压铸模具设计和制造介绍材料
压铸件工艺流程
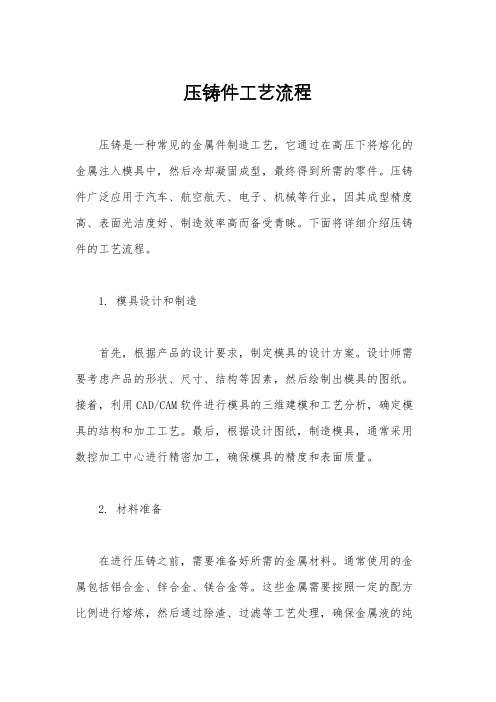
压铸件工艺流程压铸是一种常见的金属件制造工艺,它通过在高压下将熔化的金属注入模具中,然后冷却凝固成型,最终得到所需的零件。
压铸件广泛应用于汽车、航空航天、电子、机械等行业,因其成型精度高、表面光洁度好、制造效率高而备受青睐。
下面将详细介绍压铸件的工艺流程。
1. 模具设计和制造首先,根据产品的设计要求,制定模具的设计方案。
设计师需要考虑产品的形状、尺寸、结构等因素,然后绘制出模具的图纸。
接着,利用CAD/CAM软件进行模具的三维建模和工艺分析,确定模具的结构和加工工艺。
最后,根据设计图纸,制造模具,通常采用数控加工中心进行精密加工,确保模具的精度和表面质量。
2. 材料准备在进行压铸之前,需要准备好所需的金属材料。
通常使用的金属包括铝合金、锌合金、镁合金等。
这些金属需要按照一定的配方比例进行熔炼,然后通过除渣、过滤等工艺处理,确保金属液的纯净度和稳定性。
3. 熔炼和保温将准备好的金属材料加入熔炉中进行熔炼,直至达到所需的温度和流动性。
然后将熔融金属倒入保温炉中进行保温,以保持金属液的温度和流动性,为后续的压铸工艺做准备。
4. 压铸成型在保温炉中保持金属液的温度和流动性后,将金属液注入压铸机的射出室。
通过高压注射系统,将金属液压入模具腔内,填充整个模腔。
在一定的压力和温度下,金属液在模具中凝固成型,形成所需的压铸件。
5. 冷却和固化在金属液填充模腔后,需要等待一定时间,让压铸件在模具中冷却和固化。
冷却时间的长短取决于金属的种类和厚度等因素。
在固化完成后,打开模具,取出成型的压铸件。
6. 修磨和处理取出的压铸件通常会存在一些毛刺、气孔等缺陷,需要进行修磨和处理。
通过去毛刺、抛光、喷砂等工艺,使压铸件的表面光洁度达到要求。
同时,还可以进行热处理、表面处理等工艺,提高压铸件的性能和表面质量。
7. 检验和包装最后,对成型的压铸件进行检验,包括尺寸、外观、化学成分等方面的检测。
合格后,对压铸件进行包装,通常采用防震防潮的包装方式,以确保产品的质量和运输安全。
压铸模具设计范文

压铸模具设计范文压铸模具设计是指为了生产压铸件而设计的模具,其主要任务是将液态金属注入模具中,并在模具中冷却、凝固,最终得到所需形状的金属零件。
压铸模具设计的主要工作包括设计模具的结构、选材、计算模具的合理尺寸和形状等。
一、压铸模具结构设计1.模具整体结构设计:根据压铸件的形状和尺寸,确定模具的整体结构。
一般情况下,压铸模具采用上下模结构,上模为固定模,下模为活动模。
针对复杂形状的压铸件,可能需要设计多个滑模和拉杆。
2.模腔设计:根据压铸件的形状和尺寸,确定模腔的几何形状和尺寸。
模腔的设计应保证在模具关闭时,模腔中的液态金属能够充满整个腔体,并且在冷却凝固过程中,金属能够均匀收缩,避免产生缩孔和其他缺陷。
3.浇口和导流系统设计:浇口和导流系统的设计对于压铸件的质量和生产效率有着重要的影响。
浇口的设计应尽量避免金属的湍流流动,避免气泡的产生。
导流系统的设计应考虑金属的顺序填充和排气,以及冷却和凝固过程中的温度控制。
二、压铸模具选材压铸模具的选材应根据金属的性能和压铸工艺的要求来确定。
通常情况下,模具会选用高强度和耐磨损的合金钢作为材料,以保证模具的使用寿命和精度。
同时,还需要考虑模具的热传导性能,以确保压铸件能够快速冷却、凝固。
