位置随动控制系统设计与实现
激光切割Z轴位置随动控制系统设计
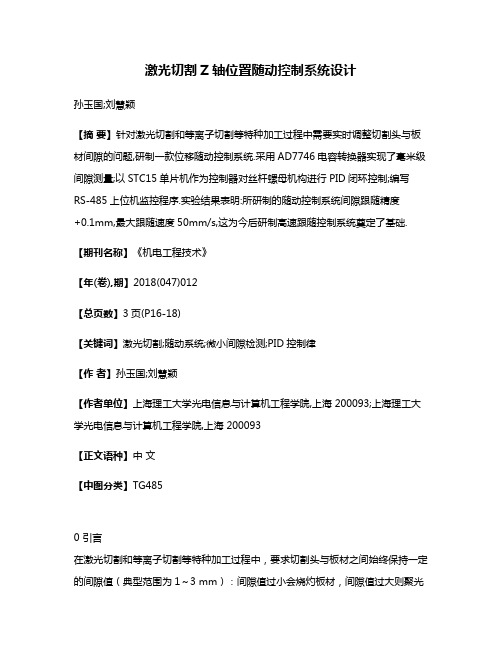
激光切割Z轴位置随动控制系统设计孙玉国;刘慧颖【摘要】针对激光切割和等离子切割等特种加工过程中需要实时调整切割头与板材间隙的问题,研制一款位移随动控制系统.采用AD7746电容转换器实现了毫米级间隙测量;以STC15单片机作为控制器对丝杆螺母机构进行PID闭环控制;编写RS-485上位机监控程序.实验结果表明:所研制的随动控制系统间隙跟随精度+0.1mm,最大跟随速度50mm/s,这为今后研制高速跟随控制系统奠定了基础.【期刊名称】《机电工程技术》【年(卷),期】2018(047)012【总页数】3页(P16-18)【关键词】激光切割;随动系统;微小间隙检测;PID控制律【作者】孙玉国;刘慧颖【作者单位】上海理工大学光电信息与计算机工程学院,上海 200093;上海理工大学光电信息与计算机工程学院,上海 200093【正文语种】中文【中图分类】TG4850 引言在激光切割和等离子切割等特种加工过程中,要求切割头与板材之间始终保持一定的间隙值(典型范围为1~3 mm):间隙值过小会烧灼板材,间隙值过大则聚光能量不足、加工件出现毛刺[1-3]。
从运动控制原理来看,这是一个典型的位移随动负反馈控制系统[4-8]。
目前,国内激光切割和等离子切割设备生产厂家一般不具备位移随动控制系统的研发能力,多通过购买国外的调高器与设备的X、Y轴实现联动。
鉴于以上工程背景,设计一款丝杆螺母驱动的位移随动控制系统,其跟随精度+0.1 mm,最大跟随速度50 mm/s,可望为国内激光切割设备生产厂家的自主研发提供理论参考。
1 位移随动控制系统框图位移随动控制系统框图如图1所示:受机架振动和板材自身凹凸不平的影响,切割头与板材之间的间隙会时刻发生变化,可由变间隙式电容传感器检测。
通过PID 负反馈控制,可在线调节滚珠丝杠滑台的运动速度和运动方向,从而实时调整切割头与板材之间的间隙值。
可通过RS-485接口与工控机进行通信,以便于Z轴间隙数的设定以及与X、Y轴控制系统的集成。
《自动控制原理》课程设计位置随动系统的超前校正
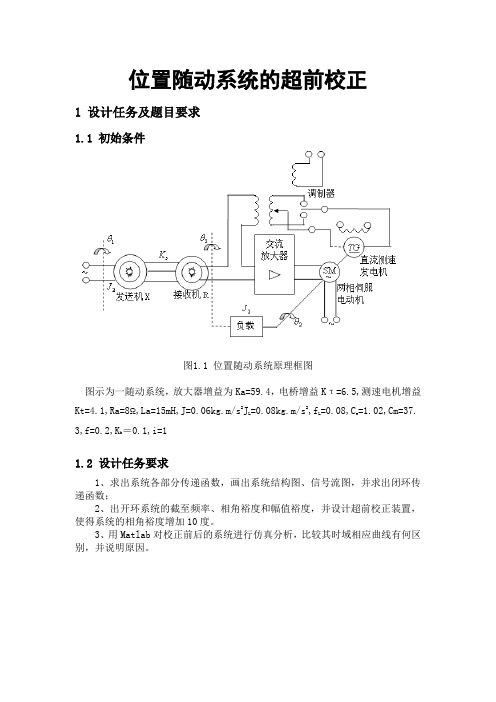
位置随动系统的超前校正1 设计任务及题目要求1.1 初始条件图1.1 位置随动系统原理框图图示为一随动系统,放大器增益为Ka=59.4,电桥增益Kτ=6.5,测速电机增益Kt=4.1,Ra=8Ω,La=15mH,J=0.06kg.m/s2JL =0.08kg.m/s2,fL=0.08,Ce=1.02,Cm=37.3,f=0.2,Kb=0.1,i=11.2 设计任务要求1、求出系统各部分传递函数,画出系统结构图、信号流图,并求出闭环传递函数;2、出开环系统的截至频率、相角裕度和幅值裕度,并设计超前校正装置,使得系统的相角裕度增加10度。
3、用Matlab对校正前后的系统进行仿真分析,比较其时域相应曲线有何区别,并说明原因。
2 位置随动系统原理2.1 位置随动系统工作原理工作原理:该系统为一自整角机位置随动系统,用一对自整角机作为位置检测元件,并形成比较电路。
发送自整角机的转自与给定轴相连;接收自整角机的转子与负载轴(从动轴)相连。
TX 与TR 组成角差测量线路。
