氧气转炉留渣-冶金之家
【doc】转炉炼钢瘤渣操作初探

转炉炼钢瘤渣操作初探24江苏冶金?1991第6期?转炉炼钢留渣操作初探张义才(南京钢铁厂)1.前言氧气顶吹转一的终渣,具有高温,高碱度和较高的含铁量.出钢时,将部分炉渣茸F参与下一炉的炼钢反应,这种不完全的渣钢逆流方式,不仅加速早期成渣,促进脱磷,保护炉衬,而且节约石灰,降低金属料损失,并使废钢比提高.但是,具有高温高氧化性的终渣,在兑铁时,与铁水进行剧烈的碳氧反应,可能产生爆发性喷渣,又使人被迫放卉这种操作.然而,向留渣中兑铁,并非必然发生喷渣现象,只有达到某种条件l【寸才能出现.本文从热力学方面探讨喷渡条件,根据试验制定了适合的处埋方式,从而保证了留渣操作的安全,获得了较好的冶金效果.2.安全留渣操作的热力学条件留渣操作兑铁时发生的喷渣是铁水中的碳与-渣中的FeO反应急烈,产生大量的CO所引起的,只要抑制碳氧反应的进行,就-fI避免喷洒现象的Ⅲ现.2.I影响碳氧反应的热力学条件m留的炉内兑铋时,铁水冲击炉渣.在铁水与渣的接艇界面上,渣中(∑FeO)将铁水中转移并吸热:fFco).=f『0l转移到铁水中的[o],将列铁水中的[c】, :si],[Mn],[P],[sl等反应.枉熔池温度较低时,则[Sil,[Mn]5~q:【c]而氧化,尤其是si劬氧化抑制了脱碳反应的进行:[s+2[0】=(SiO,)△G.=一139300+53.55T(1)[c]+【O{co}.△G.一一5150—9.48Tf2)将(1)与(2)式联立解出:(SiO)+2[c】=2{co}+【Si]△G.128600+72.51Tf3)AG~-AGo+RTl:△G.as.o.'a蚓+RTln(4)a?f?【%c】Slu】南钢高炉铁水[C]≈4.O%,[Si】=O.6-- O.8%(汁算取0.6%),[Mn]=0.11~O.31%,[P]=0.10--029%,[S】=0.015~O.036%,温度为1250-~l35O℃.-计算时忽略Mn,P,S对C,Si活度的影.响:Igrs.=c?[~/osil+~c,?【%c】:0.11×0.6+0.18×4.0=0.786Igrc=《?[%q+姥?[%si]=0.14×4.0+0.08×0.6=0608则△G=128600—78.53T+9—5TIgPc0—4.575Tlga(5)l"2当△G>0时,则兑铁时不会发生[C]一[0】反应.由(5)式可知:影响兑铁时的碳氧反应的因素为渣的a和炉气的l"2CO分2.2渣中SO,的影响南钢转炉终渣成份见表1.将其近似地看作CaO—SiO2-FeO三元渣系,拆合成份为ZFeO:l1.28~31.53%,CaO:49.38~70.35%,SiO一:12.66~24.62%,B1991第6期?江苏冶金,?25?:查得a啪.=.?..~.-.,极少数炉次as一0.03(见图1).转炉终渣成份(%)表1成份EF*O.$io2CaoMgOAl3P205Mn0B捩动lO.28lo4155l691.000.801.0028范围—29瑚一20.0~霓87~58S~4.00~3.20~2.53~4.1 缓.在分压0.01MPa~0.04MPa范围内,临界温度上升速率较块.图JCa-SiOz'Fd01600E下等ag..与渣组成关系按(5)式计算:a=o.oo1$i02/"G=128600—64.81r,+9.15TlgP∞as∞0.0l△G=128600—69.38T+9.15TlgP∞a$io20.03△G128600—71,56T+9.15TIgPco提高炉渣碱度或降低渣温,都将使al2进一步降低,使铁水中[f]对[c】与炉渣间的反应的抑制作用增强,将其热力学的临界温度线提高(图2).2.3炉气中Pc.的影响按式(5)计算绘制的[c卜[0】反应临界温度图(图2).炉气的Pco每增加0.01MPa,其临界温度增加1O~50"C,随着Pc0的增加,其临界温度上升速率减M-囤2妒气.∞对[c卜[0】反应临界温度的影响3.留渣处理效果分析根据热力学计算,对留渣采用焦碳(煤粉)预还原加石灰(自云石),先加废钢的提高炉气Pc0.降低炉渣温度的处理方式. 3.1留渣处理试验的工艺过程上炉出钢过程中取渣样,测温一出钢毕,炉内加焦碳粒一炉体前后45.晃动一取炉气样,取渣样一加石灰(或白云石)一炉体前后45.晃动一取渣样一加废钢一缓慢兑铁水一吹炼前期每隔2分钟倒炉取渣样,测温,取钢样一常规冶炼.3.2加焦碳处理的炉气Pco变化转炉出钢后,炉气的Po0≈0.01MPa;对留渣加焦碳处理时,它与渣中∑FeO反应生成CO,使炉气中Pc0提高.