酸性镀铜液中抑制添加剂的测定
酸性镀铜添加剂的三度平衡

酸性镀铜添加剂三维平衡酸性镀铜添加剂工艺上分为抑制剂A、加速剂B、开缸剂C。
我们可以从位置、大小、阴阳属性三个角度重新将A、B、C分类,便于快速准确定位工艺故障和迅速排除故障。
一.位置:按照三种添加剂主要吸附赫氏槽试片或镀件高低电位的特征可分为,抑制剂A高电位优先吸附,且称“高位剂”;加速剂B易于吸附作用于过电位较小的深位、低洼,且称“低位剂”;开缸剂C高低位均匀吸附,且称为“中位剂”。
开缸剂C中含有20%左右的加速剂B,比抑制剂A抑制性更强的强走位剂及大量表面活性剂。
只有其中的B剂显示位置极性。
故,我们可以得到添加剂的极性位置均衡式:位置均衡:A≈B+C二.大小:按照三种添加剂分子大小特征可分为高分子,大分子,小分子三种,高分子一般是大分子的几百到几万倍,大分子是小分子的几十倍。
开缸剂C主要组分是高分子,抑制剂A主要组分是大分子,加速剂B主要组分是小分子。
故,我们可以得到添加剂的分子大小搭配均衡式:大小均衡:C≈A+B三.阴阳属性:按照三种添加剂对阴极反应速度即阴极极化度的贡献特征可分为阳性,阴性两种,能够加速阴极反应降低阴极极化度的称为“阳性剂”,能够抑制阴极反应速度提高阴极极化度的称为“阴性性剂”,抑制剂A和开缸剂C均属阴性,加速剂B则属阳性。
故,我们可以得到添加剂分子阴阳搭配的阴阳均衡式:阴阳均衡:B≈A+C.四.结论:酸性镀铜抑制剂A、加速剂B和开缸剂C三种添加剂在镀液中必须同时满足位置均衡、大小均衡和阴阳均衡,才是正在意义上的均衡,且称“完全均衡”或“三度均衡”,只有三度均衡,才能将添加剂的作用发挥到极致。
我们以位置、大小、阴阳属性三维坐标来定位添加剂的搭配情况,借助于10分钟、0.25A的赫氏槽试片,就能准确定位抑制剂A、加速剂B和开缸剂C三种添加剂的多寡,比如镜面填平宽度太窄,低位很容易发黑,那一定是大小失衡,开缸剂C<<A+B,应逐步提高开缸剂C的比例。
而镜面填平区超过70%,但镀件光面易于朦雾,那也是大小失衡,开缸剂C>>A+B,应逐步提高A、B剂对开缸剂C的比例。
印制电路板酸性电镀铜电镀添加剂的应用及其机理研究

中文摘要摘要印制电路板(Printed Circuit Board, PCB)是电子产品的必要组成部分,是支撑电子产品中电子元件的载体,其广泛应用于不同种类的电子器件中。
随着社会的不断进步,人类所追求的电子产品快速向微型化、便捷化、智能化方向发展,拥有高密度互联的多层印刷电路板(HDI-PCB)是制造这些复杂电子产品的重要成分之一。
目前,为了满足社会要求,所需PCB盲孔孔径不断缩小,孔的深径比越来越大,对PCB电镀工艺的要求更高。
而盲孔孔金属化是PCB电镀的核心,是实现多层电路板层与层之间连接的重要路径之一,也是目前PCB生产工艺中非常重要而成熟的技术之一。
但在直流电镀过程中,由于盲孔内电流密度分布不均,孔口电流密度较大,容易出现封孔现象,导致盲孔填充质量下降。
因此,为了获得良好的盲孔填充性能和均匀的铜镀层,镀液中采用添加有机添加剂的方式是非常有效而经济的。
为此,本文以微盲孔填充电镀铜添加剂为主要研究目标,首先对盲孔电镀添加剂的各种成分进行预筛选并通过电镀试验验证该组合添加剂体系并与之确定;其次,研究了各种添加剂成分对PCB微盲孔填铜效果的影响及其性能表征。
