注塑模成型部分(模仁)设计原则
塑料加工工艺中的模具设计原则

塑料加工工艺中的模具设计原则引言对于塑料制品的生产而言,其模具设计是至关重要的步骤。
一款均衡、合理的模具设计将能够为塑料加工工艺中的高效、稳定和持续的生产打下基础,同时还能缩短生产周期和降低生产成本。
因此,本文将从以下几个方面入手,谈谈在塑料加工工艺中模具设计的原则。
一、选择合适的模具材料模具材料是模具设计的重要原则之一。
在模具设计中,必须确保所选材料的物理、化学特性满足生产过程的要求。
而对于塑料制品的生产而言,常用的模具材料主要有钢、铝、钛、铸铁、硅铁等。
这些材料各有优缺点,所以在实际生产中要根据产品的需求和生产的要求来选择合适的模具材料。
例如,钢材的硬度高、强度大、耐磨损性能好,能承受高压和高温等极端环境条件,因此在生产大型、复杂、长寿命的产品时,钢模具是最佳选择。
二、模具的结构设计模具结构设计是模具设计的另一个重要原则。
模具的结构应具有足够的强度和稳定性,能够承受生产过程中的高压和高温等极端环境条件,同时还要考虑成形件的尺寸精度、表面质量和竖向尺寸的一致性等要素。
而在选择模具结构时,还要考虑生产成本和加工难度等因素,以便生产过程中的高效、稳定和持续性。
三、模具的加工工艺设计在模具设计中,加工工艺的选择和设计也是非常重要的原则之一。
因为模具的加工精度和外观质量直接决定了成品的质量。
而在选择加工工艺时,也要根据模具的结构特点和生产成本、加工周期等因素来进行综合考虑,以确保生产加工过程的高效、稳定和持续性。
四、模具的维护保养模具的设计是非常关键的,但在生产过程中同样重要的是模具的维护保养。
因为模具的长期使用和高强度的生产加工过程会导致其损耗和磨损,从而影响塑料制品的生产质量。
而为了尽可能地延长模具的使用时间、保证生产效率和成本效益,在生产过程中必须对模具进行定期维修和保养,以确保其长寿命、稳定和持续性。
结论模具设计是塑料制品生产过程中非常重要的环节,也决定了塑料制品的质量和生产效率。
因此在模具设计中,必须依据产品需求和生产要求,选择合适的材料、设计合理的结构、选择合适的加工工艺,并对模具进行定期维修和保养,以确保生产加工过程的高效、稳定和持续性。
注塑模具设计原则

注塑模的设计原则
注塑模的设计-----注塑模的设计原则一般包括如下:
单向流动。
流动平衡。
恒定压力梯度。
最大剪切应力。
熔接痕/熔合痕放置。
避免滞留。
避免潜流。
可控制的摩擦加热。
流道热阀。
可接受流道/型腔比
以下是这些模具设计原则的基本解释:
单方向的流动设计原则是保证在填充过程中,塑料应该在一个方向上流动 ,并且保持一个直的流动前沿。
这导致单方向定位的产生。
平衡的流动所有的流动路径应该是平衡的那就是,在相同时间以相同压力进行充填。
压力梯度最有效率的填充方式是压力梯度 (压力降低对单位长度) 沿着流动
路径是固定的时候。
最大剪应力最大剪应力剪应力在填充的时候应该是小于材料临界的最大剪切应力,数值依赖于材料和应用。
熔接/融合位置在最不敏感部位放置熔接和融合线。