分组试验表明:炉内加入20~30Kg焦碳粒,0,5~1分钟后取炉气分析,Po0:0.0750.085MPa,再增加焦碳,只起到炉渣稠化-1991第6期-江苏冶金?27?形成好的熔渣;处理留渣的石灰,在留渣中被预热,并为FenOm浸蚀,在冶炼初期提前熔化,使早期炉渣B在l~2rain内即达到2以上,前期炉渣的泡沫稳定性降低,从而避免了碳强烈氧化开始时发生的低温喷渣现象:而对采用石灰生烧较严重的南钢转炉,未留渣炉次通常采用很软吹的铁质成渣路线以促使石灰早化,而吹至脱sj基本完成时,B仍低于1.5(表1).FeO/SiO2高达1.9(平均),使脱碳开始时的低温喷渣现象较为严重.初期成渣效果表2操作韧期碱度BfE—v—,o一前期米方式2min4jnISiO2喷趋卑t.不留渣1.叫5l41—9一~39.5%I1—5~2?2留渣2.01.,o}04.2前期脱磷及终点情况开吹就具有较高碱度的熔渣和石灰的提前熔化,冶炼前期去磷效果比不留渣炉次有显着提高.从图5看出:未留遗炉次,吹炼4rain时,[P】绔为0.080%;至6分钟时仍太于0.06%:而留渣炉次吹炼4rain时[P】约为0.039%,至6min时为0.030%左右.由于留渣炉次的前期有效去P,使冶炼后期完全能够做到脱P 保碳,避免拉后吹造成的钢水过氧化现象同时使倒炉次数减少,从开吹至终点的总时间缩短1~2min.rain图5前期熔化的变化43石友用量减少高碱度的留渣参与下炉冶炼,显着地降低了石灰,萤石等散状料用量.留渣量一般为总渣量的l/2左右.实际石灰节约l/3左右,即石灰吨钢用量减少30~35Kg(采用石灰作冷却荆炉次除外).4.4减少热支出,有利提高废钢比留渣量每炉约1.5t,石灰节约600Kg/炉则其节支的热耗为4952290KJ,可多吃废钢3000Kg,即在同等条件下吨钢废钢比比不留渣炉次提高130Kg左右.4.5金属收得率提高未倒出的留渣其TF~在冶炼时得到回收:因石灰用量减少而进一步降低的渣量及喷溅(特别是碳强烈氧化开始时的低温喷渣)的明显减少,使金属损失减少.计算及实际统计表明.留钢操作可使吨钢金属料消耗减少20Kg左右. 4.6炉衬浸蚀翦期炉渣的高碱度,特别是采用白云石处理留渣炉次的较高MgO 含量,将减少前期炉渣对炉村的谩蚀:高温熔液在炉内停留时间的缩短及氧化性降低, 减轻炉衬损失:但在实际生产中,炉龄并无明显提高,其原因有等进一步探索.s.结论5.1采用高炉铁水的转炉炼钢,安全留渣操作的热力学临界温度为l36O℃:降低口.或提高,c0可使I临界温度提高.5.2安全留渣操作的工艺方法:向留渣中加入20~30Kg/炉焦碳粒提高Pco.石灰200250Kg/t渣,先加废钢冷却捌化炉渣.5.3留渣渣操作促进快速成渣,消除前期末的低温喷渣现象,做到脱磷保碳.避免终点钢水过氧化,5.4节约石灰30kg/t?钢.降低金属料耗20kg/t-钢.可使废钢比显着提高.。
转炉留渣操作技术
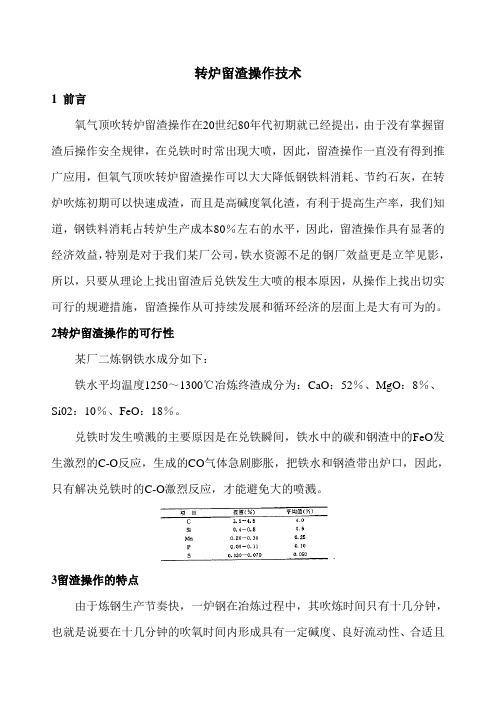
转炉留渣操作技术1 前言氧气顶吹转炉留渣操作在20世纪80年代初期就已经提出,由于没有掌握留渣后操作安全规律,在兑铁时时常出现大喷,因此,留渣操作一直没有得到推广应用,但氧气顶吹转炉留渣操作可以大大降低钢铁料消耗、节约石灰,在转炉吹炼初期可以快速成渣,而且是高碱度氧化渣,有利于提高生产率,我们知道,钢铁料消耗占转炉生产成本80%左右的水平,因此,留渣操作具有显著的经济效益,特别是对于我们某厂公司,铁水资源不足的钢厂效益更是立竿见影,所以,只要从理论上找出留渣后兑铁发生大喷的根本原因,从操作上找出切实可行的规避措施,留渣操作从可持续发展和循环经济的层面上是大有可为的。
2转炉留渣操作的可行性某厂二炼钢铁水成分如下:铁水平均温度1250~1300℃冶炼终渣成分为:CaO:52%、MgO:8%、Si02:10%、FeO:18%。
兑铁时发生喷溅的主要原因是在兑铁瞬间,铁水中的碳和钢渣中的FeO发生激烈的C-O反应,生成的CO气体急剧膨胀,把铁水和钢渣带出炉口,因此,只有解决兑铁时的C-O激烈反应,才能避免大的喷溅。
3留渣操作的特点由于炼钢生产节奏快,一炉钢在冶炼过程中,其吹炼时间只有十几分钟,也就是说要在十几分钟的吹氧时间内形成具有一定碱度、良好流动性、合适且TFe和MgO含量正常泡沫化的炉渣,以保证冶炼成分和温度同时双命中的钢水,并减少对炉衬的侵蚀,留渣操作贯穿于炼钢整个冶炼周期,主要是靠所留炉渣的物理热和炉渣化学性能,使其具有迅速参与反应、并促进前期炉渣的快速形成、提高去除P、S的效率、节省石灰用量。
