复合材料综述
复合材料文献综述
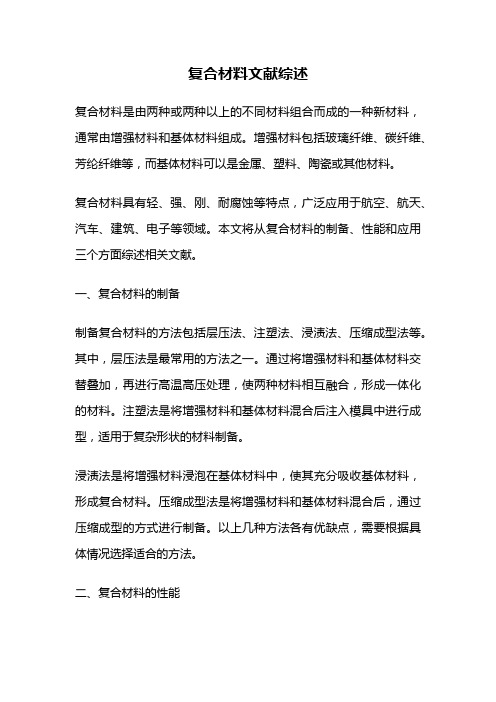
复合材料文献综述复合材料是由两种或两种以上的不同材料组合而成的一种新材料,通常由增强材料和基体材料组成。
增强材料包括玻璃纤维、碳纤维、芳纶纤维等,而基体材料可以是金属、塑料、陶瓷或其他材料。
复合材料具有轻、强、刚、耐腐蚀等特点,广泛应用于航空、航天、汽车、建筑、电子等领域。
本文将从复合材料的制备、性能和应用三个方面综述相关文献。
一、复合材料的制备制备复合材料的方法包括层压法、注塑法、浸渍法、压缩成型法等。
其中,层压法是最常用的方法之一。
通过将增强材料和基体材料交替叠加,再进行高温高压处理,使两种材料相互融合,形成一体化的材料。
注塑法是将增强材料和基体材料混合后注入模具中进行成型,适用于复杂形状的材料制备。
浸渍法是将增强材料浸泡在基体材料中,使其充分吸收基体材料,形成复合材料。
压缩成型法是将增强材料和基体材料混合后,通过压缩成型的方式进行制备。
以上几种方法各有优缺点,需要根据具体情况选择适合的方法。
二、复合材料的性能复合材料具有轻、强、刚、耐腐蚀等特点,其主要性能取决于增强材料和基体材料的选择及其比例。
例如,碳纤维增强复合材料具有高强度、高刚度、低密度等优点,适用于航空、航天和汽车等领域。
玻璃纤维增强复合材料则具有低成本、良好的电绝缘性和耐腐蚀性等特点,适用于建筑、电子等领域。
复合材料的热膨胀系数和热导率也是其性能考虑的重要因素。
热膨胀系数低的复合材料具有良好的热稳定性,适用于高温环境下的应用。
热导率低的复合材料则适用于需要绝缘的场合。
三、复合材料的应用复合材料在航空、航天、汽车、建筑、电子等领域都有广泛应用。
在航空航天领域,碳纤维增强复合材料被广泛应用于飞机和火箭等结构件的制造中,以提高其强度和刚度,降低重量。
在汽车领域,玻璃纤维增强复合材料被用于制造汽车外壳和底盘等部件,以提高其耐腐蚀性和减轻重量。
在建筑领域,复合材料被用于制造墙板、地板、屋顶等结构件,以提高其抗震性和防火性。
在电子领域,复合材料被用于制造电路板、电容器等部件,以提高其绝缘性和耐高温性。
铜钢复合材料的应用与生产综述

铜/钢复合材料的应用与生产综述0 引言为了使金属材料最大限度地发挥出其所具有的性能,其方法之一就是把性能不同的材料加以组合制成复合材料。
金属复合板的研究最早是美国于1860年开始的,工业性生产始于20世纪30年代。
当时美国为了降低成本,提高强度,开始了镍复合钢板的生产,其后不断进行了旨在提高结合性能的制造技术开发。
20世纪30年代,苏联也对铝、锡、钢等金属与合金的复合材料进行了初步研究,所采用的生产工艺主要有轧制法、铸造法、爆炸法、扩散焊接法等。
其中,对冷轧复合法的工艺及力学性能研究较为深入,试生产了08F钢基体上复合18-8型不锈钢的三层耐蚀复合板。
20世纪50-60年代,英国伯明翰大学等单位对固相复合进行了较为系统的研究,取得了很大成就。
日本在复合材料方面的研究虽较晚,但进步迅速,近年来成为从事金属复合材料研究最多的国家之一。
我国的复合板研究始于20世纪60年代初,主要方法有爆炸焊接、爆炸焊接+轧制、热轧、冷轧等,主要研究单位有上海钢铁研究所、东北大学、北京科技大学、武汉大学等。
铜/钢复合材料(在钢表面复合铜或铜合金)由于具有防腐蚀、抗磨损、导电导热性优良、美观、成本低等优点, 在军工、电子、造币、炊具及建筑装饰等领域有着广阔的应用前景, 其研究也越来越引起国内外的关注。
本文主要介绍铜/钢复合材料的应用、生产方法的新进展。
1 铜/钢复合材料的应用1.1 民用方面铜/钢复合材料在民用方面的应用主要体现在炊具及建筑装饰领域。
为了保护食品, 日常使用不锈钢锅, 但不锈钢锅导热不良, 加热时容易产生局部高温而粘底, 通过复一层高导热材料铜制成铜/钢复合材料可很好地解决这个问题。
