锻造工艺规范
锻造及锻后热处理工艺规范

目录1.钢质自由锻件加热工艺规范2.钢锭(坯)加热规范若干概念3.加热操作守则4.锻造操作守则5.锻件锻后冷却规范6.锻件锻后炉冷工艺曲线7.锻件锻后热装炉工艺曲线8.冷锻件校直前加热、校直后(补焊后)回火工艺曲线9.锻件各钢种正火(或退火)及高温回火温度表10.锻件有效截面计算方法钢质自由锻件加热工艺规范一.范围:本规范规定了钢质自由锻件的通用加热技术条件。
本规范适用于碳素钢、合金钢、高合金钢、高温合金钢(铁基、镍基)的冷、热、半热钢锭(坯)的锻造前加热二.常用钢号分组和始、终锻加热温度范围:注1:始锻温度为锻前加热允许最高炉温,由于钢锭的铸态初生晶粒加热时过热倾向比同钢号钢坯小,故两者的锻前加热温度相差20℃~30℃;注2:根据产品的特性、锻件技术条件、变形量等因素,始锻温度可以适当调整;注3:本规范未列入的钢种,可按化学成分相近的钢号确定;注4:重要的、关键产品的、特殊材质的钢号,其加热工艺曲线由技术部编制;注5:几种不同的钢种,不同尺寸的钢锭(或坯料),在同一加热炉加热时,要以合金成分高的,尺寸大的钢锭(或坯料)为依据编制加热工艺曲线。
三.冷钢坯。
钢锭加热规范:钢锭(坯)加热规范若干概念1.钢锭(坯)入炉前的表面温度≥550℃的称为热钢锭,400~550℃的称为半热钢锭(坯),≤400℃的称为冷钢锭。
2.锻件半成品坯料的加热平均直径计算原则:δ -壁厚H- 高度或长度D- 外径1)实心圆类:当D>H时,按H计算;当D<H时,按D计算。
2)筒类锻坯:H>D 当H>δ时,按1.3δ计算。
3)空心盘(环)类:H<D当H>δ时,按δ计算;当H<δ时,按H计算。
3.为了避免锻件粗晶组织,最后一火的始锻温度可按其剩余锻造比(Y)确定:Y=1.3~1.6 最高加热温度1050℃Y<1.3 最高加热温度950℃4.不同钢种不同规格的坯料同炉加热时,装炉温度和升温速度均按较低的选用,保温时间按较长的选用。
锻造及锻后热处理工艺规范
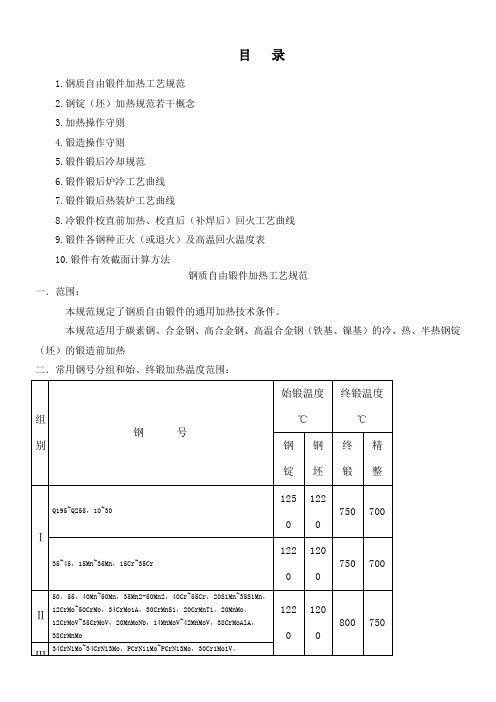
目录1.钢质自由锻件加热工艺规范2.钢锭(坯)加热规范若干概念3.加热操作守则4.锻造操作守则5.锻件锻后冷却规范6.锻件锻后炉冷工艺曲线7.锻件锻后热装炉工艺曲线8.冷锻件校直前加热、校直后(补焊后)回火工艺曲线9.锻件各钢种正火(或退火)及高温回火温度表10.锻件有效截面计算方法钢质自由锻件加热工艺规范一.范围:本规范规定了钢质自由锻件的通用加热技术条件。
本规范适用于碳素钢、合金钢、高合金钢、高温合金钢(铁基、镍基)的冷、热、半热钢锭(坯)的锻造前加热二.常用钢号分组和始、终锻加热温度范围:注1:始锻温度为锻前加热允许最高炉温,由于钢锭的铸态初生晶粒加热时过热倾向比同钢号钢坯小,故两者的锻前加热温度相差20℃~30℃;注2:根据产品的特性、锻件技术条件、变形量等因素,始锻温度可以适当调整;注3:本规范未列入的钢种,可按化学成分相近的钢号确定;注4:重要的、关键产品的、特殊材质的钢号,其加热工艺曲线由技术部编制;注5:几种不同的钢种,不同尺寸的钢锭(或坯料),在同一加热炉加热时,要以合金成分高的,尺寸大的钢锭(或坯料)为依据编制加热工艺曲线。
三.冷钢坯。
钢锭加热规范:钢锭(坯)加热规范若干概念1.钢锭(坯)入炉前的表面温度≥550℃的称为热钢锭,400~550℃的称为半热钢锭(坯),≤400℃的称为冷钢锭。