若发送自整角机的转子离开平衡位置转过一个角度1θ,则在接收自整角机转子的单相绕组上将感应出一个偏差电压e u ,它是一个振幅为em u 、频率与发送自整角机激励频率相同的交流调制电压,即sin e em u u t ω=⋅在一定范围内,em u 正比于12θθ-,即12[]em e u k θθ=-,所以可得12[]sin e e u k t θθω=-这就是随动系统中接收自整角机所产生的偏差电压的表达式,它是一个振幅随偏差(12θθ-)的改变而变化的交流电压。
因此,e u 经过交流放大器放大,放大后的交流信号作用在两相伺服电动机两端。
电动机带动负载和接收自整角机的转子旋转,实现12θθ=,以达到跟随的目的。
为了使电动机转速恒定、平稳,引入了测速负反馈。
系统的被控对象是负载轴,被控量是负载轴转角2θ,电动机施执行机构,功率放大器起信号放大作用,调制器负责将交流电调制为直流电供给直流测速发电机工作电压,测速发电机是检测反馈元件。
电力拖动自动控制系统:运动控制系统:第九章

图9-12 双环位置伺服系统结构图
§9.3伺服系统的设计
三.双环位置伺服系统
系统的开环传递函数为
W op (s)
系统的开环放大系数
K p ( i s 1) CT /( jJ ) K ( i s 1) 3 2 is s (Ti s 1) s (Ti s 1)
K
三.双环位置伺服系统
由Routh稳定判据求得系统稳定的条件
i d Ti ( i d ) K ( i d )( i d Ti ( i d )) 1
图9-13 采用PID控制的双环控制伺服系统开环传递函数对数幅频特性
§9.3伺服系统的设计
常用的调节器有比例-微分(PD)调节器、比例-积分(PI)调 节器以及比例-积分-微分(PID)调节器,设计中可根据实际 伺服系统的特征进行选择。
§9.3伺服系统的设计
一.调节器及其传递函数
在系统的前向通道上串联PD调节器校正装置,可以使相位超前, 以抵消惯性环节和积分环节使相位滞后而产生的不良后果。
机械传动机构的状态方程
d m dt j
§9.2伺服系统控制对象的数学模型
一.直流伺服系统控制对象的数学模型
驱动装置的近似等效传递函数
状态方程
Ks Ts s 1
dUd 0 Ks 1 Ud0 uc dt Ts Ts
§9.2伺服系统控制对象的数学模型
一.直流伺服系统控制对象的数学模型
图9-11 双环位置伺服系统
§9.3伺服系统的设计
三.双环位置伺服系统
忽略负载转矩时,带有电流闭环控制对象的传递函数为
Wobj ( s )
PLC—自整角机随动控制系统

PLC—自整角机随动控制系统作者:陆晨吴东御来源:《消费电子》2012年第17期摘要:运用永磁低速同步电动机和自整角机测角位移的工作原理来实现随动系统的运行,PLC A/D工作模块的工作原理调控控制系统,通过PLC技术、伺服系统位置测量技术和机械传动技术,形成了机电一体化的实践平台。
关键词:随动系统;永磁同步低速电动机;自整角机;PLC A/D模块中图分类号:TP275 文献标识码:A 文章编号:1674-7712(2012)14-0071-01对于自整角机随动控制系统,在以往是通过机械结构传动来控制的,本项目通过机电一体化随动控制系统来改变机械位置或角度。
这样的装置耗能少、工作效率高。
一、角位移随动系统的现状与总体设计原理(一)角位移随动系统的现状目前的角位移随动控制系统,如数控机床的刀具给进和工作台的定位控制,工业机器人的工作动作,工业自动导引的运动,国防上的雷达跟踪、导弹制导、火炮瞄准等。