在建筑装饰领域使用铜/钢复合材料代替铜及铜合金做屋顶、门窗的框架及屋顶的气窗等, 不仅庄严美观, 而且强度高, 成本低;同时,由于内层的钢板导热率较低, 因此可使用较小的烙铁以较低的温度进行焊接, 进而可缩短焊接时间。
此外, 还使用钢复黄铜H62或H68制做标牌、扶手、家具等。
陶瓷基复合材料综述

不同金属、陶瓷基体和陶瓷基复合材料的断裂韧性比较
整体陶瓷
颗粒增韧
相变增韧
材
料
AlB2BO B3B
SiC
AlB2BOB 3B/Ti C
SiB3BNB4B /TiC
ZrOB2B/ MgO
ZrOB2B/Y B2BOB3
B
ZrOB2B/ AlB2B O3B
断裂韧性
MPa/mP1/2 2.7~4.2
P
4.5~ 6.0
烧结
(温度, 时间)
后处理
(二次 加工)
成品
2.1 传统普通工艺
2.1.1 粉末冶金工艺 (冷压与烧结工艺)
粉末制备
表 3-1 颗粒形状和粉末生产方式
粉体: 粉体是介于致密体与 胶体之间的颗粒集合物,其 颗粒当量直径在 0.1 微米和 1 毫米之间。
颗粒形状
球状 液滴状 板片状 碟状 角状 树枝状 多孔海绵状 不规则形状
很明显,传统的单一材料无法满足以上综合要 求,当前作为单一的金属、陶瓷、聚合物等材料虽 然仍在不断日新月异地发展,但是以上这些材料由 于其各自固有的局限性而不能满足现代科学技术发 展的需要。
复合材料的发展历史
6000年前人类就已经会用稻草加粘土作为建筑复 合材料。
水泥复合材料已广泛地应用于高楼大厦和河堤大坝 等的建筑,发挥着极为重要的作用;20世纪40年代,美 国用碎布酚醛树脂制备枪托、代替木材,发展成为玻璃 纤维增强塑料(玻璃钢)这种种广泛应用的较现代化复 合材料。
气相法多用于制备超细、高纯的非氧化物陶瓷材料。
2.1 传统普通工艺
2.1.1 粉末冶金工艺 (冷压与烧结工艺) 压制工艺 单向或双向的模压 等静压制、振动压制、粉末轧制及粉浆浇注
无人机结构用复合材料及制造技术综述
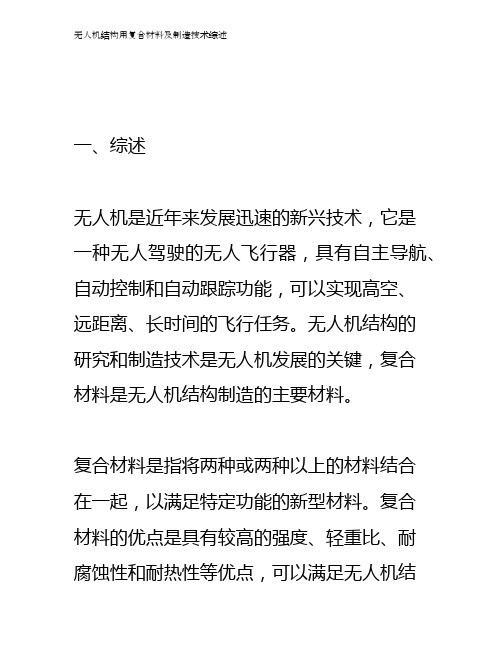
一、综述无人机是近年来发展迅速的新兴技术,它是一种无人驾驶的无人飞行器,具有自主导航、自动控制和自动跟踪功能,可以实现高空、远距离、长时间的飞行任务。
无人机结构的研究和制造技术是无人机发展的关键,复合材料是无人机结构制造的主要材料。
复合材料是指将两种或两种以上的材料结合在一起,以满足特定功能的新型材料。
复合材料的优点是具有较高的强度、轻重比、耐腐蚀性和耐热性等优点,可以满足无人机结构的高性能要求。
目前,复合材料已经成为无人机结构的主要材料,广泛应用于无人机的机身、机翼、尾翼和螺旋桨等部件的制造。
1、复合材料的分类复合材料可以分为两大类:有机复合材料和无机复合材料。
有机复合材料主要由碳纤维和树脂组成,具有较高的强度、轻重比和耐腐蚀性,可以用于制造无人机的机身、机翼、尾翼和螺旋桨等部件。
无机复合材料主要由陶瓷纤维、玻璃纤维和金属纤维组成,具有较高的强度、耐热性和耐腐蚀性,可以用于制造无人机的发动机、燃料系统和控制系统等部件。
2、复合材料的制造技术复合材料的制造技术主要包括碳纤维增强塑料(CFRP)技术、玻璃纤维增强塑料(GFRP)技术和金属纤维增强塑料(MFRP)技术。
(1)碳纤维增强塑料(CFRP)技术碳纤维增强塑料(CFRP)技术是将碳纤维和树脂结合在一起制成的复合材料,具有较高的强度、轻重比、耐腐蚀性和耐热性等优点,可以用于制造无人机的机身、机翼、尾翼和螺旋桨等部件。
CFRP技术的制造过程主要包括碳纤维层压、树脂浇注、固化和表面处理等步骤。
(2)玻璃纤维增强塑料(GFRP)技术玻璃纤维增强塑料(GFRP)技术是将玻璃纤维和树脂结合在一起制成的复合材料,具有较高的强度、耐热性和耐腐蚀性,可以用于制造无人机的发动机、燃料系统和控制系统等部件。
GFRP技术的制造过程主要包括玻璃纤维层压、树脂浇注、固化和表面处理等步骤。
