焊接件、铸钢件去应力退火工艺
要消除铸件或锻件的应力,应选择何种热处理方法
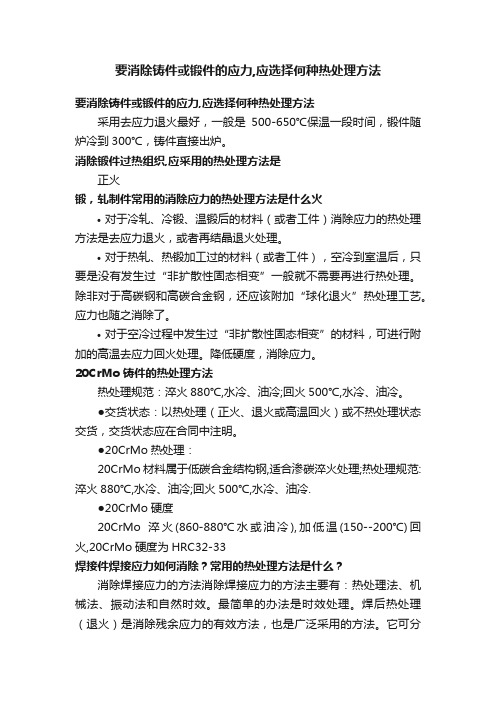
要消除铸件或锻件的应力,应选择何种热处理方法要消除铸件或锻件的应力,应选择何种热处理方法采用去应力退火最好,一般是500-650℃保温一段时间,锻件随炉冷到300℃,铸件直接出炉。
消除锻件过热组织,应采用的热处理方法是正火锻,轧制件常用的消除应力的热处理方法是什么火•对于冷轧、冷锻、温锻后的材料(或者工件)消除应力的热处理方法是去应力退火,或者再结晶退火处理。
•对于热轧、热锻加工过的材料(或者工件),空冷到室温后,只要是没有发生过“非扩散性固态相变”一般就不需要再进行热处理。
除非对于高碳钢和高碳合金钢,还应该附加“球化退火”热处理工艺。
应力也随之消除了。
•对于空冷过程中发生过“非扩散性固态相变”的材料,可进行附加的高温去应力回火处理。
降低硬度,消除应力。
20CrMo铸件的热处理方法热处理规范:淬火880℃,水冷、油冷;回火500℃,水冷、油冷。
●交货状态:以热处理(正火、退火或高温回火)或不热处理状态交货,交货状态应在合同中注明。
●20CrMo热处理:20CrMo材料属于低碳合金结构钢,适合渗碳淬火处理;热处理规范:淬火880℃,水冷、油冷;回火500℃,水冷、油冷.●20CrMo硬度20CrMo淬火(860-880℃水或油冷),加低温(150--200℃)回火,20CrMo硬度为HRC32-33焊接件焊接应力如何消除?常用的热处理方法是什么?消除焊接应力的方法消除焊接应力的方法主要有:热处理法、机械法、振动法和自然时效。
最简单的办法是时效处理。
焊后热处理(退火)是消除残余应力的有效方法,也是广泛采用的方法。
它可分为整体热处理和局部热处理。
HT200铸件热处理方法规范?HT200热处理方式1、消除应力退火(或称人工时效):消除铸造后存在于铸件内部的残余应力。
常需进行消除应力退火:(残余应力可能引起铸件翘曲和裂纹)一般为500-550℃。
加热温度越高,应力消除越快。
温度越高会发生石墨化和珠光体化,降低性能。
铸造厂退火炉操作规程
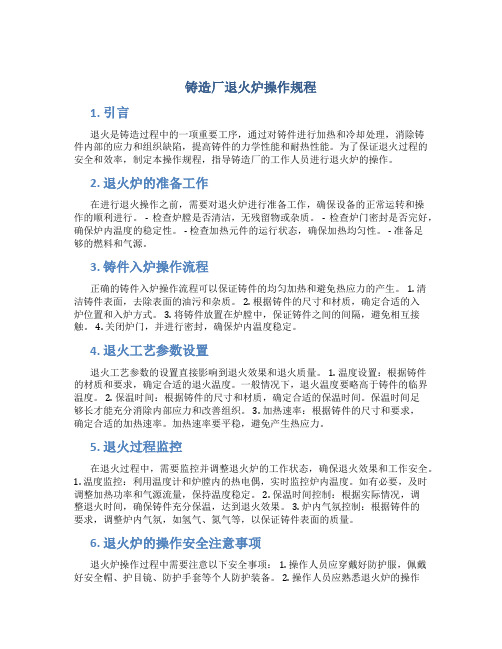
铸造厂退火炉操作规程1. 引言退火是铸造过程中的一项重要工序,通过对铸件进行加热和冷却处理,消除铸件内部的应力和组织缺陷,提高铸件的力学性能和耐热性能。
为了保证退火过程的安全和效率,制定本操作规程,指导铸造厂的工作人员进行退火炉的操作。
2. 退火炉的准备工作在进行退火操作之前,需要对退火炉进行准备工作,确保设备的正常运转和操作的顺利进行。