3.1有利于去磷在氧气顶吹转炉中,磷的氧化是在炉渣-金属界面中进行的,其反应式为:生成的磷酸铁在高温下极其不稳定,它可以重新分解生成P2O5,而P2O5是不稳定的化合物,因此,仅靠生成P2O5。
不能去除磷,但P2O5是酸性化合物,若用碱性化合物与其结合生成稳定的化合物可以去除。
研究认为,在碱性渣中P2O5与CaO形成稳定的(CaO)x P2O5型的化合物,其中x为3或4,因此,操作中需加入石灰,使其生成稳定的化合物3CaO· P2O5。
首秦100t氧气转炉“留渣双渣”炼钢工艺实践
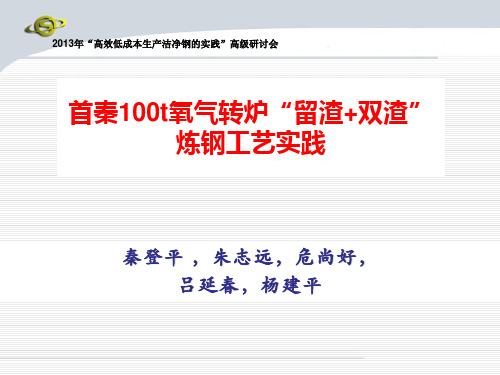
SGRS工艺应用效果
➢渣量的确定— 理论计算渣量
使用普通活性石灰,铁水Si含量在0.50%左右, SGRS工艺渣量70-80kg/t,普通工艺渣量100-120kg/t。 SGRS工艺比普通工艺降低35kg/t,降低比例31.8%。
➢渣量的确定—铁水称量实测渣量
使用普通石灰,铁水Si含量在0.50%左右,SGRS工 艺渣量75kg/t,普通工艺渣量108kg/t。SGRS工艺比普通 工艺降低33kg/t,降低比例31.4%。 渣量的降低和Tfe含量的变化合计钢铁料消耗降低8.25 kg/t钢。
脱磷期回收工艺:
CO浓度>30%,O2<1.5%; 下枪吹炼≥2分钟; 达标时间≤3.5分钟; 氧枪下枪吹炼(氧枪在开氧点以下) 罩裙低位;
SGRS转炉煤气的回收技术应用
脱碳期回收工艺技术优化 脱碳期吹炼前期转炉煤气发生特点: •前期CO浓度上升很快,且波动小 •O2浓度下降速率较快,稳定 前期达标即回收,CO>30%,O2<1.5%,无时间和延时限制; 回收末期控制条件与常规冶炼工艺相同;
脱磷期结束倒渣控制研究
脱磷期结束倒渣量,t
6
5
4
3
2
1
0
0
5
10
15
脱磷期结束倒渣时间,min
倒渣时间增加到一定程度后,倒渣量增加不再显著。
脱磷期结束倒渣控制研究
25.0
出钢后倒渣
20.0
脱磷倒渣
15.0
12.7
倒渣量,t
10.0
5.0 4.3 6.5 7.1 7.0 7.3 6.8 7.2
0.0 第一炉 第二炉 第三炉 第四炉 第五炉 第六炉 第七炉 SGRS循环周期
氧气转炉“留渣+ 双渣” 炼钢工艺技术研究
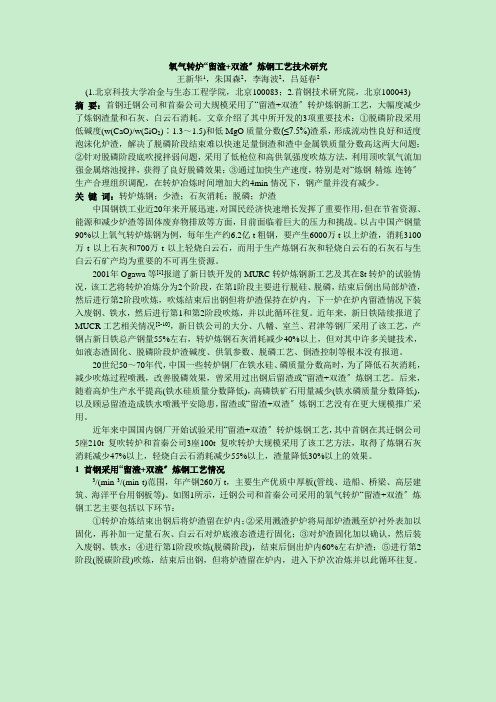
氧气转炉“留渣+双渣〞炼钢工艺技术研究王新华1,朱国森2,李海波2,吕延春2(1.北京科技大学冶金与生态工程学院,北京100083;2.首钢技术研究院,北京100043)摘要:首钢迁钢公司和首秦公司大规模采用了“留渣+双渣〞转炉炼钢新工艺,大幅度减少了炼钢渣量和石灰、白云石消耗。
文章介绍了其中所开发的3项重要技术:①脱磷阶段采用低碱度(w(CaO)/w(SiO2)∶1.3~1.5)和低MgO质量分数(≤7.5%)渣系,形成流动性良好和适度泡沫化炉渣,解决了脱磷阶段结束难以快速足量倒渣和渣中金属铁质量分数高这两大问题;②针对脱磷阶段底吹搅拌弱问题,采用了低枪位和高供氧强度吹炼方法,利用顶吹氧气流加强金属熔池搅拌,获得了良好脱磷效果;③通过加快生产速度,特别是对“炼钢-精炼-连铸〞生产合理组织调配,在转炉冶炼时间增加大约4min情况下,钢产量并没有减少。
关键词:转炉炼钢;少渣;石灰消耗;脱磷;炉渣中国钢铁工业近20年来开展迅速,对国民经济快速增长发挥了重要作用,但在节省资源、能源和减少炉渣等固体废弃物排放等方面,目前面临着巨大的压力和挑战。
以占中国产钢量90%以上氧气转炉炼钢为例,每年生产约6.2亿t粗钢,要产生6000万t以上炉渣,消耗3100万t以上石灰和700万t以上轻烧白云石,而用于生产炼钢石灰和轻烧白云石的石灰石与生白云石矿产均为重要的不可再生资源。
2001年Ogawa等[1]报道了新日铁开发的MURC转炉炼钢新工艺及其在8t转炉的试验情况,该工艺将转炉冶炼分为2个阶段,在第1阶段主要进行脱硅、脱磷,结束后倒出局部炉渣,然后进行第2阶段吹炼,吹炼结束后出钢但将炉渣保持在炉内,下一炉在炉内留渣情况下装入废钢、铁水,然后进行第1和第2阶段吹炼,并以此循环往复。
近年来,新日铁陆续报道了MUCR工艺相关情况[2-10],新日铁公司的大分、八幡、室兰、君津等钢厂采用了该工艺,产钢占新日铁总产钢量55%左右,转炉炼钢石灰消耗减少40%以上,但对其中许多关键技术,如液态渣固化、脱磷阶段炉渣碱度、供氧参数、脱磷工艺、倒渣控制等根本没有报道。
转炉“留渣+双渣”少渣炼钢工艺实践

