冲压件模具工艺性分析毕业论文
冲压模具毕业设计论文

冲压模具毕业设计1。
绪论1。
1冲压的概念、特点及应用冲压是利用安装在冲压设备(主要是压力机)上的模具对材料施加压力,使其产生分离或塑性变形,从而获得所需零件(俗称冲压或冲压件)的一种压力加工方法。
冲压通常是在常温下对材料进行冷变形加工,且主要采用板料来加工成所需零件,所以也叫冷冲压或板料冲压。
冲压是材料压力加工或塑性加工的主要方法之一,隶属于材料成型工程术。
冲压所使用的模具称为冲压模具,简称冲模.冲模是将材料(金属或非金属)批量加工成所需冲件的专用工具。
冲模在冲压中至关重要,没有符合要求的冲模,批量冲压生产就难以进行;没有先进的冲模,先进的冲压工艺就无法实现。
冲压工艺与模具、冲压设备和冲压材料构成冲压加工的三要素,只有它们相互结合才能得出冲压件。
与机械加工及塑性加工的其它方法相比,冲压加工无论在技术方面还是经济方面都具有许多独特的优点。
主要表现如下.(1) 冲压加工的生产效率高,且操作方便,易于实现机械化与自动化.这是因为冲压是依靠冲模和冲压设备来完成加工,普通压力机的行程次数为每分钟可达几十次,高速压力要每分钟可达数百次甚至千次以上,而且每次冲压行程就可能得到一个冲件。
(2)冲压时由于模具保证了冲压件的尺寸与形状精度,且一般不破坏冲压件的表面质量,而模具的寿命一般较长,所以冲压的质量稳定,互换性好,具有“一模一样”的特征。
(3)冲压可加工出尺寸范围较大、形状较复杂的零件,如小到钟表的秒表,大到汽车纵梁、覆盖件等,加上冲压时材料的冷变形硬化效应,冲压的强度和刚度均较高。
(4)冲压一般没有切屑碎料生成,材料的消耗较少,且不需其它加热设备,因而是一种省料,节能的加工方法,冲压件的成本较低。
但是,冲压加工所使用的模具一般具有专用性,有时一个复杂零件需要数套模具才能加工成形,且模具制造的精度高,技术要求高,是技术密集形产品。
所以,只有在冲压件生产批量较大的情况下,冲压加工的优点才能充分体现,从而获得较好的经济效益。
冲压工艺与模具设计毕业论文
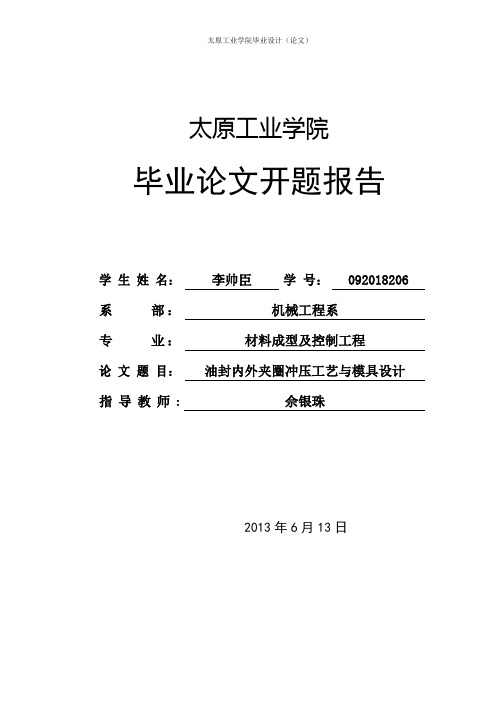
太原工业学院毕业设计(论文)太原工业学院毕业论文开题报告学生姓名:李帅臣学号:092018206系部:机械工程系专业:材料成型及控制工程论文题目:油封内外夹圈冲压工艺与模具设计指导教师:佘银珠2013年6月13日毕业论文开题报告一.论文研究目的及意义:本论文主要研究油封内外夹圈的冲压工艺与模具设计,对内夹圈和外夹圈分别做一些分析,然后来确定它们加工的工艺方法,从而再确定模具的设计。
通过对零件加工工艺的分析和生产模具的设计,要去掌握模具设计当中的一些分析方法。
冲压模具的设计主要包括工件的分析、工艺方案的确定、模具结构形式的选则、必要的工艺计算、主要零部件的设计、压力机型号的选择,以及零件图和装配图的绘制。
对每一步的分析,去深刻掌握和了解有关冲压模具设计的基础知识,同时开拓设计的思路,培养创新设计能力。
通过对零件结构的分析计算,来确定加工的工艺方法,从而去回顾并深入理解冲压工艺的分类以及每一种工艺的特点和其适合的范围,进一步总体上掌加工工艺类型。
通过工艺力的计算来选择模具的压力机型号,这样可以巩固曾经学到的知识,同时对内外夹圈的选择,可以做出比较,更深层次的学习实际生产当中的压力机选择的分析方法。
通过对零部件结构的设计,可以了解标准零部件的选择及其设计。
绘制零件图和装配图,加深对二维CAD软件的进一步掌握。
做这篇论文的研究,不仅有助于基础知识的巩固和学习,而且能够进一步开拓思维,深入学习模具设计的新思路。
对各种文献的阅读,增加了模具方面的专业知识,使零碎的知识更加专业化和整体化。
这篇论文的研究也为以后的工作和读研打下了基础。
