船体建造原则工艺
船舶设计与建造技术手册
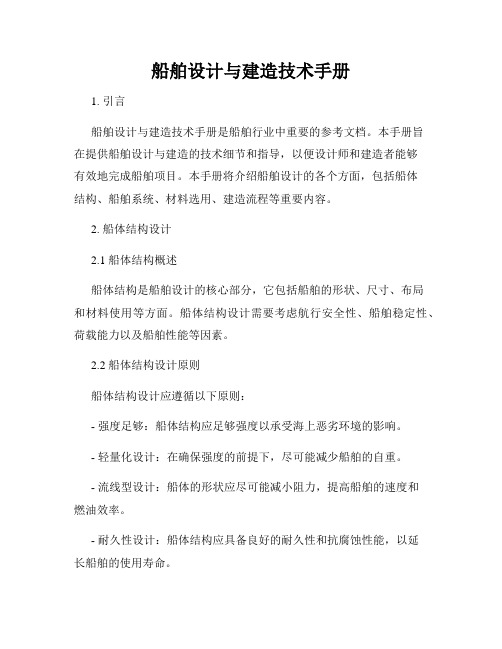
船舶设计与建造技术手册1. 引言船舶设计与建造技术手册是船舶行业中重要的参考文档。
本手册旨在提供船舶设计与建造的技术细节和指导,以便设计师和建造者能够有效地完成船舶项目。
本手册将介绍船舶设计的各个方面,包括船体结构、船舶系统、材料选用、建造流程等重要内容。
2. 船体结构设计2.1 船体结构概述船体结构是船舶设计的核心部分,它包括船舶的形状、尺寸、布局和材料使用等方面。
船体结构设计需要考虑航行安全性、船舶稳定性、荷载能力以及船舶性能等因素。
2.2 船体结构设计原则船体结构设计应遵循以下原则:- 强度足够:船体结构应足够强度以承受海上恶劣环境的影响。
- 轻量化设计:在确保强度的前提下,尽可能减少船舶的自重。
- 流线型设计:船体的形状应尽可能减小阻力,提高船舶的速度和燃油效率。
- 耐久性设计:船体结构应具备良好的耐久性和抗腐蚀性能,以延长船舶的使用寿命。
2.3 船体结构设计流程船体结构设计流程包括以下步骤:- 确定船舶的功能和使用要求。
- 进行船舶的初步设计,包括船舶的外形和尺寸。
- 进行船舶的结构计算和分析,确保船体结构的强度和稳定性。
- 设计船舶的船体细节,包括甲板、舱口、舷梯等。
3. 船舶系统设计3.1 船舶系统概述船舶系统包括船舶动力系统、操纵系统、供电系统、通信系统等。
船舶系统设计需要考虑船舶的功能需求、工作效率以及操作和维护的便捷性。
3.2 船舶动力系统设计船舶动力系统设计的关键是选择适当的主机和推进系统。
主要考虑的因素包括功率需求、船舶速度、燃料消耗以及可靠性等。
3.3 船舶操纵系统设计船舶操纵系统设计包括操纵装置、驾驶台设计以及液压系统。
船舶的操纵系统需要确保操作的准确性和船舶的操纵灵活性。
3.4 船舶供电系统设计船舶供电系统需要提供足够的电力以支持船舶设备的正常运行。
设计时需要考虑电力需求、电力分配以及安全性等方面。
4. 材料选用4.1 材料选用原则船舶的材料选用需要考虑以下原则:- 强度和韧性:材料应具备足够的强度和韧性以承受荷载和海上环境的影响。
(完整版)建造船舶船体焊接工艺
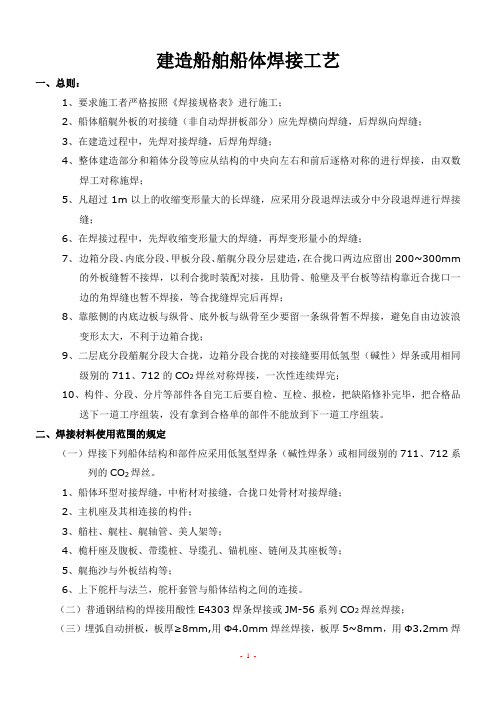
建造船舶船体焊接工艺一、总则:1、要求施工者严格按照《焊接规格表》进行施工;2、船体艏艉外板的对接缝(非自动焊拼板部分)应先焊横向焊缝,后焊纵向焊缝;3、在建造过程中,先焊对接焊缝,后焊角焊缝;4、整体建造部分和箱体分段等应从结构的中央向左右和前后逐格对称的进行焊接,由双数焊工对称施焊;5、凡超过1m以上的收缩变形量大的长焊缝,应采用分段退焊法或分中分段退焊进行焊接缝;6、在焊接过程中,先焊收缩变形量大的焊缝,再焊变形量小的焊缝;7、边箱分段、内底分段、甲板分段、艏艉分段分层建造,在合拢口两边应留出200~300mm的外板缝暂不接焊,以利合拢时装配对接,且肋骨、舱壁及平台板等结构靠近合拢口一边的角焊缝也暂不焊接,等合拢缝焊完后再焊;8、靠舷侧的内底边板与纵骨、底外板与纵骨至少要留一条纵骨暂不焊接,避免自由边波浪变形太大,不利于边箱合拢;9、二层底分段艏艉分段大合拢,边箱分段合拢的对接缝要用低氢型(碱性)焊条或用相同级别的711、712的CO2焊丝对称焊接,一次性连续焊完;10、构件、分段、分片等部件各自完工后要自检、互检、报检,把缺陷修补完毕,把合格品送下一道工序组装,没有拿到合格单的部件不能放到下一道工序组装。
