火车车轮锻造工艺分析(最新版)
火车车轮成形新工艺的开发研究
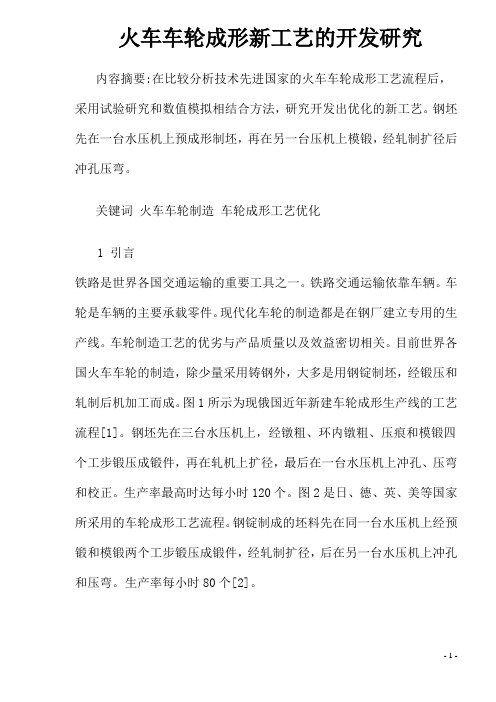
火车车轮成形新工艺的开发研究内容摘要:在比较分析技术先进国家的火车车轮成形工艺流程后,采用试验研究和数值模拟相结合方法,研究开发出优化的新工艺。
钢坯先在一台水压机上预成形制坯,再在另一台压机上模锻,经轧制扩径后冲孔压弯。
关键词火车车轮制造车轮成形工艺优化1 引言铁路是世界各国交通运输的重要工具之一。
铁路交通运输依靠车辆。
车轮是车辆的主要承载零件。
现代化车轮的制造都是在钢厂建立专用的生产线。
车轮制造工艺的优劣与产品质量以及效益密切相关。
目前世界各国火车车轮的制造,除少量采用铸钢外,大多是用钢锭制坯,经锻压和轧制后机加工而成。
图1所示为现俄国近年新建车轮成形生产线的工艺流程[1]。
钢坯先在三台水压机上,经镦粗、环内镦粗、压痕和模锻四个工步锻压成锻件,再在轧机上扩径,最后在一台水压机上冲孔、压弯和校正。
生产率最高时达每小时120个。
图2是日、德、英、美等国家所采用的车轮成形工艺流程。
钢锭制成的坯料先在同一台水压机上经预锻和模锻两个工步锻压成锻件,经轧制扩径,后在另一台水压机上冲孔和压弯。
生产率每小时80个[2]。
两种车轮成形工艺流程的后半部基本相同,不同的是前半部锻压部分。
前者钢坯经四个工步分别在三台水压机上完成,后者钢坯经两个工步在同一台水压机上完成。
前者生产率较高,但需要增加两台水压机并加大模锻水压机的吨位,设备投资和占地面积大。
后者锻压工步和水压机台数少,但生产率不高,也未充分发挥后续工序设备的效能。
我国现行火车车轮的生产线是60年代引进前苏联技术建造的。
钢锭折断下料的钢坯,经加热后先在一台30MN的水压机上用自由镦粗、环内镦粗和压痕三个工步制坯,再在80MN水压机上模锻成形,然后在轧机上轧制扩径,并在另一台30MN水压机上冲孔和压弯。
如图3所示,生产率每小时80个。
2 车轮成形新工艺的试验研究为了比较分析各种火车车轮的制造工艺,对车轮的锻压工艺流程进行了系统全面的试验研究,以求得优化的新工艺。
火车车轮成形新工艺的开发研究
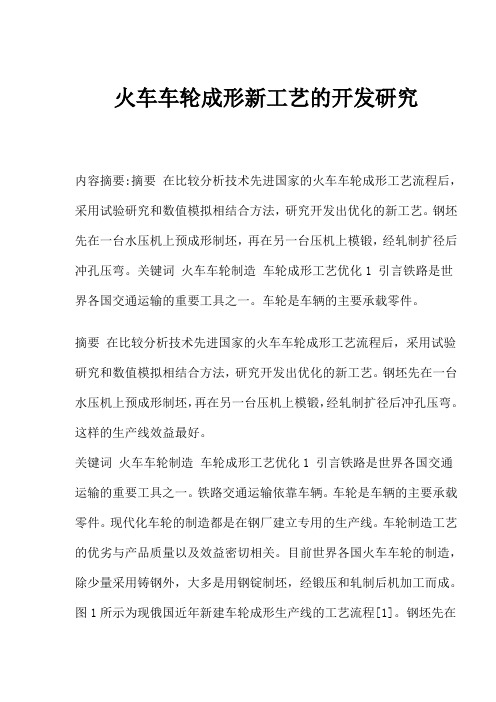
火车车轮成形新工艺的开发研究内容摘要:摘要在比较分析技术先进国家的火车车轮成形工艺流程后,采用试验研究和数值模拟相结合方法,研究开发出优化的新工艺。
钢坯先在一台水压机上预成形制坯,再在另一台压机上模锻,经轧制扩径后冲孔压弯。
关键词火车车轮制造车轮成形工艺优化1 引言铁路是世界各国交通运输的重要工具之一。
车轮是车辆的主要承载零件。
摘要在比较分析技术先进国家的火车车轮成形工艺流程后,采用试验研究和数值模拟相结合方法,研究开发出优化的新工艺。
钢坯先在一台水压机上预成形制坯,再在另一台压机上模锻,经轧制扩径后冲孔压弯。
这样的生产线效益最好。
关键词火车车轮制造车轮成形工艺优化1 引言铁路是世界各国交通运输的重要工具之一。
铁路交通运输依靠车辆。
车轮是车辆的主要承载零件。
现代化车轮的制造都是在钢厂建立专用的生产线。
车轮制造工艺的优劣与产品质量以及效益密切相关。
目前世界各国火车车轮的制造,除少量采用铸钢外,大多是用钢锭制坯,经锻压和轧制后机加工而成。
图1所示为现俄国近年新建车轮成形生产线的工艺流程[1]。
钢坯先在三台水压机上,经镦粗、环内镦粗、压痕和模锻四个工步锻压成锻件,再在轧机上扩径,最后在一台水压机上冲孔、压弯和校正。
生产率最高时达每小时120个。
图2是日、德、英、美等国家所采用的车轮成形工艺流程。
钢锭制成的坯料先在同一台水压机上经预锻和模锻两个工步锻压成锻件,经轧制扩径,后在另一台水压机上冲孔和压弯。