- 检查炉膛是否清洁,无残留物或杂质。
- 检查炉门密封是否完好,确保炉内温度的稳定性。
- 检查加热元件的运行状态,确保加热均匀性。
- 准备足够的燃料和气源。
3. 铸件入炉操作流程正确的铸件入炉操作流程可以保证铸件的均匀加热和避免热应力的产生。
1. 清洁铸件表面,去除表面的油污和杂质。
2. 根据铸件的尺寸和材质,确定合适的入炉位置和入炉方式。
3. 将铸件放置在炉膛中,保证铸件之间的间隔,避免相互接触。
4. 关闭炉门,并进行密封,确保炉内温度稳定。
4. 退火工艺参数设置退火工艺参数的设置直接影响到退火效果和退火质量。
1. 温度设置:根据铸件的材质和要求,确定合适的退火温度。
一般情况下,退火温度要略高于铸件的临界温度。
2. 保温时间:根据铸件的尺寸和材质,确定合适的保温时间。
保温时间足够长才能充分消除内部应力和改善组织。
3. 加热速率:根据铸件的尺寸和要求,确定合适的加热速率。
加热速率要平稳,避免产生热应力。
5. 退火过程监控在退火过程中,需要监控并调整退火炉的工作状态,确保退火效果和工作安全。
1. 温度监控:利用温度计和炉膛内的热电偶,实时监控炉内温度。
如有必要,及时调整加热功率和气源流量,保持温度稳定。
2. 保温时间控制:根据实际情况,调整退火时间,确保铸件充分保温,达到退火效果。
3. 炉内气氛控制:根据铸件的要求,调整炉内气氛,如氢气、氮气等,以保证铸件表面的质量。
6. 退火炉的操作安全注意事项退火炉操作过程中需要注意以下安全事项: 1. 操作人员应穿戴好防护服,佩戴好安全帽、护目镜、防护手套等个人防护装备。
铸钢件热处理作业指导书
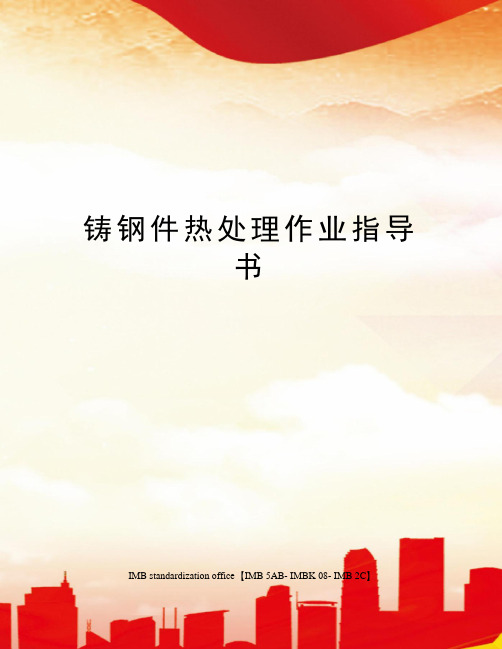
铸钢件热处理作业指导书IMB standardization office【IMB 5AB- IMBK 08- IMB 2C】热处理作业指导书1.目的保证热处理质量。
2.热处理方式按加热和冷却条件不同,铸钢件的主要热处理方式有:退火、正火、均匀化处理、淬火、回火、固溶处理、沉淀硬化、消除应力处理及除氢处理。
3.热处理操作要求.退火退火是将铸钢件加热到Acs 以上20~30℃,保温一定时间,冷却的热处理工艺。
退火的目的是为消除铸造组织中的柱状晶、粗等轴晶、魏氏组织和树枝状偏析,以改善铸钢力学性能。
碳钢退火后的组织:亚共析铸钢为铁素体和珠光体,共析铸钢为珠光体,过共析铸钢为珠光体和碳化物。
适用于所有牌号的铸钢件。
图1—1为几种退火处理工艺的加热规范示意图。
表l—1为铸钢件常用退火工艺类型及其应用。