(3)金属纤维增强塑料(MFRP)技术金属纤维增强塑料(MFRP)技术是将金属纤维和树脂结合在一起制成的复合材料,具有较高的强度、耐热性和耐腐蚀性,可以用于制造无人机的发动机、燃料系统和控制系统等部件。
MOFs柔性复合材料综述
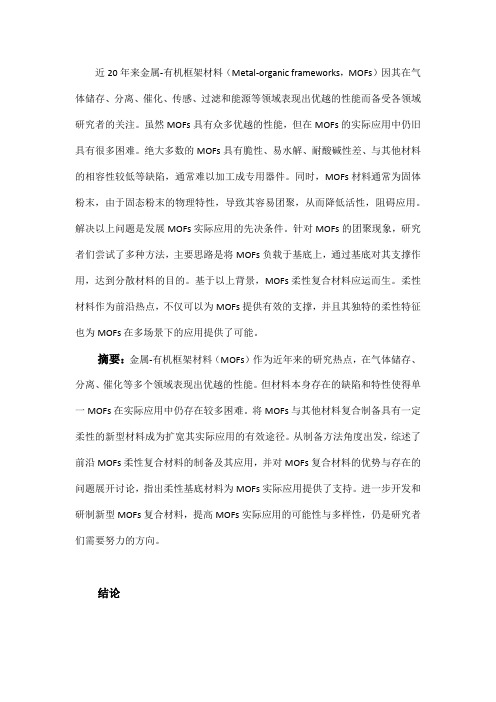
近20年来金属-有机框架材料(Metal-organic frameworks,MOFs)因其在气体储存、分离、催化、传感、过滤和能源等领域表现出优越的性能而备受各领域研究者的关注。
虽然MOFs具有众多优越的性能,但在MOFs的实际应用中仍旧具有很多困难。
绝大多数的MOFs具有脆性、易水解、耐酸碱性差、与其他材料的相容性较低等缺陷,通常难以加工成专用器件。
同时,MOFs材料通常为固体粉末,由于固态粉末的物理特性,导致其容易团聚,从而降低活性,阻碍应用。
解决以上问题是发展MOFs实际应用的先决条件。
针对MOFs的团聚现象,研究者们尝试了多种方法,主要思路是将MOFs负载于基底上,通过基底对其支撑作用,达到分散材料的目的。
基于以上背景,MOFs柔性复合材料应运而生。
柔性材料作为前沿热点,不仅可以为MOFs提供有效的支撑,并且其独特的柔性特征也为MOFs在多场景下的应用提供了可能。
摘要:金属-有机框架材料(MOFs)作为近年来的研究热点,在气体储存、分离、催化等多个领域表现出优越的性能。
但材料本身存在的缺陷和特性使得单一MOFs在实际应用中仍存在较多困难。
将MOFs与其他材料复合制备具有一定柔性的新型材料成为扩宽其实际应用的有效途径。
从制备方法角度出发,综述了前沿MOFs柔性复合材料的制备及其应用,并对MOFs复合材料的优势与存在的问题展开讨论,指出柔性基底材料为MOFs实际应用提供了支持。
进一步开发和研制新型MOFs复合材料,提高MOFs实际应用的可能性与多样性,仍是研究者们需要努力的方向。
结论MOFs作为一种新兴的多孔材料,在气体储存、催化、分离、传感和能源等多个领域展现出优异的性能。
然而,MOFs的粉体形式限制了其应用的进一步拓展。
MOFs通过与不同的基底材料相结合,制备的MOFs新型复合材料成为解决其实际应用的有效手段。
但发展中仍存在一些不足:(1)混合基质膜虽可以很好地包裹MOFs,一定程度上增加了MOFs材料的稳定性,但同时也牺牲了MOFs与目标物的接触,降低了有效成分的活性。
导电高分子复合材料综述

导电高分子复合材料综述导电高分子复合材料是一种结合了导电填料和高分子基体的非金属导电材料。
由于其优异的导电性能和高分子材料的良好工艺性能,导电高分子复合材料在电子、电器、电磁波屏蔽、静电防护等领域得到了广泛应用。
本文将从导电填料、高分子基体、制备方法和应用领域等方面综述导电高分子复合材料的研究进展。
导电填料是导电高分子复合材料中的关键组成部分。
目前常用的导电填料包括金属填料、碳黑、导电纤维和导电聚合物等。
金属填料具有良好的导电性能,但其加工性差,易生锈。
碳黑填料性能稳定,但存在聚集现象,导致流变性能下降。
导电纤维可以提供较高的导电性能,但通常与高分子基体的相容性较差。
导电聚合物由于能够形成连续的导电网络,并且可以与高分子基体较好地相容,因此成为近年来发展的研究热点。
高分子基体对导电高分子复合材料的力学性能、导电性能和工艺性能等起着重要影响。
常用的高分子基体包括聚合物树脂、热塑性弹性体和热塑性聚合物等。
聚合物树脂由于具有良好的力学性能和化学稳定性,因此广泛应用于导电高分子复合材料。
热塑性弹性体由于可以在一定温度范围内恢复弹性,因此在导电弹性体材料中得到了广泛应用。
热塑性聚合物由于具有良好的工艺性能,在导电高分子复合材料中也得到了较好的应用效果。
制备方法是影响导电高分子复合材料性能的关键因素之一、常用的制备方法包括溶液共混法、熔融共混法、反应挤出法和电沉积法等。
溶液共混法通过将导电填料和高分子基体溶解在适当的溶剂中,然后通过挥发溶剂的方式获得导电高分子复合材料。
熔融共混法是将导电填料和高分子基体在高温下混炼,然后通过冷却固化得到复合材料。
