疲劳试验-大纲
运动疲劳判断实验报告

一、实验目的本实验旨在通过一系列生理和生化指标的检测,结合主观感觉,对受试者在运动过程中产生的疲劳进行判断,并分析不同运动强度和持续时间对疲劳程度的影响。
二、实验材料与方法1. 实验对象选取20名身体健康、无慢性疾病、年龄在20-30岁之间的志愿者作为受试者。
2. 实验分组将受试者随机分为四组,每组5人,分别进行不同强度的运动:低强度组(50%最大心率)、中强度组(70%最大心率)、高强度组(90%最大心率)和对照组(不进行运动)。
3. 实验方法(1)生理指标检测:- 肌肉力量:通过背肌力和握力测试,分别在运动前后进行,计算数值差。
- 呼吸肌耐力:连续测量5次肺活量,每次间歇30秒,观察肺活量变化。
- 反应时:通过按键反应测试,记录运动前后反应时间的变化。
- 膝跳反射阈值:测量运动前后膝跳反射阈值的变化。
- 血压体位反射:受试者静息5分钟后测血压,随后仰卧3分钟,再被动坐起,每30秒测一次血压,观察血压恢复情况。
- 肌电图:观察运动前后肌电图的变化。
(2)生化指标检测:- 血液乳酸浓度:运动前后采集血液样本,检测乳酸浓度变化。
- 尿蛋白:运动前后采集尿液样本,检测尿蛋白含量变化。
(3)主观感觉评价:- 运动后疲劳程度:通过RPE(Rate of Perceived Exertion)量表对运动后疲劳程度进行评估。
4. 数据分析采用SPSS软件对实验数据进行统计分析,比较不同运动强度和持续时间下,生理、生化指标和主观感觉评价的差异。
三、实验结果1. 生理指标- 肌肉力量:高强度组运动后背肌力和握力显著下降,低、中强度组无显著变化。
- 呼吸肌耐力:高强度组肺活量逐次下降,低、中强度组无显著变化。
- 反应时:高强度组反应时间延长,低、中强度组无显著变化。
- 膝跳反射阈值:高强度组阈值升高,低、中强度组无显著变化。
- 血压体位反射:高强度组血压恢复不完全,低、中强度组血压恢复良好。
- 肌电图:高强度组出现肌电图异常,低、中强度组无显著变化。
关节轴承疲劳试验大纲
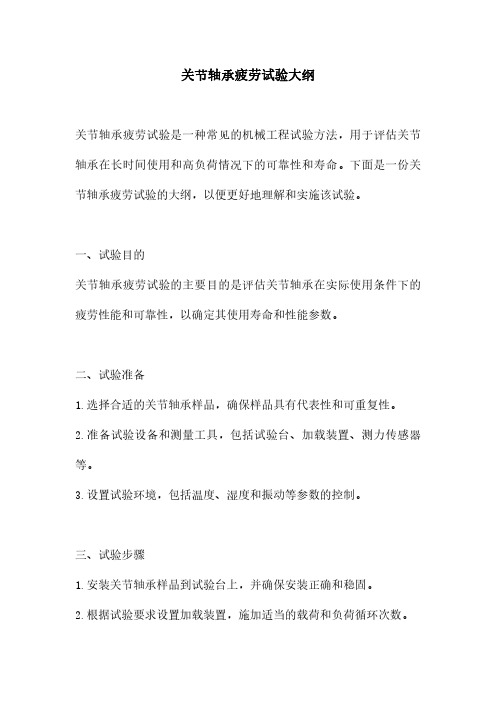
关节轴承疲劳试验大纲关节轴承疲劳试验是一种常见的机械工程试验方法,用于评估关节轴承在长时间使用和高负荷情况下的可靠性和寿命。
下面是一份关节轴承疲劳试验的大纲,以便更好地理解和实施该试验。
一、试验目的关节轴承疲劳试验的主要目的是评估关节轴承在实际使用条件下的疲劳性能和可靠性,以确定其使用寿命和性能参数。
二、试验准备1.选择合适的关节轴承样品,确保样品具有代表性和可重复性。
2.准备试验设备和测量工具,包括试验台、加载装置、测力传感器等。
3.设置试验环境,包括温度、湿度和振动等参数的控制。
三、试验步骤1.安装关节轴承样品到试验台上,并确保安装正确和稳固。
2.根据试验要求设置加载装置,施加适当的载荷和负荷循环次数。
3.记录关节轴承在试验过程中的振动、温度和位移等数据。
