铁矿粉烧结生产工艺流程
详述烧结工艺的具体流程

烧结厂工艺技术规程第一章概述烧结生产是现代钢铁联合企业的重要组成部分。
烧结是铁矿粉造块的主要方法之一,是为高炉冶炼提供“精料”的重要措施。
烧结矿的产质量直接影响高炉生铁的产质量和焦化。
因此,发展烧结生产,不断提高烧结矿的产、质量,对提高企业经济效益和促进钢铁工业的发展具有重要意义。
我厂烧结用含铁原料由公司码头的2台500t/h桥式抓斗卸船机卸下,通过皮带运输机及三台DQLK300/600-25型斗轮堆取料机(定点堆积)堆放到一次料场,小批量的高炉灰、转炉灰及轧钢皮通过车运至一次料场附近堆放,再通过推取料机、前装载机按照原料场一次配料的需要,有皮带机送至一次配料仓,一次配料按规定指标配制成铁料混匀料,铁料混匀料通过皮带机送至规格为HDB600.19.5小型混匀机,混匀堆料机通过往复走行不间断堆积以造长堆为主,达到分层匀矿的目的,再由规格为QLQS2 400-30桥式双斗轮取料机从铁料混匀料堆的横断面截取,皮带机送烧结配料仓进行二次配料,通过对铁料的平铺截取、中和混匀,使得铁料混匀后TFe和SiQ2波动范围比混匀前大大缩写,标准偏差在规定范围之内,稳定了原料的化学成分。
1.1.2.2溶剂准备:白云石、石灰石粉由公司供应部门直接外购质量符合要求的合格产品,通过码头带机运至原料场堆存,使用时,再由原料场皮带机运至烧结配料仓进行二次配料。
生石灰粉由金康集团石灰厂生产的生石灰经破碎后供给,通过风动输送将生石灰粉送至烧结配料仓。
1.1.2.3燃料准备燃料焦屑、无烟煤破碎,为烧结配料工序准备符合要求的燃料,粗破为对辊,细破为四辊,破碎后的燃料粒度≤3㎜的部分达80%以上。
1.1.2.4配料与混合制粒1.1.2.4.1配料:其任务是根据技术要求和烧结矿的化学成分,通过计算按比例进行给料,保证混合料和烧结矿化学成分的稳定。
1.1.2.4.2混合与制粒:其任务是加水润湿混合料,使混合料混匀和制粒,并担负混合料的预热。
烧结和球团
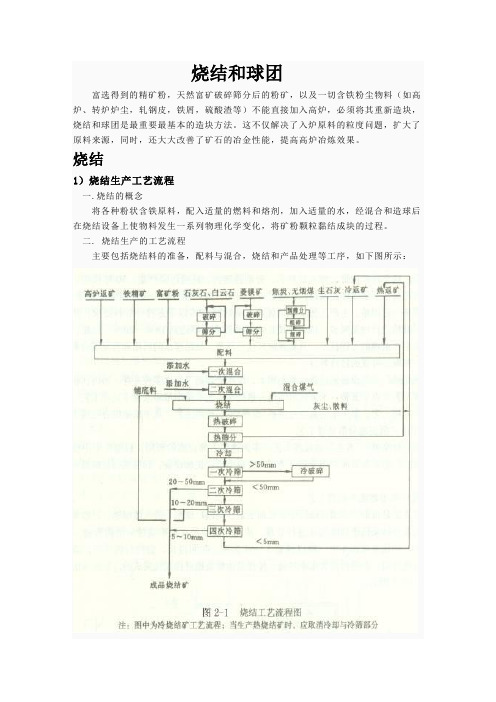
烧结和球团富选得到的精矿粉,天然富矿破碎筛分后的粉矿,以及一切含铁粉尘物料(如高炉、转炉炉尘,轧钢皮,铁屑,硫酸渣等)不能直接加入高炉,必须将其重新造块,烧结和球团是最重要最基本的造块方法。
这不仅解决了入炉原料的粒度问题,扩大了原料来源,同时,还大大改善了矿石的冶金性能,提高高炉冶炼效果。
烧结1)烧结生产工艺流程一.烧结的概念将各种粉状含铁原料,配入适量的燃料和熔剂,加入适量的水,经混合和造球后在烧结设备上使物料发生一系列物理化学变化,将矿粉颗粒黏结成块的过程。
二. 烧结生产的工艺流程主要包括烧结料的准备,配料与混合,烧结和产品处理等工序,如下图所示:1.烧结原料的准备①含铁原料含铁量较高、粒度<5mm的矿粉,铁精矿,高炉炉尘,轧钢皮,钢渣等。
一般要求含铁原料品位高,成分稳定,杂质少。
②熔剂要求熔剂中有效CaO含量高,杂质少,成分稳定,含水3%左右,粒度小于3mm 的占90%以上。
在烧结料中加入一定量的白云石,使烧结矿含有适当的MgO,对烧结过程有良好的作用,可以提高烧结矿的质量。
③燃料主要为焦粉和无烟煤。
对燃料的要求是固定碳含量高,灰分低,挥发分低,含硫低,成分稳定,含水小于10%,粒度小于3mm的占95%以上。
2.配料与混合配料目的:获得化学成分和物理性质稳定的烧结矿,满足高炉冶炼的要求。
混合目的:使烧结料的成分均匀,水分合适,易于造球,从而获得粒度组成良好的烧结混合料,以保证烧结矿的质量和提高产量。