2.锻件半成品坯料的加热平均直径计算原则:δ -壁厚 H- 高度或长度 D- 外径1)实心圆类:当D>H时,按H计算;当D<H时,按D计算。
2)筒类锻坯:H>D 当H>δ时,按1.3δ计算。
3)空心盘(环)类:H<D当H>δ时,按δ计算;当H<δ时,按H计算。
3.为了避免锻件粗晶组织,最后一火的始锻温度可按其剩余锻造比(Y)确定:Y=1.3~1.6 最高加热温度1050℃Y<1.3 最高加热温度950℃4.不同钢种不同规格的坯料同炉加热时,装炉温度和升温速度均按较低的选用,保温时间按较长的选用。
锻造工艺规范
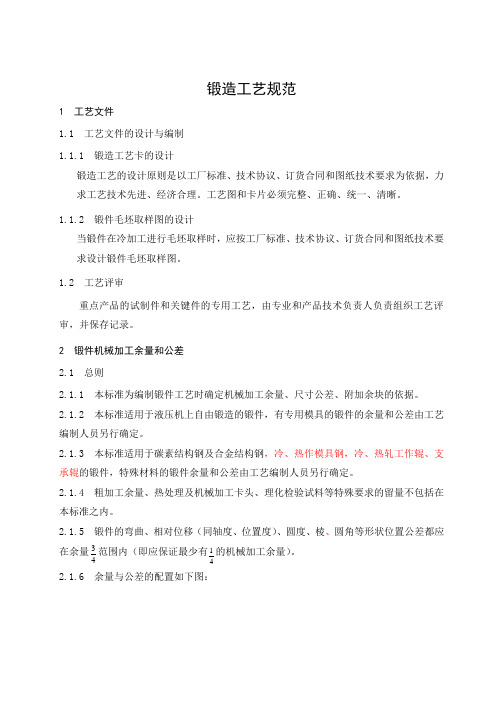
锻造工艺规范1 工艺文件1.1 工艺文件的设计与编制 1.1.1 锻造工艺卡的设计锻造工艺的设计原则是以工厂标准、技术协议、订货合同和图纸技术要求为依据,力求工艺技术先进、经济合理。
工艺图和卡片必须完整、正确、统一、清晰。
1.1.2 锻件毛坯取样图的设计当锻件在冷加工进行毛坯取样时,应按工厂标准、技术协议、订货合同和图纸技术要求设计锻件毛坯取样图。
1.2 工艺评审重点产品的试制件和关键件的专用工艺,由专业和产品技术负责人负责组织工艺评审,并保存记录。
2 锻件机械加工余量和公差 2.1 总则2.1.1 本标准为编制锻件工艺时确定机械加工余量、尺寸公差、附加余块的依据。
2.1.2 本标准适用于液压机上自由锻造的锻件,有专用模具的锻件的余量和公差由工艺编制人员另行确定。
2.1.3 本标准适用于碳素结构钢及合金结构钢,冷、热作模具钢,冷、热轧工作辊、支承辊的锻件,特殊材料的锻件余量和公差由工艺编制人员另行确定。
2.1.4 粗加工余量、热处理及机械加工卡头、理化检验试料等特殊要求的留量不包括在本标准之内。
2.1.5 锻件的弯曲、相对位移(同轴度、位置度)、圆度、棱、圆角等形状位置公差都应在余量43范围内(即应保证最少有41的机械加工余量)。
2.1.6 余量与公差的配置如下图:D :零件尺寸 C :锻件公称尺寸(基本尺寸) C ′:锻件最大尺寸 C ″:锻件最小尺寸 а:锻件名义机械加工余量δ′:下偏差(负公差) δ″:上偏差(正公差)2.1.7 本规范未包括的特殊形状的锻件及尺寸超出本规范的锻件,其余量和公差由工艺编制人员参照本规范确定。
2.1.8 在确定锻件余量时,必须兼顾零件的局部尺寸与整体尺寸的关系,局部应照顾整体,以减少加工余量。
2.1.9 易焊钢种和留有粗加工余量在粗加工后允许存在可以加工掉的局部黑皮的锻件,其锻造余量应比本标准表中规定值减少10~20%(按复杂程度)。
对易产生裂纹又不易焊补钢种(如9Cr2Mo 、32Cr2MnMo 、60CrMnMo )等锻件的余量不应比表中规定值减少。
s31254 锻件标准

s31254 锻件标准S31254锻件标准属于钢材标准的一部分,用于指导S31254材料的锻造工艺和质量要求。
本文将对S31254锻件的标准进行详细介绍。
一、材料要求S31254是一种超级奥氏体不锈钢,具有优异的耐腐蚀性能。
在锻造过程中,材料的化学成分和机械性能需满足以下要求:1. 化学成分:C≤0.02%,Si≤0.8%,Mn≤1.0%,P≤0.03%,S≤0.01%,Cr 19.5~20.5%,Ni 17.5~18.5%,Mo 6.0~6.5%,Cu 0.50~1.00%,N0.20~0.30%,Fe余量。
2. 机械性能:抗拉强度σb≥650MPa,屈服强度σ0.2≥300MPa,延伸率δ≥35%,断面收缩率ψ≥45%,冲击功AKV≥100J。