4.在试验过程中定期检查关节轴承的磨损情况,并记录下来。
5.当关节轴承出现破损或达到试验要求的循环次数时,停止试验并记录试验结果。
四、试验数据分析1.根据试验数据计算关节轴承的平均疲劳寿命和标准差。
2.根据试验结果评估关节轴承的可靠性和性能参数,如疲劳极限、可靠度等。
3.比较不同关节轴承样品的试验结果,找出其差异和原因。
五、试验报告根据试验数据和分析结果撰写试验报告,报告中应包括试验目的、试验准备、试验步骤、试验数据和分析、结论及建议等内容,并确保报告结构清晰、语言准确。
六、试验安全在进行关节轴承疲劳试验时,应严格遵守相关安全规定和操作规程,确保试验人员的人身安全和设备安全。
以上是关节轴承疲劳试验的大纲,该试验方法在评估机械设备可靠性和寿命方面具有重要作用。
实施该试验需要严格按照大纲要求进行,并根据试验结果做出相应的评估和改进措施,以提高关节轴承的性能和可靠性。
关节轴承疲劳试验大纲

关节轴承疲劳试验大纲
摘要:
1.关节轴承简介
2.疲劳试验的背景和重要性
3.关节轴承疲劳试验的目的和方法
4.关节轴承疲劳试验的结果和分析
5.关节轴承疲劳试验的应用和展望
正文:
1.关节轴承简介
关节轴承是一种广泛应用于各种机械设备的关键部件,它能够承受较大的径向和轴向载荷,同时具有较高的旋转精度和稳定性。
关节轴承的主要失效模式包括磨损、疲劳、腐蚀等,其中疲劳失效是最为常见的一种。
2.疲劳试验的背景和重要性
疲劳试验是一种模拟关节轴承在实际工况下承受循环载荷的过程,通过测试关节轴承在特定条件下的寿命,以此来评估其抗疲劳性能。
疲劳试验在关节轴承的研发、生产和应用中具有重要意义,能够为关节轴承的设计、选型和使用提供重要的参考依据。
3.关节轴承疲劳试验的目的和方法
关节轴承疲劳试验的主要目的是评估关节轴承在实际工况下的抗疲劳性能,以此来提高关节轴承的使用寿命和可靠性。
关节轴承疲劳试验通常采用专用的疲劳试验机进行,通过模拟关节轴承在实际工况下的载荷和转速,测试其在一定循环次数下的寿命。
4.关节轴承疲劳试验的结果和分析
关节轴承疲劳试验的结果通常包括疲劳寿命、疲劳强度和疲劳裂纹等指标。
通过对这些指标的分析,可以评估关节轴承的抗疲劳性能,并为其设计和选型提供参考。
5.关节轴承疲劳试验的应用和展望
关节轴承疲劳试验在关节轴承的研发、生产和应用中具有重要作用,能够为关节轴承的设计、选型和使用提供重要的参考依据。
飞机疲劳试验大纲

飞机疲劳试验大纲一、试验目的本次试验旨在评估飞机在长时间运行和特殊环境下的疲劳性能,以验证其结构的可靠性和耐久性。
二、试验对象本试验选择一架类型机进行测试,包括机身、机翼、动力系统、附件等相关部件。
三、试验条件1.试验持续时间:连续X小时。
2.温度和湿度:试验期间温度范围在X℃~X℃,相对湿度保持在X%~X%之间。
3.压力条件:压强维持在XPa。
4.飞行模式:采用模拟器模拟典型飞行模式。
