理光TNPM——全面规范化生产维护简述
TnPM管理简述

12、小结
.
3
T n P M现代设备管 理基础
.
4
T n P M现代设备管理基础
一项伟业 设备是工厂的骨骼、肌肉、脉管 和神经系统, 是工厂的肉体!
设备管理工作者肩负重大责任!
.
5
T n P M现代设备管理基础
二大公理 全员对设备的了解、爱护与维护 Is Best。
系统完备性设计、长远的思考 Is 可持续发展
各方面不可或缺,才能取得这 场战役的胜利
.
25
T n P M核心—检维修系统解决方案
维修模式与策略研究
·事后维修 ·周期性预防维修 ·状态维修(预知维修) ·改善维修 ·主动维修 ·机会维修
.
26
T n P M的点检管理
.
27
T n P M的点检管理
点检管理定义
·安排专人 ·利用人的五感、简单仪表工具等 ·按照一定周期和标准检查设备部位 ·发现隐患,掌握故障初期信息 ·及时采取对策,将故障消灭在萌芽 状态
.
48
T n P M的维修组织与维修规范
企业人机系统生产现场大有潜力可挖 使设备有效工作(EAT)时间最长
.
49
T n P M的六项改善 有氧活动
.
50
T n P M的六项改善有氧活动
六项改善--6I(相互联系支持) ·改善效率 ·改善成本 ·改善安全与环境 ·改善质量 ·改善员工疲劳 ·改善工作与 服务态度
.
51
T n P M的六项改善有氧活动
有氧活动O2
OPS-One Point Suggestion 一点建议
OPL-One Point Lesson
一点课
.
全员规范化生产维护(TnPM)在石化企业中的应用
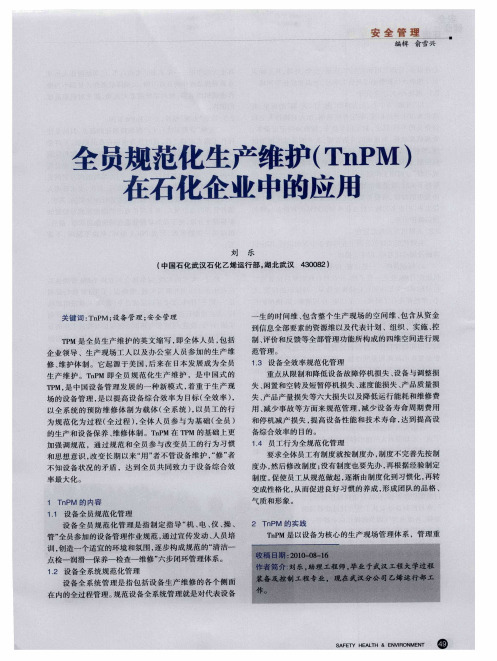
SE L &NR MN 0 ATH T E INE FY 卧 H V O T
安全、 健 境
安 全 管 理
心在设备 , 管理 范围涵盖生产 、 量 、 质 安全 、 境 , 环 甚至涵 盖 员工绩效评估 和激励 以及 员1 学 习 、 : 培训 和成长 等领域 。
21 现 场 6 . S的综 合 治 理
以“ 五源” 中心 , 为 大力整 治“ 、 、 、 ” 跑 胃 滴 漏 的现 象 , 提 高机 泵卫生 评价标 准 , 制定 考核 条例 , 大对 操作 人员 和 加
设备 员 的考核 ; 次 , 定机 泵盘 车 、 换 油 登记记 录本 , 其 制 加
“ 五源” 管理 是进行生 产现场精 细化 的起 点 , 目的是使 操 作1 做实 巡检 工作 , 时发现 现场存 在 的隐患 , 将隐 二 及 并 患分 为 5类 : 漏源 、 泄 清扫 困难源 、 缺陷 源 、 费源 和危险 浪 隐患 源。 在五源过程管 理 中, 首先规范 “ 生产现场 五源发现 分析 表” ,要 求规范填 写 ,对每 一列需填 写的 内容 实例说
气 质 和形 象 。
2 n M 的 实 践 T P
11 设 备 全 员 规 范 化 管 理 .
