mdf生产线现场配制液压油管酸洗方案
mdf生产线现场配制液压油管酸洗方案_
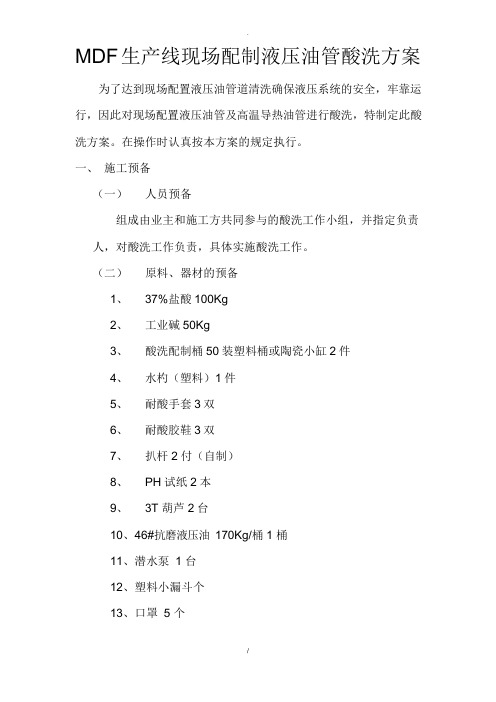
MDF 生产线现场配制液压油管酸洗方案为了达到现场配置液压油管道清洗确保液压系统的安全,牢靠运行,因此对现场配置液压油管及高温导热油管进行酸洗,特制定此酸洗方案。
在操作时认真按本方案的规定执行。
一、施工预备(一)人员预备组成由业主和施工方共同参与的酸洗工作小组,并指定负责人,对酸洗工作负责,具体实施酸洗工作。
(二)原料、器材的预备1、37%盐酸100Kg2、工业碱50Kg3、酸洗配制桶50 装塑料桶或陶瓷小缸2 件4、水杓(塑料)1 件5、耐酸手套3 双6、耐酸胶鞋3 双7、扒杆2 付(自制)8、PH 试纸2 本9、3T 葫芦2 台10、46#抗磨液压油170Kg/桶1 桶11、潜水泵1 台12、塑料小漏斗个13、口罩5 个14、小空压机 1 台(三)现场预备1、接通水源至主油管沟旁2、疏通或开拓室外排水通道3、制作盲板,加液漏斗和木塞4、清理施工现场,预备固定管道的垫木和抓钉5、接通压缩空气(四)现场施工1、拆除主油管直出口与设备联接口,用2 台链条葫芦将主油管吊在扒杆上,并使进油端尽可能向上倾斜。
进口端制作钢板漏斗及法兰,用螺栓加橡胶石棉板紧固。
下口端用盲板加垫紧固。
2、将全部现场配置已安装的油管全部拆卸,平摆在车间地面。
带弯头管道使其一端置于朝上,另一端加木塞楔紧。
直管一端加木塞,竖直置于压机地坑。
3、压机基坑注水,深度约100mm,并加入25Kg 经热水熔解成的碱液注入地坑。
4、配置酸洗液:按每百公斤37%浓度的盐酸加200~250公斤洁净水配制成酸洗液备用。
5、灌液:用塑料杓将已配制好的酸液经漏斗缓缓地灌入管内,使管内液体灌满。
6、排液:酸液注入管内静置8~12 小时,使被酸洗管道内壁呈现金属本色,即可排液。
将废液直接排入压机机坑。
7、排液后,用清水对管内冲洗数遍后,在管内注入清水约80%,操作方法按昭5 执行。
8、将配置的1~3%的碱液缓缓注入管内,并用试纸检查其PH 值,使PH 值≥6,静置4 小时,即可排去中和液。
液压、润滑管道酸洗方案
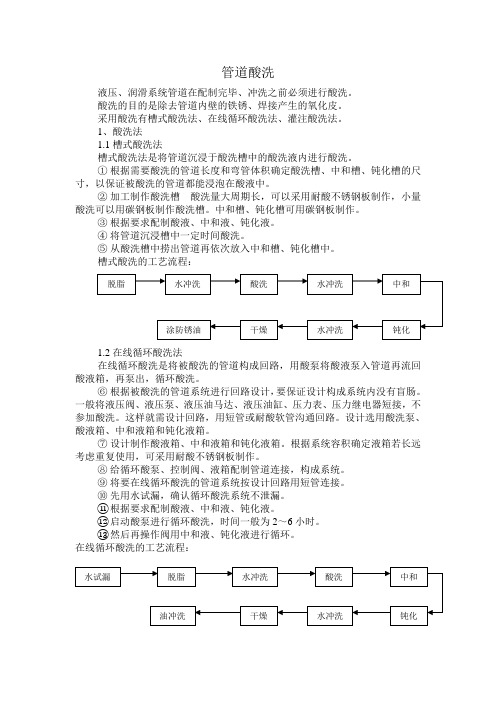
管道酸洗液压、润滑系统管道在配制完毕、冲洗之前必须进行酸洗。
酸洗的目的是除去管道内壁的铁锈、焊接产生的氧化皮。
采用酸洗有槽式酸洗法、在线循环酸洗法、灌注酸洗法。
1、酸洗法1.1槽式酸洗法槽式酸洗法是将管道沉浸于酸洗槽中的酸洗液内进行酸洗。
① 根据需要酸洗的管道长度和弯管体积确定酸洗槽、中和槽、钝化槽的尺寸,以保证被酸洗的管道都能浸泡在酸液中。
② 加工制作酸洗槽 酸洗量大周期长,可以采用耐酸不锈钢板制作,小量酸洗可以用碳钢板制作酸洗槽。
