翘曲变形
产品翘曲变形的原因
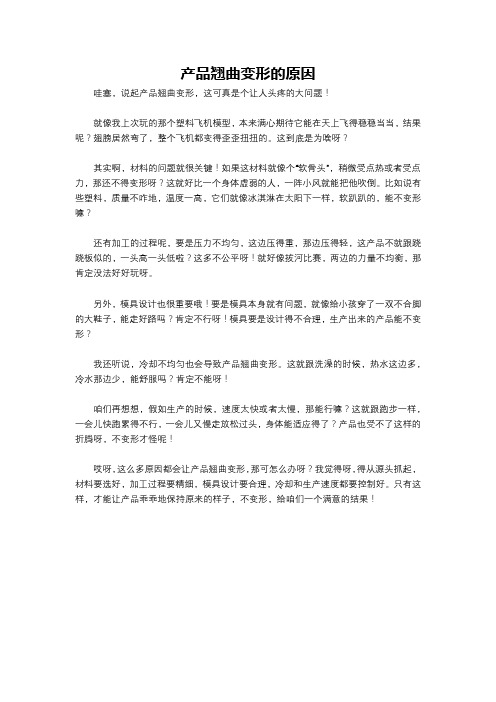
产品翘曲变形的原因
哇塞,说起产品翘曲变形,这可真是个让人头疼的大问题!
就像我上次玩的那个塑料飞机模型,本来满心期待它能在天上飞得稳稳当当,结果呢?翅膀居然弯了,整个飞机都变得歪歪扭扭的。
这到底是为啥呀?
其实啊,材料的问题就很关键!如果这材料就像个“软骨头”,稍微受点热或者受点力,那还不得变形呀?这就好比一个身体虚弱的人,一阵小风就能把他吹倒。
比如说有些塑料,质量不咋地,温度一高,它们就像冰淇淋在太阳下一样,软趴趴的,能不变形嘛?
还有加工的过程呢,要是压力不均匀,这边压得重,那边压得轻,这产品不就跟跷跷板似的,一头高一头低啦?这多不公平呀!就好像拔河比赛,两边的力量不均衡,那肯定没法好好玩呀。
另外,模具设计也很重要哦!要是模具本身就有问题,就像给小孩穿了一双不合脚的大鞋子,能走好路吗?肯定不行呀!模具要是设计得不合理,生产出来的产品能不变形?
我还听说,冷却不均匀也会导致产品翘曲变形。
这就跟洗澡的时候,热水这边多,冷水那边少,能舒服吗?肯定不能呀!
咱们再想想,假如生产的时候,速度太快或者太慢,那能行嘛?这就跟跑步一样,一会儿快跑累得不行,一会儿又慢走放松过头,身体能适应得了?产品也受不了这样的折腾呀,不变形才怪呢!
哎呀,这么多原因都会让产品翘曲变形,那可怎么办呀?我觉得呀,得从源头抓起,材料要选好,加工过程要精细,模具设计要合理,冷却和生产速度都要控制好。
只有这样,才能让产品乖乖地保持原来的样子,不变形,给咱们一个满意的结果!。
翘曲变形原因

翘曲变形原因统计第一种说法:注塑件的翘曲、变形是很棘手的问题,主要应从模具的设计方面着手解决,而成型条件的调整效果则是很有限的,翘曲变形的原因及解决方法可以参照以下各项;1)由成型条件引起残余应力造成变形时,可通过降低注射压力,提高模具温度并使模具温度均匀及提高树脂温度或采用退火方法予以消除应力。
2)脱模不良引起应力时,可通过增加推杆数量或面积、设置脱模斜度等方法加以解决。
3)由于冷却方法不合适,使冷却不均匀或冷却时间不足时,可调整冷却方法及延长冷却时间等。
例如,尽可能地在贴近变形的地方设置冷却回路。
4)对于成型收缩引起的变形,就必须修正模具的设计了,其中,最重要的是应注意使制品的壁厚一致。
有时,再不得已的情况下,只好测量制品的变形,按相反的方向修正模具,加以校正。
一般结晶性树脂(POM/PA/PP/PET等)比非结晶性树脂(如PMMA,PVC,PS,ABS,AS)的变形大。
另外,由于玻璃纤维增强树脂具有纤维配向性,变形也大。
第二种说法:一模具方面:(1)浇口位置不当或数量不足。
(2)顶出位置不当或制品受力不均匀。
二工艺方面:(1)模具、机筒温度太高。
(2)注射压力太高或注射速度太快。
(3)保压时间太长或冷却时间太短。
三原料方面:酞氰系颜料会影响聚乙烯的结晶度而导致制品变形。
四制品设计方面:(1)壁厚不均,变化突然或壁厚过小。
(2)制品结构造型不当。
第三种说法:肉厚不均、冷却不均。
塑胶的冷却速度不一样,冷却快的地方收缩小,冷却慢的地方收缩大,从而发生变形。
☐料温高,收缩大,从而变形大。