参考文献:[1]郝滨海主编. 冲压模具简明设计手册[M]. 北京:化学工业出版社,2005、10-402[2]模具实用技术丛书编委会编. 冲模设计应用实例[M]. 北京:机械工业出版社,2000、 232-239[3]梁炳文主编. 冷冲压工艺手册[M]. 北京:北京航空航天大学出版社,2004、20-593[4]中国机械工程学会,中国模具设计大典编委会编著.中国模具设计大典第三卷[M]. 江西:江西科学技术出版社.2003.167-172[5]冲压工艺及模具设计编写委员会. 冲压工艺及模具设计[M]. 北京:国防工业出版社,1993、54-55[6]候义馨. 冲压工艺及模具设计[M]. 北京:兵器工业出版社,1994、 62-65[7]卢险峰. 冲压工艺模具学[M]. 北京:机械工业出版社,1999、 44-46[8]胡亚民. 材料成形技术基础[M]. 重庆:重庆大学出版社,2000、15-17二.本课题要研究或解决的问题和拟采用的研究手段(途径):本课题要研究解决油封内外夹圈冲压工艺以及其模具设计,这副冲压模具的设计主要包括工件的分析、工艺方案的确定、模具结构形式的选择、必要的工艺计算、主要零部件的设计、压力机型号的选择,以及零件图和装配图的绘制。
毕业论文(设计)托板的冲压工艺分析及模具设计

诚信声明本人郑重声明:本论文及其研究工作是本人在指导老师的指导下独立完成的。
在完成论文时所利用的一切资料均已在参考文献中列出。
本人签名:年月日托板的冲压工艺分析及模具设计摘要:本设计介绍了冲压级进模具的结构设计及其工作过程。
通过对冲裁图样零件工艺性的正确分析,设计了一套冲孔落料级进模。
通过冲裁力、卸料力等计算,确定模具结构。
本设计包括了模具成型零件凸模、凹模及其他零件,如卸料板、固定板、垫板、导柱、导套等的设计和选用过程,重要零件的工艺参数的选择与计算,冲裁机构与送料挡料以及其它结构的设计过程,并着重对模具的设计部分作了详细介绍。
该模具性能可靠,运行平稳,能提高产品质量和生产效率,降低劳动强度和生产成本。
关键词:冲孔,落料 ,级进模 ,模具结构Splint Analysis of Stamping Process and Design ofDie for Valve PlateAbstract:Compound progressive die structure design and working process was introduced. Through to technological correct analysis of the blanking patterns components, has designed a continual blanking punching die blanking .Die type was determined through the calculation of blanking force and ejecting force. This design introduced the mold formation components including the plunger, the lower die and other components like unload the yard lumber, the dead plate, the backing strip, the guide pillar, the guide busher and so on design and select the process, the technological parameter's choice and the computation of the important components, the blanking organization