反应挤出法是通过聚合反应实现导电高分子复合材料的制备。
电沉积法是将金属填料等导电材料沉积在高分子基体上来制备导电高分子复合材料。
导电高分子复合材料在电子、电器、电磁波屏蔽、静电防护等领域具有广阔的应用前景。
在电子和电器领域,导电高分子复合材料可以用于生产导电薄膜、导线、印刷电路板等;在电磁波屏蔽领域,导电高分子复合材料可以用于制备导电涂层和导电材料;在静电防护领域,导电高分子复合材料可以用于制备静电消除器和防静电材料。
陶瓷基复合材料综述报告
陶瓷基复合材料综述报告陶瓷基复合材料是以陶瓷为基体与各种纤维复合的一类复合材料,具有优异的耐高温性能,主要用作高温及耐磨制品。
陶瓷基体可为氮化硅、碳化硅等高温结构陶瓷。
这些先进陶瓷具有耐高温、高强度和刚度、相对重量较轻、抗腐蚀等优异性能,而其致命的弱点是具有脆性,处于应力状态时,会产生裂纹,甚至断裂导致材料失效。
而采用高强度、高弹性的纤维与基体复合,则是提高陶瓷韧性和可靠性的一个有效的方法。
纤维能阻止裂纹的扩展,从而得到有优良韧性的纤维增强陶瓷基复合材料。
迄今,陶瓷基复合材料已实用化或即将实用化的领域有刀具、滑动构件、发动机制件、能源构件等。
有些发达国家已将长纤维增强碳化硅复合材料应用于制造高速列车的制动件,显示出优异的摩擦磨损特性,取得了不错的使用效果[1]。
一、陶瓷基复合材料增强体用于复合材料的增强体品种很多,根据复合材料的性能要求,主要分为以下几种[2-4] :1.1纤维类增强体纤维类增强体有连续长纤维和短纤维。
连续长纤维的连续长度均超过数百。
纤维性能有方向性,一般沿轴向均有很高的强度和弹性模量。
1.2颗粒类增强体颗粒类增强体主要是一些具有高强度、高模量。
耐热、耐磨。
耐高温的陶瓷等无机非金属颗粒,主要有碳化硅、氧化铝、碳化钛、石墨。
细金刚石、高岭土、滑石、碳酸钙等。
主要还有一些金属和聚合物颗粒类增强体,后者主要有热塑性树脂粉末1.3晶须类增强体晶须是在人工条件下制造出的细小单晶,一般呈棒状,其直径为0.2~1微米,长度为几十微米,由于其具有细小组织结构,缺陷少,具有很高的强度和模量。
1.4金属丝用于复合材料的高强福、高模量金属丝增强物主要有铍丝、钢丝、不锈钢丝和钨丝等,金属丝一般用于金属基复合材料和水泥基复合材料的增强,但前者比较多见。
1.5片状物增强体用于复合材料的片状增强物主要是陶瓷薄片。
将陶瓷薄片叠压起来形成的陶瓷复合材料具有很高的韧性。
二、陶瓷基的界面及强韧化理论陶瓷基复合材料(CMC)具有高强度、高硬度、高弹性模量、热化学稳定性等优异性能,被认为是推重比10以上航空发动机的理想耐高温结构材料。
碳纤维复合材料发展方向及前景综述
在当今世界,碳纤维复合材料作为一种轻量化、高强度的新型材料,已经在诸多领域展现出了巨大的发展潜力。
从航空航天到汽车制造,从体育器材到建筑材料,碳纤维复合材料都展现出了其独特的优势和潜力。
本文将对碳纤维复合材料的发展方向及前景进行综述,旨在帮助读者更全面、深刻地了解这一重要材料的未来走向。
1. 碳纤维复合材料的基本概念碳纤维复合材料是由碳纤维和树脂基体组成的复合材料。
碳纤维具有轻质、高强度、高模量、耐高温和耐腐蚀等优点。
而树脂基体则起着粘结和保护作用。
碳纤维复合材料的制备工艺主要包括预浸法、纺丝法和层压法等。
2. 碳纤维复合材料在航空航天领域的应用碳纤维复合材料在航空航天领域具有重要意义。
它们可以减轻飞机和航天器的重量,提高飞行性能,延长使用寿命,并且有利于节能减排。
未来的发展方向包括更高强度、更低密度的碳纤维复合材料的研发,以及更加智能化的制造工艺和设计方法。
3. 碳纤维复合材料在汽车制造领域的应用碳纤维复合材料在汽车制造领域也有着广阔的应用前景。
它们可以降低汽车的整体重量,提高燃油效率,增加汽车的安全性和舒适性。
未来汽车领域的发展方向包括降低碳纤维复合材料的成本,加快大规模生产工艺的研发,以及更加环保和可持续的材料回收利用方案。
