数控机床中英文翻译资料
数控机床英文操作面板.docx

数控机床的英文操作面板1. EMERGENCY STOP 紧急制动2. MODE SELECT 模式选择3. EDIT 编辑4. MEMORY 存储5. MDI 人工数据输入6. HANDLE 手动7. JOG 点动8. CYCLE START 循环启动9. FEED HOLD 进给锁定10 . SINGLE BLOCK 单程序段11 . DRY RUN 空运行12 . REFERENCE RETURN 零点返回13 . FEED RATE OVERRIDE 进给倍率14 . RAPID TRAVERSE OVERRIDE 快速进给倍率15 . MACHINE LOCK 机床面板16 . CONTROL PANEL 控制面板17 . POWER ON AND POWER OFF 电源开和关18 . RESET 复位19.CRT CHARACTER DISPLAY 显示数控技术常用术语中英文大全1. 计算机数值控制:Computerized Numerical Control, CNC2. 车由:(Axis)3. 机床坐标系:Machine Coordinate System4. 机床坐标原点:Machine Coordinate Origin5. 工件坐标系:Work-piece Coordinate System6. 工件坐标原点:Work-piece Coordinate Origin7. 机床零点:Machine Zero8. 参考位置:Reference Position9. 绝对尺寸( Absolute Dimension) / 绝对坐标值( IncrementalCoordinates)10. 增量尺寸( Incremental Dimension ) / 增量坐标( IncrementalDimension)11. 最小输入增量:Least Input Increment12. 命令增量:Least Command Increment13. 插补:Interpolation14. 直线插补:Line Interpolation15. 圆弧插补:Circular Interpolation16. 顺时针圆弧:Clockwise Arc17. 逆时针圆弧:Counterclockwise Arc18. 手工零件编程:Manual Part Programming19. 计算机零件编程:Computer Part Programming20. 绝对编程:Absolute Programming21. 增量编程:Increment Programming22. 字符:Character23. 控制字符:Control Character24. 地址:Address25. 程序段格式:Block Format26. 指令码:Instruction Code27. 程序号:Program Number28. 程序名:Program Name29. 指令方式:Command Mode30. 程序段:Block31. 零件程序:Part Program32. 加工程序:Machine Program33. 程序结束:End of Program34. 数据结束:End of Data35. 程序暂停:Program Stop36. 准备功能:Preparatory Function37. 辅助功能:Miscellaneous Function38. 刀具功能:Tool Function39. 进给功能:Feed Function40. 主轴速度功能:Spindle Speed Function41. 进给保持:Feed Hold42. 刀具轨迹:Tool Path43. 零点偏置:Zero Offset44. 刀具偏置:Tool Offset45. 刀具长度偏置:Tool Length Offset46. 刀具半径偏置:Tool Radius Offset47. 刀具半径补偿Cutter Radius Compensation48. 刀具轨迹进给速度:Tool Path Feed Rate49. 固定循环:Fixed cycle, Canned cycle50. 字程序:Subprogram51. 工序单:Planning Sheet52. 执行程序:Executive Program53. 倍率:Override54. 伺服机构:Servo-Mechanist55. 误差:Error56. 分辨率:Resolution。
数控机床刀具设计论文中英文资料外文翻译文献综述
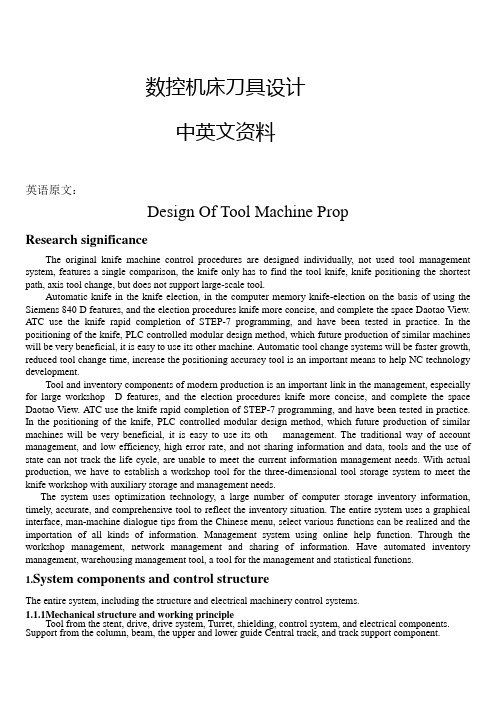
数控机床刀具设计中英文资料英语原文:Design Of Tool Machine PropResearch significanceThe original knife machine control procedures are designed individually, not used tool management system, features a single comparison, the knife only has to find the tool knife, knife positioning the shortest path, axis tool change, but does not support large-scale tool.Automatic knife in the knife election, in the computer memory knife-election on the basis of using the Siemens 840 D features, and the election procedures knife more concise, and complete the space Daotao View. ATC use the knife rapid completion of STEP-7 programming, and have been tested in practice. In the positioning of the knife, PLC controlled modular design method, which future production of similar machines will be very beneficial, it is easy to use its other machine. Automatic tool change systems will be faster growth, reduced tool change time, increase the positioning accuracy tool is an important means to help NC technology development.Tool and inventory components of modern production is an important link in the management, especially for large workshop D features, and the election procedures knife more concise, and complete the space Daotao View. ATC use the knife rapid completion of STEP-7 programming, and have been tested in practice. In the positioning of the knife, PLC controlled modular design method, which future production of similar machines will be very beneficial, it is easy to use its oth management. The traditional way of account management, and low efficiency, high error rate, and not sharing information and data, tools and the use of state can not track the life cycle, are unable to meet the current information management needs. With actual production, we have to establish a workshop tool for the three-dimensional tool storage system to meet the knife workshop with auxiliary storage and management needs.The system uses optimization technology, a large number of computer storage inventory information, timely, accurate, and comprehensive tool to reflect the inventory situation. The entire system uses a graphical interface, man-machine dialogue tips from the Chinese menu, select various functions can be realized and the importation of all kinds of information. Management system using online help function. Through the workshop management, network management and sharing of information. Have automated inventory management, warehousing management tool, a tool for the management and statistical functions.1.System components and control structureThe entire system, including the structure and electrical machinery control systems.1.1.1Mechanical structure and working principleTool from the stent, drive, drive system, Turret, shielding, control system, and electrical components. Support from the column, beam, the upper and lower guide Central track, and track support component.1) Drive for the system chosen VVVF method. Cone used brake motors, with VVVF by Cycloid reducer through sprocket drive.2) Drag a variable frequency drive system and control technology. VVVF adopted, will speed drive shaft in the normal range adjustment to control the speed rotary turret to 5 ~ 30mm in, the drive shaft into two, two under through sprocket, the two profiled rollers Chain driven rotating shelves. Expansion chain adopted by the thread tight regulation swelling, swelling the regular way. - Conditi D features, and the election procedures knife more concise, and complete the space Daotao View. ATC use the knife rapid completion of STEP-7 programming, and have been tested in practice. In the positioning of the knife, PLC controlled modular design method, which future production of similar machines will be very beneficial, it is easy to use its at six other Des V oeux a knife, can be categorized with some of knife auxiliary equipment, such as bits, such as turning tools.1.1.2.Electrical Control SystemThis tool storage systems is the