水泥窑余热发电能力计算方法
余热发电计算依据
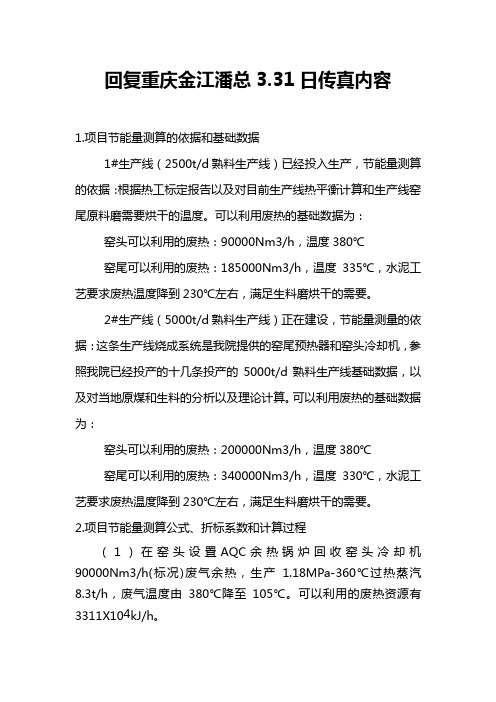
回复重庆金江潘总3.31日传真内容1.项目节能量测算的依据和基础数据1#生产线(2500t/d熟料生产线)已经投入生产,节能量测算的依据:根据热工标定报告以及对目前生产线热平衡计算和生产线窑尾原料磨需要烘干的温度。
可以利用废热的基础数据为:窑头可以利用的废热:90000Nm3/h,温度380℃窑尾可以利用的废热:185000Nm3/h,温度335℃,水泥工艺要求废热温度降到230℃左右,满足生料磨烘干的需要。
2#生产线(5000t/d熟料生产线)正在建设,节能量测量的依据:这条生产线烧成系统是我院提供的窑尾预热器和窑头冷却机,参照我院已经投产的十几条投产的5000t/d熟料生产线基础数据,以及对当地原煤和生料的分析以及理论计算。
可以利用废热的基础数据为:窑头可以利用的废热:200000Nm3/h,温度380℃窑尾可以利用的废热:340000Nm3/h,温度330℃,水泥工艺要求废热温度降到230℃左右,满足生料磨烘干的需要。
2.项目节能量测算公式、折标系数和计算过程(1)在窑头设置AQC余热锅炉回收窑头冷却机90000Nm3/h(标况)废气余热,生产1.18MPa-360℃过热蒸汽8.3t/h,废气温度由380℃降至105℃。
可以利用的废热资源有3311X104kJ/h。
(2)在窑尾设置SP余热锅炉回收窑尾预热器185000Nm3/h(标况)废气余热,生产1.18MPa-310℃过热蒸汽13.04t/h,废气温度由335℃降至230℃。
可以利用的废热资源有3083X104kJ/h。
5000t/d熟料线废气余热条件为:(1)在窑头设置AQC余热锅炉回收窑头冷却机220000Nm3/h(标况)废气余热,生产1.18MPa-360℃过热蒸汽18.44t/h,废气温度由380℃降至119℃。
可以利用的废热资源有6989X104kJ/h。
(2)在窑尾设置SP余热锅炉回收窑尾预热器340000Nm3/h(标况)废气余热,生产1.18MPa-310℃过热蒸汽22.81t/h,废气温度由330℃降至230℃。
水泥窑标准煤耗计算公式

水泥窑标准煤耗计算公式水泥窑标准煤耗是衡量水泥生产过程中能源利用效率的重要指标,搞清楚它的计算公式对于优化生产、降低能耗以及节约成本都有着至关重要的作用。
咱先来说说这标准煤耗到底是咋回事。
标准煤耗,简单来说,就是生产一定量的水泥,所消耗的标准煤的数量。
这就好比咱们开车,跑了一定的里程,用了多少油一样。
只不过在水泥窑里,这个“油”换成了标准煤。
那这计算公式是咋来的呢?其实就是根据一系列的能量平衡和物料平衡原理推导出来的。
比如说,要考虑水泥窑的热收入和热支出。
热收入包括燃料燃烧放出的热量、物料带入的热量等等;热支出呢,有熟料形成吸收的热量、废气带走的热量、窑体散热等等。
具体的计算公式是这样的:标准煤耗(kg/t 熟料)=(燃料用量×燃料低位发热量×1000)÷(熟料产量×熟料烧成热耗)。
这里面的“燃料用量”就是咱们烧的煤的量,“燃料低位发热量”是指燃料燃烧能释放出的实际热量,“熟料产量”很好理解,就是生产出来的熟料的量,“熟料烧成热耗”则是生产每吨熟料所需要的理论热量。