避免滞留仅可能避免在流体流动路径分为厚的和薄流动路径那里设置浇口。
避免潜流通过浇口的设置避免潜流保证流体在最后充填区相遇。
磨擦加热为控制的磨擦加热设计流道, 增加型腔熔体温度,这将在产品中获得较低的应力,而不不引起塑料的降解因塑料长期处于较高的温度。
流道热阀利用热阀设计流道系统, 保证浇口冻结时型腔刚好充填完毕和已
充分保压这避免在模具充填完毕后过保压或产生倒流。
流道/型腔比为高压力降设计流道系统, 使流道材料最小获得一个低比率的流道/型腔设计。
在通常的模具设计过程中,应遵循基本的设计原则,保证设计模具的合理性,而这些原则对注塑CAE分析结果的研究提供的分析依据。
注塑模具设计之PL模仁模座的设计

PL面的設計
強度與加工的考量
插破面角度1.5
模仁設計
模仁厚度的決定需要考慮加上冷卻水管後所需的基本厚 度,與維持模仁強度的厚度。模仁強度主要考量是能承 受射出壓力,不致因射出壓力而導致模板變形,進而使 產品產生毛邊。模仁強度設計需考慮到a.射出壓力 b.產品 投影面積 c.產品高度 d.產品厚度 e.產品外型 f.產品投影外 型 g.模穴總數量。
下固定板
大水口模座
有托道套 直道套 道柱G.P
回針 面針板
大水口系列模座
上固定板
脫板
母模板 A Plate
推板
公模板
B Plate
托板 托銷 S.P
方鐵
C Plate
底針板
下固定板
細水口模座
有托道套 直道套 道柱G.P
回針 面針板
細水口模座
工字模
直身 模
簡化型細水口
細水 口
• 模仁寬度必須可以放置在兩個 模腳之間的距離。
• 模仁長度儘量不要超過回位銷 的距離。
• 如果有滑塊機構可以適當的加 大模座。
R.P. Return Pin 回位銷
模座
❖ 因為模仁長為630mm﹐加2RP及安全距 ❖ 所以模板長大約為800mm, ❖ 因為寬為400mm,加2模腳寬大約100mm ❖ 所以模板寬為 600 ❖ 又因為是直身模 ❖ 所以 模座為 CT6080 A200 B200 C150
模仁安全尺寸參考表
產品(制件)尺寸
產產品品 ((制制件件))
安全距離
註:模具設計時,會要求設計人員將模仁尺寸取為整數,因 此安全距離並非定值;可根據產品(制件)尺寸做調整。
模仁厚度與模板厚度參考表
母(定)模板厚 公(動)模板厚
注塑模具设计原则和核心是什么

注塑模具设计原则和核心是什么一、开模方向和分型线每个注塑产品在开始设计时首先要确定其开模方向和分型线,以保证尽可能减少抽芯滑块机构和消除分型线对外观的影响。
1、开模方向确定后,产品的加强筋、卡扣、凸起等结构尽可能设计成与开模方向一致,以避免抽芯减少拼缝线,延长模具寿命。
2、开模方向确定后,可选择适当的分型线,避免开模方向存在倒扣,以改善外观及性能。
二、脱模斜度1 、适当的脱模斜度可避免产品拉毛(拉花)。
光滑表面的脱模斜度应≥0.5度,细皮纹(砂面)表面大于1度,粗皮纹表面大于1.5度。
2 、适当的脱模斜度可避免产品顶伤,如顶白、顶变形、顶破。
3、深腔结构产品设计时外表面斜度尽量要求大于内表面斜度,以保证注塑时模具型芯不偏位,得到均匀的产品壁厚,并保证产品开口部位的材料强度。