三、压铸模具尺寸和形状计算1.模具尺寸计算:模具尺寸的计算包括模腔尺寸、模板尺寸、滑模尺寸、导流系统尺寸等。
模具尺寸的计算需要考虑压铸件的最终尺寸、缩孔和收缩率等因素。
2.模具形状计算:模具的形状计算主要是指模腔内部的曲面和棱角的设计。
对于复杂形状的压铸件,需要使用CAD软件进行三维建模和形状优化,以确保模具的制造精度和压铸件的质量。
压铸模具设计需要充分考虑压铸件的形状和尺寸、材料的性能、压铸工艺要求等因素,通过合理的结构设计、选材和计算,能够提升压铸件的质量和生产效率。
在设计过程中,还需要考虑模具的制造难度和制造成本,以确保模具的可行性和经济性。
常见的压铸模具结构及设计
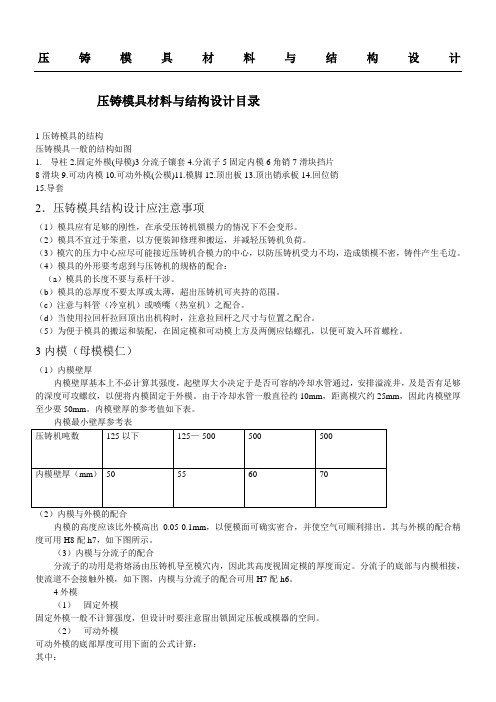
压铸模具材料与结构设计压铸模具材料与结构设计目录1压铸模具的结构压铸模具一般的结构如图1.导柱2.固定外模(母模)3分流子镶套4.分流子5固定内模6角销7滑块挡片8滑块9.可动内模10.可动外模(公模)11.模脚12.顶出板13.顶出销承板14.回位销15.导套2.压铸模具结构设计应注意事项(1)模具应有足够的刚性,在承受压铸机锁模力的情况下不会变形。
(2)模具不宜过于笨重,以方便装卸修理和搬运,并减轻压铸机负荷。
(3)模穴的压力中心应尽可能接近压铸机合模力的中心,以防压铸机受力不均,造成锁模不密,铸件产生毛边。
(4)模具的外形要考虑到与压铸机的规格的配合:(a)模具的长度不要与系杆干涉。
(b)模具的总厚度不要太厚或太薄,超出压铸机可夹持的范围。
(c)注意与料管(冷室机)或喷嘴(热室机)之配合。
(d)当使用拉回杆拉回顶出出机构时,注意拉回杆之尺寸与位置之配合。
(5)为便于模具的搬运和装配,在固定模和可动模上方及两侧应钻螺孔,以便可旋入环首螺栓。
3内模(母模模仁)(1)内模壁厚内模壁厚基本上不必计算其强度,起壁厚大小决定于是否可容纳冷却水管通过,安排溢流井,及是否有足够的深度可攻螺纹,以便将内模固定于外模。
由于冷却水管一般直径约10mm,距离模穴约25mm,因此内模壁厚至少要50mm。
内模壁厚的参考值如下表。
内模最小壁厚参考表(2)内模与外模的配合内模的高度应该比外模高出0.05-0.1mm,以便模面可确实密合,并使空气可顺利排出。
其与外模的配合精度可用H8配h7,如下图所示。
(3)内模与分流子的配合分流子的功用是将熔汤由压铸机导至模穴内,因此其高度视固定模的厚度而定。
分流子的底部与内模相接,使流道不会接触外模,如下图,内模与分流子的配合可用H7配h6。
4外模(1)固定外模固定外模一般不计算强度,但设计时要注意留出锁固定压板或模器的空间。
(2)可动外模可动外模的底部厚度可用下面的公式计算:其中:h:外模底部之厚度(mm)p:铸造压力(kg/cm2)L:模脚之间距(mm)a:成品之长度(mm)b:成品之宽度(mm)B:外模之宽度(mm)E:钢的杨氏模数=2.1×106kg/cm2d:外模在开模方向的最大变形量(mm),一般取d≤0.05mm.例:某铸件长300mm,宽250mm,铸造压力选定280(kg/cm2),外模之宽度560(mm),模脚之间距360(mm),最大变形量取0.05(mm)。
压铸模具基础知识介绍
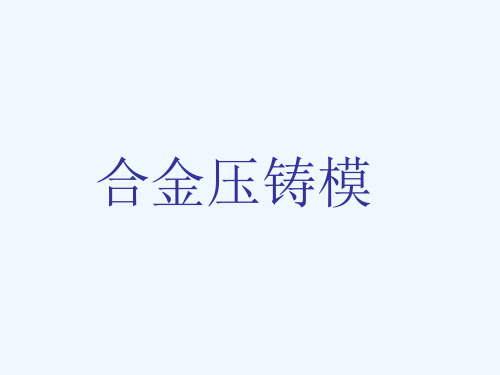
材料: T8A、T10A、H13 热处理: HRC 42~47
(6).限位块
作用: 滑块抽出后要求稳固保持在一定位置上,以便于再