给您讲个我之前遇到的事儿吧。
有一次我去一家水泥工厂参观,正好碰上他们在核算标准煤耗。
那场面,一堆技术人员拿着各种数据表格,计算器按得噼里啪啦响。
我凑过去看了看,发现他们的数据采集可真是细致入微。
比如说,燃料的用量精确到了千克,而且还考虑了不同批次燃料的质量差异。
还有废气温度的测量,每隔一段时间就有人去记录,为的就是能更准确地计算出废气带走的热量。
我当时就想,这可真是一点都不能马虎啊,一个小数据的偏差可能就会影响整个标准煤耗的计算结果。
在实际操作中,要准确计算水泥窑标准煤耗,可不是一件容易的事儿。
得确保各种数据的准确采集,测量仪器要精准,人员操作要规范。
而且,不同类型的水泥窑,工艺条件不同,计算公式中的参数也会有所差异。
所以啊,这就需要咱们的技术人员有扎实的专业知识和丰富的实践经验。
总之,水泥窑标准煤耗的计算公式虽然看起来有点复杂,但只要咱们把每个环节都搞清楚,把数据弄准确,就能通过它来发现问题,采取措施提高能源利用效率,让水泥生产既高效又节能。
余热发电计算依据
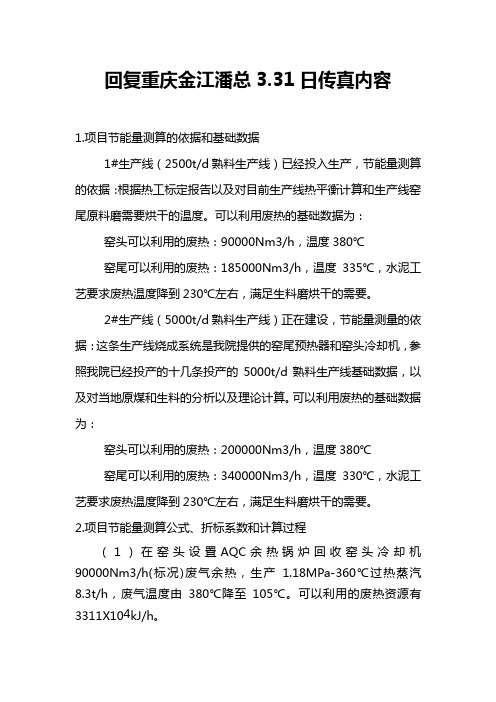
回复重庆金江潘总3.31日传真内容1.项目节能量测算的依据和基础数据1#生产线(2500t/d熟料生产线)已经投入生产,节能量测算的依据:根据热工标定报告以及对目前生产线热平衡计算和生产线窑尾原料磨需要烘干的温度。
可以利用废热的基础数据为:窑头可以利用的废热:90000Nm3/h,温度380℃窑尾可以利用的废热:185000Nm3/h,温度335℃,水泥工艺要求废热温度降到230℃左右,满足生料磨烘干的需要。
2#生产线(5000t/d熟料生产线)正在建设,节能量测量的依据:这条生产线烧成系统是我院提供的窑尾预热器和窑头冷却机,参照我院已经投产的十几条投产的5000t/d熟料生产线基础数据,以及对当地原煤和生料的分析以及理论计算。
可以利用废热的基础数据为:窑头可以利用的废热:200000Nm3/h,温度380℃窑尾可以利用的废热:340000Nm3/h,温度330℃,水泥工艺要求废热温度降到230℃左右,满足生料磨烘干的需要。
2.项目节能量测算公式、折标系数和计算过程(1)在窑头设置AQC余热锅炉回收窑头冷却机90000Nm3/h(标况)废气余热,生产1.18MPa-360℃过热蒸汽8.3t/h,废气温度由380℃降至105℃。
可以利用的废热资源有3311X104kJ/h。
(2)在窑尾设置SP余热锅炉回收窑尾预热器185000Nm3/h(标况)废气余热,生产1.18MPa-310℃过热蒸汽13.04t/h,废气温度由335℃降至230℃。
可以利用的废热资源有3083X104kJ/h。
5000t/d熟料线废气余热条件为:(1)在窑头设置AQC余热锅炉回收窑头冷却机220000Nm3/h(标况)废气余热,生产1.18MPa-360℃过热蒸汽18.44t/h,废气温度由380℃降至119℃。
可以利用的废热资源有6989X104kJ/h。
(2)在窑尾设置SP余热锅炉回收窑尾预热器340000Nm3/h(标况)废气余热,生产1.18MPa-310℃过热蒸汽22.81t/h,废气温度由330℃降至230℃。
新型干法水泥窑低温废气余热最大发电能力的判定与计算讨论!