二、焊接材料使用范围的规定(一)焊接下列船体结构和部件应采用低氢型焊条(碱性焊条)或相同级别的711、712系列的CO2焊丝。
1、船体环型对接焊缝,中桁材对接缝,合拢口处骨材对接焊缝;2、主机座及其相连接的构件;3、艏柱、艉柱、艉轴管、美人架等;4、桅杆座及腹板、带缆桩、导缆孔、锚机座、链闸及其座板等;5、艉拖沙与外板结构等;6、上下舵杆与法兰,舵杆套管与船体结构之间的连接。
(二)普通钢结构的焊接用酸性E4303焊条焊接或JM-56系列CO2焊丝焊接;(三)埋弧自动拼板,板厚≥8mm,用Ф4.0mm焊丝焊接,板厚5~8mm,用Ф3.2mm焊丝焊接;三、间断焊角接焊缝,局部加强焊的规定1)组合桁材、强横梁、强肋骨的腹板与面板的角焊接缝在肘板区域内应为双面连续焊;2)桁材、肋板、强横梁、强肋骨的端部加强焊长度应不小于腹板的高度,但间断的旁桁材端部可适当减小但要≥300mm;3)纵骨切断处端部的加强焊长度应不小于1个肋距;4)骨材端部削斜时,其加强焊长度不小于削斜长度,在肘板范围内应双面连续焊;5)用肘板连接的肋骨、横梁、扶强材的端部的加强焊,在肘板范围内应双面连续焊;6)各种构件的切口、切角、开孔(如流水孔、透气孔、通焊孔等)的两端应按下述长度进行包角焊;①当板厚>12mm时,包角焊长度≥75mm;②当板厚≤12mm时,包角焊长度≥50mm;7)各种构件对接接头的两侧应有一段对称的角焊缝其长度不小于75mm;四、其他的规定:1)锚机座、链闸、系缆桩底座、桅杆底座等受力部位的甲板与横梁、纵骨等是间断焊缝的应改为双面连续角缝。
船舶修造工艺
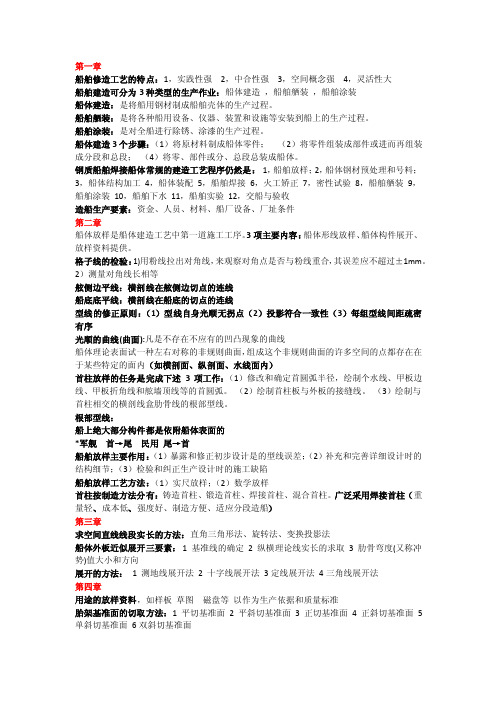
第一章船舶修造工艺的特点:1,实践性强2,中合性强3,空间概念强4,灵活性大船舶建造可分为3种类型的生产作业:船体建造,船舶舾装,船舶涂装船体建造:是将船用钢材制成船舶壳体的生产过程。
船舶舾装:是将各种船用设备、仪器、装置和设施等安装到船上的生产过程。
船舶涂装:是对全船进行除锈、涂漆的生产过程。
船体建造3个步骤:(1)将原材料制成船体零件;(2)将零件组装成部件或进而再组装成分段和总段;(4)将零、部件或分、总段总装成船体。
钢质船舶焊接船体常规的建造工艺程序仍然是:1,船舶放样;2,船体钢材预处理和号料;3,船体结构加工4,船体装配5,船舶焊接6,火工矫正7,密性试验8,船舶舾装9,船舶涂装10,船舶下水11,船舶实验12,交船与验收造船生产要素:资金、人员、材料、船厂设备、厂址条件第二章船体放样是船体建造工艺中第一道施工工序。
3项主要内容:船体形线放样、船体构件展开、放样资料提供。
格子线的检验:1)用粉线拉出对角线,来观察对角点是否与粉线重合,其误差应不超过±1mm。