生产率每小时80个[2]。
两种车轮成形工艺流程的后半部基本相同,不同的是前半部锻压部分。
前者钢坯经四个工步分别在三台水压机上完成,后者钢坯经两个工步在同一台水压机上完成。
前者生产率较高,但需要增加两台水压机并加大模锻水压机的吨位,设备投资和占地面积大。
后者锻压工步和水压机台数少,但生产率不高,也未充分发挥后续工序设备的效能。
我国现行火车车轮的生产线是60年代引进前苏联技术建造的。
钢锭折断下料的钢坯,经加热后先在一台30MN的水压机上用自由镦粗、环内镦粗和压痕三个工步制坯,再在80MN水压机上模锻成形,然后在轧机上轧制扩径,并在另一台30MN水压机上冲孔和压弯。
车轮锻造技术要求
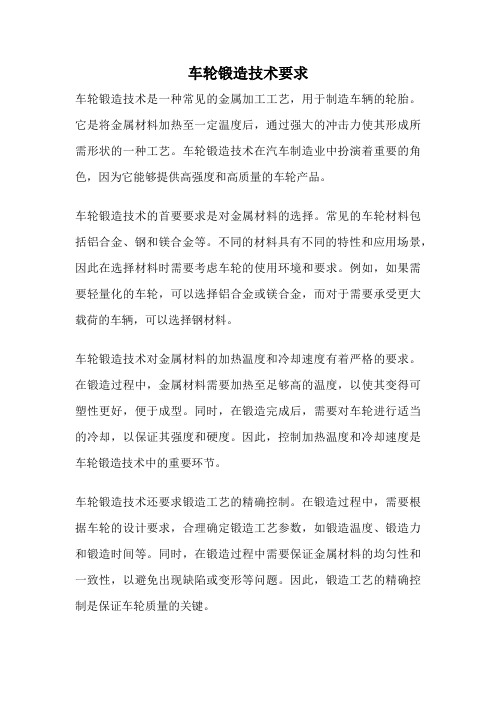
车轮锻造技术要求车轮锻造技术是一种常见的金属加工工艺,用于制造车辆的轮胎。
它是将金属材料加热至一定温度后,通过强大的冲击力使其形成所需形状的一种工艺。
车轮锻造技术在汽车制造业中扮演着重要的角色,因为它能够提供高强度和高质量的车轮产品。
车轮锻造技术的首要要求是对金属材料的选择。
常见的车轮材料包括铝合金、钢和镁合金等。
不同的材料具有不同的特性和应用场景,因此在选择材料时需要考虑车轮的使用环境和要求。
例如,如果需要轻量化的车轮,可以选择铝合金或镁合金,而对于需要承受更大载荷的车辆,可以选择钢材料。
车轮锻造技术对金属材料的加热温度和冷却速度有着严格的要求。
在锻造过程中,金属材料需要加热至足够高的温度,以使其变得可塑性更好,便于成型。
同时,在锻造完成后,需要对车轮进行适当的冷却,以保证其强度和硬度。
因此,控制加热温度和冷却速度是车轮锻造技术中的重要环节。
车轮锻造技术还要求锻造工艺的精确控制。
在锻造过程中,需要根据车轮的设计要求,合理确定锻造工艺参数,如锻造温度、锻造力和锻造时间等。
同时,在锻造过程中需要保证金属材料的均匀性和一致性,以避免出现缺陷或变形等问题。
因此,锻造工艺的精确控制是保证车轮质量的关键。
车轮锻造技术还要求设备和工具的高质量和精确性。
锻造设备需要具备足够的力量和稳定性,以产生足够的冲击力来完成锻造过程。
同时,锻造模具和工具需要具备高度精确性,以确保车轮的尺寸和形状的准确性。
因此,高质量和精确性的设备和工具是保证车轮锻造质量的基础。
车轮锻造技术还要求对成品车轮进行适当的热处理和表面处理。
热处理可以提高车轮的强度和硬度,增加其使用寿命。
表面处理可以提高车轮的耐腐蚀性和美观度,同时也可以提高车轮与轮胎之间的粘附力。
因此,热处理和表面处理是车轮锻造技术中不可忽视的环节。
车轮锻造技术是一种重要的金属加工工艺,具有高强度和高质量的特点。
它要求对金属材料的选择、加热和冷却控制、锻造工艺的精确控制、设备和工具的高质量和精确性,以及适当的热处理和表面处理。
火车车轮生产工艺

火车车轮生产工艺火车车轮生产工艺火车车轮作为火车重要零部件之一,在火车运行过程中承受着巨大的压力和摩擦力。
因此,火车车轮的质量和性能对火车的运行安全和效率起着至关重要的作用。
下面是火车车轮的生产工艺。
1. 材料选择:火车车轮一般采用耐磨铸铁或英国标准的耐磨铸钢制造。
这些材料具有良好的强度、韧性和磨损特性,能够承受高速列车长时间运行的要求。
2. 铸造工艺:火车车轮一般采用砂型铸造工艺。
首先,根据车轮的尺寸和重量,制作适当大小的砂型。
然后,在砂型中注入熔化的铸造材料,保持一定的浇注温度和时间,使得熔融金属填充整个砂模腔体。
待金属冷却后,砂型被敲击击碎,得到初步成型的车轮。
3. 精修工艺:初步成型的车轮还需要经过精修工艺才能符合要求。