新型干法水泥窑低温废气余热最大发电能力的讨论大连易世达新能源发展股份有限公司总工程师唐金泉二00九年四月六日摘要:本文用能质“ ”的概念对新型干法水泥窑纯低温余热发电技术所能达到的理论极限发电能力及实际最大发能力进行了分析,对诸如:目前已投产的余热电站实际发电情况、我国新型干法水泥窑纯低温余热发电技术目前处于什么水平、实现水泥熟料生产电能零消耗的途径、水泥生产企业在决定建设余热电站时应注意研究的问题等几个行业关心的问题进行了讨论。
在我国水泥工业迅速普及推广新型干法水泥窑纯低温余热发电技术的今天,相信本文能够起到水泥行业加强对我国目前纯低温余热发电技术际情况的了解及对水泥生产企业确定余热发电项目方案有一定的参考作用。
主题词:水泥工业低温余热发电最大发电能力实际发电能力1. 新型干法水泥窑低温废气余热最大发电能力1.1. 概念的导入“热量”有两个方面的概念:一是“量”的概念,通常我们所讲的“热量”一般都是仅指量的概念;另一个是“质”的概念(从热能---动力转换角度来讲,也是最重要的概念),它是与温度联系在一起的,它可以描述:某一数量的热量,在不同温度下理论上可以转换为最大“有用功”的能力,这个“有用功”通常定义为“ ”。
在火力发电领域,这个“有用功”或者“ ”也可以称为发电能力。
热量的“质”或称“ ”的概念,说明了:对于相同的热量,如果温度不同,其发电能力是有极大差别的,是研究热能---动力转换的基础理论之一。
举例如下:1Kg/h--1000℃的热水,其含有的热量为1Kg/h×1000℃×1KCal/Kg.℃=1000KCal/h,这个1000KCal/h--1000℃热量,理论上转化为最大电能的能力N=[1-273K/(1000℃+273K)]×1000KCal/h×4.1868KJ/KCal÷3600S=0.9135KW。
1000KCal/h 就是热量,而0.9135KW就是1000KCal/h 热量在1000℃时的质量-- 。
水泥工厂余热发电设计规范

1 总则为在水泥工厂余热发电工程设计中,贯彻国家能源综合利用基本方针政策,做到安全可靠、技术先进、降低能耗、节约投资,制定本规范。
本规范适用于新建、扩建、改建新型干法水泥生产线余热发电的工程设计。
新建、扩建水泥工厂的余热发电工程或既有水泥生产线改造增设余热发电系统,设计基本原则应符合国家产业政策和现行国家标准《水泥工厂设计规范》GB50295和《水泥工厂节能设计规范》GB50443。
当余热发电工程设计内容含有热电联供或设有补燃锅炉时,相关部分应符合现行国家标准《小型火力发电厂设计规范》GB50049的有关规定。
水泥工厂余热发电工程环境保护和劳动安全设计,必须贯彻执行国家有关法律、法规和标准。
水泥工厂余热发电工程设计,除应符合本规范外,尚应符合国家现行有关标准的规定。
2 术语余热发电工程设计文件、图纸使用术语应符合本规范规定。
本规范未纳入与水泥工厂余热发电工程相关的术语应符合现行国家标准《工业余热术语、分类、等级及余热资源量计算办法》GB/T1028、《电力工程基本术语标准》GB50297及国家有关术语标准的规定。
余热利用Waste Heat Recovery以环境温度为基准,对生产过程中排出的热载体可回收热能的利用。
窑头余热锅炉 Air Quenching Cooler Boiler利用窑头熟料冷却机排出的废气余热生产热水或蒸汽等工质的换热装置,简称AQC炉。
窑尾余热锅炉Suspension Preheater Boiler利用窑尾预热器排出的废气余热生产热水或蒸汽等工质的换热装置,简称SP 或PH锅炉。
余热发电Waste Heat Power Generation仅利用工业生产过程中排放的余热进行发电,也称纯余热发电。
热电联供 Cogeneration余热发电在生产电能的同时,还可生产热水或蒸汽供热。
主厂房 Main Power Building设有汽轮发电机组及附属设备、设施的厂房。
闪蒸器 Flasher具有一定温度和压力的不饱和水进入压力较低的容器中时,由于压力的突然降低使不饱和水变成容器压力下的饱和蒸汽和饱和水的容器。
水泥窑余热发电能力计算方法

水泥窑余热发电能力计算方法水泥窑是水泥生产过程中的重要设备,其工作过程中会产生大量的余热。
利用余热发电可以提高水泥窑的能源利用效率,降低环境污染。
下面将介绍水泥窑余热发电能力的计算方法。
1. 热量平衡法热量平衡法是计算水泥窑余热发电能力的常用方法。
