转炉留渣操作原因与注意事项
莱钢60t转炉单渣留渣操作实践

莱钢60t转炉单渣留渣操作实践安全规律,因此一直没有得到大范围推广应用。
但氧气转炉留渣操作能够充分利用前炉钢终点炉渣的热量、碱度和氧化性,大幅降低渣料消耗,在转炉吹炼初期可以快速造就高碱度氧化渣,有利于提高生产效率,并具有显著的经济效益,特别在铁水资源不足的钢厂效益更加突出。
因此各钢厂一直在进行生产试验,以求实现留渣操作的稳定。
留渣操作主要有两方面的危害:一是兑铁时碳氧剧烈反应发生大喷;二是转炉开吹打不着火,转炉烟道内氧气和一氧化碳达到爆炸极限,产生烟道爆炸事故。
1.1兑铁大喷的原因及预防即温度低于1507℃时,铁水和上一炉的炉渣接触,首先是硅的氧化(但也不排除有碳的氧化,因为铁水中含碳量较高),也就限制了碳的激烈氧化。
另外,也可根据不同温度下各种纯氧化物的分解压力找出碳和硅优先氧化的温度。
由氧化物标准生成自由焓的变化与温度的关系可知:SiO2分解壓力曲线与CO分解压力曲线相交的对应温度为1530℃。
当t小于1530℃时,[Si]先于[C]被氧化;当t大于1530℃时则[C]先于[Si]被氧化。
既便是在热力学满足式(3)的情况下,反应也不一定进行或进行的很缓慢而不会造成喷溅,这是由复杂的动力学因素决定的。
上式表明,化学反应速度随温度升高而加快,也就是说温度越高发生喷溅的概率越大。
反之,化学反应速度降低,发生喷溅的概率越小。
从热力学和动力学的分析都可以看出,降低炉渣温度是避免出现兑铁大喷的关键因素,目前转炉大部分实现了溅渣护炉,溅渣后炉渣温度均低于1500℃。
可以说留渣操作的条件已经具备。
同时在溅渣操作时,通过溅干炉渣,防止有液态炉渣,溅渣终点由炉长亲自查看炉渣状态,溅渣时加入一部分石灰等渣料等措施,可以确保兑铁时不出现大喷危害。
1.2 开吹打不着火的原因及预防开吹打不着火主要是由于留渣操作炉渣、加入的废钢带入的渣钢以及铁水带入的铁水渣量大,漂浮在表面,导致氧气流股不能够直接穿透渣层,发生反应。
开吹打火时间超过40s,则前期氧气流股一部分冲击炉渣表面,造成(FeO)聚集,一部分进入烟道内,造成烟道内氧气含量大于2%。
转炉铸渣安全操作规程
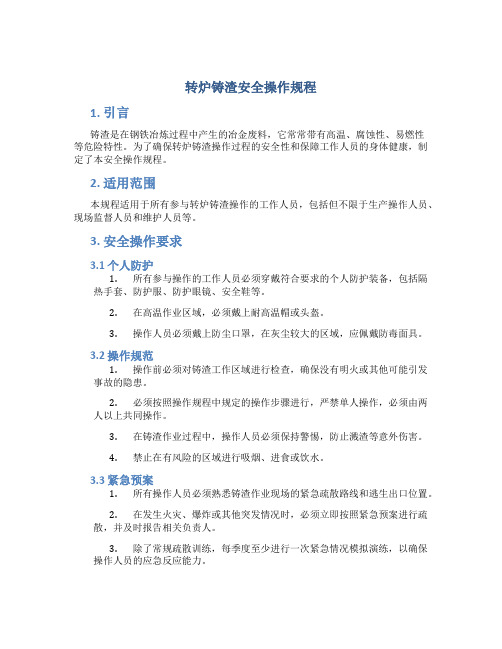
转炉铸渣安全操作规程1. 引言铸渣是在钢铁冶炼过程中产生的冶金废料,它常常带有高温、腐蚀性、易燃性等危险特性。
为了确保转炉铸渣操作过程的安全性和保障工作人员的身体健康,制定了本安全操作规程。
2. 适用范围本规程适用于所有参与转炉铸渣操作的工作人员,包括但不限于生产操作人员、现场监督人员和维护人员等。
3. 安全操作要求3.1 个人防护1.所有参与操作的工作人员必须穿戴符合要求的个人防护装备,包括隔热手套、防护服、防护眼镜、安全鞋等。
2.在高温作业区域,必须戴上耐高温帽或头盔。
3.操作人员必须戴上防尘口罩,在灰尘较大的区域,应佩戴防毒面具。
3.2 操作规范1.操作前必须对铸渣工作区域进行检查,确保没有明火或其他可能引发事故的隐患。
2.必须按照操作规程中规定的操作步骤进行,严禁单人操作,必须由两人以上共同操作。