详细研究内容及相关结论如下:1、盲孔电镀添加剂的筛选及体系确定(1)通过对大量学者以往研究内容进行比较分析,确定了适宜的卤素离子(Cl-)、加速剂(聚二硫二丙烷磺酸钠:SPS)和抑制剂(聚乙二醇8000:PEG-8000)。
(2)借助筛选金属缓蚀剂的手段筛选出合适的电镀整平剂(4,6-二甲基-2-巯基嘧啶:DMP,2-硫代巴比妥酸:TBA),通过原子力显微镜(AFM)和X射线光电子能谱(XPS)测试并结合量子化学计算和分子动力模拟探究了DMP和TBA分子在铜表面的吸附行为和吸附机理,证明了它们可以通过嘧啶环平行吸附于铜的表面,使得进行电化学反应的有效面积减小,铜的表面沉积速度越慢,沉积层也就越均匀,从而有利于微盲孔的填充,也间接性的证明了它们可能是一种潜在的,有效的电镀整平剂。
电镀添加剂之电镀液分析

电镀添加剂之电镀液分析电镀添加剂在使用过程中经常需要分析镀液,一般的电镀厂没有自己的化验室,我们公司可以为客户分析化验电镀添加剂镀液,电镀厂就能随时掌控电镀槽镀液的情况。
常见电镀液的分析方法一、酸性镀锌(硫酸盐镀锌)1、锌测定:取镀液10ml于100容量瓶中,加水至刻度,取此稀释液5ml,加水30ml,逐滴滴加1:1NH3·H2O调至微浑浊,加入1:4三乙醇胺10ml,pH=10缓冲溶液5ml,EBT指示剂少许,用0.05mol/lEDTA标准液滴定至兰色。
CZnSO4·7H2O=M×V×288/n (g/l)M——EDTA标准液浓度,mol/lV——消耗EDTA标准液体积,mln——吸取镀液毫升数。
2、铝的测定取镀液1ml于250ml锥形瓶中,加水50mL,加入0.05mol/lEDTA标准液40ml,pH=5的缓冲溶液15ml,煮沸2min,冷却,加XO2滴,用0.05mol/l标准锌溶液滴定至紫红色,体积不记。
加NH4F1.5g,加热近沸腾,冷却,补加XO1~2滴,用0.05mol/l标准锌溶液滴定至紫红色为终点。
CAl2(SO4)3·18H2O=MV×666.4/2 (g/l)M——锌标准溶液浓度,mol/lV——EDTA标准溶液体积,ml666.4——Al2(SO4)3·18H2O分子量3、氯化物测定取镀液10ml于100容量瓶中,加水至刻度,取此稀释液5ml于250ml锥形瓶中,加水100mL,1ml5%K2CrO4指示剂,以0.1mol/lAgNO3标液滴定至白色沉淀中有红色沉淀为终点。
CnaCl=MV×58.5/0.5 (g/l)M——AgNO3标液浓度mol/lV——AgNO3消耗标准液体积,ml试剂:5%K2CrO4指示剂:5gK2CrO4溶于95ml水中;0.1mol/lAgNO3标准溶液二、钾盐镀锌(氯化钾镀锌添加剂)1、锌测定:同“一中1”2、NaCl测定:同“一中2”3、H3BO3测定取500ml镀液,预先调pH=5左右。
酸性镀铜工艺及添加剂使用

酸性镀铜工艺及添加剂使用刘强高级工程师1. 前言全光亮酸性镀铜工艺参数即基础成分和操作参数严格按照电镀产品要求确定:要求最高光亮度和最高填平速度的铜酸比(五水硫酸铜与硫酸之比)最高可达到4.6,硫酸铜最高可达到230g/l,硫酸最低可达50g/l;随着对均镀能力和走位深度要求的提高,必须通过调低对最高光亮度和最高填平速度的要求,装饰性电镀铜酸比最低可降至1.8,硫酸铜最低可降至150g/l,硫酸最高可达到85g/l。