其基本原理是通过对水泥窑工艺过程中产生的热量进行平衡,计算出可利用的余热能力。
首先,需要确定水泥窑各个热量输入、输出的量值。
热量输入主要包括燃料燃烧时释放的热量,燃料输送和均化所消耗的热量;热量输出主要包括炉体内对流传热、辐射传热以及炉体表面散热等。
其次,通过对热量输入、输出进行平衡,计算出水泥窑的净热量。
即热量输入减去热量输出的差值。
这个差值就是可利用的余热能力。
最后,根据余热发电设备的性能参数,如假设发电效率为35%,可以将净热量除以发电效率,即可计算出水泥窑的余热发电能力。
2. 热力性能法热力性能法是另一种计算水泥窑余热发电能力的方法。
其基本原理是通过对水泥窑热力性能参数的估算和计算,得出余热发电的能力。
首先,需要确定水泥窑的工作参数,如进料温度、出料温度、进气温度、出气温度等。
其次,根据水泥窑的工作参数,结合相应的热力性能指标,计算出热力性能参数。
如热损失率、热效率等。
最后,根据热力性能参数和余热发电设备的技术指标,计算出水泥窑的余热发电能力。
方法类似于热量平衡法,根据热力性能指标计算出净热量,再除以发电效率即可得到余热发电能力。
3. 数据统计法数据统计法是通过对已经运行的水泥窑余热发电设备所得到的数据进行分析和统计,得出水泥窑余热发电的能力。
首先,收集和统计近期运行的水泥窑余热发电设备的水泥窑工作参数和发电能力数据。
其次,对数据进行分析和处理,得出水泥窑余热发电的能力。
可以采用平均值、最大值、最小值等方式,得出一个较为合理的水泥窑余热发电能力。
需要注意的是,以上的计算方法只是一种基本的计算思路,具体的计算方法和参数配置还需要根据实际情况进行调整和优化。
中国水泥窑余热发电技术
中国水泥窑余热发电技术摘要:水泥工业是高耗能的工业。
在水泥生产中,水泥窑在350℃左右排放大量中低温废气,约占燃料总热输入的30%。
如果直接排放到大气中,会造成严重的能源浪费。
利用低温余热发电技术对该部分中低温废气余热进行回收利用。
产生的高温过热蒸汽进入汽轮机发电。
发电机的输出功率可满足水泥生产线和水泥厂自身的生活用电,并积极实施节能减排措施。
与火力发电厂相比,余热发电不需要燃烧煤炭等燃料,不产生二氧化碳等环境污染物。
关键词:水泥窑;余热发电技术;前言:节能减排是我国经济社会发展的一项长期战略方针,也是一项极其紧迫的任务。
回收余热,降低能耗,对我国节能减排和环境保护的发展战略具有重要的现实意义。
同时,余热利用在改善工作条件、节约能源、增产、提高产品质量、降低生产成本等方面发挥着越来越重要的作用。
其中一些已经成为工业生产的一部分。
20世纪六七十年代以来,余热利用技术在世界范围内得到了迅速发展。
目前,我国的余热利用技术也取得了长足的进步,但与世界先进水平仍有一定的差距,有的余热没有得到充分利用,有的余热在使用中存在着许多问题。
1 目的要求1.1 降低能耗环境。
在水泥熟料燃烧过程中,窑尾预热器和窑头熟料冷却器排放的低温废气余热占水泥熟料燃烧总热量的30%以上,造成严重的能源浪费。
一方面,水泥生产消耗大量热能,另一方面,水泥生产也需要大量电力。
将400℃以下低温废气余热转化为电能用于水泥生产,可使水泥熟料生产综合电耗降低60%或30%以上。
对于水泥生产企业来说,可以大大减少从社会发电厂购买的电力,或者大大减少水泥生产企业燃烧的燃料。
自备电厂发电可以大大降低水泥生产的能耗;避免了水泥窑余热直接排入大气的热岛现象;同时可以降低社会发电厂或水泥生产企业自用电厂的燃料消耗,减少CO2等燃烧废弃物的排放,有利于环境保护。
1.2 政策的推行提供技术支持。
自然资源如能源、原材料、水、土地等,随着经济的发展,资源有限之间的矛盾越来越明显。
水泥回转窑热平衡、热效率、综合能耗计算方法
水泥回转窑热平衡、热效率、综合能耗计算方法水泥回转窑是水泥生产过程中的重要设备,其热平衡、热效率和综合能耗的计算方法是评估其能源利用情况的重要指标。
下面是一种常见的计算方法:热平衡计算方法:水泥回转窑的热平衡计算旨在确定进料、燃烧和排放之间的热平衡状态。
基本原理是进料和燃料中的化学能通过燃烧转化为热能,并在水泥生产过程中被利用或散失。
首先,收集相关数据,包括进料和燃料的物料流量、温度、化学成分等信息,以及气体排放的温度和组成。
然后,使用热平衡计算方法,计算进料和燃料中的化学能以及废气中的热能。
最后,将进料和燃料中的化学能与废气中的热能进行比较,以确定热平衡状态。