在现代计算机集成制导系统(CIMC)、柔性制造系统(FMS)等领域,位置随动系统得到越来越广泛的应用。
位置随动系统可以分为两类,开环控制系统和闭环控制系统。
相对于闭环控制系统而言,开环控制系统设计更加简单,但其在跟随精度上可能不如闭环控制系统。
但对于一般系统而言开环系统足矣。
(二)总体设计原理本设计的角位移随动系统采用开环设计,首先,通过两台同步电机分别对两根轴驱动,两根轴分别带动三相对接的两台自整角机的转子,当两根轴的转速不同时,输出交流误差电信号,并将此交流电信号经过相敏解调器转换为直流电信号,再输入PLC的AD模块,最后通过PLC驱动电机改变转速,消除转动误差,使两根轴达到同步随动的效果。
二、自整角机的选用及其工作原理(一)自整角机介绍自整角机是利用自整步特性将转角变为交流电压或由转角变为转角的感应式微型电机,在伺服系统中被用作测量角度的位移传感器。
自整角机还可用以实现角度信号的远距离传输、变换、接收和指示。
一类位置随动系统的测速反馈控制

一类位置随动系统的测速反馈控制1位置随动系统原理1.1位置随动系统工作原理图1-1位置随动系统原理图该系统为一自整角机位置随动系统,用一对自整角机作为位置检测元件,并形成比较电路。
发送自整角机的转子与给定轴相连:接收自整角机的转子与负载轴(从动轴)相连。
TX 与TR 组成角差测量线路。
若发送自整角机的转子离开平衡位置转过一个角度r θ,则在接收自整角机的单相绕组转子的单相绕组上将感应出一个偏差电压e u ,它是一个振幅为em u 、频率与发送自整角机激励相同的交流调制电压。
即sin e em u u t ω=∙在一定范围内,em u 正比于r c θθ-,即[]em e r c u k θθ=-,所以可得[]sin e e r c u k t θθω=-这就是随动系统中接收自整角机所产生的偏差电压的表达式,它是一个振幅随偏差()r c θθ-的改变而改变的交流电压。
因此,e u 经过交流放大器放大,放大后的交流信号作用在两相伺服电动机两端。
电动机带动负载和接收自整角机的转子旋转,实现r c θθ=,以达到跟随的目的。
为了使电动机转速恒定、平稳,引入了测速负反馈。
系统的被控对象是负载轴,被控量使负载轴转角c θ,电动机是执行机构,功率放大器器信号放大作用,调制器负责将交流调制为直流电供给直流测速发电机工作电压,测速电动机是检测反馈元件。
1.2单元电路模块分析1.2.1自整角机自整角机是常用的位置检测装置,将角位移或者直线位移转换成模拟电压信号的幅值或相位。
自整角机作为角位移传感器,在位置随动系统中是成对使用的。
与指令轴相连的是发送机,与系统输出轴相连的是接收机。
则自整角机的表达式为()[()()]()r c u t K t t K t εεθθθ=-=∆在零初始条件下,拉氏变换为()()u s K s εθ=∆,则自整角机的传递函数为1()()()u s G s K s εθ==∆ 自整角机的结构图如图1-2所示图1-2 自整角机1.2.2功率放大器由于运算放大器具有输入阻抗很大,输出阻抗小的特点,在工程上被广泛用来作信号放大器。
自动控制原理课程设计
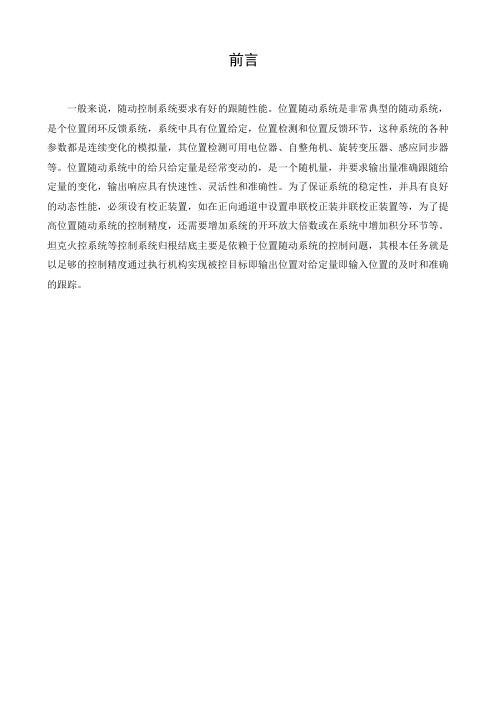
前言一般来说,随动控制系统要求有好的跟随性能。
