渗碳件质量检查
马氏体级别”的探讨

对《汽车渗碳齿轮金相检验》标准中“马氏体级别”的探讨董秦铮(爱协林工业炉工程(北京)有限公司,北京 100086)摘要:通过生产中的试验例证和检验结果,针对《汽车渗碳齿轮金相检验》标准中“马氏体级别”的概念和评级方法进行了分析和讨论。
认为不宜将“马氏体级别”作为一项独立的质量指标。
关键词:马氏体级别;残留奥氏体;奥氏体晶粒度QC/T262—1999《汽车渗碳齿轮金相检验》是我国汽车行业中长期使用的一项覆盖面较广、影响较大的标准。
在该标准中,“马氏体级别”被作为一项重要的、不可缺少的质量指标。
标准中规定:马氏体等级按其针体大小确定,共分8个级别,评定马氏体级别和评定残留奥氏体级别一样,共同使用一套残留奥氏体、马氏体级别的标准图片(400倍,8张),所评定的结果均在1~5级内为合格。
但是,汽车零部件生产者对“马氏体级别”这一概念一直是有争议的。
争议的焦点集中在马氏体级别的实质概念,马氏体级别超差或合格的依据以及它对产品性能和质量的影响。
在实际生产中,除渗碳淬火工艺外,影响马氏体级别的还有哪些主要因素,如何防止马氏体级别超差,试样的马氏体级别超差后,如何处理等,也常常使人们感到困惑。
本文通过一些试验例证和检验结果,对这些问题进行分析和讨论,并对该标准中将马氏体级别作为一项独立的质量指标的必要性提出质疑。
1渗碳试块和工件的金相检验实例1.1试验工艺表1列举了实际生产中经不同炉次渗碳的试块和工件的金相检验结果。
工件和试块的材料均为20CrMnTi钢。
试验过程如下:①工件与试块同炉,930℃×(6~8)h渗碳,降温至840℃淬油,180℃×2.5h回火。
用金相显微镜按标准图片分别对试块的残留奥氏体和马氏体评级并检查表层奥氏体晶粒度。
将样品浸入80℃的苦味酸+少量洗涤剂混合液,于80℃浸泡腐蚀。
按YB/T5148-1993《金属平均晶粒度测定方法》评定表层奥氏体晶粒度。
②上述试验完成后,对同一试块进行冷处理(干冰+酒精,-40℃~-60℃×0.5h)。
热处理特殊外包工艺过程确认检查评价标准

记录以核实是否按委托工艺要求进行热处理作业。对最终检验记录还应进行实地抽验, 要求也被视为严重不合格,不得分。
记录当场测得的数据以确认其保存的记录是否真实、准确、可靠。
存在其他可整改问题,每项酌情扣 1~3 分。
评价准则:
1、 资质确认项目为否决项,出现严重不符合时应更换供应商。 2、 检查确认时其他项目中只允许出现一个严重不符合项,如又出现第二个严重不符合项,则也应考虑更换供应商。 3、检查后合计评分分值≥85 分确认通过;评分分值<70 分为不符合要求,应考虑更换供应商;70≤评分分值<85 分为整改单位,要求限期在 1 个月内将不合格 项目整改完成,第二次确认检查评分分值<85 分的供应商将同样视为不符合要求,应考虑更换供应商;各次检查所有开出的不符合项目均应进行有效整改。
料以证明这些机床是否符合高频、中频、工频表面 淬火的工艺应用频率要求,并查看这些淬火机床的 开机运作状态及相应功能(如自动冷却喷水等),判 断其机床是否处于良好正常运行。
2.3 热处理方法表面发黑工艺必须具备的基本设备: ⑴ 除锈池; ⑵ 去油池; ⑶ 发黑池; ⑷ 皂化池; ⑸ 发黑前后用的若干高温、常温清洗池; ⑹ 用于增加发黑光亮度效果的高温油池。 对照供应商提供的发黑工艺流程判断发黑处理