2)测量对角线长相等舷侧边平线:横剖线在舷侧边切点的连线船底底平线:横剖线在船底的切点的连线型线的修正原则:(1)型线自身光顺无拐点(2)投影符合一致性(3)每组型线间距疏密有序光顺的曲线(曲面):凡是不存在不应有的凹凸现象的曲线船体理论表面试一种左右对称的非规则曲面,组成这个非规则曲面的许多空间的点都存在在于某些特定的面内(如横剖面、纵剖面、水线面内)首柱放样的任务是完成下述3项工作:(1)修改和确定首圆弧半径,绘制个水线、甲板边线、甲板折角线和舷墙顶线等的首圆弧。
(2)绘制首柱板与外板的接缝线。
(3)绘制与首柱相交的横剖线盒肋骨线的根部型线。
根部型线:船上绝大部分构件都是依附船体表面的*军舰首→尾民用尾→首船舶放样主要作用:(1)暴露和修正初步设计是的型线误差;(2)补充和完善详细设计时的结构细节;(3)检验和纠正生产设计时的施工缺陷船舶放样工艺方法:(1)实尺放样;(2)数学放样首柱按制造方法分有:铸造首柱、锻造首柱、焊接首柱、混合首柱。
船舶建造施工工艺
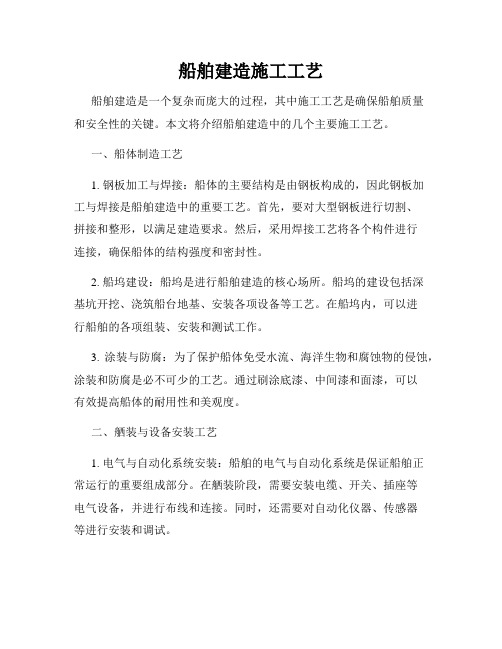
船舶建造施工工艺船舶建造是一个复杂而庞大的过程,其中施工工艺是确保船舶质量和安全性的关键。
本文将介绍船舶建造中的几个主要施工工艺。
一、船体制造工艺1. 钢板加工与焊接:船体的主要结构是由钢板构成的,因此钢板加工与焊接是船舶建造中的重要工艺。
首先,要对大型钢板进行切割、拼接和整形,以满足建造要求。
然后,采用焊接工艺将各个构件进行连接,确保船体的结构强度和密封性。
2. 船坞建设:船坞是进行船舶建造的核心场所。
船坞的建设包括深基坑开挖、浇筑船台地基、安装各项设备等工艺。
在船坞内,可以进行船舶的各项组装、安装和测试工作。
3. 涂装与防腐:为了保护船体免受水流、海洋生物和腐蚀物的侵蚀,涂装和防腐是必不可少的工艺。
通过刷涂底漆、中间漆和面漆,可以有效提高船体的耐用性和美观度。
二、舾装与设备安装工艺1. 电气与自动化系统安装:船舶的电气与自动化系统是保证船舶正常运行的重要组成部分。
在舾装阶段,需要安装电缆、开关、插座等电气设备,并进行布线和连接。
同时,还需要对自动化仪器、传感器等进行安装和调试。
2. 管道与通风系统安装:船舶的管道和通风系统包括给水管道、排水管道、燃油管道、空调通风系统等。
这些系统的安装需要严格按照设计要求进行,确保系统的正常运行和船舶内部环境的适宜性。
3. 船舶设备安装:船舶上涉及到各种设备,如发动机、推进器、锚具、舵机等。
在设备安装过程中,需要考虑设备的定位、安装和连接方式,确保其功能正常且与船舶其他系统协调配合。
三、舾装与内部装饰工艺1. 船舱隔舱板安装:船舶内部的船舱需要安装隔舱板,以便划分出不同的区域。
隔舱板可以采用钢板、玻璃钢板和木质板材等材料,通过螺栓连接或焊接固定。
2. 内饰装饰工艺:为了提高船舶的舒适度和美观度,内部装饰工艺至关重要。
这包括墙壁、天花板、地板、家具等的安装和装饰处理,同时还需考虑船舶的防火、防水和隔音要求。
四、试航与交付工艺1. 试航准备:在船舶建造完成后,需要进行试航前的准备工作。