二、工艺规范1. 热处理:S31254锻件在锻造前需要进行固溶退火处理,温度范围为1100~1200℃,保温时间不少于1小时。
锻件完成锻造后需要进行快速冷却处理。
2. 锻造温度:S31254锻件的加热温度一般为1150~1250℃,保温时间根据锻件的大小和形状而定。
3. 锻件形状:S31254锻件的最大厚度不宜超过360mm,最大宽度不应超过500mm。
对于较大尺寸的锻件,可以采用多次锻造的方式进行。
4. 锻造比例:锻件的尺寸比例应控制在1:4以内,超出比例范围将导致不均匀的应力分布和变形。
三、质量要求1. 外观质量:锻件表面应光滑、无裂纹、气泡等缺陷。
2. 化学成分和机械性能:锻件应符合上述材料要求中的化学成分和机械性能指标。
3. 结构一致性:锻件的组织应均匀一致,不应出现太大的晶粒和过多的夹杂物。
4. 尺寸精度:锻件的尺寸公差应符合技术要求,在许用偏差范围内。
5. 出厂检验:锻件出厂前应进行严格的检验,包括化学成分分析、机械性能测试、外观检查和尺寸测量等。
四、应用领域S31254锻件广泛应用于海洋石油、化工、海水淡化等领域,尤其适用于具有高腐蚀介质和高温高压条件下的工作环境。
锻造工艺质量控制规范

锻造工艺质量控制规范1 主题内容与适用范围本标准规定了对锻造工艺进行全过程质量控制的通用原则和要求。
本标准适用于锻造车间的锻造工艺质量控制。
2 引用标准GB 12361 钢质模锻件通用技术条件GB 12362 钢质模锻件公差及机械加工余量GB 13318 锻造车间安全生产通则GB/T 12363 锻件功能分类JB 4249 锤上钢质自由锻件机械加工余量与公差JB 4385 锤上钢质自由锻件通用技术条件JB/T 6052 钢质自由锻件加热通用技术要求JB/T 6055 锻造车间环境保护导则3 锻件分类本标准质量控制所涉及的锻件分类按GB/T 12363 执行。
4 环境的控制锻造厂的工作环境包括厂房地面、天窗、温度、通风、照明、噪声、通道、管道以及坯料、锻件和工夹模具的存放等均应按GB 13318 第3 章和JB/T 6055 第3、4 章的要求和国家的有关法规、法律制订本企业的具体实施要求。
5 设备、仪表与工装的控制5. 1 设备、仪表5. 1. 1 各类设备必须完好,并有操作规程和维修、检定制度。
5. 1. 2 各类在用主要设备必须挂有完好设备标牌,并有检验有效期及下次检定日期。
不合格设备及超过检定合格有效期的设备必须挂“停用”标牌。
5. 1. 3 设备的控制系统及检测显示仪表应定期检查,确保仪表和其精度的显示数值准确。
5. 1. 4 加热设备的温度显示及测点布置应正确反应加热区炉温及炉温均匀性。
5. 1. 5 所用设备都必须建立档案,其具体内容包括:a. 设备使用说明书;b.台时记录;c.故障记录d.修理记录e. 历年检定报告及检定合格证。
5. 2 模具及其他工装5. 2. 1 新模具应按模具图的要求制造,检验合格后进行试模,确认达到设计、制造要求后方可投入生产。
5. 2. 2 在每批锻件生产结束时,应将锻造的尾件上打标记并经检验尺寸合格后,模具方可返库继续使用。
5. 2. 3 锻造所用工具,必须按工艺文件的规定选用,并经检查完好方可使用。
锻造工艺作业指导书
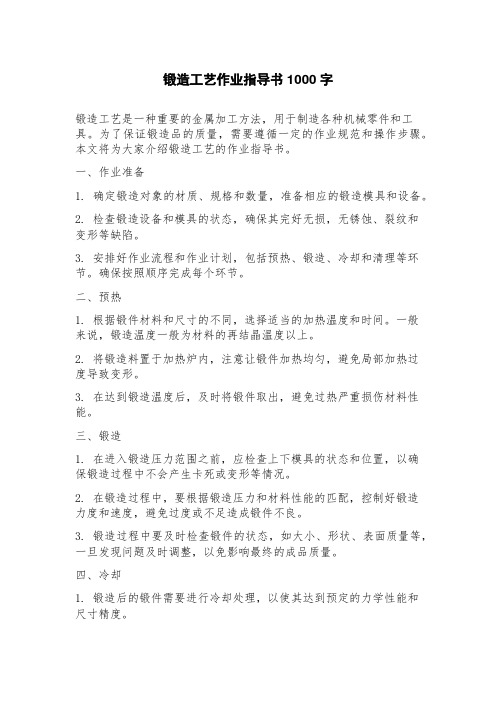
锻造工艺作业指导书1000字锻造工艺是一种重要的金属加工方法,用于制造各种机械零件和工具。