行有效控制。
第 2 页 共3页
热处理特殊外包工艺过程确认检查评价标准
热处理工艺过程(常规热处理:调质、淬火、渗碳、表面发黑等)
项目分类
检查内容和方法
评分标准
满分分值
4 确认供应商
4.1 检测设施确认:
的检测 能力满
⑴ 是否具备基本的硬度测试仪器;
所有检查内容符合要求,给予满分。
足工艺 过程要 求
⑵ 加热炉自动温控记录仪; ⑶ 人工操控的仪器(如测温、金相、化学分析等)。 ⑷ 各检测仪器设备是否检定合格有效并有相应检定证明。
金相组织检验标准与质量判定
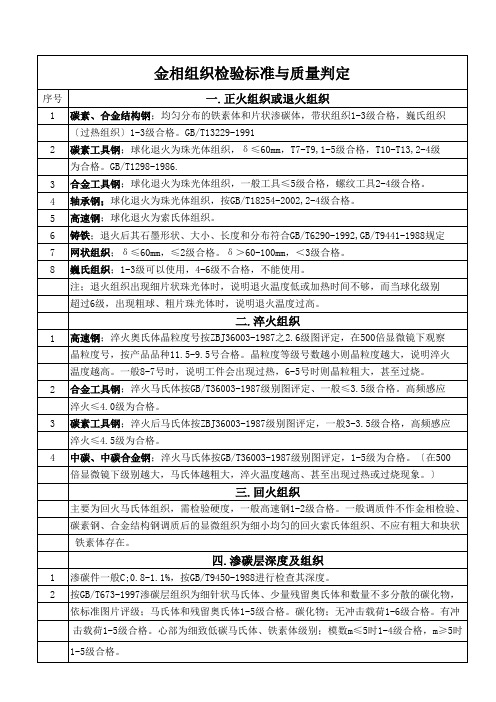
淬火≤4.5级为合格。
4 中碳、中碳合金钢;淬火马氏体按GB/T36003-1987级别图评定,1-5级为合格。〔在500 倍显微镜下级别越大,马氏体越粗大,淬火温度越高、甚至出现过热或过烧现象。〕
三.回火组织
主要为回火马氏体组织,需检验硬度,一般高速钢1-2级合格。一般调质件不作金相检验、
碳素钢、合金结构钢调质后的显微组织为细小均匀的回火索氏体组织、不应有粗大和块状
3 合金工具钢;球化退火为珠光体组织,一般工具≤5级合格,螺纹工具2-4级合格。 4 轴承钢;球化退火为珠光体组织,按GB/T18254-2002,2-4级合格。 5 高速钢;球化退火为索氏体组织。 6 铸铁;退火后其石墨形状、大小、长度和分布符合GB/T6290-1992,GB/T9441-1988规定
1-5级合格。
五.感应加热淬火淬硬层及组织
淬硬层金相组织检验在400倍显微镜小,在零件表面0.5mm处进行评定。按JB/T9204-1999 共分10级;1-2级过热〔粗、较粗马氏体〕,3-7级合格〔细、较细马氏体〕,8-10级加热 不足。〔微细马氏体+网络状极细珠光体+未溶铁素体〕均与标准图片对比评定。 注;HRC≥55时 3-7级合格,HRC<55时 3-9级合格。﹙JB/T9204-1999﹚
7 网状组织;δ≤60mm,≤2级合格。δ>60-100mm,<3级合格。
8 巍氏组织;1-3级可以使用,4-6级不合格,不能使用。 注;退火组织出现细片状珠光体时,说明退火温度低或加热时间不够,而当球化级别
超过6级,出现粗球、粗片珠光体时,说明退火温度过高。
二.淬火组织
1 高速钢;淬火奥氏体晶粒度号按ZBJ36003-1987之2.6级图评定,在500倍显微镜下观察
渗碳炉操作规程1

渗碳炉操作规程
1、检查提升炉盖机构动作、控制仪表是否正常,检查渗碳剂是否够用,确保线路及电器无故障。
2、检查待渗工件的外观质量,了解工件的渗碳技术要求和渗碳部位,确定防渗措施。
3、在对炉盖的操作时,一人扶着悬臂手柄(防止炉盖左右移动,撞坏氧探头),一人操作按钮,并对炉盖的行动位置进行密切关注。
(本炉所有动作设有互锁,炉盖没关好不能加热。
)
4、加热,加热前必须先开冷却水、开循环风机;根据工艺要求在仪表设置加热工艺参数并运行仪表。
开主令开关,工作指示灯亮,如果不亮可能是炉盖没有关好或线路故障。
5、在炉子整个工作过程中,要求操作员对系统密切关注,定期巡检,检查渗碳温度、碳势、渗碳剂的滴量、废气火焰颜色及长度是否符合工艺要求。
