状态为单向沿轴拉伸,即简单应力状态。它具有简单易行、试样便于制备等特点。通过拉伸试验可以得到材断后伸长率、断面收缩率、应变硬化指数和塑性应变比等。缺口拉伸试验可以衡量材料的脆性破坏倾向。高温拉伸试验可以了解材料在高温下的失效情况;而低温拉伸试验则不但可以测定材料在低温下的强度和塑性指标,而且还可以用于评定材料在低温下的脆性。
第一阶段为弹性阶段(ob段)。试样变形为弹性变形,一旦取消外力,试样完全恢复原状,不会产生残余伸长,b点对应的外力F。为试样产生弹性变形的极限外力,超过b点,便会产生塑性变形。在该阶段的一定范围内(oa段),试样伸长与载荷之间符合虎克定律,即成正比关系,称为比例变形阶段,a点对应的外力Fp分为产生比例变形的极限外力,一旦超过此外力,变形与外力之间比例关系也即破坏。ab段为弹性变形的非比例阶段,时间很短,要靠很精密的仪器才能测量得出。
试样初始受力,宏观上逐渐被均匀拉长,然后在某一点横截面渐渐变细(缩颈),直至在该处断裂。塑性较好的材料一般有明显的缩颈现象。但也有例外,如奥氏体钢、铝青铜等塑性金属材料不发生缩颈,这类材料通常有圈套的加工硬化能力。而对于较脆弱的材料,一般由伸长到最终断裂前,通常无明显缩颈现象发生。
拉伸过程中,材料试验机上的自动记录装置也可自动绘出拉伸曲线图,该图以力F/N作为纵坐标,试样的伸长量 /mm为横坐标,即F- 曲线,习惯上称为拉伸图。现在以20低碳钢为例,具体说明拉伸过程中的几个阶段。
对于不同的材料,其拉伸时所表现出的物理现象和力学性质不尽相同,因面有着不同的σ—ε曲线。下面列举几种常见的σ—ε曲线。
图a是一般低碳钢的σ—ε曲线。有锯齿状的屈服阶段,分上下屈服点,产生缩颈现象后,试样断裂。
拉伸试验所得到的材料强度和塑性性能数据,对于设计和选材、新材料的研制、材料的采购和验收、产品的质量控制、设备的安全和评估,都有很重要的应用价值和参考价值,有些则直接以拉伸试验的结果为依据。例如:进行强度计算时,材料所受的应力应小于屈服强度,否则会因塑性变形而导致破坏。材料的强度越高,能承受的外力就越大,所用的材料也越少。又如:断后伸长率和断面收缩率大的材料,轧制和锻造的可塑性也越大,反之,可塑必就越小。此外,拉伸试验指标还和其他的力学性能指标建立了经验关系。如:热轧软钢的抗拉强度与布氏硬度之间有Rm =1/3HB等。
第二阶段为屈服阶段(cd段),即试样屈服于外力产生较大塑性变形阶段。此时试样伸长急剧增加,但载荷却在很小的范围内波动,若忽略这一微小的波动,F- 曲线上该段可见一水平线段,该段对应的外力Fs以表示,这是由弹性变形阶段到塑性变形阶段的分界点。
第三阶段为强化阶段(de)(均匀塑性变形阶段)。试样屈服变形阶段结束后,要使之继续变形,就要继续施加外力,克服试样内部不断增加的抗变形力。因为材料本身在塑性变形中会产生强化,也称为加工硬化。该阶段的塑性变形比弹性变形大得多,所以曲线上可见 有很大增加。由d点开始,屈服结束,试样某部位产生塑性变形,截面变小,但加工硬化使该部位抗变形力增加,这样,下一步变形就转移到试样的其它部位。由此,在de段试样各部位产生较均匀的塑性变形之间近似遵循直线关系,且此直径gh与弹性现阶段内直线oa近似平行。由此可见,试样的变形包括了弹性变形 e和塑性变形 p。如卸载时的载荷,此后原则上遵循着原来的拉伸曲线。
我国2002年颁布了国家标准GB/T228——2002《金属材料室温拉伸试验方法》。按照金属力学性能试验方法标准体系逐步与国际接轨的方针,该标准等效采用了ISO6892:1998《金属材料室温拉伸试验》。将原GB/T228——1987《金属拉抻试验方法》、GB/T6397——1986《金属拉伸试验试样》和GB/T3076——1982《金属薄板(带)拉伸试验方法》合并,不但技术内容、要求和规定采用国际标准,而且相关术语、性能名称、符号也采用国际标准。
ε=
ε和σ是拉伸试验中两个最基本的参数,它们相互之间有一定的联系。
对于不同材料的试样,由于其化学成分及组织的不同,在拉伸过程中会体现出不同的物理现象及力学性质,但从外表看来,一般分为以下几个基本过程。以金属试样为例,将试样装夹在材料试验机上,按照有关标准规定选择合适的速率,均匀地对试样施加作用力F,可以观察试样由开始到破坏(一般是断裂)的几个阶段。
将物体简化为杆件.杆件受到外力F作用,在其任意横截面上均产生内力F.一般,截面上的内力并不是均匀分布的,因此,用单位横截面上的内力,即应力来表示材料抗破坏与变形的能力.由于横截面积So随着构件不断被拉伸而逐渐减小,故而一般用初始截面积SO来计算应力σ,该σ称为工程应力:
σ=
在材料性能测试中,除了要测出应力,经常还要了解材料经拉伸后的变形程度。设杆件的初始长度为 ,则工程应变ε为:
第二节拉伸试验原理
物体因外力作用产生变形,其内部各部分之间因相对位置的变化而引起的相互作用称为内力.众所周知,即使不受外力,物体各质点间也存在相互作用力.我们所称的内力,是在外力作用下,上述各作用力的变化量,随着该变化量的逐渐加大,物体内部发生一系列的物理变化,当到达某一极限时,物体就会被破坏,该极限与物体的强度有直接关系.