and the feeding keep off the material as well as other structure design process, and to has made the detailed introduction emphatically to mold's design parts.The die works stable so that the product quality and efficiency has been improved and working intensity and production cost has been reduced.Key words:piercing ,blanking , progressive die, die structure毕业设计任务书设计题目:托板的冲压工艺分析及模具设计系部:机械工程系专业:材料成型及控制工程学号:102018139学生:王志勇指导教师(含职称):原涛(讲师)专业负责人:赵跃文1.设计的主要任务及目标(1)通过毕业设计能够巩固所学的各类基础知识、初步掌握冲压模具设计的流程,熟练掌握使用各类工具书籍。
冲压模具毕业设计论文 (14)

目录摘要 (2)1 模具的介绍 (3)1.1冲压技术的进步 (3)1.2 模具的发展与现状 (3)2 冲压工艺方案的制定 (5)2.1 工艺分析 (5)2.2 排样图设计 (6)3 模具总体结构设计 (8)3.1 条料定位装置 (8)3.2 出料装置 (10)3.3 模具结构特点 (10)3.4 模具工作过程 (10)4 模具零件的设计与计算 (12)4.1 凸、凹模刃口尺寸的计算 (12)4.1.1 凸、凹模间隙的选择 (12)4.1.2 凸、凹模刃口尺寸计算 (12)4.2 凸、凹模的设计 (17)4.2.1 凸模的结构和固定形式 (17)4.2.2 凸模长度的确定 (18)4.2.3 凸模的强度计算 (18)4.2.4 凹模结构形式设计 (20)4.2.5 凹模结构尺寸的确定 (20)4.3 模板的设计 (22)4.4 卸料弹簧的选用 (22)4.5 其它零件的设计 (23)5 冲压设备的选用 (25)5.1 冲压力的计算 (25)5.2 选择压力机 (26)6 压力中心的计算 (27)6.1 计算步骤 (27)6.2 计算压力中心 (27)7 总结 (28)参考文献 (29)致谢 (30)摘要冲压成形作为现代工业中一种十分重要的加工方法,用以生产各种板料零件,具有很多独特的优势,其成形件具有自重轻、刚度大、强度高、互换性好、成本低、生产过程便于实现机械自动化及生产效率高等优点,是一种其它加工方法所不能相比和不可替代的先进制造技术,在制造业中具有很强的竞争力,被广泛应用于汽车、能源、机械、信息、航空航天、国防工业和日常生活的生产之中。
在吸收了力学、数学、金属材料学、机械科学以及控制、计算机技术等方面的知识后,已经形成了冲压学科的成形基本理论。
以冲压产品为龙头,以模具为中心,结合现代先进技术的应用,在产品的巨大市场需求刺激和推动下,冲压成形技术在国民经济发展、实现现代化和提高人民生活水平方面发挥着越来越重要的作用。
冲压模具毕业设计论文[2]
![冲压模具毕业设计论文[2]](https://img.taocdn.com/s3/m/9200aa4902d8ce2f0066f5335a8102d276a26185.png)
冲压模具毕业设计论文[2]1. 引言冲压模具是冲压工艺中不可或缺的关键组成部分。
它的优劣直接影响着冲压产品的质量和生产效率。
因此,在冲压模具的设计和制造上要注重各个方面的优化,以实现高效、高质量的冲压生产。
本文将探讨冲压模具在毕业设计中的应用,通过分析冲压模具的设计要点和制造过程,提出一种在制造过程中提高模具质量和降低成本的方法。