热效率计算方法:水泥回转窑的热效率是衡量其能源利用效率的指标。
通常使用下述公式计算热效率:热效率= 实际产生的热能/ 理论上可产生的热能实际产生的热能可以通过测量窑筒表面温度、废气温度、回收热量等方式获得。
理论上可产生的热能可以通过燃料的热值以及进料的化学能来估算。
综合能耗计算方法:水泥回转窑的综合能耗是指生产单位水泥所消耗的总能源量。
计算综合能耗的方法包括以下步骤:收集生产过程中消耗的各种能源的数据,包括燃料的消耗量、电力的消耗量等。
将各种能源的消耗量转换为标准能源单位,例如转化为煤当量单位。
将各种能源的消耗量相加,得到总能源消耗量。
将总能源消耗量除以生产的水泥量,得到单位水泥的综合能耗。
以上是一般常见的计算方法,具体计算过程可能因不同水泥生产线的配置和参数而有所不同。
在实际应用中,可能还需要考虑一些其他因素,如能源转换效率、热损失等。
因此,建议在具体的水泥生产工艺中,参考相应的标准和技术规范,并根据实际情况进行计算和评估。
水泥工厂余热发电设计规范
1总则1.0.1为在水泥工厂余热发电工程设计中,贯彻国家能源综合利用基本方针政策,做到安全可靠、技术先进、降低能耗、节约投资,制定本规范。
1.0.2本规范适用于新建、扩建、改建新型干法水泥生产线余热发电的工程设计。
1.0.3新建、扩建水泥工厂的余热发电工程或既有水泥生产线改造增设余热发电系统,设计基本原则应符合国家产业政策和现行国家标准《水泥工厂设计规范》GB50295和《水泥工厂节能设计规范》GB50443。
1.0.4当余热发电工程设计内容含有热电联供或设有补燃锅炉时,相关部分应符合现行国家标准《小型火力发电厂设计规范》GB50049的有关规定。
1.0.5 水泥工厂余热发电工程环境保护和劳动安全设计,必须贯彻执行国家有关法律、法规和标准。
1.0.6水泥工厂余热发电工程设计,除应符合本规范外,尚应符合国家现行有关标准的规定。
2术语2.0.1余热发电工程设计文件、图纸使用术语应符合本规范规定。
本规范未纳入与水泥工厂余热发电工程相关的术语应符合现行国家标准《工业余热术语、分类、等级及余热资源量计算办法》GB/T1028、《电力工程基本术语标准》GB50297及国家有关术语标准的规定。
2.0.2余热利用Waste Heat Recovery以环境温度为基准,对生产过程中排出的热载体可回收热能的利用。
2.0.3窑头余热锅炉Air Quenching Cooler Boiler利用窑头熟料冷却机排出的废气余热生产热水或蒸汽等工质的换热装置,简称AQC炉。
2.0.4窑尾余热锅炉Suspension Preheater Boiler利用窑尾预热器排出的废气余热生产热水或蒸汽等工质的换热装置,简称SP或PH 锅炉。
2.0.5余热发电Waste Heat Power Generation仅利用工业生产过程中排放的余热进行发电,也称纯余热发电。
2.0.6热电联供Cogeneration余热发电在生产电能的同时,还可生产热水或蒸汽供热。
水泥回转窑物料平衡热平衡与热效率计算方
水泥工业窑热能平衡4.1.6.1 水泥工业窑热能平衡的基本概念熟料烧成综合能耗comprehensive energy consumption of clinker burning熟料烧成综合能耗指烧成系统在标定期间内,实际消耗的各种能源实物量按规定的计算方法和单位分别折算成标准煤的总和,单位为千克(kg)。
熟料烧成热耗heat consumption of clinker burning熟料烧成热耗指单位熟料产量下消耗的燃料燃烧热,单位为千焦每千克(kJ/kg )。
回转窑系统热效率heat efficiency of rotary kiln system回转窑系统热效率指单位质量熟料的形成热与燃料(包括生料中可燃物质)燃烧放出热量的比值,以百分数表示(%)。
根据热平衡参数测定结果计算,热平衡参数的测定按JC/T733 规定的方法进行。
窑的主要设备情况及热平衡测定结果记录表参见附录A。
熟料形成热的理论计算方法参见附录B4.1.6.2 水泥回转窑物料平衡物料平衡计算的范围是从冷却机熟料出口到预热器废弃出口(即包括冷却机、回转窑、分解炉和预热器系统)并考虑了窑灰回窑操作的情况。