1.船体整体建造施工工艺

船体整体建造施工工艺A、船体建造程序一、准备工作:1、清理打扫水泥船台;2、船台中心部位涂带状红漆;3、用激光经纬仪在红漆带上打(画)出中心线并作为永久标记;4、同时测量并计算出该船台实际倾斜度。
二、排墩1、在中心线位置排放中心墩;2、确定墩位前后倾斜度(一般不超过);3、墩距不超过2m;4、确定艏艉中心线,做上记号及标杆,以便以后测量船的直线度,测定轴中心的正确度,即舵筒中心的正确度用;5、做好中心各墩的高度。
三、样台及放样样台可用角铁上铺铁板,也可直接铺放在平整地面上,拼好并到好油漆,按型值放样,放样必须准确,否则装配合会有难度。
四、下料在船台墩排好,材料进场后,内底板以下构件及扶强材开始下料,如实肋板、水密补板、边纵桁、舭肘桁等,下料样板尺寸要准,划线明确准确,切割力求光顺、平整、无毛刺,较长平直部位,尽量用半自动机切割,并归堆待用。
做好记录。
五、上K桁板在中心墩排好,测量倾斜度后开始上K桁板,船中先上向首、尾铺开,在上K珩板时,板的对接缝不要在墩子上,K桁板对接缝采用刨边机或半自动切割开坡口后焊前打磨,并要用507焊条。
也要注意对接外板缝不能在舱壁或肋部位,最佳位置在距舱壁或肋骨100—150mm以内。
在装K桁板同时,着手下双层底内的构件,如实肋板、纵桁材,节点肘板,支撑,衬板等。
在装K桁板同时,未装肋板之前,把船肿两边底板A、B、C行板,预先在船台到位,并纵向拼好板缝用自动焊焊好(横向不要焊),此时拍片检查施焊情况。
拼板时焊缝两端安装好引、熄弧极。
六、xx,划K板上的中纵桁安装线K板安装完成后,可上中纵桁,中纵桁下料后,四边坡口,打磨(自动割刀开坡口),用507拼装,与K板必须垂直并固定。
在上主龙筋前除划好主龙筋安装线外,还需划好肋位线,在划肋位线时,一般每道肋位放大1mm~1.5mm,防止焊接收缩面造成船总长缩短。
上中纵桁,按K桁板上的肋距线划肋位线垂直线,K桁斑上肋位线与主龙筋肋位线都是从船中向艏艉进行。
船体分装配造工艺
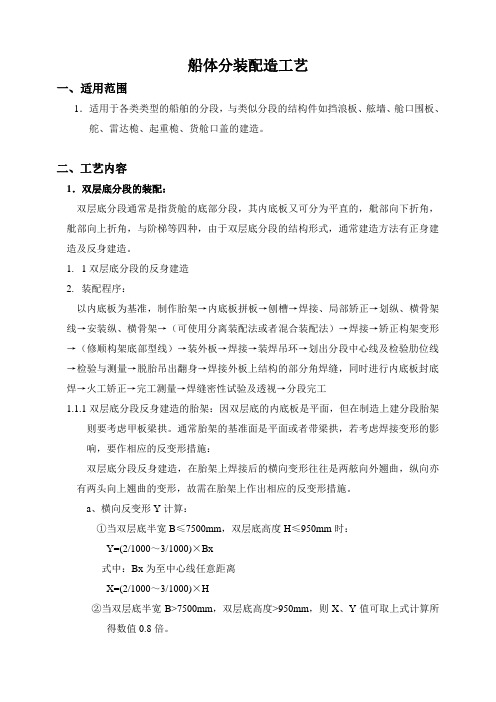
船体分装配造工艺一、适用范围1.适用于各类类型的船舶的分段,与类似分段的结构件如挡浪板、舷墙、舱口围板、舵、雷达桅、起重桅、货舱口盖的建造。
二、工艺内容1.双层底分段的装配:双层底分段通常是指货舱的底部分段,其内底板又可分为平直的,舭部向下折角,舭部向上折角,与阶梯等四种,由于双层底分段的结构形式,通常建造方法有正身建造及反身建造。
1.1双层底分段的反身建造2.装配程序:以内底板为基准,制作胎架→内底板拼板→刨槽→焊接、局部矫正→划纵、横骨架线→安装纵、横骨架→(可使用分离装配法或者混合装配法)→焊接→矫正构架变形→(修顺构架底部型线)→装外板→焊接→装焊吊环→划出分段中心线及检验肋位线→检验与测量→脱胎吊出翻身→焊接外板上结构的部分角焊缝,同时进行内底板封底焊→火工矫正→完工测量→焊缝密性试验及透视→分段完工1.1.1双层底分段反身建造的胎架:因双层底的内底板是平面,但在制造上建分段胎架则要考虑甲板梁拱。