位置随动系统是非常典型的随动系统,是个位置闭环反馈系统,系统中具有位置给定,位置检测和位置反馈环节,这种系统的各种参数都是连续变化的模拟量,其位置检测可用电位器、自整角机、旋转变压器、感应同步器等。
位置随动系统中的给只给定量是经常变动的,是一个随机量,并要求输出量准确跟随给定量的变化,输出响应具有快速性、灵活性和准确性。
为了保证系统的稳定性,并具有良好的动态性能,必须设有校正装置,如在正向通道中设置串联校正装并联校正装置等,为了提高位置随动系统的控制精度,还需要增加系统的开环放大倍数或在系统中增加积分环节等。
坦克火控系统等控制系统归根结底主要是依赖于位置随动系统的控制问题,其根本任务就是以足够的控制精度通过执行机构实现被控目标即输出位置对给定量即输入位置的及时和准确的跟踪。
1.控制系统的设计步骤根据综述所述,坦克火炮控制系统可抽象为位置随动系统,主要解决位置跟随的控制问题,其根本任务就是通过执行机构实现被控量即输出位置对给定量即输入位置的及时和准确的跟踪,并要求具有足够的控制精度。
根据设计任务的要求,本设计采用双闭环系统,实现输出信号对输入信号的跟踪和复现。
初步设计的环节如下角差检测装置可以选择电位器组成的检测器,或者自整角机检测装置。
有两个运算放大器环节:第一个运放为角差检测装置,它可以选择可以选择电位器组成的检测器,或者自整角机检测装置。
第二个运算放大器:给定电压与反馈电压在此合成,产生偏差电压,将经过该运算放大器放大。
功率放大器:给定电压与反馈电压在此合成,产生偏差电压,经过放大器放大。
执行部件:系统中执行元件可选用电枢控制直流伺服电动机和两相伺服电动机,电枢控制的直流伺服电动机在控制系统中广泛用作执行机构,能够实现对被控对象的机械运动的快速控制。
减速器:减速器对随动系统的工作有重大影响,减速器速比的选择和分配将影响到系统的惯性矩,并影响到快速性。
机电一体化系统设计伺服系统设计
二、伺服电机及其控制
2 直流电机的功率驱动 直流电机的调速电路目前以脉冲宽度调制电路应
用最为广泛.
桥式(H形)PWM变换器主电路
二、伺服电机及其控制
作用在电机两端的 平均电压为:
UAB(2Tton1)Us
二、伺服电机及其控制 3 直流伺服系统模型
二、伺服电机及其控制
1校正环节:一般速度环调节器为比例环节 G1S =Kp
1 系统等效转动惯量 的计算
系统运动部件动能的总和J d为x
E1 2im 1Mi Vi21 2jn1Jj
2 j
二、伺服系统稳态设计
设等效到执行元件输出轴上的总动能为
Edx
1 2
Jdx
d2
根据动能不变的原则,有 Edx ,E系统等效转动惯量
为
Jdxim 1Mi Vid2jn1Jj dj 2
一、方案设计
4.控制系统方案的选择 控制系统方案的选择包括微型机、步进电动机
控制方式、驱动电路等的选择.常用的微型机有单 片机、单板机、工业控制微型机等,其中单片机由 于在体积、成本、可靠性和控制指令功能等许多 方面的优越性,在伺服系统的控制中得到了广泛的 应用.
二、伺服系统稳态设计
系统方案确定后,应进行方案实施的具体化设 计,即各环节设计,通常称为稳态设计.其内容主要 包括执行元件规格的确定、系统结构的设计、系 统惯量参数的计算以及信号检测、转换、放大等 环节的设计与计算.稳态设计要满足系统输出能力 指标的要求.
可按下面公式计算
360
0பைடு நூலகம்
Zm
式中 为步距角; Z为转子上的齿数;m为
步进电动机运行的拍数.