6、排出的废气应点燃,火焰颜色呈浅黄色,火焰应稳定,保持80~100mm长度;炉内压力保持恒定,一般为1960 ~ 4910Pa。
7、工艺结束后,炉温超过150℃时禁止关冷却水、关风机。
设备运行中严禁停冷却水,否则会损坏冷却水套和循环风机;冷却水出水口水温不得超过65℃,当出现任何意外事项时,请立即把总电源关闭。
8、煤油、甲醇属于易燃品,操作时请注意。
700℃以下禁止向炉内滴入甲醇,否则易发生爆炸事故。
9、如果设备长期不用请关闭总电源。
链条原材料及热处理加工的检验和评定标准
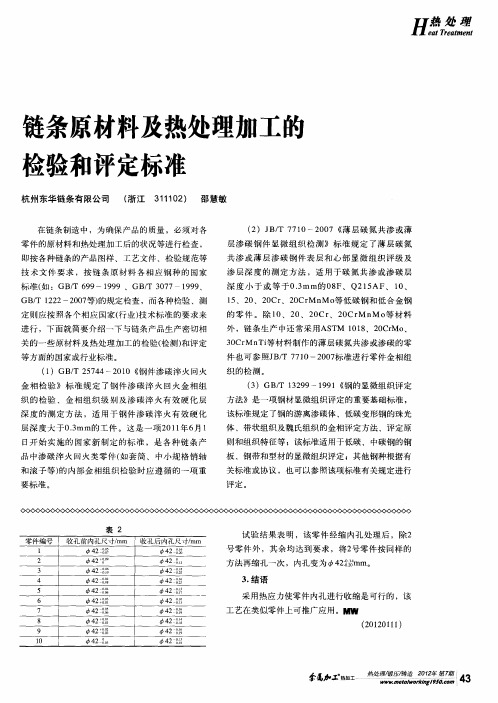
缺陷。根据 供需双方协议 ,也可用作评定其他钢类
低倍 组 织 的缺 陷 。
耐磨性能和整链抗拉强度等性能,通常链条原材料
检验规范 中都对表面脱碳 层规定了深度的要求 ,而 如何测定脱碳层深度则需遵照G / 2 —2 0 标准 BT2 4 0 8
标准适用于渗碳和碳氮共渗淬火硬化 层;并经最终 热处理 后 ,距表面3 于淬火硬化 层深度处硬度值 倍
小于 4 0 V的零 件 。不 能 满足 上 述 条件 的 钢 件 ,应 5H
T 5 7 —2 0 低、 中碳钢球化体评级》 、J / 0 4 0 7 BT 9 1 —2 0 中碳钢与 中碳 合金结构钢马 氏体等 21 08
链条原材料及热处理加工的
检验和评定标准
杭 州东华链 条有限公 司 ( 江 浙 3 1 0 ) 邵 慧敏 1 1 2
在 链 条制 造 中 ,为 确保 产 品的 质 量 ,必须 对 各 零 件 的原 材 料 和 热处 理 加 工 后 的状 况 等 进 行检 查 , 即 按 各种 链 条 的 产 品 图样 、工 艺 文件 、检 验规 范等 技 术 文 件 要 求 ,按 链 条 原 材 料 各 相 应 钢 种 的 国家 标 准 ( :G / 9 —19 、GBT 3 7 —19 、 如 BT69 99 / 0 7 9 9
( )J / 7 0 0 7 薄层碳氮 共渗或薄 2 B T 7 1 —2 0
层 渗 碳 钢 件 显 微 组 织 检 测 ) 准 规 定 了薄 层 碳 氮 )标
共渗或薄 层渗碳 钢件表 层和心部 显微组织 评级及
渗 层 深 度 的 测 定 方 法 ,适 用 于 碳 氮 共 渗 或 渗 碳 层 深 度 小 于 或 等 于 03 .mm的 0 F Q 1 AF 1 、 8 、 2 5 、 0
钢的渗碳热处理
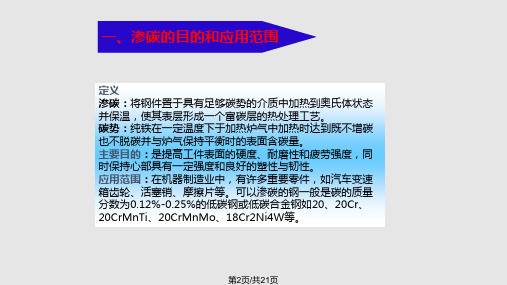
20钢 4%硝酸酒精 500× 渗碳后空冷
表层全脱碳,白亮部分为铁素体 次表层为部分脱碳层,即珠光体+少量铁素体
过渡区为珠光体+铁素体(白色网块)
第18页/共21页
20钢 4%硝酸酒精 150× 渗碳后淬火
表层脱碳,次表层也略有脱碳层,冷却不足 马氏体+屈氏体
第19页/共21页
2.回火 渗碳件淬火后尚需进行低温回火,回火温度通常为150~190℃。 3.冷处理 作用是减少或消除残余奥氏体,从而适当提高渗层硬度。由于冷处 理生产成本高,又增加了工序,目前生产中除特殊渗碳零件外,一般很少采用。
第12页/共21页
20钢 4%硝酸酒精 500× 930℃气体渗碳8小时,直接淬火 表层组织照片:马氏体+碳化物(白色颗粒)+残余奥氏体
第20页/共21页
感谢您的观看。