次合模时斜销准确插入滑块斜孔,使滑块准确复位.
横浇道长度:取(直浇道)1/2 +(35~50) 横浇道长度尺寸不可以过短小,否那么使金属液起稳流和导
向作用不明显。
横浇道
3、内浇口:
内浇口应使金属液以最正确的流动状态充填型腔应先充填
型腔深腔部位,最后流向分型面,防止先封闭分型
面,防止金属液对型芯等薄弱部位冲击,易导致型
芯变形。
内浇口调整着从横浇道输送过来金属液速度,其位置和方向最
二 溢排系统:
据熔融金属在模具内填充情况,而开设排气通道。 用于容纳液态金属在充填过程中排出气体、杂物冷污合金等。
溢流槽
溢流槽的结构形式: (1)布置在模具分型面上的溢流槽 (2)布置在模具型腔内部的溢流槽。 其形式有: 杆形溢流槽 管形溢流槽 环形溢流槽 双级溢流槽 波纹状溢流槽
第二局部 压铸模浇排系统
一、 浇注系统:
引导金属液以一定的方式充填型腔,对金属液流动方向、 压力传递、充填速度、排气条件、模具的热平衡都能起 到控制和调节作用。 包括三个方面:
1。 直浇道 :
要求:有利压射力传递和金属液充填
平稳,。
对于冷室压铸模一般由压室和浇口套组成。
直浇道尺寸确实定是跟据铸件结构和重量等要 求来选择确立。
三 加热和冷却系统: 压铸模具在压铸生产前应进行充分地预热,并在压
铸过程中保持在一定温度范围内。 压铸生产中模具的温度由加热与冷却系统进行控制
压铸成型工艺与模具设计第章压铸模常用材料

压铸成型工艺与模具设计第章压铸模常用材料一、引言压铸是工程塑料成型加工中使用广泛的一种方法,其在汽车、家电、电信设备、医疗设备等领域有着广泛的应用。
压铸模是实现压铸成型的核心部件,其制造材料的选择及质量直接影响到压铸成型的精度和寿命,因此正确选择压铸模常用材料十分重要。
本文将介绍目前较为常用的压铸模制造材料,主要包括铝合金、钢和铜合金。
二、铝合金铝合金是一种常用的压铸模制造材料,其主要有以下特点:1.密度小,比重约为钢材的1/3,铜材的1/2,使得铝合金模具重量轻,便于加工和操作;2.导热性能好,热膨胀系数小,能够有效地保证模具的温度稳定性;3.良好的加工性能,可以通过数控机床进行加工,精度高;4.抗腐蚀性能好,能够避免模具生锈和磨损。
铝合金可以分为纯铝、铝硅、铝镁、铝铜等多种型号,其中以铝硅合金最为常用,其强度和硬度相对较高,热膨胀系数小,加工性能也较好。
铝合金模具在使用过程中需要注意防止过度切削和损伤表面,避免在表面涂覆保护膜带来的影响,同时要注意防潮、防腐蚀。
三、钢材钢材是压铸模制造中较为常用的材料,其优点在于:1.强度高、韧性好;2.颜色均匀、质地细致,适宜进行精密加工;3.抗蚀性能好,耐磨性能优良。
钢材经常用于制作大件的模具,其硬度和强度较高,可以耐受来自铝等硬度更低的金属的高压压力,有着较强的耐用性。
但是钢材也有其缺点,例如制造成本较高、加工难度大等问题,需要对各种型号的钢材进行合理选择,同时注意防止模具表面生锈和腐蚀。
四、铜合金铜合金是一种高性能模具材料,其优点在于:1.密度较大,强度高、耐磨性好;2.热传导系数高、导电率好;3.具有良好的耐蚀性,能够避免模具表面生锈和腐蚀。
铜合金可以分为锡青铜、锰铜、铝青铜等多种型号,其中以锡青铜最为常见,其强度和韧性较好,可以用于制造中大型、复杂的模具。
铜合金不仅可以用于制造压铸模具,同时也可以用于制造各种冲压模、挤压模等模具,具有广泛的应用前景。
压铸加工流程
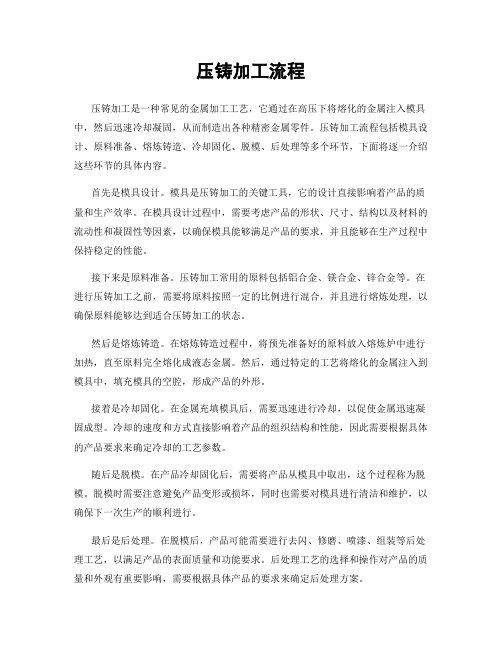