对于均镀能力和走位深度要求极高的线路板行业电镀铜,铜酸比最低可降至0.33,硫酸铜最低可降至50g/l,硫酸最高可达到150g/l。
因此全光亮酸性镀铜工艺的逻辑是:①硫酸铜与硫酸的维护方向因同离子效应限制,填平光亮和均匀走深要求重点的限制而完全相反;②要提高填平速度和出光光亮度,就要提高铜酸比和硫酸铜绝对含量,牺牲部分均镀能力和走位深度;要提高均镀能力和走位深度,就要降低铜酸比和硫酸铜绝对含量,牺牲部分填平速度和出光光亮度。
通过对铜酸比和硫酸铜含量的检测,就能知道在0.33-4.6铜酸比所处的位置,以及当前位置是填平光亮度不能满足要求还是均匀走深度不能满足要求。
当铜酸比、硫酸铜策略确定后,添加剂的抑制比策略应与铜酸比策略大方向一致以保持重点要求最佳化,局部相对抗,以防一边倒产生均匀走深或填平出光性能恶化。
镀液高低区沉积速度相对均衡。
例如对于填平出光型镀液,硫酸铜很高,硫酸很低,填平剂、开缸剂要低,光亮剂要高,当低位走深和均匀度不能满足要求时适当提高提高填平剂、开缸剂比例;对于均匀走深型镀液,硫酸铜很低,硫酸很高,填平剂、开缸剂要高,光亮剂要低,当填平出光速度不能满足要求时适当提高提高光亮剂比例;要达到良好的效果,不仅高低铜酸比充分发挥其长,更关键在于添加剂杨其长,避其短,力量均衡。
对填平出光要求低对均匀走深要求高的产品,大比例使用光亮剂,不仅浪费,而且导致低位达不到要求;对填平出光要求高对均匀走深要求低的产品,大比例使用填平剂、开缸剂导致出光填平速度慢,低位孔隙难填平,发黑发暗,高位电流范围被压缩,易起雾朦,甚至烧焦。
添加剂对酸性镀铜耐蚀性的研究
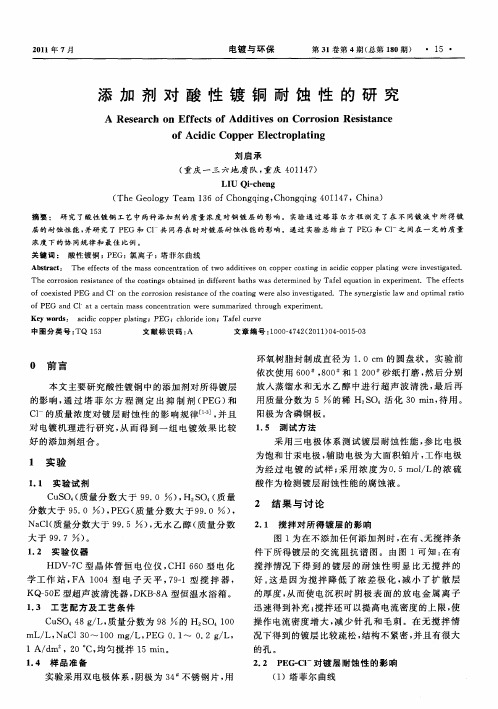
o EG n 。 ta c ran ma s c n e ta i n we e s mma ie h o g x e i n . fP a d C1 a e t i s o c n r t r u o r dt r u h e p r z me t Ke r s a i i c p e l t g;PEG;c l rd n y wo d : cd c o p r pa i n h o i ei ;Ta e u v o l 1c r e
21 年 7 01 月
电镀与环 保
第 3 卷第 4 总第 10 ・1 ・ l 期( 8 期) 5
添 加 剂 对 酸 性 镀 铜 耐 蚀 性 的 研 究
A s a c Ol Ef e t f Ad tv s O r o i n Re i t nc Re e r b i f cs o dii e i Co r so s s a e l o i c Co f Ac di ppe e t 0 a i g r Elc r pl tn
Th o r so e it n eo h o t g b an d i i e e tb t s wa e e mi e y Ta e q a i n i x e i n .Th fe t ec r o i n r ss a c f e c a i so t i e n d f r n a h sd t r n d b f 1 u t e p rme t t n f e o n ee f c s
阳极 为含磷 铜板 。
1 5 测 试 方 法 .