第21页/共21页
渗碳层厚度δ
图7 低碳钢渗碳缓冷后的显微组织 第9页/共21页
典型零件渗碳层厚度确定方法
零件种类 轴类 齿轮
薄片工件
渗碳层厚度δ(mm) (0.1~0.2)R (0.2~0.3)m (0.2~0.3)t
备注 R--半径(mm)
m--模数 t--厚度(mm)
第10页/共21页
五、渗碳后的热处理
1.淬火 淬火是为了获得马氏体组织,以得到高硬度。通常有三种方法, 即预冷直接淬火、一次加热淬火和二次加热淬火。渗碳零件淬火温度的 选择要兼顾高碳的渗层和低碳的心部两方面的要求。原则上,过共析层 的淬火温度低于Accm,而亚共析层的淬火温度高于Ac3。如果Accm> Ac3,很容易选择一个淬火温度来同时满足这两者的要求;果Accm≤Ac3, 则很难同时兼顾。在这种情况下,要根据对零件的主要技术要求、钢件 的心部能否淬透、渗碳后零件的表面含碳量和所采用的淬火方法等综合 考虑加以决定。
齿轮钢锻件等温正火质量检验规范

齿轮钢锻件等温正火质量检验规范1. 目的与范围1.1目的为正确评定渗碳齿轮钢钢制锻件及毛坯粗车零件的等温正火硬度均匀性及正火组织级别等相关质量物性,规范和完善公司对齿轮钢锻件等温正火零件的质量检验,特制定本评定规范。
1.2 范围本规定适用于公司及外协等温正火供应商。
2. 具体描述2.1等温正火质量要求2.1.1渗碳齿轮钢的等温正火硬度要求根据不同的钢材其等温正火硬度要求一般可参照下表1的范围,具体要求须按各工厂制造供应商签定的《零〔部〕件检验标准》执行,但须满足切削加工及热冷变形要求。
表1 公司常用齿轮钢零件的等温正火硬度要求2.1.2渗碳齿轮钢的等温正火金相组织要求按与锻件供应商签订的《零〔部〕件检验标准》或相关文件要求执行,如无相关文件要求则按GB/T13320执行,正火金相组织≤3级评定为合格。
2.2检验内容与方法2.2.1零件状态检查2.2.1.1公司内等温正火检验部门人员以抽查的方式,核对零件名称、材料牌号、操作记录纸的有关内容,以了解生产过程中的工艺执行情况,并作好相关的检查记录。
2.2.1.2外协等温正火检验部门人员核对零件名称、材料牌号、钢的冶炼炉号、钢材质保书及供应商对零件材料的化学成份(要求参见2.3表2),淬透性、低倍组织等复检报告和对零件的金相组织、硬度检测报告等本批产品相关内容,以了解外协正火零件的材料、金相组织及硬度情况,并做好相关的检查记录。
注:对于己批产的产品,其零件锻件的下料规格必须唯一,锻造供应商不得任意更改,但有变更必须向需方提交申请并得到批准后才可执行。
2.2.2外观检查零件正火后并经表面清理,表面应不得残留未脱落的氧化皮,不能有明显的变形弯曲及其它可见缺陷。
2.2.3硬度检验2.2.3.1正火硬度要求常用的齿轮钢参照表2.1.1表1执行,当有特殊要求的以工艺图纸规定为准。
正火硬度均匀性要求,若另有其它要求可按与锻件供应商签订的《零〔部〕件检验标准》执行。
怎样判断钢铁热处理前后的组织

钢铁中常见的金相组织区别简析一.钢铁中常见的金相组织1.奥氏体—碳与合金元素溶解在γ-fe中的固溶体,仍保持γ-fe的面心立方晶格。
晶界比较直,呈规则多边形;淬火钢中残余奥氏体分布在马氏体间的空隙处。
2.铁素体—碳与合金元素溶解在a-fe中的固溶体。