混合作业:加水润湿、混匀和造球。
根据原料性质不同,可采用一次混合或二次混合两种流程。
一次混合的目的:润湿与混匀,当加热返矿时还可使物料预热。
二次混合的目的:继续混匀,造球,以改善烧结料层透气性。
3.烧结生产烧结作业是烧结生产的中心环节,它包括布料、点火、烧结等主要工序。
①布料将铺底料、混合料铺在烧结机台车上的作业。
当采用铺底料工艺时,在布混合料之前,先铺一层粒度为10~25mm,厚度为20~25mm 的小块烧结矿作为铺底料,其目的是保护炉箅,降低除尘负荷,延长风机转子寿命,减少或消除炉箅粘料。
烧结工艺介绍

烧结工艺的简单介绍目前,随着市场竞争的加剧,钢铁工业设备向大型化发展,对原料的要求日益提高,而高炉炼铁生产技术指标的提高,主要依靠入炉原料性质的改善,烧结矿是我国高炉的主要入炉料,因此,保证和提高烧结矿的质量,是保证钢铁工业稳定发展的重要手段。
一、烧结的概念烧结是钢铁生产工艺中的一个重要环节,它是将各种粉状含铁原料,配入适量的燃料和熔剂,加入适量的水,经混合和造球后在烧结设备上使物料发生一系列物理化学变化,将矿粉颗粒黏结成块的过程。
二、烧结矿的来源以及意义铁矿粉造块目前主要有两种方法:烧结法和球团法。
两种方法所获得的块矿分别为烧结矿和球团矿。
球团法通常在选贫矿的地区采用,尤其是北美地区。
而在有天然富矿可以开采使用的地方,烧结法则是一种成本较低的方法,在世界的其它地区被广泛采用。
虽然新的炼铁方法会不断出现,但是烧结矿的需求在很长一段时间内仍将保持在较高的水平。
在我国,高炉入炉的炉料90%^上都是靠烧结法提供的。
因此,铁矿石烧结对我国的钢铁工业有重大的意义。
三、烧结工艺流程介绍经烧结而成的有足够强度和粒度的烧结矿可作为炼铁的熟料。
利用烧结熟料炼铁对于提高高炉利用系数、降低焦比、提高高炉透气性保证高炉运行均有一定意义。
烧结生产的工艺流程如下图所示。
主要包括烧结料的准备,配料与混合, 烧结和产品处理等工序。
[警_1水I ~Sri~ —»j _|~点火: *%结礦辟rwv ~~iI讨烧站矿上鹿炉旷棺1、烧结的原材料准备:含铁原料:含铁量较高、粒度<5mm 的矿粉,铁精矿,高炉炉尘,轧钢皮, 钢渣等。
一般要求含铁原料品位高,成分稳定,杂质少。
熔剂:要求熔剂中有效CaO 含量高,杂质少,成分稳定,含水3%左右,粒 度小于3mm 的占90%以上。
在烧结料中加入一定量的白云石,使烧结矿含有适 当的MgQ 对烧结过程有良好的作用,可以提高烧结矿的质量。
燃料:主要为焦粉和无烟煤。
对燃料的要求是固定碳含量高,灰分低,挥 发分低,含硫低,成分稳定,含水小于 10%,粒度小于3mm 勺占95%以上。
炼铁的炼制过程

炼铁是将铁矿石在高炉中还原,得到生铁的过程。
具体的炼制过程如下:
1. 烧结:将铁矿石、燃料和熔剂混合后,在烧结机上进行烧结,制成烧结矿。
2. 焦化:将煤在焦炉中进行干馏,制成焦炭。
3. 炼铁:将烧结矿、焦炭和石灰石等原料按一定比例装入高炉,从高炉下部的风口吹入热风,在高温下进行还原反应,生成生铁和炉渣。
4. 炼钢:将生铁在转炉或电炉中进行炼钢,去除生铁中的杂质,制成钢水。
5. 连铸:将钢水通过连铸机铸成钢坯。
需要注意的是,在炼制过程中需要严格控制各项参数,以保证生铁和钢的质量。
同时,还需要对产生的废气、废水和废渣进行处理,以保护环境。
铁矿石的烧结与冶炼

04
铁矿石烧结与冶炼的环境 影响与控制
大气污染物排放与控制
大气污染物排放
在铁矿石的烧结和冶炼过程中,会产生大量的烟尘、二氧化硫、氮氧化物等大气污染物。这些污染物不仅对环境 造成严重污染,还会对人类健康产生严重影响。
