生产线不良异常处理标准流程
公司制造异常处理流程

公司制造异常处理流程公司制造异常处理流程通常包括以下几个步骤:一、异常检测:-在生产过程中,设备、传感器或人工操作会不断产生数据。
异常检测的第一步是收集这些数据,包括生产线上的传感器数据、设备状态数据、产品质量数据等。
异常检测是制造业中非常重要的一环,它旨在及时识别和捕捉生产过程中的异常情况,以便采取相应的措施来避免或减少不良影响。
以下是对异常检测的详细介绍:1. 数据收集:-在生产过程中,各种设备、传感器和生产线会产生大量数据,包括温度、湿度、压力、振动等各种传感器数据,以及设备状态数据、产品质量数据等。
异常检测的第一步是收集这些数据,通常通过自动化系统或数据采集设备进行实时或定期采集。
2. 数据预处理:-收集到的数据可能存在噪声、缺失值或异常值,因此需要进行数据预处理。
这包括数据清洗(去除噪声和异常值)、填补缺失值、数据转换等操作,以确保数据的准确性和完整性。
3. 特征提取:-在异常检测中,需要从原始数据中提取特征,这些特征可以是统计量、频域特征、时域特征等。
特征提取的目的是将原始数据转换为更具代表性和可分辨性的特征,以便后续的异常检测算法能够更好地识别异常情况。
4. 异常检测算法:-异常检测算法可以采用各种方法,包括基于统计学的方法(如均值、标准差、箱线图等)、基于机器学习的方法(如聚类、支持向量机、神经网络等)、基于规则的方法等。
这些算法可以用来识别数据中的异常模式或行为。
5. 模型训练与评估:-如果使用机器学习或统计模型进行异常检测,需要对模型进行训练和评估。
这包括将数据集划分为训练集和测试集,使用训练集训练模型,并使用测试集评估模型的性能。
6. 实时监测与反馈:-异常检测通常需要实时监测生产过程中的数据,并对异常情况进行及时反馈。
这可能涉及到实时数据流处理、报警系统的触发、以及相关人员的及时介入和处理。
异常检测在制造业中扮演着非常重要的角色,它可以帮助企业及时发现生产过程中的异常情况,减少损失,提高生产效率,保障产品质量。
公司生产管理制度生产线异常情况处理与应急预案
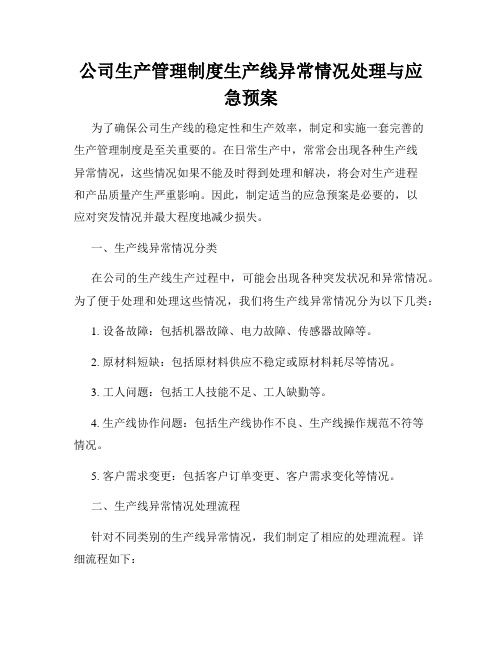
公司生产管理制度生产线异常情况处理与应急预案为了确保公司生产线的稳定性和生产效率,制定和实施一套完善的生产管理制度是至关重要的。
在日常生产中,常常会出现各种生产线异常情况,这些情况如果不能及时得到处理和解决,将会对生产进程和产品质量产生严重影响。
因此,制定适当的应急预案是必要的,以应对突发情况并最大程度地减少损失。
一、生产线异常情况分类在公司的生产线生产过程中,可能会出现各种突发状况和异常情况。
为了便于处理和处理这些情况,我们将生产线异常情况分为以下几类:1. 设备故障:包括机器故障、电力故障、传感器故障等。
2. 原材料短缺:包括原材料供应不稳定或原材料耗尽等情况。
3. 工人问题:包括工人技能不足、工人缺勤等。
4. 生产线协作问题:包括生产线协作不良、生产线操作规范不符等情况。
5. 客户需求变更:包括客户订单变更、客户需求变化等情况。
二、生产线异常情况处理流程针对不同类别的生产线异常情况,我们制定了相应的处理流程。
详细流程如下:1. 设备故障处理流程:- 员工应立即报告设备故障,并停止生产线。
- 维修人员需要及时前往现场检查和修复设备。
- 维修人员应填写设备维修记录,包括故障原因、修复过程和时间。
- 维修完成后,生产线恢复正常运转,并进行设备测试和调整。
2. 原材料短缺处理流程:- 员工应及时报告原材料短缺情况,并通知供应部门。
- 供应部门需要尽快安排原材料采购,并与供应商联系确认交货时间。
- 生产计划部门需要调整生产计划,以适应原材料的到货时间。
- 如果原材料到货延迟,生产线需要暂停并等待配送。
3. 工人问题处理流程:- 员工应及时汇报工人问题,包括技能不足或缺勤情况。
- 人力资源部门需要评估工人问题的严重性,并采取适当的措施。
- 如果是技能不足,人力资源部门需要提供培训计划。
- 如果是工人缺勤,人力资源部门需要调配其他工人替补。
4. 生产线协作问题处理流程:- 员工应及时报告协作问题,包括协作不良或操作规范不符。
SMT产线异常处理流程