对 电镀机 理进 行研 究 , 而 得 到 一组 电镀 效 果 比较 从 好 的添加剂 组 合 。
采 用 三 电极 体 系测 试 镀层 耐 蚀 性 能 , 比 电极 参
酸性硫酸盐镀铜溶液有机杂质处理chenqiwu

铜包钢酸性镀铜溶液有机杂质处理王长喜陈启武(青岛技师学院26000)(湖北三众金属制品公司443200)在电镀生产时,酸性硫酸盐镀铜因其效率高,溶液成分简单,其溶液相对其它工艺稳定性较好,因此,在铜包钢加厚镀铜厚生产中得到应用。
但是溶液因长期使用,添加剂会分解成有害的有机杂质,并会越积越多,干涉铜离子的正常沉积,大大降低铜包钢丝的镀铜层质量。
有机杂质也是镀液中最常见、最容易产生的杂质,其含量达到一定的数量时,使得电镀生产无法进行。
必须正确分析其产生的原因、对镀铜层的危害、并运用最佳的方法,对存在于镀铜溶液中的有机杂质进行有效处理,才能生产出合格的铜包钢产品。
一、有机杂质产生的主要原因有:⑴添加剂的分解产物,这是镀液中产生有机杂质的重要途径之一。
镀液使用时间太长,没有及时进行处理,这样添加剂的分解产物越积越多,达到一定的量后,对镀液产生破坏性的影响。
⑵原材料不纯,或是没有把有机杂质处理干净就配成镀液,直接把有机杂质带入镀槽。
⑶上道工序中的有机杂质没有清洗彻底,或由清洗水中的有机杂质带入到镀液中。
⑷镀液温度过高(超过工艺规范规定的温度),这样加速添加剂的分解。
⑸大剂量添加硫酸(一次性添加达10升)时,集中在镀槽一个固定位置,这样也会造成镀液局部温度升高,分解添加剂。
二、有机杂质在酸性镀铜液中存在的现象:镀液的颜色。
正常镀液在常温下是蓝色清澈的,而有机物存时,溶液则是混浊湿绿。
镀液湿绿是有机杂质在镀液中的存在重要症状:轻度污染时,镀液呈蓝绿色,污染严重时,镀液呈绿色,且这时表明镀液中有相当高含量的有机物,必须加以处理,使之从镀液中清除。
三、有机杂质对镀铜层造成的具体不良反应有:⑴镀铜层表面光亮差;⑵降低酸性镀铜层与预镀铜层间的结合力;⑶正常电流状态下,电镀铜层容易被烧焦。
四、有机杂质的处理方法:镀铜溶液中的有机杂质处理常用氧化—还原法、活性碳吸附法两方法的联合运用。
一般首先使用氧化—还原法,将镀液中的有机物氧化分解掉,再用活性碳吸附、沉淀、过滤除去。
酸性镀铜溶液化分析方法
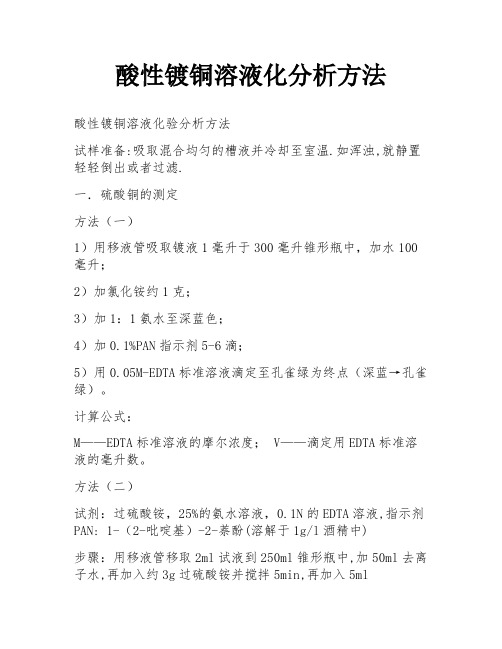
酸性镀铜溶液化分析方法酸性镀铜溶液化验分析方法试样准备:吸取混合均匀的槽液并冷却至室温.如浑浊,就静置轻轻倒出或者过滤.一.硫酸铜的测定方法(一)1)用移液管吸取镀液1毫升于300毫升锥形瓶中,加水100毫升;2)加氯化铵约1克;3)加1:1氨水至深蓝色;4)加0.1%PAN指示剂5-6滴;5)用0.05M-EDTA标准溶液滴定至孔雀绿为终点(深蓝→孔雀绿)。
计算公式:M——EDTA标准溶液的摩尔浓度; V——滴定用EDTA标准溶液的毫升数。
方法(二)试剂:过硫酸铵,25%的氨水溶液,0.1N的EDTA溶液,指示剂PAN: 1-(2-吡啶基)-2-萘酚(溶解于1g/l酒精中)步骤:用移液管移取2ml试液到250ml锥形瓶中,加50ml去离子水,再加入约3g过硫酸铵并搅拌5min,再加入5ml氨水和7滴指示剂,用 EDTA溶液滴定,颜色滴定到灰绿色为终点.计算:消耗的EDTA的毫升数×3.18=g/l铜注意:每提高2.5g/l Cu含量,须加入10g/l CuSO45H20方法(三)1) 用移液管取样本2毫升。