首先,进行车轮的切割和修削,将车轮的外形和尺寸修整到标准要求。
然后,进行车轮的磨削和抛光,使其表面光滑,减小摩擦阻力。
最后,进行车轮的热处理,提高其硬度和强度,增加其使用寿命。
4. 车轮组装:经过精修工艺的车轮需要进行组装。
首先,将车轮与火车车轴连接,使用螺栓将车轮固定在车轴上。
然后,进行车轮的动平衡调整,使车轮在运行时不会产生过大的振动。
最后,进行车轮的润滑和防锈处理,以保护车轮不受到湿气和腐蚀的影响。
5. 检验和测试:制造完成的车轮需要经过严格的检验和测试才能出厂。
常见的检验项目包括外观检查、尺寸测量、硬度检测、磨损测试等。
只有通过各项检验项目的要求,车轮才能符合质量标准并投入使用。
总之,火车车轮的生产工艺包括材料选择、铸造工艺、精修工艺、车轮组装以及检验和测试等环节。
只有在每个工艺环节严格控制和质量检测的基础上,才能生产出质量优良、性能稳定的火车车轮,确保火车运行的安全和效率。
火车车轮锻造工艺分析(正式)
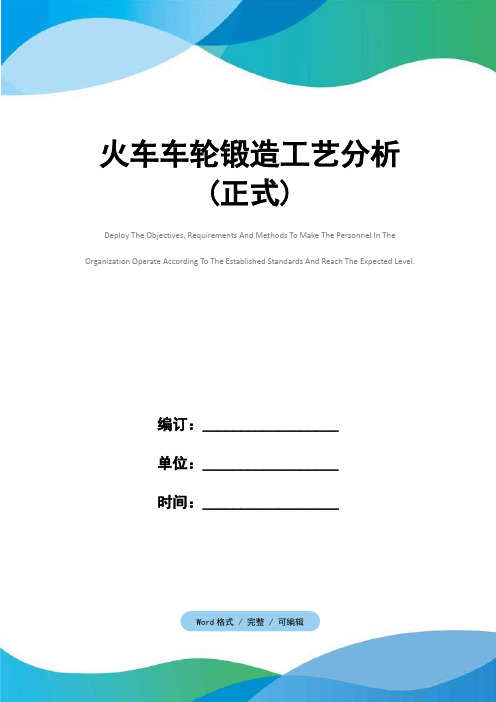
编订:__________________单位:__________________时间:__________________火车车轮锻造工艺分析(正式)Deploy The Objectives, Requirements And Methods To Make The Personnel In The Organization Operate According To The Established Standards And Reach The Expected Level.Word格式 / 完整 / 可编辑文件编号:KG-AO-4032-19 火车车轮锻造工艺分析(正式)使用备注:本文档可用在日常工作场景,通过对目的、要求、方式、方法、进度等进行具体、周密的部署,从而使得组织内人员按照既定标准、规范的要求进行操作,使日常工作或活动达到预期的水平。
下载后就可自由编辑。
铁路交通是我国运输系统的重要组成部分,在国民经济和社会发展过程中,铁路运输扮演着不可替代的重要角色。
我国一直以来都十分重视铁路运输的发展。
最近几年以来,随着以高铁为代表的新型铁路运输技术的应用,我国铁路运输朝着高速、重载方向发展,车轮在复杂的运行工况和恶劣的工作条件下,受到来自于速度效应和制动方式的双重影响,对其耐磨性、强韧性以及抗疲劳性提出了更高的要求。
但是我国现有的车轮锻压生产技术,还不能完全满足铁路运输发展对火车车轮质量的要求。
尤其是我国高速列车的车轮,在车轮的制造中,还存在废品率较高的现象。
因此,笔者认为,研究火车车轮锻压生产工艺,提高我国火车车轮锻压生产技术水平,制造优质火车车轮,对于降低我国火车整车生产成本,促进铁路运输的发展,有十分重要的现实意义。
1.火车车轮概述。
1.1.我国火车车轮形制特征简析火车车轮是火车整车零件中的一个关键组成部分,是火车机车生产中技术较高的环节之一。
由于火车的种类繁多,工作环境和机车构造也不尽相同,所以火车车轮的结构形式和形制特征也多种多样。
火车车轮锻造工艺分析
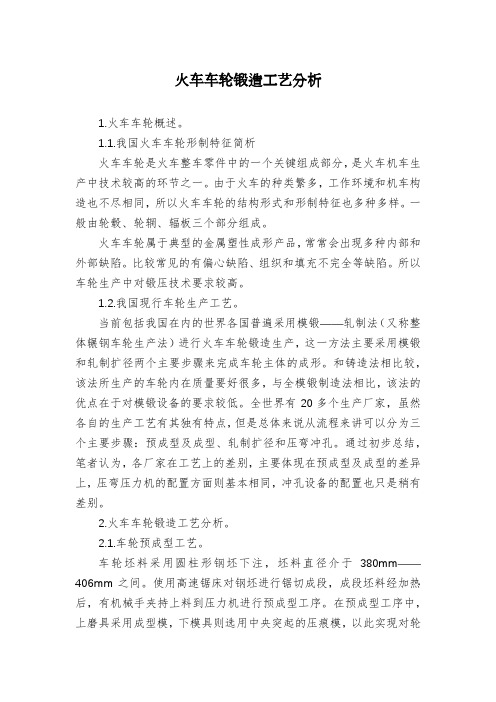
火车车轮锻造工艺分析1.火车车轮概述。
1.1.我国火车车轮形制特征简析火车车轮是火车整车零件中的一个关键组成部分,是火车机车生产中技术较高的环节之一。
由于火车的种类繁多,工作环境和机车构造也不尽相同,所以火车车轮的结构形式和形制特征也多种多样。
一般由轮毂、轮辋、辐板三个部分组成。
火车车轮属于典型的金属塑性成形产品,常常会出现多种内部和外部缺陷。