main electrical control their shelves for operational control and position control. Operational control equipment, including operation of the start of braking control. Position Control is the main location and address of the shelves for testing.1) Electric Transmission horizontal rotary tool storage systems are the mechanical movements are repeated short-term work system. And the run-time system needs some speed, speed transmission needs, the system will use VVVF method can be used simple structure, reliable operation of the motor and frequency inverter.2) Control of the system is divided into two kinds of manual control and automatic control, manual control as a general reserve and debugging methods of work; ways to the system control computer (IPC) and the control unit (inverter contactor , etc.) consisting of a control system.3) location and positioning accuracy of the system automatically identify the site and location using a detection device tion, timely, accurate, and comprehensive tool to reflect the inventory situation. The entire system uses a graphical interface, man-machine dialogue tips from the Chinese menu, select various functions can be realized and the importation of all kinds of information. Management system using online help function. Through the workshop management, network management and sharing of information. Have automated inventory management, warehousing management tool, a tool for the management and statistical fu as proximity switches, relays through the plate-point isolation and the number plate recorded close to the switching signal acquisition and operation of Hutchison with a Optimal Path addressable identify the current location and shelves of the purpose of the shelf location. In order to enable a more accurate positioning system, adopted two photoelectric switches, to detect the two shelves of the two films.1.2.The functions of the knifeknife The is the role of reserves a certain number of tools, machine tool spindle in hand to achieve the fungibility a disc sc knife in the library with discoid knife, cutting tool along See how vertical arrangement (including radial and axial from knife from knife), along See how radial array into acute or arranged in the form of the knife. Simple, compact, more applications, but are ring-cutter, low utilization of space. Figure 2.7 a) to c). D features, and the election procedures knife more concise, and complete the space Daotao View. ATC use the knife rapid completion of STEP-7 programming, and have been tested in practice. In the positioning of the knife, PLC controlled modular design method, which future production of similar machines will be very beneficial, it is easy to use its. If the knife cutter knife is the type of library, the chain knives, and other means, in the form of the knifeand capacity according to the Machine Tool to determine the scope of the process.s, but are ring-cutter, low utilization of space. Figure 2.7 a) to c). D features, and the election procedures knife more concise, and com mon typesThe knife is a tool storage devices, the common knife mainly in the following forms:(1) the turret knifeIncluding the first level turret vertical turret and the first two, see Figure 2.6 a) and b):(2) the disc cutterDisc knife in the library with discoid knife, cutting tool along See how vertical arrangement (includingradial and axial from knife from knife), along See how radial array into acute or arranged in the form of theknife. Simple, compact, more applications, but are ring-cutter, low utilization of space. Figure 2.7 a) to c).D features, and the election procedures knife more concise, and complete the space Daotao View. ATC use theknife rapid completion of STEP-7 programming, and have been tested in practice. In the positioning of theknife, PLC controlled modular design method, which future production of similar machines will be verybeneficial, it is easy to use its. If the knife storage capacity must be increased to increase the diameter of theknife, then the moment of inertia also increased correspondingly, the election campaign long knife. Toolnumber not more than 32 general. Cutter was multi-loop order of the space utilization knife, but inevitablygiven the knife from complex institutions, applicable to the restricted space Machine Tool storage capacity andmore occasions. Two-disc structure is two smaller capacity knife on both sides of the sub-spindle place, morecompact layout, the number ofapply to small and medium-sizedprocessing center.(3) the chain knife Includingsingle-and multi-ring chain ringchain, chain link can take many forms change, see Figure 2.8 a) to c), the basic structure shown in Figure 2. 8 doFeatures: knife apply to the larger capacity of the occasion, the space of the small number of generally applicable to the tool in the 30-120. Only increase the length of the chain tool will increase the number should not be increased circumferential speed of its moment of inertia of the knife does not increase the disc as large.(4) linear combination knife and the knife libraryThe linear knife simple structure in Figure 2.9, tool single order, the capacity of small knife, used for CNC lathe and drill press on. Because the location of fixed knife, ATC completed action by the spindle without manipulator. The cutter knife is generally the turret combination turret with a combination of the disc cutter knife and the chain combination. Every single knife the knife certificates of smaller, faster tool change. There are also some intensive drum wheel, and the lattice-type magazine for the knife, the knife-intensive though.Small footprint, but because of structural constraints, basically not used for single processing center, the concentration used for FMS for the knife system.1.4 Tool storage capacityTool storage capacity of the first to consider the needs of processing, from the use of point of view,generally 10 to 40 knives, knife will be the utilization of the high, and the structure is compact.1.5 Tool options(1) choose to order processing tool according to the order, followed Add to the knife every knife in the Block. Each tool change, the order of rotation of a cutter knife on location, and remove the need knives, has been used by the cutter knife can be returned to the original Block, can also order Add Block, a knife. However, as the knife in the tool in different processes can not be repeated use of the knife must increase the capacity and lower utilization rate.