物料基础:1kg 熟料1. 收入部分(1) 燃料消耗量1)固体或液体燃料消耗量(4-1 )式中:m r -------------- 每千克熟料燃料消耗量,单位为kg/kg ;M yr ------------ 每小时如窑燃料量,单位为kg/h ;M Fr ------------ 每小时入分解炉燃料量,单位为kg/h ;M sh――每小时熟料产量,单位为kg/h。
2)气体燃料消耗量v r 叫(4-2)式中:V y――每小时气体燃料消耗体积,单位为NriVh ;3气体燃料的标况密度,单位为kg/NmC O CC 2C。
CO °2 C2C m H m C m H m H2 H2N2(4-3)cq、CO、C2C m H m H2N2、H2O 各成分的标况密度,单位为kg/m3N,参见式中:CO 2、CO C2、CH m H、2、HO—一气体燃料中各成分的体积分数,以百分数表示( %;附录Co(2) 生料消耗量(4-4)式m s ----- 每千克熟料生料消耗量,单位为kg/kg ;M ---- 每小时生料喂料量,单位为kg/h(3) 入窑回灰量(4-5)式中:m yh ------------- 每千克熟料入窑回灰量,单位为kg/kg ;yh每小时入窑回灰量,单位为kg/hmik1k P 1K次空气的标况密度,单位为kg/Nm51k CO k cq CO k c。
- 1、下载文档前请自行甄别文档内容的完整性,平台不提供额外的编辑、内容补充、找答案等附加服务。
- 2、"仅部分预览"的文档,不可在线预览部分如存在完整性等问题,可反馈申请退款(可完整预览的文档不适用该条件!)。
- 3、如文档侵犯您的权益,请联系客服反馈,我们会尽快为您处理(人工客服工作时间:9:00-18:30)。
水泥窑余热发电能力计算方法一、目前在开发、应用水泥窑纯低温余热发电技术及装备过程当中有许多新的情况产生,例如:从装机容量上,同样是5000t/d级的水泥窑,水泥生产条件、废气参数条件也类似,但装机容量确有6.0MW、7.5MW、9.0MW等多种;从蒸汽参数上,有0.69~1.27MPa—280~340℃、1.57~2.47MPa-325~400℃等多种;从实际发电能力上,有的宣称2500t/d窑装机已达6000KW或发电功率已超过4000KW, 有的宣称5500t/d 窑发电已达9300KW等;从宣传上,一些设计、承建单位为说明自己有先进的水泥窑纯低温余热发电技术从而有很高的发电量,采用不报熟料热耗、利用三次风或其它水泥生产用的高温气体来发电、在发电机功率表上做手脚、低报熟料实际产量等不正当手段进行宣传。
由于上述新情况的产生,同时也由于为了规范水泥窑纯低温余热发电技术及装备的研究、开发、工程设计、工程建设工作,目前制定科学的水泥窑纯低温余热发电技术评价方法是十分必要的。
二、目前水泥行业已经推广应用的几种纯低温余热发电技术目前水泥行业已经推广应用的几种纯低温余热发电技术,以蒸汽参数来分,基本上有两类:一类为0.69~1.27MPa—280~340℃的低压低温系统,一类为1.57~2.47MPa-325~400℃的次中压中温系统。
对于0.69~1.27MPa—280~340℃的低压低温系统,其热力系统构成有如下三种模式:技术要点:利用水泥窑窑尾预热器排出的350℃以下废气设置一台窑尾预热器余热锅炉(简称SP锅炉)、利用水泥窑窑头熟料冷却机排出的400℃以下废气设置一台熟料冷却机废气余热锅炉(简称AQC炉)、两台锅炉设置一台蒸汽轮机、发电系统主蒸汽参数为0.69~1.27MPa—280~340℃。
上述三种技术没有本质的区别,共同的特点:都是利用在水泥窑头熟料冷却机中部增设抽废气口或直接利用冷却机尾部废气出口的400℃以下废气及窑尾预热器排出的300~350℃的废气余热;最重要的特点是采用0.69~1.27MPa-280~340℃低压低温主蒸汽。
区别仅在于:窑头熟料冷却机在生产0.69~1.27MPa-280~340℃低压低温蒸汽的同时或同时再生产0.1~0.5MPa-饱和~160℃低压低温蒸汽、或同时再生产85~200℃的热水;汽轮机采用补汽式或不补汽式汽轮机;复合闪蒸补汽式适用于汽轮机房与冷却机距离较远的情况而多压补汽式适用于汽轮机房与冷却机距离较近的情况。
对于1.57~2.47MPa—325~400℃的次中压中温系统,其热力系统构成有如下两种模式:其一:冷却机多级取热纯余热发电技术,见图4。