同一台步进电动机,因通电方式不同,运行时步 距角也是不同的
自动控制原理第五版课后答案完整版
1-1 图1-2是液位自动控制系统原理示意图。在任意情况下,希望液面高度c维持不变,试说明系统工作原理并画出系统方块图。
图1-2 液位自动控制系统
解:被控对象:水箱;被控量:水箱的实际水位;给定量电位器设定水位(表征液位的希望值);比较元件:电位器;执行元件:电动机;控制任务:保持水箱液位高度不变。
(4)因为c(t)的表达式中r(t)的系数为非线性函数,所以该系统为非线性系统。
(5)因为该微分方程不含变量及其导数的高次幂或乘积项,且各项系数均为常数,所以该系统为线性定常系统。
(6)因为c(t)的表达式中包含变量的二次项,表示二次曲线关系,所以该系统为非线性系统。
(7)因为c(t)的表达式可写为,其中,所以该系统可看作是线性时变系统。
解:(1)
① n=3,根轨迹有3条分支,且均趋于无穷远处;
② 实轴上的根轨迹:[-50,0],(00];
③ 渐进线:,;
④ 分离点:
求解得:,(舍去);
作出根轨迹如图所示:
(2)临界开环增益为根轨迹与虚轴交点对应的开环增益。
令,代入,并令其实部、虚部分别为零,即
,
解得:(舍去)
当时,
当时,
当时,
3-11设随动系统的微分方程为
其中,T1、T2和K2为正常数。若要求r(t)=1+ t时,c(t)对r(t)的稳态误差不大于正常数ε0,试问K1应满足什么条件?
分析:先求出系统的误差传递函数,再利用稳态误差计算公式,根据题目要求确定参数。
解: 由题意知:
因为该系统为Ⅰ型系统,且输入为单位速度信号时,系统的稳态误差为0.1,即
所以:
自动跟随小车的系统设计
自动跟随小车的系统设计发布时间:2021-10-29T14:49:08.823Z 来源:《论证与研究》2021年9期作者:李成龙 裘 实 车玉倩 杨 凌[导读] 摘要:如今,随着社会经济的快速发展和城市人口的快速增加,城市的交通压力越来越大,严重的交通堵塞和交通事故时有发生。
因此,解决交通问题迫在眉睫,仅仅依靠交通管理部门是远远不够的。
也有必要从科技的角度来解决这个问题。
随着人工智能技术的快速发展,小车的智能化设计已经成为一种趋势,自动跟车逐渐进入人们的视野,而具有自动跟车功能的行李箱,如京东无人配送,也进入了商用。
自动跟车系统通过安装在小车上的传感器获取道路信息,通过通信技术实现车与车之间的通信,辅以算法分析,从而实现小车的自动跟车行驶。
自动跟车系统还可以降低堵车概率,检测可能发生的危险事故,避免交通事故。
自动跟随小车的系统设计李成龙 裘 实 车玉倩 杨 凌(南京工程学院 江苏 南京 211167) 摘要:如今,随着社会经济的快速发展和城市人口的快速增加,城市的交通压力越来越大,严重的交通堵塞和交通事故时有发生。
因此,解决交通问题迫在眉睫,仅仅依靠交通管理部门是远远不够的。
也有必要从科技的角度来解决这个问题。
随着人工智能技术的快速发展,小车的智能化设计已经成为一种趋势,自动跟车逐渐进入人们的视野,而具有自动跟车功能的行李箱,如京东无人配送,也进入了商用。
自动跟车系统通过安装在小车上的传感器获取道路信息,通过通信技术实现车与车之间的通信,辅以算法分析,从而实现小车的自动跟车行驶。
自动跟车系统还可以降低堵车概率,检测可能发生的危险事故,避免交通事故。
关键词:智能小车;自动跟随;系统设计本文以AT89S52单片机为核心,结合多个功能模块,设计了一种自动随动小车系统。
该系统利用QTI传感器监测的位置,控制两台电机的运行,从而实现两车的跟踪。
利用HC-05蓝牙设备实现两车之间的通信,通过控制两车的速度来保持两车之间的距离相对恒定。
8 位置随动系统解析
指导教师评定成绩:审定成绩:重庆邮电大学自动化学院自动控制原理课程设计报告设计题目:位置随动系统单位(二级学院):学生姓名:专业:班级:学号:指导教师:设计时间:重庆邮电大学自动化学院制目录一、设计题目 (2)二.报告正文 (3)摘要 (3)2.1 问题一的分析与求解 (4)2.2 问题二的分析与求解 (5)2.3 问题三的分析与求解 (10)2.4 问题四的分析与求解 (14)三、设计总结 (18)四、参考文献 (19)五、附录 (20)附录一 (20)附录二 (20)一、 设计题目自动控制原理课程设计任务书1某位置随动系统原理如下图所示。
输入量为转角r θ,输出量为转角c θ,p R 为圆盘式滑动电位器,SM 为伺服电动机,TG 为测速发电机。
要求:(1)查阅相关资料,分析系统的工作原理,指出被控对象、被控量和给定量,画出系统方框图。
(2)分析系统每个环节的输入输出关系,代入相关参数求取系统传递函数。