四、试验内容1.结构疲劳试验- 选择代表性航班任务,进行多次往返飞行模拟,以重复受到载荷和震动压力,模拟实际运营环境。
- 记录并监测飞机在试验过程中发生的载荷变化和结构疲劳情况。
2.燃油系统疲劳试验- 连续对燃油系统进行模拟运行,观察系统在疲劳状态下的工作情况。
- 检测并记录系统在试验过程中可能产生的漏油、泄漏等异常情况。
3.电子设备疲劳试验- 在模拟运行过程中,对飞机内各种电子设备进行持续运行测试,以验证其在高温、低温和高湿度环境下的可靠性和耐久性。
- 记录设备在试验过程中是否产生故障、电气隔离或其他异常现象。
- 对机载设备如座椅、卫生间等进行连续使用测试,以验证其在实际运营中的耐用性。
五、试验结果评估1.通过数据分析和实验结果评估,总结飞机在试验过程中表现出的结构疲劳情况、燃油系统疲劳情况及其他关键部件的可靠性。
2.根据结果评估,提出适当的改进措施和建议,以提高飞机的可靠性和耐久性。
六、安全措施1.根据相关安全规定,制定详尽的安全操作程序,并确保试验人员严格执行。
2.在试验过程中,对可能存在的安全风险进行全面评估并采取相应措施,确保试验人员和试验设备的安全。
备注:本试验大纲仅作为参考使用,具体试验内容和条件应根据实际情况进行调整和制定,以确保试验目的的实现和试验安全的保障。
疲劳试验-大纲

金属疲劳试验一、实验目的1.了解疲劳试验的基本原理;2.掌握疲劳极限、S-N曲线的测试方法;3.观察疲劳失效现象和断口特征二、实验原理1.疲劳抗力指标的意义目前评定金属材料疲劳性能的基本方法就是通过试验测定其S-N曲线(疲劳曲线),即建立最大应力σmax或应力振幅σa与相应的断裂循环周次N之间的曲线关系。
不同金属材料的S-N曲线形状是不同的,大致可以分为两类,如图1所示。
其中一类曲线从某应力水平以下开始出现明显的水平部分,如图1(a)所示。
这表明当所加交变应力降低到这个水平数值时,试样可承受无限次应力循环而不断裂。
因此将水平部分所对应的应力称之为金属的疲劳极限,用符号σR表示(R为最小应力与最大应力之比,称为应力比)。
若试验在对称循环应力(即R=-1)下进行,则其疲劳极限以σ-1表示。
中低强度结构钢、铸铁等材料的S-N曲线属于这一类。
实验表明,黑色金属试样如经历107次循环仍未失效,则再增加循环次数一般也不会失效。
故可把107次循环下仍未失效的最大应力作为持久极限。
另一类疲劳曲线没有水平部分,其特点是随应力降低,循环周次N不断增大,但不存在无限寿命,如图1(b)所示。
在这种情况下,常根据实际需要定出一定循环周次(108或5×107…)下所对应的应力作为金属材料的“条件疲劳极限”,用符号σR(N)表示。
(a)(b)图1 金属的S-N曲线示意图(a)有明显水平部分的S-N曲线(b)无明显水平部分的S-N曲线2. S-N 曲线的测定(1) 条件疲劳极限的测定测试条件疲劳极限采用升降法,试件取13根以上。
每级应力增量取预计疲劳极限的5%以内。
第一根试件的试验应力水平略高于预计疲劳极限。