为了保证锻造品的质量,需要遵循一定的作业规范和操作步骤。
本文将为大家介绍锻造工艺的作业指导书。
一、作业准备1. 确定锻造对象的材质、规格和数量,准备相应的锻造模具和设备。
2. 检查锻造设备和模具的状态,确保其完好无损,无锈蚀、裂纹和变形等缺陷。
3. 安排好作业流程和作业计划,包括预热、锻造、冷却和清理等环节。
确保按照顺序完成每个环节。
二、预热1. 根据锻件材料和尺寸的不同,选择适当的加热温度和时间。
一般来说,锻造温度一般为材料的再结晶温度以上。
2. 将锻造料置于加热炉内,注意让锻件加热均匀,避免局部加热过度导致变形。
3. 在达到锻造温度后,及时将锻件取出,避免过热严重损伤材料性能。
三、锻造1. 在进入锻造压力范围之前,应检查上下模具的状态和位置,以确保锻造过程中不会产生卡死或变形等情况。
2. 在锻造过程中,要根据锻造压力和材料性能的匹配,控制好锻造力度和速度,避免过度或不足造成锻件不良。
3. 锻造过程中要及时检查锻件的状态,如大小、形状、表面质量等,一旦发现问题及时调整,以免影响最终的成品质量。
四、冷却1. 锻造后的锻件需要进行冷却处理,以使其达到预定的力学性能和尺寸精度。
2. 冷却过程中,应根据材料和尺寸的不同,采取不同的冷却方法和速度,以保证锻件内部和表面温度的均匀性。
3. 完成冷却后,要对锻件进行质量检查,如硬度、尺寸、外观等方面的检查。
如发现问题需要及时进行调整和处理。
五、清理1. 锻件完成后,要及时将加热炉和周边设备进行清理和维护,以保证下一次的作业安全进行。
2. 锻件表面可能残留有灰泥、氧化皮等杂质,需要对其进行去除清洗,以便对表面进行进一步的加工和处理。
3. 最后,要对锻造成品进行统计和存储,以保持其质量和安全,同时也为下一步的加工和生产打好基础。
总之,锻造工艺的作业指导书是锻造生产中的重要文件,必须遵循和落实。
自由锻锻造规范
1 目的对本公司的锻压过程作出具体规定,确保产品的最终质量。
2 范围适用于本公司的自由锻工序。
3 职责生产部负责开发和维护此作业流程,并且确定各设备操作中的负责人4 程序4.1 自由锻工序自由锻工序:基本工序、辅助工序和修整工序。
4.1.1 基本工序使金属坯料产生一定程度的塑性变形,以得到所需形状、尺寸或改善材质性能的工艺过程。
它是锻件成形过程中必需的变形工序,如镦粗、拔长、弯曲、冲孔、切割、扭转和错移等。
实际生产中最常用的是镦粗、拔长和冲孔三个工序。
4.1.1.1镦粗沿工件轴向进行锻打,使其长度减小,横截面积增大的操作过程。
常用来锻造齿轮坯、凸缘、圆盘等零件,也可用来作为锻造环、套筒等空心锻件冲孔前的预备工序。
镦粗可分为全镦粗和局部镦粗两种形式,如图4.1镦粗时,坯料不能过长,高度与直径之比应小于2.5,以免镦弯,或出现细腰、夹层等现象。
坯料镦粗的部位必须均匀加热,以防止出现变形不均匀。
图4.1 镦粗a)全镦粗b)局部镦粗4.1.1.2拔长拔长是沿垂直于工件的轴向进行锻打,以使其截面积减小,而长度增加的操作过程,如图4.2常用于锻造轴类和杆类等零件。
对于圆形坯料,一般先锻打成方形后再进行拔长,最后锻成所需形状,或使用V型砧铁进行拔长,如图4.3图4.2拔长图4.3用V型砧铁拔长圆坯料4.1.1.3冲孔利用冲头在工件上冲出通孔或盲孔的操作过程。
常用于锻造齿轮、套筒和圆环等空心锻件,对于直径小于25mm的孔一般不锻出,而是采用钻削的方法进行加工。
a)在薄坯料上冲通孔时,可用冲头一次冲出。
