工艺管线酸洗方案
工艺管道酸洗钝化方案

工艺管道酸洗钝化方案XXX新制剂质检楼洁净项目的酸洗钝化方案概述如下。
在系统试压完成后,对纯水和纯蒸汽系统进行酸洗钝化,以确保洁净管道符合输送纯水和纯蒸汽的要求,并且经过酸洗钝化的洁净管道在管路灭菌后不会对所输送的介质产生新的污染。
纯水系统利用系统水泵循环酸洗钝化,而纯蒸汽管路计划在制水间和每个支路末端,利用软管与纯水管路连接成环路,与纯水系统一起进行酸洗钝化。
具体管路连接方案需要考虑到水机厂家提供的水罐不允许使用的前提下,自备一台储酸碱的储罐,容积不小于3.5米3.纯水系统的连接方案是将纯水罐与泵体之间的管路从罐底阀门处与纯水罐隔离,该段管路和经过板换的回水水管路串联到水泵循环系统,并用耐酸软管与自备储罐连接在一起,形成环路进行酸洗钝化。
选用系统中最大的流量泵做酸洗钝化,根据比较选用编号为P104的水泵(即去蒸馏水机和纯蒸汽发生器的环路)做为循环泵。
其余三个循环环路,在水泵的进口阀门处与原系统拆离,用耐酸软管与自备储罐连接在一起。
回水管路在回水主管的小环路阀门处与原系统拆离,利用软管将循环回水接入自备储罐。
纯蒸汽系统连接方案是计划与纯水管路并在一起进行酸洗纯化,注水口选在各个纯蒸汽使用点,用耐酸软管与纯水管路管处连接在一起。
为确保安全,需要采取必要的安全防护措施,并组织好人员机构。
本方案的编制依据为GB-97工业金属管道工程施工及验收规范、质检楼工程洁净工艺管道招标文件、纯化水、纯蒸汽管路设计施工说明、质检楼洁净工艺管道施工方案、药品生产验证指南(2003年版)、XXX投标技术文件及施工组织设计。
为方便排放酸碱液,软管两头需加设阀门。
纯蒸汽系统的回水管路,在分汽缸上方主管处与设备断开(阀门关闭),利用耐酸软管与自备储罐连接形成环路。
纯蒸汽分汽缸单独进行连接,单独循环进行酸洗钝化。
不能形成循环的纯蒸汽使用点,采用浸泡的方法。
酸洗纯化完成后,利用软管和塑料桶排出管路中的酸碱液,中和后进行排放。
在注射水环路形成循环时,需要操作主管路上的阀门,保证小环路能够进水循环。
纯化水管线 酸洗钝化方案

纯化水管线酸洗钝化方案
纯化水管线的酸洗钝化方案可以参考以下步骤:
1. 清洗管线:使用高压水枪或清洗机械对管线内部进行彻底清洗,以去除污垢和杂质。
2. 酸洗处理:在清洗后,使用适当的酸洗溶液对管线进行处理。
常用的酸洗溶液包括硝酸、磷酸或硫酸等。
注意使用酸洗溶液时要戴好防护眼镜、手套等个人防护装备,并确保通风良好。
3. 中和处理:酸洗后,使用碱性溶液对管线进行中和处理,以中和酸洗溶液的残留物。
常用的碱性溶液可选用氢氧化钠或碳酸氢钠溶液等。
1
4. 钝化处理:在中和处理后,使用适当的钝化剂对管线进行钝化处理,以提高其耐腐蚀性。
常用的钝化剂包括铬酸钾、亚硝酸钠或硝酸钠等。
5. 冲洗管线:最后,对钝化后的管线进行彻底的冲洗,以去除处理过程中的溶液残留物和杂质。
以上是纯化水管线酸洗钝化的一般方案,具体操作应根据实际情况和要求来确定。
在进行处理时,应密切注意安全事项,并根据需要进行监测和测试,确保处理效果符合要求。
2。
工艺管道系统酸洗钝化施工方案

中国核工业第二三建设公司项目名称表A 2011.12.01 CFC 第一次发布修改版日期状态编制人审核人修改---评语批准人文件标题:核燃料后处理放化实验设施不锈钢工艺管道系统酸洗钝化方案文件类型:技术程序级别:一般级发行:中国核工业第二三建设公司放化实验设施工程项目部文件编号JJ/放化-H407中国核工业第二三建设公司放化实验设施工程项目部文件未经许可,不得外用、复制和泄露修改页日期章节页附录修改范围A 2011.12.01 ──────第一次发布目录1.目的 (3)2.适用范围 (3)3.工程概况 (3)4.编制依据 (4)5.酸洗钝化方法的确定 (4)6.准备工作 (5)7.酸洗钝化的操作规程 (6)8.注意事项 (7)附表1: (9)核燃料后处理放化实验设施不锈钢工艺管道系统酸洗钝化方案1.目的根据设计文件《工艺设备及管道安装、试验和验收技术条件》-000101JTS01中1.11.5条:不锈钢管道经水压、气压试验后,应进行系统酸洗钝化处理。
酸洗钝化液配方和工作条件:15~25Vol%酸洗钝化液:HNO3温度:室温~60℃浸泡时间:15~30分钟该工程的不锈钢工艺管道在安装前进行了酸洗钝化,上述技术要求的主要目的是为了对焊缝内壁进行钝化及对管道进行清洗,但是根据该工程工艺管道工艺流程及管道布置情况,无法全部采用浸泡法,对于无法浸泡的采用循环法(见图1所示)。
为了明确该工程不锈钢工艺管道系统酸洗钝化的要求、操作方法、注意事项等而编制该方案,用于指导现场工艺管道系统酸洗钝化的操作。
2.适用范围本酸洗钝化方案适用于核燃料后处理放化实验设施需要进行系统酸洗钝化的不锈钢工艺管道。