中和槽、钝化槽可用碳钢板制作。
③ 根据要求配制酸液、中和液、钝化液。
④ 将管道沉浸槽中一定时间酸洗。
⑤ 从酸洗槽中捞出管道再依次放入中和槽、钝化槽中。
槽式酸洗的工艺流程:1.2在线循环酸洗法在线循环酸洗是将被酸洗的管道构成回路,用酸泵将酸液泵入管道再流回酸液箱,再泵出,循环酸洗。
⑥ 根据被酸洗的管道系统进行回路设计,要保证设计构成系统内没有盲肠。
一般将液压阀、液压泵、液压油马达、液压油缸、压力表、压力继电器短接,不参加酸洗。
这样就需设计回路,用短管或耐酸软管沟通回路。
设计选用酸洗泵、酸液箱、中和液箱和钝化液箱。
⑦ 设计制作酸液箱、中和液箱和钝化液箱。
根据系统容积确定液箱若长远考虑重复使用,可采用耐酸不锈钢板制作。
⑧ 给循环酸泵、控制阀、液箱配制管道连接,构成系统。
⑨ 将要在线循环酸洗的管道系统按设计回路用短管连接。
⑩ 先用水试漏,确认循环酸洗系统不泄漏。
⑪ 根据要求配制酸液、中和液、钝化液。
⑫ 启动酸泵进行循环酸洗,时间一般为2~6小时。
⑬ 然后再操作阀用中和液、钝化液进行循环。
在线循环酸洗的工艺流程:1.3灌注酸洗法将酸液灌入管道内静置酸洗的方法。
对于零星的管道酸洗可采用此方法。
⑭将被酸洗的管道封堵,形成容腔,留出浇灌口和排泄口;⑮对被酸洗的管道容腔进行灌水试漏;⑯卸水,灌注酸液进行酸洗,一般静置4~8小时;⑰排泄酸液,进行水冲洗、中和、钝化。
油管路酸洗方案

酸洗过程中产生的废水必须经过 处理后才能排放,防止对环境造 成污染。
安全操作规程
酸洗前检查
在进行酸洗前,必须对设备进行 检查,确保设备处于良好状态。
严格遵守操作规程
在进行酸洗操作时,必须严格遵 守操作规程,不得随意更改操作
步骤。
安全事后检查
在酸洗完成后,必须对设备进行 安全检查,确保设备没有受到损
3. 根据实际情况进行安全员和操作员的轮换。
步骤三:结束阶段(1小时)
03
实施步骤及时间节点
01
02
03
1. 进行设备的清理和复 位。
2. 进行数据的整理和总 结。
3. 进行安全措施的检查 和复核。
06
方案效果评估
清洗效果评估标准
01
02
03
04
清洗后的管路内壁应无残留物 ,光滑洁净。
清洗后的管路应无损伤,不变 形。
酸洗的必要性
01
02
03
提高传输效率
通过酸洗去除油管路内表 面的杂质,可以减小流体 传输的阻力,提高传输效 率。
保障安全
通过对油管路进行酸洗, 可以预防因杂质导致的堵 塞、泄漏等问题,降低安 全事故发生的概率。
延长使用寿命
定期对油管路进行酸洗可 以延长其使用寿命,减少 更换频率,降低维护成本 。
酸洗的可行性
实施步骤及时间节点
步骤一:准备阶段(1小时) 1. 检查设备和工具的准备情况。 2. 检查安全措施的落实情况。
实施步骤及时间节点
1. 根据分工进行操作。
步骤二:实施阶段(6小时 )
3. 进行人员的分工和职责 确认。