4. 碳纤维复合材料在体育器材领域的应用在体育器材领域,碳纤维复合材料已经成为了许多高端器材的首选材料。
它们轻盈、坚固、具有良好的弹性和吸震性能,可以有效提高运动员的表现。
未来,随着运动科技的不断发展,碳纤维复合材料在体育器材领域的应用前景将会更加广阔。
5. 碳纤维复合材料在建筑材料领域的应用在建筑领域,碳纤维复合材料在结构加固、新型材料研发等方面具有广泛的应用前景。
它们具有较高的抗拉强度、抗压强度和耐久性能,可以提高建筑结构的安全性和耐久性,同时减轻结构自重,有利于节能减排。
总结回顾通过本文的综合介绍,我们可以看到碳纤维复合材料作为一种新型材料,具有广阔的应用前景和发展空间。
复合材料简介
复合材料简介学院:电子信息与自动化专业:电气工程及其自动化学号:11023214姓名:乔盖群综述:复合材料,是由两种或两种以上不同性质的材料,通过物理或化学的方法,在宏观上组成具有新性能的材料。
各种材料在性能上互相取长补短,产生协同效应,使复合材料的综合性能优于原组成材料而满足各种不同的要求。
复合材料使用的历史可以追溯到古代。
从古至今沿用的稻草或麦秸增强粘土和已使用上百年的钢筋混凝土均由两种材料复合而成。
20世纪40年代,因航空工业的需要,发展了玻璃纤维增强塑料(俗称玻璃钢),从此出现了复合材料这一名称。
50年代以后,陆续发展了碳纤维、石墨纤维和硼纤维等高强度和高模量纤维。
70年代出现了芳纶纤维和碳化硅纤维。
这些高强度、高模量纤维能与合成树脂、碳、石墨、陶瓷、橡胶等非金属基体或铝、镁、钛等金属基体复合,构成各具特色的复合材料。
定义:由异质、异性、异形的有机聚合物、无机非金属、金属等材料作为基体或增强体,通过复合工艺组合而成的材料。
除具备原材料的性能外,同时能产生新的性能。
分类:复合材料是一种混合物。
在很多领域都发挥了很大的作用,代替了很多传统的材料。
复合材料按其组成分为金属与金属复合材料、非金属与金属复合材料、非金属与非金属复合材料。
按其结构特点又分为:①纤维增强复合材料。
将各种纤维增强体置于基体材料内复合而成。
如纤维增强塑料、纤维增强金属等。
②夹层复合材料。
由性质不同的表面材料和芯材组合而成。
通常面材强度高、薄;芯材质轻、强度低,但具有一定刚度和厚度。
分为实心夹层和蜂窝夹层两种。
③细粒复合材料。
将硬质细粒均匀分布于基体中,如弥散强化合金、金属陶瓷等。
④混杂复合材料。
由两种或两种以上增强相材料混杂于一种基体相材料中构成。
与普通单增强相复合材料比,其冲击强度、疲劳强度和断裂韧性显著提高,并具有特殊的热膨胀性能。
分为层内混杂、层间混杂、夹芯混杂、层内/层间混杂和超混杂复合材料。
60年代为满足航空航天等尖端技术所用材料的需要,先后研制和生产了以高性能纤维(如碳纤维、硼纤维、芳纶纤维、碳化硅纤维等)为增强材料的复合材料,其比强度大于4×106厘米(cm),比模量大于4×108cm。
复合材料 (2)综述
陶瓷基复合材料摘要: 材料是科学技术发展的基础,材料的发展可以推动科学技术的发展,材料主要有金属材料、聚合物材料、无机非金属材料和复合材料四大类. 复合材料是不同的材料结合在一起、形成一种结构较为复杂的材料。
近年来,通过往陶瓷中加入或生成成颗粒、晶须、纤维等增强材料,使陶瓷的韧性大大地改善,而且强度及模量也有一定的提高。
陶瓷复合基材料就是以陶瓷材料为基体,并以陶瓷、碳纤维、难熔金属纤维、晶须、晶片和颗粒等为增强体,通过适当的复合工艺所构成的复合材料。
本文主要综述了陶瓷基复合材料的发展状况,分类,基体,增强体,以及制备工艺等内容。
关键词:陶瓷基复合材料、基体、增强、制备。
1 陶瓷基复合材料的发展概况。
陶瓷材料作为技术革命的新材料早在十几年前就引起了美国的关注。
近年来由于日本、美国、欧洲的竞相研究陶瓷材料技术得到迅速发展。
作为能适应各种环境的新型结构材料陶瓷材料已步入了实用化阶段。
为使陶瓷在更大范围内达到实用化国内外都对能改善陶瓷韧性陶瓷基复合材料进行了广泛研究。