(2) most of the arbitrary choice of the current system of using arbitrary NC election knives, divided into Daotao coding, coding and memory-cutter, three. Daotao coding tool code or knives or Daotao need to install the code used to identify, in accordance with the general principle of binary coding coding. Tool knife election coding method uses a special knife handle structure, and each of the coding tool. Each of the tool has its own code, thereby cutting tool can be in different processes repeatedly used, not to replace the tool back at the original knife, the knife capacity can be reduced accordingly. Memory-election this paper knife, in this way can knives and knife in the position corresponding to the Daotao memory of the PLC in the NC system, no matter which tool on the Inner knife, tool information is always there in mind, PLC . On the knife with position detection devices, will be the location of each Daotao. This tool can be removed and sent back to arbitrary. On the knife is also a mechanical origin, every election, the nearest knife selection.1.6.Control of the knife(1) the knife as a system to control the positioning axis. In the ladder diagram in accordance with the instructions for computing T code comparison of the output angle and speed of instructions to the knife the knife servo drive servo motor. Tool storage capacity, rotation speed, and / deceleration time, and other system parameters can be set in such a manner free from any outside influence positioning accurate and reliable but the cost is higher.(2) knife from the hydraulic motor drives, fast / slow the points, with proximity switches count and positioning. In comparison ladder diagram of the current storage system knife (knife spindle) and goals knife (pre-knife) and computing, then output rotation instructions, judging by the shortest path rotation in place. This approach requires sufficient hydraulic power and electromagnetic valve knife the rotational speed can be adjusted through the throttle. But over time may be oily hydraulic, oil temperature and environmental factors impact the change in velocity and accuracy. Not generally used in large and medium-sized machine tool change frequently.(3) the knife from AC asynchronous motor driven cam mechanism (Markov institutions), with proximity switches count, which means stable operation, and generally accurate and reliable positioning cam used in conjunction with a mechanical hand, ATC fast-positioning.2. ATC, the main types, characteristics, and the scope of application2.1 Auto Rotary ToolRotary Tool automatically on the use of CNC machine tool is a simpleinstallation of automatic tool change, the Quartet and 47.60 Turret Tool various forms, such as rotary turret were installed on four, six or more of the Tool , NCinstructions by ATC. Rotary Tool has two vertical and horizontal, relatively simple structure, applicable to economic CNC lathe.Rotary Tool in the structure must have good strength and stiffness, resistance to bear rough Cutting Tool in the cutting force and reduce the role of deformation and improve processing accuracy. Rotating Tool to choose reliable positioning programme structure and reasonable position, in order to ensure that each rotary turret to a higher position after repeated positioning accuracy (typically 0.001 to 0.005mm). Figure 2.1 shows the spiral movements of the Quartet Turret.Auto Rotary Tool in the simplest of ATC, is 180 º rotary ATC devices, as shown in Figure 2.2 ATC instructions received, the machine control system put ATC spindle control to the designated location at the same time, the tool movement to the appropriate location, ATC, with the rotary axis and at the same time, the knives matching tool; drawbars from Spindle Cutting Tools rip, ATC, will be the tool from their position removed; ATC, 180 º rotary tool spindle and the tool and tool away; ATC, the Rotary At the same time, thetool refocusing its position to accept Spindle removed from the cutting tool; Next, ATC, will be replaced with the cutter knives were unloaded into the spindle and tool: Finally, back to the original ATC, "standby" position. At this point, ATC completed procedures to continue to run. This ATC, the main advantage of simple structure,the less movement, fast tool change. The main disadvantage is that knives must be kept in parallel with the axis of the plane, and after the home side compared to the tool, chip and liquid-cutting knife into the folder, it is necessary to the tool plus protection. Cone knife folder on the chip will cause ATC error, or even damage knife folders, and the possibility of spindle. Some processing centre at the transfer, and the tool side. When the ATC command is called, the transfer-cutter knives will be removed, the machine go forward, and positioning with the ATC, in line with the position. 180 º "Rotary ATC devices can be used horizontal machine, can also be used for vertical machining centers.2. 