☐分子排向差异;侧壁的内弯曲。
☐制品脱模时的内部应力所致的变形,是制品未充分冷却固化前从模具顶出所致。
☐一般为防止制品变形,可在顶出后,用夹具对制品定型,矫正变形或防止进一步的变形,但制品在使用中若再次碰到高温时又会复原,对此点需特别加以注意。
第四种说法:如果制件的收缩均匀,那么成型件不会发生变形或翘曲,只是单纯地变小了。
pcb翘曲形变

pcb翘曲形变
PCB翘曲形变的原因有多种,包括但不限于以下几点:
1. 电路板本身的重量会导致板子凹陷变形,如果板子上有重物或尺寸过大,由于板子的量,中间会出现凹陷,导致板子弯曲。
2. V-cut太深,导致两侧V-cut处翘曲。
V-Cut在原大片材上切槽,因此容易翘曲。
3. PCB由芯板、半固化片和外层铜箔压制而成,芯板和铜箔在压在一起时会因热而变形。
翘曲量取决于两种材料的热膨胀系数(CTE),如果铜箔和芯板的CTE差异较大,也可能导致翘曲。
4. PCB加工过程中引起的翘曲,主要分为热应力和机械应力。
其中,热应力主要在压制过程中产生,机械应力主要在板材的堆垛、搬运和烘烤过程中产生。
5. 工程设计的原因,例如电路板上的铜表面积不均匀、特殊的介质或阻抗关系导致层压结构不对称、板子镂空位置过大且多、板上的面板数量过多等,都可能导致板子翘曲。
6. 储存不当也可能造成PCB翘曲。
以上信息仅供参考,如需了解更多信息,建议查阅PCB制造相关书籍或咨询专业人士。
3d打印翘曲变形解决的方法
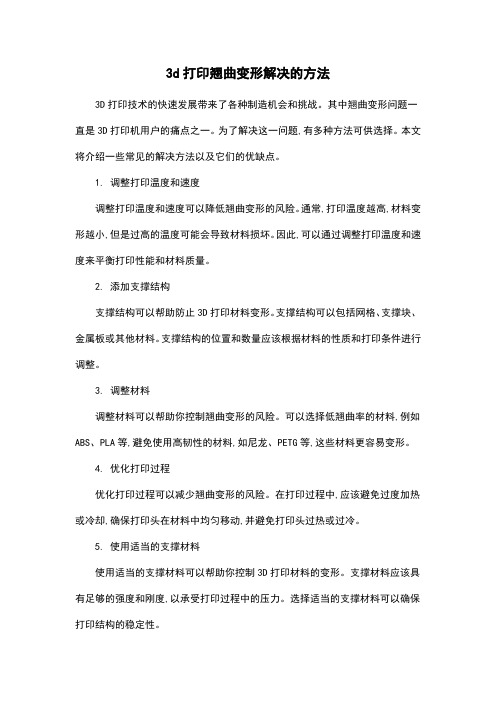
3d打印翘曲变形解决的方法3D打印技术的快速发展带来了各种制造机会和挑战。
其中翘曲变形问题一直是3D打印机用户的痛点之一。
为了解决这一问题,有多种方法可供选择。
本文将介绍一些常见的解决方法以及它们的优缺点。
1. 调整打印温度和速度调整打印温度和速度可以降低翘曲变形的风险。
通常,打印温度越高,材料变形越小,但是过高的温度可能会导致材料损坏。
因此,可以通过调整打印温度和速度来平衡打印性能和材料质量。
2. 添加支撑结构支撑结构可以帮助防止3D打印材料变形。
支撑结构可以包括网格、支撑块、金属板或其他材料。
支撑结构的位置和数量应该根据材料的性质和打印条件进行调整。
3. 调整材料调整材料可以帮助你控制翘曲变形的风险。
可以选择低翘曲率的材料,例如ABS、PLA等,避免使用高韧性的材料,如尼龙、PETG等,这些材料更容易变形。
4. 优化打印过程优化打印过程可以减少翘曲变形的风险。
在打印过程中,应该避免过度加热或冷却,确保打印头在材料中均匀移动,并避免打印头过热或过冷。
5. 使用适当的支撑材料使用适当的支撑材料可以帮助你控制3D打印材料的变形。
支撑材料应该具有足够的强度和刚度,以承受打印过程中的压力。
选择适当的支撑材料可以确保打印结构的稳定性。
6. 进行测试和优化在实际应用中,你可以根据测试结果和打印条件进行调整和优化。
例如,你可以进行温度、速度和材料的测试,以确定最佳的打印条件。
你还可以进行打印结构的测试,以确定其稳定性和翘曲变形的风险。
综上所述,翘曲变形问题可以通过调整打印温度和速度、添加支撑结构、调整材料、优化打印过程和使用适当的支撑材料以及进行测试和优化等多种方法来解决。