02
铁矿石烧结过程
原料准备
01
02
03
铁矿石
选择品位高、成分稳定的 铁矿石作为原料,确保烧 结矿的质量和产量。
燃料
通常使用焦粉或煤粉作为 燃料,提供烧结所需的热 量。
熔剂
加入适量的熔剂,如石灰 石、白云石等,以调整烧 结矿的矿物组成和化学成 分。
配料与混料
配料
根据原料的化学成分和烧结矿的质量 要求,计算各种原料的配比,确保烧 结矿的品位、碱度和其它化学成分符 合要求。
利用
将处理后的烧结矿作为高炉炼铁的原 料,通过高炉冶炼提取出铁水,进一 步加工成各种钢材和铁制品。
03
铁矿石冶炼工艺
直接还原冶炼
直接还原冶炼是一种将铁矿石在还原气氛下进行高温处理,直接将铁矿石中的铁 氧化物还原成金属铁的过程。该工艺通常使用气体或固体还原剂,如天然气、煤 、焦炭等。
直接还原冶炼工艺具有流程短、能耗低、污染小等优点,但生产出的铁金属品位 较低,通常需要进一步加工处理。
混料
将各种原料按照配比混合均匀,确保 烧结过程中各组分能够均匀反应。
烧结矿的冷却与破碎
冷却
烧结矿从烧结机下来后,通过冷却设备将其冷却至适宜的温度,以利于后续的破 碎和运输。
破碎
烧结矿冷却后,经过破碎设备将其破碎至合适的粒度,以便于高炉冶炼。
烧结及工艺流程
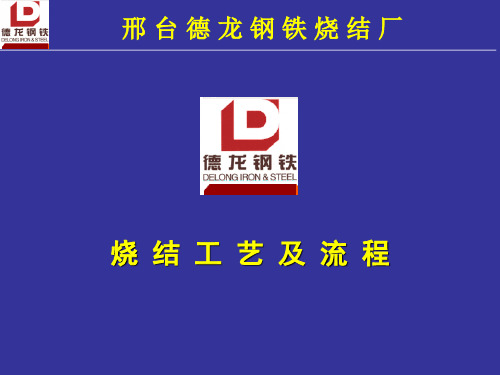
MgO 3.08 4.75 2.96 38.00 9.14 0.33 0.63 0.47 0.38
邢台德龙钢铁烧结厂
焦粉通过四辊破碎机进行破碎,并通过皮带输送到原料 料仓,其他原料直接由天车运至料仓,通过计算,按一 定的配料比进行自动配料,通过配料皮带输送至混料皮 带;混合料配加各除尘产物,并输送至一次混合机,经 一次混合机混匀、加水润湿,经皮带输送至二次混合机, 进行充分混匀、制粒,再由皮带运送至混合料矿槽;混 合料通过圆辊与多辊布料机,布到台车上,并适当平料。 布好的混合料进行点火并通过抽风作用,使混合料中的 焦粉燃烧,产生高温,混合物软化或熔化,生成液相, 随温度降低,液相冷却而凝固成块;抽风烧结完毕后, 经单辊破碎机将烧结料破碎,再经环式冷却机,通过鼓 风进行冷却,冷却完毕后通过振动筛进行筛分、整粒后 直接进入成品仓,最后经皮带送至高炉。
它对烧结过程及烧结矿产量、品质影响很大。 烧结燃料是指在烧结料层中燃烧的固体燃料,常用
的是焦粉和无烟煤粉,我厂主要使用焦粉。 对烧结所使用的固体燃料总的要求是:固定碳含量
高、挥发分、灰分、硫含量要低。
邢台德龙钢铁烧结厂
三、烧结工艺流程
烧结生产过程就是根据炼铁的要求,将细粒的含铁 原料、熔剂、燃料进行配料、混合造球、铺料点火、抽 风烧结,而后再降温固结,经破碎筛分、冷却整粒后把 成品烧结矿运往高炉。
41.5 Al2O3
SiO2 0.52 0.36 0.15 0.21 0.20 0.73 1.13 0.85 1.17 0.28 5.59 2.74
烧结与烧结矿制备
烧结矿的市场需求
钢铁产业发展
随着全球钢铁产业的不断发展,对烧结矿的需求也不断增长。
基础设施建设
基础设施建设对烧结矿的需求较大,特别是在发展中国家。
环保政策影响
各国政府对环保的重视程度不断提高,对烧结矿的生产和消费产生 一定影响。
烧结矿的发展趋势
1 2
高效低耗
提高烧结矿的生产效率和降低能耗是未来的重要 发展方向。
土壤污染
烧结矿生产过程中产生的废渣 和废弃物随意堆放,对土壤造 成污染。
资源消耗
烧结矿生产需要大量的矿石、 燃料等资源,加剧了资源的开
采和消耗。
烧结矿的可持续发展策略
清洁生产