3.工程概况核燃料后处理放化实验设施(简称CRARL)的工艺管道分布在C、D座,工艺管道规格有φ57×3.5、φ32×3、φ25×3、φ22×3、φ17×3、φ14×2、φ10×2、φ6×1.5,绝大部分材质为0Cr18Ni10Ti,小部分材质为0Cr18Ni12Mo2Ti,管道长度大致如下:材料名称规格型号数量(米) 管道容积(m3)不锈钢无缝管φ6×1.5 0Cr18Ni10Ti 1697 0.012不锈钢无缝管φ10×2 0Cr18Ni10Ti 937 0.026不锈钢无缝管φ14×2 0Cr18Ni10Ti 437 0.034不锈钢无缝管φ17×3 0Cr18Ni10Ti 1713 0.163不锈钢无缝管φ22×3 0Cr18Ni10Ti 14 0.003不锈钢无缝管φ25×3 0Cr18Ni10Ti 1502 0.426不锈钢无缝管φ32×3 0Cr18Ni10Ti 1931 1.025不锈钢无缝管φ32×3 0Cr18Ni12Mo2Ti 157 0.083不锈钢无缝管φ57×3.5 0Cr18Ni10Ti 30 0.059 合计8418 1.8314.编制依据核工业第二研究设计院所编制的技术条件—《工艺设备及管道安装、试验和验收技术条件》000101JTS01 A版;核工业第二研究设计院所设计的施工图—《核燃料后处理放化实验设施工艺安装流程图》000101GYS02 A版;核工业第二研究设计院所设计的施工图—《核燃料后处理放化实验设施D座工艺设备管道布置图》000101GYS04 A版;核工业第二研究设计院所设计的施工图—《核燃料后处理放化实验设施B、C座工艺设备管道布置图》000101GYS03 A版;5.酸洗钝化方法的确定5.1该工程的工艺管道输送的物料清单如下:物料代号物料名称物料代号物料名称S6 0.6MPa蒸汽DR 冷却下水A6 0.6MPa压缩空气DM 去离子水As1.8 0.18MPa压缩空气(增湿) SC 蒸汽冷凝液W 生产上水VT 蒸汽排气OG1 溶解排气DKY 倒空液OGO 量槽间呼排1AW 1A萃取器萃余液OG 贮槽排气1CW 1C萃取器萃余液(30%TBP-OK)VE 真空排气U U、Np、Pu粗产品液H 0.5mol/L硝酸1CU 硝酸铀酰溶液OK 煤油R.E R.E粗产品液LW 其他废液Cs 铯粗产品OLW 废有机相Sr 锶粗产品LLLW 低放废液Ma Ma粗产品ILLW 中放废液JM 夹醚粗产品HLLW 高放废液2EU 硝酸铀酰溶液SH 2mol/L氢氧化钠2AW 2A萃取器萃余液DE1 碱性解吸液DSL 溶解液DE2 酸性解吸液BY 备用5.2酸洗钝化方法的确定由于该工程的工艺管道无法构成循环回路,在进行酸洗钝化时只有单根单根进行。
工艺处理管道酸洗钝化方案

洁净管道酸洗钝化方案编制:审核:批准:中国电子系统工程第二建设有限公司华北制药新制剂质检楼洁净项目二0一一年九月八日目录一酸洗钝化方案概述 (1)二主要施工机械计划 (2)三具体酸洗钝化方案 (3)四安全防护措施 (6)五人员组织机构 (7)编制说明本方案的编制依据为:1.GB50235-97工业金属管道工程施工及验收规范。
2.质检楼工程洁净工艺管道招标文件。
3.纯化水、纯蒸汽管路设计施工说明。
4.质检楼洁净工艺管道施工方案。
5.药品生产验证指南(2003年版)。
6.中电二公司投标技术文件及施工组织设计。
一酸洗钝化方案概述根据招标文件及业主要求,在系统试压完成后,要对纯水,纯蒸汽系统进行酸洗钝化。
目的:通过该程序,使洁净管道能够达到符合输送纯水和纯蒸汽的要求。
要求:经过酸洗、钝化的洁净管道,在管路灭菌后对所输送的介质不产生新的污染。
纯水系统利用系统水泵,进行循环酸洗钝化。
纯蒸汽管路计划在制水间和每个支路末端,利用软管,分别与纯水管路连接成环路,与纯水系统一起进行酸洗钝化。
具体管路连接方案:1.在水机厂家提供的水罐不允许使用的前提下。
为满足酸洗钝化的要求,需自备一台储酸碱的储罐。
储罐容积不小于3.5米3。
2.纯水系统的连接方案:纯水罐与泵体之间的管路从罐底阀门处与纯水罐隔离。
该段管路和经过板换的回水水管路,并串联到水泵循环系统。
并用耐酸软管与自备储罐连接在一起,形成环路进行酸洗钝化。
选用系统中最大的流量泵做酸洗钝化。
根据比较选用编号为P104的水泵(即去蒸馏水机和纯蒸汽发生器的环路)做为循环泵。
其余三个循环环路,在水泵的进口阀门处与原系统拆离,用耐酸软管与自备储罐连接在一起。
回水管路在回水主管的小环路阀门处与原系统拆离,利用软管将循环回水接入自备储罐。
3.纯蒸汽系统连接方案:计划与纯水管路并在一起进行酸洗纯化。
注水口选在各个纯蒸汽使用点,用耐酸软管与纯水管路管处连接在一起。
软管两头加设阀门。
要便于排放酸碱液。
工艺管道酸洗方案