2 ATC head-turret installedWith rotating CNC machine tool often used such ATC devices, with a few turret head spindle, each with a spindle on both knives, the first tower interim process can be automatic tool change-realization. The advantage is simple structure, tool change time is short, only about 2 s. However, due to spatial constraints, the number of spindle can not be too much, usually only apply to processes less, not to high precision machine tools, such as the NC drill, such as CNC milling machine. In recent years there has been a mechanical hand and the turret head with a knife for the automatic tool change ATC devices, as shown in Figure 2.3. It is in fact a turret head ATC, and the knife-ATC device combination. The principle is as follows:5 turret on the first two tool spindle 3 and 4, when using the tool spindle 4 processing tool, the manipulator 2 will be the next step to the need for the tool does not work on the tool spindle 3 until after the completion of this process , the first rotary turret 180 º, ATC completed. ATC most of their time and processing time coincidence, the only real tool change time turret transposition of the first time, this approach mainly used for ATC and NC NC drilling file bed.2. 3.Daidao system for the automatic tool changeFigure 2.4 shows the knife and the whole machine tool CNC machine tools for the appearance of Fig. Figure 2.5 shows the knife and split-type machine to the appearance of CNC machine tool plans.At this point, knife storage capacity, a heavier tool can, and often additional transport unit to complete the knife between the spindle and cutting tool transport.Daidao the knife from the ATC, the election knives, automatic loading and unloading machine tool and tool exchange institutions (manipulator), composed of four parts, used widely.Tool Automatic Tool Change When CNC tool code and the code in line with directives of the tool selected, the rotary cutter knives will be sent to the ATC position, waiting to grab manipulator. Random knife election is the advantage of the cutter knife in the order has nothing to do with the processing sequence, the same tool can be used repeatedly. Therefore, the relatively small number of knives, knife the corresponding smaller. Random elections knife on the tool must be coded to identify. There are three main coding.1. Tool coding. Adopt special knife handle structure coding, the drawbars on the knife handle back-endpackages such as spacing of the coding part of the lock-nut fixed. Coding diameter ring diameter of a size two,respectively, said that binary "1" and "0" to the two rings are different, can be a series of code. For example, there are six small diameter of the ring can be made to distinguish between 63 (26-1 = 63) of the coding tool. All of 0 normally not allowed to use the the manipulator system, the whole process more complicated ATC. We must first used in the processing of all installed in the standard tool on the knife handle in the machine outside the pre-size, according to a certain way Add to the knife. ATC, selected first in the knife knife, and then from ATC, from the knife from the knife or spindle, exchange, the new knife into the spindle, the old knife back into the knife.ATC, as the former two knives to accommodate a limited number can not be too many, can not meet the needs of complex parts machining, CNC machine tool Automatic Tool Change Daidao the use of the automatic tool change devices. The knife has more capacity, both installed in the spindle box side or above. As for the automatic tool change Daidao device CNC machine tool spindle box only a spindle, spindle components to high stiffness to meet the machining requirements. The number of establishments in larger knife, which can meet the more complex parts of the machining processes, significantly improving productivity. Daidao system for the automatic tool change applied to drilling centres and CNC machining centers. The comparison drawn Daidao automatic tool change system is the most promising.3.PLC control of the knife random mode of election3. 1Common methods of automatic election knifeAutomatic control of the knife CNC refers to the system after the implementation of user instructions onthe knife library automation process, including the process to find knives and automatic tool change [(63,71]. CNC Machining Center device (CNC) directive issued by the election knife , a knife, the tool required to take the knife position, said the election automatic knife. automatically elected knife There are two ways: randomsequence election knives and knife election method.3.1.1 order election knifeTool Selection order is the process tool according to the sequence of the insert knife, the use of knives in order to take place, used knives back at the original knife, can also order Add Block, a knife. In this way, no need Tool identification devices, and drive control is a relatively simple, reliable and can be used directly from the points of the knife machinery to achieve. But the knives in each of the tool in different processes can not be reused, if the tool is installed in accordance with the order of the knife, there will be serious consequences. Theneed to increase the number of knives and knife the capacity of the tool and reduce the utilization of the knife.3.1.2Random election knifeRandom election under the knife is arbitrary instructions to select the required tools, then there must be tool identification devices. Tool knife in the library do not have the processing in accordance with the order of the workpiece can be arbitrary storage. Each of the tool (or knife blocks) are for a code, automatic tool change, the rotary cutter, every tool have been the "tool identification device" acceptable identification. When CNCtool code and the code in line with directives of the tool selected, the rotary cutter knives will be sent to the ATC position, waiting to grab manipulator. Random knife election is the advantage of the cutter knife in the order has nothing to do with the processing sequence, the same tool can be used repeatedly. Therefore, the relatively small number of knives, knife the corresponding smaller. Random elections knife on the tool must be coded to identify. There are three main coding.1. Tool coding. Adopt special knife handle