设备 全 员规 范化 管理 是 指制 定指 导 “ 、 、 、 、 机 电 仪 操 管” 全员参 加的设备管理 作业规范 , 通过 宣传发 动 、 人员培
TP n M是以设备 为核心 的生产 现场管理 体系 ,管理重
训, 创造一 个适宜 的环境 和氛 围 , 步构成规 范的 “ 逐 清洁一 点 检一 润滑一保 养一 检查一 维修” 步闭环管理 体系。 六 12 设备全 系统规范化管理 . 设备全 系统 管理 是指 包括设 备生 产维 修 的各个 侧 面
全面规范化生产维护TnPM基本知识

全面规化生产维护TnPM设备管理模式学习材料之一TnPM基本知识中国石油天然气运输公司二OO八年二月全面规化生产维护TnPM基本知识一、全面规化生产维护TnPM产生全员生产维修,又译为全员生产保全,即Total Productive Maintenance(TPM),20世纪70年代以来在日本企业推广,后逐步在世界围企业得到应用。
它是以提高设备综合效率为目标,以全系统的预防维修为过程,全体人员参与为基础的设备保养和维修管理体系。
TPM管理模式自20世纪80年代就引进到中国,但多年来很多中国企业推广应用得并不成功。
1998年,大学葆文教授在多年研究和推广TPM的基础上,结合中国企业员工行为特点,提出了规化的TPM的概念,即全面规化生产维护。
TnPM是以设备综合效率和完全有效生产率为目标,以全系统的预防维修体系为载体,以员工的行为规为过程,全体人员参与为基础的生产和设备系统的维护、保养和维修体制。
二、TnPM的核心1、开展TnPM主要环节如下:(1)研究运行现场(现场、现事、现物)(2)找出规律(原理、优化)(3)制订行为(操作、维护、保养、维修)规(原则)(4)评估效果(评价)(5)持续改善(改进)2、 TnPM规化的畴TNPM规化的畴:维修程序规化、备件管理规化、前期管理规化、维修模式规化、润滑管理规化、现场管理规化、组织结构规化以及其它方面的规化。
TnPM的理念是文明企业的修炼过程,是“绿色”企业的营造过程,也是企业文化和灵魂的模塑过程。
3 、TnPM的核心——四个“全”(1)以全效率和完全有效生产率为目标对于设备系统而言,TnPM追求的是最大的设备综合效率;对于整个生产系统而言,TnPM追求的是最大的完全有效生产率。
设备综合效率反映了设备本身的潜力挖掘和发挥,即对设备时间利用上、速度上和质量上的追求。
管理者致力于六大损失的控制。
完全有效生产率反映了整个生产系统的潜力挖掘和发挥,即从设备前期管理的有效性、企业生产排程、系统同步运行、瓶颈工序攻关、生产计划、组织协调、主次分析等方面提升效率,达到最优。
TnPM简要介绍
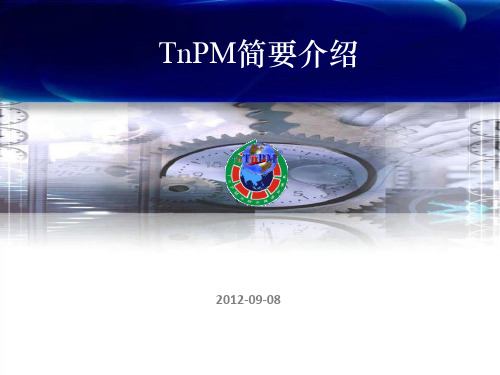
一句话现状描述:
改进方法和建议:
××公司
卡果或效益:
理由: 采纳
正面
不采纳
查六源 提建议 写改善 拿大奖
a
反面
17
员工填写LOOK卡 1
流程示意图
2 完成后放置 到提交栏
4 根据需要填写正式表格,归档
3
Yes
车间定期收
No
集并审核
a
5
暂时不合适,填 写理由,放回 “未采纳”
合理化建议 工会 或行政部门 标准不足,比较粗 只管提,自己不一定做 没有追求 无或很少开展促进活动 ……
16
a
16
××公司
卡
填写人
日期
六源 类别
□污染源 □清扫困难源 □故障源 □浪费源 □质量缺陷源 □危险源
建议 类别
○生产运营 ○工艺质量 ○设备管理 ○设计研发 ○仓储物流 ○人力资源 ○安全环保 ○企业文化 ○其它
a
5
TnPM推进的五个里程碑
a
6
TnPM推行步骤的对应表
阶
段
步
骤
第一阶段:
第 一 步: 企业的战略目标和现状全面调研;
确定目标,建立组织, 培训人才,制订计划。
第 二 步: TnPM导入、建立推进组织及培训;
第 三 步: TnPM启动、制定推进目标及计划;