技术要点:利用水泥窑窑尾预热器排出的350℃以下废气设置一台窑尾预热器余热锅炉(简称SP锅炉)或同时利用窑尾C2级预热器内筒设置过热器;利用熟料冷却机排出的400℃以下废气设置一台熟料冷却机废气余热锅炉(简称AQC炉),或者通过改变窑头熟料冷却机废气排放方式:利用熟料冷却机排出的部分360℃以下废气设置一台AQC余热锅炉、利用熟料冷却机排出的部分500℃以下废气设置一台熟料冷却机废气余热过热器(简称ASH过热器);将AQC炉排出的废气部分或全部返回冷却机,窑头熟料冷却机冷却风采用循环风方式;利用两台锅炉或者增设的余热过热器设置补汽式蒸汽轮机,发电系统主蒸汽参数为1.57~3.43MPa—340~435℃、补汽参数为0~0.15MPa—饱和~160℃。
三、研究、开发、应用纯低温余热发电技术应注意的几个原则性问题3.1研究、开发、应用水泥窑纯低温余热发电技术应遵循的基本原则水泥窑纯低温余热发电技术是以节能降耗从而降低水泥生产成本为目的,它的内涵是:将水泥生产过程中产生的并且水泥生产过程本身已不能再利用的余热回收从而转化为电能的技术,因此,研究、开发、应用水泥窑纯低温余热发电技术应遵循的基本原则:不影响水泥生产、不增加水泥熟料热耗及电耗、不改变水泥生产用原燃料的烘干热源、不改变水泥生产的工艺流程及设备。
3.2对水泥生产影响的控制:水泥窑配套建设余热电站,原则上要求不影响水泥生产,但由于在一条完整的熟料生产线窑头、窑尾各串接相应的余热锅炉,因此,余热电站对水泥生产不产生任何影响是不可能的。
根据已投产的余热电站实际生产运行情况,对于遵循上述原则配套建设的余热电站,投入运行后对水泥生产的影响主要集中在如下几个方面:(1)窑尾高温风机:在窑尾SP锅炉漏风控制、结构设计、受热面配置、清灰设计、除灰设计、废气管道设计合适的条件下,电站投入运行后,窑尾高温风机负荷将有所降低,这种影响是正面的。
(2)增湿塔:将随着电站的投入或解出调整喷水量,直至停止或全开喷水。
(3)生料磨及煤磨:随着电站的投入或解出,烘干废气温度将产生较大幅度的变化,需要根据烘干废气温度的变化调整烘干废气量或磨的运行方式。
(4)窑尾电收尘:如果窑尾采用电收尘,电站投入运行后对其收尘效果总是有影响的,只是由于地区不同、配料不同、燃料不同或其它条件不同,对收尘效果的影响程度不同。
但当窑尾采用袋收尘时,电站投入运行对提高收尘效果是有显著作用的。
(5)水泥窑头电收尘器:电站投入运行后,窑头电收尘器工作温度大为降低,粉尘负荷也相应降低。
(6)窑系统操作:由于窑系统增加了两台余热锅炉,而余热锅炉废气不但取自还要送回水泥窑系统,因此势必需要增加窑系统窑头、窑尾、废气处理、生料粉磨、煤制备系统的操作环节。
对水泥窑生产造成的上述几方面的影响,综合起来为两个方面:一是增加了水泥窑生产的操作环节(例如:随着电站的投入、运行和解出,水泥窑需调整窑尾高温风机、增湿塔喷水、生料磨及煤磨、窑头排风机等系统的运行参数;二是如果窑尾采用电收尘,电站投入运行后对其收尘效果总是有或大或小的影响。
对水泥窑生产造成的影响应当而且必须控制在上述范围以内,在目前水泥熟料烧成工艺技术及设备、纯低温余热发电热力循环系统配置技术及设备条件下,为了提高发电量而采用抽取三次风或窑头罩等高温风、生料或燃料烘干改用燃烧燃料而将原来用于烘干的废气用于发电等措施都是不可取的。
采用这些措施,表面上增加了发电量,实际不但不会有助于水泥生产综合能耗的降低,反而由于熟料热耗的增加会使水泥生产综合能耗增加(当水泥厂建设余热电站不是以节能为主要目的,在一公斤标准煤的价格与一度电的购电价格之比小于0.7的条件下,采用这些措施可以增加水泥生产综合效益)。
3.3准确的余热发电技术发电能力指标目前对于余热发电技术发电能力指标,大家往往只注意每吨熟料发电量,而很少注意相关因素对发电量的影响,这是目前产生许多新情况的主要原因。
对于水泥窑纯余热发电,影响吨熟料发电量的因素很多,如:熟料热耗(涉及窑头、窑尾废气温度等);熟料形成热(涉及生料配料成份);原料、燃料烘干所需要的废气温度、废气量(涉及可用于发电的余热量);电站热力系统构成方式及蒸汽参数(涉及发电系统循环效率);熟料实际产量和规模(涉及锅炉、汽轮机等设备效率);废热取热方式(涉及对窑生产及熟料热耗的影响)等等。
由于影响余热发电能力的上述因素,加之这些因素在实际生产中的复杂性,仅采用吨熟料余热发电量来评价纯低温余热发电技术是不科学、不完整、不准确的,不能全面代表纯低温余热发电技术水平。
因此,根据目前的情况,研究、确定水泥窑纯低温余热发电技术的评价方法既是必要的,条件也是成熟的而且也是急需的。