这些方法可以单独或组合使用,以实现最佳的3D打印效果。
塑料翘曲变形的原因
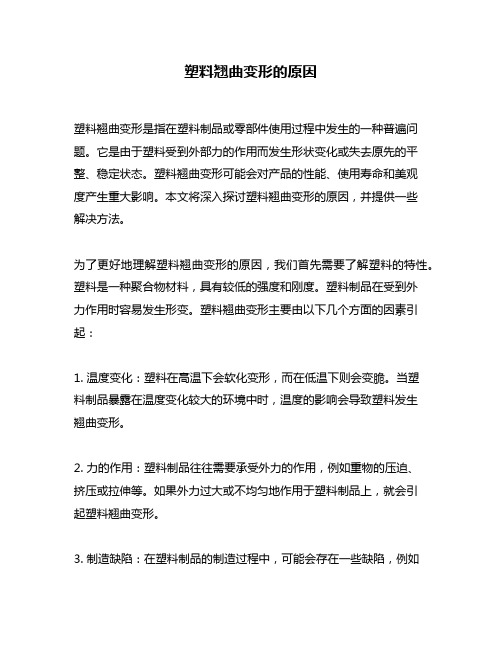
塑料翘曲变形的原因塑料翘曲变形是指在塑料制品或零部件使用过程中发生的一种普遍问题。
它是由于塑料受到外部力的作用而发生形状变化或失去原先的平整、稳定状态。
塑料翘曲变形可能会对产品的性能、使用寿命和美观度产生重大影响。
本文将深入探讨塑料翘曲变形的原因,并提供一些解决方法。
为了更好地理解塑料翘曲变形的原因,我们首先需要了解塑料的特性。
塑料是一种聚合物材料,具有较低的强度和刚度。
塑料制品在受到外力作用时容易发生形变。
塑料翘曲变形主要由以下几个方面的因素引起:1. 温度变化:塑料在高温下会软化变形,而在低温下则会变脆。
当塑料制品暴露在温度变化较大的环境中时,温度的影响会导致塑料发生翘曲变形。
2. 力的作用:塑料制品往往需要承受外力的作用,例如重物的压迫、挤压或拉伸等。
如果外力过大或不均匀地作用于塑料制品上,就会引起塑料翘曲变形。
3. 制造缺陷:在塑料制品的制造过程中,可能会存在一些缺陷,例如气泡、疏松区域或不均匀的厚度等。
这些制造缺陷会导致塑料制品在使用过程中容易发生翘曲变形。
4. 冷却不均匀:在塑料制品的加工过程中,冷却是一个重要的环节。
如果冷却不均匀或过快,就会导致塑料材料产生内部应力,从而引起翘曲变形。
那么,如何解决塑料翘曲变形问题呢?以下是一些建议:1. 选择合适的塑料材料:不同的塑料材料具有不同的特性,如强度、刚度和耐温性等。
在设计和选择塑料制品时,需要考虑到使用环境的要求,并选择合适的塑料材料来减少翘曲变形的可能性。
2. 改善制造工艺:优化塑料制品的制造工艺,确保塑料材料均匀冷却和充分固化。
这有助于减少内部应力和制造缺陷,从而降低翘曲变形的风险。
3. 增加支撑结构:对于长而细的塑料制品,在设计时可以增加合适的支撑结构,以增强整体的强度和稳定性,减少翘曲变形的可能性。
4. 控制使用环境:在使用塑料制品时,需要控制使用环境的温度和湿度。
避免过高或过低的温度对塑料造成不利影响,同时注意湿度对塑料的吸湿性。
塑料制品的翘曲变形分析

一、引言翘曲变形是指注塑制品的形状偏离了模具型腔的形状,它是塑料制品常见的缺陷之一。
随着塑料工业的发展,人们对塑料制品的外观和使用性能要求越来越高,翘曲变形程度作为评定产品质量的重要指标之一也越来越多地受到模具设计者的关注与重视。
模具设计者希望在设计阶段预测出塑料件可能产生翘曲的原因,以便加以优化设计,从而提高注塑生产的效率和质量,缩短模具设计周期,降低成本。
本文主要对在注塑模具设计过程中影响注塑制品翘曲变形的因素加以分析。
二、模具的结构对注塑制品翘曲变形的影响在模具设计方面,影响塑件变形的因素主要有浇注系统、冷却系统与顶出系统等。
1.浇注系统的设计注塑模具浇口的位置、形式和浇口的数量将影响塑料在模具型腔内的填充状态,从而导致塑件产生变形。
流动距离越长,由冻结层与中心流动层之间流动和补缩引起的内应力越大;反之,流动距离越短,从浇口到制件流动末端的流动时间越短,充模时冻结层厚度减薄,内应力降低,翘曲变形也会因此大为减少。