第二阶段:
第 四 步: 以 6 S 活动为切入点;
TnPM体系的基 础和着力点:涵 盖面的广泛,参 与人员和部门的 广泛
TnPM体系的精 髓和载体:首先 是人行为的规范, 再到设备管理环 节和流程的规范, 最后是系统的规 范
TnPM体系的目 的和归宿:服务 主营业务,关注 效益
TNPM--全员规范化生产维修

TNPM──全员标准化生产维修一条比拟适应中国企业现状的设备管理之路李葆文广州大学维修工程技术学部广州市小北登峰麓景路狮带岗中,广州大学,510091一TNPM思想概述TNPM 〔Total Normalized Productive Maintenance〕是在TPM----“全员生产维修〞思想的根底上提出的新设备管理模式。
众所周知,全员生产维修是日本企业在美国生产维修根底上,吸收了英国综合工程学、中国鞍钢宪法的设备管理群众路线做法而提出的现场设备管理模式,简称TPM (Total Productive Maintenance)。
这一设备管理模式已在全世界得到广泛传播,受到各国企业界的欢送,而且给许多企业带来效益。
由于日本及其国际企业应用TPM管理模式取得了良好的效果,使这一管理模式成为当代企业管理有代表性的手段之一,同时也成为国际上应用最多的设备管理方法。
国内也有不少企业在设备管理工作中全面或局部引进了这种管理模式。
全员生产维修体制在实施中强调设备管理的“全员〞参与。
“全员〞成为这一管理模式的理念和精髓,也是最难跨越阶梯。
无论在欧洲、美洲,还是在中国,TPM在不少企业的推行或者是虎头蛇尾,或者是流于形式,也主要因为“全员〞不彻底。
这主要是由于各国的国情不同,文化不同,对“全员〞理念的认同程度、贯彻力度有所不同所至。
例如,一些西方国家认为TPM使工人劳动强度增加,企业的工会或劳工组织出面对TPM加以抵抗。
还有一些西方国家的工人并不情愿做超过工资所得的“额外〞工作,执行TPM十分勉强。
中国的企业在推行TPM时,也遇到两方面的困难:一是操作工人缺乏自主、主动参与TPM活动的积极性;二是工人的文化素质偏低,很难适应越来越先进的设备维修,使TPM的“自主维修〞难于操作。
综观TPM的全部内容,主要表达了现场设备管理的“全员〞化,注重设备的根底保养工作。
这一点恰恰是不少企业的弱点,是应该提倡和强力推行的。
TnPM简述
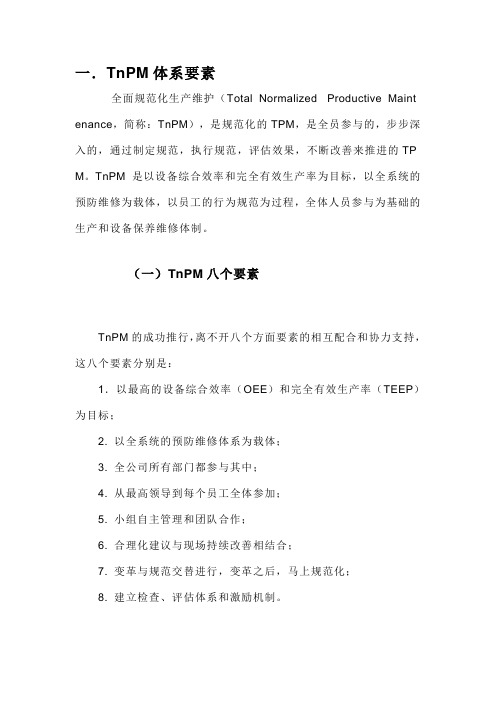
一.TnPM体系要素全面规范化生产维护(Total Normalized Productive Maint enance,简称:TnPM),是规范化的TPM,是全员参与的,步步深入的,通过制定规范,执行规范,评估效果,不断改善来推进的TP M。
TnPM 是以设备综合效率和完全有效生产率为目标,以全系统的预防维修为载体,以员工的行为规范为过程,全体人员参与为基础的生产和设备保养维修体制。
(一)TnPM八个要素TnPM的成功推行,离不开八个方面要素的相互配合和协力支持,这八个要素分别是:1.以最高的设备综合效率(OEE)和完全有效生产率(TEEP)为目标;2. 以全系统的预防维修体系为载体;3. 全公司所有部门都参与其中;4. 从最高领导到每个员工全体参加;5. 小组自主管理和团队合作;6. 合理化建议与现场持续改善相结合;7. 变革与规范交替进行,变革之后,马上规范化;8. 建立检查、评估体系和激励机制。
(二)TnPM四个“全”1. 以设备综合效率和完全有效生产率为目标2. 以全系统的预防维修体制为载体3. 以员工的行为全规范化为过程4. 以全体人员参与为基础(三)TnPM五个“六”1. 6S:整理、整顿、清扫、清洁、安全、素养2. 6I,即6 个Improvement, 又称 6 项改善,其内容是:(1)改善影响生产效率和设备效率的环节;(2)改善影响产品质量和服务质量的细微之处;(3)改善影响制造、维护成本之处;(4)改善造成员工疲劳状况;(5)改善造成灾害的不安全之处;(6)改善工作和服务态度。