采用先进的生产工艺和 技术,减少烧结过程中 的污染物排放,提高资
源利用弃物的产生,提 高经济效益和环境效益
满足使用要求。
粒度与级配
对烧结矿的粒度和级配进行控制 ,以满足高炉冶炼的要求。
03
烧结矿的应用与市场
烧结矿的应用领域
钢铁行业
烧结矿是钢铁冶炼的主要原料之一,用于高炉炼 铁,提高生铁产量和质量。
化工行业
烧结矿中的某些成分可用于生产硫酸、磷酸等化 工产品。
建筑行业
烧结矿可作为建筑材料,如混凝土骨料、砖瓦等 。
环保生产
加强环保措施,减少烧结矿生产过程中的污染物 排放。
3
多元化应用
拓展烧结矿在非钢铁行业的应用领域,提高其附 加值。
04
烧结矿的环境影响与可持续发展
烧结矿的环境影响
空气污染
烧结过程中产生的烟尘和废气 排放对大气环境造成污染,影
响空气质量。
水体污染
烧结矿生产过程中产生的废水 未经处理直接排放,对周边水 体造成污染。
铁矿粉烧结理论
烧结速度/mm/min
21 20 19 18 17 16 15 14 1.6 1.5 1.4 1.3 1.2 1.1 1.0 29 28 27 26 25 24 23 22 21 4.1 4.0 3.9 3.8 3.7 3.6 3.5 4.0 4.5 5.0 5.5 6.0 6.5 3.5 4.0 4.5 5.0 5.5 6.0 6.5
一般来说,碳的燃烧在较低温度和氧含量较高的条件下,以生成CO2为主;在较高 温度和氧含量较低的条件下,以生成CO为主。烧结废气中,碳的氧化物是以CO2为 主,只含少量的CO。
图4-2 在烧结试验过程测得废气中的 氧气、二氧化碳和一氧化碳的变化
(试验所用燃料量为7%)
通常用燃烧比(CO/CO+CO2)来衡量烧结过程中碳的化学能利用程度,用废气成分 来衡量烧结过程的气氛。燃烧比大则碳的利用差,还原性气氛较强,反之碳的利用 好,氧化气氛较强。还原性气氛较强时,CO可以将Fe2O3还原为Fe3O4,因此,烧结 混合料中配碳量越过,烧结矿亚铁含量越高。 影响燃烧比的因素有: a.燃料粒度 (图4-3) b.混合料中燃料含量 (图4-4) c.烧结负压 (图4-5) d.料层高度 (图4-6) e.返矿量 (图4-7)
R
当扩散速率与化学反应同步,即 = 时,整个反应稳定进行, 则碳粒燃烧的总速度为:
V VR KD KR S CO2 KCO2 KD KR
VD
VR
K K K ≈ ,此时,过程的总速度取决于化学 在低温下, K ﹤﹤ , 反应速度,称燃烧处于“动力学燃烧区”。
R D R
在高温下, ﹤﹤ , ≈ ,此时,过程的总速度取决于氧的 扩散速度,称燃烧处于“扩散燃烧区”。 当燃烧处于动力燃烧区时,燃烧速度受温度影响较大,随温 度升高而增加,而不受气流速度、压力和固体燃料粒度的影响。 当燃烧处于扩散燃烧区时,燃烧速度取决于气体的扩散速度, 而温度的改变影响不大。 烧结过程在点火后不到一分钟,料层温度升高到1200℃~ 1350℃,故其燃烧反应基本上是在扩散区内进行,因此,一切 能够增加扩散速度的因素,如减小燃料粒度、增加气流速度 (改善料层透气性、增加风机风量)和气流中的氧含量,都能 提高燃烧反应速度,强化烧结过程。
烧结生产线工艺流程
固体燃料
无烟煤是煤中固定碳含量最高, 挥发份最少的煤。对固体燃料 化学成分要求:固定碳含量高, 灰分、挥发份、含硫低。
固体燃料的运输及破碎
265m2烧结机使用燃料由原料 厂通过皮带机运至烧结区域燃 料破碎室料斗内,经电子皮带 秤直接拖出供三台Φ900×700 四辊破碎机破碎,成品由皮带 机运至配料室。