转炉“留渣+双渣”少渣炼钢工艺实践李伟东;杨明;何海龙;刘鹏飞;乔冠男【摘要】The key technologies on steelmaking based on the slag reserving and duplex slag process in converter in General Steelmaking Plant of Angang Steel Co., Ltd. are introduced, in-cluding slag reserving and slag solidifying technology, slag fluidity controlling and high efficient dephosphorization technology, fast slagging sufficiently and deslagging technology from molten iron, control technology for slag getting dry and content of FeO in final slag and fast operation technolo-gy based on slag reserving and duplex slag process. After these technologies are used the cost is reduced by 12.19 yuan RMB per ton steel.%介绍了鞍钢股份有限公司炼钢总厂转炉“留渣+双渣”工艺的关键技术,包括留渣及炉渣固化技术、炉渣流动性控制及高效脱磷技术、快速足量放渣及渣铁分离技术、炉渣返干控制及终渣FeO控制技术以及“留渣+双渣”快速生产技术,采用这些技术后,吨钢成本降低12.19元。
【期刊名称】《鞍钢技术》【年(卷),期】2015(000)005【总页数】5页(P41-45)【关键词】转炉;少渣;留渣;双渣;脱磷【作者】李伟东;杨明;何海龙;刘鹏飞;乔冠男【作者单位】鞍钢股份有限公司炼钢总厂,辽宁鞍山114021;鞍钢股份有限公司科技质量部,辽宁鞍山114021;鞍钢股份有限公司炼钢总厂,辽宁鞍山114021;鞍钢股份有限公司炼钢总厂,辽宁鞍山114021;鞍钢股份有限公司炼钢总厂,辽宁鞍山114021【正文语种】中文【中图分类】TF777少渣炼钢是指转炉冶炼总渣量极少化的一种炼钢工艺。
氧气顶吹转炉炼钢挡渣出钢
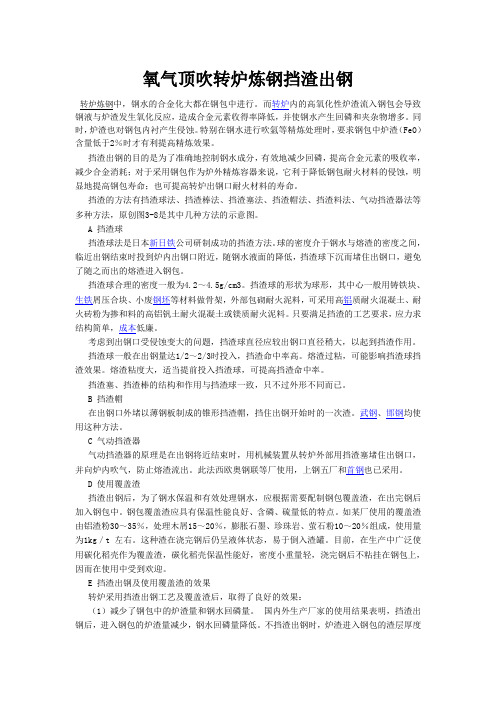
氧气顶吹转炉炼钢挡渣出钢转炉炼钢中,钢水的合金化大都在钢包中进行。
而转炉内的高氧化性炉渣流入钢包会导致钢液与炉渣发生氧化反应,造成合金元素收得率降低,并使钢水产生回磷和夹杂物增多。
同时,炉渣也对钢包内衬产生侵蚀。
特别在钢水进行吹氩等精炼处理时,要求钢包中炉渣(FeO)含量低于2%时才有利提高精炼效果。
挡渣出钢的目的是为了准确地控制钢水成分,有效地减少回磷,提高合金元素的吸收率,减少合金消耗;对于采用钢包作为炉外精炼容器来说,它利于降低钢包耐火材料的侵蚀,明显地提高钢包寿命;也可提高转炉出钢口耐火材料的寿命。
挡渣的方法有挡渣球法、挡渣棒法、挡渣塞法、挡渣帽法、挡渣料法、气动挡渣器法等多种方法,原创图3-8是其中几种方法的示意图。
A 挡渣球挡渣球法是日本新日铁公司研制成功的挡渣方法。
球的密度介于钢水与熔渣的密度之间,临近出钢结束时投到炉内出钢口附近,随钢水液面的降低,挡渣球下沉而堵住出钢口,避免了随之而出的熔渣进入钢包。
挡渣球合理的密度一般为4.2~4.5g/cm3。
挡渣球的形状为球形,其中心一般用铸铁块、生铁屑压合块、小废钢坯等材料做骨架,外部包砌耐火泥料,可采用高铝质耐火混凝土、耐火砖粉为掺和料的高铝钒土耐火混凝土或镁质耐火泥料。
只要满足挡渣的工艺要求,应力求结构简单,成本低廉。
考虑到出钢口受侵蚀变大的问题,挡渣球直径应较出钢口直径稍大,以起到挡渣作用。
挡渣球一般在出钢量达1/2~2/3时投入,挡渣命中率高。
熔渣过粘,可能影响挡渣球挡渣效果。
熔渣粘度大,适当提前投入挡渣球,可提高挡渣命中率。
挡渣塞、挡渣棒的结构和作用与挡渣球一致,只不过外形不同而已。
B 挡渣帽在出钢口外堵以薄钢板制成的锥形挡渣帽,挡住出钢开始时的一次渣。
武钢、邯钢均使用这种方法。
C 气动挡渣器气动挡渣器的原理是在出钢将近结束时,用机械装置从转炉外部用挡渣塞堵住出钢口,并向炉内吹气,防止熔渣流出。
此法西欧奥钢联等厂使用,上钢五厂和首钢也已采用。
氧气转炉“留渣+双渣”炼钢工艺技术131210王新华