陶瓷基复合材料(CMC)由于具有高强度、高硬度、高弹性模量、热化学稳定性等优异性能,是制造推重比10 以上航空发动机的理想耐高温结构材料。
一方面,它克服了单一陶瓷材料脆性断裂的缺点,提高了材料的断裂韧性;另一方面,它保持了陶瓷基体耐高温、低膨胀、低密度、热稳定性好的优点。
陶瓷基复合材料的最高使用温度可达1650℃,而密度只有高温合金的70%。
因此,近几十年来,陶瓷基复合材料的研究有了较快发展。
目前CMC 正在航空发动机的高温段的少数零件上作评定性试用。
2 陶瓷基复合材料的分类按增强材料形态分类,陶瓷基复合材料可分为颗粒增强陶瓷复合材料、纤维增强陶瓷复合材料、片材增强陶瓷复合材料。
按基体材料分类,陶瓷基复合材料可分为氧化物基陶瓷复合材料、非氧化物基陶瓷复合材料、碳/碳复合材料、微晶玻璃基复合材料。
3 瓷基体的种类陶瓷基体材料主要以结晶和非结晶两种形态的化合物存在,按照组成化合物的元素不同,又可以分为氧化物陶瓷、碳化物陶瓷、氮化物陶瓷等。
- 1、下载文档前请自行甄别文档内容的完整性,平台不提供额外的编辑、内容补充、找答案等附加服务。
- 2、"仅部分预览"的文档,不可在线预览部分如存在完整性等问题,可反馈申请退款(可完整预览的文档不适用该条件!)。
- 3、如文档侵犯您的权益,请联系客服反馈,我们会尽快为您处理(人工客服工作时间:9:00-18:30)。
金属基陶瓷复合材料制备技术研究进展与应用*付鹏,郝旭暖,高亚红,谷玉丹,陈焕铭(宁夏大学物理电气信息工程学院,银川750021)摘要综述了国内外在金属基陶瓷复合材料制备技术方面的最新研究进展与应用现状,展望了国内金属基陶瓷复合材料的未来发展。
关键词金属基陶瓷复合材料制备技术应用Development and Future Applications of Metal Matrix CompositesFabrication TechniqueFU Peng, HAO Xunuan, GAO Yahong, GU Yudan, CHEN Huanming (School of Physics & Electrical Information Engineering, Ningxia University, Yinchuan 750021) Abstract Recent development and future applications of metal matrix compositesfabricationtechnique are reviewed andsome prospects of the development in metal matrix composites at home are put forward.Key words metal-based ceramic composites, fabrication technique, applications前言:现代高技术的发展对材料的性能日益提高,单料已很难满足对性能的综合要求,材料的复合化是材料发展的必然趋势之一。
陶瓷的高强度、高硬度、高弹性模量以及热化学性稳定等优异性能是其主要特点,但陶瓷所固有的脆性限制着其应用范围及使用可靠性[1—3]。
因此,改善陶瓷的室温韧性与断裂韧性,提高其在实际应用中的可靠性一直是现代陶瓷研究的热点。
与陶瓷基复合材料相比,通常金属基复合材料兼有陶瓷的高强度、耐高温、抗氧化特性,又具有金属的塑性和抗冲击性能,应用范围更广,诸如摩擦磨损类材料、航空航天结构件、耐高温结构件、汽车构件、抗弹防护材料等。
1 金属基陶瓷复合材料的制备金属基陶瓷复合材料是20世纪60年代末发展起来的,目前金属基陶瓷复合材料按增强体的形式可分为非连续体增强(如颗粒增强、短纤维与晶须增强)、连续纤维增强(如石墨纤维、碳化硅纤维、氧化铝纤维等)[4—6]。
实际制备过程中除了要考虑基体金属与增强体陶瓷之间的物性参数匹配之外,液态金属与陶瓷间的浸润性能则往往限制了金属基陶瓷复合材料的品种。