图1为大型平板形塑件,如果只使用一个中心浇口(如图1a所示)或一个侧浇口(如图1b所示),因直径方向上的收缩率大于圆周方向上的收缩率,成型后的塑件会产生扭曲变形;若改用多个点浇口(如图1c所示)或薄膜型浇口(如图1d所示),则可有效地防止翘曲变形。
a)中心浇口 b) 侧浇口 c)多点浇口 d) 薄膜型浇口图1 浇口形式对塑料件变形的影响当采用点浇进行成型时,同样由于塑料收缩的异向性,浇口的位置、数量都对塑件的变形程度有很大的影响。
图2为一箱形制件在不同浇口数目与分布下的试验图。
a)直浇口 b)10个点浇口 c)8个点浇口d)4个点浇口 e) 6个点浇口 f) 4个点浇口图2 实验浇口的设置由于采用的是30%玻璃纤维增强PA6,而得到的是重量为4.95kg的大型注塑件,因此沿四周壁流动方向上设有许多加强肋,这样,对各个浇口都能获得充分的平衡。
实验结果表明,按图f设置浇口具有较好的效果。
塑料制品的翘曲变形的原因分析和解决方法图文稿
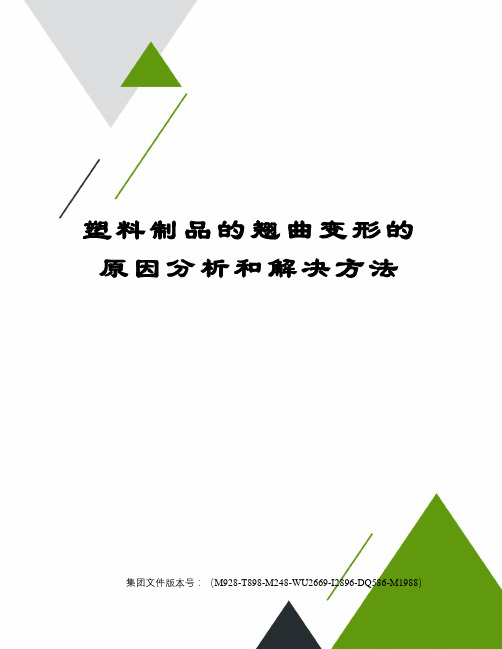
塑料制品的翘曲变形的原因分析和解决方法集团文件版本号:(M928-T898-M248-WU2669-I2896-DQ586-M1988)塑料制品的翘曲变形的原因分析和解决方法一、前言翘曲变形是指注塑制品的形状偏离了模具型腔的形状,它是塑料制品常见的缺陷之一。
出现翘曲变形的原因很多,单靠工艺参数解决往往力不从心。
结合相关资料和实际工作经验,下面对影响注塑制品翘曲变形的因素作简要分析。
二、模具的结构对注塑制品翘曲变形的影响。
在模具方面,影响塑件变形的因素主要有浇注系统、冷却系统与顶出系统等。
1.浇注系统注塑模具浇口的位置、形式和浇口的数量将影响塑料在模具型腔内的填充状态,从而导致塑件产生变形。
流动距离越长,由冻结层与中心流动层之间流动和补缩引起的内应力越大;反之,流动距离越短,从浇口到制件流动末端的流动时间越短,充模时冻结层厚度减薄,内应力降低,翘曲变形也会因此大为减少。
一些平板形塑件,如果只使用一个中心浇口,因直径方向上的收缩率大于圆周方向上的收缩率,成型后的塑件会产生扭曲变形;若改用多个点浇口或薄膜型浇口,则可有效地防止翘曲变形。
当采用点浇口进行成型时,同样由于塑料收缩的异向性,浇口的位置、数量都对塑件的变形程度有很大的影响。
另外,多浇口的使用还能使塑料的流动比(L/t)缩短,从而使模腔内熔体密度更趋均匀,收缩更均匀。
同时,整个塑件能在较小的注塑压力下充满。
而较小的注射压力可减少塑料的分子取向倾向,降低其内应力,因而可减少塑件的变形。
2. 冷却系统在注射过程中,塑件冷却速度的不均匀也将形成塑件收缩的不均匀,这种收缩差别导致弯曲力矩的产生而使塑件发生翘曲。
如果在注射成型平板形塑件(如手机电池壳)时所用的模具型腔、型芯的温度相差过大,由于贴近冷模腔面的熔体很快冷却下来,而贴近热模腔面的料层则会继续收缩,收缩的不均匀将使塑件翘曲。
因此,注塑模的冷却应当注意型腔、型芯的温度趋于平衡,两者的温差不能太大(此时可考虑使用两个模温机)。
翘曲变形原因
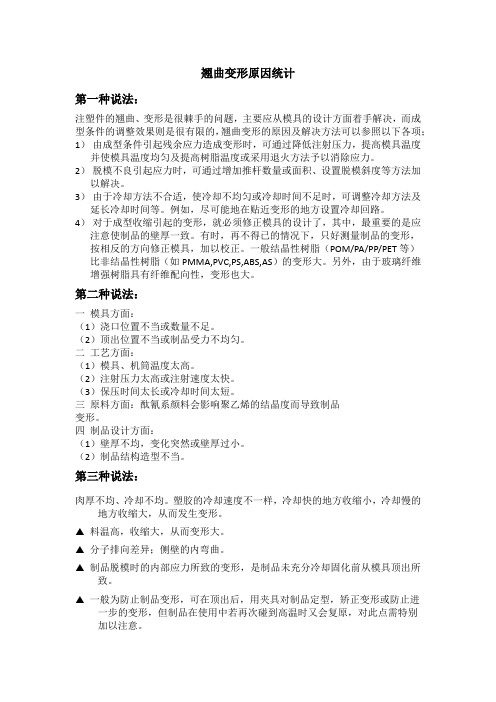