中国石化股份有限公司安庆分公司增设航煤生产设施Ⅰ标段工艺管道清洗方案编制:审核:批准:施工单位: 中国化学工程第十四建设有限公司日期:2015年8月27日目录第一章编制说明................................................................................1.1 编制依据 ......................................................................................................................1.2 工程概况 ...................................................................................................................... 第二章清洗流程................................................................................2.1 施工条件及工艺说明 ..............................................................................................2.2 清洗工艺及工序 ......................................................................................................2.3 清洗技术要求 ..........................................................................................................2.4 清洗临时系统 ..........................................................................................................2.5 清洗流程示意简图 ..................................................................................................2.6 应对长线管道PIG气动弹结合化学清洗工艺的清洗方法及原理.....................2.7 质量要求及控制措施 .............................................................................................. 第三章机具、人员计划 .....................................................................3.1 人员计划 ....................................................................................................................3.2 主要施工机具计划 .................................................................................................... 第四章 HSE措施.................................................................................4.1 HSE方针和目标 .......................................................................................................4.2 HSE组织结构 (18)4.3 不安全因素分析 ........................................................................................................4.4 安全保障措施 ............................................................................................................4.5 HSE评价表 ............................................................................................................... 第五章文明施工................................................................................5.1文明施工 .......................................................................................................................5.2文明施工的目标 ...........................................................................................................5.3施工管理保障措施 .......................................................................................................5.4环境保护的措施 ...........................................................................................................5.5临时用电安全管理保障措施 ....................................................................................... 第六章工作危害分析(JHA)记录表................................................第一章编制说明1.1 编制依据1. 相关设计图纸2. (HG/T2387-2007)化工行业标准《工业设备化学清洗质量标准》3. GB/T 25146-2010 工业设备化学清洗质量验收规范4. GB/T 25147-2010 工业设备化学清洗中金属腐蚀率及腐蚀总量的测试方法重量法5. GB/T 25148-2010 工业设备化学清洗中除垢率和洗净率测试方法6. GB16297-2004 大气污染物综合排放标准9.GB50275-2010 风机、压缩机、泵安装工程施工及验收标准10.GB50235-2010工业金属管道施工规范11.SH3538-2005石油化工机器设备安装工程施工及验收通用标准12.SH3503-2007石油化工建设工程项目交工技术文件通用规范13.SH3543-2007石油化工建设工程项目施工过程技术文件规定14.GB50517-2010 石油化工金属管道工程施工质量验收规范15.SH3501-2011 石油化工有毒、可燃介质钢制管道工程施工及验收规范16. 本方案的编制还参考了以下文件:1)、中石化九江公司800万吨/年油品升级改造项目蒸汽管线、高纯度气管线施工方案2)、河南金大地化工有限公司30万吨/年合成氨、60万吨尿素动力蒸汽管线及装置项目润滑油管道的清洗方案;3)、中国石油大庆石化公司60万吨/年乙烯装置压缩机润滑油管线、蒸汽管线化学清洗施工方案;4)、中石化湖北化肥20万吨/年乙二醇示范装置项目蒸汽管线、高压氧气管线、装置润滑油管线化学清洗;增补项目罐区至码头乙二醇4公里物料管线清洗。
工艺管道酸洗方案

工艺管道酸洗方案(1) 《化工设备及管道清洗规范》(GB20202-2000);(2) 《火电工程调整试运行质量检验及评定标准》(1996年版)(3) 《火力发电厂基本建设工程启动及竣工验收规程实施办法》(1996版)(4) 《火力发电厂锅炉化学清洗导则》(5) 《污水综合排放标准》GB8978-1996(6) 《电力建设安全健康与环境管理工作规定》(7) 《电力建设安全工作规程》(第一部分:火力发电厂)主要处理管道内成分:灰尘、油脂、焊渣、铁锈、黑色高温氧化皮施工工艺:管路:试压----水冲洗-----脱脂、酸洗----漂洗-----水洗----钝化----水洗-----干燥化学清洗回路及清洗泵选择1.化学清洗回路分两个回路,清洗回路如下:1.1回路1清洗箱—→清洗泵—→西侧管道进口—→换热器—→东侧管道进口—→清洗箱1.2回路2清洗箱——清洗泵——东侧管道进口—→换热器—→西侧管道进口———清洗箱2.清洗循环流速及清洗泵选择根据《火力发电厂锅炉化学清洗导则》的规定,管道流速应在0.1 m/s~0.3m/s,省煤器流速在0.1 m/s~0.2m/s左右,清洗泵流量在100t/h。
泵扬程应大于省煤器静液位及系统流动阻力之和,约为30m。
根据上述考虑,清洗选用的临时进药和回药母管管径125mm,选用一台流量为100 t/h、扬程40米的清洗泵。
具体步骤:1、管路:(1)、试压将临时系统和系统总管线连接好打开相应阀门、换热器进出水阀门和排气门,关闭测量仪表一次门。
补水进行大流量冲洗,待出水无杂质关闭排水。