亚共析钢中的慢冷铁素体呈块状,晶界比较圆滑,当碳含量接近共析成分时,铁素体沿晶粒边界析出。
3.渗碳体—碳与铁形成的一种化合物。
在液态铁碳合金中,首先单独结晶的渗碳体(一次渗碳体)为块状,角不尖锐,共晶渗碳体呈骨骼状。
过共析钢冷却时沿acm线析出的碳化物(二次渗碳体)呈网结状,共析渗碳体呈片状。
铁碳合金冷却到ar1以下时,由铁素体中析出渗碳体(三次渗碳体),在二次渗碳体上或晶界处呈不连续薄片状。
4.珠光体—铁碳合金中共析反应所形成的铁素体与渗碳体的机械混合物。
珠光体的片间距离取决于奥氏体分解时的过冷度。
过冷度越大,所形成的珠光体片间距离越小。
在A1~650℃形成的珠光体片层较厚,在金相显微镜下放大400倍以上可分辨出平行的宽条铁素体和细条渗碳体,称为粗珠光体、片状珠光体,简称珠光体。
在650~600℃形成的珠光体用金相显微镜放大500倍,从珠光体的渗碳体上仅看到一条黑线,只有放大1000倍才能分辨的片层,称为索氏体。
在600~550℃形成的珠光体用金相显微镜放大500倍,不能分辨珠光体片层,仅看到黑色的球团状组织,只有用电子显微镜放大10000倍才能分辨的片层称为屈氏体。
5.上贝氏体—过饱和针状铁素体和渗碳体的混合物,渗碳体在铁素体针间。
过冷奥氏体在中温(约350~550℃)的相变产物,其典型形态是一束大致平行位向差为6~8o铁素体板条,并在各板条间分布着沿板条长轴方向排列的碳化物短棒或小片.典型上贝氏体呈羽毛状,晶界为对称轴,由于方位不同,羽毛可对称或不对称,铁素体羽毛可呈针状、点状、块状。
若是高碳高合金钢,看不清针状羽毛;中碳中合金钢,针状羽毛较清楚;低碳低合金钢,羽毛很清楚,针粗。
- 1、下载文档前请自行甄别文档内容的完整性,平台不提供额外的编辑、内容补充、找答案等附加服务。
- 2、"仅部分预览"的文档,不可在线预览部分如存在完整性等问题,可反馈申请退款(可完整预览的文档不适用该条件!)。
- 3、如文档侵犯您的权益,请联系客服反馈,我们会尽快为您处理(人工客服工作时间:9:00-18:30)。
渗碳件质量检查
零件渗碳前的检验:
1.根据GB699-88《优质碳素钢技术条件》和GB3077-88《合金结构钢技术条件》等标准,对零件材质进行分析,发现异常,及时处理并报告
2.零件表面不得有刀迹,尖锐角、氧化、生锈等,表面粗糙度应低于Ra3.2μm
3.零件内部应无偏析、疏松等缺陷,原材料带状组织应≤2~3级,魏氏组织≤1级,晶粒度≥5级
渗碳层总深度检验:
1.渗碳层总深度≤0.3mm的渗碳件,按GB9451-88《钢件薄表面总硬化层深度或有效硬化层深度的测定》的具体规定进行检验,常用显微组织测量法和显微硬度测量法
1)显微组织测量法是零件热处理后导致零件表层和心部显微组织的变化,测定零件总硬化层深度或有效硬化层深度
2)显微硬度测量法是零件经热处理后导致零件表面至心部“维氏显微硬度”
的变化,测定零件总硬化层深度或有效硬化层深度
2.日常生产渗碳层总深度一般用金相法检验,试样应是退火的平衡状态。
碳素钢渗碳层总深度为过共析层+共析层+1/2过渡层之间的垂直距离;合金钢渗碳层总深度为过共析层+共析层+全部过渡层(过共析层+共析层应为总渗碳层深的60%~70%)之间的垂直距离
3.渗碳工艺过程中间检验以试样为主,常用断口目测法和磨片蚀显法