压铸加工流程压铸加工是一种常见的金属加工工艺,它通过在高压下将熔化的金属注入模具中,然后迅速冷却凝固,从而制造出各种精密金属零件。
压铸加工流程包括模具设计、原料准备、熔炼铸造、冷却固化、脱模、后处理等多个环节,下面将逐一介绍这些环节的具体内容。
首先是模具设计。
模具是压铸加工的关键工具,它的设计直接影响着产品的质量和生产效率。
在模具设计过程中,需要考虑产品的形状、尺寸、结构以及材料的流动性和凝固性等因素,以确保模具能够满足产品的要求,并且能够在生产过程中保持稳定的性能。
接下来是原料准备。
压铸加工常用的原料包括铝合金、镁合金、锌合金等。
在进行压铸加工之前,需要将原料按照一定的比例进行混合,并且进行熔炼处理,以确保原料能够达到适合压铸加工的状态。
然后是熔炼铸造。
在熔炼铸造过程中,将预先准备好的原料放入熔炼炉中进行加热,直至原料完全熔化成液态金属。
然后,通过特定的工艺将熔化的金属注入到模具中,填充模具的空腔,形成产品的外形。
接着是冷却固化。
在金属充填模具后,需要迅速进行冷却,以促使金属迅速凝固成型。
冷却的速度和方式直接影响着产品的组织结构和性能,因此需要根据具体的产品要求来确定冷却的工艺参数。
随后是脱模。
在产品冷却固化后,需要将产品从模具中取出,这个过程称为脱模。
脱模时需要注意避免产品变形或损坏,同时也需要对模具进行清洁和维护,以确保下一次生产的顺利进行。
最后是后处理。
在脱模后,产品可能需要进行去闪、修磨、喷漆、组装等后处理工艺,以满足产品的表面质量和功能要求。
后处理工艺的选择和操作对产品的质量和外观有重要影响,需要根据具体产品的要求来确定后处理方案。
总之,压铸加工流程需要经过模具设计、原料准备、熔炼铸造、冷却固化、脱模、后处理等多个环节,每个环节都需要严格控制工艺参数,以确保产品能够达到设计要求。
只有在每个环节都做到精益求精,才能够生产出高质量的压铸产品。
压铸模具设计方案
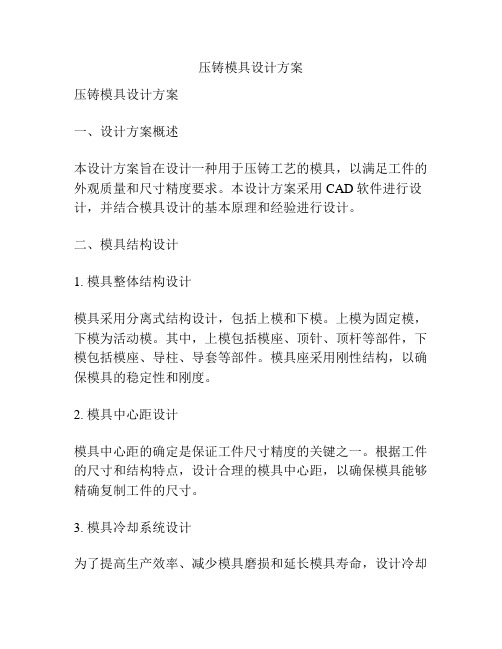
压铸模具设计方案压铸模具设计方案一、设计方案概述本设计方案旨在设计一种用于压铸工艺的模具,以满足工件的外观质量和尺寸精度要求。
本设计方案采用CAD软件进行设计,并结合模具设计的基本原理和经验进行设计。
二、模具结构设计1. 模具整体结构设计模具采用分离式结构设计,包括上模和下模。
上模为固定模,下模为活动模。
其中,上模包括模座、顶针、顶杆等部件,下模包括模座、导柱、导套等部件。
模具座采用刚性结构,以确保模具的稳定性和刚度。
2. 模具中心距设计模具中心距的确定是保证工件尺寸精度的关键之一。
根据工件的尺寸和结构特点,设计合理的模具中心距,以确保模具能够精确复制工件的尺寸。
3. 模具冷却系统设计为了提高生产效率、减少模具磨损和延长模具寿命,设计冷却系统对模具进行冷却。
冷却系统包括冷却孔和进水口,通过冷却水的流动,迅速冷却模具,以提高生产效率和模具寿命。
4. 模具材料选择模具的材料选择是保证模具寿命和使用效果的重要因素。
根据工件的材料和要求,选择适当的模具材料,保证模具具有良好的硬度和耐磨性。
三、模具生产工艺1. 加工工艺规程模具的加工工艺包括数控加工、外圆磨削等。
根据模具的具体结构和工艺要求,制定合理的加工工艺规程,以确保模具的加工质量。
2. 检测工艺模具加工完成后,进行检测以验证模具的质量。
检测工艺包括模具尺寸检测、表面质量检测等,通过合适的检测工艺,确保模具符合设计要求。