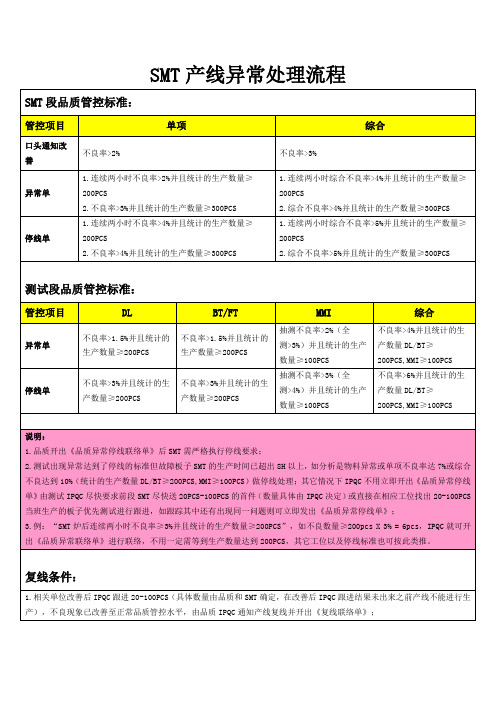
3.注意事项:复现条件成立时,速度要快,可先口头通知再签复线单。
停线后处理事宜:
1.品质部主导停线改善事宜,重点跟踪改善效果的跟进,尽量缩短停线时间;
不良率>6%并且统计的生产数量DL/BT≥200PCS,MMI≥100PCS
说明:
1.品质开出《品质异常停线联络单》后SMT需严格执行停线要求;
2.测试出现异常达到了停线的标准但故障板子SMT的生产时间已超出8H以上,如分析是物料异常或单项不良率达7%或综合不良达到10%(统计的生产数量DL/BT≥200PCS,MMI≥100PCS)做停线处理;其它情况下IPQC不用立即开出《品质异常停线单》由测试IPQC尽快要求前段SMT尽快送20PCS-100PCS的首件(数量具体由IPQC决定)或直接在相应工位找出20-100PCS当班生产的板子优先测试进行跟进,如跟踪其中还有出现同一问题则可立即发出《品质异常停线单》;
3.例:“SMT炉后连续两小时不良率≥3%并且统计的生产数量≥200PCS”,如不良数量≥200pcs X 3% = 6pcs,IPQC就可开出《品质异常联络单》进行联络,不用一定需等到生产数量达到200PCS,其它工位以及停线标准也可按此类推。
复线条件:
1.相关单位改善后IPQC跟进20-100PCS(具体数量由品质和SMT确定,在改善后IPQC跟进结果未出来之前产线不能进行生产),不良现象已改善至正常品质管控水平,由品质IPQC通知产线复线并开出《复线联络单》;
SMT产线异常处理流程
异常处理标准
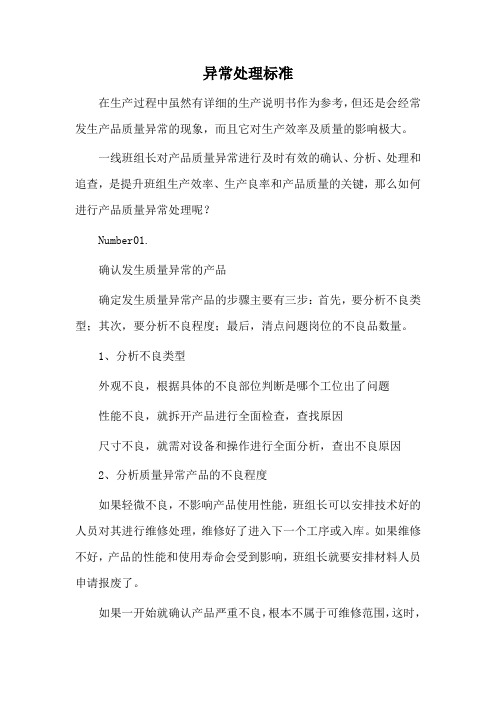
异常处理标准在生产过程中虽然有详细的生产说明书作为参考,但还是会经常发生产品质量异常的现象,而且它对生产效率及质量的影响极大。
一线班组长对产品质量异常进行及时有效的确认、分析、处理和追查,是提升班组生产效率、生产良率和产品质量的关键,那么如何进行产品质量异常处理呢?Number01.确认发生质量异常的产品确定发生质量异常产品的步骤主要有三步:首先,要分析不良类型;其次,要分析不良程度;最后,清点问题岗位的不良品数量。
1、分析不良类型外观不良,根据具体的不良部位判断是哪个工位出了问题性能不良,就拆开产品进行全面检查,查找原因尺寸不良,就需对设备和操作进行全面分析,查出不良原因2、分析质量异常产品的不良程度如果轻微不良,不影响产品使用性能,班组长可以安排技术好的人员对其进行维修处理,维修好了进入下一个工序或入库。
如果维修不好,产品的性能和使用寿命会受到影响,班组长就要安排材料人员申请报废了。
如果一开始就确认产品严重不良,根本不属于可维修范围,这时,可以直接申请报废。
如果出现的不良以前从未发生过的,班组长无法确定产品不良的程度,就有必要暂时停止生产线的生产,并立即向上级领导汇报,等待领导下达处理意见,这样就能避免不良品数量的增多。
3、清点问题岗位的不良品数量当不良类型和不良程度都确定后,还要清点问题岗位的不良品数量,如果某个工位连续出现五个甚至更多的不良品,就要暂停生产,查明原因。
如果不良品是断断续续出现的,可以边分析边生产。
Number02.根据质量异常原因进行相应的处理对质量异常产品,就需要根据实际原因,做好相应的处理。
那造成质量异常一般都有哪些原因,又该如何处理呢?对质量异常的原因,主要可以从五个方面进行分析处理,1、工艺文件问题首先要确认生产工艺文件是否正确,一般产品质量异常是工艺文件出现问题的可能性很小,它是一个标准性的参考文件,一旦有问题,那就是非常大的问题了,这种情况一般发生在刚开始投产或者工艺变更后,而大批量生产的时候,是很少出现这种情况的。
生产线异常紧急处理流程
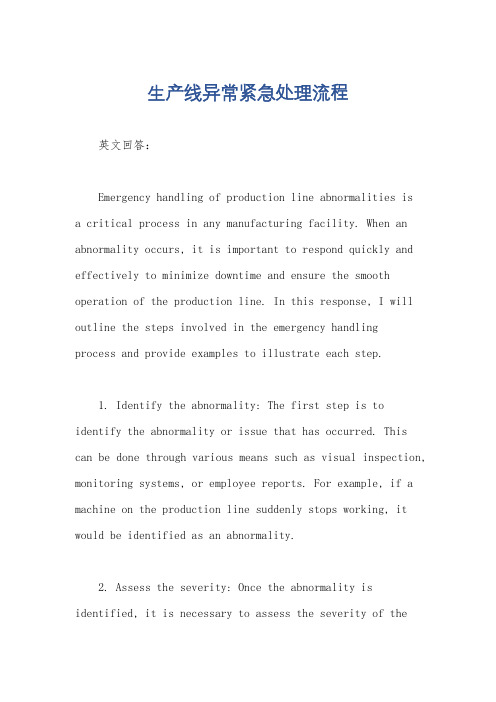