三、产品壁厚1 、各种塑料均有一定的壁厚范围,一般0.5~4mm,当壁厚超过4mm 时,将引起冷却时间过长,产生缩印等问题,应考虑改变产品结构。
2 、壁厚不均会引起表面缩水。
3 、壁厚不均会引起气孔和熔接痕。
四、加强筋1、加强筋的合理应用,可增加产品刚性,减少变形。
2、加强筋的厚度必须≤ (0.5~0.7)T产品壁厚,否则引起表面缩水。
3、加强筋的单面斜度应大于1.5°,以避免顶伤。
五、圆角1、圆角太小可能引起产品应力集中,导致产品开裂。
2、圆角太小可能引起模具型腔应力集中,导致型腔开裂。
3、设置合理的圆角,还可以改善模具的加工工艺,如型腔可直接用R刀铣加工,而避免低效率的电加工。
4 、不同的圆角可能会引起分型线的移动,应结合实际情况选择不同的圆角或清角。
六、孔1 、孔的形状应尽量简单,一般取圆形。
2 、孔的轴向和开模方向一致,可以避免抽芯。
3 、当孔的长径比大于2时,应设置脱模斜度。
此时孔的直径应按小径尺寸(最大实体尺寸)计算。
4 、盲孔的长径比一般不超过4。
防孔针冲弯5 、孔与产品边缘的距离一般大于孔径尺寸。
七、注塑模的抽芯、滑块机构及避免1、当塑件按开模方向不能顺利脱模时,应设计抽芯滑块机构。
模具设计原则和核心以及注意事项
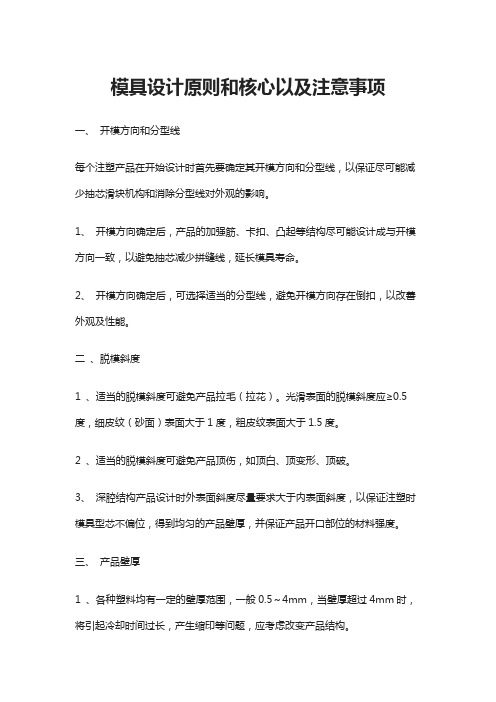
模具设计原则和核心以及注意事项 一、 开模方向和分型线每个注塑产品在开始设计时首先要确定其开模方向和分型线,以保证尽可能减少抽芯滑块机构和消除分型线对外观的影响。
1、 开模方向确定后,产品的加强筋、卡扣、凸起等结构尽可能设计成与开模方向一致,以避免抽芯减少拼缝线,延长模具寿命。
2、 开模方向确定后,可选择适当的分型线,避免开模方向存在倒扣,以改善外观及性能。
二 、脱模斜度1 、适当的脱模斜度可避免产品拉毛(拉花)。
光滑表面的脱模斜度应≥0.5度,细皮纹(砂面)表面大于1度,粗皮纹表面大于1.5度。
2 、适当的脱模斜度可避免产品顶伤,如顶白、顶变形、顶破。
3、 深腔结构产品设计时外表面斜度尽量要求大于内表面斜度,以保证注塑时模具型芯不偏位,得到均匀的产品壁厚,并保证产品开口部位的材料强度。
三、 产品壁厚1 、各种塑料均有一定的壁厚范围,一般0.5~4mm,当壁厚超过4mm时,将引起冷却时间过长,产生缩印等问题,应考虑改变产品结构。
2、壁厚不均会引起表面缩水。
3 、壁厚不均会引起气孔和熔接痕。
四、加强筋1、 加强筋的合理应用,可增加产品刚性,减少变形。
2、 加强筋的厚度必须≤ (0.5~0.7)T产品壁厚,否则引起表面缩水。
3、 加强筋的单面斜度应大于1.5°,以避免顶伤。
五、圆角1、 圆角太小可能引起产品应力集中,导致产品开裂。
2、圆角太小可能引起模具型腔应力集中,导致型腔开裂。
3、 设置合理的圆角,还可以改善模具的加工工艺,如型腔可直接用R刀铣加工,而避免低效率的电加工。
4 、不同的圆角可能会引起分型线的移动,应结合实际情况选择不同的圆角或清角。