翘曲变形原因统计第一种说法:注塑件的翘曲、变形是很棘手的问题,主要应从模具的设计方面着手解决,而成型条件的调整效果则是很有限的,翘曲变形的原因及解决方法可以参照以下各项;1)由成型条件引起残余应力造成变形时,可通过降低注射压力,提高模具温度并使模具温度均匀及提高树脂温度或采用退火方法予以消除应力。
2)脱模不良引起应力时,可通过增加推杆数量或面积、设置脱模斜度等方法加以解决。
3)由于冷却方法不合适,使冷却不均匀或冷却时间不足时,可调整冷却方法及延长冷却时间等。
例如,尽可能地在贴近变形的地方设置冷却回路。
4)对于成型收缩引起的变形,就必须修正模具的设计了,其中,最重要的是应注意使制品的壁厚一致。
有时,再不得已的情况下,只好测量制品的变形,按相反的方向修正模具,加以校正。
一般结晶性树脂(POM/PA/PP/PET等)比非结晶性树脂(如PMMA,PVC,PS,ABS,AS)的变形大。
另外,由于玻璃纤维增强树脂具有纤维配向性,变形也大。
第二种说法:一模具方面:(1)浇口位置不当或数量不足。
(2)顶出位置不当或制品受力不均匀。
二工艺方面:(1)模具、机筒温度太高。
(2)注射压力太高或注射速度太快。
(3)保压时间太长或冷却时间太短。
三原料方面:酞氰系颜料会影响聚乙烯的结晶度而导致制品变形。
四制品设计方面:(1)壁厚不均,变化突然或壁厚过小。
(2)制品结构造型不当。
第三种说法:肉厚不均、冷却不均。
塑胶的冷却速度不一样,冷却快的地方收缩小,冷却慢的地方收缩大,从而发生变形。
☐料温高,收缩大,从而变形大。
☐分子排向差异;侧壁的内弯曲。
☐制品脱模时的内部应力所致的变形,是制品未充分冷却固化前从模具顶出所致。
☐一般为防止制品变形,可在顶出后,用夹具对制品定型,矫正变形或防止进一步的变形,但制品在使用中若再次碰到高温时又会复原,对此点需特别加以注意。
第四种说法:如果制件的收缩均匀,那么成型件不会发生变形或翘曲,只是单纯地变小了。
- 1、下载文档前请自行甄别文档内容的完整性,平台不提供额外的编辑、内容补充、找答案等附加服务。
- 2、"仅部分预览"的文档,不可在线预览部分如存在完整性等问题,可反馈申请退款(可完整预览的文档不适用该条件!)。
- 3、如文档侵犯您的权益,请联系客服反馈,我们会尽快为您处理(人工客服工作时间:9:00-18:30)。
变形的调试心得1、首先是温度问题,按照我们常规理解的,变形会往温度高的方向变,但是事实却不一定如此,这与产品的近胶口有很大的关系,如果是胶口在产品中间的话,平板产品一般会完前模变形,这时通过增加后模模具的温度,产品的变形量会减小很多!如果胶口是在边上的话,变形那就不同了!2、二次压使用高大会导致变形量加大,所以建议尽量使用一次压,将转换位置减小,保压速度加快!二次压就能减到最小,但是这样如果锁模力不够的话,批锋会比较严重的哦!所以说,在新模调试的时候要尽量想办法去控制变形量,最好是从模具温度以及参数上去想办法!(这当然是建立在模具结构不能改变的基础上来说的)塑料射出成形先天上就会发生收缩,因为从制程温度降到室温,会造成聚合物的密度变化,造成收缩。
整个塑件和剖面的收缩差异会造成内部残留应力,其效应与外力完全相同。
在射出成形时假如残留应力高于塑件结构的强度,塑件就会于脱模后翘曲,或是受外力而产生破裂。