2. 冲压模具设计要点冲压模具的设计是一个综合性的工作,需要考虑多个方面的因素。
下面列举了冲压模具设计的要点:2.1 材料选择冲压模具需要具备高强度和耐磨损的特性。
因此,在材料选择上应当考虑使用高硬度材料,如合金工具钢。
同时,还要考虑材料的加工性能和耐热性能。
2.2 结构设计冲压模具的结构设计应当考虑到产品形状和尺寸的特点,并且要与冲压设备的工作方式相匹配。
在结构设计中,需要合理安排模具的凸模、凹模和导向系统,确保冲压过程中的定位和导向准确。
2.3 寿命设计冲压模具的寿命设计是一个重要的考虑因素。
寿命设计时要考虑冲压过程中的应力、变形和磨损等因素,以确保模具在长期使用中具有稳定的性能。
2.4 润滑设计冲压模具在工作过程中需要进行润滑,以降低摩擦和磨损。
因此,在模具设计中需要考虑润滑系统的设计,合理设置润滑通道和喷油装置。
3. 冲压模具制造过程冲压模具的制造过程可以分为以下几个步骤:3.1 制造工艺规划制造工艺规划是整个制造过程的基础。
在制造工艺规划中,需要确定模具的加工顺序、方法和工艺参数等,确保模具的加工精度和质量要求。
3.2 加工制造冲压模具的加工制造包括以下几个方面:材料切割、零件加工、工艺装配和热处理等。
其中,热处理是提高模具硬度和耐磨性的重要步骤。
3.3 调试与试模制造完成后,需要对模具进行调试和试模。
通过调试和试模可以发现和解决模具的问题,确保模具在使用时能够正常运行。
4. 优化冲压模具制造过程的方法为了提高冲压模具制造的效率和质量,可以采用以下方法进行优化:4.1 CAD/CAM技术应用CAD/CAM技术可以提高冲压模具的设计和制造效率。
冲压工艺与模具设计毕业论文
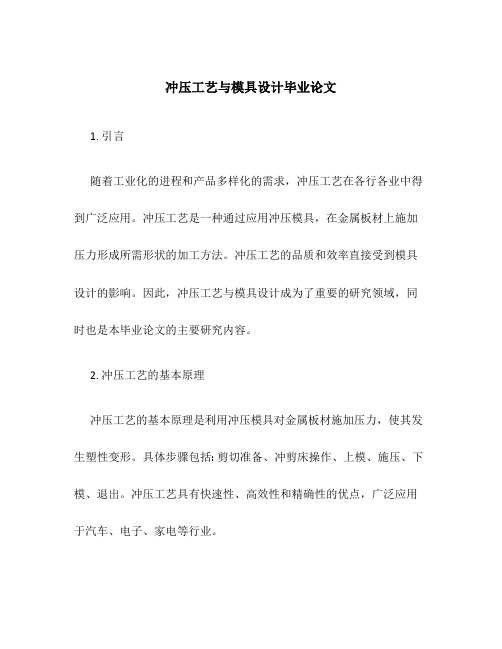
冲压工艺与模具设计毕业论文1. 引言随着工业化的进程和产品多样化的需求,冲压工艺在各行各业中得到广泛应用。
冲压工艺是一种通过应用冲压模具,在金属板材上施加压力形成所需形状的加工方法。
冲压工艺的品质和效率直接受到模具设计的影响。
因此,冲压工艺与模具设计成为了重要的研究领域,同时也是本毕业论文的主要研究内容。
2. 冲压工艺的基本原理冲压工艺的基本原理是利用冲压模具对金属板材施加压力,使其发生塑性变形。
具体步骤包括: 剪切准备、冲剪床操作、上模、施压、下模、退出。
冲压工艺具有快速性、高效性和精确性的优点,广泛应用于汽车、电子、家电等行业。
3. 冲压模具设计的基本原则冲压模具设计应遵循以下基本原则:3.1 模具结构设计原则模具设计应考虑到材料的特性、制作工艺和模具使用寿命等因素,选择合适的模具结构。
常见的模具结构有单工位模和多工位模,根据实际需求进行选择。
3.2 冲孔设计原则冲孔设计是冲压模具设计的重要内容,其目的是通过切割或穿孔来获得所需形状。
冲孔设计需要考虑到材料特性、孔的数量和布局等因素,确保冲孔的准确性和效率。
3.3 净形状设计原则净形状是指通过冲压模具得到的金属零件的最终形状。
净形状设计需要考虑到材料的流动性和伸缩性,选择合适的冲压工艺参数,确保零件的质量和尺寸精度。
3.4 材料选择和处理原则冲压模具设计需要选择合适的材料,并进行适当的处理,以提高模具的硬度和耐磨性。
常用的模具材料包括合金钢、高速钢和硬质合金等。
4. 冲压工艺与模具设计的优化方法为了提高冲压工艺和模具设计的效率和品质,可以采用以下优化方法:4.1 CAD/CAE技术的应用CAD(计算机辅助设计)和CAE(计算机辅助工程)技术可以帮助设计师进行模具设计和工艺分析。
通过使用CAD软件进行三维建模和设计,可以提高设计的精度和效率。
而CAE技术可以进行模具结构和冲压工艺的分析,找出潜在的问题和改进方案。