新工艺基本原理
在温度升至对脱磷不利前尽量将炉渣倒出, 加入渣料进行第二阶段吹炼。 冶炼结束炉渣在高温下 已基本不具备去磷能力。
下炉吹炼前期,由于温度低, 所留炉渣重新具备去磷能力。
11
MURC工艺能够显著降低石灰耗量
T. Matsumiya, et al, 10th Japan-China Symposium on Science and Technology of Iron and Steel, 2004, Chiba
6
渣量比较
工艺A:传统炼钢工艺; 工艺B:铁水罐脱磷预处理; 工艺C:转炉铁水脱磷预处理; 工艺D:转炉铁水预处理,80% 脱碳转炉渣返回脱磷转 炉利用。
S. Kitamura, et al., 9th China-Japan Symposium on Science and Technology of Iron and Steel, 2001, Xian 7
SGRS工艺:
SGRS工艺应用情况
• • • 迁钢和首秦公司采用SGRS工艺产钢比率分别达到了79.1% 和81.1% ; 吨钢石灰消耗分别降低了47.3%和41.1% (迁钢降低至 22.0kg/t,首秦降低至37.2kg/t); 轻烧白云石消耗分别降低了55.2%和56.6% (迁钢降低至 8.0kg/t,首秦降低至8.2kg/t);
新日铁开发“MURC”炼钢工艺
岩崎正樹,松尾充高,製鋼技術開発の歩みと今後の展望,新日鉄技報, 2011 ,第 391 号,p88-93 8 小川雄司,転炉を用いた脱りん脱炭連続処理プロセスの開発,鉄と鋼, 87(2001) , p21-28
新日铁炼钢工厂
1. 君津製鉄所(950万吨):
一炼钢厂: 220t转炉×3 二炼钢厂: 300t转炉×2 炼钢厂: 380t转炉×3
转炉定量留渣-溅渣-全留渣的工艺实践
9.96——降低石灰消耗,kg/吨钢
0.4 ——石灰成本,元/kg 0.8 ——钢铁料消耗与留渣溅渣率相关系数
0.4 ——项目本身贡献系数
四、溅渣护炉效果与经济效益
4.3经济效益
通过应用转炉定量留渣溅渣技术研究成果后,溅渣效果较好,降低补 炉耐材消耗。 按降低耐材消耗0.49元/吨钢计算,年可降低耐材消耗效益: 200×1.53×0.24×0.4=29.38万元/年 其中: 200 ——年钢产量,万吨/年
8.4 ——降低钢铁料消耗,kg/吨钢
2.75 ——钢铁料成本,元/kg 0.7 ——钢铁料消耗与留渣溅渣率相关系数
0.4 ——项目本身贡献系数
四、溅渣护炉效果与经济效益
4.3经济效益
溅渣后可利用热态渣提高转炉化渣效果,同时,可充分提高转炉初期 渣碱度,从而提高转炉脱磷效果,达到降低石灰消耗的目的; 按按降低石灰消耗9.96kg/吨钢计算,年可降低石灰消耗效益: 200×9.96×0.4×0.8×0.4=254.97万元/年 其中: 200 ——年钢产量,万吨/年
渣制度、温度制度和终点控制的优化,成功解决传统全留渣工艺存在的 问题。
三、定量留渣-溅渣-全留渣的工艺实践
3.5定量留渣-溅渣-全留渣工艺制度
表9 定量留渣-溅渣-全留渣工艺制度
溅渣前渣量控制 渣量适中(根据 炉体侵蚀情况调 整适当转炉倾角 ,保证留渣量2~ 2.5)且稳定
溅渣压力 Mpa
溅渣时间 min
溅渣枪位(标尺) m
全留渣控制
1.1~1.3
1.5-2.5
1.5→0,交变溅渣 枪位
溅渣完毕全 部留渣
四、溅渣护炉效果与经济效益
4.1 溅渣护炉效果
表10 溅渣护炉效果对比
100t转炉留渣操作工艺的研究与实践
设: 。 = 0 . 9 x l O l ( K P a ) ( 炉气 中 9 0 %为 c 0气体 ) ( F e 0 ) = 0 . 1 7 将上列数据代入得 : <1 1 2 0 0 K= 8 4 7 o C 由此可 以看 出在兑铁时不 发生大喷 的必要条件是温度低 于 8 4 7 ℃ 即可 , 同时降低渣中 F e O的浓度也是抑制此反应最直 接有效 的办法 。 在生 产操作 上 . 可以延长溅渣护 炉的时间 . 在溅渣 过程中加入 白云石
的研 究, 优化 了留渣冶炼的吹 炼制度 、 造渣制度、 温度 制度等 , 使 冶炼过程平稳顺行 , 减少了因大渣量导致大喷 的发 生。 实践证 明, 实施 留渣操 作 对转 炉冶炼时的初 期化 渣和脱磷 十分有利 , 不仅 大大增强 了脱磷 效果 , 还可 以 提 高出钢碳 , 从 而降低 了石灰消耗 、 脱 氧剂消耗、 降低钢铁料 消 耗、 提 高炉龄和 出钢 口 龄, 取得 了显著的经济效益。