进行循环试压(运行半个小时候检查系统是否有泄漏现象,如果有马上停泵检修;如运行正常进行下一步操作)。
(2)、脱脂、酸洗脱脂和酸洗可单独进行循环清洗。
酸洗采用无机酸、缓蚀剂(zlm-927缓蚀剂0.3%)、表面活性剂(TX-100. 0.1%)材料循环清洗,与水配比为10:1,总量约5吨。
系统水冲洗试压后,无泄漏的情况下,缓慢加入清洗剂进行循环清洗;清洗时间大约4-6小时。
纯化水管线-酸洗钝化方案
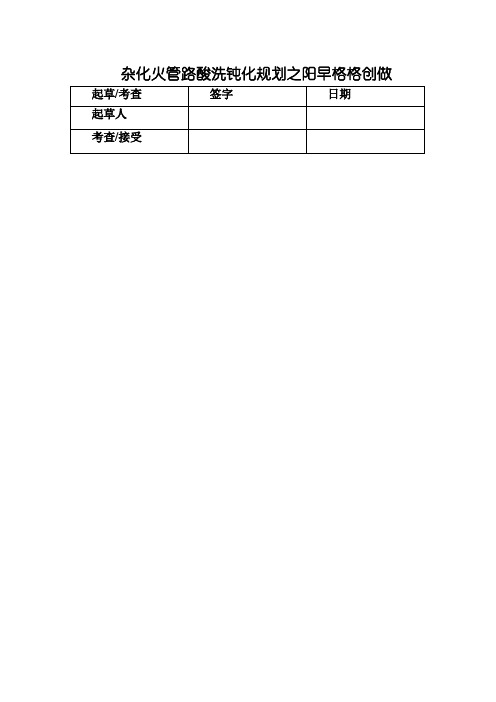
杂化火管路酸洗钝化规划之阳早格格创做目录TABLE OF CONTENTS1体例规划的依据 (3)2处事范畴 (3)3荡涤工艺 (3)4荡涤历程 (4)5兴液处理 (7)6甲圆提供的条件 (7)7临时配管 (8)8考验与查支 (8)9仄安 (8)1体例规划的依据1.1管讲荡涤的需要性杂化火不锈钢管讲正在使用前,要举止脱脂、酸洗、钝化战消毒处理,管讲才搞达到死产使用的技能央供.1.2《脱脂工程动工及查支典型》HG20202-2000.1.3《工业设备化教荡涤品量尺度》HG/T2387-2007.1.4工艺过程图及管讲安插图.1.5管线的材量为局部为316L,如有其余材量,荡涤前必须证明.2处事范畴主要为卫死级不锈钢SS316L管讲1.1从杂火制制机到杂火TANK交心前级的循环管讲;1.2杂火循环管讲;3荡涤工艺1.3采与尔公司多年老练的不锈钢管讲荡涤工艺.1.4 管讲的荡涤工艺为:临时配管修坐循环回路——火浑洗——脱脂——火浑洗——酸洗钝化——火浑洗——系统回复1.5设备、管线系统内不宜荡涤的部件:荡涤系统中的仪容类(一次仪容、二次仪容及仪容传感器)战对于荡涤液敏感的部件应临时裁撤.1.6管线系统内不介进荡涤的短管等裁撤的部件采与浸泡荡涤,荡涤完毕后经考验合格后用塑料保陈膜包扎,等管线系统荡涤完毕后再拆置复位.1.7荡涤过程1.1.1.所有需要荡涤的管讲用临时管讲连交产死荡涤循环系统,采与循环荡涤,荡涤时修坐一个循环回路.1.1.2.荡涤过程图4荡涤历程所有荡涤系统的历程是一般的.1.8人为处理1.1.3.管线正在荡涤前要搞周到查看,设备材量战规划中所列要普遍.1.1.4.不介进荡涤的被断绝的仪容阀门等要正在荡涤前查看确认1.1.5. 尝试样品必须包罗二个新焊的,已荡涤的焊缝.一个拆置正在将要荡涤的管路中,其余一个搁正在化教荡涤罐内;.1.9火浑洗:火浑洗及试压的手段正在与消管线内表面积灰、泥沙、脱降的金属氧化物及其余疏紧污秽,并正在模拟荡涤状态下对于临时荡涤回路举止揭收查看.用杂化火(氯离子小于0.1ppM)举止浑洗,浑洗时统制出进火仄稳.浑洗的共时查看荡涤循环系统是可有揭收等情况爆收,如果有,正在荡涤剂增加前要处理佳.1.10脱脂:脱脂处理的手段系统内表面正在创制、拆置、历程中爆收的油脂,使酸洗液能实足,实足天战系统内表面交触,进而使荡涤实足,钝化膜完备;1.1.6.支配步调,系统加进杂化火(氯离子小于0.1ppM)至预约液位,启初循环,并加进碱洗药剂.1.1.7.工艺条件:Process温度常温循环时间 2小时循环时间可根据天气、管讲搀杂情况适合延少或者支缩.1.1.8.脱脂药剂:1.1.9. 尝试名目:PH 1次/半小时脱脂液PH央供保护正在12以上,当PH小于12时应增加氢氧化钠.PH尝试使用PH试纸1.11火力浑洗:火力浑洗的手段是与消脱脂后脱降的污物,并将系统表面残留的脱脂液浑洗搞洁.1.1.10.支配步调,排尽系统内脱脂液,用洪量火浑洗.1.1.11.尝试名目,用视觉瞅察浑洗火至透明无微粒,测定PH小于9.PH 2次/半小时PH尝试使用PH试纸,当PH小于等于9时火浑洗完毕.1.12酸洗:酸洗的手段是利用酸洗液将金属表面的铁锈氧化物等污秽举止化教战电化教反应,死成可溶性物量,并利用酸洗液的冲刷效率与消污秽.1.1.12.支配步调,排洁系统火浑洗残液后,随即系统加火至一定液位循环,加进不锈钢博用酸洗剂,随后补充火至统制液位.荡涤历程中定期排污排空.1.1.13.工艺条件:荡涤温度常温循环时间 2小时1.1.14.酸洗钝化药剂:1.1.15. 尝试名目:pH值 PH value 1次/半小时酸洗液PH央供小于等于1,当PH大于1时应增加硝酸,包管浓度正在20.PH尝试使用PH试纸1.13火浑洗:钝化完毕后的火浑洗是为了把残留的钝化液与消.1.1.16.钝化中断后,排尽钝化液洗液,用杂化火(氯离子小于0.1ppM)举止浑洗,与消残留的钝化液,当PH曲交近中性Ph>6,电导率好小于μs/cm,即可中断.1.1.17. 工艺条件荡涤温度常温1.1.18. 