3. 6Z,即 6 个Zero, 又称六个“零”的活动,其内容是:(1)追求质量零缺陷:Zero Defect(2)追求材料零库存:Zero Inventory(3)追求安全零事故:Zero Accident(4)追求工作零差错:Zero Mistake(5)追求设备零故障:Zero Fault(6)追求生产零浪费:Zero Waste4. 6T,即6个Tool,又称6大工具,其内容是:(1)单点课程OPL 体系;(2)可视化管理;(3)目标管理;(4)绩效管理;(5)团队合作;(6)项目管理。
TnPM全面规范化生产维护体系知识

从“全员生产维修”到“全面规范化生产维护”摘要:在我国,如何实施全员生产维修(TPM)并取得成效是一个非常值得关注和研究的话题。
与发达国家相比,我国企业在传统习惯、企业文化和员工技能素养等方面存在着差距,许多国内企业在推进TPM过程中也遇到了许多的困惑。
通过多年来对50多家企业的调研和指导,广州大学李葆文教授团队提出了全面规范化生产维护(TnPM)的概念,强调如何通过员工行为的规范化来引导企业现场持续改善。
TnPM进一步完善和发展了TPM推进的7个阶段内容,并结合中国企业实际提出系统的解决方案,总结出了TnPM的四个“全”、“五个六架构”和六大支柱活动,在继续坚持6S活动和员工自主维护的基础上,提出检维修模式的SOON流程、员工与企业共同成长的FROG体系,以及五阶六维的评价指标考核方法。
TnPM是中国企业的TPM之路。
关键词:TPM,TnPM概述:为什么要TnPMTPM作为一个较成熟的设备管理维护体系,已经在全世界多个国家和地区的企业得到推广应用。
与欧美、日韩等发达国家相比,在中国这样的发展中国家实施TPM却遇到了极大的挑战和困难。
主要的原因在于文化与传统不同、企业员工平均文化水平不同、以及习惯和素养不同等。
国内外许多文献资料也总结出:TPM的成功主要在于人力资源管理上(员工自主维护),对设备本身的维修模式如何建立涉及的内容却不多,一旦遇到不同国情和员工素养的实际情况,在TPM推进和移植上就会遇到麻烦。
在通过多年来对50多家企业的调研和指导的实践后,以李葆文教授为核心的广州大学团队提出了更适合中国这样发展中国家企业特点的“全面规范化生产维护”管理模式。
简单而言,TnPM就是以设备综合效率和完全有效生产率为目标,以全系统的预防维修系统为载体,以员工的行为规范为过程,全体人员参与为基础的生产和设备维护、保养和维修体制。
(1)TnPM的四个“全”TnPM的精要可概括为四个“全”,设备的综合效率和完全有效生产率简称为“全效率”;全系统的预防维修体系简称为“全系统”,员工的行为规范化简称为“全规范”;全体人员参与简称为“全员”。
TNPM_全员规范化生产维修

TNPM──全员规化生产维修一条比较适应中国企业现状的设备管理之路葆文大学维修工程技术学部市小北登峰麓景路狮带岗中,大学,510091一TNPM思想概述TNPM (Total Normalized Productive Maintenance)是在TPM----“全员生产维修”思想的基础上提出的新设备管理模式。
众所周知,全员生产维修是日本企业在美国生产维修基础上,吸收了英国综合工程学、中国鞍钢宪法的设备管理群众路线做法而提出的现场设备管理模式,简称TPM (Total Productive Maintenance)。
这一设备管理模式已在全世界得到广泛传播,受到各国企业界的欢迎,而且给许多企业带来效益。
由于日本及其国际企业应用TPM管理模式取得了良好的效果,使这一管理模式成为当代企业管理有代表性的手段之一,同时也成为国际上应用最多的设备管理方法。
国也有不少企业在设备管理工作中全面或部分引进了这种管理模式。