灰尘由仓式泵气力输送至灰尘仓。
配料室排料系统
混匀矿采用Φ2800圆盘给料机 排料,配料电子秤称重;
燃料和熔剂及冷返矿直接用配 料电子秤拖出;
生石灰的排料、称量及消化通 过叶轮给料机、螺旋秤及消化 器完成。
配料室排料系统
灰尘经叶轮给料机、螺旋、加 湿机、配料电子秤称重;
以上几种原料按设定比例经称 量后给到混合料的胶带机上, 送往一次混合室。
二次混合机为了提高混合料温度, 混合机配一套蒸汽预热装置。
混合机组成
根据烧结工艺的要求,该设备配 有一套喷水装置,以保证物料达 到一定湿度,从而有利于混合和 造球。为了便于观察物料混合情 况,给水法兰设置在排料端,给 水阀门由烧结工艺配置,用来调 节给水量的大小。
烧结室
烧结机的有效抽风面积为 265m2,台车宽度3.5m,栏 板 高 度700mm。经点火炉点 火后开始烧结,烧结终结的热 烧结饼经机尾卸至 Φ2000×3740mm的单辊破碎 机。
配
料
配料是按烧结矿的质量指标要求和 原料成分将各种烧结料按一定比例 配合在一起的工序过程。
265m烧结机采用单列配料室,共 设14个矿槽(为称重矿槽),其中 混匀矿5个、灰尘仓1个、冷返矿2 个、燃料2个、石灰石2个、生石灰 2 个。
配料
配料目前一般有两种方法,即容 积配料法和质量配料法。
铁矿粉烧结生产工艺流程
1.烧结的概念将各种粉状含铁原料,配入适量的燃料和熔剂,加入适量的水,经混合和造球后在烧结设备上使物料发生一系列物理化学变化,将矿粉颗粒黏结成块的过程。
2. 烧结生产的工艺流程目前生产上广泛采用带式抽风烧结机生产烧结矿。
烧结生产的工艺流程如图2 —4 所示。
主要包括烧结料的准备,配料与混合,烧结和产品处理等工序。
图2-4 抽风烧结工艺流程◆烧结原料的准备①含铁原料含铁量较高、粒度<5mm 的矿粉,铁精矿,高炉炉尘,轧钢皮,钢渣等。
普通要求含铁原料品位高,成份稳定,杂质少。
②熔剂要求熔剂中有效CaO 含量高,杂质少,成份稳定,含水3%摆布,粒度小于3mm 的占90%以上。
在烧结料中加入一定量的白云石,使烧结矿含有适当的MgO,对烧结过程有良好的作用,可以提高烧结矿的质量。
③燃料主要为焦粉和无烟煤。
对燃料的要求是固定碳含量高,灰分低,挥发分低,含硫低,成份稳定,含水小于10%,粒度小于3mm 的占95%以上。
对入厂烧结原料的普通要求见表2 —2。
表2-2 入厂烧结原料普通要求◆配料与混合①配料配料目的:获得化学成份和物理性质稳定的烧结矿,满足高炉冶炼的要求。
常用的配料方法:容积配料法和质量配料法。
容积配料法是基于物料堆积密度不变,原料的质量与体积成比例这一条件进行的。
准确性较差。
质量配料法是按原料的质量配料。
比容积法准确,便于实现自动化。
②混合混合目的:使烧结料的成份均匀,水分合适,易于造球,从而获得粒度组成良好的烧结混合料,以保证烧结矿的质量和提高产量。
混合作业:加水润湿、混匀和造球。
根据原料性质不同,可采用一次混合或者二次混合两种流程。
一次混合的目的:润湿与混匀,当加热返矿时还可使物料预热。
二次混合的目的:继续混匀,造球,以改善烧结料层透气性。
用粒度10~Omm 的富矿粉烧结时,因其粒度已经达到造球需要,采用一次混合,混合时间约50s。
使用细磨精矿粉烧结时,因粒度过细,料层透气性差,为改善透气性,必须在混合过程中造球,所以采用二次混合,混合时间普通不少于2.5~3min。
- 1、下载文档前请自行甄别文档内容的完整性,平台不提供额外的编辑、内容补充、找答案等附加服务。
- 2、"仅部分预览"的文档,不可在线预览部分如存在完整性等问题,可反馈申请退款(可完整预览的文档不适用该条件!)。