2) 加100毫升纯水。
3) 加热至40-50℃。
4) 加10毫升 1:1氨水(NH4OH)溶液。
5) 加5滴PAN指示剂。
6) 用0.1N EDTA标准液滴定由深蓝色变绿色为终点。
硫酸铜 (g/L) =所用0.1N EDTA之毫升数 x 12.49于分析期间,若发现有大量棕色沉淀物产生,请采用以下分析方法:1) 用移液管取样本2毫升。
2) 加100毫升纯水。
3) 加入2克氯化铵 ( NH4Cl )。
4) 加入10毫升氨缓冲液,并加热至50℃。
5) 静置一会,此时瓶中液体会分为两层:上层为深紫蓝色,下层为棕色沉淀物。
6) 将液体过滤,用纯水冲洗滤纸三次,然后将已过滤之液体倒入三角锥瓶中。
7) 加热至50–60℃。
8) 加入5滴PAN指示剂。
9) 用 0.1 N EDTA标准液滴定由深蓝色变绿色为终点。
TSV制程中控制深孔镀铜液中防腐剂的添加量

TSV制程中控制深孔镀铜液中防腐剂的添加量在TSV(Through-Silicon Via)制程中,控制深孔镀铜液中防腐剂的添加量是非常重要的。
深孔镀铜液是一种用于在芯片背面创建导电路径的化学溶液,而防腐剂则是为了防止深孔镀铜液在使用过程中受到污染和腐蚀。
在TSV制程中,深孔镀铜液中的防腐剂的添加量需要精确控制,以确保镀铜过程的稳定性和可靠性。
如果添加的防腐剂过少,可能导致深孔镀铜液容易受到氧化和污染,从而影响到镀铜膜的质量和厚度。
另一方面,如果添加的防腐剂过多,可能会引起深孔镀铜液的粘度增加,导致流动性变差,从而影响到镀铜的均匀性和一致性。
因此,在TSV制程中,控制深孔镀铜液中防腐剂的添加量是需要经过严格的实验和控制的。
首先,需要通过实验确定最佳的防腐剂添加量范围。
这可以通过在深孔镀铜液中逐渐添加不同量的防腐剂,并测量其镀铜膜的质量和厚度来进行评估。
通过这些实验数据,可以确定出最佳的防腐剂添加量范围。
一旦确定了最佳的防腐剂添加量范围,就需要制定相应的控制措施。
首先,需要建立一套准确的检测方法和设备,以实时监测深孔镀铜液中的防腐剂浓度。
这可以通过使用光谱分析、电化学分析或其他相应的技术手段来实现。
通过实时监测,可以及时发现防腐剂浓度的变化,并及时采取补充或调整的措施,以确保防腐剂浓度始终在最佳范围之内。
其次,需要建立一套严格的质量控制流程。
这包括了深孔镀铜液的储存、搅拌和供应等环节。
在储存过程中,需要采取措施避免深孔镀铜液与空气接触,以减少防腐剂的挥发。
在搅拌过程中,需要保证搅拌的均匀性,以确保防腐剂能够充分混合。
在供应过程中,需要确保深孔镀铜液的供应稳定,以防止防腐剂浓度的波动。
另外,还需要定期进行深孔镀铜液的监测和分析。
这可以通过取样并进行实验室分析来实现。
通过这些分析数据,可以了解到深孔镀铜液中防腐剂的消耗和浓度的变化趋势,进而调整和优化防腐剂的添加量。
综上所述,在TSV制程中,控制深孔镀铜液中防腐剂的添加量是非常重要的。
- 1、下载文档前请自行甄别文档内容的完整性,平台不提供额外的编辑、内容补充、找答案等附加服务。