比较常见的有偏心缺陷、组织和填充不完全等缺陷。
所以车轮生产中对锻压技术要求较高。
1.2.我国现行车轮生产工艺。
当前包括我国在内的世界各国普遍采用模锻——轧制法(又称整体辗钢车轮生产法)进行火车车轮锻造生产,这一方法主要采用模锻和轧制扩径两个主要步骤来完成车轮主体的成形。
和铸造法相比较,该法所生产的车轮内在质量要好很多,与全模锻制造法相比,该法的优点在于对模锻设备的要求较低。
全世界有20多个生产厂家,虽然各自的生产工艺有其独有特点,但是总体来说从流程来讲可以分为三个主要步骤:预成型及成型、轧制扩径和压弯冲孔。
通过初步总结,笔者认为,各厂家在工艺上的差别,主要体现在预成型及成型的差异上,压弯压力机的配置方面则基本相同,冲孔设备的配置也只是稍有差别。
2.火车车轮锻造工艺分析。
2.1.车轮预成型工艺。
车轮坯料采用圆柱形钢坯下注,坯料直径介于380mm——406mm之间。
使用高速锯床对钢坯进行锯切成段,成段坯料经加热后,有机械手夹持上料到压力机进行预成型工序。
在预成型工序中,上磨具采用成型模,下模具则选用中央突起的压痕模,以此实现对轮辋、轮毂的金属体积分配。
在压力机模锻工序采用的是静压力锻造,整个锻造过程在一次行程中完成。
优异的车轮预成型工艺,不但能够保证车轮初步形状的成形,同时还可以起到改善车轮内部组织结构和金属流线的双重作用。
但是如果此阶段的工艺不合理,则会直接导致车轮偏心、填充不完全等缺陷。
给后续加工阶段操作带来困难,严重的还会直接导致车轮报废。
2.2.车轮成型工艺。
火车车轮锻造工艺分析正式样本
文件编号:TP-AR-L5280In Terms Of Organization Management, It Is Necessary To Form A Certain Guiding And Planning Executable Plan, So As To Help Decision-Makers To Carry Out Better Production And Management From Multiple Perspectives.(示范文本)编制:_______________审核:_______________单位:_______________火车车轮锻造工艺分析正式样本火车车轮锻造工艺分析正式样本使用注意:该解决方案资料可用在组织/机构/单位管理上,形成一定的具有指导性,规划性的可执行计划,从而实现多角度地帮助决策人员进行更好的生产与管理。
材料内容可根据实际情况作相应修改,请在使用时认真阅读。
铁路交通是我国运输系统的重要组成部分,在国民经济和社会发展过程中,铁路运输扮演着不可替代的重要角色。
我国一直以来都十分重视铁路运输的发展。
最近几年以来,随着以高铁为代表的新型铁路运输技术的应用,我国铁路运输朝着高速、重载方向发展,车轮在复杂的运行工况和恶劣的工作条件下,受到来自于速度效应和制动方式的双重影响,对其耐磨性、强韧性以及抗疲劳性提出了更高的要求。
但是我国现有的车轮锻压生产技术,还不能完全满足铁路运输发展对火车车轮质量的要求。
尤其是我国高速列车的车轮,在车轮的制造中,还存在废品率较高的现象。
因此,笔者认为,研究火车车轮锻压生产工艺,提高我国火车车轮锻压生产技术水平,制造优质火车车轮,对于降低我国火车整车生产成本,促进铁路运输的发展,有十分重要的现实意义。
1.火车车轮概述。
1.1.我国火车车轮形制特征简析火车车轮是火车整车零件中的一个关键组成部分,是火车机车生产中技术较高的环节之一。
铁路机车车轮毂孔精加工工艺分析及优化
铁路机车车轮毂孔精加工工艺分析及优化铁路是维持国家经济运行的交通命脉,机车车轮是保证列车高速运行的关键部件,也是制造难度最高的工业产品之一。