- 3、如文档侵犯您的权益,请联系客服反馈,我们会尽快为您处理(人工客服工作时间:9:00-18:30)。
铁矿粉烧结生产工艺流程1.烧结的概念将各种粉状含铁原料,配入适量的燃料和熔剂,加入适量的水,经混合和造球后在烧结设备上使物料发生一系列物理化学变化,将矿粉颗粒黏结成块的过程。
2. 烧结生产的工艺流程目前生产上广泛采用带式抽风烧结机生产烧结矿。
烧结生产的工艺流程如图2—4所示。
主要包括烧结料的准备,配料与混合,烧结和产品处理等工序。
图2-4 抽风烧结工艺流程◆烧结原料的准备①含铁原料含铁量较高、粒度<5mm的矿粉,铁精矿,高炉炉尘,轧钢皮,钢渣等。
②熔剂要求熔剂中有效CaO含量高,杂质少,成分稳定,含水3%左右,粒度小于3mm的占90%以上。
在烧结料中加入一定量的白云石,使烧结矿含有适当的MgO,对烧结过程有良好的作用,可以提高烧结矿的质量。
③燃料主要为焦粉和无烟煤。
对燃料的要求是固定碳含量高,灰分低,挥发分低,含硫低,成分稳定,含水小于10%,粒度小于3mm 的占95%以上。
对入厂烧结原料的一般要求见表2—2。
表2-2 入厂烧结原料一般要求◆配料与混合①配料配料目的:获得化学成分和物理性质稳定的烧结矿,满足高炉冶炼的要求。
常用的配料方法:容积配料法和质量配料法。
容积配料法是基于物料堆积密度不变,原料的质量与体积成比例这一条件进行的。
准确性较差。
质量配料法是按原料的质量配料。
比容积法准确,便于实现自动化。
②混合混合目的:使烧结料的成分均匀,水分合适,易于造球,从而获得粒度组成良好的烧结混合料,以保证烧结矿的质量和提高产量。
混合作业:加水润湿、混匀和造球。
根据原料性质不同,可采用一次混合或二次混合两种流程。
一次混合的目的:润湿与混匀,当加热返矿时还可使物料预热。
二次混合的目的:继续混匀,造球,以改善烧结料层透气性。
用粒度10~Omm的富矿粉烧结时,因其粒度已经达到造球需要,采用一次混合,混合时间约50s。
使用细磨精矿粉烧结时,因粒度过细,料层透气性差,为改善透气性,必须在混合过程中造球,所以采用二次混合,混合时间一般不少于2.5~3min。
我国烧结厂大多采用二次混合。
◆烧结生产烧结作业是烧结生产的中心环节,它包括布料、点火、烧结等主要工序。
①布料将铺底料、混合料铺在烧结机台车上的作业。
当采用铺底料工艺时,在布混合料之前,先铺一层粒度为10~25mm,厚度为20~25mm的小块烧结矿作为铺底料,其目的是保护炉箅,降低除尘负荷,延长风机转子寿命,减少或消除炉箅粘料。
铺完底料后,随之进行布料。
布料时要求混合料的粒度和化学成分等沿台车纵横方向均匀分布,并且有一定的松散性,表面平整。
目前采用较多的是圆辊布料机布料。
②点火点火操作是对台车上的料层表面进行点燃,并使之燃烧。
点火要求有足够的点火温度,适宜的高温保持时间,沿台车宽度点火均匀。
点火温度取决于烧结生成物的熔化温度。
常控制在1250±50℃。
点火时间通常40~60s。
点火真空度4~6kPa。
点火深度为10~20mm。
③烧结准确控制烧结的风量、真空度、料层厚度、机速和烧结终点。
烧结风量:平均每吨烧结矿需风量为3200m3,按烧结面积计算为(70~90)m3/(cm2.min)。
真空度:决定于风机能力、抽风系统阻力、料层透气性和漏风损失情况。
料层厚度:合适的料层厚度应将高产和优质结合起来考虑。
国内一般采用料层厚度为250~500mm。
机速:合适的机速应保证烧结料在预定的烧结终点烧透烧好。
实际生产中,机速一般控制在1.5~4m/min为宜。