01
03 02
实施步骤及时间节点
油管酸洗规范

油管酸洗规范
油管路酸洗工艺
油管路的循环酸洗分碱洗、酸洗和钝化三道工序,每道工序进行前后都需用40℃的除盐水或软化水冲洗管路,碱洗溶液的配比为0.8%氢氧化钠和0.2%的磷酸三钠;酸洗溶液的配比为4%~5%工业盐酸加入0.2%~0.3%的缓蚀剂若丁;钝化液的配比为2%~3%亚硝酸钠溶液,同时加入工业氨水,调整溶液的PH值在9~11范围内。
为提高酸洗效果可采用加热循环,一般碱洗时溶液温度为80~90℃,循环4~6H;酸洗时溶液温度为50℃,循环6~8H,循环流速可在0.1m/s。
油管路静泡酸洗的酸液配比以10%盐酸加入0.2%的缓蚀剂若丁为宜。
浸泡前应先以上述碱液碱洗,酸液静泡时间一般在4H以上。
浸酸后的油管应经清水冲净后再放入钝化液槽中钝化,钝化液为2%的亚硝酸钠溶液(PH值为9.5~10),钝化时间一般在3H以上。
管子钝化后用清水冲洗干净,再用压缩空气吹干并封闭。
油管路酸洗方案
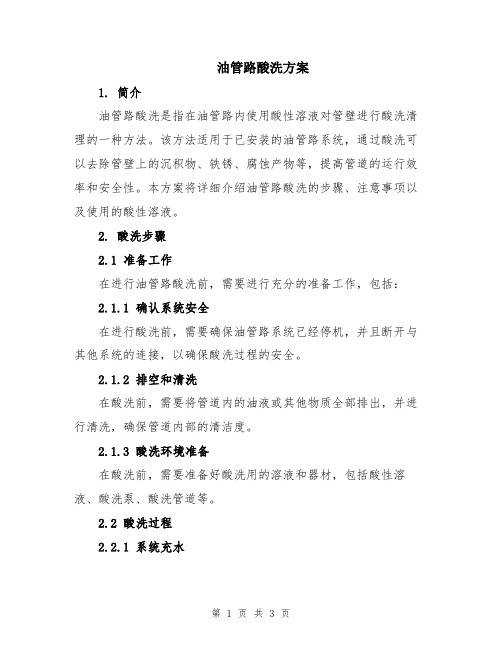
油管路酸洗方案1. 简介油管路酸洗是指在油管路内使用酸性溶液对管壁进行酸洗清理的一种方法。
该方法适用于已安装的油管路系统,通过酸洗可以去除管壁上的沉积物、铁锈、腐蚀产物等,提高管道的运行效率和安全性。
本方案将详细介绍油管路酸洗的步骤、注意事项以及使用的酸性溶液。
2. 酸洗步骤2.1 准备工作在进行油管路酸洗前,需要进行充分的准备工作,包括:2.1.1 确认系统安全在进行酸洗前,需要确保油管路系统已经停机,并且断开与其他系统的连接,以确保酸洗过程的安全。
2.1.2 排空和清洗在酸洗前,需要将管道内的油液或其他物质全部排出,并进行清洗,确保管道内部的清洁度。
2.1.3 酸洗环境准备在酸洗前,需要准备好酸洗用的溶液和器材,包括酸性溶液、酸洗泵、酸洗管道等。
2.2 酸洗过程2.2.1 系统充水首先,将酸洗用溶液与水按照一定比例混合,将混合后的溶液通过酸洗泵注入到管道系统中,直到管道系统充满溶液。
2.2.2 酸洗循环启动酸洗泵,使溶液在管道系统中形成循环。
可以通过控制酸洗泵的流量和压力来控制酸洗速度和强度。
酸洗时间根据管道系统的情况而定,一般为数小时到数天不等。
2.2.3 酸洗后清洗酸洗完成后,需要将酸洗用的溶液和管道内附着物一起排出。
可以通过接通清洗水源和启动清洗泵,将管道内的溶液冲洗干净。
2.3 监测和检查在酸洗过程中,需要不断监测酸洗溶液的酸度、温度和流速等参数,确保酸洗过程的控制和安全。
酸洗完成后,需要对管道系统进行检查,确保管道内表面的清洁度和无损伤。
3. 注意事项3.1 安全措施在进行油管路酸洗前,需要做好安全措施,包括佩戴防护眼镜、手套、防护服等,避免酸溶液对人体造成伤害。