structure coding, the drawbars on the knife handle back-end packages such as spacing of the coding part of the lock-nut fixed. Coding diameter ring diameter of a size two, respectively, said that binary "1" and "0" to the two rings are different, can be a series of code. For example, there are six small diameter of the ring can be made to distinguish between 63 (26-1 = 63) of the coding tool. All of 0 normally not allowed to use the code, to avoid the cutter knife Block did not confuse the situation.2. Knife Block coding. On the knife Block coding, coding tool, and tool into line with the number of knives in the Block. ATC knife when the rotation, so that each knife seats followed through knowledge knife, knife found blocks, knives stopped the rotation. At this time there is no knife handle encoding part of the knife handle simplified.3. Annex coding methods. This style of coding keys, coded cards, coding and coding-disc, which is the most widely used coding keys. First to knives are attached to a tool of the show wrapped coding keys, and when the cutter knife to the store at knife in, so put the number of keys to remember knife Block Road, will be inserted into key to the coding Block next to the key hole in the seat for the knife to the numbers. ConclusionFocused on in today's manufacturing environment tool storage and management of new models and methods, practical application of good results in systems integration and optimization, and other aspects of operations will be further explored, so that it has a higher theoretical and practical level.译文:机床刀具设计课题研究意义机床原来的刀库控制程序是单独设计的,没有采用刀具管理系统,功能也比较单一,只实现了刀库刀具的找刀、刀库最短路径定位、主轴换刀,而且不支持大型刀具。
数控机床设备资料中英文对照

数控机床设备资料中英文对照数控机床设备资料中英文对照一:说明书名次解释:lubrication hole[机]润滑孔; [机]滑油孔; 加油孔; [机]注润滑油孔Pressure Lubrication[机]压力润滑; 强制润滑; [机]加压润滑lubrication device润滑装置; 润滑油; 润滑装配AUTO LUBE 自动润滑Spindle motor 主轴马达Hydraulic pump motor 油压马达Auto Cross feed motor 前后马达High Pressure Through Coolant刀具高压冷却系统once-through coolant system一次流过冷却系统Coolant through spindle油水分离机sp. through coolant主轴通过冷却液through coolant通过冷却剂coolant jet冷却剂喷嘴flood coolant motor洪水冷却电机base coolant/gun motor基地冷却剂/枪电动机mist collect motor雾收集电动机Coolant motor (for tools/chips) 切削水马达Chip conveyor motor 铁屑输送机马达ATC motor 储刀仓马达fan cooler风扇冷却器fan draught cooler冷风机fan cooler(for amp):风扇冷却器(对放大器(amplifier))containment fan cooler安全壳风机冷却器fan-draught cooler风扇冷却器fan unit 风扇设备风扇单元风扇装置panel cooling 嵌入式降温panel door 镶板门panel heating 板壁供热tool counter工具柜台MAGAZINE CW 刀库正转MAGAZINE CCW 刀库反转 ...COUNTER (计数器)TOTAL COUNTER(总计数器)Mate:配对物(伴侣)Rotation:旋转回转Caution:谨慎radiator brake:散热器制动air duster blow gun吹尘器喷枪air-blow pipe喷气管Air Blow:鼓风Overload:超载overload protection防止过载,超载防护information overload信息过载;信息超载;信息超负荷overload capacity过载容量overload operation超负荷运行,超载运行thermal overload relay热继电器;热过载继电器overload current[电]过载电流 ; 过载电流过负荷电流dis connect jumper pin in case of using sub op存保计划连接跳线针如果使用子运算(in case of using如果使用;usb op 子运算)disconnect jumper pin断开连接跳线针beta-i servo :β-i 伺服spindle amplifer:主轴放大器manual feed delay:手动进给延迟rigid tapping ontime:刚性攻丝准时z-axis cancel:z轴取消Current Tool Number现行刀具号Reset Current Tool恢复当前工具预设servo amp module伺服放大器模块optical fiber cable:光缆、光纤光缆sheet key板键Head sheet Key头型图要点key sheet键盘纸; 转印盘纸i series servo motor:i系列伺服电动机call light:警示灯lub. motor on :润滑泵接通(lubricant润滑剂motor-on signal马达接通信号ATC forward:ATC 向前ATC reverse :ATC反向Ball screw: 滚珠丝杠Binary code :二进制DETACH:分离,脱开Follow-up :位置跟踪Black format:程序段格式Tool post interference check:刀架碰撞检查Abnormal load detection:异常负载检测Manual handle interruption:手轮中断Ladder diagram:梯形图(阶梯,关系图)Tool counter:工具柜台Magazine:刀库Brake module:制动模块Machine side:机侧Twist pair:双绞线Main power source:主电源Wiring diagram:接线图Current:现时状态、现行状态Dual table :双工作台Spare:备用件、预置Aux:辅助Brake on:制动器Mist :雾状、雾Coolant tank capacity:冷却泵油箱容量Enclosure:外壳、套、附件Overload:过载Flag:标志Condition:条件Machine ready delay:机床准备延迟Encoder:编码器Etherent:以太网口Orientation:主轴定向Spindle positioning:主轴定位Fault:故障Motion:运转Dwell:停歇,保压Feed rate:进给率Interlock/start-lock:互锁/启动-锁Spindle speed arrival check:主轴速度到达检测concent for maintenance答应为维护AC reactor:交流电抗器APC:绝对位置编码器反馈(Absolute position encoder feedback)arm in position z-axis interlock:手臂位置Z轴互锁Pressure:压力,压强,是……压迫Pressure valve[机]压力阀; [机]压力值; 止回阀; [机]回压阀air pressure气压; 空气压力; [建]工作气压; [物]气源压力consuming volume耗用量Oil:油Oller:n. 轮胎式压路机Capacity: n. 能力;容量;资格,地位;生产力bearing capacity[力]承载能力; [力]承载力; [力]承重能力; 支持力oil type 油的类型pumping n. [机] 抽吸;脉动;抽气效应v. 抽水(pump的ing形式)pumping out抽空; 扬水; 排出; 泵出pumping frequency[电子]泵频; 抽运频率; 泵送频率interval:间隔间距class interval[统计]组距; 组区间; 级距; 标度分组间隔Time interval[天]时间间隔; [天]时间区间; 时距; [天]时段interval scale[统计]区间尺度; 等距量表; [计]等距尺度; 等距量尺capacity:容量consuming:adj. 消费的;强烈的v. 消耗(consume的ing形式distributor分配器metering n. 计量,[测] 测量;测光模式v. 以计量器计量(meter 的ing形式metering valve[机]计量阀; 限流阀; [机]限量阀; [机]配量阀metering jet量孔; [油气]测油孔; 计量喷流OPTION:选择(选择功能块)ARM:机械手ARM home position:机械手原点位置soft key cable:软键电缆PUNCH PANEL:开孔面板MOTHER BOARD:母版Name:名称Description:描述Connector:连接器二、操作面板中英文对照:ABS和REL——在法那克系统中,按这两个键分别来切换当前机床的相对坐标和绝对坐标ALL——全选,程序编辑时用PRGRM——程序(program)的缩写,用于查看程序NEXT——查看程序和查看参数时,下一页OPRT——在法那克系统中,选择编辑程序时,也就是按下PRGRM后,再按这个键,才能输入程序号HOST,CONECT——这两个是在系统与外界通信时用的,我没试过,不知道什么作用HELP——查看帮助信息SHIFT——换档键,有些键有两个字符,按下这个键,用来输入顶部那个字符ALTER——程序修改键,编辑程序时用INSERT——程序插入键,编辑程序时用EOB——程序结束符,在编辑程序时,没段程序结束时,要加这个符号CAN——取消键,用来取消输入INPUT——输入键,用来输入程序或参数POS——按此键显示当前机床位置画面PROS——按此键显示当前程序画面OFFSET——按此键显示刀具偏置画面SETTING——按此键显示刀具偏置设定画面SYSTEM——按此键显示系统信息及系统状态画面GRAPH——按此键显示加工时刀具轨迹的图形画面CUSTOM——按此键显示用户宏程序画面手动数据输入(MDI)直接数字控制方法(DNC)控制器单元或机控制器单元(MCU)法拉克:ALTER 修改程序及代码INSRT 插入程序DELET 删除程序EOB 完成一句(END OF BLOCK)CAN 取消(EDIT 或MDI MODE 情况下使用)INPUT 输入程序及代码OUTPUT START 输出程序及指令OFFSET 储存刀具长度、半径补当值AUX GRAPH 显示图形PRGRM 显示程序内容ALARM 显示发生警报内容或代码POS 显示坐标DGONS PARAM 显示自我诊断及参数功能RESET 返回停止CURSOR 光标上下移动PAGE 上下翻页三、常用缩写:启动start STRT停止stop ST运行run正转forward FWD反转reverse REV加速accelerate减速reduce RED低速low L中速medium M高速high H主轴方向spindle direction向前forward FWD向后backward向左left L向右 right R诊断:DGNOS信息:MSG操作员:OPER参数:PARAM目录:DIR取代:ALTER公共地线,公共线:COM四、其它常用词句中英文对照:金属切削 