生产线异常紧急处理流程英文回答:Emergency handling of production line abnormalities isa critical process in any manufacturing facility. When an abnormality occurs, it is important to respond quickly and effectively to minimize downtime and ensure the smooth operation of the production line. In this response, I will outline the steps involved in the emergency handlingprocess and provide examples to illustrate each step.1. Identify the abnormality: The first step is toidentify the abnormality or issue that has occurred. This can be done through various means such as visual inspection, monitoring systems, or employee reports. For example, if a machine on the production line suddenly stops working, it would be identified as an abnormality.2. Assess the severity: Once the abnormality is identified, it is necessary to assess the severity of thesituation. This will help determine the level of urgencyand resources required for the emergency handling. For instance, if the abnormality is causing a complete halt in production, it would be considered a high-severity issue requiring immediate attention.3. Notify the relevant personnel: The next step is to notify the relevant personnel about the abnormality. This includes the production line supervisor, maintenance team, and any other individuals who need to be involved in the emergency handling process. Communication is crucial to ensure everyone is aware of the situation and can take appropriate actions. For example, the production line supervisor would immediately inform the maintenance team about the machine breakdown.4. Take immediate actions: Once the relevant personnel are notified, immediate actions should be taken to address the abnormality. This may involve troubleshooting the issue, repairing or replacing faulty equipment, or implementing temporary measures to resume production. For instance, if a machine breakdown is causing a production delay, themaintenance team would quickly