3.2 酸洗溶液选择酸洗溶液的选择需要根据管道系统的材质和污染程度来确定。
常用的酸洗溶液包括盐酸、硫酸等强酸溶液,以及EDTA、柠檬酸等缓蚀剂。
3.3 温度控制酸洗溶液的温度对酸洗效果有一定影响。
一般情况下,温度越高,酸洗效果越好,但过高的温度可能对管道系统造成损害。
油管路酸洗方案

油管路酸洗方案近年来,随着石油化工行业的日益发展,油管路的需求量与日俱增。
然而,油管路在长期的使用中也会出现一些问题,比如管道内部腐蚀、结垢等,影响其正常的运转。
因此,对于油管路的保养和维护显得尤为重要。
其中,油管路的酸洗处理也是不可避免的一项工作。
一、油管路酸洗方案的概述油管路的酸洗处理是指将含有酸性溶液的液体注入油管路内,对管道内的腐蚀、结垢等问题进行短期的处理。
酸洗处理的主要目的是清除油管路内的凝胶、硫化物、铁碳化合物等物质,降低管道内的腐蚀程度,提高油管路的正常运行效率。
同时,酸洗处理也可以为后续的维护和保养工作创造更好的条件。
二、油管路酸洗方案的操作流程1.准备工作在进行油管路酸洗处理之前,需要进行充分的准备工作,以确保操作的安全和顺利。
首先,需要对油管路的材料、压力大小、管径等进行详细的了解,确定酸洗液的类型、浓度以及酸洗液的注入和排放方式。
其次,需要对酸洗液使用的设备和工具进行检查,确保其功能正常。
最后,还需要对操作人员进行安全培训和评估,指导操作过程。
2.清洗工艺清洗工艺是整个酸洗处理的核心环节。
其步骤如下:(1)对管路内的杂质和污垢进行彻底的清洗,防止这些物质对工艺后续的影响。
(2)采用酸性溶液对管路进行浸泡,彻底清除铁锈、铁碳化物等物质。
(3)使用配合的缓蚀剂,对管路进行浸泡,减缓酸性溶液对管道内部的腐蚀。
缓蚀剂的使用比例一般控制在1%-5%之间。
3.水洗工艺清洗完毕后,需要进行充分的水洗,以彻底清除管道内的酸性溶液和缓蚀剂。
水洗的工艺流程如下:(1)用清水对管道进行多次的冲洗,直到洗涤出的水呈现出中性或者碱性。
(2)进行化学中和,并与有关部门协商后严格依据环保法规进行处置。
4.管道脱水脱水是保证管道正常运行的重要环节。
其脱水工艺如下:(1)对管道内的水分渗透等现象进行处理。
(2)采用干燥剂对管道内的水分进行吸附处理。
(3)通过逐渐降低温度、增加气体流速等方式,将管道内部的水分完全排除。
现场液压系统清洗工艺规程

现场液压系统清洗工艺规程一、清洗的基本要求:1)环境:有条件尽可能在室内进行清洗,如果必须在现场或室外也应避免周围环境有尘土较多的情况下进行清洗。
2)清洗剂:可采用干净的汽油、煤油、柴油等轻质油。
3)容器:清洗应具有清洗的容器,可用脸盆、饭盒等作为容器。
4)擦试布:应采绸布之类不掉纤维的拭布进行擦试。
5)过滤纸:精洗时应把清洗剂进行过滤后再清洗元件或零件,或用多层绸布进行过滤。
6)毛刷:用不易掉毛的毛刷刷洗元件、零件。