四、水泥窑纯低温余热发电技术的评价方法初探尽管影响余热发电能力的因素较多也比较复杂,但水泥熟料煅烧过程及纯低温余热发电必定都是热工过程,因此,研究、确定出全面、科学、准确的纯低温余热发电技术评价方法是可能的。
本文提出的评价方法是初步的,仅供同行讨论、参考,其由如下二部分构成:第一部分:实用部分,即“每公斤熟料热耗-吨熟料余热发电量”。
目前水泥行业已经习惯用吨熟料余热发电量来做为衡量余热发电技术水平的指标,因此,评价方法中保留这个指标是必要的。
但由于吨熟料余热发电量没有考虑熟料热耗、熟料形成热、原燃料烘干所需废气温度及废气量等因素对发电量的影响,因此,为了考虑影响余热发电量的主要因素即熟料热耗对余热发电能力的影响,应改为采用“每公斤熟料热耗-吨熟料余热发电量”(仍简称“吨熟料余热发电量”)这一指标来评价。
尽管如此,由于这个指标仍然没有考虑熟料形成热、原燃料烘干所需废气温度及废气量对发电能力的影响,对于这个指标:(1)在建设余热电站之前比较、确定余热电站技术方案时,在熟料产量、熟料热耗、用于发电的废气参数(废气温度、废气量、含尘浓度等,下同)、用于原燃料烘干的废气参数条件都相同的条件下,采用“吨熟料余热发电量”来对不同的余热电站技术方案进行评价是准确、可靠的;(2)对于已投产的余热电站,采用“吨熟料余热发电量”来对余热电站及水泥窑自身进行综合考核同样也是准确、可靠的;(3)对于已投产的不同水泥窑间的余热电站进行比较:当熟料产量、熟料热耗、用于发电的废气参数、用于原燃料烘干的废气参数等生产条件大体相同的条件下,采用“吨熟料余热发电量”进行比较是相对准确、可靠的。
当上述生产条件差别较大,如:一条窑的熟料热耗是750×4.1868kj/kg,而另一条窑为780×4.1868kj/kg;或一条窑的生料烘干废气温度为200℃,而另一条窑为230℃时,采用“吨熟料余热发电量”进行比较则是不准确、不可靠的。
对于熟料热耗对发电能力的影响:根据研究及实际生产情况,一般来讲,当熟料热耗增加或减少7~8Kcal/Kg时,吨熟料余热发电量也响应增加或减少1kwh以上。
也就是说,余热电站每多发1kwh电,窑系统将多消耗1~1.12Kg标准煤的燃料(这种结果,间接说明了采用提高熟料热耗增加发电量的办法是浪费能源的不可取的办法)。
第二部分:理论部分,即混合热效率(简称热效率)如前所述,水泥窑纯低温余热发电技术的内涵是将水泥生产过程中产生的并且水泥生产过程本身已不能再利用的余热回收从而转化为电能,因此,采用理论上的“混合热效率”(既不是绝对热效率,也不是相对热效率)来对不同的纯低温余热发电技术的热量转换效果进行评价是科学、准确、可靠的,可以消除熟料热耗、熟料形成热、原燃料烘干所需废气参数、电站热力系统构成方式及蒸汽参数、熟料实际产量和规模、废热取热方式等因素的影响。
(1)定义:水泥窑纯低温余热系统热效率是指可用于发电的水泥窑总余热量转化为电能的比例,其数学表达式为:热效率η= 发电功率D×860×4.1868可用于发电的总余热量∑Qi(2)物理意义:发电功率D:即是余热发电系统输出功率,单位为kw可用于发电的总余热量∑Qi由以下几部分组成,即∑Qi=QSP+QAQC+Qtt+Qgt,①QSP为可用于发电的窑尾废气余热,其计算方法为:Qsp=Vzs(Tjs·Ctjs-Ths·Cths)+Vys·(Cths·Ths-135×1.42)式中:Qsp—为可用于发电的窑尾总废气热量,KJ/hVzs—窑尾预热器排出的总废气量,Nm3/hTjs—窑尾预热器排出的废气平均温度,℃Ctjs—对应于Tjs的窑尾废气比热,KJ/Nm3·℃Ths—物料烘干所需要的废气平均温度,℃Cths—对于应Ths的窑尾废气比热,KJ/Nm3·℃Vys—扣除物料烘干所需窑尾废气量后剩余的窑尾废气量,Nm3/h135—扣除物料烘干所需窑尾废气量后剩余的窑尾废气进入电收尘器允许的最低温度,135℃1.42—对应于135℃的窑尾废气比热,1.42KJ/Nm3·℃②QAQC为可用于发电的窑头废气余热,其计算方法为:QAQC=VZA·TjA·CtjA式中:QAQC—可用于发电的窑头总废气余热量,KJ/hVZA—电站不投入运行时(或电站投产前)冷却机总排入大气的废气量,Nm3/hTjA—电站不投入运行时(或电站投产前)冷却机总排入大气的废气平均温度,℃CtjA—对应于TjA的冷却机排入大气废气比热,KJ/Nm3·℃③Qtt为用于发电的窑胴体废热热量,单位为KJ/h。