根据上根试件的试验结果,是失效还是通过(即达到循环基数不破坏)来决定下根试件应力增量是减还是增,失效则减,通过则增。
直到全部试件做完。
第一次出现相反结果(失效和通过,或通过和失效)以前的试验数据,如在以后试验数据波动范围之外,则予以舍弃;否则,作为有效数据,连同其他数据加以利用,按以下公式计算疲劳极限: ∑==n i i i N R v m 1)(1σσ式中m —有效试验总次数;n —应力水平级数;σi —第i 级应力水平;v i —第i 级应力水平下的试验次数。
疲劳试验
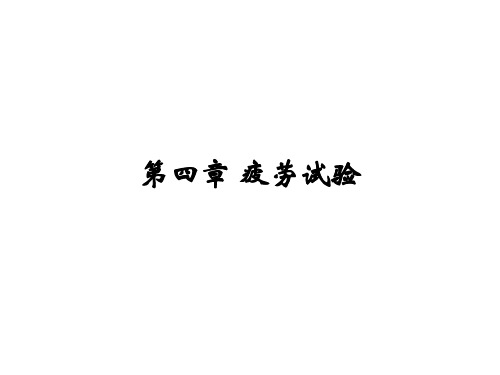
第一步 采用升降法测定条件疲劳极限, 第二步 用成组法测定σ一N曲线有限寿命段上各 点的数据, 第三步 绘制σ一N曲线。 二、不同应力状态下的疲劳极限 根据大量的实验结果,弯曲与拉压、扭转疲劳 极限之间的关系: 钢:σ-1p=0.85σ-1,铸铁σ-1p=0.65σ-1 铜及轻合金:τ-1=0.55σ-1,铸铁τ-1=0.8σ-1 σ-1>σ-1p>τ-1
(2)σmax~σm 图 y轴上的边界点为σ-1和 -σ-1,x轴则同前图。 σmax=σb ,利用不同的 应力比r来作图。若为韧性 材料σmax=σ0.2 (3)公式法 上两图中的曲线可用数学 公式表示 可以很方便利用 σb ,σ-1, σ0.2和r,求得σr。
第二节 疲劳抗力指标及其测定 一、疲劳极限的测定
一、变动载荷和循环应力
1、变动载荷 大小、方向或者大小和方向均随时间而变化。 变化分为周期性,无规则性。相对应的应力,称为循环 应力。 (P94-图5-1) 2、循环应力 (1)循环应力的特性 平均应力 σm=1/2(σmax+σmin) 应力幅 σa=1/2(σmax-σmin) 应力循环对称系数 γ=σmin/σmax (2)循环应力的种类(P95-图5-2) 对称;脉动;不对称循环应力。
第四节 低周疲劳与热疲劳
疲劳寿命为102-105次的疲劳断裂,称为低周 疲劳。
一、低周疲劳的特点
1、局部产生宏观变形,应力与应变之间呈非 线性。 总应变△εt=△εe+△εp
2、裂纹成核期短,有多个裂纹源。 3、断口呈韧窝状、轮胎花样状。 4、疲劳寿命取决于塑性应变幅。
二、金属的循环硬化与循环软化
(二)疲劳极限
1、对称疲劳极限 97 循环载荷,r=-1。 σ-1,τ-1,σ-1p(对称拉压)
金属疲劳试验方法
在足够大的交变应力作用下,于金属构件外形突变或表面刻痕或内部缺陷等部位,都可能因较大的应力集中引发微观裂纹ቤተ መጻሕፍቲ ባይዱ分散的微观裂纹经过集结沟通将形成宏观裂纹。已形成的宏观裂纹逐渐缓慢地扩展,构件横截面逐步削弱,当达到一定限度时,构件会突然断裂。金属因交变应力引起的上述失效现象,称为金属的疲劳。静载下塑性性能很好的材料,当承受交变应力时,往往在应力低于屈服极限没有明显塑性变形的情况下,突然断裂。疲劳断口(见图2-30)明显地分为两个区域:较为光滑的裂纹扩展区和较为粗糙的断裂区。裂纹形成后,交变应力使裂纹的两侧时而张开时而闭合,相互挤压反复研磨,光滑区就是这样形成的。载荷的间断和大小的变化,在光滑区留下多条裂纹前沿线。至于粗糙的断裂区,则是最后突然断裂形成的。统计数据表明,机械零件的失效,约有70%左右是疲劳引起的,而且造成的事故大多数是灾难性的。因此,通过实验研究金属材料抗疲劳的性能是有实际意义的。