(3)分析系统时域性能和频域性能。
(4)运用根轨迹法或频率法校正系统,使之满足给定性能指标要求。
(已知条件和性能要求待定)二、设计报告正文摘要随动系统是指系统的输出以一定的精度和速度跟踪输入的自动控制系统,并且输入量是随机的,不可预知的,主要解决有一定精度的位置跟随问题,如数控机床的刀具给进和工作台的定位控制,工业机器人的工作动作,导弹制导、火炮瞄准等。
控制技术的发展,使随动系统得到了广泛的应用。
位置随动系统是反馈控制系统,是闭环控制,其位置指令是经常变化的,要求输出量准确跟随给定量的变化,输出响应的快速性、灵活性和准确性成了位置随动系统的主要特征。
本次课程设计研究的是一类位置随动系统的滞后校正,首先通过分析原理求出传递函数,并利用主导极点进行降阶,得出一个二阶系统传递函数,并通过MATLAB分析时域和频域的各个性能,得出相角裕度太小和超调量太大,然后设计PD控制装置,改善系统的阻尼比,来使系统的各个性能达到要求。
- 1、下载文档前请自行甄别文档内容的完整性,平台不提供额外的编辑、内容补充、找答案等附加服务。
- 2、"仅部分预览"的文档,不可在线预览部分如存在完整性等问题,可反馈申请退款(可完整预览的文档不适用该条件!)。
- 3、如文档侵犯您的权益,请联系客服反馈,我们会尽快为您处理(人工客服工作时间:9:00-18:30)。
位置随动控制系统设计与实现王桂霞, 李 媛(中国船舶重工集团公司第704研究所,上海 200031) 摘 要:计算机控制系统是保证位置随动系统功能和性能的重要部分,文中结合船用仿真转台阐述了多机集散控制结构形式的位置随动转台的计算机控制系统方案,并以某位置随动转台为背景,对系统工程实现中的接口电路设计、电机、伺服放大器以及采样频率选取、程序设计等一系列问题进行了讨论,设计结果在位置随动试验样机中应用取得了良好效果. 关键词:位置随动;控制系统;采样频率;设计 中图分类号:T M571,TP273 文献标识码:A 文章编号:100528354(2007)1220029204Desi gn and reali zati on of control syste m of rando m positi onWANG Gui 2Xia,L I Yuan(No .704Research I nstitute,CSI C,Shanghai 20031,China )Abstract :The co m puter control syste m is an i m portant part of guaranteeing perfor m ance of control syste m ofrando m position .Co m bining the m arine si m ulation turntable,this paper set forth the co m puter control syste m sche m e on the rando m position turntable w ith m ulti 2co m puter distributes control structure .Then taking a certain turntable of rando m position as background,it respectively discussed such key proble m s of syste m engineering re 2alization as the interface circuit design,choice of m otor ,servo am plifier and sam ple frequency and the program design .The design sche m e is applied in a rando m position proto type and gets a good result .Key words :rando m position;control syste m;sam ple frequency;design收稿日期:2007211219作者简介:王桂霞(19772),女,工程师,主要从事自动控制的工作位置随动控制系统设计与实现0 引言位置随动转台系统由机械台体和计算机控制系统两个重要部分组成,前者是实现仿真功能的基础,而后者是保证转台系统功能和性能的核心部分.转台既要满足一定的动态、静态指标要求,也要为试验提供方便的操作界面和数据采集、处理手段,计算机控制系统不仅要具有实时控制功能,而且应具备监控管理功能,因此,计算机控制系统设计就成为仿真转台设计和工程实现的重要内容.