assess and repair the machine to minimize downtime.5. Monitor and evaluate: After the immediate actions are taken, it is important to continuously monitor the situation and evaluate the effectiveness of the emergency handling measures. This allows for adjustments to be made if necessary to prevent similar issues in the future. For example, if a temporary fix is implemented to resume production, the team would monitor the machine closely to ensure it is functioning properly and evaluate if any permanent repairs or improvements are needed.6. Document the incident: Lastly, it is essential to document the incident and the emergency handling process. This includes recording the details of the abnormality, the actions taken, and any lessons learned from the experience. Documentation serves as a reference for future incidents and helps improve the overall emergency response system. For example, the incident report would include information about the machine breakdown, the steps taken to address it, and any recommendations for preventing similar issues inthe future.In conclusion, the emergency handling process for production line abnormalities involves identifying the abnormality, assessing the severity, notifying relevant personnel, taking immediate actions, monitoring and evaluating, and documenting the incident. By following this process, manufacturing facilities can effectively respond to emergencies and ensure the smooth operation of their production lines.中文回答:生产线异常紧急处理流程是任何制造工厂中的一个关键过程。
产线异常处理方法及流程

产线异常处理方法及流程
咱先说说这产线异常啊,那可真是让人头疼的事儿!就像上次,小李负责的那一段产线,突然机器“嘎吱嘎吱”响个不停,产品也都不合格了,哇,那场面!
说到处理方法,首先得眼尖,能快速发现问题。
我记得我刚开始的时候,眼神儿不好使,经常错过一些小细节,唉,没少吃亏!后来我学聪明了,每次都瞪大眼睛,仔细瞧。
流程这一块儿呢,一般是先停机,可别傻乎乎地让机器继续瞎转。
然后赶紧排查原因,是零件坏了?还是操作失误?我跟你们讲,有一回我以为是零件的问题,结果查了半天,发现是小王操作的时候打瞌睡弄错了,把我给气的哟!