若坯料较厚时,可先在坯料的一边冲到孔深的2/3深度后,拔出冲头,翻转工件,从反面冲通,以避免在孔的周围冲出毛刺,如图4.4b)实心冲头双面冲孔时,圆柱形坯料会产生畸变。
畸变程度与冲孔前坯料直径D0、高度H0和孔径d1等有关。
D0/d1愈小,畸变愈严重,另外冲孔高度过大时,易将孔冲偏,因此用于冲孔的坯料直径D0与孔径d1之图4.4孔a)薄坯料冲孔b)厚坯料冲孔1-冲头2-坯料3-垫环4-芯料4.2 辅助工序4.2.1 为使基本工序操作方便而进行的预变形工序称为辅助工序(压钳口、切肩等)。
锻压工艺规范
1.3 墩粗工序的操作要点和规则墩粗是使坯料高度减小而横截面积增大的锻造工序。
它主要用于锻造齿轮坯、凸缘和圆盘等类锻件,也作为提高拔长锻造比和冲孔前的预备工序。
操作中应注意:1)坯料在墩粗前应加热到材料所允许的最高加热温度,并进行适当的保温,以便坯料内外温度均匀一致,降低其变形抗力,防止墩粗时坯料中心出现偏移,造成钢锭偏析区移向一边,从而使墩件质量变坏。
2)合金钢和重量大于8~12t的碳素钢钢锭,墩粗前必须倒棱,以锻合其皮下缺陷,使墩粗表面不致产生裂纹,同时去除钢锭棱边和锥度,可保证锭身平直,避免不均匀性墩粗。
3)为了防止坯料墩粗时产生纵向弯曲,坯料墩粗前的高度H与直径D 之比不应超过3,最好将H/D控制在2~2.5之间。
对于正六面体锻坯的墩粗,其高度和最小基边之比应小于3.5~4。
4)檄粗前的坯料两端面必须平整,且应与坯料的轴心线垂直。
在坯料的侧表面上,不应有凹坑、划痕和裂纹等缺陷,以防在墩粗过程中进一步扩大。
5)钢坯墩粗时,为了防止出现墩粗裂纹和不均匀变形,应不断地绕着坯料的轴心线转动,每次墩粗的压下量不应超过该材料所允许的极限值。
墩后再拔时其高度应满足拔长要求。
6)锤上墩粗时,坯料的高度应与锤头的行程空间尺寸相适应,即应使H-h0>0.25H式中H—锤头的最大行程(mm);h0——坯料的原始高度(mm)。
7)水压机上墩粗时,其锭身高度、上墩粗板高度和下墩粗盘高度之和,应小于水压机的最大净空距,即应使H n≥H u+H i+H b+(100~200)式中H n——水压机的最大净空距(mm);H u——上墩粗板高度(mm);H i——锭身高度(mm));H b——下墩粗盘高度(mm)。
8)为了使墩粗坯料组织均匀和不出现过大的侧面鼓肚,应视情况采取相应的改善措施,这些可行的措施有:①预热墩粗工具,以防坯料过快冷却。
一般均应预热到200—300℃。
②对于低塑性材料的墩粗,应在上、下端面使用玻璃粉、玻璃棉和石墨粉等润滑剂,以提高变形均匀性。
硬铝锻造标准最新规范
硬铝锻造标准最新规范硬铝锻造是一种金属加工技术,它涉及到将硬铝材料加热至一定温度后进行锻造以改善其物理性能和加工特性。
以下是硬铝锻造的最新标准规范:1. 材料选择与准备:- 硬铝材料应符合ASTM B221或相应的国际标准。
- 材料在锻造前应进行彻底的清洁和检查,以确保无杂质和缺陷。
2. 加热温度:- 硬铝的加热温度应控制在450°C至500°C之间,以确保材料的可塑性。
3. 锻造工艺:- 锻造应在加热后的硬铝材料处于热塑性状态下进行。
- 锻造过程中应控制锻造速度,避免过快或过慢导致材料性能下降。
4. 锻造设备:- 使用的锻造设备应定期进行维护和校准,确保其精度和可靠性。
5. 锻造后处理:- 锻造完成后,材料应进行适当的冷却处理,以稳定其微观结构。
- 冷却后的材料应进行硬度测试和微观结构分析,确保符合性能要求。