尝试名目:IPH 2次/半小时电导率 2次/半小时PH尝试使用PH试纸使用电导率仪测定电导率1.14系统回复,荡涤完毕后将系统回复本样.1.15如果系统万古间不加进使用,修议用氮气启存.5兴液处理1.16各荡涤历程中的浑洗火,已增加荡涤剂,不妨曲交排搁.1.17酸洗液的兴液,钝化液的兴液,用槽罐车把兴火输送到兴火处理厂处理排搁.6甲圆提供的条件甲圆控制提供如下公用办法:1.18火:齐程采与杂化火,杂化火央供氯离子小于0.1ppM,使用ORION杂化火.1.19电源(荡涤时使用杂化火泵).1.20搞燥无油的压缩气氛或者氮气,0.5-1 MPa.7临时配管1.21临时配管是指将荡涤系统中管讲连交起去,产死荡涤循环回路,荡涤完毕后需要裁撤的管讲战办法.1.22临时配管用硬塑料管.8考验与查支1.23钝化表面目测,钝化膜完备,颜色普遍.1.24正在回路的末尾一个焊缝采与铁氰化钾溶液隐蓝测定,变色时间大于30秒钟.(蓝面考查:用1克铁氰化钾K3[Fe(CN6)]加3毫降(65%_85%)硝酸HNO3战100毫降火配制成溶液(宜现用现配).而后用滤纸浸渍溶液后,揭附于待测表面或者曲交将溶液涂、滴于待测表面,30秒内瞅察表面表露蓝面情况,有蓝面为分歧格.)1.25酸洗钝化完毕后提供“管讲荡涤战钝化报告”.9仄安主要为卫死级不锈钢SS316L管讲.1.26正在举止荡涤处事时,咱们必须要得到处事许可;1.27正在战化教产品有关的处事时,惟有具备灵验部分防备(脸部呵护,防备衣,防备鞋等)的人才允许介进;1.28现场附近需要树坐应慢浑洗火面,不妨浑洗身体战眼睛1.29处事天区战伤害位子必须推警戒线预防已授权的战不呵护的人员加进;1.30将正在所有处事天区/房间悬挂地步标记;1.31持绝监控关关的容器;1.32化教品必须存搁正在指定的仄安天区,处事中断后兴液必须即时从现场移除;1.33氢氧化钠,硝酸的资料仄安技能证明书籍要搁正在现场。
管道酸洗、钝化施工方案4(精)

管道酸洗、钝化施工方案4(精)
在工程施工中,管道酸洗和钝化工作是非常关键的一环,对于管道设备的使用
寿命和安全性有着重要的影响。
本文将详细介绍管道酸洗和钝化的施工方案,讨论工艺流程和施工注意事项,以确保工程质量和安全性。
管道酸洗施工方案
管道酸洗是清除管道内壁沉积物和保护管道表面的一种方法,能够有效延长管
道的使用寿命。
下面是管道酸洗的施工方案:
1.准备工作:确定酸洗液成分和浓度,检查管道的材质和耐酸性。
2.封堵管道:先将管道两端封堵,确保只有管道内部接触酸洗液。
3.注入酸洗液:使用泵将酸洗液注入管道,注意控制流速和压力,避
免管道受损。
4.保持一定时间:根据管道材质和沉积物情况,确定酸洗时间,通常
为数小时至一天。
5.冲洗清洁:酸洗结束后,用清水反复冲洗管道,确保酸洗液完全清
除。
管道钝化施工方案
管道钝化是在酸洗后对管道表面进行处理,形成保护膜,防止管道再次腐蚀。
下面是管道钝化的施工方案:
1.清洁表面:确保管道表面干净无油污,可用化学品清洁或砂纸打磨。
2.浸泡处理:将管道浸泡在钝化液中,根据材质和条件控制钝化时间。
3.中和处理:将处理过的管道放入碱性溶液中中和,保证管道表面中
性。
4.水洗干燥:最后用清水冲洗管道,待干燥。
以上是管道酸洗和钝化的施工方案,关键在于严格控制每个步骤的细节,确保
处理效果和安全性。
在施工过程中,应配备好防护措施,避免酸洗液或钝化液对人员造成伤害。
只有合理的施工操作和严谨的管理才能保证管道设备的长期稳定运行。
- 1、下载文档前请自行甄别文档内容的完整性,平台不提供额外的编辑、内容补充、找答案等附加服务。
- 2、"仅部分预览"的文档,不可在线预览部分如存在完整性等问题,可反馈申请退款(可完整预览的文档不适用该条件!)。
- 3、如文档侵犯您的权益,请联系客服反馈,我们会尽快为您处理(人工客服工作时间:9:00-18:30)。
编号:神华煤直接液化项目加氢稳定装置工艺管道化学清洗技术方案XXX内蒙古项目部2007年5月25日编制及审批表目录1. 编制说明................................................. 错误!未定义书签。
.概述 ............................................................... 错误!未定义书签。
.编制依据............................................................ 错误!未定义书签。
2. 工程概况................................................. 错误!未定义书签。
.施工内容............................................................ 错误!未定义书签。
.工程实物量及计划开竣工日期.......................................... 错误!未定义书签。
3.施工进度计划............................................. 错误!未定义书签。