车轮的运行条件对其强韧性、耐磨性等提出了更高的要求,因此研究车轮加工工艺,提升车轮综合质量,是实现铁路运输提速的有力保证。
标签:机车车轮;加工工艺;优化设计1 概述目前机车车轮大部分采用整轧车轮。
车轮材料属难加工材料,文章主要针对我厂涉及较多的材质为CL60的车轮精加工工艺进行分析及优化设计。
2 车轮加工工艺分析及工艺设计2.1 车轮材料特性常用车轮材料CL60是制造铁路车轮的专业用钢,其含碳量介于中碳钢和高碳钢之间,并含有硅锰等多种合金元素,化学成分见表1。
CL60属于较难切削材料,主要体现在以下几点:(1)材料导热性差,导致切削区域温度高,加快刀具磨损。
(2)刀刃与切屑接触长度短。
(3)单位切削力大。
(4)断屑困难。
2.2 车轮制造过程车轮制造过程为炼钢、下料、钢坯加热、车轮轧制、热处理、机加工、探伤、喷丸强化。
我厂所购车轮为经热处理、半精加工及探伤检验的半成品,到厂后根据轮轴组装过盈量要求精加工毂孔及注油孔。
2.3 车轮毂孔精加工工艺分析及工艺设计工艺设计通常包括分析产品图纸及相关标准,确定加工余量拟定工艺路线,确定设备、刀、夹、量具及辅助工具,确定切削用量,编写工艺文件等。
文章以图1所示图样为例进行加工工艺分析及工艺设计。
车轮到厂状态应满足毂孔及轮辋内侧面半精加工,毂孔尺寸Φ225mm,其余各部精加工。
工序安排为:(1)对车轮辐板磁粉探伤。
(2)钻注油孔。
(3)精加工毂孔、端面及油槽。
(4)对毂孔内表面超声波探伤。
(5)检验。
2.3.1 油路孔及螺纹孔的加工此工序的加工难点在于确定加工油路孔时刀具的入刀点位置,即毂孔表面沿轮毂端面与注油孔相交点的位置尺寸。
此工序可在摇臂钻床利用加工57°注油孔专用胎具来完成。
轮辋内侧面为半精加工状态,可作为定位基准并保证车轮与胎具紧贴、无间隙、稳固。
火车车轮加工工艺分析
总结
1.通过网上查阅资料可知火车车轮的主要技术要求 和制造工艺。
2.通过查阅有关资料绘制出火车车轮零件图和夹具 简图。
3.通过对火车车轮的机械加工工艺分析,以及资料 、视频的汇总,组员之间的探讨,PPT的制作,图 纸的绘制,使我们分析问题、资料查阅和处理问题 的能力得到提升,团队意识也得到增强。
火车车轮加工工艺分析
车轮的构成
1.突出的圆弧部分称为轮缘,它是保持车辆沿钢轨运行,防止脱轨的重 要部分。
2.车轮与钢轨的接触面称为踏面。
3.轮辋是车轮踏面下最外的一圈。
4.辐板是联接轮辋(和轮毂的部分。
5.轮毂是车轮与车轴互相配合的部分。
加工工艺流程
• 备料:锻造毛胚 • 调制:整体调质。 • 粗车:以内孔为基准,粗车外圆。 • 镗孔:以外圆为基准,粗镗内孔。 • 粗车:对车轮其他表面进行粗车。 • 半精车: 以内孔作为基准,半精车外圆。 • 半精镗孔:以外圆作为基准,半精镗内孔。 • 半精车:对车轮其它表面进行半精车,达到精度要求。 • 精车:以内孔为基准,精车外圆,达到精度要求。 • 精镗孔:以外圆作为基准,精镗内孔,达到精度要求。
• 2.垂直刀架,液压系统备有保压装置。 • 3.横梁夹紧机构采用弹簧夹紧,液压松开。 • 4.备有数显装置 。 • 5.主变速箱及工作台主轴支撑及传动自动润滑。 • 6.主传动皮带拉力、主轴轴承间隙、垂直滑枕螺母间隙及
横梁夹紧力均可调。
• 7.进给机构有保险装置。 • 8.CJ5710定梁立车其横梁固定无行程,不带计基准重合。 2.尽可能使各加工面采用同一定位基准。 3.选择的定位基准必须使工件定位夹紧方便。 4.对精度要求高或余量大的工件精加工时应重 新 找正,适当减小夹紧力。 5.避免切削温度引起的加工误差。 6.保持加工各圆面与内孔同轴。 7.保证内孔中心线与定位表面垂直。