表1-2铸钢件退火工艺及退火后的硬度。
图1—1为几种退火处理工艺的加热规范示意图表l—1为铸钢件常用退火工艺类型及其应用表1-2铸钢件退火工艺及退火后的硬度.正火正火是将铸钢件目口热到Ac。
温度以上30~50o C 保温,使之完全奥氏体化,然后在静止空气中冷却的热处理工艺。
图1—2为碳钢的正火温度范围示意图。
表1-3铸钢件正火工艺及退火后的硬度,表1-4常用低合金铸件正火或正火+回火工艺及硬度。
正火的目的是细化钢的组织,使其具有所需的力学性能,也司作为以后热处理的预备处理。
正火与退火工艺的区别有两个:其一是正火加热温度要偏高些;其二是正火冷却较快些。
经正火的铸钢强度稍高于退火铸钢,其珠光体组织较细。
一般工程用碳钢及部分厚大、形状复杂的合金钢铸件多采用正火处理。
图1—2为碳钢的正火温度范围示意图正火可消除共析铸钢和过共析铸钢件中的网状碳化物,以利于球化退火;可作为中碳钢以及合金结构钢淬火前的预备处理,以细化晶粒和均匀组织,从而减少铸件在淬火时产生的缺陷。
表1-3铸钢件正火工艺及退火后的硬度表1-4常用低合金铸件正火或正火+回火工艺及硬度.淬火淬火是将零件加热到奥氏体化后(Ac。
常见的退火工艺

共析、过共析钢及合金钢锻件、扎件等
当有网状Fe3C存在时,必需先用正火消除Fe3C网,再球化退火
扩散退火
(均匀化退火)
降低钢锭、铸件或锻坯成份偏析和组织不均匀性
加热到钢熔点以下100~200℃,长时间保温后炉冷
粗大组织(组织严重过烧)
合金钢铸锭及大型铸钢件或铸件
扩散退火后钢晶粒很大,所以通常要进行完全退火或正火处理
刃具、量具、冲模、轴承、渗碳件、表面淬火件
中温回火
350~500℃
T回
高屈服极限、弹性极限和韧性, HRC35~50弹簧来自弹性夹具、热锻模高温回火
500~650℃
S回
良好综合机械性能, HRC200~300
轴、齿轮、连杆、螺栓
去应力退火
(低温退火)
为消除铸件、锻件、焊接件、冷加工件内应力,以预防钢件再以后加工或使用过程变形或开裂
加热至Ac1以下某一温度(对于碳钢为500~600℃),保温后随炉冷却
无改变
铸、锻、焊、冷压件及机加工件等
能够消除内应力约50%~80%
淬火工艺参数
淬火工艺参数
加热温度
对于亚共析钢Ac3以上30~70℃
常见退火工艺
名称
目
工艺特点
组织
应用
其她
完全退火
(重结晶退火)
使中碳以上亚共析钢和合金钢得到靠近平衡状态组织,以降低硬度,改善切削加工性能,并能够消除内应力
加热至Ac3以上30~50℃保温后随炉冷却
F+P
亚共析钢铸、锻、扎件,焊接件
等温退火