有时候啊,问题还挺复杂,我记得好像是这样,不过也可能记错喽,得找几个懂行的一起商量商量。
要是碰到那种从来没见过的异常,我这又扯远啦,别慌,先冷静下来,慢慢琢磨。
现在这技术发展太快啦,有些新玩意儿我还不太明白,还得跟你们这些年轻人多学学。
假设说,要是你发现异常的时候正着急赶产量,那也得先处理异常,不然越弄越糟。
不知道你们听明白没有?反正我是把我知道的都倒出来啦。
我刚入行的时候,也是一头雾水,慢慢才摸清楚门道。
这行业变化也大,以前那些老办法现在不一定管用啦。
就像之前说的那个小李,他现在可长进不少,再也不出那种低级错误啦。
好啦,我就先说这么多,剩下的就靠你们自己在实践中摸索啦!。
产线异常处理流程及技巧
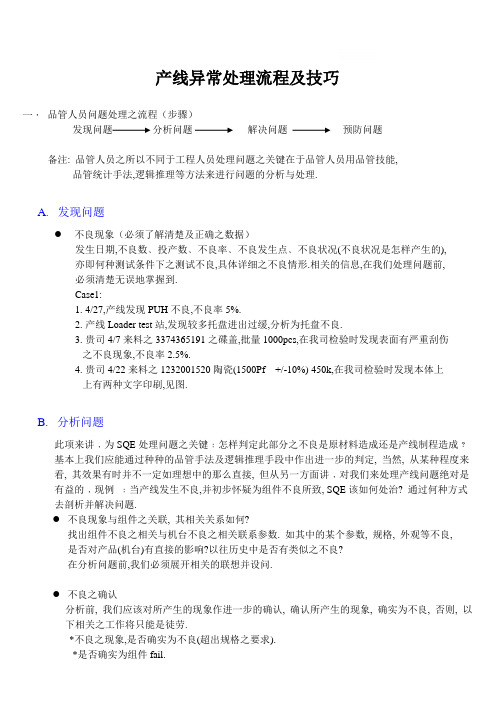
产线异常处理流程及技巧一.品管人员问题处理之流程(步骤)发现问题分析问题解决问题预防问题备注: 品管人员之所以不同于工程人员处理问题之关键在于品管人员用品管技能,品管统计手法,逻辑推理等方法来进行问题的分析与处理.A.发现问题●不良现象(必须了解清楚及正确之数据)发生日期,不良数﹑投产数﹑不良率﹑不良发生点﹑不良状况(不良状况是怎样产生的),亦即何种测试条件下之测试不良,具体详细之不良情形.相关的信息,在我们处理问题前,必须清楚无误地掌握到.Case1:1.4/27,产线发现PUH不良,不良率5%.2.产线Loader test站,发现较多托盘进出过缓,分析为托盘不良.3.贵司4/7来料之3374365191之碟盖,批量1000pcs,在我司检验时发现表面有严重刮伤之不良现象,不良率2.5%.4.贵司4/22来料之1232001520陶瓷(1500Pf +/-10%) 450k,在我司检验时发现本体上上有两种文字印刷,见图.B.分析问题此项来讲﹐为SQE处理问题之关键﹕怎样判定此部分之不良是原材料造成还是产线制程造成﹖基本上我们应能通过种种的品管手法及逻辑推理手段中作出进一步的判定, 当然, 从某种程度来看, 其效果有时并不一定如理想中的那么直接, 但从另一方面讲﹐对我们来处理产线问题绝对是有益的﹐现例﹕当产线发生不良,并初步怀疑为组件不良所致, SQE该如何处治? 通过何种方式去剖析并解决问题.●不良现象与组件之关联, 其相关关系如何?找出组件不良之相关与机台不良之相关联系参数. 如其中的某个参数, 规格, 外观等不良,是否对产品(机台)有直接的影响?以往历史中是否有类似之不良?在分析问题前,我们必须展开相关的联想并设问.●不良之确认分析前, 我们应该对所产生的现象作进一步的确认, 确认所产生的现象, 确实为不良, 否则, 以下相关之工作将只能是徒劳.*不良之现象,是否确实为不良(超出规格之要求).*是否确实为组件fail.相关的不良之判定,需经验之积累.针对一些比较模糊的规格,希望尽量能量化来定义.如: 杂音的判定,焊锡性不良之判定等.●分析过程及方法: 前提:( 若初步分析为原材不良所致)组件不良确认:a.交叉实验法(尽可能多机种, 多状态, 多次实验作确认, 尽可能比较全面地得到第一信息.)*单体简单比较(单次)*多因子之间比较(机种, F/W, 线别, DISC,厂商,Date Code)*单体多次比较(PCBA, Mega)举例: ( PUH, MOTOR, CHIP-C等)b. 借助我们现有之零件测试设备对零件参数作测试确认.