中( c a 0 ) 含量提高。这样 3 ( F e o ) ・ ( P 2 0 5 ) 不稳定 。有如下反应 : 4 ( C a O ) + 3 ( F e O ) ・ ( P 2 05 ) = 4 ( C a 0 ) ・ ( P 2 O s ) + 3 ( F e O ) 综合上述两个 反应方程式得到 :
2 0 1 3 年2 3 期
科技 一向导
◇ 科技论坛◇
l O O t 转炉留渣操作工艺的研究与实践
时伟伟 ( 福建省三钢< 集团> 有限责任公司 福建 三明 3 6 5 0 0 0 )
【 摘 要】 本文介 绍了福建三钢一炼钢厂 1 0 0 Байду номын сангаас 复吹转炉的 留渣双渣操作 工艺。 针 对留渣操作 台 炼 中的喷溅, 氧枪结冷钢等 问题进行 了深入
氧枪刮渣器在转炉氧枪中的应用
氧枪刮渣器在转炉氧枪中的应用摘要:本文分析了氧气顶吹转炉氧枪粘渣机理,阐述了氧枪粘渣的危害及处理方法,介绍了氧枪自动刮渣器的应用。
关键词:氧枪粘渣氧枪刮渣器一、前言韶钢转炉炼钢部目前有3座120t和2座130t顶底复吹转炉,氧枪粘渣是一直存在的问题,在生产过程中,当氧枪粘渣时,不但会造成氧枪局部散热条件恶化,容易被烧坏,而且还会造成提枪困难,容易损坏氮封口;严重时还会造成氧枪提不出炉口,转炉炼钢无法正常吹炼。
主要存在的问题如下:1.氧枪粘渣造成枪体局部散热,导致烧枪,氧枪更换频率高。
2.转炉氧枪发生粘枪,枪体粘的钢渣人工很难清理,在生产过程被迫移枪,严重时因粘钢枪体提不出氮封孔,不得不采取割枪措施。
3.当喷头和喷头以上部位粘钢,发生回火,导致氧枪外套管烧穿漏水,被迫换枪。
二、氧枪粘渣的分析1.氧枪粘渣的主要原因①冶炼中当采用低枪位或较高氧压操作时,氧气流股对熔池面有较大冲击力,熔池被打成深坑,此时面积小冲击深度大,一部分金属液被粉碎随着反射气流从深坑中喷溅出来粘结氧枪,这是氧枪粘渣的一个原因。
②当冶炼中采用高枪位或较低氧压操作时,氧气流股对熔池面冲击较小,冲击深度也小,其冲击力在熔池表面形成一个浅而大的坑,此时熔池搅拌弱,金属液传氧慢,脱碳速度低,但是渣中氧化铁含量增加,引起泡末渣喷溅粘结氧枪,这是氧枪粘渣的又一个原因。
③转炉溅渣护炉技术对氧枪的影响;在吹溅过程中不可避免地会在氧枪外层钢管上粘附钢渣。
如果不能及时将其清除,随着冶炼炉数的增加,每溅一次渣便会使已经粘渣的氧枪上的渣层厚度增加,如同“滚雪球”一样,致使氧枪粘渣愈来愈厚,从而导致氧枪粘渣,有时仅能吹炼几炉钢就因为粘渣太厚而不得不更换氧枪,由此直接带来的问题是氧枪消耗成本迅速增加。
2.粘结渣的主要成分氧枪粘结渣成分复杂,基本由(CaO、MgO 、MnO 、FeO 、Al2O3 、Fe2O3 、SiO2 、S)等组成。
大多数炉渣组织比较松散,硬度较高,碎性大,受压或受冲击都比较容易脱落。
- 1、下载文档前请自行甄别文档内容的完整性,平台不提供额外的编辑、内容补充、找答案等附加服务。
- 2、"仅部分预览"的文档,不可在线预览部分如存在完整性等问题,可反馈申请退款(可完整预览的文档不适用该条件!)。
- 3、如文档侵犯您的权益,请联系客服反馈,我们会尽快为您处理(人工客服工作时间:9:00-18:30)。
氧气转炉“留渣+双渣”炼钢工艺技术研究王新华1,朱国森2,李海波2,吕延春2(1.北京科技大学冶金与生态工程学院,北京100083;2.首钢技术研究院,北京100043)摘要:首钢迁钢公司和首秦公司大规模采用了“留渣+双渣”转炉炼钢新工艺,大幅度减少了炼钢渣量和石灰、白云石消耗。
文章介绍了其中所开发的3项重要技术:①脱磷阶段采用低碱度(w(CaO)/w(SiO2)∶1.3~1.5)和低MgO质量分数(≤7.5%)渣系,形成流动性良好和适度泡沫化炉渣,解决了脱磷阶段结束难以快速足量倒渣和渣中金属铁质量分数高这两大问题;②针对脱磷阶段底吹搅拌弱问题,采用了低枪位和高供氧强度吹炼方法,利用顶吹氧气流加强金属熔池搅拌,获得了良好脱磷效果;③通过加快生产速度,特别是对“炼钢-精炼-连铸”生产合理组织调配,在转炉冶炼时间增加大约4min情况下,钢产量并没有减少。
关键词:转炉炼钢;少渣;石灰消耗;脱磷;炉渣中国钢铁工业近20年来发展迅速,对国民经济快速增长发挥了重要作用,但在节省资源、能源和减少炉渣等固体废弃物排放等方面,目前面临着巨大的压力和挑战。
以占中国产钢量90%以上氧气转炉炼钢为例,每年生产约6.2亿t粗钢,要产生6000万t以上炉渣,消耗3100万t以上石灰和700万t以上轻烧白云石,而用于生产炼钢石灰和轻烧白云石的石灰石与生白云石矿产均为重要的不可再生资源。