通常胎架的基准面是平面或者带梁拱,若考虑焊接变形的影响,要作相应的反变形措施:双层底分段反身建造,在胎架上焊接后的横向变形往往是两舷向外翘曲,纵向亦有两头向上翘曲的变形,故需在胎架上作出相应的反变形措施。
a、横向反变形Y计算:①当双层底半宽B≤7500mm,双层底高度H≤950mm时:Y=(2/1000~3/1000)×Bx式中:Bx为至中心线任意距离X=(2/1000~3/1000)×H②当双层底半宽B>7500mm,双层底高度>950mm,则X、Y值可取上式计算所得数值0.8倍。
b、纵向反变形计算:①当分段长度L≤6m可不放反变形。
②当分段长度L=6~12m时,则Y=(2/1000)×Lx式中:Lx为至1/2L处的任意距离,Y为分段胎架放反变形值③当分段长度L>12m时,则Y=(1.5/1000)×Lx假如胎架上不作反变形措施,则要求在分段制造中使用加强固定措施,把内底的周围与中部搭焊牢固。
散货船驳船船体建造原则工艺

散货船驳船船体建造原则工艺1 目的为了确保各项目建造质量,指导各项目的船体建造和施工,特制定本通用工艺。
2 适用范围本原则工艺规定了本船船体建造的工艺要求及过程,适用于公司内所有船舶产品的建造过程。
3 引用文件相关造船质量标准。
4 材料用于船体建造的钢材是要经过船级社认可的标准品质的普通钢和高强度钢,所有钢料包括铸钢件和锻钢件都要在质量上符合船级社的要求。
普通钢和高强度钢用于主船体的建造,高强度钢和普通钢又可清楚地识别。
没有经过船级社认定的钢材要符合船舶行业标准和建造方的标准。
所有船体构件的尺寸都要基于结构吃水进行计算,并得到船级社的认可。
船级社没有明确要求的构件,其尺寸要符合建造方的标准。
5 船体建造(通用工艺)5.1 钢材表面预处理本船满足PSPC规定,预处理及涂装要求必须符合本船涂装原则工艺;本船所有板材及型材均应进行钢材表面预处理,钢材经预处理后,材料的牌号、钢号及炉批号等应及时跟踪标注。
5.2 放样下料5.2.1 放样间地板应保持平整,其局部不平度,以3米平直尺在任何方向检查,不得超过5mm。
线条宽度不大于0.1mm~0.12mm,线条应光顺连续,粗细均匀,不应有间断和不清楚的地方;5.2.2 船体型线放样时,对型线图中型值的修改,一般不要超过型线图面比例;5.2.3 样板形状准确,边缘与零件展开面的曲线轮廓相符合,其结构牢固,防止变形,制作好的样板应根据其用途不同划上必要的线条与标记,如角尺线、检验线、外板或甲板接缝线、船体中心线、水平检验线、胎架中心线、所属产品名称及图号、零件名称、安装位置、材料规格、号料数量以及加工符号和余量数值等;5.2.4 样条和样杆截面均匀,边缘平直,变形小,各种标记清楚正确;5.2.5 船体理论线见《理论线图》及各分段结构图;5.2.6 下料前,应清除钢材表面的铁锈、油污、检查表面有无缺陷,边缘有无裂缝、分层,如发现钢板表面有大量麻点、氧化铁压入物等表面缺陷时,应及时与检验部门联系,并按《中国造船质量标准》(2005 版)有关规定进行处理,应做好拓印存档工作;5.2.7 零件号料应用记号笔,不得使用油漆及硬质号料工具;5.2.8 严禁不必要的随意切割,切割后产生的缺陷应自行修补完整,不计工时。