4.2 模具试验与实验分析模具试验和实验分析可以通过实际加工样件的测试,验证和优化设计。
冲压模具毕业设计论文[1]
![冲压模具毕业设计论文[1]](https://img.taocdn.com/s3/m/f70dea08376baf1ffc4fadf4.png)
第一章绪论1.1 中国冲压模具现状根据考古发现,早在2000多年前,我国已有冲压模具被用于制造铜器,证明了中国古代冲压成型和冲压模具方面的成就在世界领先。
1953年,长春第一汽车制造厂在中国首次建立了冲模车间,该厂于1958年开始制造汽车覆盖件模具。
我国于20世纪60年代开始生产精冲模具。
在走过了漫长的发展道路之后,目前我国已形成了300多亿元(未包括港、澳、台的统计数字,下同。
)各类冲压模具的生产能力。
近年来,我国冲压模具水平已有很大提高。
大型冲压模具已能生产单套重量达50多吨的模具。
为中档轿车配套的覆盖件模具国内也能生产了。
精度达到1~2μm,寿命2亿次左右的多工位级进模国内已有多家企业能够生产。
表面粗糙度达到Ra≦1.5μm的精冲模,大尺寸(Φ≧300mm)精冲模及中厚板精冲模国内也已达到相当高的水平。
1.1.1 模具CAD/CAM技术状况我国模具CAD/CAM技术的发展已有20多年历史。
由原华中工学院和武汉733厂于1984年共同完成的精冲模CAD/CAM系统是我国第一个自行开发的模具CAD/CAM 系统。
由华中工学院和北京模具厂等于1986年共同完成的冷冲模CAD/CAM系统是我国自行开发的第一个冲裁模CAD/CAM系统。
上海交通大学开发的冷冲模CAD/CAM系统也于同年完成。
20世纪90年代以来,国内汽车行业的模具设计制造中开始采用CAD/CAM技术。
国家科委863计划将东风汽车公司作为CIMS应用示范工厂,由华中理工大学作为技术依托单位,开发的汽车车身与覆盖件模具CAD/CAPP/CAM集成系统于1996年初通过鉴定。
在此期间,一汽和成飞汽车模具中心引进了工作站和CAD/CAM 软件系统,并在模具设计制造中实际应用,取得了显著效益。
1997年一汽引进了板料成型过程计算机模拟CAE软件并开始用于生产。
模具CAD/CAM技术能显著缩短模具设计与制造周期,降低生产成本,提高产品质量,已成为人们的共识。
冲压模具毕业设计论文范文

冲压模具毕业设计论文范文冲压模具设计是冲压工艺中重要的一环,合理的模具设计能够提高产品质量、提高生产效率和降低生产成本。
本论文将以冲压模具设计为研究对象,探讨其设计理念和方法,以及在工程实践中的应用。
一、引言随着冲压工艺的广泛应用,冲压模具设计的重要性逐渐凸显。
良好的冲压模具设计能够提高产品的精度和质量,降低产品的成本和生产周期。
因此,冲压模具设计已成为冲压工艺中不可或缺的一部分。
二、冲压模具设计的理念1.综合运用先进技术冲压模具设计应充分利用先进的CAD/CAM/CAE技术,结合数字化模具设计和制造,提高设计效率和精度。
2.优化设计思路通过合理的设计思路,最大限度地降低模具的结构复杂度,减少零部件数量,提高模具的强度和刚度,降低模具重量和成本。
3.标准化设计冲压模具设计应遵循国家和行业的相关标准,确保设计的合理性和安全性。
同时,建立一套适合企业实际情况的标准化设计流程,提高设计的一致性和可操作性。
三、冲压模具设计的方法1.确定工艺参数根据产品的设计要求和冲压工艺的特点,确定冲床的类型和规格,进而确定模具的结构和尺寸。
2.分析产品特点对产品的结构和性能进行分析,确定产品的冲压工艺,包括冲床的振动频率、冲击力大小等参数。
3.设计冲床结构根据冲压工艺的要求和产品特点,设计冲床的结构,包括上模架、下模架、导向装置、传动装置、夹持系统等。
4.设计模具结构根据冲床结构的要求和产品特点,设计模具的结构,包括上模、下模、导向柱、顶针、滑块、模台等。