4.化学清洗方案............................................. 错误!未定义书签。
.化学清洗目的........................................................ 错误!未定义书签。
.化学清洗方法........................................................ 错误!未定义书签。
.化学清洗前应具备的条件.............................................. 错误!未定义书签。
.化学清洗步骤........................................................ 错误!未定义书签。
.管道内表面化学清洗.................................................. 错误!未定义书签。
.不锈钢管焊接接头外表面化学清洗...................................... 错误!未定义书签。
.化学清洗效果评定.................................................... 错误!未定义书签。
.废液处理............................................................ 错误!未定义书签。
5.质量保证措施............................................. 错误!未定义书签。
质量方针及质量目标................................................... 错误!未定义书签。
质量保证体系......................................................... 错误!未定义书签。
质量控制............................................................. 错误!未定义书签。
6.安全目标和安全技术措施................................... 错误!未定义书签。
.项目安全目标........................................................ 错误!未定义书签。
.安全技术措施........................................................ 错误!未定义书签。
.安全风险评价........................................................ 错误!未定义书签。
7.劳动力平衡计划........................................... 错误!未定义书签。
8.降低工程成本措施......................................... 错误!未定义书签。
9.主要药剂................................................. 错误!未定义书签。
10.施工机具及手段用料...................................... 错误!未定义书签。
11.附图.................................................... 错误!未定义书签。
1.编制说明1.1.概述神华煤直接液化项目加氢稳定装置是煤直接液化项目四联合装置之一,该加氢稳定装置在神华煤直接液化项目中的主要作用是为煤液化装置提供满足要求的溶剂,并且对煤液化装置生产出来的液化油进行加氢。
该装置位于煤液化装置东侧、加氢改制装置西侧,该装置由中国石化工程建设公司设计,XXX公司负责承建,XXX工程有限公司进行全程监理。
为保证工艺管道的化学清洗质量,并确保工期,特编制本方案以指导施工。
.编制依据中国石化工程建设公司设计的施工图纸;《工业金属管道工程施工及验收规范》GB50235-97《石油化工钢制管道工程施工工艺标准》SH/T3517-2001《工业设备化学清洗质量标准》HG/T2387-92《污水综合排放标准》GB8978-1996《工业金属管道工程质量检验评定标准》GB50184-93《石油化工施工安全技术规程》SH3505-1999神华工程统一规定神华有关的质量及HSE管理文件公司质量管理手册及程序文件2.工程概况.施工内容根据设计、规范及厂方要求,104单元2台国产压缩机与油站和高位油箱间的润滑油线、3台进口压缩机与油站间的润滑油线和本体之间的工艺线、从补充氢压缩机一级入口分液罐(104-D-108)到补充氢压缩机一级入口缓冲罐的氢气线以及反应进料泵与润滑油站间的润滑油线需要进行化学清洗。