船舶建造安全规范

船舶建造安全规范船舶作为水上交通工具的重要组成部分,严格遵守建造安全规范是确保航行安全的关键。
船舶建造安全规范包括设计、结构、装备、施工等多个方面。
以下将以此为主线,分述各项规范的重要内容。
一、设计规范1. 结构设计:船舶结构设计要根据不同类型、尺寸和用途的船舶,依据相关标准和规定进行合理设计。
确保船舶结构的强度、稳定性和抗疲劳性,同时考虑到航行环境和操作条件的变化。
2. 电气设计:船舶电气系统的设计应遵循国际和国内相关规范,确保正常运行和安全性。
设计中应加强对电路保护、防火措施、接地系统以及电气设备的可靠性等方面的考虑。
3. 系统设计:包括航行、通信、供能和管道系统等,要求设计合理、可靠、安全,并与其他系统相匹配。
同时要考虑到系统的易用性、维护性和升级扩展性。
二、结构规范1. 材料选择:船舶材料应符合国际和国内相关标准,具备必要的强度、韧性、防腐性和耐久性。
同时要对材料的质量进行严格控制,确保船体的结构强度和船舶的寿命。
2. 焊接工艺:船舶结构中的焊接应按照相关规范,采用合适的焊接工艺。
焊接质量要求高,要通过严格检测和监控确保焊接接头的可靠性和密封性。
3. 强度计算与验证:船舶结构的强度计算要符合相关规范,并进行合理的验证。
要考虑船舶在各种条件下的受力情况,确保船舶在正常使用和极端情况下的安全性。
三、装备规范1. 航行装备:包括定位装备、导航系统、通信设备和自动化控制系统等,要按照国际和国内的标准和规范进行选配和安装。
装备的性能、可靠性和适用性要符合船舶的实际需求。
2. 安全装备:船舶安全装备包括救生艇、救生衣、救生圈和消防设备等,要符合国际和国内的标准和规范。
安全装备的选型、数量和布置要根据船舶的类型和乘员数量合理确定。
3. 管道装备:船舶的管道装备包括供水、排水、燃油和气体管道等,要按照相关标准和规范设计和安装。
管道的材料、连接方式、泄漏预防和紧急关闭等方面要符合要求。
四、施工规范1. 施工质量控制:船舶建造过程中要严格遵守相关工艺规程和质量标准,加强质量控制,确保船舶结构、装备和系统的正确安装和完好无损。
- 1、下载文档前请自行甄别文档内容的完整性,平台不提供额外的编辑、内容补充、找答案等附加服务。
- 2、"仅部分预览"的文档,不可在线预览部分如存在完整性等问题,可反馈申请退款(可完整预览的文档不适用该条件!)。
- 3、如文档侵犯您的权益,请联系客服反馈,我们会尽快为您处理(人工客服工作时间:9:00-18:30)。
1船体建造原则工艺
1概述
1.1船舶用途及航区
本船为广州出入境边防检查总站执勤执法交通艇,主要担负珠江水域及沿岸黄埔港至珠江口三门岛锚地监管水域常规巡逻、应急处置、联合执法、交通运输等边检执勤、交通任务。
航区为中国沿海航区及内河A级航区。
L2法规、规范
CCS《海上高速船入级与建造规范》(2015)及修改通报(2017);
CMSA《公务船技术规则》(2020);
CMSA《公务船检验规则》(2020);
CCS《材料与焊接规范》(2021)