锻造车轮生产工艺
锻造车轮生产工艺
锻造车轮是指利用金属材料进行锻造加工,生产出用于汽车、火车、重型机械等交通工具的车辆轮胎的一种生产工艺。
下面将以锻造一款汽车轮胎为例,介绍其生产工艺。
首先,需要准备锻造车轮的原材料。
一般来说,锻造车轮主要采用铸锻材料,如碳素钢或合金钢。
原材料需要经过铸造、浇注,并进行均热处理,以提高材料的塑性和韧性。
接下来,将经过均热处理的原材料送入锻压机进行锻造。
锻造车轮的形状通常是平面或轮缘。
锻造过程中,原材料需要经过多道模具的挤压和拉伸,使其逐渐变形为车轮的形状。
在锻造过程中,为了保证车轮的质量和强度,需要控制锻造温度、锻造过程中的应力分布和加工工艺参数。
通常,锻造温度约为材料的再结晶温度的0.6-0.7倍,以保证材料处于塑性状态。
同时,为了避免冷断,锻造过程中需要实施适当的凸模支撑和冷却措施。
在锻造完成后,车轮需要进行热处理,以增强其材料的硬度和强度。
常见的热处理方法包括正火、淬火和回火等。
热处理过程中,需要严格控制温度和保持时间,以提高车轮的耐久性和承载能力。
最后,车轮还需要进行表面处理。
一般来说,车轮表面需要经过除锈、喷砂、喷漆等工艺,以防止锈蚀和提高外观。
综上所述,锻造车轮的生产工艺包括准备原材料、锻造、热处理和表面处理等步骤。
通过严格控制每个步骤的工艺参数和质量要求,可以生产出质量优良、性能稳定的车轮产品,满足不同车辆使用的需求。
同时,随着技术的不断进步,锻造车轮生产工艺也在不断改进和优化,以提高生产效率和节约能源。
- 1、下载文档前请自行甄别文档内容的完整性,平台不提供额外的编辑、内容补充、找答案等附加服务。
- 2、"仅部分预览"的文档,不可在线预览部分如存在完整性等问题,可反馈申请退款(可完整预览的文档不适用该条件!)。
- 3、如文档侵犯您的权益,请联系客服反馈,我们会尽快为您处理(人工客服工作时间:9:00-18:30)。
( 安全管理 )
单位:_________________________
姓名:_________________________
日期:_________________________
精品文档 / Word文档 / 文字可改
火车车轮锻造工艺分析(最新
版)
Safety management is an important part of production management. Safety and production are in
the implementation process
火车车轮锻造工艺分析(最新版)
铁路交通是我国运输系统的重要组成部分,在国民经济和社会发展过程中,铁路运输扮演着不可替代的重要角色。
我国一直以来都十分重视铁路运输的发展。
最近几年以来,随着以高铁为代表的新型铁路运输技术的应用,我国铁路运输朝着高速、重载方向发展,车轮在复杂的运行工况和恶劣的工作条件下,受到来自于速度效应和制动方式的双重影响,对其耐磨性、强韧性以及抗疲劳性提出了更高的要求。
但是我国现有的车轮锻压生产技术,还不能完全满足铁路运输发展对火车车轮质量的要求。
尤其是我国高速列车的车轮,在车轮的制造中,还存在废品率较高的现象。
因此,笔者认为,研究火车车轮锻压生产工艺,提高我国火车车轮锻压生产技术水平,制造优质火车车轮,对于降低我国火车整车生产成本,促进铁路运输的发展,有十分重要的现实意义。
1.火车车轮概述。
1.1.我国火车车轮形制特征简析
火车车轮是火车整车零件中的一个关键组成部分,是火车机车生产中技术较高的环节之一。
由于火车的种类繁多,工作环境和机车构造也不尽相同,所以火车车轮的结构形式和形制特征也多种多样。