3.在铸渣作业过程中,操作人员必须保持警惕,防止溅渣等意外伤害。
4.禁止在有风险的区域进行吸烟、进食或饮水。
3.3 紧急预案1.所有操作人员必须熟悉铸渣作业现场的紧急疏散路线和逃生出口位置。
2.在发生火灾、爆炸或其他突发情况时,必须立即按照紧急预案进行疏散,并及时报告相关负责人。
3.除了常规疏散训练,每季度至少进行一次紧急情况模拟演练,以确保操作人员的应急反应能力。
4. 设备维护和检查4.1 检查频率1.转炉铸渣设备必须定期进行检查和维护。
2.对液压系统、电气系统、运输设备等相关设备必须进行每月一次的全面检查。
4.2 维护要求1.发现设备故障或异常情况时,必须立即停止作业并报告维护人员进行处理。
2.维护人员必须按照维护计划进行维护和检修,并及时更新设备维护记录。
5. 废料处理5.1 废渣处理1.废渣必须分类收集,按照相关规定进行储存和处理。
2.废渣储存区域必须保持清洁,并设置明显的警示标志。
5.2 废气处理1.废气排放必须符合相关环保法律法规的要求,严禁未经处理直接排放。
2.废气处理设施必须进行定期维护和检修,并确保正常运行。
转炉车间溅渣操作要点11.19概要

转炉车间溅渣操作管理制度针对目前各班溅渣操作不统一,不能正确的通过溅渣来维护炉子,造成炉子频频告急,给厂部和车间带来极大的工艺事故和安全事故隐患,通过这几个月来对炉前工艺操作和终点控制情况,特对溅渣作出下规定:一、溅渣条件1、钢水必须出尽炉长、必须炉炉关注后大面的情况,不能出现凹坑或不平,必须观察出钢口位置高低,确保出钢口不高于后大面,保证每炉钢钢水都出尽,(如有钢水出不完的现象,跟班技术员、作业长、炉长必须在3炉钢内处理好保证炉渣的可溅性。
2、在出钢过程中,炉长、操枪工必须从炉后观察炉内炉渣情况,炉长需及时指导操枪工的调渣密度和用量,确保渣子不调死,保证溅渣时间和效果,并指导自己下一炉的化渣枪位和方法。
3、操枪工必须确定有正常的工作氮压和流量,确保溅渣过程效果。
4、值班长必须保证炉后有充份的丢补料,每炉钢保证在出钢过程中向炉内加入10-15包的丢补料(30kg(遇渣很粘时,可以少丢或不丢。
5、遇拉后吹严重时,操枪工必须先加入轻烧白云石或改渣剂来稠渣,稠渣后倒掉1/3再进行溅渣。
6、在钢水没出尽或溅渣发现炉口钢花很严重时,但炉况又很差时,溅渣枪位必须比正常高200mm以上,并且通过调渣来把渣子溅干。
二、溅渣操作要点1 、调渣工艺及要求调渣工艺是指在炼钢结束后,通过炉口观察炉渣状况,判定炉渣是否适宜溅渣。
如果炉渣过于稀,应加入少量改渣剂调整炉渣,增强炉渣的黏稠度,如果炉渣过热度高,炉渣稀,流动性良好,应加入少量轻烧白云石降低熔渣温度,提高炉渣黏度,使之更适宜溅渣的操作工艺。
(1直接溅渣工艺:即以炼钢过程中调整炉渣为主,炼钢后的渣较好适合溅渣基本不进行调渣,而直接进行溅渣操作。
要求铁水及原燃料条件比较稳定,吹炼平稳,终点控制准确,出钢温度低,终渣较好,适合出钢[C]>0.10%,出钢<1660℃的炉次。
(2出钢后调渣工艺:即在炼钢结束后,根据炉渣状况适当加入少量改渣剂或轻烧白云石用以降低炉渣过热度,提高炉渣黏度,改善炉渣的渣系使溅渣层更耐高温和侵蚀。