与完全退火相同,但转变较易控制,能取得均匀预期组织;对于奥氏体较稳定合金钢,常可大大缩短退火时间
铸钢件的热处理方式
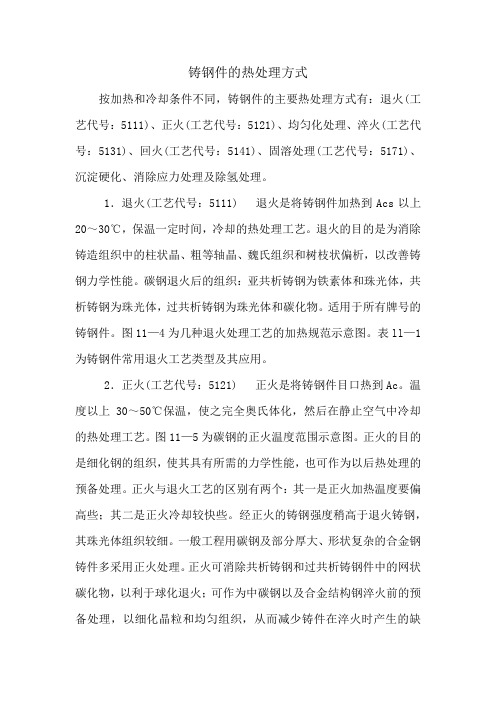
铸钢件的热处理方式按加热和冷却条件不同,铸钢件的主要热处理方式有:退火(工艺代号:5111)、正火(工艺代号:5121)、均匀化处理、淬火(工艺代号:5131)、回火(工艺代号:5141)、固溶处理(工艺代号:5171)、沉淀硬化、消除应力处理及除氢处理。
1.退火(工艺代号:5111) 退火是将铸钢件加热到Acs以上20~30℃,保温一定时间,冷却的热处理工艺。
退火的目的是为消除铸造组织中的柱状晶、粗等轴晶、魏氏组织和树枝状偏析,以改善铸钢力学性能。
碳钢退火后的组织:亚共析铸钢为铁素体和珠光体,共析铸钢为珠光体,过共析铸钢为珠光体和碳化物。
适用于所有牌号的铸钢件。
图11—4为几种退火处理工艺的加热规范示意图。
表ll—1为铸钢件常用退火工艺类型及其应用。
2.正火(工艺代号:5121) 正火是将铸钢件目口热到Ac。
温度以上30~50℃保温,使之完全奥氏体化,然后在静止空气中冷却的热处理工艺。
图11—5为碳钢的正火温度范围示意图。
正火的目的是细化钢的组织,使其具有所需的力学性能,也可作为以后热处理的预备处理。
正火与退火工艺的区别有两个:其一是正火加热温度要偏高些;其二是正火冷却较快些。
经正火的铸钢强度稍高于退火铸钢,其珠光体组织较细。
一般工程用碳钢及部分厚大、形状复杂的合金钢铸件多采用正火处理。
正火可消除共析铸钢和过共析铸钢件中的网状碳化物,以利于球化退火;可作为中碳钢以及合金结构钢淬火前的预备处理,以细化晶粒和均匀组织,从而减少铸件在淬火时产生的缺陷。
3.淬火(工艺代号:5131) 淬火是将铸钢件加热到奥氏体化后(Ac。
或Ac•以上),保持一定时间后以适当方式冷却,获得马氏体或贝氏体组织的热处理工艺。
常见的有水冷淬火、油冷淬火和空冷淬火等。
铸钢件淬火后应及时进行回火处理,以消除淬火应力及获得所需综合力学性能。
图11—6为淬火回火工艺示意图。
铸钢件淬火工艺的主要参数:(1)淬火温度:淬火温度取决于铸钢的化学成分和相应的临界温度点。
焊后去应力退火方案
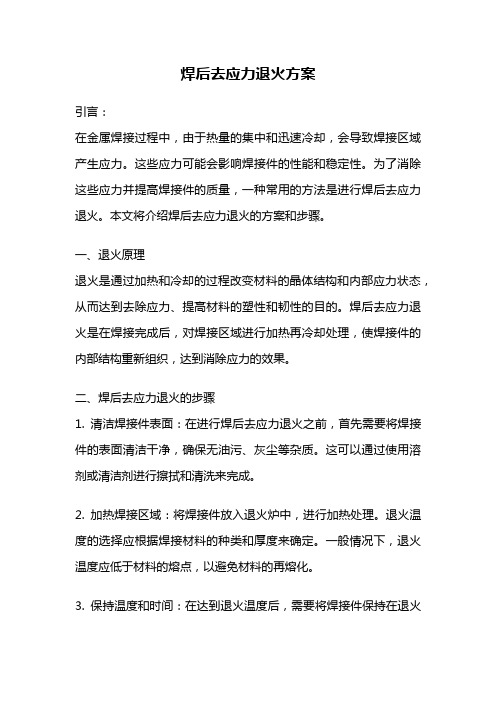
焊后去应力退火方案引言:在金属焊接过程中,由于热量的集中和迅速冷却,会导致焊接区域产生应力。
这些应力可能会影响焊接件的性能和稳定性。
为了消除这些应力并提高焊接件的质量,一种常用的方法是进行焊后去应力退火。
本文将介绍焊后去应力退火的方案和步骤。