二、清洗的方法:1}粗洗:对擦洗的元件、零件、管件应对外面的明显可见脏物进行清洗。
2)半精洗:对元件的内部进行清洗,对元件的阀芯应尽可能的活动清洗。
清洗后应放到干净处,并遮盖好防止再污染。
(注意:放置的元件开口不应朝下,应侧放或向上放置)3)精洗:对清洗剂进行过滤后再对元件、零件进行清洗,清洗后应马上安装。
不易放置。
三、清洗规程1)油箱的清洗油箱是主要囤积脏物的地方,先放出油箱里的油到清洗干净的容器里存放好,然后用清洗油箱。
清洗干净后,用揉好的面(粉)对油箱内部进行粘贴(注意:揉好的面应以表光不粘手为易),粘贴的面不能掉渣,粘贴干净后,应立即封油箱盖。
2)元件、零件等清洗元件、零件应在清洗前取下安装用的密封圈,并将密封圈放置好,以免损伤,然后用清洗剂对元件和零件进行粗洗和半精洗,对特别脏的元件应进行分解清洗(对分解的元件应仔细拆卸,并注意拆卸的顺序,但禁止拆卸复杂元件和比例伺服阀)。
清洗后应检查密封件外表是否有损伤,并对损伤件进行更换,然后安装到元件的原密封位置处。
清洗后的元件和零件能够立刻安装的应立刻安装,不能安装的,应将油口封装好,放置在干净处,待安装。
3)管件清洗拆下的管件清洗时应尽可能采用冲洗的方法,冲洗时的清洗液应进行过滤,清洗后,能安装的尽量先安装,不能安装的也应将管子两端用干净的塑料布封装好,以防止污染物进入管内。
4)油路块的清洗对油路块的油孔,最好采用注射器注射清洗,如无条件,一事实上采用先在油液中涮洗,然后用干净的清洁剂对管中反复涮洗。
油管路酸洗方案
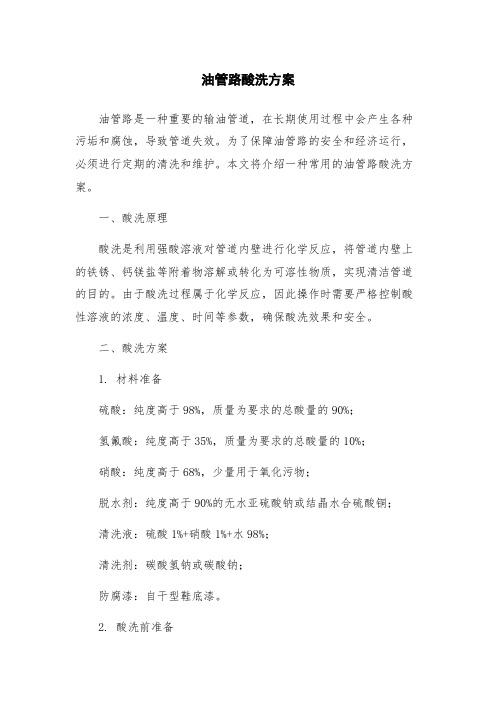
油管路酸洗方案
油管路是一种重要的输油管道,在长期使用过程中会产生各种污垢和腐蚀,导致管道失效。
为了保障油管路的安全和经济运行,必须进行定期的清洗和维护。
本文将介绍一种常用的油管路酸洗方案。
一、酸洗原理
酸洗是利用强酸溶液对管道内壁进行化学反应,将管道内壁上的铁锈、钙镁盐等附着物溶解或转化为可溶性物质,实现清洁管道的目的。
由于酸洗过程属于化学反应,因此操作时需要严格控制酸性溶液的浓度、温度、时间等参数,确保酸洗效果和安全。
二、酸洗方案
1. 材料准备
硫酸:纯度高于98%,质量为要求的总酸量的90%;
氢氟酸:纯度高于35%,质量为要求的总酸量的10%;
硝酸:纯度高于68%,少量用于氧化污物;
脱水剂:纯度高于90%的无水亚硫酸钠或结晶水合硫酸铜;
清洗液:硫酸1%+硝酸1%+水98%;
清洗剂:碳酸氢钠或碳酸钠;
防腐漆:自干型鞋底漆。
2. 酸洗前准备。
- 1、下载文档前请自行甄别文档内容的完整性,平台不提供额外的编辑、内容补充、找答案等附加服务。
- 2、"仅部分预览"的文档,不可在线预览部分如存在完整性等问题,可反馈申请退款(可完整预览的文档不适用该条件!)。