7-1 残留应力残留应力(residual stress)是塑件成形时,熔胶流动所引发(flow-induced)或者热效应所引发(thermal-induced),而且冻结在塑件内的应力。
假如残留应力高过于塑件的结构强度,塑件可能在射出时翘曲,或者稍后承受负荷而破裂。
残留应力是塑件收缩和翘曲的主因,可以减低充填模穴造成之剪应力的良好成形条件与设计,可以降低熔胶流动所引发的残留应力。
同样地,充足的保压和均匀的冷却可以降低热效应引发的残留应力。
对于添加纤维的材料而言,提升均匀机械性质的成形条件可以降低热效应所引发的残留应力。
7-1-1 熔胶流动引发的残留应力在无应力下,长链高分子聚合物处在高于熔点温度呈现任意卷曲的平衡状态。
于成形程中,高分子被剪切与拉伸,分子链沿着流动方向配向。
假如分子链在完全松弛平衡之前就凝固,分子链配向性就冻结在塑件内,这种应力冻结状态称为流动引发的残留应力,其于流动方向和垂直于流动方向会造成不均匀的机械性质和收缩。
一般而言,流动引发的残留应力比热效应引发的残留应力小一个次方。
塑件在接近模壁部份因为承受高剪应力和高冷却速率的交互作用,其表面的高配向性会立即冻结,如图7-1所示。
假如将此塑件存放于高温环境下,塑件将会释放部份应力,导致.的收缩与翘曲。
凝固层的隔热效应使聚合物中心层维持较高温度,能够释放较多应力,所以中心层分子链具有较低的配向性。
保压的多段应用对变形有什么作用一段补缩,二段封浇口,三段缓冲一段消除產品應力,二段補縮,三段消除澆口應力原因:[1]冷却不充分[2]直浇口的脱模不良[3]冷却不均匀[4]射出压力不适宜[5]浇口位置不适当[6]模芯偏倚解决办法:i)延长冷却时间ii)降低模具温度i)请参阅"直浇口的脱模不良"一节i)尽量使成形品的壁厚均匀ii)减少型腔与模蕊温差,产品会向温度偏高的模具方向弯曲变形。
iii)缩小棱i )修正冷却水槽沟i)调到弯曲最小的压力,同时注意分段压力对产品变形影响。
i)设置到薄层部位i)修正模蕊ii)改为多点浇口消除制品变形的方法一.产生变形的原因1-1品的形状,特别是成形收缩率同制品厚度的关系而引起的残留应力。
1-2 由于成型条件产生的残余应力;1-3 脱模时产生的残余应力;1-4 由于冷却时间不足而引起变形二.相关联的知识2-1 制品的变形(翘曲、弯曲、小皱纹)同产生裂纹的原因一样。
即制品内残余内应力。
成型的设定条件应朝消除制品内应力的方向设定。
即提高料筒温度、模具温度后,在材料流动性变好的状态下,射出压力不要太高。
2-2 为了减少残余内应力,有进行退火处理,即在热变形温度10度以下,2小时以上的加热就有消除内应力的效果。
但这种方式的退火因费用高而使用的不普遍。
2-3 如果模具的冷却水孔不能对制品进行均匀冷却,也会产生残余应力,这就意味着冷却水孔不能太浅。
三、解决方法。
3-1 即时:在模具内充分冷却固化(延长冷却时间记时器),提高料筒温度,降低射出压力。
3-2 短期:使模具冷却均匀化。
3-3 长期:避免制品厚度的差异,在制品厚度大的地方设置浇口(1-1),因直线容易引起翘曲,做成大的R曲线(图A),制品可逆弯曲的模具(图B),增加顶出杆个数,增加脱模斜度。