当前在各种控制系统中计算机已得到非常广泛的应用,根据不同的情况,控制系统的结构形式各不相同,一般分为操作指示系统、直接数字控制系统(DDC )和集散控制系统(DCS )等类型,在下文中将讨论集散控制结构形式的计算机控制系统的设计问题,其中主要包括结构设计、系统工程实现中的接口线路设计、采样频率选择、程序设计等内容,并给出设计结果.1 结构设计本仿真转台采用多机集散控制形式,即采用上下位机的两级式结构.图1为集散控制系统应用于本转图1 原理框图台的原理框图. 在该控制系统中,上位机主要接收来自船惯导平台的船的姿态信号,通过RS232串行接口与下位机通讯,作为该随动控制系统的输入信号,上位机还完成管理功能,为操作者提供人机接口.下位机完成控制功能,当它接受到上位机的输入信号后,通过PC I2 8136运动控制卡的脉冲输入(P I)读取位置信号进行P I D运算,通过PC I28136运动控制卡的D/A发出±10V控制电压,伺服放大器把±10V的速度控制信号放大,输出直流电压来控制直流力矩电机的转速,从而实现位置随动控制.采用上下位机结构,管理计算机和控制计算机相分离,上位机可以有更充裕的时间完成数据采集、存储、分析、图形显示等功能.上位机使用W indows操作系统,用Labview做图形界面,能够快速完成数据采集、存储、分析和图形显示等功能,使操作者能直观地看到转台的运转情况,进行数据分析.下位机的工作集中在实现转台的实时控制任务,采用DOS操作系统,主要完成控制率计算、控制量输出、位置反馈量的输入,构成转台的数字式位置/速率控制系统.采用上下位两级分布的结构使系统的管理功能和实时控制功能由两台计算机分担,非常有利于系统的控制和管理,上下位机之间采用RS232串行接口进行通讯.下面对本转台控制系统实现中的一些问题进行讨论,并给出设计结果.2 系统实现确定了转台计算机控制系统的结构之后,再进行软硬件设计.2.1 硬件设计2.1.1 接口线路设计上下位机之间采用RS232串行通讯接口实现信息传递,传输速率为19200kbp s,下位机和被控对象之间是通过PC I总线与PC I28136运动控制卡连接的, PC I28136运动控制卡集成了16位精度的A/D、D/A、2500v光电隔离的D I、DO及编码器脉冲输入P I功能,P I读取编码器的A+、A2、B+、B2、Z+、Z2六路信号,得到位置信号的零脉冲信号.下位机通过A/D采集测速机的速度信号,通过编码器脉冲输入端口读取来自编码器的位置信号,进行P I D运算后通过D/A 输出±10的控制电压给伺服放大器,伺服放大器进行放大和转换后输出直流电压给直流力矩电机,控制电机的转速,从而实现位置/速率控制.2.1.2 电机、伺服放大器及采样频率的选取1)电机伺服系统设计需从选择电机开始,作为伺服系统的执行元件,应能方便地实现连续平滑地对控制信号反应快捷,以保证整个系统带动被控对象按所需要的规律运动.执行电机是伺服系统中的一个重要组成部分,同时又靠它驱动被控对象,因此它是伺服系统与被控对象相联系的一个关键部件.被控对象的运动是与执行电机的运动同时进行的.执行电机除了要克服被控对象所形成的负载外,还必须克服电机自身的干摩擦力矩、电机转子的惯性转矩(电机转子转动惯量和电机转动角加速度).普通的伺服电机通常转速高而转矩小,在系统中作为执行元件去拖动负载时,都必须经过齿轮减速装置,但由于齿隙的影响,往往使系统的精度和稳定性下降,因此为了减小甚至消除误差,简化系统结构,提高精度和稳定性,达到少用不用减速器的目的,需选用具有低转速、大转矩和高精度等特点的力矩电机.位置随动系统的主要作用是跟随舰在海上航行的姿态,由于海上浪大风大,而大船在风和海浪的影响下,其摇摆周期约为5~25s,频率为0.04~0.2HZ,故船的摇摆速度很慢,这就要求电机在低速状态下能输出较大的力矩.而直流力矩电机是特种电机,可由直流电压调节转速,其负载特性(M2I)具有很高的线性度,其转矩特性是一条直线,在位置控制方式的伺服系统中,可在低速状态下工作,并能输出较大的力矩,尤其在平稳低速运行时更为突出.因此选用低转速、大力矩的直流力矩电机作为执行电机,以提高系统精度和稳定性.2)伺服放大器选用直流力矩电机,伺服放大器也相应地选用直流伺服放大器,直流伺服放大器把来自下位机的±10V速度控制信号放大,输出直流电压来控制直流力矩电机的转速.直流力矩电机和直流伺服放大器是构成直流伺服系统的主要部件.作为伺服系统的一个重要部件,伺服放大器需具有一定的带宽,以快速跟踪舰的摇摆.