5.进行模具制造根据模具结构设计的要求,进行模具的加工和制造,包括CAD设计、数控加工、装配等环节。
四、冲压模具设计的工程实践冲压模具设计的工程实践主要包括以下几个方面:模具设计、模具制造、调试和生产。
1.模具设计根据产品的设计要求,进行冲床和模具的结构设计,确定模具的尺寸、材料和加工工艺。
2.模具制造根据设计要求,进行模具的制造和加工,包括材料准备、数控加工、装配和调试等环节。
- 1、下载文档前请自行甄别文档内容的完整性,平台不提供额外的编辑、内容补充、找答案等附加服务。
- 2、"仅部分预览"的文档,不可在线预览部分如存在完整性等问题,可反馈申请退款(可完整预览的文档不适用该条件!)。
- 3、如文档侵犯您的权益,请联系客服反馈,我们会尽快为您处理(人工客服工作时间:9:00-18:30)。
冲压件模具工艺性分析毕业论文第一章引言是工业产品生产用的重要工艺装备,它是以其自身的特殊形状通过一定的方式使原材料成形(成型)。
现代产品生产中,模具由于其加工效率高、互换性好、节约原材料,所以得到广泛的应用[1]。
冲压加工是利用安装在压力机上的模具,对放置在模具的板料施加变形力,使板料在模具产生变形,从而获得一定形状、尺寸和性能的产品零件的生产技术。
由于冲压加工常在室温下进行,因此也称冷冲压。
冲压成形是金属压力加工方法之一,是建立在金属塑性变形理论基础上的材料成形工程技术。
冲压加工的原材料一般为板料或带料,故称为板料冲压。
冲压工艺是指冲压加工的具体方法和技术经验,冲压模具是指将板料加工成冲压零件的特殊专用工具。
冲压生产靠模具和压力机完成加工过程,其特点有:质量稳定,互换行好;可以获得难以制造的壁薄、重量轻、刚性好、表面质量高、形状复杂的零件;不但节能,而且节约金属;它是一种高效率的加工方法。
生产中为满足冲压零件形状、尺寸、精度、批量大小、原材料性能的要求,冲压加工的方法是多种多样的。
但是,概括起来可以分为分离工序与成形工序两大类。
分离工序又可分为落料、冲孔和剪切等,目的是在冲压过程中使冲压件与板料沿一定的轮廓线分离。
成形工序可分为弯曲、拉深、翻孔、翻边、胀形、缩口等,目的是使冲压毛坯在不破坏的条件下发生塑性变形,并转化成所要求的制件形状。
第二章冲压件工艺性分析2.1冲裁件的工艺性分析冲裁件的工艺性是指冲裁件对冲压工艺的适应性。
即冲裁件的结构、形状、尺寸及公差等技术要求是否符合冲裁加工的工艺要求,难易程度如何。
工艺性是否合理,对冲裁件的质量、模具寿命和生产效率有很大影响。
良好的冲裁工艺性能使材料消耗少、工序数量少、模具结构简单且使用寿命长、产品质量稳定。
2.1.1 冲裁件的形状和尺寸(1)冲裁件的形状设计应尽量简单、对称,同时应减少排样废料。
(2)除在少、无废料排样或采用镶拼模结构是,允许工件有尖锐的清角外,冲裁件的外形或孔交角处应采用圆角过渡,避免清角。
(3)尽量避免冲裁件上过长的悬臂与窄槽,它们的最小宽度tb5.1≥。
(4)冲裁件的凸起和凹槽宽度不应小于板料厚度t的两倍,冲裁件孔与孔之间,孔与零件边缘间的壁厚,因受模具强度和零件质量的限制,其值不能太小。
一般要求.5tc'≥。
1c≥,t(5)冲裁件的孔径因受冲孔凸模强度和刚度的限制,不宜太小,否则容易折断和压弯。
冲孔最小直径与孔的形状、板料力学性能、板料厚度有关。
2.1.2 冲裁件的尺寸精度和表面粗糙度(1)冲裁件的尺寸精度要求,应在经济精度围以,对于普通冲裁件,起经济精度不高于IT11级,冲孔件比落料件高一级。
金属冲裁件的、外形的经济精度不高于IT11级。
一般落料精度最好低于IT10级,冲孔精度最好低于IT9级。
(2)非金属冲裁件、外形的经济精度为IT14、IT15级。
(3)冲裁尺寸标注符合冲压工艺要求。
2.2 异形垫圈工艺分析冲裁件材料是08钢,属于优质碳素结构钢,具有较好的塑性和韧性,主要用来制造冷冲压零件。