四、模具的维护、维修和更换为了保证模具的正常使用和延长其寿命,进行模具的定期维护、维修和更换。
维护工作包括清洁模具、添加润滑剂等,维修工作包括修复模具损伤、更换模具部件等,更换工作包括根据模具磨损程度,定期更换模具部件。
五、结论本设计方案是一种用于压铸工艺的模具设计方案,通过合理的结构设计、材料选择和加工工艺,可以满足工件的外观质量和尺寸精度要求。
同时,通过模具的定期维护、维修和更换,可以保证模具的正常使用和延长其寿命。
压铸模具的介绍

压铸模具的介绍压铸模具是一种用于压铸工艺的工具,它起到了定型、成型和冷却的作用。
压铸模具的设计和制造直接影响产品的质量和生产效率。
本文将介绍压铸模具的基本原理、设计要点和制造工艺。
一、压铸模具的基本原理压铸模具是一种用于将熔融金属注入到模具中并冷却凝固的工具。
它由上模、下模和导柱组成。
在压铸过程中,上模和下模会通过导柱固定,形成一个封闭的空腔。
熔融金属经过喷嘴注入到模具中,并在冷却后形成所需的产品形状。
压铸模具的设计需要考虑产品的结构、尺寸和材料特性,以及冷却系统和排气系统的设置。
二、压铸模具的设计要点1. 产品结构设计:压铸模具的设计首先要根据产品的结构特点确定上模和下模的形状和尺寸。
对于复杂的产品,需要考虑分模的设计,以方便脱模和冷却。
2. 模具材料选择:模具材料需要具有足够的硬度、强度和耐磨性,以抵御高温和高压的工作环境。
常用的模具材料包括铝合金、钢和铜合金等。
3. 冷却系统设计:在压铸过程中,模具需要快速冷却以使产品能够凝固并保持形状。
因此,冷却系统的设计非常重要。
合理的冷却系统可以提高生产效率和产品质量。
4. 排气系统设计:在压铸过程中,熔融金属会产生气体,如果不及时排出,会导致产品表面出现气孔或缺陷。
因此,排气系统的设计也是压铸模具设计的重要一环。
三、压铸模具的制造工艺压铸模具制造工艺包括模具结构设计、数控加工、装配和试模等环节。
1. 模具结构设计:根据产品的结构特点,设计模具的上模、下模和分模等零部件,并确定模具的材料和热处理工艺。
2. 数控加工:根据设计图纸,利用数控机床进行模具的精密加工,包括铣削、车削、钻孔等工序,以保证模具的尺寸和形状精度。
3. 装配:将加工好的各零部件进行装配,包括上模和下模的组装、导柱和导套的安装等。
4. 试模:在模具制造完成后,进行试模,检验模具的性能和准确性。
如果需要调整,可以进行相应的修正和改进。
总结:压铸模具在现代工业生产中起到了至关重要的作用。
- 1、下载文档前请自行甄别文档内容的完整性,平台不提供额外的编辑、内容补充、找答案等附加服务。
- 2、"仅部分预览"的文档,不可在线预览部分如存在完整性等问题,可反馈申请退款(可完整预览的文档不适用该条件!)。
- 3、如文档侵犯您的权益,请联系客服反馈,我们会尽快为您处理(人工客服工作时间:9:00-18:30)。
模具分类与条款Awintech已向客户建立了三类压铸模具,这三类压铸模具为原型模具、预生产模具和生产模具。
生产模具使用在与全能力生产的有关方面,它符合本手册中提到的标准压铸设计和制造。
其模具寿命与常规模具非常相似。
数量达到20,000件以上则适合于这类模具。
上内模和滑阀面是用优质的H13级钢制成的。
预生产模具使用在这些方面,如客户需要生产有限的超越产品寿命的的零件。
用铝压铸的这种模具能持续达到近20,000射出。
铸造时使用锌或镁都将延长其使用寿命。
原型模具则使用在这些方面,当客户只要求用380铝生产非常有限数量,仅达到500件这样的零件。