- 2、"仅部分预览"的文档,不可在线预览部分如存在完整性等问题,可反馈申请退款(可完整预览的文档不适用该条件!)。
- 3、如文档侵犯您的权益,请联系客服反馈,我们会尽快为您处理(人工客服工作时间:9:00-18:30)。
酸性镀铜液中抑制添加剂的测定
摘要:本文建立了用离子色谱分离,蒸发光散射检测酸性镀铜液中Enthone和Shipley抑制剂的方法。
关键词:酸性;镀铜液;Enthone;Shipley;抑制剂
电镀铜系统是将铜沉积在半导体晶片上[1],[2]。
酸性镀铜液的主要成分是硫酸铜、硫磺酸和盐酸。
所有的抑制添加剂都会影响铜的沉积质量。
循环伏安溶出法(CVS)广泛用于测定添加剂和副产物对电镀质量产生的结合作用[3]~[6]。
然而,CVS不能检测单独的化合物、副产物以及没有电化学活性的化合物。
离子色谱已经成功的应用于酸性镀铜槽液中的Cl-[7]和所有的催化剂[8]。
因为保持抑制剂在规定范围内可以保证镀铜的质量,需要建立了一种测定抑制添加剂的方法。
该方法用IonPac NS1柱分离,以蒸发光散射检测器测定了酸性镀铜液中两种不同的抑制剂。
1 实验部分
1.1 仪器及试剂
Dionex DX-600离子色谱系统:GP50梯度泵;AS50自动进样器;Polymer Labs PL-ELS 1000蒸发光散射检测器(ELSD);UCI-100通用色谱界面;PeakNet色谱工作站;柱子:IonPac NS1分析柱(4×250 mm);100μLPEEK材料的样品定量环;去离子水(DI H2O),18.2M Ω-cm或更好的高纯水;乙腈,色谱纯(Burdick 和Jackson 或相当的)
1.2 样品的处理
将硫酸铜、硫酸和盐酸三种溶液混合后得到酸性镀铜液。
按厂商规定的浓度将抑制剂添加到制得的酸性镀铜液中。
1.3 色谱条件
乙腈/水,梯度分析,分析时间:15 min;流速:1.0 mL/min;ELSD蒸发温度:80 ℃;ELSD雾化温度:75 ℃;氮气流速:1.0L/min;进样量:100μL。
2 结果与讨论
2.1 仪器条件选择
酸性镀铜液中有机添加剂需用特殊的仪器进行测定。
抑制剂的测定会受到过量的硫酸和硫酸铜的干扰。
因为强酸性的电镀液样品(10%硫酸)会腐蚀不锈钢流路,所以酸性镀铜液的测定不适合用典型的液相色谱法。
因此流路为PEEK材料的离子色谱系统可以用在该项测定上。
这种惰性的聚合体不会被镀铜液腐蚀。
通常认为硅胶反相柱可以用作分离柱。
然而,硅胶柱不适合分析强酸性基体的样品。
相反,聚合物填料的反相色谱柱IonPac NS1在pH为0-14范围内都是比较稳定的,所以它更适合分析该样品。
选用优化的色谱条件来分离酸性镀铜液中两种不同的抑制剂,选用乙腈作梯度淋洗(40%-90%)。
因为抑制添加剂中没有强发色团不能用UV检测器检测,所以它的测定是一个很具挑战性的工作。
ELSD曾作为一种检测器被用于添加剂的测定[9]~[12]。
用ELSD检测时,目标物在柱子上进行分离,然后流出液通过一个喷雾器。
流动相蒸发并且形成一缕不易挥发的溶质颗粒。
一束光照向这些待分析的颗粒然后检测其散射光。
分析物的响应值和浓度成一定比例。
2.2 线性分析