6. 质量控制:- 锻造过程中应实施严格的质量控制措施,包括但不限于尺寸精度、表面光洁度和内部缺陷检测。
7. 安全与环保:- 锻造操作应遵守相关的安全标准,确保操作人员的安全。
- 锻造过程中产生的废气、废液等应进行妥善处理,符合环保要求。
8. 记录与追溯:- 所有锻造过程的参数和结果都应详细记录,以便追溯和分析。
9. 产品标识:- 完成锻造的产品应有清晰的标识,包括材料类型、锻造日期、批次号等信息。
10. 后续加工:- 对于需要进一步加工的硬铝锻造件,应按照特定的加工标准进行操作。
结束语:硬铝锻造标准的最新规范旨在确保产品质量的同时,提高生产效率和安全性。
随着技术的发展和行业标准的更新,这些规范可能会有所变化,因此制造商和操作人员应持续关注最新的行业动态和技术进步。
锻造及锻后热处理工艺规范DOC.doc
目录1.钢质自由锻件加热工艺规范2.钢锭(坯)加热规范若干概念3.加热操作守则4.锻造操作守则5.锻件锻后冷却规范6.锻件锻后炉冷工艺曲线7.锻件锻后热装炉工艺曲线8.冷锻件校直前加热、校直后(补焊后)回火工艺曲线9.锻件各钢种正火(或退火)及高温回火温度表10.锻件有效截面计算方法钢质自由锻件加热工艺规范一.范围:本规范规定了钢质自由锻件的通用加热技术条件。
本规范适用于碳素钢、合金钢、高合金钢、高温合金钢(铁基、镍基)的冷、热、半热钢锭(坯)的锻造前加热二.常用钢号分组和始、终锻加热温度范围:组号钢别Q195~Q255, 10~30Ⅰ35~45,15Mn~35Mn ,15Cr~35Cr50,55,40Mn~50Mn ,35Mn2-50Mn2 ,40Cr~55Cr ,20SiMn~35SiMn ,12CrMo~50CrMo ,34CrMo1A ,30CrMnSi , 20CrMnTi ,20MnMo ,Ⅱ12CrMoV~35CrMoV , 20MnMoNb , 14MnMoV~42MnMoV,38CrMoAlA ,38CrMnMo34CrNiMo~34CrNi3Mo,PCrNi1Mo~PCrNi3Mo,30Cr1Mo1V,25Cr2Ni4MoV ,22Cr2Ni4MoV ,5CrNiMo ,5CrMnMo ,37SiMn2MoV 30Cr2MoV ,40CrNiMo ,18CrNiW ,50Si2~60Si2 ,65Mn ,50CrNiW ,50CrMnMo ,60CrMnMo ,60CrMnVT7~T10 , 9Cr,9Cr2, 9Cr2Mo , 9Cr2V ,9CrSi ,70Cr3Mo ,Ⅲ1Cr13~4Cr13 ,86Cr2MoV ,Cr5Mo , 17-4PH0Cr18Ni9~2Cr18Ni9 ,0Cr18Ni9Ti , Cr17Ni2 , F316LN50Mn18Cr4 , 50Mn18Cr4N , 50Mn18Cr4WN , 18Cr18Mn18NGCr15,GCr15SiMn , 3Cr2W8V ,CrWMo , 4CrW2Si~6CrW2SiCr12MoV1 , 4Cr5MoVSi(H11) , W18Cr4VGH80, GH901, GH904 ,GH4145 ,WR26 ,ⅣNiCr20TiAl , incone1600, incone1800始锻温度终锻温度℃℃钢锭钢坯终锻精整12501220750700 1220120075070012201200800750 12001180850800 120011808508001200 1180 850 800 1180 1160 950 900 1130 1100 