烧结终点的判断与控制:控制烧结终点,即控制烧结过程全部完成时台车所处的位置。
中小型烧结机终点一般控制在倒数第二个风箱处,大型烧结机控制在倒数第三个风箱处。
带式烧结机抽风烧结过程是自上而下进行的,沿其料层高度温度变化的情况一般可分为5层,各层中的反应变化情况如图2—5所示。
点火开始以后,依次出现烧结矿层,燃烧层,预热层,干燥层和过湿层。
然后后四层又相继消失,最终只剩烧结矿层。
图2-5烧结过程各层反应示意图经高温点火后,烧结料中燃料燃烧放出大量热量,使料层中矿物产生熔融,随着燃烧层下移和冷空气的通过,生成的熔融液相被冷却而再结晶(1000—1100℃)凝固成网孔结构的烧结矿。
这层的主要变化是熔融物的凝固,伴随着结晶和析出新矿物,还有吸入的冷空气被预热,同时烧结矿被冷却,和空气接触时低价氧化物可能被再氧化。
②燃烧层燃料在该层燃烧,温度高达1350~1600℃,使矿物软化熔融黏结成块。
该层除燃烧反应外,还发生固体物料的熔化、还原、氧化以及石灰石和硫化物的分解等反应。
③预热层由燃烧层下来的高温废气,把下部混合料很快预热到着火温度,一般为400~800℃。
此层内开始进行固相反应,结晶水及部分碳酸盐、硫酸盐分解,磁铁矿局部被氧化。
④干燥层干燥层受预热层下来的废气加热,温度很快上升到100℃以上,混合料中的游离水大量蒸发,此层厚度一般为l0~30mm。
实际上干燥层与预热层难以截然分开,可以统称为干燥预热层。
该层中料球被急剧加热,迅速干燥,易被破坏,恶化料层透气性。
⑤过湿层从干燥层下来的热废气含有大量水分,料温低于水蒸气的露点温度时,废气中的水蒸气会重新凝结,使混合料中水分大量增加而形成过湿层。
此层水分过多,使料层透气性变坏,降低烧结速度。
烧结过程中的基本化学反应①固体碳的燃烧反应固体碳燃烧反应为:反应后生成C0和C02,还有部分剩余氧气,为其他反应提供了氧化还原气体和热量。
燃烧产生的废气成分取决于烧结的原料条件、燃料用量、还原和氧化反应的发展程度、以及抽过燃烧层的气体成分等因素。
②碳酸盐的分解和矿化作用烧结料中的碳酸盐有CaC03、MgC03、FeC03、MnC03等,其中以CaC03为主。
在烧结条件下,CaC03在720℃左右开始分解,880℃时开始化学沸腾,其他碳酸盐相应的分解温度较低些。
碳酸钙分解产物Ca0能与烧结料中的其他矿物发生反应,生成新的化合物,这就是矿化作用。
反应式为:CaCO3+SiO2=CaSiO3+CO2CaCO3+Fe2O3=CaO ·Fe2O3+ CO2如果矿化作用不完全,将有残留的自由Ca0存在,在存放过程中,它将同大气中的水分进行消化作用:CaO+H2O=Ca(OH)2使烧结矿的体积膨胀而粉化。
③铁和锰氧化物的分解、还原和氧化铁的氧化物在烧结条件下,温度高于l300℃时,Fe203可以分解:Fe304在烧结条件下分解压很小,但在有Si02存在、温度大于1300℃时,也可能分解:烧结矿的冷却与整粒一、烧结矿冷却的目的和意义烧结矿在烧结机上烧成后从机尾卸下时其温度大约在600~1000℃,对这样的赤热烧结矿,在现代化得烧结厂中,一般却要将其冷却到150℃以下,这是因为以下几个原因:1、保护运输设备,使厂区配置紧凑。
如果烧结矿不冷却,运送赤热得烧结矿就需要使用较多得专用矿车来装载,当烧结配比不当、残碳较多时,烧结矿还会在专用得矿车中继续燃烧,致使矿车烧坏变形,而且使用矿车时还要有较长的铁路运输线,会使烧结厂与炼铁厂在配置上不得不拉得很远。
若将烧结矿冷却就可采用胶带机运输,使厂区配置紧凑,少占农田用地。