由于舰的摇摆频率为0.04~0.2HZ,在选用伺服放大器时,其频率范围应高于跟踪信号最高频率,以确保放大器有大的加速度,在短时间内输出大电压大电流,快速跟踪舰的摇摆,以提高系统的动态精度.另外在选取伺服放大器时,伺服放大器的额定电流要大于直流力矩电机的峰值堵转电流,且应留有一定的安全裕量.3)采样频率位置随动控制系统的控制器是由下位机实现的,构成数字式角位置/角速率伺服系统.在确定采样频率时,需要考虑系统的动态要求.位置随动转台的主要作用是跟随舰在海上航行的姿态,对其动态跟踪精度要求较高,在±9角分范围内.对这种动态精度要求很高的转台,必须选择较高的采样频率,以满足系统的性能指标要求.目前这类转台角位置伺服系统的采样周期多取1m s,在本试验样机中,由于考虑到机械间隙对精度的影响,采样周期取为0.8m s .2.2 程序设计程序设计包括上位机程序设计和下位机程序设计两部分.上位机程序应包括以下几部分的内容:1)向下位机发送自检命令,接受自检信息,并在检测到故障信息时进行故障处理.2)设置转台的工作状态和工作参数.3)通讯功能,即接受来自舰上惯导平台的舰的姿态角信号,向下位机发送给定信号,并接受下位机的返回信息.4)数据采集和处理功能.5)图形显示功能.上位机的程序流程图如图2所示,采用Labview 可视化语言编程,以模板/按钮与弹出式窗口相结合的形式为操作人员提供操作界面.图2 上位机程序流程图 下位机的主要功能是根据上位机的命令完成对转台各种运动状态的实时控制,其程序框图如图3所示,其中各子程序的功能分别为:初始化子程序对PC I 28136运动控制卡进行初始化,包括初始化A /D和D /A 的电压范围,以及增量式编码器脉冲输入(P I )方式等;自检子程序在初始化之后检测系统是否正常;工作方式管理子程序完成对转台各工作状态的管理和调度;通讯处理子程序负责接受上位机的给定信号和向上位机发送转台的控制信息等.图3 下位机程序流程图 对转台伺服系统的实时控制在中断服务程序中完成,每0.8m s 发出一次控制指令,每20m s 向上位机发送一次转台状态信息,其流程图如图4所示.图4 实时控制流程图3 调试位置随动系统试验样机的调试包括速度环和位置环的调试,先调节速度环,速度环调节好后,再调节位置环.3.1 速度环调节在位置环断开的前提下,首先进行零漂调节,即给伺服放大器的速度给定电压为0V,电机的转速为零,无零漂,测速机反馈电压为零.然后进行速度标定,在速度给定电压为0V时,电机转速为零,而在给定电压为10V或210V时,电机达到额定转速或被控对象的最大转速.最后进行速度环增益调节,用信号发生器给伺服放大器的速度给定端输入±2V的方波信号,频率为1~2HZ(频率要高于被控对象的频率),再用示波器显示测速机反馈信号,反馈曲线为阶跃响应曲线,通过调节伺服放大器的速度环增益,使阶跃响应曲线达到最佳.一般超调量为15%左右,要小于20%.3.2 位置环调节接通位置环,通过PC I28136运动控制卡的D/A 段输出控制电压,而从P I端读取编码器测得的被控对象的位置信息,通过下位机与上位机之间的通讯,从上位机的图形显示和数据分析结果,可以了解系统的跟踪状态,分析误差产生的原因,调节位置环的P I D参数,提高系统的跟踪精度.从上位机的图形显示发现,系统跟踪有明显的滞后,误差主要是由滞后引起的,需要增加速度前馈校正环节,通过调节速度前馈系数,减小跟踪误差.通过分析,编码器的分辨率及机械结构的间隙对跟踪精度有一定的影响,对高精度的位置随动系统,机械间隙一定要尽可能小,而且编码器的分辨率要高.最后,在现有编码器分辨率低且存在机械间隙的情况下,系统的跟踪误差≤5角分,满足动态指标要求.如果提高编码器的分辨率和减小机械间隙,系统精度可以得到进一步提高.5 结束语本文对位置随动控制系统的主要设计问题进行了讨论,对具体工程实现中的若干关键问题作了深入研究,所设计的位置随动控制系统成功应用于位置随动试验样机,达到了指标要求.参考文献:[1]胡寿松.自动控制原理[M].北京:国防工业出版社,1994.[2]谭浩强.C程序设计[M].北京:清华大学出版社,1999.[3]刘金琨.先进P I D控制MAT LAB仿真[M].北京:电子工业出版社,2004.(上接第13页)用过程中效果较好.4 结论本文通过对现有型线的分析对比,从数学理论上进行分析,发现曲线连接处存在拐点曲线不能光滑连接.进一步对其做了相应的修改,找到合适的连接方式,消除了曲线连接的拐点,整条曲线光滑连接.并对现有五螺杆泵存在的问题及结构改进进行了探讨,提出了改进设想.本文通过对五螺杆泵型线和结构的探讨,为以后进一步改进五螺杆泵型线和结构提供了一定的理论基础.。