metal cutting机床 machine tool金属工艺学 technology of metals 刀具 cutter 摩擦 friction联结 link传动 drive/transmission轴 shaft弹性 elasticity频率特性 frequency characteristic 误差 error 响应 response定位 allocation机床夹具 jig动力学 dynamic运动学 kinematic静力学 static分析力学 analyse mechanics拉伸 pulling压缩 hitting剪切 shear扭转 twist弯曲应力 bending stress强度 intensity三相交流电 three-phase AC磁路 magnetic circles变压器 transformer异步电动机 asynchronous motor几何形状 geometrical精度 precision正弦形的 sinusoid交流电路 AC circuit机械加工余量 machining allowance 变形力 deforming force 变形 deformation应力 stress硬度 rigidity热处理 heat treatment退火 anneal正火 normalizing脱碳 decarburization渗碳 carburization电路 circuit半导体元件 semiconductor element 反馈 feedback发生器 generator直流电源 DC electrical source门电路 gate circuit逻辑代数 logic algebra外圆磨削 external grinding内圆磨削 internal grinding平面磨削 plane grinding变速箱 gearbox离合器 clutch绞孔 fraising绞刀 reamer螺纹加工 thread processing螺钉 screw铣削 mill铣刀 milling cutter功率 power工件 workpiece齿轮加工 gear mechining齿轮 gear主运动 main movement主运动方向 direction of main movement进给方向 direction of feed进给运动 feed movement合成进给运动 resultant movement of feed合成切削运动 resultant movement of cutting合成切削运动方向 direction of resultant movement of cutting 切削深度 cutting depth前刀面 rake face刀尖 nose of tool前角 rake angle后角 clearance angle龙门刨削 planing主轴 spindle主轴箱 headstock卡盘 chuck加工中心 machining center车刀 lathe tool车床 lathe钻削镗削 bore车削 turning磨床 grinder基准 benchmark钳工 locksmith锻 forge压模 stamping焊 weld拉床 broaching machine拉孔 broaching装配 assembling铸造 found流体动力学 fluid dynamics流体力学 fluid mechanics加工 machining液压 hydraulic pressure切线 tangent机电一体化 mechanotronics mechanical-electrical integration 气压 air pressure pneumatic pressure稳定性 stability介质 medium液压驱动泵 fluid clutch液压泵 hydraulic pump阀门 valve失效 invalidation强度 intensity载荷 load应力 stress安全系数 safty factor可靠性 reliability螺纹 thread螺旋 helix键 spline销 pin滚动轴承 rolling bearing滑动轴承 sliding bearing弹簧 spring制动器 arrester brake十字结联轴节 crosshead联轴器 coupling链 chain皮带 strap精加工 finish machining粗加工 rough machining变速箱体 gearbox casing腐蚀 rust氧化 oxidation磨损 wear耐用度 durability随机信号 random signal离散信号 discrete signal超声传感器 ultrasonic sensor集成电路 integrate circuit挡板 orifice plate残余应力 residual stress套筒 sleeve扭力 torsion冷加工 cold machining电动机 electromotor汽缸 cylinder过盈配合 interference fit热加工 hotwork摄像头 CCD camera倒角 rounding chamfer优化设计 optimal design工业造型设计industrial moulding design 有限元finiteelement滚齿 hobbing插齿 gear shaping伺服电机 actuating motor铣床 milling machine钻床 drill machine镗床 boring machine步进电机 stepper motor丝杠 screw rod导轨 lead rail组件 subassembly可编程序逻辑控制器 Programmable Logic Controller PLC 电火花加工 electric spark machining电火花线切割加工electrical discharge wire - cutting 相图phase diagram热处理 heat treatment固态相变 solid state phase changes有色金属 nonferrous metal陶瓷 ceramics合成纤维 synthetic fibre电化学腐蚀 electrochemical corrosion车架 automotive chassis悬架 suspension转向器 redirector变速器 speed changer板料冲压 sheet metal parts孔加工 spot facing machining车间 workshop工程技术人员 engineer气动夹紧 pneuma lock数学模型 mathematical model画法几何 descriptive geometry机械制图 Mechanical drawing投影 projection视图 view剖视图 profile chart标准件 standard component零件图 part drawing装配图 assembly drawing尺寸标注 size marking技术要求 technical requirements刚度 rigidity内力 internal force位移 displacement截面 section疲劳极限 fatigue limit断裂 fracture塑性变形 plastic distortion脆性材料 brittleness material刚度准则 rigidity criterion垫圈 washer垫片 spacer直齿圆柱齿轮 straight toothed spur gear 斜齿圆柱齿轮 helical-spur gear直齿锥齿轮 straight bevel gear运动简图 kinematic sketch齿轮齿条 pinion and rack蜗杆蜗轮 worm and worm gear虚约束 passive constraint曲柄 crank摇杆 racker凸轮 cams共轭曲线 conjugate curve范成法 generation method定义域 definitional domain值域 range导数\\\\微分 differential coefficient求导 derivation定积分 definite integral不定积分 indefinite integral曲率 curvature偏微分 partial differential毛坯 rough游标卡尺 slide caliper千分尺 micrometer calipers攻丝 tap二阶行列式 second order determinant逆矩阵 inverse matrix线性方程组 linear equations概率 probability随机变量 random variable排列组合 permutation and combination气体状态方程 equation of state of gas 动能 kinetic energy势能 potential energy机械能守恒conservation of mechanical energy 动量momentum桁架 truss轴线 axes余子式 cofactor逻辑电路 logic circuit触发器 flip-flop脉冲波形 pulse shape数模 digital analogy液压传动机构 fluid drive mechanism 机械零件 mechanical parts淬火冷却 quench淬火 hardening回火 tempering调质 hardening and tempering磨粒 abrasive grain结合剂 bonding agent砂轮 grinding wheel。
机床术语中英文对照表汇总
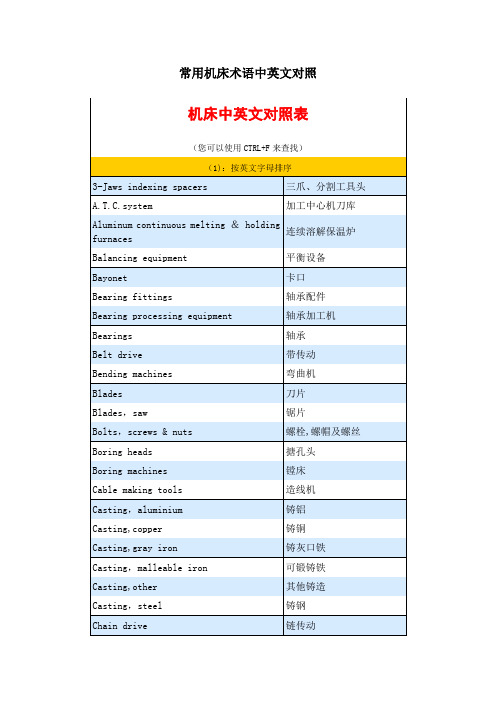
Lapping machines,centerless
无心精研机
Laser cutting
激光切割
Laser cutting for SMT stensil
激光钢板切割机
Lathe bench
车床工作台
Lathes,automatic
自动车床
Lathes,heavy—duty
重型车床
Lathes,high-speed
Die casting machines
压铸机
Dies—progressive
连续冲模
Disposable toolholder bits
舍弃式刀头
Drawing machines
拔丝机
Drilling machines
钻床
Drilling machines bench
钻床工作台
Drilling machines,high-speed
电脑数控磨床
CNC lathes
电脑数控车床
CNC machine tool fittings
电脑数控机床配件
CNC milling machines
电脑数控铣床
CNC shearing machines
电脑数控剪切机
CNC toolings
CNC刀杆
CNC wire—cutting machines
presses,crank
曲柄压力机
Presses,eccentric
离心压力机
Presses,forging
锻压机
Presses,hydraulic
液压冲床
Presses,knuckle joint
肘杆式压力机
Presses,pneumatic
数控机床英语
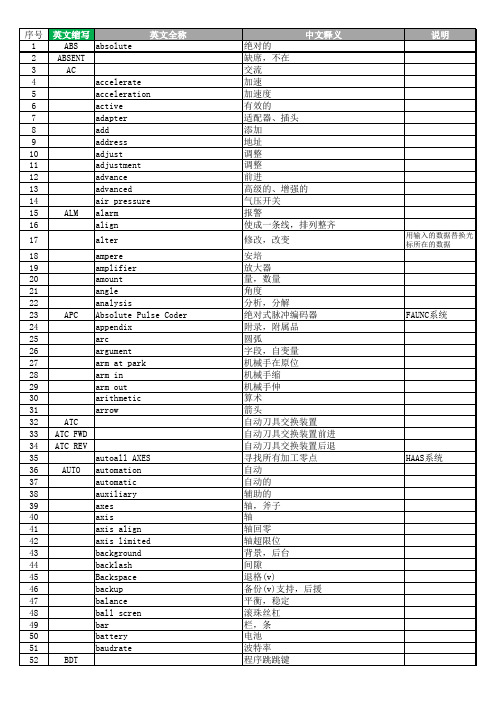
显示器
data date datum damage DC deceleration decimal piont decrease deep define deg degree DEL delete delay delete/deletion des cription detect/detection device DGN/DGNOS diagnose DI DIAG diagnosis diameter
序号 1 2 3 4 5 6 7 8 9 10 11 12 13 14 15 16 17 18 19 20 21 22 23 24 25 26 27 28 29 30 31 32 33 34 35 36 37 38 39 40 41 42 43 44 45 46 47 48 49 50 solute ABSENT AC accelerate acceleration active adapter add address adjust adjustment advance advanced air pressure ALM alarm align alter ampere amplifier amount angle analysis Absolute Pulse Coder appendix arc argument arm at park arm in arm out arithmetic arrow
DIR
disk
DISP
diamond digital dimension directory direction disconnect/disconnection diskette dispense display dispose/disposal distance divide
DMR DNC DO dog switch DOS DRAM drawing dress/dresser drift drill drive/driver drop droop dry dry run DTE drum drum to park drum to spindle duplicat/duplication dwell edbug edit electrical electronic emergency empty enable encoder end enter entry end of block equal equipment erase error escape emergency stop exact