冲裁件结构形状简单,无尖角,零件图上所有尺寸均未标注公差,属于自由尺寸,按IT14级确定工件的尺寸公差,如图2.1所示。
经查公差表[3],各尺寸为:mm 60074.0-Φ , mm 3052.00+ , mm 3052.00+ ,mm 63.00+R ,mm 325.00+R 。
图2.1 制件图经上诉分析,产品的材料性能符合冲压加工要求。
2.3 制定工艺方案2.3.1 冲裁模的选择(1)单工序冲裁模单工序冲裁模是指在压力机一次行程只完成一种冲压工序,而不论冲裁的凸(或凹)模是单个还是多个.单工序模有落料模、冲孔模、切断模、切口模、切边模等。
如采用单工序冲裁模,该零件需落料单工序模和冲孔单工模。
由于采用单工序模进行加工,模具制造简单、维修方便,但加工效率底、零件精度较低,所以不适合大批量生产。
若采用单工序冲裁模,需要落料和冲孔两道工序才能完成,不但零件的精度难以保证,模具数量和工序会增加,而且工序管理也变得复杂。
(2)级进冲裁模级进冲裁模又称连续冲裁模,是指压力机在一次行程中,依次在模具几个不同位置上同时完成多到冲压工序的冲模。
连续冲裁模生产效率高,便于实现生产的自动化,操作方便、安全,适零件大批量生产。
其缺点是模具结构复杂、制造加工困难、模具成本较高。
(3)复合冲裁模复合冲裁模是指压力机在一次行程中,在模具同一部位同时完成数倒冲压工序的模具。
复合模结构紧凑、生产效率高、工件精度高,特别是制件孔对外形的位置容易保证。
对条料的要求不高,对边角余料也可进行加工。
但是模具结构复杂,模具制造成本低、周期长。
适用于大批量生产。
因此适用于大批量加工冲孔和落料两道工序的零件的是连续冲裁模和复合冲裁模,两者比较后采用复合冲裁模。
2.3.2 确定复合模类型按照凹模位置的不同,复合模分为倒装复合模和顺装复合模两种。
(1)顺装复合模冲裁时冲孔的废料在下模或条料上,不易清除,故很少采用。
(2)倒装式复合模废料直接由凸模从凸凹模孔推出,零件被凸凹模顶入凹模孔,待冲压结束后由推件板推出。
因此加工该零件采用倒装式复合模。
2.4 排样设计排样设计是指冲裁件在条料或板料上的布置方式。
排样与否不但影响材料的经济利用,还影响到制件的质量、模具的结构与寿命、制件的生产率和模具的成本等技术、经济指标[9]。
2.4.1 排样设计原则(1)提高材料利用率。
(2)改善操作性。
(3)使模具结构简单合理、寿命高。
(4)保证制件质量。
2.4.2 排样的选择(1)有废料排样有废料排样是指在冲裁件与冲裁件之间、冲裁件与条料侧边之间均有工艺余料废料,冲裁是沿冲裁件的封闭轮廓进行的。
(2)少废料排样少废料排样是指只在冲裁件之间或只在冲裁件与条料侧边之间留有搭边。
冲裁只沿冲裁件的部分轮廓进行,材料利用率可达70%~90%。
(3)无废料排样无废料排样是指在冲裁件与冲裁件之间、冲裁件与条料侧边之间均无搭边存在,冲裁件直接由切断条料获得的。
材料利用率可高达85%~90%。
采用少废料、无废料排样时,材料利用率高,不但有利于一次行程获得多个冲裁,还可以简化模具结构、降低冲裁力,但是因为条料本身的公差以及条料导向与定位所产生的误差将直接影响冲裁件,所以冲裁件的尺寸精度较低。
同时,在有些无废料排样中,冲裁时模具会单面受力,不但会加剧模具的磨损,降低模具寿命,而且也直接影响到冲裁件的断面质量。
有废料排样时冲裁件质量和模具寿命较高。
所以,在排样设计中选择有废料排样。
2.4.3排样形式根据冲裁件板料上的排样方式,有直排、单行排、多行排、斜排、对头直排和对头斜排等多种排列方式。
2.4.4 排样设计(1)搭边冲裁件与冲裁件之间、冲裁件与条料侧边之间留下的工艺余料称为搭边。
搭边的作用:补偿定位误差,保持条料有一定的距离,以保证零件质量和送料方便[9]。