此类模具寿命会比用其它合金制成的模具寿命要长一些。
在本手册以后章节中会提到与设计和制造有关的特定模具条款。
最值得一提是在每一类模具中为客户制造合格的压铸产品的生产性能作为最首要的目标。
如果模具生产无法满足客户的需求,则毫无价值。
我们尝试详细说明一下品质标准,在这三类模具中每一个品质标准都要向客户提供。
另外,我们也在努力确保他们对每一类模具生产的铸件质量有所了解。
与Awintech作生意Awintech的目标就是向客户提供符合预期要求并交付及时的高品质模具。
本手册中我们详细说明向客户提供的模具标准。
不过,如果有任何关于模具设计和制造的疑问,请与我们联系。
铸造模,电极、CNC程序、设计、计算机程序、模板以及与该工作有关的需采购的所有东西都是Awintech所具备的。
它们应由模具制造商保留或根据客户要求提供给我们。
以下是模具加工付款条件:随订购单先预付50%模具加工费,模具加工完成后再付40%,最后模具样品合格后再付10%。
备注:以上条件需双方共同达成一致,否则无效。
目录1.0.0 模具分类与条款1.1.0 与Awintech作生意1.2.0 总体步骤与规格1.3.0 胚模规格1.4.0 料表1.5.0 上内模1.6.0 公模滑块零件1.7.0 拉圾钉1.8.0 顶出系统1.9.0 加热与冷却2.0.0 胚模零件2.1.0 液压汽缸筒和接近开关2.2.0 合金工具钢的热处理2.3.0 合金工具钢表面处理2.4.0 焊接2.5.0 金属进料与真空系统2.6.0 文档资料与证明2.7.0 压铸冲模设计和制造总指南和专用指南设计检测表模具加工检测表Awintech模具改善表Awintech模具检测规划报告拉极钉概要热电偶安装设计压铸机台板布局真空安装规格1.2.0 总体步骤与规格1、Awintech会向模具供应商提供最新的客户产品印刷物或资料库用以询价,模具设计和制造。
产品印刷物或资料库按要求在不断更新。
任何与原先不同之处必须要经Awintech确认才可。
2、除非另外说明,模具制造商负责模具设计。
由Awintech 提供设计时,凡与设计有不符之处都要经核准才可。
3、所有供应商设计的模具在订购材料和制造前必须经Awintech核准。
否则所产生的后果则由模具供应商负责。
4、所有给Awintech设计和制造的模具必须符合本手册阐明的标准。
如不按这些说明去做的话,模具供应商就是在冒险,只会给自己带来麻烦。
5、下列技术数据由Awintech或指派的压铸工提供:1)浇口、流道、通风、溢流井和真空设计2)加热和冷却铰接装置尺寸和位置3)热电偶孔位置4)推杆位置和尺寸5)分型面6)标识、数据印章、型控号及模槽区中的一些其它信息7)修边带、闪光环,去毛边和加工定位器8)机床坯料( 包括孔与表面)6.Awintech的采购订单号必须出现在所有的文件中。
7.在交货时所有文件必须要跟模具在一起(见2.6.0章文件与证明)8.所有模具在装船前要由Awintech人员检查。
程序负责人的职责是确保模具准备生产。
在模具装船前要向Awintech提供一份填写完整的模具检测表。
9.由于受外界和加工方法的影响,Awintech已越来越认识到该文件具有机密性这一点至关重要,它要由合适人员保管。
严禁复印或复制。
10.以前你会注意到用来识别压铸冲模、原型模具、生产之间的胚隙宽度这三类的术语对我们取得成功很重要。
为了向客户提供合乎要求的模具,一种不同的模具设计和制造的方法是非常有必要的。