四、于材料的差异:4-1 结晶性的材料(聚乙稀、聚丙稀、聚甲醛、尼龙)成型收缩率大,还有容易引起偏向,非结晶性材料(聚苯乙稀、ABS)容易引起残余应力。
五、参考事项:5-1 成型后在常温下用矫正器保持,能稍微防止变形,但不能抱有太大的期望。
5-2 在薄形的箱子成型中,因成型温度引起的弯曲,这常见于单单是热膨胀翘曲定义取出治具图示[此帖子已被 yushang200 在 2007-11-21 18:44:00 编辑过]所用设备(东芝全电式射出成型机)这是材料的分子取向性流动及受热不均匀导致收缩量不一致;1模具温度的分布均匀性,加水道2料管温度,看产品储料位置一定很长,故材料热比重不均匀(适当降低第二段温度);2模具尾端的排气要增加!是压克力的,主要是用的PMMA,摸具温度一般在75度左右,因为要保证光学,目前主要是靠改善模具温度来调整产品冷却后的取向以及在产品取出时用治具强制取向,冷却后靠应力恢复来控制翘曲,产品不会有过填充的情况.17寸的产品周期在45S左右,因为用以上方式翘曲大小很难掌握,希望能有通过成型条件来控制翘曲的变化.模温控制只是一种方式,有时候调整模温效果不明显,而且公母模温不能相差太大看一下进胶位置,射速不要太快,射胶时间调整,保压小些,不缩水就好模温是一种改变变形的方法,有时效果不是太大可以通过压缩功能来调整,第一段压力大往下递减动定模各用个模温机方便通过温度来改变变形注意动定模温度不能相差太大翘曲变形一、模具方面:(1)浇口位置不当或数量不足。
(2)顶出位置不当或制品受力不均匀。
二、工艺方面:(1)模具、机筒温度太高。
(2)注射压力太高或注射速度太快。
(3)保压时间太长或冷却时间太短。
三、原料方面:酞氰系颜料会影响聚乙烯的结晶度而导致制品变形。
四、制品设计方面:(1)壁厚不均,变化突然或壁厚过小。
(2)制品结构造型不当。
对于薄壁投影面积大的产品一般来说都存在着变形这一问题,主要表现在刚生产出来时,平面很直,但过了一段时间后中间部位就会凹进去,所以我们在生产此类部品时就应该让产品出模时平面呈凸形,待其冷却后就直了。
要让产品呈凸形还是凹形其实很简单。
可通过调整前后模温或产品饱满程度来实现,一般来说,模温高的那一面会凹,产品打得越饱其凸形越大。
注塑制品的翘曲变形分析一、引言翘曲变形是指注塑制品的形状偏离了模具型腔的形状,它是塑料制品常见的缺陷之一。
随着塑料工业的发展,人们对塑料制品的外观和使用性能要求越来越高,翘曲变形程度作为评定产品质量的重要指标之一也越来越多地受到模具设计者的关注与重视。
模具设计者希望在设计阶段预测出塑料件可能产生翘曲的原因,以便加以优化设计,从而提高注塑生产的效率和质量,缩短模具设计周期,降低成本。
本文主要对在注塑模具设计过程中影响注塑制品翘曲变形的因素加以分析。
二、模具的结构对注塑制品翘曲变形的影响在模具设计方面,影响塑件变形的因素主要有浇注系统、冷却系统与顶出系统等。
1.浇注系统的设计注塑模具浇口的位置、形式和浇口的数量将影响塑料在模具型腔内的填充状态,从而导致塑件产生变形。
流动距离越长,由冻结层与中心流动层之间流动和补缩引起的内应力越大;反之,流动距离越短,从浇口到制件流动末端的流动时间越短,充模时冻结层厚度减薄,内应力降低,翘曲变形也会因此大为减少。