一般由轮毂、轮辋、辐板三个部分组成。
火车车轮属于典型的金属塑性成形产品,常常会出现多种内部和外部缺陷。
比较常见的有偏心缺陷、组织和填充不完全等缺陷。
所以车轮生产中对锻压技术要求较高。
1.2.我国现行车轮生产工艺。
当前包括我国在内的世界各国普遍采用模锻——轧制法(又称整体辗钢车轮生产法)进行火车车轮锻造生产,这一方法主要采用模锻和轧制扩径两个主要步骤来完成车轮主体的成形。
和铸造法相比较,该法所生产的车轮内在质量要好很多,与全模锻制造法相比,该法的优点在于对模锻设备的要求较低。
全世界有20多个生产厂家,虽然各自的生产工艺有其独有特点,但是总体来说从流程来讲可以分为三个主要步骤:预成型及成型、轧制扩径和压弯冲孔。
通过初
步总结,笔者认为,各厂家在工艺上的差别,主要体现在预成型及成型的差异上,压弯压力机的配置方面则基本相同,冲孔设备的配置也只是稍有差别。
2.火车车轮锻造工艺分析。
2.1.车轮预成型工艺。
车轮坯料采用圆柱形钢坯下注,坯料直径介于380mm——406mm 之间。
使用高速锯床对钢坯进行锯切成段,成段坯料经加热后,有机械手夹持上料到压力机进行预成型工序。
在预成型工序中,上磨具采用成型模,下模具则选用中央突起的压痕模,以此实现对轮辋、轮毂的金属体积分配。
在压力机模锻工序采用的是静压力锻造,整个锻造过程在一次行程中完成。
优异的车轮预成型工艺,不但能够保证车轮初步形状的成形,同时还可以起到改善车轮内部组织结构和金属流线的双重作用。
但是如果此阶段的工艺不合理,则会直接导致车轮偏心、填充不完全等缺陷。
给后续加工阶段操作带来困难,严重的还会直接导致车轮报废。
2.2.车轮成型工艺。
在车轮的成型阶段,主要得到的是轮毂和压制辐板的形状,同时完成轮辋主要部位的成形。
其过程属于典型的开式无飞边模锻。
模具压下后,首先受压的是车轮的辐板处,车轮内层金属受到来自中央冲头的作用力,带动外侧金属沿水平方向流动。
随着下压量的急剧增大,轮坯的最外侧金属和成形模的内壁接触。
在中央冲头和成形模内壁的共同作用下,轮坯内的金属形成一个分流面,分别流向轮毂和轮辋下侧以及轮辋上侧。
在该流程中,轮辋下侧的填充情况最佳。
此外,由于该工序中模具模膛的高度有所不同,所以直接导致轮坯中不同部分的金属变形量不一样,其中辐板处变形量最为突出,而轮辋部分的变形量则最小。
车轮成形工艺是热成形机组轧压能力匹配的关键工艺。
合理科学的成形工艺,不仅要保证压力机的压力极限数值满足事先设定的工艺数值,同时还要满足下道工序中轧机的轧制能力需求。
2.3.车轮压弯工艺。
车轮压弯工序一般情况下是和冲孔工序一起在同一台压力机上进行,是火车车轮热成形中的最后一道工序。
其主要目的是对辐板
进行压弯成形、对轮辋表面进行平整以及确定车轮两侧和车轮内径等的成形。
2.4.轮坯各个部位加工余量的确定。
车轮加工中的锻造余量,是整个车轮锻造工艺设计中非常重要的环节。
它与车轮材料的利用率、成品率以及生产率密切相关,直接决定着车轮生产的成本。
因此,要合理确定轮坯合理的锻造余量。
踏面余量的确定。
在确定轮坯踏面余量时,轮坯的椭圆度和热处理过程中直径0.1—0.2%的变化量应该予以充分考虑。
但是,主要还是要注意踏面上表面氧化皮压入、裂纹以及结疤等的消除。
经过实践中的反复摸索,笔者认为,踏面锻造余量的确定取8mm较为合适。
轮毂外径余量确定。
轮毂外径余量的确定,主要取决于设备对轮毂、轮辋偏心的精度控制。
目前,山西某重型机械集团公司在这一精度控制上可以达到6mm以内。
为了确保最大偏心后,轮毂能有3mm的加工余量,初期生产中,应该把轮毂余量确定为9mm。