转炉溅渣护炉技术

转炉溅渣护炉技术的应用方法1.溅渣护炉的基本原理,是在转炉出完钢后加入调渣剂,使其中的Mg与炉渣产生化学反应,生成一系列高熔点物质,被通过氧枪系统喷出的高压氮气喷溅到炉衬的大部分区域或指定区域,粘附于炉衬内壁逐渐冷凝成固态的坚固保护渣层,并成为可消耗的耐材层。
转炉冶炼时,保护层可减轻高温气流及炉渣对炉衬的化学侵蚀和机械冲刷,以维护炉衬、提高炉龄并降低耐材包括喷补料等消耗。
氧气顶吹转炉溅渣护炉是在转炉出钢后将炉体保持直立位置,利用顶吹氧枪向炉内喷射高压氮气(1. 0MPa) ,将炉渣喷溅在炉衬上。
渣粒是以很大冲击力粘附到炉衬上,与炉壁结合的相当牢固,可以有效地阻止炉渣对炉衬的侵蚀。
复吹转炉溅渣护炉是将顶吹和底吹均切换成氮气,从上、下不同方向吹向转炉内炉渣,将炉渣溅起粘结在炉衬上以实现保护炉衬的目的。
溅渣护炉充分利用了转炉终渣并采用氮气作为喷吹动力,在转炉技术上是一个大的进步,它比干法喷补、火焰喷补、人工砌砖等方法更合理,其既能抑制炉衬砖表面的氧化脱碳,又能减轻高温渣对炉砖的侵蚀冲刷,从而保护炉衬砖,降低耐火材料蚀损速度,减少喷补材料消耗,减轻工人劳动强度,提高炉衬使用寿命,提高转炉作业率,减少操作费用,而且不需大量投资,较好地解决了炼钢生产中生产率与生产成本的矛盾。
因此,转炉溅渣护炉技术与复吹炼钢技术被并列为转炉炼钢的2项重大新技术。
2 溅渣护炉主要工艺因素2. 1 合理选择炉渣并进行终渣控制炉渣选择着重是选择合理的渣相熔点。
影响炉渣熔点的物质主要有FeO、MgO和炉渣碱度。
渣相熔点高可提高溅渣层在炉衬的停留时间,提高溅渣效果,减少溅渣频率,实现多炉一溅目标。
由于FeO易与CaO和MnO等形成低熔点物质,并由MgO和FeO的二元系相图可以看出,提高MgO的含量可减少FeO相应产生的低熔点物质数量,有利于炉渣熔点的提高。
从溅渣护炉的角度分析,希望碱度高一点,这样转炉终渣C2 S 及C3 S之和可以达到70%~75%。
转炉冶炼操作的关键点
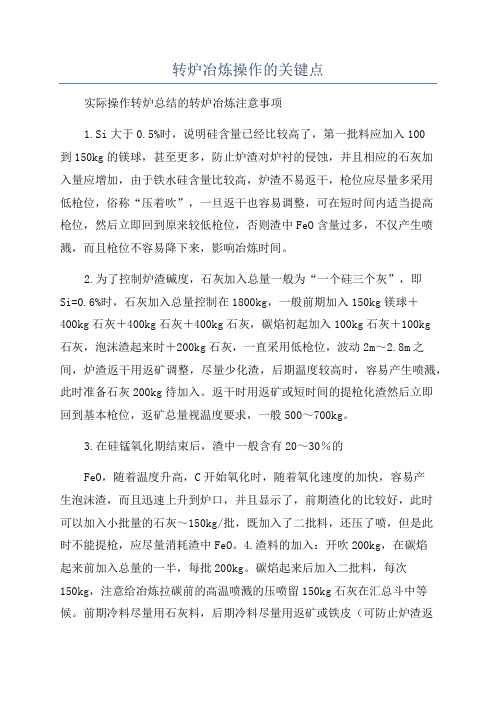
转炉冶炼操作的关键点实际操作转炉总结的转炉冶炼注意事项1.Si大于0.5%时,说明硅含量已经比较高了,第一批料应加入100到150kg的镁球,甚至更多,防止炉渣对炉衬的侵蚀,并且相应的石灰加入量应增加,由于铁水硅含量比较高,炉渣不易返干,枪位应尽量多采用低枪位,俗称“压着吹”,一旦返干也容易调整,可在短时间内适当提高枪位,然后立即回到原来较低枪位,否则渣中FeO含量过多,不仅产生喷溅,而且枪位不容易降下来,影响冶炼时间。
2.为了控制炉渣碱度,石灰加入总量一般为“一个硅三个灰”,即Si=0.6%时,石灰加入总量控制在1800kg,一般前期加入150kg镁球+400kg石灰+400kg石灰+400kg石灰,碳焰初起加入100kg石灰+100kg石灰,泡沫渣起来时+200kg石灰,一直采用低枪位,波动2m~2.8m之间,炉渣返干用返矿调整,尽量少化渣,后期温度较高时,容易产生喷溅,此时准备石灰200kg待加入。