另外不锈钢管道焊接接头焊完后,也要进行酸洗钝化处理。
.工程实物量及计划开竣工日期2.2.1.工程实物量2.2.2.计划开竣工日期计划开工日期2007年6月1日,计划竣工日期2007年7月5日。
3.施工进度计划施工进度计划 (见附图二)4.化学清洗方案.化学清洗目的化学清洗的目的是清除油脂、油污、焊渣、泥砂、锈垢等污物,使管道的内壁和焊接接头外表面形成一层钝化膜,保证管道表面的清洁、干净。
.化学清洗方法管道内表面化学清洗采用在线常温化学清洗-系统循环法。
根据现场实际情况将管道分成若干个化学清洗系统,并连在一起采用清洗泵、清洗槽循环进行化学清洗。
不锈钢管道焊接接头焊完后,也要进行酸洗钝化处理,处理时在焊接接头及其附近部位涂刷酸洗钝化膏或浓硝酸,停留足够时间,用不锈钢丝刷刷除表皮的黑疤,用水冲洗、擦干。
此次化学清洗由专业的清洗队伍进行清洗,并有成功的经验。
.化学清洗前应具备的条件化学清洗方案已经审批,并进行技术交底。
清洗前,管道已按图纸和规范全部完成,试压吹洗合格。
清洗前,临时系统连接安装完毕。
对不允许参与化学清洗的部件,如流量计、孔板、调节阀、压力表、温度计等测试、测量仪表、过滤网、视油器等拆除。
并采取临时短管、临时旁路及盲板等措施对拆除部件的位置进行处理。
关闭并隔离与化学清洗系统无关的阀门并加装盲板,以防清洗液的外泄。
拆装部位均应进行挂牌,标明位置,对拆下的盲端管件按要求浸泡处理,以备清洗后安装复位,具体清洗以实际情况而定。
化学清洗临时系统(包括清洗站)的建立,PH值、浓度及分析取样点均设在循环泵进出口的管线上。
为了检查化学清洗效果和监测腐蚀速度,在循环系统中分别安装监测管段和腐蚀挂片。
公用工程条件● 清洗用水:洁净水, Q≥10 m3/h●电:380v 3相5线制,50Hz,15KW●压缩空气:无油干燥,~.化学清洗步骤不锈钢管道内表面的化学清洗步骤是:水冲洗及系统试漏→脱脂→水冲洗→酸洗→水冲洗→钝化→水冲洗→吹扫、干燥→封闭保护碳钢管道内表面的化学清洗步骤是:水冲洗及系统试漏→脱脂→水冲洗→酸洗→水冲洗→漂洗→中和钝化→吹扫、干燥→封闭保护不锈钢管焊接接头外表面的化学清洗步骤是:清理焊缝表面→涂刷酸洗钝化膏或浓硝酸→刷除焊缝表面的黑疤→水冲洗、擦干.管道内表面化学清洗4.5.1.水冲洗及系统试漏水冲洗及系统试漏的目的是除去系统中的积灰、泥沙、脱离的金属氧化物及其它疏松污垢,并在模拟清洗状态下对临时接管处泄漏情况进行检查。
水压检漏试验时,将全系统注满水,调节出口回水阀门,检查系统中焊缝、法兰、阀门、管段连接处泄漏情况并及时处理,以保证清洗过程中的正常进行。
按高进低出进行水冲洗,当冲洗排水清澈透明,目测与进水水质基本一致时即可结束冲洗。
工艺条件流速:~1.2m/s时间:小时4.5.2.脱脂脱脂的目的是去除系统中油斑、石墨等有机物,使酸洗过程中的有效成分更完全、彻底地与设备管道内表面接触,从而促进金属氧化物和垢的溶解,以保证达到均匀的清洗效果。
排尽积水,将新鲜水充满系统,低进高出循环。
逐渐加入脱脂药剂,混合均匀后按所分系统进行正向循环,当系统脱脂液碱度基本平衡即可结束脱脂。
需用药剂:脱脂主剂氢氧化钠~%脱脂助剂碳酸钠~%表面活性剂 OP-10 ~%渗透剂 JFC ~%检测项目脱脂液浓度:每隔30分钟检验1次PH值:每隔30分钟检验1次工艺条件流速:~1.0m/s时间:4~6小时温度:常温4.5.3.水冲洗脱脂后的水冲洗是冲洗掉系统内的脱脂残液。
脱脂液排净后,即刻用大量水进行冲洗,当进出口水PH=7-8,即可结束冲洗。
检测项目PH值:每隔30分钟检验1次工艺条件流速:~1.2m/s时间:1~2小时温度:常温4.5.4.酸洗酸洗的目的是利用酸洗液与垢类物质和腐蚀产物进行化学和电化学反应,生成可溶物,使设备表面清洁;酸洗是整个化学清洗过程的关键步骤。
将系统内充满新鲜水,配制酸洗液,添加酸洗助剂和缓蚀剂、还原剂等助剂。
当有清洗液返回时,通过放空和导淋检查酸洗液是否充满系统,确定充满后,进行循环清洗,并定期切换进回液阀门,在循环过程中每隔一定时间进行排污和放空,以避免产生气阻和导淋堵塞,影响清洗效果。
定时取样分析,当系统内酸洗液浓度、铁离子含量进步达到稳定,监测管段污垢已经完全除尽,呈金属本色时,即为终点,可结束酸洗。
需用药剂:酸洗主剂硝酸 5~6%酸洗助剂氟化物~%缓蚀剂 Lan-826 ~%还原剂~%检测项目酸洗液浓度:每隔30分钟检验1次[Fe 2+]/[Fe 3+]:每隔30分钟检验1次PH值:每隔30分钟检验1次工艺条件流速:~1.0m/s时间:3~4小时温度:常温4.5.5.水冲洗酸洗结束后,排净酸液,充满新鲜水对全系统进行开路冲洗,去除残留在系统中的酸液和洗落的颗粒,不断轮换开启系统各导淋以便使沉积在短管内的杂物,残液排净。