使有时要停止生产修补矿槽,影响作业率,降低产量。
使用不经过冷却得烧结矿,高炉炉顶温度高,为了保护炉顶设备,一般炉顶压力不敢提高。
而使用冷烧结矿,可以提高炉顶压力,对强化高炉冶炼、提高产质量有利,高炉的上料系统及炉顶设备不易损坏,使用寿命也大大提高了。
3、改善高炉、烧结厂的劳动条件。
由于烧结矿冷却后可以筛除粉末,冷烧结矿在由烧结厂到高炉矿槽以及高炉上料系统的一系列装卸运输运转过程所产生的污染环境的灰尘比热烧结矿大大减少,从而改善了劳动条件和环境卫生。
4、为烧结矿的整粒及分出铺底料创造了条件。
烧结矿不经过冷却,由于温度高,很难进行较彻底的破碎筛分以及分出烧结厂需要的铺底料。
烧结矿冷却到150℃以下,就可使用在常温下工作的破碎机,筛子及胶带运输机进行冷破碎,以及多次的筛分运输作业,较彻底地筛除粉末(5~0mm),分出铺底料(10~20mm)。
5、为实现高炉生产技术现代化创造条件。
现代化的高炉生产技术已发展到超高压炉顶操作,无料钟炉顶,胶带机炉顶上料,外燃式热风炉,炉内料位控制等等,所有这些都必须建立在烧结矿冷却及整粒分级的基础上,因而烧结矿如不冷却也无法实现高炉技术现代化。
二、烧结矿的冷却方法烧结矿的冷却方法很多,从方法上来分,有自然冷却和强制通风冷却两类;从冷却的地点和设备来分,有烧结机外冷却和烧结机上冷却两种。
1、烧结机外冷却,即烧结矿在烧结机上烧成之后卸出来,另外进行冷却,其方法有以下几种:(1)在空气中自然冷却。
由于效率低、时间长、不能连续作业、环境条件差等原因,现在已不再采用。
(2)强制通风冷却。
热烧结矿在卸离烧结机后,经过筛分,除去粉末,然后在特制的冷却机中强制通风的办法使其冷却下来。
强制通风的方法有两种:一种是抽风冷却,另一种是鼓风冷却。
采用强制通风的冷却机的种类很多,主要有鼓风或抽风带式冷却机、鼓风或抽风环式冷却机、盘式冷却机、格式冷却机、塔式振动冷却机、水平式振动冷却机等,使用效果较好的有鼓风或抽风带式冷却机、鼓风或抽风环式冷却机。
2、机上冷却。
机上冷却的方法是将烧结机延长,将烧结机的前段作为烧结段,后段作为冷却段,当台车上的混合料在烧结段已烧成为烧结矿后,台车继续前进,进入冷却段,通过抽风将热烧结矿冷却下来,冷却的空气是通过烧结饼的裂缝、孔隙以及冷却过程中因收缩而新产生的裂隙将烧结矿冷却下来,一般情况下烧结段与冷却段备有专用的风机。
三、烧结矿整粒的目的和意义烧结矿的整粒,就是对烧结矿进行破碎、筛分、控制烧结矿上、下限粒度,并按需要进行粒度分级,以达到提高烧结矿质量的目的。
烧结机的铺底料也在筛分过程中分出。
经过整粒后的烧结矿粒度均匀、粉末少、强度高,对改善高炉冶炼指标有很大作用。
一般情况下,烧结矿整粒后保持在50~5mm(或60~5mm,对于小型高炉可保持在35~5mm)范围内,其中经整粒后的粉末含量(5~0mm),不超过5%。
1、使供给高炉的成品烧结矿粉末量降到最低限度。
在整粒过程中烧结矿要经过多次筛分,小于5mm 粒级的粉末得到较彻底的筛除,一般情况下整粒后出厂的烧结矿小于5mm粒级含量小于5%,且由于经过破碎,没有大块,在运转过程中新生的小于5mm粒级不再增加。
小于5mm的粉末减少大大有利于高炉料柱透气性的改善,有利于高炉的顺行,从而使高炉节焦增产。
2、消除大块烧结矿,烧结矿各级含量趋于合理。
一般整粒流程中首先将烧结矿进行一次冷破碎,控制烧结矿的上限不大于50mm(或60mm),这样就消除了烧结矿中的过大块(100~150mm粒级),使成品烧结矿各级粒度趋于合理。
过大块烧结矿的存在使高炉布料产生偏析,不利于料柱透气性的均匀分布。