冲裁件冲裁时,搭边过大,会造成材料浪费,搭边太小,冲裁是容易翘曲或被拉断,不仅会增大冲件毛刺,有时还会拉入凸、凹模间隙中损坏模具刃口,降低模具寿命,或影响送料工作。
搭边值的合理数值主要取决于冲裁件的板料厚度,材料性质,外廓形状及尺寸大小等,一般来说,材料硬时,搭边值可取小些,软材料或脆性材料,搭边值应取大些,板料厚度大,需要的搭边值大,冲裁件的形状复杂,尺寸大,过渡圆角半径小,需要的搭边值大,手工送料或有侧压板导时, 搭边值可取小些。
根据此零件材料的厚度0.8mm 、外轮廓形状及尺寸查找有关资料:0.81=a 0.1=a(2)送料进距与条料宽度模具每冲裁一次,条料在模具上前进的距离称为送料进距。
当单个进距只冲裁一个零件时,送料进距的大小等于条料上两个零件对应点之间的距离:1D a A +=式中 A —送料进距,mm 。
D —平行于送料方向的冲裁件宽度,mm 。
1a —冲裁件之间搭边值,mm 。
在式中 mm 60=D 8.01=a故: 60.8m m 0.860D A 1=+=+=a(3)条料宽度冲裁前通常需要按要求将板料裁剪为适当宽度的条料,为保证送料顺利,不因条料过宽而发生卡死现象,条料的下料公差规定为负偏差,条料在模具上送进时,一般都有导料装置,有时还要使用侧压装置(侧压装置是指在条料送进过程中,在条料侧边作用一横向压力,使条料紧贴料板一侧送进的装置)。
当条料在无侧压装置的导料板之间送料时,条料宽度B 按下式计算:0]c a 2 D [B δδ-+++=)(式中 B — 条料宽度的基本尺寸,D — 条料宽度方向零件轮廓的最大尺寸,a — 侧搭边值,δ— 条料下料剪切公差,c — 条料与导料板之间的间隙,本设计采用的是无侧压装置的,公式为:]c a 2 D [B δδ-+++=)(在式中 60=L0.1a = 5.0=δ 1.0=c故: 0]c a 2 D [B δδ-+++=)(5.00.1)]0.51.0(2 60 [-++⨯+=mm 2.6305.0-=(4)排样图图2.2 排样图(5)材料利用率材料利用率是冲压工艺中一个非常重要的经济技术指标。
其计算可用一个进距冲裁件的实际面积与毛坯面积的百分比表示:%100/⨯=BS A η式中 A — 一个进距冲裁件实际面积, 2mm 。
S — 送料进距, mm 。
B — 条料宽度,A 经cad 软件画图后直接测量出面积为2296.82mmB=63.2mm,S=60.8mm故: %100/⨯=BS A η%1008.602.638.2296⨯⨯=%10056.38428.2296⨯= %60≈此制件排样利用率为60%。
第三章 冲裁工艺计算3.1 冲裁模刃口尺寸计算3.1.1 凸、凹模刃口尺寸计算原则(1)落料件尺寸由凹模尺寸决定,冲孔时孔的尺寸由凸模尺寸决定。
(2)设计落料模时,凹模基本尺寸应取尺寸公差围的较小尺寸;设计冲孔模时,凸模基本尺寸则应取工件孔尺寸公差围的较大尺寸。
(3)凹模和凸模制造公差主要与冲裁件的精度和形状有关。
3.1.2 凸、凹模刃口尺寸计算由于模具加工方法不同,凸模与凹模刃口部分尺寸的计算公式与制造的表注也不同,刃口尺寸的计算方法可分为两种情况,一种是互换法,另一种是配作法。
互换法适于加工圆形和规则形状的冲裁件。
配作法适于加工形状复杂或薄料冲裁件。
在这里根据该零件料厚t=0.8选用配作法加工。
(1)查找有关资料[1]:A =mm 60074.0-Φ,5.0=X ,B=mm 3052.00+ 5.0=X ,C=mm 3052.00+ 5.0=X , D=mm 63.00+R 5.0=X ,E=mm 325.00+R ,5.0=X 。
(2)凹模尺寸刃口尺寸计算公式:∆+∆-=25.00max )(x A A 式中 A — 磨损后增大的刃口尺寸,mm 。