一、退火原理退火是通过加热和冷却的过程改变材料的晶体结构和内部应力状态,从而达到去除应力、提高材料的塑性和韧性的目的。
焊后去应力退火是在焊接完成后,对焊接区域进行加热再冷却处理,使焊接件的内部结构重新组织,达到消除应力的效果。
二、焊后去应力退火的步骤1. 清洁焊接件表面:在进行焊后去应力退火之前,首先需要将焊接件的表面清洁干净,确保无油污、灰尘等杂质。
这可以通过使用溶剂或清洁剂进行擦拭和清洗来完成。
2. 加热焊接区域:将焊接件放入退火炉中,进行加热处理。
退火温度的选择应根据焊接材料的种类和厚度来确定。
一般情况下,退火温度应低于材料的熔点,以避免材料的再熔化。
3. 保持温度和时间:在达到退火温度后,需要将焊接件保持在退火温度下一定的时间。
这个时间称为保温时间,其长短也需要根据焊接材料的种类和厚度来确定。
4. 冷却焊接件:在保温时间结束后,将焊接件从退火炉中取出,进行自然冷却或其他冷却方式。
这一步骤的目的是使焊接件的温度逐渐降低,从而使其内部结构得以稳定。
5. 检查焊后退火效果:在完成焊后去应力退火后,需要对焊接件进行检查,以确保退火效果的达到。
可以通过金相显微镜、硬度计等仪器来观察和测试焊接区域的晶粒结构和硬度等性能指标。
三、焊后去应力退火的注意事项1. 退火温度的选择应根据焊接材料的种类和厚度来确定,需要避免过高或过低的温度对材料造成不良影响。
2. 保温时间的长短应根据焊接材料的种类和厚度来确定,过短的保温时间可能无法达到退火效果,过长的保温时间则可能导致材料的再结晶。
3. 冷却方式的选择应根据焊接件的材料和尺寸来确定,可以采用自然冷却、水淬或风冷等方式。
4. 检查焊后退火效果时,需要确保检测仪器的准确性和可靠性,以避免误判。
铸钢件常见热处理工艺

按加热和冷却条件不同,铸钢件的主要热处理方式有:退火、正火、均匀化处理、淬火、回火、固溶处理、沉淀硬化、消除应力处理及除氢处理。
1.退火:退火是将铸钢件加热到Ac3以上20~3(FC,保温一定时间,冷却的热处理工艺。
退火的目的是为消除铸造组织中的柱状晶、粗等轴晶、魏氏组织和树枝状偏析,以改善铸钢力学性能。
碳钢退火后的组织:亚共析铸钢为铁素体和珠光体,共析铸钢为珠光体,过共析铸钢为珠光体和碳化物。
适用于所有牌号的铸钢件。
2,正火:正火是将铸钢件加热到Ac3温度以上30~50。
C保温,使之完全奥氏体化,然后在静止空气中冷却的热处理工艺。
正火的目的是细化钢的组织,使其具有所需的力学性能,也是作为以后热处理的预备处理。
正火与退火工艺的区别有两个:其一是正火加热温度要偏高些;其二是正火冷却较快些。
经正火的铸钢强度稍高于退火铸钢,其珠光体组织较细。