圆弧形光滑小试样如图2-34所示,其最小直径为7~10mm,试样的其他外形尺寸,因疲劳试验机不同而异,没有统一规定。
六﹑实验步骤
以M= Pa和I= 代式(2-17),求得最小直径截面上的最大弯曲正应为:σ=
令K= ,则上式可改写成
P=Kσ(2-18)
K称为加载乘数,它可根据试验机的尺寸a和试样的直径dmin事先算出,并制成表格。在试样的应力σ确定后,便可计算出应施加的载荷P。载荷中包括套筒﹑砝码盘和加力架的重量G,所以,应加砝码的重量实为
单点实验法至少需8~10根试样,第一根试样的最大应力约为σ1=(0.6~0.7)σb,经N1次循环后失效。继取另一试样使其最大应力σ2=(0.40~0.45)σb,若其疲劳寿命N<107,则应降低应力再做。直至在σ2作用下,N2>107。这样,材料的持久极限σ-1在σ1与σ2之间。在σ1与σ2之间插入4~5个等差应力水平,它们分别为σ3﹑σ4﹑σ5﹑σ6,逐级递减进行实验,相应的寿命分别为N3﹑N4﹑N5﹑N6。这就可能出现两种情况:(1)与σ6相应的N6<107,持久极限在σ2与σ6之间。这时取σ7= (σ2+σ6)再试,若N7<107,且σ7-σ2小于控制精度△σ*(关于△σ*,将在下面说明),即σ7-σ2<△σ*,则持久极限为σ7与σ2的平均值,即σ-1= (σ7+σ2)。
试验六疲劳试验示范
实验六疲劳试验(示范)一、实验目的1、了解测定材料疲劳极限的方法。
2、观察疲劳破坏的现象。
二、实验设备疲劳试验机有各种类型,用来在不同受力形式下和不同条件下进行试验。
常用的是旋转弯曲疲劳试验机,有纯弯曲和悬臂弯曲两种型式。
本试验采用纯弯曲式疲劳试验机,其构造示意图如图26(A)所示。
试件4的两端被夹紧在两个空心轴1中,两空心轴与试件构成一个整体杆,支持于两个滚珠轴承3上。
电动机5通过软轴6使这个整体杆转动。
横杆8挂在滚珠轴承2上,处于静止状态。
在横杆中央的砝码盘上放置砝码9,使试样中段受纯弯曲(图26—B),最大弯曲正应力为(A)纯弯曲疲劳试验机示意图(B)试件弯矩图图26 纯弯曲式疲劳试验机三、试件本实验需用一组8~13根材料和尺寸均相同的光滑小试件,直径为d=6~lOmm,表而须磨光,无锈蚀或伤痕,圆角处要光滑过度。
四、实验原理疲劳破坏与静力破坏有本质的不同。
当交变应力小于材料的静强度极限σb时,材料就可产生疲劳裂纹或完全断裂。
即使是塑性材料,断裂时也无显著的塑性变形。
在疲劳破坏的断口上,一般呈现两个区域,即光滑区和粗粒状区。
材料断裂前所经历的循环次数称为疲劳寿命N,试件所受应力愈小,则疲劳寿命愈长。