这一点要求我们所有的SQE 人员在执行时日常的工作中应不断地提升我们对零件, 产品相关的认知, 不断提升 IQC检验之精准度, 可用性及实效性, 尽可能地从组件本身参数特性及与我们产品之相配性作检测, 如塑料件(尺寸, 实配治具等).以厂商认可的测试判定方法来进行量化的判定.b.待不良确认后, 用罗辑, QC方法进一步展开原因之深入调查.品管人员在处理问题时,最重要的一点同时也是最首要的工作是进行相关数据的收集统计并分析,从而得出我们所需求的信息.*不良现象之集中性? 变羿性? 是我们考究的重点. 在此仅以材料羿常处理查德检表, 以供各位在日常工作中能灵活运用, 势必在处理相关问题时会得心应手.1.问题确认➢不良现象发生之日期, 时间?➢在哪一段时间这不良率DPPM是多少?➢不良数是否集中在哪一条件?➢不良数是否集中在哪一个班?➢不良数是否集中在哪一产品型号(版别)?➢不良品之DATE CODE 为何? 是否有信集中之趋势?➢不良数是否集中在哪一个基板位置?➢以前是否有类似现象发生过?➢不良是否集中在哪一个测试治具?➢仪嚣治具是否有维修或不良?➢不良出现前后, 生产条件是否有变更(5M: 人,机,材,法,量测)➢其他供货商之供料是否有类似疵病?➢IQC 之SIP是否有针对此项疵病作检验?➢IQC是否有检验仪具与能力?以上经由收集相关资料来进一步判定不良现象之集中性及相关之 QC手法(查检表, 层别法), 对不良问题点作初步的判定并相关对策之实施.不良分析Case1:●手插5条线.●Function test ‘27项’不良.●初步分析为C221电容不良(Chip-C)d. 利用前后制程的一致性来推断不良产生之原因.利用各前后制程之测试状况作相应之判定.相关以上不良问题而产生的一种重要的分析方法------实验法.各种实验的实施,能有效地辅助我们进行问题的分析与处理.C. 解决问题内部➢满足产线正常生产为第一需求, 利上以上相关判定之信息, 换用其他DATE CODE, 厂商, 批次等料正常上线并追踪。
食品公司生产线异常情况处理流程

食品公司生产线异常情况处理流程随着社会的进步和人们生活水平的提高,食品安全问题备受关注。
食品公司在生产过程中,可能会遇到各种异常情况,如设备故障、原料受污染等。
为了保障食品质量与安全,公司需要建立一套完善的异常情况处理流程。
下面将详细介绍食品公司生产线异常情况处理流程。
一、异常情况发现与报告1. 员工负责问题发现:在生产过程中,所有员工都应密切关注生产线的运行情况,并及时发现任何异常情况,如设备故障、原料异样等。
2. 异常情况报告:员工发现异常情况后,应立即向所属班组长或质量控制部门报告,并在报告中详细描述异常情况的性质和发现地点。
二、异常情况评估与分类1. 评估异常情况严重程度:根据异常情况的性质和严重程度,质量控制部门将异常情况划分为不同的级别,以便更好地处理和追溯。
2. 分类异常情况:根据异常情况的性质和原因,将其分类整理,并与之前发生的相似情况进行对比和分析,以便找出问题的根源并采取相应的措施。
三、异常情况处理措施1. 立即停产:对于严重的异常情况,质量控制部门有权决定立即停产,以避免食品质量和安全受到进一步威胁。
2. 隔离和标识:如果异常情况对正在生产的食品批次造成影响,应立即将该批次食品隔离并标识,以便后续的处理和追溯。
3. 进行原因分析:质量控制部门应立即进行原因分析,找出异常情况发生的原因,如设备故障、操作不当等,并记录在案。
4. 制定修复计划:根据原因分析结果,制定出修复计划,明确修复的时间和措施,并进行相关部门的沟通和安排。