目前,金属基陶瓷复合材料的制备方法主要有以下几种。
1.1 粉末冶金法粉末冶金法制备金属基陶瓷复合材料即把陶瓷增强体粉末与金属粉末充分混合均匀后进行冷压烧结、热压烧结或者热等静压,对于一些易于氧化的金属,烧结时通入惰性保护气体进行气氛烧结。
颗粒增强、短纤维及晶须增强的金属基陶瓷复合材料通常采用此种方法,其主要优点是可以通过控制粉末颗粒的尺寸来实现相应的力学性能,而且,粉末冶金法制造机械零件是一种终成型工艺,可以大量减少机加工量,节约原材料,但粉末冶金法的生产成本并不比熔炼法低[7]。
1.2 熔体搅拌法熔体搅拌法是将制备好的陶瓷增强体颗粒或晶须逐步混合入机械或电磁搅拌的液态或半固态金属熔体中冷却形成坯锭的过程,制备过程对设备的要求较低,生产制备工艺相对简单。
由于伴随搅拌过程,材料中容易形成气孔和夹杂而影响产品的质量,同时基体和增强体之间的密度差往往造成增强体分布不均匀的现象。
熔体搅拌法制备的工件通常需要进一步的热处理和二次机加工来达到使用性能的要求[8]。
1.3 金属陶瓷共沉积法在喷射沉积制备金属材料的基础上发展的金属陶瓷共沉积法是将液态金属通过氩气等惰性气体雾化成金属液滴,金属液滴在喷射途中与增强体陶瓷颗粒碰撞会合,共同沉积于水冷衬底上复合形成金属基陶瓷复合材料。
由于金属液滴尺寸小,凝固冷却速率快,无宏观偏析等快速凝固材料的优越特性,抑制了界面的高温反应,材料微观组织均匀性高,但金属陶瓷共沉积法工艺优化条件复杂,容易出现不够密实的组织疏松等冶金缺陷[9,10]。
1.4 叠层复合法叠层式金属基复合材料是先将不同金属板用扩散方法结合,然后用离子溅射或分子束外延将金属层/陶瓷层叠合成复合材料。
这种复合材料性能好,已经少量应用于航空航天及军用设备上,如航天飞机中部的货舱桁架、卫星上的天线结构件、波导管、运输机货舱地板等,但叠层复合法工艺复杂,材料有明显的各向异性[11—13]。
1.5 浸渗法浸渗法分为压力浸渗和无压浸渗,首先需要把增强体做成多孔预制件,然后在压力或无压条件下将液态金属渗入多孔预制件。
对于液态金属与陶瓷浸润性能差的复合体系采用压力浸渗法将液态金属压入多孔预制件,对于浸润性能好、预制件孔径小的复合体系可利用熔体的毛细力无压浸渗。
无论是压力浸渗还是无压浸渗,多孔预制件的互连通性对复合材料的密实度及力学性能等有重要影响,另外,为消除气体对材料性能的影响,发展了真空热压与真空无压浸渗[14—17]。
2 金属基陶瓷复合材料的应用近十多年来,工业发达国家都制定了全国性的研究计划来大力发展金属基复合材料,其长远目标是发展一种使用温度和力学性能介于Ni基高温合金和高温陶瓷材料之间的高温结构材料,使其使用温度更高而高温力学性能特别是强韧性更好。
金属基陶瓷复合材料是实施这一目标的一个重要方面。
迄今为止,金属基陶瓷复合材料的加工工艺尚不够完善,还没有形成大规模批量生产,受到的主要制约因素是加工难度高、加工时间长等。
目前最大的应用出路是在汽车工业方面,如氧化铝增强铝合金制成镶圈以代替含镍奥氏体铸铁镶圈,不仅耐磨性相当,还可以减轻质量、简化工艺和降低成本。
另外,发动机缸套、连杆、连杆销、刹车盘等也在试用金属基陶瓷复合材料制造。
其他方面如运动器材、自行车车架、各种型材以及装甲车履带、轻质防弹装甲等也有报道,但用量较少[18]。
由于其制造成本高,工艺复杂,使之与金属材料相比出现价格高、稳定性差等问题,阻碍其应用进程。
通过深入研究组织结构与性能的关系,适度控制界面反应,探索新的复合工艺方法等提高生产效率和改善制品质量是进一步扩大金属基陶瓷复合材料应用的关键。
近年来发展了一种以多孔陶瓷作为预制体,利用无压浸渍工艺制备具有金属/陶瓷网络互穿结构的金属基复合材料的工艺路线,从而找到了一个有可能突破应用困难的缺口[19,20]。
金属基陶瓷复合材料的研究热点3.1 金属基陶瓷复合材料的界面结构金属基陶瓷复合材料的界面结构对复合材料性能的影响极大,多数金属基复合材料是以界面反应的形式相结合,但是界面反应的程度受工艺方法及温度参数的控制,所以制备的界面微区结构非常复杂。