2001年Ogawa等[1]报道了新日铁开发的MURC转炉炼钢新工艺及其在8t转炉的试验情况,该工艺将转炉冶炼分为2个阶段,在第1阶段主要进行脱硅、脱磷,结束后倒出部分炉渣,然后进行第2阶段吹炼,吹炼结束后出钢但将炉渣保持在炉内,下一炉在炉内留渣情况下装入废钢、铁水,然后进行第1和第2阶段吹炼,并以此循环往复。
近年来,新日铁陆续报道了MUCR工艺相关情况[2-10],新日铁公司的大分、八幡、室兰、君津等钢厂采用了该工艺,产钢占新日铁总产钢量55%左右,转炉炼钢石灰消耗减少40%以上,但对其中许多关键技术,如液态渣固化、脱磷阶段炉渣碱度、供氧参数、脱磷工艺、倒渣控制等基本没有报道。
20世纪50~70年代,中国一些转炉钢厂在铁水硅、磷质量分数高时,为了降低石灰消耗,减少吹炼过程喷溅,改善脱磷效果,曾采用过出钢后留渣或“留渣+双渣”炼钢工艺。
后来,随着高炉生产水平提高(铁水硅质量分数降低),高磷铁矿石用量减少(铁水磷质量分数降低),以及顾忌留渣造成铁水喷溅安全隐患,留渣或“留渣+双渣”炼钢工艺没有在更大规模推广采用。
近年来中国国内钢厂开始试验采用“留渣+双渣”转炉炼钢工艺,其中首钢在其迁钢公司5座210t复吹转炉和首秦公司3座100t复吹转炉大规模采用了该工艺方法,取得了炼钢石灰消耗减少47%以上,轻烧白云石消耗减少55%以上,渣量降低30%以上的效果。
1 首钢采用“留渣+双渣”炼钢工艺情况首钢迁钢公司第一和第二炼钢分厂共拥有5座210t顶底复吹转炉,氧枪采用5孔喷头,马赫数为2.0,供氧强度在3.3~3.4m3/(min·t)范围,年产钢810万t,主要产品包括汽车、家电用冷轧钢板、电工钢板、管线钢板、容器板、造船板等。
首秦公司拥有3座100t顶底复吹转炉,氧枪采用4孔喷头,马赫数为2.0,供氧强度在3.6~3.8m3/(min·t)范围,年产钢260万t,主要生产优质中厚板(管线、造船、桥梁、高层建筑、海洋平台用钢板等)。
如图1所示,迁钢公司和首秦公司采用的氧气转炉“留渣+双渣”炼钢工艺主要包括以下环节:①转炉冶炼结束出钢后将炉渣留在炉内;②采用溅渣护炉将部分炉渣溅至炉衬表面加以固化,再补加一定量石灰、白云石对炉底液态渣进行固化;③对炉渣固化加以确认,然后装入废钢、铁水;④进行第1阶段吹炼(脱磷阶段),结束后倒出炉内60%左右炉渣;⑤进行第2阶段(脱碳阶段)吹炼,结束后出钢,但将炉渣留在炉内,进入下炉次冶炼并以此循环往复。
炼钢脱磷反应可由(1)式表示,图2为根据(2)式[10-11]计算得到的脱磷反应平衡常数与温度的关系。
可以看到,温度对脱磷反应的影响非常显著,当温度由1680℃降低至1350℃时,脱磷反应平衡常数可大幅度增加6个数量级以上。
“留渣+双渣”炼钢工艺的基本原理便是利用转炉冶炼前期温度低这一有利于脱磷反应热力学条件,将上炉终渣(由于温度高已基本不具备脱磷能力),用于下炉吹炼初期(由于温度低,炉渣重新具备脱磷能力)进行脱磷,并在温度上升至对脱磷不利之前,将炉渣部分倒出,然后加入少量渣料造渣进行第2阶段吹炼(可进一步脱磷)。
由于上炉炉渣可以被下炉再利用,因而能够大幅度减少炼钢石灰、轻烧白云石等原材料消耗和炼钢渣量。
根据该工艺能够显著减少炼钢渣量的特点,首钢将其简称为“SGRS”工艺(SlagGenerationReducedSteelmaking)。
SGRS炼钢工艺除能够减少石灰、轻烧白云石等原材料消耗和炼钢渣量之外,还具有以下优点:①炼钢炉渣通常含14%~25%氧化铁,渣量减少因而可以降低钢铁料消耗;②常规炼钢工艺外排炉渣碱度高(大于3.0),渣中自由CaO质量分数多。
采用41SGRS工艺,外排炉渣主要为脱磷阶段的低碱度渣,因此可以简化炉渣处理;③常规工艺炼钢,出钢后留在炉内部分钢水随炉渣倒出,采用新工艺吹炼终点不倒渣,因而可以提高钢水收得率。
至2012年底,首钢迁钢公司和首秦公司采用SGRS工艺产钢比率分别达到了63.8%和81.5%,与常规转炉炼钢工艺相比,转炉炼钢石灰消耗分别降低了47.3%和48.5%(迁钢公司降低至22.0kg/t,首秦公司降低至32.1kg/t),轻烧白云石消耗分别降低了55.2%和70.0%(迁钢公司降低至8.0kg/t,首秦公司降低至5.7kg/t),转炉炼钢渣量分别减少了32.6%和30.7%,钢铁料消耗分别降低了6.517kg/t和8.250kg/t,取得了显著经济效益。
2 关键工艺技术2.1 脱磷阶段炉渣流动性控制与足量倒渣采用SGRS炼钢工艺,脱磷阶段结束后能否快速倒出足量炉渣具有重要意义。