对钢和铸铁等黑色金属,如果在某一交变应力下经受107次循环仍不破坏,则实际上可以承受无限次循环而不会发生破坏。
所以,对这些金属以试件能承107循环所对应的最大应力σ值作为疲劳极限σ-1。
maX五、实验步骤1、试件准备取8~13根试件,检查试件表面加工质量,如有锈蚀或擦伤,用细砂纸或砂布沿试件轴向抛光加以消除。
测量试件的直径。
2、装夹试件安装试件时必须很仔细,避免灰尘和杂质进入空心轴的锥孔中。
将试件牢固夹紧,使试件与试验机的转轴保持良好的同心度。
试件安装好后用手慢慢旋转试验机的转轴,用百分表在试件上测得的径向跳动量应不大于0.03mm。
然后空载运转,试件的径向跳动量应不大于0.06mm。
3、进行试验第一根试件的交变应力的最大值约取材料强度极限的60%,即σlmax=0.6而砝码重量P1二0.6σbπd3/16a。
实验六工作疲劳测定实验
人因工程实验实验六:工作疲劳测定实验刚晓名:张姓20130555号:学1301业业:工专金海哲伏指导老师:郭刘倩宇小组成员:李雨晴01日月年2016077/ 1.一、实验目的通过实验使用功率自行车作为体力作业,使被试者在不同的体力负荷下作业,测定被试作业前(前安静期)、作业中(即负荷期)和作业后(后安静期)等三个阶段的心率(呼吸循环机能的指标)变化,判断作业负担及疲劳恢复的规律。
当然在实际工作疲劳研究中,还要结合其它的检查法(生理学检查法,心理检查法等方法)来综合地判断疲劳程度。
二、实验内容实验分2个作业进行,分别进行下列测定。
第2个作业要等第1个作业停止后,操作者完全恢复到安静期水平时才能开始。
1.作业前(前安静期)的心率测定;2.作业中(即负荷)的心率测定;3.作业后(后安静期)的心率测定。
三、实验仪器心率发射机,带有MF调频的收录机,脉搏表,普通秒表,功率自行车,导电膏,医用胶布等。
四、实验原理实验时,每组选一人为被试,其余为测试和记录者,其中有一人调节接收机并负责向被试和测试者发出时间信号,每隔20秒钟发出信号一次,通知被试和测试者。
测脉搏时,每次听到信号后立即启动秒表,同时数从收音机里接收来的心率声音,数至15次时立即停表,记下该瞬间的心率值。
然后立即使表回零,等待下一次信号,以后重复7 / 2.上面的测记过程。
每次测定分三个阶段:1.作业前5分钟时间,被试安静地坐在椅子上。
2.作业中5分钟时间,被试开始按规定的速度(或按节拍器频率)蹬车。
3.作业后10分钟时间,在10分钟以内恢复到安静时的心率值,作业测定结束,若10分钟以内尚未恢复到安静期心率值可适当延长时间。
这里要注意进行作业二时也应有5分钟的作业前安静期时间。
本实验作业一加负荷30kg,作业二加负荷50kg,速度值均定为90公里/小时。
测定者从作业的安静期到作业后恢复结束要连续记录,如遗失了某瞬间的心率值,仍要继续记录以后的数值。
疲劳实验
疲劳实验
实验目的:了解疲劳破坏特征。
了解疲劳实验的方法。
(测疲劳极限?)