六、 孔1 、孔的形状应尽量简单,一般取圆形。
2 、孔的轴向和开模方向一致,可以避免抽芯。
3 、当孔的长径比大于2时,应设置脱模斜度。
此时孔的直径应按小径尺寸(最大实体尺寸)计算。
4 、盲孔的长径比一般不超过4。
防孔针冲弯5 、孔与产品边缘的距离一般大于孔径尺寸。
注塑模设计规范

注塑模具设计规范1.产品结构要求制品工艺性分析与脱模斜度确定1)制品应有足够的强度和刚性。
2)制品壁厚均匀,变化不超过40%;对于特别厚的部位要采取减胶措施。
3)加强筋大端的厚度不超过制品壁厚的一半。
4)制品上的文字原则上采用凸型字,以便于加工。
5)制品形状应避免产生模具结构上的薄钢位。
6)不影响制品装配及外观的部位应设计1°以上的脱模斜度,影响外观的部位需防止缩水,应通过计算确定合理的脱模斜度。
7)有特殊要求(如蚀皮纹等)的制品,脱模斜度应不小于2.5°。
8)在不影响外观的前提下,尽量出工艺圆角,避免锐角处不加过渡圆角。
9)产品颜色及蚀纹必须在产品策划时确定。
2. 模具分类:根据模架尺寸将模具分为大、中、小三类。
1)模架尺寸6060以上称为大型模具。
2)模架尺寸3030~6060之间为中型模具。
3)模架尺寸3030以下为(小模)具。
3. 模架选用与设计1)优先选用标准模架,具体按QJ/MM03.01《标准塑胶模架》执行。
2)若选用选用非标模架,应优先选用标准板厚,具体参照QJ/MM03.01《标准塑胶模架》。
3)大型非标模架,导柱直径不小于Φ60mm,导套采用铸铜制做。
4)大型非标模架导套孔壁厚不得小于10mm,回针孔壁厚为35~40mm,回针直径不小于Φ30。
5)大型非标模架A板、B板起吊螺钉孔为M36~M48。
6)450T注塑机以上的模具,模板的四面要有吊环孔,各模板间要有撬模角7)如有可能产生较大侧压力时(型腔深度超过50mm),非标大型模架应设计原身止口。
8)使用尽可能多的支柱,保证模具在工作中不变形,支柱用螺钉固定在动模座板上。
9)模具导柱长度应比最高的动模型芯长20mm以上。
10)模具上须安装模脚,如果零件突出模具之外,模脚的高度须高出突出在模具之外的零件。
4. 分型面设计原则1)选择分型面选择首先必须符合我方要求。
2)避免在制品外表产生夹线,如无法避免时应尽量将夹线设计在不易看见的部位。
模具设计原则

模具设计原则
模具设计原则是指在进行模具设计时应该遵循的一些基本原则,包括以下几点:
1. 功能性原则:模具设计必须满足产品的功能要求,能够正确、稳定地加工出产品。
2. 合理性原则:模具设计应尽量简化结构,并考虑加工、操作、维护等各个环节的方便性,提高生产效率。
3. 经济性原则:模具设计应尽量降低制造成本,包括材料费用、加工费用等。
4. 可靠性原则:模具设计应保证模具的寿命长,能够稳定地使用,不易出现故障。
5. 互换性原则:模具设计应考虑产品的标准化、系列化要求,使得多款产品可以共用一套模具。
6. 可维护性原则:模具设计应考虑模具使用过程中的保养、维修等方面,便于日常维护与修理。