界面结构一方面起到传递应力的作用,另一方面使裂纹偏转和吸收能量[21],因此通过控制工艺方法和优化制备过程获得最佳界面结合状态是金属基陶瓷复合材料界面结构研究的重要内容之一。
而且,对于界面精细结构的测定和表征,比较清楚地了解界面结构与力学性能间的关系,以及对界面进行预处理来改善界面润湿性和控制界面反应产物等方面的工作对于提高金属基陶瓷复合材料的综合力学性能也至关重要。
近几年来,发展的增强体和增韧体在三维空间网络互穿分布的复合材料复合方法具有显著的特点,如这种复合材料可以容纳更高体积分数的陶瓷相,从而有利于将应力集中迅速分散和传递,抑制基体合金的塑性变形和高温软化,大幅度提高材料的承载能力或抗冲击能力、抗耐磨性等[22—24]。
因此,这种金属/陶瓷网络互穿复合材料由于可以避免传统金属基复合材料存在各向异性的弊端,其界面结构对损伤容限的影响、界面分布状态与形式对裂纹的桥接作用等也是研究者关注的主要方面。
3.2 连续增强金属基陶瓷复合材料的制备连续增强金属基陶瓷复合材料是指陶瓷增强体具有三维连通骨架结构的复合材料。
从材料相组成的空间拓扑分布形式上看,这种三维网络金属/陶瓷骨架复合材料内部金属/ 陶瓷在三维空间上呈连续分布的特点,材料性能更高且成本降低,材料失效的危险性大大降低,引起了国内外学者的广泛关注。
这种三维双连续复合材料制备方法[25,26]可分为两大类:(1)化学反应直接合成(原位复合工艺)微结构连接的复合材料;(2)制造孔隙连通的预制体,然后浸渗金属并凝固成型。
其中,原位复合工艺基本上能克服基体与增强体浸润不良、界面反应产生脆性层、增强体分布不均匀等问题,作为一种具有突破性的新工艺方法而受到普遍的重视,包括直接氧化法、自蔓延法、原位共晶生长法等。
这些方法虽各有特点,但具有共性,即复合材料的强度、韧性以及其他力学性能取决于原位生长的增强相本身物理性质和几何尺寸以及显微组织形态和基体相的含量。
研究热点集中在合金的配制、参与反应物质的设计、工艺方法、原位反应机理和过程的研究以及原位复合材料微结构与性能的研究等方面。
值得一提的是近20年来发展非常迅速的自蔓延高温合成材,由于燃烧过程中反应速度快,温度梯度高,造成生成物的晶体点阵具有高密度的缺陷,易于生成多孔的骨架结构,使生成物具有很大的表面积。
这种方法生产周期短、能耗小、工艺简单较成熟的多孔陶瓷预制体成型与制备技术主要有海绵预制体挂浆成型、陶瓷泡沫成型、陶瓷粉末烧结、溶胶-凝胶等方法。
近年来发展了微波加热工艺、颗粒堆积工艺、注凝成型工艺、凝胶铸造工艺、模板添隙工艺、冷冻干燥工艺等新的制备技术[20,27—29]。
孔隙尺寸则具有较大的变化范围,从溶胶-凝胶法的几纳米、冷冻干燥工艺的几微米到有机泡沫浸浆法可达到的几毫米。
文献[30]报道了连通结构的Al/Al2O3复合材料,孔隙率约1%,陶瓷体体积分数达75%。
实验结果表明陶瓷预制体中的孔隙形貌为略有变形的颗粒堆积空隙,尺寸在0.08~1μm之间。
这种细观结构导致了在陶瓷/金属界面上生成了大量的界面反应过渡带,所制备的材料断裂韧性达10.5MP a穖1/2,断裂强度达810MPa。
3.3 力学性能多尺度计算与设计金属基陶瓷复合材料的力学行为取决于其微观结构特点,正确认识并计算微结构对宏观行为的影响是金属基陶瓷复合材料设计的基础。
该领域的研究人员通过发展微米尺度、纳米尺度和原子尺度的多尺度计算模拟方法[31—35],定量揭示不同层次结构及其演化对宏观力学行为的影响,为材料设计、力学性能预报、实验工艺制定等提供理论指导。
一、复合材料的定义与分类由两个或两个以上独立的物理相,包括粘结材料(基体)和粒料、纤维或片状材料所组成的一种固体产物称为复合材料。
复合材料的组成分为两大部分:基体与增强材料。
基体:构成复合材料连续相的单一材料。
如玻璃钢中的树脂就是基体。
增强材料:复合材料中不构成连续相的材料。