930 930注 1:始锻温度为锻前加热允许最高炉温,由于钢锭的铸态初生晶粒加热时过热倾向比同钢号钢坯小,故两者的锻前加热温度相差 20℃~30℃;注 2:根据产品的特性、锻件技术条件、变形量等因素,始锻温度可以适当调整;注 3:本规范未列入的钢种,可按化学成分相近的钢号确定;注 4:重要的、关键产品的、特殊材质的钢号,其加热工艺曲线由技术部编制;注 5:几种不同的钢种,不同尺寸的钢锭(或坯料),在同一加热炉加热时,要以合金成分高的,尺寸大的钢锭(或坯料)为依据编制加热工艺曲线。
- 1、下载文档前请自行甄别文档内容的完整性,平台不提供额外的编辑、内容补充、找答案等附加服务。
- 2、"仅部分预览"的文档,不可在线预览部分如存在完整性等问题,可反馈申请退款(可完整预览的文档不适用该条件!)。
- 3、如文档侵犯您的权益,请联系客服反馈,我们会尽快为您处理(人工客服工作时间:9:00-18:30)。
ZX/JS-0058
江苏新中信电器设备有限公司
锻造工艺规范
编制:审核:审批:
二零三年三月
江苏新中信电器设备有限公司
ZX/JS-005
锻造工艺规范———————————————————
1 主题内容与适用范围
本规程规定了煤炉加热、空(蒸)气锤锻造的操作程序及要点。
本规程适用于公司外协锻造件煤炉加热、空(蒸)气锤上的锻造,锻造件。
2 准备工作
2.1 材料检查
2.1.1 操作者必须根据锻造工艺卡上规定的材质和下料规格核对材质和规格,并核查实际下料毛坯尺寸,发生疑问时应将信息反馈到发料部门和技术部门。
2.1.2 操作者必须目视检查原材料,不得有可能导致锻造宏观缺陷存在,有缺陷之原材料经打磨或切削加工等方法处理后,再经无损检验或目视检查,在不影响锻造质量的情况下方可加热锻造。
2.2 设备及模具的检查
2.2.1 生产前,应认真检查设备及所有附件,一切正常方可投入生产。
2.2.2 操作者应根据派工单和锻造工艺卡片领用,检查核对模具,并根据锻造工艺核查模具尺寸,不得有误。
3 材料加热
锻造加热设备为灶或炉和室式炉,燃料为煤,在加热过程中应特别注意尽量减少氧化,防止过热过烧。
3.1 为了减少氧化皮,在加热过程可采取以下措施:
a、在保证加热质量前提下,直径小于200㎜的小规格低、中碳钢和低合金钢尽
量采用快速加热,缩短加热时间,尤其是金属在高温下的停留时间不宜过长,尽
量用少装勤装的操作方法。
b、在燃料完全燃烧的条件下,尽可能减少过剩空气量,以免炉内剩余氧气过多,
并注意减少燃料中水分。
c、炉堂应保持不大的正压力,防止冷空气吸入炉堂。
d、工件加热到温后尽快出炉锻打。
3.2 防止过热、过烧的措施:
a、熔点较钢材低的铜屑等不能落入炉底,以防渗入金属内部,导致过烧。
b、控制加热温度和时间,钢材温度不得高于材料所允许的始锻温度,如果锻压
设备发生故障而长时间停锻时,必须降低炉温或采取其它措施。
c、高、中合金钢和直径大于200㎜的高碳钢加热时应适当控制加热速度,可采取
适当降低装炉温度并在此温度下保温一段时间的方法,以防形成内裂。
4 锻造
4.1 基本要点
4.1.1 操作者在锻打之前,必须熟悉锻件图及锻造工序,准备好自检量具和工具。
4.1.2 根据工艺规定,使用相应锻压设备。
4.1.3 材料达到锻造温度(可目测或用光学高温计测量)即可出炉锻造,在操作时避免局部过冷,工模具要预热到足够温度,操作要迅速,又要避免局部重复打击。
4.1.4 严格控制终锻温度,不允许在高出规定终锻温度太高的温度下停止锻打,否则会形