中国造船工业标准(CB)、中国造船质量标准(CSQC)及其他标准的最新要求。
1.3主要尺度及参数
总长45.50m
设计水线长43.40m
垂线间长型宽42.80m 7.60m
型深 3.50m
设计吃水
最大航速2船体建造方案1.85m 25.5kn
2.1本船船体采用分段塔式建造,
2.2分段划分
船台合拢下水的建造方案。
本船将主船体划为4个立体分段,分别为101、102、103、104分段;
一层上层建筑(上甲板及下围壁)为2个立体分段,分别为201、202立体分段; 二层上层建筑(驾驶甲板及下围壁)为1个立体分段,为301分段;
2.3分段建造简介
胎架采取反造甲板胎架(模板每2肋位设置)
主船体分段以主甲板为基准面进行反造;
上层建筑分段分别以上甲板、驾驶甲板为基准面进行反造。
各分段采取各构件按铺板贴胎、板缝焊接、划线、结构安装、验收、焊接的工艺顺序进行制作
全船板材采用数控切割下料,型材采用手工下料。
2.4分段合拢
根据本船分段划分特点,本船将按下列合拢顺序进行本船的船台合拢:
3船体下料加工工艺程序
3.1船体下料工艺准备
3.1.1 根据光顺过的型线对图形文件进行校对和修订。
3.1.2 下料指导文件:
①放样及样板制作、下料图表及技术表格绘制;
②甲板号料拼板、外板号料拼板、舱壁号料拼板;
③纵横骨架型材下料、加工线、焊缝线绘制;
④各种肘板下料、各种艇装件下料;
⑤分段及结构中心线、安装线、对合线、检验线、地面线等绘制。
3.1.3 制作电脑切割文件,尽量集中相同板厚的材料规格一起下料,保证材料的利用率。
3.1.4 为了保证肋骨框架的型线焊接后的准确度,肋板对接处,放焊接收缩余量。
3.2材料准备:
①检查记录材料编号、炉号和检验证书号等等。
②检查板材、型材外表有无伤痕和缺陷。
③检查运输设备对材料的保护措施,防止运输过程的损坏。
3.3下料工艺
3.3.1 对于构件型线为曲线的,采用水床等离子数控下料。
较大较长的构件,可分为尽量少的数段拼接。
3.3.2 对于型线平直,以及长度超过水床切割尺寸具有对称性的T型构件可采用手工下料。
3.3.3 大型组合型材的组装画线,采用成对组装工艺:在两块型材复板之间,根据材料余量的多少相应留下少量空间,当组合型构件装焊完成,可预先在空间区域进行校正焊接,达到控制变形的目的。
4焊接工艺
1)经过焊接试验、评定、船检(CCS)送审及认可的焊接工艺,方可在本船上实施。
2)《焊接规格表》及《焊接原则工艺》、《船舶建造精度标准》作为焊接作业指导书,必须严格按照相关进行焊接作业及检验。
5质量要求
5.1 号料划线按《船舶建造精度标准》要求进行作业及检验。
5.2 部件切割按《船舶建造精度标准》要求进行作业及检验。
5.3 余量配置
①构件对接板缝处留焊接余量。
②平面分段合拢口拼板余量:单边30~50mm0
③曲面板加工余量根据详细而具体的要求来确定。
④需要加工的骨材,预留加工余量,待加工完成对线割除。
5.4 本文没有规定的质量、精度要求,按具体图纸要求部件、分段组装工艺
6部件、分段组装工艺要求
6.1曲面板加工