7. 安全性原则:模具设计应考虑使用者的安全,避免发生意外事故。
8. 环保性原则:模具设计应尽量减少对环境的污染,降低能源消耗,节约资源。
这些原则在模具设计中起到了指导作用,可以提高模具的使用效果和寿命,降低生产成本,提高产品质量。
注塑模--成型部分(模仁)设计原则
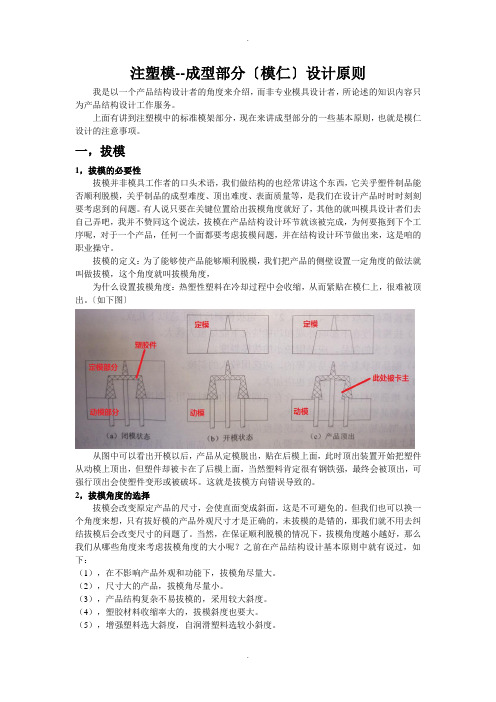
注塑模--成型部分〔模仁〕设计原则我是以一个产品结构设计者的角度来介绍,而非专业模具设计者,所论述的知识内容只为产品结构设计工作服务。
上面有讲到注塑模中的标准模架部分,现在来讲成型部分的一些基本原则,也就是模仁设计的注意事项。
一,拔模1,拔模的必要性拔模并非模具工作者的口头术语,我们做结构的也经常讲这个东西,它关乎塑件制品能否顺利脱模,关乎制品的成型难度、顶出难度、表面质量等,是我们在设计产品时时时刻刻要考虑到的问题。
有人说只要在关键位置给出拔模角度就好了,其他的就叫模具设计者们去自己弄吧,我并不赞同这个说法,拔模在产品结构设计环节就该被完成,为何要拖到下个工序呢,对于一个产品,任何一个面都要考虑拔模问题,并在结构设计环节做出来,这是咱的职业操守。
拔模的定义:为了能够使产品能够顺利脱模,我们把产品的侧壁设置一定角度的做法就叫做拔模,这个角度就叫拔模角度,为什么设置拔模角度:热塑性塑料在冷却过程中会收缩,从而紧贴在模仁上,很难被顶出。
〔如下图〕从图中可以看出开模以后,产品从定模脱出,贴在后模上面,此时顶出装置开始把塑件从动模上顶出,但塑件却被卡在了后模上面,当然塑料肯定很有钢铁强,最终会被顶出,可强行顶出会使塑件变形或被破坏。
这就是拔模方向错误导致的。
2,拔模角度的选择拔模会改变原定产品的尺寸,会使直面变成斜面,这是不可避免的。
但我们也可以换一个角度来想,只有拔好模的产品外观尺寸才是正确的,未拔模的是错的,那我们就不用去纠结拔模后会改变尺寸的问题了。
当然,在保证顺利脱模的情况下,拔模角度越小越好,那么我们从哪些角度来考虑拔模角度的大小呢?之前在产品结构设计基本原则中就有说过,如下:(1),在不影响产品外观和功能下,拔模角尽量大。
(2),尺寸大的产品,拔模角尽量小。
(3),产品结构复杂不易拔模的,采用较大斜度。
(4),塑胶材料收缩率大的,拔模斜度也要大。
(5),增强塑料选大斜度,自润滑塑料选较小斜度。
- 1、下载文档前请自行甄别文档内容的完整性,平台不提供额外的编辑、内容补充、找答案等附加服务。
- 2、"仅部分预览"的文档,不可在线预览部分如存在完整性等问题,可反馈申请退款(可完整预览的文档不适用该条件!)。
- 3、如文档侵犯您的权益,请联系客服反馈,我们会尽快为您处理(人工客服工作时间:9:00-18:30)。
注塑模--成型部分(模仁)设计原则
我是以一个产品结构设计者的角度来介绍,而非专业模具设计者,所论述的知识内容只为产品结构设计工作服务。
上面有讲到注塑模中的标准模架部分,现在来讲成型部分的一些基本原则,也就是模仁设计的注意事项。
一,拔模
1,拔模的必要性