实验原理:在交变应力的应力循环中,最小应力和最大应力的比值
max min /σσ=r
称为循环特征或应力比。
在r 一定的情况下,如试样的最大应力为某一值时,经过N 次循环后,发生疲劳失效,则称N 为此应力下的疲劳寿命。
在同一循环特征下,最大应力越大。
则寿命越短。
最大应力与寿命的关系曲线见图(1)。
图(1)
实验方法:按照金属轴向或纯弯疲劳实验方法进行实验。
试 样:一批试样需8~13根,按国标的要求加工,从毛坯到试样制成,要
经过机械加工、热处理、尺寸测量、表面检验等一系列措施。
如进行光滑试样测试,则试样表面必须光滑(Ra>0.4)
实验设备:
1、高频疲劳实验机
频率:80~250Hz
能力:100kN
负载形式:拉压,对称循环最大±50kN
2、纯弯疲劳试验
试样受力见图(2)
图(2)
负载形式:纯弯曲
最高转速:100000rpm/min
疲劳破坏特征:
它是一种潜在的失效方式,在静载荷下无论显示脆性与否,在疲劳断裂时都不会产生明显的塑性变形,而断裂是突发的没有预兆。
构件上存在表面缺陷(缺口、沟槽),即使在名义应力不高的情况下,由局部的应力集中而形成裂纹,随着加载循环的增加,裂纹不断扩展,直至断裂。
图(3)。
图(3)。
- 1、下载文档前请自行甄别文档内容的完整性,平台不提供额外的编辑、内容补充、找答案等附加服务。
- 2、"仅部分预览"的文档,不可在线预览部分如存在完整性等问题,可反馈申请退款(可完整预览的文档不适用该条件!)。
- 3、如文档侵犯您的权益,请联系客服反馈,我们会尽快为您处理(人工客服工作时间:9:00-18:30)。
金属疲劳试验
一、实验目的
1.了解疲劳试验的基本原理;
2.掌握疲劳极限、S-N曲线的测试方法;
3.观察疲劳失效现象和断口特征
二、实验原理
1.疲劳抗力指标的意义
目前评定金属材料疲劳性能的基本方法就是通过试验测定其S-N曲线(疲劳曲线),即建立最大应力σmax或应力振幅σa与相应的断裂循环周次N之间的曲线关系。
不同金属材料的S-N曲线形状是不同的,大致可以分为两类,如图1所示。
其中一类曲线从某应力水平以下开始出现明显的水平部分,如图1(a)所示。
这表明当所加交变应力降低到这个水平数值时,试样可承受无限次应力循环而不断裂。
因此将水平部分所对应的应力称之为金属的疲劳极限,用符号σR表示(R为最小应力与最大应力之比,称为应力比)。
若试验在对称循环应力(即R=-1)下进行,则其疲劳极限以σ-1表示。
中低强度结构钢、铸铁等材料的S-N曲线属于这一类。
实验表明,黑色金属试样如经历107次循环仍未失效,则再增加循环次数一般也不会失效。
故可把107次循环下仍未失效的最大应力作为持久极限。
另一类疲劳曲线没有水平部分,其特点是随应力降低,循环周次N不断增大,但不存在无限寿命,如图1(b)所示。
在这种情况下,常根据实际需要定出一定循环周次(108或5×107…)下所对应的应力作为金属材料的“条件疲劳极限”,用符号σR(N)表示。
(a)(b)
图1 金属的S-N曲线示意图
(a)有明显水平部分的S-N曲线(b)无明显水平部分的S-N曲线
2. S-N 曲线的测定
(1) 条件疲劳极限的测定
测试条件疲劳极限采用升降法,试件取13根以上。
每级应力增量取预计疲劳极限的5%以内。
第一根试件的试验应力水平略高于预计疲劳极限。
根据上根试件的试验结果,是失效还是通过(即达到循环基数不破坏)来决定下根试件应力增量是减还是增,失效则减,通过则增。
直到全部试件做完。
第一次出现相反结果(失效和通过,或通过和失效)以前的试验数据,如在以后试验数据波动范围之外,则予以舍弃;否则,作为有效数据,连同其他数据加以利用,按以下公式计算疲劳极限: ∑==n i i i N R v m 1)(1σσ
式中m —有效试验总次数;n —应力水平级数;σi —第i 级应力水平;v i —第i 级应力水平下的试验次数。
例如某实验过程如图2所示,共14根试件。