返干时用返矿或短时间的提枪化渣然后立即回到基本枪位,返矿总量视温度要求,一般500~700kg。
3.在硅锰氧化期结束后,渣中一般含有20~30%的FeO,随着温度升高,C开始氧化时,随着氧化速度的加快,容易产生泡沫渣,而且迅速上升到炉口,并且显示了,前期渣化的比较好,此时可以加入小批量的石灰~150kg/批,既加入了二批料,还压了喷,但是此时不能提枪,应尽量消耗渣中FeO。
4.渣料的加入:开吹200kg,在碳焰起来前加入总量的一半,每批200kg。
碳焰起来后加入二批料,每次150kg,注意给冶炼拉碳前的高温喷溅的压喷留150kg石灰在汇总斗中等候。
前期冷料尽量用石灰料,后期冷料尽量用返矿或铁皮(可防止炉渣返干)。
5.Si小于0.4%时,说明硅含量已经比较低了,相应的石灰加入量应减少,由于硅含量比较低,碳焰起来的较早,应及时提前加入二批料。
铁水硅低时炉渣容易返干,注意提前提枪化渣。
6.不论硅高低,开吹时尽量采用30秒高、30秒次高再到正常的低枪位,可以帮助化好前期渣。
转炉炼钢中留渣技术的原理及应用

2.3留渣安锂 近年来,随着我国转炉炼钢技术不断发展和完
善,由于顶底复合吹炼、溅渣护炉等一系列的工艺出 现之后,能有效地解决喷溅问题。对于渣循环来说, 它能够带来良好的经济效益,从单扎法中衍生出各 种各样的操作工艺,自从留渣技术应用之初,要考虑 到它自身的安全,采取留渣操作之后进入废钢以后,
间,这对前期脱离有着积极的推动作用,经过反复的 实践研究,其中影响脱离效率撮主要的因素就在于 物质的酸碱度和炉渣的含量,避免炉渣中氧化铁过 多,产生的喷溅,必须要确保它的游离氧含量大于 900x10电科学的调整留渣含量叫 32稳定留渣量
对于绝大部分的炼钢厂来说,冶炼效果和留渣 量的稳定性,两者密切相关。如果炉渣发泡过稀,此 时可以使用氮气进行溅渣 ,能有效的控制问题的发 生,进而实现渣量稳定控制。我国首先使用的是
钢工艺实践[J].新疆钢铁,2018(2):26-30.
(编辑:苗运平)
(下转第116页)
・116・
.山酉肖金 E—mail:sxyjbjb@
第44卷
问题根源,实施改进措施。
3结论 1) 棒材劈头堆钢主要由钢坯质量问题引起(偏
析、夹杂)。
2) 钢坯内裂属于铸造缺陷,但与冶炼时成分相关。 3) 冶炼时应避开包晶点,可以有效避免偏析、 内裂。
4) 提高钢中镒硫比例可防治方坯内裂。 5) 轧制过程中,粗轧岗位密切盯钢,尽量及时处 理钢质问题。
6 )年修时,对轧机的轧制线对正,跟换更耐磨的
3、5架导卫衬板。 7)适当调大2、4机架导卫扭转角。
参考文献
[1 ]王凯.降低高线粗轧机轧辐轴承消耗的措施[J] •轧钢,2006,23
转炉铸渣安全操作规程
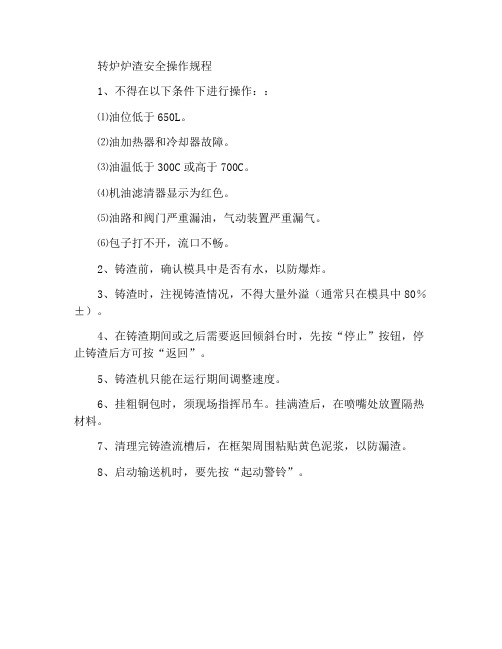
转炉炉渣安全操作规程
1、不得在以下条件下进行操作::
⑴油位低于650L。
⑵油加热器和冷却器故障。
⑶油温低于300C或高于700C。
⑷机油滤清器显示为红色。
⑸油路和阀门严重漏油,气动装置严重漏气。
⑹包子打不开,流口不畅。