全员生产维修体制在实施中强调设备管理的“全员”参与。
“全员”成为这一管理模式的理念和精髓,也是最难跨越阶梯。
无论在欧洲、美洲,还是在中国,TPM 在不少企业的推行或者是虎头蛇尾,或者是流于形式,也主要因为“全员”不彻底。
这主要是由于各国的国情不同,文化不同,对“全员”理念的认同程度、贯彻力度有所不同所至。
例如,一些西方国家认为TPM使工人劳动强度增加,企业的工会或劳工组织出面对TPM加以抵制。
还有一些西方国家的工人并不情愿做超过工资所得的“额外”工作,执行TPM十分勉强。
中国的企业在推行TPM时,也遇到两方面的困难:一是操作工人缺乏自主、主动参与TPM活动的积极性;二是工人的文化素质偏低,很难适应越来越先进的设备维修,使TPM的“自主维修”难于操作。
综观TPM的全部容,主要体现了现场设备管理的“全员”化,注重设备的基础保养工作。
这一点恰恰是不少企业的弱点,是应该提倡和强力推行的。
国的一些企业在设备管理的实践中也逐渐认识到“强化基础保养”和“全员”的必要性,如玉柴机器提出“重保养、零等待”,卷烟厂在十年前就提出“清洁、清洁、再清洁”的设备维护方针,卷烟厂在此基础上又提出“保养、保养、再保养”的口号,仪征化纤提出“党、政、工、团四位一体,机、电、仪(表)、操(作工)四位一体”的“全员”设备管理方针。
- 1、下载文档前请自行甄别文档内容的完整性,平台不提供额外的编辑、内容补充、找答案等附加服务。
- 2、"仅部分预览"的文档,不可在线预览部分如存在完整性等问题,可反馈申请退款(可完整预览的文档不适用该条件!)。
- 3、如文档侵犯您的权益,请联系客服反馈,我们会尽快为您处理(人工客服工作时间:9:00-18:30)。
董事长(总经理) 厂长
公司TNPM推进委员会 公司TNPM专职机构
经理 车间主任 组长 工人
厂级TNPM推进委员会 部门TNPM推进委员会
车间TNPM推进委员会 车间技术攻关组 TNPM活动小组
TNPM管理的五项主义
开展TNPM的主要环节
1、研究运行现场(现场、现事、现物):走进 现场,观察现事,了解现物; 2、找出规律(原理、优化):分析原理,提炼 优化; 3、制订行为(操作、维护、保养、维修)规范 (原则):给出文件化的行为准则; 4、评估效果(评价):跟踪、评价,找出不足; 5、持续改善(改进):再优化,形成新规范。
TNPM—— 全面规范化生产维护简述
TNPM的理念 文明企业的修炼 “绿色”企业的营造 企业文化和灵魂的模塑
TNPM—— 全面规范化生产维护简述
»TNPM的四个“全
1、以设备综合效率和完 全有效生产率为目标
2、以全系统的预防维修 体制为载体
3、以员工的行为全规范 化为过程
4、以全体人员参与为基 础
具体目标:PQCDSM
TNPM的目标管理计划与实施
第四步 :TNPM发动 动员大会:最高领导; 导入培训:外部专家; 刊物、看板、电子视板:宣传部门配合。
TNPM的目标管理计划与实施
第五步:“双6S”活动 整理-整顿-清扫-清洁-安全-素养 6S是基础; 6S是突破口; 6S同样要程序、规范管理:确定区域、人员、 标准、周期、方法,并有检查评估方案; 6S中必然发现根源性的问题——引入下一步的 内容。
修 批处理 批处理
批处理
批处理 M
总成维修
TNPM的“员工未来能力持续成
长”模型——FROG
一、自我工作能力分析 二、成长约束分析 三、树立新观念 四、 制订个人成长计划 五、目标导向的自上而下培训 六、员工自主式的单点课程培训体系建立 七、迈出行动的每一步 八、让员工和企业一同成长
TNPM 的组织结构
TNPM的八个要素和四个“六”
TNPM的四个“六”
6S: 整理、整顿、清扫、清洁、素养、安全 6I:改善效率、改善质量、改善成本、改善员工疲 劳状况、改善安全与环境、改善工作态度 6Z:零故障、零缺陷、零库存、零事故、零差错、