预计疲劳极限为390MPa ,取其2.5%约10 MPa 为应力增量,第一根试件的应力水平402 MPa ,全部试验数据波动如图2,可见,第四根试件为第一次出现的相反结果,在其之前,只有第一根在以后试验波动范围之外,为无效,则按上式求得条件疲劳极限如下:
σR(N)=13
1(3×392+5×382+4×372+1×362)=380MPa 图2 增减法测定疲劳极限试验过程
(2) S-N 曲线的测定
测定S-N 曲线(即应力水平-循环次数N 曲线)采用成组法。
至少取五级应力水平,各级取一组试件,其数量分配,因随应力水平降低而数据离散增大,故要随应力水平降低而增多,通常每组5根。
升降法求得的,作为S-N 曲线最低应力水平点。
然后以其为纵坐标,以循环数N 或N 的对数为横坐标,用最佳拟合法绘制成S-N 曲线,如图3所示。
图3 S-N曲线
三、疲劳试验机及疲劳试样
1.疲劳试验机
疲劳试验机有机械传动、液压传动、电磁谐振以及近年来发展起来的电液伺服等,本实验所用设备为MTS810电液伺服疲劳试验机。
图4 电液伺服材料试验机
图4所示的是MTS系列电液伺服材料试验机原理图。
给定信号Ⅰ通过伺服控制器将控制信号送到伺服阀1,用来控制从高压液压源Ⅲ来的高压油推动作动器2变成机械运动作用
到试样3上,同时载荷传感器4,应变传感器5和位移传感器6又把力、应变、位移转化成电信号,其中一路反馈到伺服控制器中与给定信号比较,将差值信号送到伺服阀调整作动器位置,不断反复此过程,最后试样上承受的力(应变、位移)达到要求精度,而力、应变、位移的另一路信号通入读出器单元Ⅳ上,实现记录功能。
2.疲劳试样
疲劳试样的种类很多,其形状和尺寸主要决定于试验目的、所加载荷的类型及试验机型号。
现将国家标准中推荐的几种轴向疲劳试验的试样列于图5至图10,以供选用。
图5 圆柱形光滑轴向疲劳试样图6 漏斗形光滑轴向疲劳试样
图7 漏斗形轴向疲劳试样图图8 矩形光滑轴向疲劳试样
图9 圆柱形V形缺口轴向疲劳试样
图10 矩形U形缺口轴向疲劳试样
以上各种试样的夹持部分应根据所用的试验机的夹持方式设计。
夹持部分截面面积与试验部分截面面积之比大于1.5。
若为螺纹夹持,应大于3。
四、实验步骤与方法
本实验在MTS810电液伺服疲劳试验机上进行,试样形状与尺寸如图8所示。
1. 领取试验所需试样,用游标卡尺测量试件的原始尺寸。
表面有加工瑕疵的试样不能使用。
2. 开启机器,设置各项试验参数,
3. 安装试件。
使试样与试验机主轴保持良好的同轴性。
4. 静力试验。
取其中一根合格试样,先进行拉伸测其σb。
静力试验目的一方面检验材质强
度是否符合热处理要求,另一方面可根据此确定各级应力水平。
5. 设定疲劳试验具体参数,进行试验。
第一根试样最大应力约为(0.6~0.7)σb,经N1次循
环后失效。
继取另一试样使其最大应力σ2=(0.40~0.45) σb,若其疲劳寿命N<107,则应降低应力再做。
直至在σ2作用下,N2>107。
这样,材料的持久极限σ-1在σ1与σ2之间。
在σ1与σ2之间插入4~5个等差应力水平,它们分别为σ3﹑σ4﹑σ5﹑σ6,逐级递减进行实验,相应的寿命分别为N3﹑N4﹑N5﹑N6。
6. 观察与记录。
由高应力到低应力水平,逐级进行试验。
记录每个试样断裂的循环周次,
同时观察断口位置和特征。
7. 实验结束,取下试件。
清理实验场地,试验机一切机构复原。
8. 根据实验记录进行有关计算。
将所得实验数据列表;然后以lgN为横坐标,σmax为纵坐
标,绘制光滑的S-N曲线,并确定σ-1的大致数值。
报告中绘出破坏断口,指出其特征。
五、思考题:
1.疲劳试样的有效工作部分为什么要磨削加工,不允许有周向加工刀痕?
2.实验过程中若有明显的振动,对寿命会产生怎样的影响?
3.若规定循环基数为N=106,对黑色金属来说,实验所得的临界应力值σmax能否称为对应于
N=106的疲劳极限?。