机床行业中英文对照

机床行业中英文对照下面是机床行业中常见的英文对照:- 机床行业:Machine tool industry- 机床:Machine tool- 数控机床:Computer Numerical Control (CNC) machine tool - 金属切削机床:Metal cutting machine tool- 金属加工机床:Metal processing machine tool- 金属成型机床:Metal forming machine tool- 车床:Lathe- 铣床:Milling machine- 钻床:Drilling machine- 磨床:Grinding machine- 塑料加工机床:Plastic processing machine tool- 精密机床:Precision machine tool- 自动化机床:Automated machine tool- 机床控制系统:Machine tool control system- 数控系统:Numerical control system- 机床加工能力:Machine tool processing capacity- 加工精度:Processing accuracy- 切削速度:Cutting speed- 进给速度:Feed rate- 主轴转速:Spindle speed- 工件夹紧:Workpiece clamping- 工件定位:Workpiece positioning- 刀具选择:Tool selection- 刀具更换:Tool change- 冷却液:Coolant- 刀柄:Tool holder- 加工中心:Machining center- 排屑:Chip removal- 刀具磨损:Tool wear- 折弯机:Bending machine- 冲床:Punching machine- 压力机:Press machine- 剪板机:Shearing machine- 抛光机:Polishing machine- 螺纹机床:Thread cutting machine tool - 铸造机床:Casting machine tool- 灰铁:Gray iron- 球墨铸铁:Ductile iron- 铝合金:Aluminum alloy- 不锈钢:Stainless steel- 最大加工尺寸:Maximum processing size - 机床设计:Machine tool design- 机床制造:Machine tool manufacturing - 机床市场:Machine tool market- 机床出口:Machine tool export- 机床进口:Machine tool import- 机床行业协会:Machine tool industry association。
数控机床中英文翻译资料

中文1700字数字控制的历史在机床领域工作的任何人都不能忽视计算机对制造业的影响。
这些机床对工业的影响能力强迫公司经理和所有者更新他们的思想来保持竞争力。
这些机床的固有准确性和反复性已经帮助了质量过程工具例如统计过程控制在金工车间获得立足处。
NC/CNC机床的演变数字控制其实不是什么新东西。
早在1808年织机装入带孔的金属卡片控制所生产布料的样式。
机器的每根针由装入的卡上孔的有无来控制。
卡片成为机器的程序。
如果改变了卡片,样式也跟着改变。
自动钢琴也是数字控制的例子。
自动钢琴使用带孔的纸卷。
孔的有无决定音符是否被演奏。
空气被用于感应孔是否存在。
计算机的发明是数字控制的一个转折点。
1943年,称作ENIAC (电子数字积分器和计算机)的第一台计算机被制成。
ENIAC计算机非常大。
它占地超过1500平方英尺并使用大约18,000根真空管运算。
但真空管发热成为一个困扰的问题。
计算机仅能运行几分钟管子就失效。
另外,计算机重达数吨并非常难于编程。
ENIAC通过使用数以万计的开关来编程。
今天价值15美圆的计算器也远比这个早期的尝试更功能强大。
计算机技术领域真正的转折点是1948年晶体管的发明。
晶体管是真空管的替换品。
它体积小,便宜,可靠,耗能少,并且发热低。
真空管的完美取代品。
直到20世纪60年代晶体管才在工业中大量使用。
集成电路原件在1959年一种新技术涌现了:集成电路(ICs)。
集成电路实际是芯片上的控制电路。
当制造商发现了如何小型化电路,它比晶体管更有助于减小尺寸和改进电子控制的可靠性。
大规模集成电路大规模生产是在1965年。
在1974年发明了微处理器。
由此产生了微型计算机,使小规模运用成为可能。
计算机记忆卡制造的巨大进步使它计算机更加功能强大而容易支付。
作为政府生产高精度副翼的方法数控机床的原始构想源于20世纪50年代。
这些复杂的零件用传统方法制造并且通过和模板作比较来检验它们。
模板也必须用传统方法制造,是非常费时和不精确的。
机床术语中英文对照表

Manifolds
集合管
Milling heads
铣头
Milling machines
铣床
Milling machines,bed type
床身式铣床
Milling machines,duplicating
仿形铣床
Milling machines,horizontal
卧式铣床
Milling machines,turret vertical
铝轮冒口切断机
P type PVC waterproof rolled sheet making plant
P型PVC高分子防水
PCB fine piecing systems
印刷电器板油压冲孔脱料系统
Pipe & tube making machines
管筒制造机
Planing machines
刨床
电动刀具
Engraving machines
雕刻机
Engraving machines,laser
激光雕刻机
Etching machines
蚀刻机
Finishing machines
修整机
Fixture
夹具
Forging dies
锻模
Forging,aluminium
锻铝
Forging,cold
冷锻
自动压力机
Pressing dies
压模
Punch formers
冲子研磨器
Quick die change systems
速换模系统
Quick mold change systems
快速换模系统
Reverberatory furnaces
- 1、下载文档前请自行甄别文档内容的完整性,平台不提供额外的编辑、内容补充、找答案等附加服务。
- 2、"仅部分预览"的文档,不可在线预览部分如存在完整性等问题,可反馈申请退款(可完整预览的文档不适用该条件!)。
- 3、如文档侵犯您的权益,请联系客服反馈,我们会尽快为您处理(人工客服工作时间:9:00-18:30)。
中文1700字数字控制的历史在机床领域工作的任何人都不能忽视计算机对制造业的影响。
这些机床对工业的影响能力强迫公司经理和所有者更新他们的思想来保持竞争力。
这些机床的固有准确性和反复性已经帮助了质量过程工具例如统计过程控制在金工车间获得立足处。
NC/CNC机床的演变数字控制其实不是什么新东西。
早在1808年织机装入带孔的金属卡片控制所生产布料的样式。
机器的每根针由装入的卡上孔的有无来控制。
卡片成为机器的程序。
如果改变了卡片,样式也跟着改变。
自动钢琴也是数字控制的例子。
自动钢琴使用带孔的纸卷。
孔的有无决定音符是否被演奏。
空气被用于感应孔是否存在。
计算机的发明是数字控制的一个转折点。
1943年,称作ENIAC (电子数字积分器和计算机)的第一台计算机被制成。
ENIAC计算机非常大。
它占地超过1500平方英尺并使用大约18,000根真空管运算。
但真空管发热成为一个困扰的问题。
计算机仅能运行几分钟管子就失效。
另外,计算机重达数吨并非常难于编程。
ENIAC通过使用数以万计的开关来编程。
今天价值15美圆的计算器也远比这个早期的尝试更功能强大。
计算机技术领域真正的转折点是1948年晶体管的发明。
晶体管是真空管的替换品。
它体积小,便宜,可靠,耗能少,并且发热低。
真空管的完美取代品。
直到20世纪60年代晶体管才在工业中大量使用。
集成电路原件在1959年一种新技术涌现了:集成电路(ICs)。
集成电路实际是芯片上的控制电路。
当制造商发现了如何小型化电路,它比晶体管更有助于减小尺寸和改进电子控制的可靠性。
大规模集成电路大规模生产是在1965年。
在1974年发明了微处理器。
由此产生了微型计算机,使小规模运用成为可能。
计算机记忆卡制造的巨大进步使它计算机更加功能强大而容易支付。
作为政府生产高精度副翼的方法数控机床的原始构想源于20世纪50年代。
这些复杂的零件用传统方法制造并且通过和模板作比较来检验它们。
模板也必须用传统方法制造,是非常费时和不精确的。
然而,在Michigan一个商店,一个叫做John Parsons的人正在研究一种新方法来改进直升机动叶片模板的制造方法。
Parsons是工具室学徒而且没有大学学位。
Parson的方法是计算沿副翼表面的坐标点。
通过计算大量的中间点然后移动机床到每个点,模板的精度就改进了。
Parsons提出用穿孔的卡片来进行大量计算的主意。
这些数据用来定位机床。
1948年Parsons向空军递交发展生产这些模板的机器的提案并得到认同。
他第一次试图在自动控制中使用穿孔卡制表机计算沿副翼曲线的方位并用普通铣床定位刀具到制表机位置。
他有二名操作员,一个移动机器的每根轴。
这种方法生产的副翼比先前方法高达十倍精度,但仍然是一个非常费时的过程。
1949年,空军要求Parsons生产能移动机器的轴来自动计算点位置的一种控制系统。
麻省理工学院(MIT)由Parsons转包来发展能控制机器轴的马达。
伺服电动机诞生了。
Parsons构想了随后的系统。
计算机能计算刀具应该遵循的轨迹并在穿孔卡上储存信息。
机器的操作者能读出卡片。
控制机器从操作者得到数据并控制附着在每根轴上的马达。
1951年 MIT被授予开发控制机器的主要合同。
第一台由Parsons和MIT生产的机器在1952年展出。
叫做Cincinnati Hydrotel,它是一台三轴垂直心轴的铣床。
这个控制机器使用真空管。
在使人编程更容易的其中一个早期尝试叫做APT(自动编程工具)符号语言。
APT,发明于1954年,使用机床能读懂的和英文相似的符号语言来编制程序。
记住,机器需要零件的几何外型和例如速度、饲料和冷却液的机器指令来运行。
APT使人们写这些程序变得更容易,这些程序随后又被翻译成机器能读懂的另一种程序。
1955年空军得到制造数控机器的35,000,000美圆的合同。
第一台数控机床非常庞大。
这个控制机器靠真空管运行并需要一个分开的计算机来生成它的二进制磁带代码。
(二进制代码系统使用0和1)。
复杂零件的编程需要非常专业的人员。
随着继续的发展和提炼,60年代初期数字控制机器在工业中变得更加普通。
数字控制机器广泛接受,它们变得更加功能强大和容易使用。
直到大约1976年这些机器被称作NC(数字控制)机器。
1976年CNC (计算机数字控制)机器出现了。
这些控制机器使用微处理器给了他们额外的功能。
他们也以外存储为特色。
代表性的NCs每次读取一步程序(块)并执行它;然而,CNC机床能够存储整个程序。
20世纪70和80年代后期计算机技术的改善使数控机床的价格跌到一个很多制造公司不能再没有它们的水平。
HISTORY OF NUMERICAL CONTROLAnyone working in the machine tool field cannot ignore the influence of the computer in manufacturing. The capabilities that these machine tools have given to the industry have forced managers and owners of companies to update their thinking to stay competitive. The inherent accuracy and repeatability of these machine tools have helped quality process tools such as statistical process control gain a foothold in machine shops.EVOLUTION OF THE NC/CNC MACHINENumerical control is nothing new. As early as 1808 weaving machines used metal cards with holes punched in them to control the pattern of the cloth being produced. Each needle on the machine was controlled by the presence or absence of a hole on the punched cards. The cards were the program for the machine. If the cards were changed, the pattern changed.The players piano is also an example of numerical control. The