在本手册末节我们详细说明每类模具的差异性。
我们的目标是在最短的时间内和以很低的成本向客户提供模具加工。
在过去以及现在仍有许多模具生产商能够快速地,但是以溢价方式来提供模具加工操捷径并不是指要减少模具的功能。
零部件仍要是可浇铸材料,同时符合现实的品质水平。
11.原型模具的工具品名形式有限,但仍须产生可接受的压模法。
它表示用作镶件的工具钢是P20或另一种预硬化钢。
使用最小水位。
零件脱模对整个脱模来说是非常必要的。
最小的孔是带芯的。
第二步是产生孔。
采用最有效和省时的方法生产上内模。
,我们有许多渠道用P20或H13钢提供供镶件和铸件。
你收到的报价申请会指出镶件钢的种类和是否是铸件。
除非另有说明,常规的热处理必须用H13。
在报价、设计或制造原型模具时,涉及滑块、推杆回位的问题和模具设计的细节情况都不适用。
胚模规格1.胚模定模厚度按照冷室机床吨位来定。
这些尺寸会有所保留。
有关伸缩式射出会有很多例外。
厚度不足3.875’’,重量为250吨厚度为4.875’’,其重量为400吨厚度为5.875’’,其重量为600 吨厚度为6.875’’,其重量为800吨厚度为7.875’’,其重量为1200吨备注:定模厚度的公差是+.005-.000因为有这些厚度规格要求,如果超过以上厚度,那么对伸缩式射出挡块则有所要求。
不过,它必须和以上尺寸相搭配。
2.撑头槽:尺寸为1.25英寸大,X1.00英寸宽,并离滚筒X1.00英寸深。
在胚模的四边和模脚内应将狭槽切割开来。
3.杠杆槽口:尺寸为.25英寸大,深X1.50英寸,角度为45度4.注塑孔径:其尺寸是根据机床运转的吨位量来定。
a)直径不足4.250尺寸,重量为250吨b)直径5.000尺寸,重量400吨c)直径6.000尺寸,重量为600吨或800吨d)直径7.000尺寸,重量为1200吨备注:孔径合适大小参见注塑孔图5.顶出挡片:该尺寸取决于注塑孔径大小,合模最小要达到1.00英寸。
一种压缩式的顶出挡片每一边有一个最小10度的出模角。
铸件每个助边上要求冷却线要攻3/8NPT螺纹牙并钻孔。
多孔用于可动模。
6.油道:其尺寸是3/4NPT螺纹牙,钻59 /64 直径。
胚模的定模和动模总是要提供油道。
凡与此规格不符的地方必须要经Awintech核准。
7.水道:尺寸是1/4NPT螺纹牙,钻59 /64 直径。
快速分离装置应凹进胚模内。
8.I形螺栓底孔:其尺寸和数量随着胚模和零件的重量不断变化,重40#的零件允许至少要有一个I形螺栓底孔。
各种各样的压铸机其最小尺寸400吨位是3/4-10,600,800和1200吨位机是1-8。
使用1/2-13,3/4-10,1-8 和1 1/2-6螺纹深1 3/4倍直径。
这些孔只位于扁平面和交叉槽上。
9.孔隙宽度:在胚模内要提供孔隙宽度用来取出镶件和模芯。
提供两个还是四个直径为1 1/8’’的孔要取决于公模和母模的尺寸。
其位置也要经工程部门认可。
10.导销和边钉最小为直径1 1/2英寸。
除非另有说明,将导销安装在胚模的定模上。
它允许铸件自动分离。
要使用撑帽式导销和边钉。
11.为了取出用来稳固拉极钉而使之不受破损的固定螺丝,那么穿过胚模、顶出系统和支承板,要提供拉圾钉孔隙宽度。
12.Die strap/pull holes are to provided in each half of the mold base(2)per half 。