拔模并非模具工作者的口头术语,我们做结构的也经常讲这个东西,它关乎塑件制品能否顺利脱模,关乎制品的成型难度、顶出难度、表面质量等,是我们在设计产品时时时刻刻要考虑到的问题。
有人说只要在关键位置给出拔模角度就好了,其他的就叫模具设计者们去自己弄吧,我并不赞同这个说法,拔模在产品结构设计环节就该被完成,为何要拖到下个工序呢,对于一个产品,任何一个面都要考虑拔模问题,并在结构设计环节做出来,这是咱的职业操守。
拔模的定义:为了能够使产品能够顺利脱模,我们把产品的侧壁设置一定角度的做法就叫做拔模,这个角度就叫拔模角度,
为什么设置拔模角度:热塑性塑料在冷却过程中会收缩,从而紧贴在模仁上,很难被顶出。
(如下图)
从图中可以看出开模以后,产品从定模脱出,贴在后模上面,此时顶出装置开始把塑件从动模上顶出,但塑件却被卡在了后模上面,当然塑料肯定很有钢铁强,最终会被顶出,可强行顶出会使塑件变形或被破坏。
这就是拔模方向错误导致的。
2,拔模角度的选择
拔模会改变原定产品的尺寸,会使直面变成斜面,这是不可避免的。
但我们也可以换一个角度来想,只有拔好模的产品外观尺寸才是正确的,未拔模的是错的,那我们就不用去纠结拔模后会改变尺寸的问题了。
当然,在保证顺利脱模的情况下,拔模角度越小越好,那么我们从哪些角度来考虑拔模角度的大小呢?之前在产品结构设计基本原则中就有说过,如下:
(1),在不影响产品外观和功能下,拔模角尽量大。
(2),尺寸大的产品,拔模角尽量小。
(3),产品结构复杂不易拔模的,采用较大斜度。
(4),塑胶材料收缩率大的,拔模斜度也要大。
(5),增强塑料选大斜度,自润滑塑料选较小斜度。
(6),制品壁厚大,拔模斜度也要打。
(7),制品精度高,拔模角度尽量小。
二,分型面
分型面的定义:模具闭合时动模和定模相接触的曲面就是分型面。
1,分型面的位置
简单来描述,当模具闭合,除了用来填充塑料溶体的空腔意外,上下模其他部分全是紧密接触的,紧密接触的这个面就是分型面。
从这里可以看出,相对于上下模而言,接触面就是分型面,但是模具就是根据分型面来分模的,就是说先有分型面,后才有模仁的上下模面。
那么分型面的位置还是要由产品结构来定。
如下图:
不同的分模面的位置都可以制造出同一个产品,但其成本、质量等就不一样了。
对于(b)图,动模部分的槽坑是很难加工的,并且塑件与后模接触面积很大,并且大部分在窄槽中,是很难被顶出的,就会造成加工成本高,生产效率低等问题。
对于(c)图,分型面在产品侧边大概中间位置,当产品顶出后,在分型面的位置处会出现合模痕迹,影响外观。
综合来看,还是(a)图比较合理。
这就告诉我们,同一个零件选择不同的分模面其造价、效率、质量等都会被影响。
2,分型面的选取原则
有些产品的结构简单明了,一看就知道在哪里分型,可有些产品结构比较复杂,可提供多种分型方案,这就需要合理分析后再确定,可这个任务也有我们结构设计者的份,因为在我们设计产品结构时,特别是对壳体零件,有时候会有个分型线要确定,不然后续结构没法完成,那模具设计者可直接参考我们的分型线来确定分型面。