2、铸渣前,确认模具中是否有水,以防爆炸。
3、铸渣时,注视铸渣情况,不得大量外溢(通常只在模具中80%±)。
4、在铸渣期间或之后需要返回倾斜台时,先按“停止”按钮,停止铸渣后方可按“返回”。
5、铸渣机只能在运行期间调整速度。
6、挂粗铜包时,须现场指挥吊车。
挂满渣后,在喷嘴处放置隔热材料。
7、清理完铸渣流槽后,在框架周围粘贴黄色泥浆,以防漏渣。
8、启动输送机时,要先按“起动警铃”。
转炉留渣操作原因与注意事项

转炉留渣操作原因与注意事项
一、转炉留渣操作可以极大降低原料消耗,在吹炼初期可以快速成渣,有利于提高生产率,因而推广应用的潜力很大,但转炉留渣操作易发生大喷溅,限制了其应用。
二、分析认为需要注意以下几点,可以使留渣操作得到切实可行:
1、安全问题:兑铁时喷溅,因此所留的炉渣应确保:一是温度不能太高(W 1500C),二是溅渣时间必须保证,因为留渣操作一般与溅渣护炉并用,必要时要加入一定量的改质剂稠渣。
2、初期渣化的早,尤其是前期低温时易发生喷溅,随之而来发生返干现象,导致沾枪沾罩操作困难,应注意。
3、开吹时打火困难,可以采用前后摇炉或者先点吹30-40s 再加废钢的办法。
4、吹气渣化得早,前期渣来得迅速,低温炉渣容易从炉口涌出,特别是吹炼到
约 6 分钟时,压料后易“返干”,特别是Si 数低时更明显,而铁水Si 含量高时,过程渣不易控制易发生喷溅,当铁水Si 数超过0.5%时,喷溅率直线上升。
5、拉碳时火焰判断不准,易拉高碳,点吹时降碳量和升温速度相比单渣法要低,由于留渣造成热平衡不好计算且留渣火焰相比单渣法时火焰亮,温度控制难度加大,需要特别注意。
- 1、下载文档前请自行甄别文档内容的完整性,平台不提供额外的编辑、内容补充、找答案等附加服务。
- 2、"仅部分预览"的文档,不可在线预览部分如存在完整性等问题,可反馈申请退款(可完整预览的文档不适用该条件!)。
- 3、如文档侵犯您的权益,请联系客服反馈,我们会尽快为您处理(人工客服工作时间:9:00-18:30)。
转炉留渣操作原因与注意事项
一、转炉留渣操作可以极大降低原料消耗,在吹炼初期可以快速成渣,有利于提高生产率,因而推广应用的潜力很大,但转炉留渣操作易发生大喷溅,限制了其应用。
二、分析认为需要注意以下几点,可以使留渣操作得到切实可行:
1、安全问题:兑铁时喷溅,因此所留的炉渣应确保:一是温度不能太高(≤1500℃),二是溅渣时间必须保证,因为留渣操作一般与溅渣护炉并用,必要时要加入一定量的改质剂稠渣。
2、初期渣化的早,尤其是前期低温时易发生喷溅,随之而来发生返干现象,导致沾枪沾罩操作困难,应注意。
3、开吹时打火困难,可以采用前后摇炉或者先点吹30-40s再加废钢的办法。
4、吹气渣化得早,前期渣来得迅速,低温炉渣容易从炉口涌出,特别是吹炼到约6分钟时,压料后易“返干”,特别是Si数低时更明显,而铁水Si含量高时,过程渣不易控制易发生喷溅,当铁水Si数超过%时,喷溅率直线上升。
5、拉碳时火焰判断不准,易拉高碳,点吹时降碳量和升温速度相比单渣法要低,由于留渣造成热平衡不好计算且留渣火焰相比单渣法时火焰亮,温度控制难度加大,需要特别注意。