成粗大晶粒影响材料性能。
4.1.5 精整工序时,终锻温度允许比规定低50~80℃。
4.1.6 自由锻每锻一只零件,操作者都必须按工艺自检,模锻件应首检,且锻制一定数量后应再次检验。
4.1.7 锻后冷却及热处理按工艺规定执行。
4.1.8 直接使用钢锭锻造的零件,应有适当的锻造比:
a、碳素钢锻件的主体最大截面锻造比不小于2.5,其凸台部分不小于1.5。
b、合金结构钢锻件的主体最大截面锻造比不小于3,其凸台部分不小于175。
上述锻造比的计算:对单纯拔长时,为各分锻造比之乘积;反复镦粗拔长时,只计算镦粗比或拔长比,总锻造比亦为各分锻造比之乘积。
4.1.9 锻件出现大飞边等缺陷时,应滚圆或冷却后用砂轮打磨。
4.2.1 镦粗前毛坯加热温度应均匀,镦粗时要把毛坯围绕轴心线不断转动,毛坯发生弯曲时必须立即校正。
4.2.2 镦粗时每次的压缩量应小于材料塑性允许的范围,如果镦粗后需进一步拔长时,应考虑到拔长的可能性,禁止在终锻温度以下镦粗。
4.3 拔长
4.3.1 每次锤击的压下量应小于材料塑性所允许的数值,而且每次压缩后听锻件宽度与高度比应小于
2~2.5,否则翻转90º再锻打时易产生弯曲和折叠,每次送进量与单边压缩量之比大于1~1.5,否则易
产生折叠。
4.3.2 为了得到平滑的锻件表面,每次送进量应小于0.75~0.8倍的砧宽。
4.3.3 沿方形毛坯对角线锻压时应锻得轻些,以免中心部分产生裂纹。
4.3.4 拔长锻件端部时,为防止产生端部内凹和夹层现象,端部压料长度必须大于拔长前
材料直径的0.3倍。
4.3.5 在平砧上拔长时,先将圆断面毛坯压成矩形截面,再将矩形截面毛坯拔长到一定尺寸,然后再压成八角,最后锻成圆形。
4.4 芯棒拔长
4.4.1 预冲孔的直径如小于芯棒直径,拔长前要进行扩孔。
4.4.2 t/d芯轴≤0.5的薄壁空心件,上下砧均应用V型砧拔长;
t/d芯轴≥0.5的厚壁空心件,拔长时下砧用V型砧,上面可用平砧;上下都用平砧时,必须先锻成六角形再进行拔长,达到一定尺寸后再锻成圆形;
H/d≤0.5的空心件,可直接用冲头拔长。
(t:锻件壁厚,d:芯轴直径,H:锻件高度,d:锻件孔径)
4.4.3 锻件两端部锻造终止温度应于比一般的终锻温度高100~150℃,锻造前芯轴应预热到150~250℃。
4.4.4为使锻件壁厚均匀和端面平整,坯料加热温度应当均匀,操作时每次转动角度应均均。
4.5 扩孔
4.5.1 冲头扩孔时,每次扩孔量不宜太大,一般不超过25㎜。
4.5.2 冲头扩孔时,如孔冲偏了,应采用局部水冷等方法使壁薄处变形,抗力增大,以保证扩孔正常进行。
4.5.3 在马杠上扩孔若扩孔前冲孔直径小于马杠直径,则应先用冲头扩孔,再用马杠扩孔。
4.5.4 在马杠上扩孔时,为保证壁厚均匀,每次转动量和压缩量应尽可能一致。
5 试样
5.1 试样必须和被评定零件同属于同成份、同规格、同一批号材料。
5.2 试样锻造比应等于或小于被评定零件的锻造比,试样总的锻造比应不超过被评定零件的总锻造比。
5.3 试样直径或厚度应与被评定零件的有效壁厚等效,但最大不得超过63㎜,其始,终锻温度及冷方法按被评定零件的锻造工艺执行。
5.4 试样应符合Q/KV-WD-10要求
6 检验
锻造质量检验按锻造工艺及检验规程进行。
单阀及整涂黄油防锈。
长期存放在零件,如垫环、法兰等涂防锈油脂。
涂油应表面完全干燥后进行,涂油应均匀一致,装配后产品涂油范围必须满足涂喷漆要求,即不得影响喷漆的质量。