穿过分模面,两孔之间的距离就为3.00英寸。
胚模应提供钢带。
13.要求在胚模上印上以下信息:客户名称料号压铸冲模号胚模(包含零件)的重量水道、油道号胚模的-0-CORNER14.合模A)从镶件的外缘到胚模的外缘,采用合模3.00英寸。
B)在上内模边缘和胚模外缘之间使用非真空管系统的胚模必须是4.50英寸钢。
C) 要求在上内模和胚模后面最小为2.50英寸。
D)从底部,顶出垫、顶出挡片或伸缩式顶出挡片有最小2.00英寸的胚模。
15.凸轮销孔:允许全部的销头凹进到胚模内。
凸轮销头不能弄碎。
应该用一个帽子来支撑钉。
16.热电偶:热电偶安装,其每种规格参见单独的章节。
17.在.001英寸TIR内,上内模动模和导销都是正方形的。
18:上内模:上内模的底部是斜面,在胚模分模面以上高出.002一.003尺寸。
19.内六角螺丝:800和1200吨位模具通常采用最小1/2-13或5/8-11。
600吨位模具为1/2-13,对于单元铸件则不到3/8-11。
20.在流道内应雕刻合金标识,高度最小是1/4,深.03。
21.Pockets for vacuum systems are to be machined in both halves of the mold base 参见特定的真空系统独立章节。
22.模脚作为真空系统的支柱,是连到胚模上,并延长至滚筒。
参见独立的真空系统章节23.按要求,要保证支撑板是对准穿过分型面的。
1.4.0 材料表品名材料1、胚模4130或4140 钢2、注道衬套和加料腔H13 hrd 248-284 bhn & nitrite3、射出导料块和射出块H13 hdr 44-48 rc4、导销碳C-1117 & hdr 58-62 rc5、边钉碳C-1013 & hdr 58-62 rc,.6、支撑板H-13 hdr 44-46 rc7、模脚1020钢8、柱状支撑1020钢9、冷铁10、拉极钉A)B)H-13 hdr 42-44rc( 见第1.2。
2章钢表面处理)C)ANVILOYJ(合金钨11.顶出系统定位1020钢12.真空筒和推杆固定板1020钢13.中托司青铜14.中托边碳414015.滑块零件A)承载挡块H13 hdr 44-46 rc STL3B)压块H13,4140 or 4150 carb hdr 52 to54C)压条AMPOCD)凸轮销和斜销S-7 or 6150 cr. carb 52 to 54 rcE)桥带O-1 oil hard hdr 50 to 54 rcF)水口铁M_Z hss hdr 58 to 60 rc used for STL3G)液压缸模脚1020钢H) 各形各色液压缸五金器具1020钢16.Vacuum components appear on a separate sheet and consist of a pocket for the blocks and keys. A valve-less vacuum block is to be used unless otherwise indicated.17.此系统的真空零件也许由Awintech采购(见1.2.章节)18.流道挡块19.镶件阴模20.液压缸1.5.0 上内模1.镶件设计和制造形式多种多样,它不限于pull down, self cleaning and push through. 2.模槽尺寸和公差除特别规定外,可使用.006’’/inch伸缩度。