实践证明,在设备正常情况下的批量生产中,轮毂外径余量取7mm比较适
宜。
轮毂、轮辋端面的余量确定。
这两项余量的确定主要取决于端面氧化皮压入、端面的不平整状况以及预成形时轮毂端面尖角部位填充不完全所造成的轮毂端部圆角三个因素。
在模具首次设计中,这一余量一般取7mm和6mm。
为了降低成本,曾经试图降低这两种余量,结果造成轮毂端面尖角部位加工不起来。
所以,最终仍然将轮毂、轮辋的单边余量设定至7mm和6mm的初期水平。
辐板和轮辋内径加工余量的确定。
由于在淬火和冷却处理过程中辐板会出现变形,因此辐板加工余量的确定,不仅要考虑氧化皮压入、表面裂纹等缺陷的去除,还要格外重视辐板变形的影响。
经生产企业长期批量生产经验的积累,辐板单边余量确定为6mm最为适合。
轮辋内径也取相同尺寸为宜。
淬火下沉量的确定。
车轮淬火后,轮辋的增大量叫做淬火下沉量。
压弯模设计时,应该确保车轮压弯成形以后,毂辋距减小一个淬火下沉量,以确保淬火后的毂辋距符合要求尺寸。
淬火下沉量的确定,和火车轮的型号有关。
据苏联资料介绍,915车轮淬火下沉量
为3—5mm。
安徽某钢厂在915车轮模具设计时,淬火下沉量取6mm。
2.5.车轮锻造过程中的数值模拟分析。
由于火车车轮的锻造工序繁多,各环节中对轮坯不同部分的数据误差要求较高,且由于涉及到材料金属物理化学性质的变更,因此对锻造过程中的数据控制和数值模拟要求较高,所以对于锻造工作的每个环节而言,建立数值模拟分析是十分必要的。
目前在数值分析方面,主要采取的是有限元数值分析法,这是一种将连续体根据实际需要,分化为若干个大小有限的单元个体集合,以方便分析连续体力学问题相关数据的方法。
这一方法应用在车轮锻造生产过程中,可以精确求解轮坯变形时内部速度场、应力场以及应变场等的变量,从而为车轮锻造各道工序,提供了科学的理论依据。
在目前我国火车车轮生产中,基于有限元理论和相关软件支持,已经普遍建立起了火车轮预成形和成形工步数值模拟分析模型、压弯过程数值模拟分析模型、冲孔过程数值模拟分析模型等一系列环节的模拟分析模型。
使得工作人员能够及时掌握各阶段数值的变化,以及由此带来的对成品质量的影响,实时调整参数设置,
确保车轮最终质量得以实现。
2.6.当前火车车轮锻造工艺存在的问题。
随着对火车车轮数量要求的增加和质量要求的提高,我国火车车轮锻造工艺的缺陷也显露出来。
目前主要问题在于各工步,尤其是在车轮预成形和压弯工步,对金属变形量的分配以及模具结构和尺寸的设计等诸多问题,有待进一步研究和改进。
这些问题的存在不仅使得车轮锻造工序和模具设计的周期更长、对模具和车轮的调试以及模具维修的过程趋于复杂,而且还会导致车轮辐板出现裂纹、车轮成形形状和尺寸满足不了设计要求等一系列质量问题,使得当前的火车车轮生产,从数量到质量都与实际需要存在相当差距。
火车车轮的锻造,是一个从材料选择、模具设计制造、到前期预成形、成形、再到后期压弯和冲孔的连续性工序系统。
由于金属在各工艺阶段会发生相应的物理和化学变化,因此常常会出现诸如填充不充分和偏心等缺陷,导致产品质量不能达到预期要求,严重者产生废品。
从加工流程优化、数值模拟分析等方面加以完善,是弥补当前车轮锻造工艺相关环节缺陷,保证车轮最终质量的有效途
径。
以有限元理论为基础的数值模拟分析模型,是目前实现锻造过程数值模拟分析的可靠途径,是实现对锻造过程中相关数值精确控制的有效手段。
笔者认为,我国火车车轮锻造工艺的改进,除了要注重生产设备和新型工艺的开发外,对以有限元理论为依托的计算机软件辅助分析系统的开发运用也应该予以重视,将其纳入工艺改进的重要组成部分。
云博创意设计
MzYunBo Creative Design Co., Ltd.。