断口目测法是将渗碳中间试样出炉后淬火打断观察断口,渗碳层为银白色瓷状,未渗碳部分为暗灰色纤维状,交界处的碳质量分数约为0.4%,此处至表面的垂直距离即定为渗碳层下限深度
磨片蚀显法是将渗碳中间试样(淬火或正火状态均可)断面磨平用体积分数为4%的硝酸酒精溶液浸蚀几秒钟后,出现黑圈,黑圈厚度即为粗略的渗碳层下限深度
4.同一批零件,渗碳层深度的波动,必须在图样规定的范围内同一零件渗碳层深度的波动范围是图样规定波动范围的1/2
碳深度梯度检验:
1.日常生产检验,可以用碳浓度(质量分数的)梯度和硬度的梯度检验互补,但质量仲裁应以硬度梯度(至心部硬度降)为准
2.常用剥层法,剥层检验交界处的碳的质量分数为0.4%,剥层在表面0.1mm内,碳浓度(质量分数)应达到图样要求,一般以0.8%~1.0%为合格,碳深度梯度过渡过应平缓,不得出现陡坡,浅层渗碳允许表面碳的质量分数低于0.8% 渗碳层淬火前的组织检验:
1.渗碳层淬火前的组织应是珠光体+碳化物+少量铁素体
2.渗碳层中有大块或网状碳化物,应建议两次淬火或一次正火,一次淬火,一般碳化物级别小于6级
3.渗碳后,心部出现3级以上带状组织或晶粒度小于5级时,应正火后,重新检验合格方可淬火
4.渗碳层中出现网状碳化物与游离铁素体不合格时应正火消除
渗碳件淬、回火后的硬度检验:
1.渗碳件表面硬度检验时,应去除氧化皮,脱碳层、增碳层,应以洛氏和维氏硬度计检验为准
2.硬度应符合图样或技术文件规定,一般碳钢(10、20钢)硬度在50~55HRC 或58~63HRC,合金钢硬度在58~63HRC
3.硬度终检以实物为准,但允许用随炉不同位置两个以上的试样代替实物检验。
试样材质、工艺过程与零件相同
4.硬度检验的百分比由工艺规定,但一般周期炉,每炉应抽验1~2个实物,连续炉每生产4~6盘或1~2个节拍应验实物1~2件
5.对无法用硬度计检验的凹槽尖角处,允许用和图样要求硬度相同级别的标准锉刀检验,当发生争议时应解剖实物,以在洛氏或维氏硬度计上检验为准6.同一批渗碳件,硬度波动范围应≤5HRC,同一只渗碳件表面硬度波动应≤3HRC,所有波动值都不超过图样规定的范围
7.图样或技术文件未规定检验心部硬度的一般不检验,汽车渗碳齿轮心部硬度检验位置在齿宽中部横截面上齿轮中心线与齿根圆相交处的硬度其它零件心部硬度值测在距表面3倍渗碳层上限深度处
8.汽车渗碳齿轮表面硬度检验在齿宽中部节圆附近,表面硬度检验位置应该在图样规定的位置或零件受力最大位置
9.不渗碳位置(镀铜、涂料保护部位、切削加工部位)的硬度检验,在去除涂层淬火、回火后,按图样规定检验
10.渗碳件表面出现软点、软块为不合格品
11.至心部硬度降(硬度梯度),在用硬度法测有效硬化层范围内,自表面向心部硬度降是每下降0.1mm硬度值差不大于45HV1(20CrMnMo、20CrMo,允许35~40HV1)
有效硬化层深度检验(DC):
1.有效硬化层深度检验按GB9450-88《钢件渗碳淬火有效硬化层深度的测定和校核》规定进行,有效硬化层深≤0.3mm的零件按GB9451-88《钢件薄表面总硬化层深度有效硬化层深度的测定》规定进行检验
2.有效硬化层深是从零件表面测至550HV1(极限硬度值)的垂直距离,采用的试验力9.807N(1kgf),用49.35N(5kgf)的试验力,测至515HV5(极限硬度值)。