图1为大型平板形塑件,如果只使用一个中心浇口(如图1a所示)或一个侧浇口(如图1b所示),因直径方向上的收缩率大于圆周方向上的收缩率,成型后的塑件会产生扭曲变形;若改用多个点浇口(如图1c所示)或薄膜型浇口(如图1d所示),则可有效地防止翘曲变形。
a) 中心浇口b) 侧浇口c)多点浇口d) 薄膜型浇口当采用点浇进行成型时,同样由于塑料收缩的异向性,浇口的位置、数量都对塑件的变形程度有很大的影响。
图2为一箱形制件在不同浇口数目与分布下的试验图。
a)直浇口b)10个点浇口c)8个点浇口d)4个点浇口e) 6个点浇口f) 4个点浇口由于采用的是30%玻璃纤维增强PA6,而得到的是重量为4.95kg的大型注塑件,因此沿四周壁流动方向上设有许多加强肋,这样,对各个浇口都能获得充分的平衡。
实验结果表明,按图f设置浇口具有较好的效果。
但并非浇口数目越多越好。
实验证明,按图c设计的浇口比图a的直浇口还差。
另外,多浇口的使用还能使塑料的流动比(L/t)缩短,从而使模腔内物料密度更趋均匀,收缩更均匀。
同时,整个塑件能在较小的注塑压力下充满。
而较小的注射压力可减少塑料的分子取向倾向,降低其内应力,因而可减少塑件的变形。
2.冷却系统的设计在注射过程中,塑件冷却速度的不均匀也将形成塑件收缩的不均匀,这种收缩差别导致弯曲力矩的产生而使塑件发生翘曲。
如果在注射成型平板形塑件时所用的模具型腔、型芯的温度相差过大,如图3所示,由于贴近冷模腔面的熔体很快冷却下来,而贴近热模腔面的料层则会继续收缩,收缩的不均匀将使塑件翘曲。
因此,注塑模的冷却应当注意型腔、型芯的温度趋于平衡,两者的温差不能太大。
除了考虑塑件内外表面的温度趋于平衡外,还应考虑塑件各侧的温度一致,即模具冷却时要尽量保持型腔、型芯各处温度均匀一致,使塑件各处的冷却速度均衡,从而使各处的收缩更趋均匀,有效地防止变形的产生。
因此,模具上冷却水孔的布置至关重要。
在管壁至型腔表面距离确定后,应尽可能使冷却水孔之间的距离小,才能保证型腔壁的温度均匀一致。
同时,由于冷却介质的温度随冷却水道长度的增加而上升,使模具的型腔、型芯沿水道产生温差。
因此,要求每个冷却回路的水道长度小于2m。
在大型模具中应设置数条冷却回路,一条回路的进口位于另一条回路的出口附近。
对于长条形塑件,应采用如图4所示的冷却回路,减少冷却回路的长度,即减少模具的温差,从而保证塑件均匀冷却,图5为回路设计方案。
3.顶出系统的设计顶出系统的设计也直接影响塑件的变形。
如果顶出系统布置不平衡,将造成顶出力的不平衡而使塑件变形。
因此,在设计顶出系统时应力求与脱模阻力相平衡。
另外,顶出杆的截面积不能太小,以防塑件单位面积受力过大(尤其在脱模温度太高时)而使塑件产生变形。
顶杆的布置应尽量靠近脱模阻力大的部位。
在不影响塑件质量(包括使用要求、尺寸精度与外观等)的前提下,应尽可能多设顶杆以减少塑件的总体变形。
用软质塑料来生产大型深腔薄壁的塑件时,由于脱模阻力较大,而材料又较软,如果完全采用单一的机械式顶出方式,将使塑件产生变形,甚至顶穿或产生折叠而造成塑件报废,如改用多元件联合或气(液)压与机械式顶出相结合的方式效果会更好。