player piano uses a roll of paper with holes punched in it. The presence or absence of a hole determined if that note was played. Air was used to sense whether a hole was present.The invention of the computer was one of the turning points in numerical control. In 1943 the first computer, called ENIAC (Electronic Numerical Integrator and Computer) was built.The ENIAC computer was very large. It occupied more than 1500 square feet and used approximately 18,000 vacuum tubes to do its calculations. The heat generated by the vacuum tubes was a constant problem. The computer could operate only a few minutes without a tube failing. In addition, the computer weighed many tons and was very difficult to program. ENIAC was programmed through the use of thousands of switches. The $15 calculator available today is much more powerful than this early attempt.The real turning point in computer technology was the invention of the transistor in 1948. The transistor was the replacement for the vacuum tube. It was very small, cheap, dependable, used very little power, and generated very little heat: the perfect replacement for the vacuum tube. The transistor did not see much industrial use until the 1960s.INTEGRATED CIRCUITRYIn 1959 a new technology emerged: integrated circuits (ICs). Integrated circuits were actually control circuits on a chip. When manufacturers discovered how to miniaturize circuits, it helped reduce the size and improve the dependability of electronic control even more than the transistor had. Large-scale integrated circuits first were produced in 1965.In 1974 the microprocessor was invented.This made the microcomputer, and thus small application, possible.Great strides in the manufacture of memory for computers helped make computers more powerful and affordable.The original conception of numerically controlled machine tools occurred in the 1950s as a method of producing airfoils of great accuracy for the government.These complex parts were made by manual machining methods and inspected by comparing them to templates. The templates also had to be manufactured by manual methods, which was very time consuming and inaccurate.However, in a shop in Traverse City, Michigan,a man named John Parsons was working on a method to improve the production of inspection templates for helicopter rotor blades. Parsons started as a tool room apprentice and had no college degree.Parsons’ method involved calculating the coordinate points along the airfoil surface. By calculating a large number of intermediate points and then manually moving the machine tool to each of these points, the accuracy of the templates was improved. Parsons came up with the idea of using punched cards for the many calculations. The data could then be used to position the machine tool. Parsons submitted a proposal to the Air Force to develop a machine to produce these templates and received a development contract in 1948. His first attempts at automatic position control used punchcard tabulating machines to calculate the positions along the airfoil curve and an ordinary manual milling machine to position the tool to the tabulated positions. He had two operators, one to move each axis of the machine. This method produced airfoils tens of times more accurate than the preceding method, but was still a very time-consuming process.In 1949,the Air Force awarded Parsons a contract to produce a control system that could move the axis of a machine to calculated points automatically. The Massachusetts Institute of Technology (MIT) was subcontracted by Parsons to develop a motor that could control the axis of the machines. The servo motor was born.Parsons envisioned the following system. A computer would calculate the path that the tool should follow and store that information on punched cards. A reader at the machine would then read the cards. The machine control would take the data from the reader and control the motors attached to each axis.In 1951 MIT was awarded the prime contract to develop the machine control. The first machine produced by Parsons and MIT was demonstrated in 1952. Called a Cincinnati Hydrotel, it was a three-axis vertical spindle milling machine. The machine control used vacuum tubes.One of the first attempts at making programming easier for people was called APT (Automatically Programmed Tool) Symbolic Language. APT, invented in 1954, used English-like symbolic language to produce a program that the machine tool could understand. Remember, a machine needs the geometry of the part and machining instructions such as speeds, feeds, and coolant to operate. APT made it easier for people to write these programs, which were then translated to a program that the machine could understand.In 1955 the Air Force awarded $35million in contracts to manufacture numerical control machines. The first numerically controlled machine tools were very bulky. The machine control was vacuum-tube operated and needed a separate computer to generate its binary tape codes. (Binary coding systems use 1s and 0s). Programming complex parts took highly specialized people. Developments and refinements continued, and by the early 1960snumerical control machines became much more common in industry. As the acceptance of numerical control machines grew, they became easier to use and more powerful.Up until about 1976 these machines were called NC (numerical control) machines. In 1976 CNC (computer numerical control) machines were produced. These machine controls used microprocessors to give them additional capability. They also featured additional memory. The NCs typically read one short program step (block) at a time and executed it; however, CNC machines could store whole programs.Improvements in computer technology in the late 1970s and 1980s brought the cost of numerical control machines down to a level where most manufacturing companies cannot afford to be without them.。