用ELDS检测前,首先用IonPac NS1-10μm聚合物反相柱将抑制剂和其它化合物分离。
图1是含有5 mL/L Enthone抑制剂的电镀槽液的色谱分离图。
该抑制剂保留时间为6min,而基体的保留时间为2 min,所以它们实现了很好的分离。
在铜电镀液中Enthone抑制剂起作用的浓度范围为4-12 mL/L。
在三个数量级的范围内具有线性,相关系数r2为0.9993。
用该方法也可以测定Shipley抑制剂(如图2所示)。
该抑制剂的保留时间为9 min,也能和基体实现很好的分离。
在铜电镀液中S-2001 Shipley抑制剂起作用的浓度范围为20-25 mL/L。
在三个数量级的范围内具有线性,线性相关系数r2为0.9798。
图1. 电解前酸性镀铜液中Enthone抑制剂的测定
图2. 电解前酸性镀铜液中Shipley抑制剂的测定
3. 维护
每天分析完成后需要关上淋洗液泵、把ELSD检测器置于“standby”模式并且关闭电源。
每个月清洗一次蒸发器的管路可以有效的防止非挥发性物质的累积。
清洗检测器时需将蒸发器温度设定为150 ℃、喷雾器的温度设定为90 ℃、气体流速设为2 L/min。
用去离子水淋洗。
参考文献
[1] Hurtubise, R.; Too, E.; Cheng, C. C. Future Fab Intl.1998, 243–245.
[2] Lin, X. W.; Pramanik, D. Solid State Technol. 1998, 41(10), 63–79.
[3] Tench, D.; Ogden, C. J. Electrochem. Soc. 1978, 125, 194.
[4] Ogden, C.; Tench, D. Plat. and Surf. Fin. 1978, 66, 30.
[5] Haak, R.; Ogden. C.; Tench, D. Plat. and Surf. Fin. 1982, 69, 62.
[6] Freitag, W. O.; Ogden, C.; Tench, D.; White, J. Plat. and Surf. Fin. 1983, 70, 55.
[7] Dionex Corporation, Application Update 143; Sunnyvale, CA.
[8] Dionex Corporation, Application Note 139; Sunnyvale, CA.
[9] Operator’s Manual for the PL-ELS 1000 Evaporative Light Scattering Detector, Polymer Labs, Amherst, MA 1999.
[10] Guiochon, G.; Moysan, A.; Holley, C. J. Liq. Chromatogr. 1988, 11, 2547.
[11] Charlesworth, J.M. Anal. Chem. 1978, 50, 1414.
[12] MacRae, R.; Dick, J. J. Chromatogr. 1981, 210, 138.。