①所有曲面结构应全部采用冷加工方式,即压力机和相应的模具进行,避免采用水火加工;
②根据型线曲度的大小,仔细绘制加工线;
③注意掌握每次进刀的层次和深度,尽量保证曲面的光顺,无明显压痕。
6.2组合型材组装、焊接要点
A组装要点
焊接线应满足“焊接规格表”要求;
结构安装对线应满足“对正”要求;
对于结构焊接,除了注意在满足设计要求的基础上,尽量保持较小的焊喉,在焊接秩序上,可采用跳焊法对控制变形比较有利。
B焊接要点
根据构件的实际情况采用下列方法控制变形:
①尽量采用对称焊接的方法,如对称型材料的下料中间不切断而组装形成工字梁后,利用工字梁焊缝布置的对称性进行焊接,有效的控制构件的变形,减少结构校正的工作量。
②采用T型材面板背靠背点焊固定的方法形成对称焊接,减少变形。
用钢质工装,对变形进行约束控制,减少变形。
6.3平面板架结构安装、焊接工艺要点
A焊接线应满足“焊接规格表”要求。
B结构安装对线应满足“对正”要求。
C甲板平面分段施工遵守以下原则。
纵骨架式的甲板结构,安装画线每档纵骨间距放焊缝收缩余量。
②在纵骨安装焊接完成后,才能进行横梁的安装、焊接。
当横梁之间有相当强度的纵向构件(如间断纵舱壁)时,要注意纵向构件与横梁之间的
点焊是在横梁焊接完成后进行。
③在进行上述点焊时,要注意对整个分段的平整度进行测量调整,满足要求后利用纵向构件进行锁定。
④点焊完成后,余下的焊缝要严格按照对称的原则焊接,减少焊接变形对分段平整度的影响。
6.4舱壁平面板架施工原则
・舱壁扶强材间距应放焊缝收缩余量。
舱壁水平桁安装焊接,应在扶强材焊接完成、对局部变形进行校正之后进行。
•舱壁在装配焊接校正完成之后,应根据实际需要进行横向码强。
码强的意义在于控制船台上船体结构的焊接对舱壁的影响。
6.5肋骨框架的拼装、焊接
①肋框复板在拼框平台上焊接成型后,才能进行面板安装。
②复板对接采用先点焊,再采用U型坡口的方式进行焊接,且对铳制U型坡口的刀锯要进行专门的磨制。
③面板加工要求与型线尽量吻合,减少结构安装内应力。
④肋框拼制完成焊接前,要利用工装材料进行加强。
同时对加强的位置要兼顾到以后船台脚手架施工的方便。
7船台合拢原则工艺
7.1船台墩位布置
①船台墩位布置之前要求确认船台地面是否符合要求,并做出墩位固定措施。
②船台墩位置的布置要跟据船台布墩图进行定位施工。
③墩木在使用之前必须对表面进行检查,以防有钉子等其他硬物划伤船体。
④墩木打紧时,上下位置要均匀错开,做到安全、稳定。
7.2分段吊装定位
在船台车间基线标杆上做好整船基线位置标记,以此作为构件高度定位依据;以船台船中地面线为船中定位依据。
分段吊装前要做好起吊、合拢方案,保证吊具、工装满足要求。
分段定位精度必须达到《船舶建造精度标准》中对船台安装精度的要求。
分段定位完毕,做好固定措施,要保证分段不发生偏移。
8船台上层建筑吊装。
・根据进度情况,可按中间向两边对称施工原则进行焊接施工。
・按质量要求标准进行控制。
9工装准备
关键及重要的工装准备,保证装配、焊接施工质量达到技术标准。
主要准备工装:组装及焊接固定码材、主机基座分段胎架、轴系拉线工装合拢安装调整工装、船台墩位及垫木。