一般工程用碳钢及部分厚大、形状复杂的合金钢铸件多采用正火处理。
正火可消除共析铸钢和过共析铸钢件中的网状碳化物,以利于球化退火;可作为中碳钢以及合金结构钢淬火前的预备处理,以细化晶粒和均匀组织,从而减少铸件在淬火时产生的缺陷。
3淬火:淬火是将铸钢件加热到奥氏体化后(AC。
或Ac•以上),保持一定时间后以适当方式冷却,获得马氏体或贝氏体组织的热处理工艺。
常见的有水冷淬火、油冷淬火和空冷淬火等。
铸钢件淬火后应及时进行回火处理,以消除淬火应力及获得所需综合力学性能铸钢件淬火工艺的主要参数:Q)淬火温度:淬火温度取决于铸钢的化学成分和相应的临界温度点。
原则上,亚共析铸钢淬火温度为Ac o以上20~30℃,常称之为完全淬火。
共析及过共析铸钢在Ac o以上30~50℃淬火,即所谓亚临界淬火或两相区淬火。
这种淬火也可用于亚共析钢,所获得的组织较一般淬火的细,适用于低合金铸钢件韧化处理。
(2)淬火介质:淬火的目的是得到完全的马氏体组织。
为此,铸件淬火时的冷却速率必须大于铸钢的临界冷却速率。
WCB铸件热处理制度及工艺规范

WCB铸件热处理制度及工艺规范(常规)根据客户要求。
对铸件(毛坯)进行退火、正火、正火+回火等热处理。
热处理工艺规范(见表)工艺名称退火正火正火+回火加热温度880-920°C940-960°C940-960°C620-680°C保温时间0.5-1h/25mm至少1h0.5-1h/25mm至少1h0.5-1h/25mm至少1h25mm/1h冷却炉冷至450°C后出炉空冷空冷空冷铸钢件焊后去应力退火加热温度600-650°C 保温1h / 25mm 空冷。
装炉温度及升温要求1、室温或者400°C以下装炉,升温至500-600°C时保温1-2h,再升温。
2、升温速率100-200°C / h,随炉冷却速率100-200°C / h。
装备(设备及设施)1、采用台车式电阻加热炉,必要时配备机械鼓风冷却。
2、温度控制采用带程序控制的PID调节器进行控温。
六、操作要求1、所有铸件在热处理前,应清砂、切冒口、清理铸件表面、对裂纹等缺陷进行补焊。
且化学成分必须检验合格、外观目视检验合格。
同时应带有同铸件冶炼炉次相同的标号的试棒。
2、铸件应放置在加热炉有效加热区内。
同炉处理的铸件壁厚相差不应太大。
在铸件加热时不至于产生变形的前提下,允许多层叠放。
试棒应和其所代表的铸件同炉进行热处理,并放置在具有代表性的位置。
3、严格执行热处理工艺规范。
加热过程中应确保温度测量、控制和记录装置的正常运行。
铸件热处理后,应按相关标准规定的检验方法检验。
浙江方文特钢有限公司2014年1月15日。