- 3、如文档侵犯您的权益,请联系客服反馈,我们会尽快为您处理(人工客服工作时间:9:00-18:30)。
mdf生产线现场配制液压油管酸洗方案为了达到现场配置液压油管道清洗确保液压系统的安全,可靠运行,因此对现场配置液压油管及高温导热油管进行酸洗,特制定此酸洗方案。
在操作时认真按本方案的规定执行。
一、施工预备
(一)人员预备
组成由业主和施工方共同参加的酸洗工作小组,并指定负责人,对酸洗工作负责,具体实施酸洗工作。
(二)原料、器材的预备
1、37%盐酸100Kg
2、工业碱50Kg
3、酸洗配制桶50装塑料桶或陶瓷小缸2件
4、水杓(塑料)1件
5、耐酸手套3双
6、耐酸胶鞋3双
7、扒杆2付(自制)
8、PH试纸2本
9、3T葫芦2台
10、46#抗磨液压油170Kg/桶1桶
11、潜水泵1台
12、塑料小漏斗个
13、口罩5个
14、小空压机1台
(三)现场预备
1、接通水源至主油管沟旁
2、疏通或开创室外排水通道
3、制作盲板,加液漏斗和木塞
4、清理施工现场,预备固定管道的垫木和抓钉
5、接通压缩空气
(四)现场施工
1、拆除主油管直出口与设备联接口,用2台链条葫芦将主
油管吊在扒杆上,并使进油端尽可能向上倾斜。
进口端制
作钢板漏斗及法兰,用螺栓加橡胶石棉板紧固。
下口端用
盲板加垫紧固。
2、将所有现场配置已安装的油管全部拆卸,平摆在车间地
面。
带弯头管道使其一端置于朝上,另一端加木塞楔紧。
直管一端加木塞,竖直置于压机地坑。
3、压机基坑注水,深度约100mm,并加入25Kg经热水熔
解成的碱液注入地坑。
4、配置酸洗液:按每百公斤37%浓度的盐酸加200~250
公斤洁净水配制成酸洗液备用。
5、灌液:用塑料杓将已配制好的酸液经漏斗慢慢地灌入管
内,使管内液体灌满。
6、排液:酸液注入管内静置8~12小时,使被酸洗管道内
壁出现金属本色,即可排液。
将废液直截了当排入压机机
坑。
7、排液后,用清水对管内冲洗数遍后,在管内注入清水约
80%,操作方法按昭5执行。
8、将配置的1~3%的碱液慢慢注入管内,并用试纸检查其
PH值,使PH值≥6,静置4小时,即可排去中和液。
中和
过程需要反复多次的进行检查。
9、清水冲洗:排放中和液后,再用清水对管内进行冲洗将
残留药液全部冲洗洁净。
10、吹干:用压缩空气对管内充分吹干,不留水渍。
11、灌油(涂油):涂油,将液压油置于管内,用压缩空气
由一端吹入,使油在管内形成油膜,以防管内生锈。
12、管道复位,按要求进行第二次安装。
二、酸洗终止后的善后工作。
1、及时将地坑废液用水泵抽至室外排除。
2、拆除临时供水、供气管
3、将余下的药液进行中和处理或入库
4、器材入库
5、清理现场,复原作业状况
三、施工安全注意事项
为了确保施工安全,在施工中须专门注意如下几点:
1、配置酸液时,施工人员须佩带耐酸手套、胶鞋和口罩。
2、与酸洗无关人员,不得随意进入现场。