零浪费 6T:6个工具,即单点教材、可视化管理、目标 管理、企业教练法则、企业形象法则、SOON
策略
现场
Checking 检查
Monitoring Organizing Normalizing
监测
组织
规范
Diagnosing 诊断
维修管理规范化 ——流程工业组合维修模式
组合维修模式总架构
机 问题记录 问题记录 点检与诊断 问题记录 T
会 设备1 设备2 故障停机设备 设备3
N
维 同步检修 同除“六源”活动
污染源 清扫困难源 故障源 浪费源 缺陷源 事故危险源
TNPM的预防维修体系设计 ——SOON
SOON—Strategy —On-site-information —
Organizing —— Normalizing
流程
SOON体系框架
Strategy On-site
TNPM—— 全面规范化生产维护简述
规范化的范畴 维修程序规范化 备件管理规范化 前期管理规范化 维修模式规范化 润滑管理规范化 现场管理规范化 组织结构规范化 其他规范化
TNPM的目标管理计划与实施
起步 领导认识,导入培训,概念开发;
第一步 企业全面调研,认识基准和起点,树立目标; 具体指标: P(OEE,TEEP,故障停机时数等); Q(合格品率,客户投诉率等); C(制造成本,维修成本,设备、备件成本、停机损失等); D(按时交货率,计划完成率,库存等); S(事故率,事故损失工时数,工伤事故数); M(TNPM员工参与率,合理化提案数,单点课程制作数等)。
TNPM—— 全面规范化生产维护简述
什么是TNPM
TOTAL NORMALIZED PRODUCTIVE MAINTENANCE
TNPM是规范化的TPM,是全员参与的, 步步深入的,通过制定规范,执行规范, 评估效果,不断改善来推进的TPM。
TNPM—— 全面规范化生产维护简述
定义
TNPM是以设备综合效率和完全有效生 产率为目标,以全系统的预防维修系统 为载体,以员工的行为规范为过程,全 体人员参与为基础的生产和设备维护、 保养维修体制。
全效率
全 系统
全规范
全
员
TNPM的八个要素和四个 “六”
TNPM的八个要素 以最高的设备综合效率(OEE)和完全有效生产 率(TEEP)为目标; 以全系统的预防维修体系为载体; 全公司所有部门都参与其中; 从最高领导到每个员工全体参加; 小组自主管理和团队合作; 合理化建议与现场持续改善相结合; 变革与规范交替进行,变革之后,马上规范化; 建立检查、评估体系和激励机制。
TNPM的目标管理计划与实施
“双6S”活动 “6 Sources”,即六种来源,重点解决在6S活 动中遇到明显的“六源”问题, 主要是污染源、清扫困难源和故障源,顺带解 决6S中发现的安全隐患源、缺陷源和浪费源问 题。 维修技术人员参加的技术攻关小组是一支活 跃的力量,无论在5S的规范和程序化,还是在 “六源”的解决,都可以起到带动作用。
TNPM的目标管理计划与实施
第六步:以规范化为主线,创建样板机台
规范化要按照动作的逻辑联系,设计既体现正确操作, 对产品质量的关注,又能够适当维护,还要保证安全 的规范体系。 机台旁展示目视管理“两书” 工艺操作作业指导书(体现正确执行操作工艺,保证 产品质量,保证作业安全); 维护保养规范作业指导书(体现清扫、点检、保养、 润滑四位一体,加上诊断、维修六步闭环) 样板机台(线段)的选择:典型性,带动性。
TNPM的目标管理计划与实施
第二步 :建立组织,成立TNPM专职机构
公司TNPM推进委员会 TNPM执行办公室
部门/车间TNPM推进委员会 TNPM联络员
TNPM技术攻关小组 TNPM小组 TNPM小组
TNPM的目标管理计划与实施
第三步:制定公司TNPM目标、推进计划和实 施计划
最终目标:八个零(零故障、零事故、零缺陷、 零浪费、零库存、零投诉、零差错、零损失);