塑件的最大外形是判断分型面的一个最基本、最重要的方法,也就是说,分型面要设在塑件脱模方向上最大投影边缘的部位。
具体分型面的选取原则:
(1),有利于塑件脱模,一般来讲,分模后,我们将塑件留在后模上面,有利于顶出。
也就是后模做成凸起的部分,定模是凹陷部分。
怎么使塑件留在后模上呢?在后模上可加一个拉料杆,可保证塑件保留在后模上。
(2),确保表面质量,尽量避免分型面走在塑件产品的外观面上。
(3),有利于模具加工。
(4),有利于排气,当分型面作为主要排气渠道时,应将分型面设计在塑料的流动末端,
以利于排气。
如下图,(b)图的排气效果就好于(a)图。
(5),尽量简化模具结构,尽可能避免侧向抽芯。
3,模具定位设计
当模具精度要求高或者分型面高低差较大时,要做定位设计,就是做管位设计。
管位是承担模具定位功能的结构,可以是虎口形、长条形、圆形等,但都时在两个模板上凹凸相对应。
三,镶件
1,镶件的做法
动定模仁并不是一块整铁加工出来的,内部是由一块块的镶件组成的。
如果一个复杂的
模仁是要一整块钢铁来加工,那会有相当高加工难度,或者直接就做不出来。
如下图来看看
模仁中镶件的情况。
可以看出不加镶件和加镶件的成型结果是一样的,动、定模仁并非是铁板一块,这里的加镶块可以将镶块和模仁同时加工,加快工作效率。
另外,请注意不要将镶件与嵌件相混淆,镶件只是模具里面用到,而嵌件则是在产品结构设计和注塑成型时用到的,比如在塑胶件成型时嵌入一个螺母,这才是嵌件。
2,镶件的意义
(1),方便加工与维修
有些形状复杂特殊,加工很困难,并且很不容易维修,所以要用镶件来降低加工和维修成本。
(2),便于成型和脱模
比如一些比较深且窄的加强筋,如果不使用镶件,不但加工困难,而且成型时排气困难,易造成射不饱、烧焦、接痕等缺陷。
如下图:
(a)图就是说加强筋太深且窄,不易充满的问题,(b)图不使用镶件容易出现包风现象,不易顶出。
(3),增加模具强度
如果成型零件上有小面积的插破(或靠破),为了提高模具强度,提高模具寿命,可以把插破(或靠破)的部分做成镶件。
模具通过插破的方式来成型这个倒扣,上下模仁在插破的地方来回接触碰撞,如果使用一般的模具材料,使用次数多就会被破坏,所以可以将此处插破部分用好的材料做成镶件来增加模具强度。
(4),节省材料,降低成本
具体来讲有以下四个方面:
①在哪里拆分镶件,要不要拆分镶件,要根据实际的加工能力来确定,形状复杂、加工困难、需要多次修配的地方需要考虑拆分镶件。
②外观面尽量不要拆镶件。
③对于大型的拼装模具,镶块尽量规则,尺寸尽量取整。
④结构件中出现通孔或者盲孔时,对应成型位置一般用镶件处理。
3,靠破、插破和枕位
在成形通孔时,有两个术语:靠破和插破。
如下图:
要成形此图中的两个通孔,通孔部分无塑料溶体填充,那这部分只能被模具中的金属填充。
对于A处通孔,采用插破和靠破方式,B处采用靠破方式,并在此处做成了镶件。
关于枕位如下图:
4,镶件的固定
镶件的固定有两种方式,一是利用自身挂台固定(镶件较小),一种是螺丝固定(镶件较大)。
如下图详解:。