如倒渣量不足,会出现:①炉内渣量逐炉蓄积,碱度不断增加,倒渣愈加困难的情况,最后导致SGRS工艺无法接续,循环被迫停止;②炉渣流动性会逐炉变差,渣中裹入金属铁珠量大,钢铁料消耗增加;③倒渣困难会增加冶炼时间,炉内渣量波动也会对吹炼过程控制稳定性造成很大影响。
能否快速倒出足量脱磷炉渣,主要取决于炉渣流动性控制,为此须做到:①炉渣充分熔化,不含未溶石灰颗粒以及MgO、2CaO·SiO2等高熔点析出相;②炉渣具有较低黏度;③适当提高脱磷阶段温度。
由图3所示CaO-SiO2-FeO系相图[11]可以看到,在SGRS工艺脱磷阶段炉渣氧化铁质量分数范围(9%~15%),为使炉渣全部熔化(均匀液相),炉渣碱度w(CaO)/w(SiO2)须控制在1.3以下。
考虑到渣中还含少量Al2O3、MnO等,能够适当扩大该三元系液相区范围,因此为使炉渣充分熔化,炉渣碱度不应超过1.5。
图4[11]为1400℃下CaO-SiO2-FeO系黏度值(Pa·s),可以看到,在脱磷阶段炉渣氧化铁质量分数9%~15%范围,当碱度在0.82~1.5范围时,炉渣具有较低的黏度(0.2~0.4Pa·s),而当碱度超过1.5时,等黏度线变得密集,黏度值随碱度增加而快速提高,炉渣流动性显著变差。
图5为迁钢公司210t转炉和首秦公司100t转炉采用SGRS炼钢工艺,脱磷阶段结束后倒渣量与炉渣碱度的关系。
可以看到,倒渣量随碱度降低而增加,当脱磷阶段炉渣碱度控制在1.5左右时,迁钢210t转炉倒渣量可大于8.0t,首秦100t转炉倒渣量可多于5.0t,保证了SGRS 工艺顺利稳定运行。
为了使炉渣具有良好流动性,还须对MgO质量分数进行严格控制。
图6为210t转炉脱磷阶段结束倒渣量与渣中MgO质量分数关系,当将MgO控制在7.5%以下时,倒渣量可在8t以上,能够满足SGRS稳定运行要求,为此规定对脱磷阶段炉渣MgO质量分数按低于7.5%控制。
这一MgO质量分数控制目标低于常规工艺初期渣MgO控制目标值,采用后并未发现对炉龄有不利影响。
采用了以上所述较低碱度和MgO质量分数渣系后,基本上解决了倒渣这一影响SGRS 工艺稳定运行的关键难题。
目前,迁钢210t转炉脱磷阶段倒渣量在6.0~12.5t(铁水[Si]质量分数变化影响),倒渣时间在4.0~5.0min;首秦100t转炉脱磷阶段倒渣量在4.0~8.0t,倒渣时间在3.0~4.5min。
2.2 脱磷阶段高效脱磷工艺技术采用SGRS炼钢工艺,由于所留炉渣中已含1.5%以上P2O5,而且为使炉渣流动性良好以快速足量倒渣,脱磷阶段必须采用较低碱度渣系,脱磷阶段脱磷难度显著加大。
而如果在脱磷阶段不能够充分脱磷,势必加重脱碳阶段的负担,严重时会造成终点钢水[P]不合格而必须进行后吹、补吹。
由(2)式给出的脱磷反应平衡常数式和高碳铁液中[P]的活度相互作用系数[12]、渣中P2O5活度系数[10],可得到磷在渣/铁间分配比的计算式(3),式中N(P2O5)为渣中P2O5克分子浓度,a[O]为铁液中氧活度。
在SGRS炼钢工艺的脱磷阶段,由于[C]质量分数高(3.3~3.8%),铁液中氧的活度a[O]由[C]控制。
由(4)和(5)式[2]给出的[C]-[O]反应平衡常数计算式和相关的活度相互作用系数eCC[11],计算得到的1330~1380℃范围铁液中氧的活度仅为0.00010~0.00015,将其代入(3)式计算得到的磷分配比(N(P2O5)/w([P])2)在10-5数量级,表明脱磷阶段在金属熔池内部脱磷反应基本不能进行。
但是,氧气转炉由于采用顶吹氧,即便铁液碳质量分数高,也可通过调整枪位、供氧速率等将渣中氧化铁控制在较高质量分数范围(8%~15%),进而将渣/铁界面氧活度控制在较高水平。
(7)式[2]和(8)式为(6)式所示Fe-O反应的标准自由能和铁液中氧活度与温度和炉渣氧化铁活度的关系,将(8)式代入(3)式,并取脱磷阶段铁水和炉渣的组成以及相关组元的活度数据[11](f[C]、a(FeO))等,可计算出在炉渣氧化铁含量为8%~15%情况下,磷的分配比(N(P2O5)/w([P])2)在165左右,表明在渣/铁界面脱磷反应可以进行。
由上述分析可知,采用SGRS工艺在脱磷阶段高效脱磷的关键是:①加强金属熔池搅拌,促进熔池内部[P]向渣/铁界面传输;②通过调整供氧或加入铁矿石、氧化铁皮等提高渣中氧化铁活度。
为保证较长的底吹元件寿命,国内顶底复吹转炉大多采用较低的底吹搅拌强度,迁钢公司、首秦公司炼钢转炉实际底吹强度在0.03~0.06m3/(min·t)。