5. 修复异常情况:按照修复计划进行修复,确保设备和工艺能够正常运行,原料得到恢复或替换,以保证食品生产符合质量和安全要求。
四、异常情况记录与追溯1. 记录异常情况:质量控制部门应对每个异常情况进行详细记录,包括异常情况的性质、发生地点、原因分析、处理措施、修复结果等。
2. 追溯异常情况:在每个异常情况的记录中,质量控制部门应标注相关批次的产品信息,以便在后续追溯过程中能够准确查找该批次食品的生产信息和处理结果。
- 1、下载文档前请自行甄别文档内容的完整性,平台不提供额外的编辑、内容补充、找答案等附加服务。
- 2、"仅部分预览"的文档,不可在线预览部分如存在完整性等问题,可反馈申请退款(可完整预览的文档不适用该条件!)。
- 3、如文档侵犯您的权益,请联系客服反馈,我们会尽快为您处理(人工客服工作时间:9:00-18:30)。
发、品管、 交责任部门。
制程序》
品检、生 参照《纠正措施管理程序》
文件
产
跟进改善后其状况变化,对同样的问
生产、工 题在解决方案后再次出现,应上报上
程、品检 级部门。对标准的变更,应参照《不
合格品控制程序》执行。
编制:
审核:
批准:
流程
评审 NO 方案
实施改善 YES 方案
问题改 善后的 跟进 结束
职责
工作要求
相关文件 /记录
工程、开 根据方案的要求进行评审,经技术和 《 纠 正
发、品管、 品质评估通过可实施方案,未通过 措 施 管
品检、生 可继续进行分析确认。
理程序》
产
依照方案内容验证实施情况,并将有 《 不 合
工程、开 关记录,实施中出现问题等信息提 格 品 控
行为报
SMT
每小时填写《工序质量日报表》。 告》
生产、工 组长、领班、物料员、IPQC、工程人 《 不 合
程、 品 员、SMT 管理人员要有问题意识,及 格 品 控
检、SMT 时迅速发现异常或不良,能预见不 制程序》
工程、生 良或异常产生的影响和后果。
产、开发、 当单项不良低于 3%时,生产管理要
品检
流程
开始 巡线 发现生产
不良或异 不良品或
常 正异式常开现出象 制订解决 《校确正认行
方案 为报告》
职责
工作要求
相关文件 /记录
生产、工 监督生产线作业员按工艺文件作业情 《 样 机
程、品 况;
校位报
检
用样机校正各测试位,并填写样机 告》
生产、工 校位记录表;
《校正
程、品检、 检查各仪器设备运行情况;
及时将不良品交修理维修,修理将
修好的不良品要贴修理编号,并从
第一 QC 位下机。
工程人员根据问题判断类型(作业、
物料、设计)总不良高于 25%以上时,
应勒令停线处理。
参照《不合格品控制程序》运行。
当单项不良超过 3%,在 15 分钟内未能
解决时,由生产线组长、领班、物料
员、IPQC、工程人员、SMT 管理人员
根据不良或异常状况开出《校正行为
报告》;
组长、领班、物料员、IPQC、工程人
员、SMT 管理人员开出的《校正行为
报告》单要如实反映问题,不得夸大
事实。
作业问题应在《校正行为报告》单
上描述纠正改善措施。
设计、物料问题按《不合格品控制
程序》执行。
改设计存在的不完善因素。
生产线不良或异常处理流程
1. 目的 及时、迅速处理,解决生产过程中阻碍生产顺利进行的各种问题, 保证生产的正常运行。 2. 适用范围 生产线不良或异常包括物料、工艺、设备、产品功能、作业及 其它方面使生产不能顺利进行的各种因素。 3. 生产线不良或异常处理流程/职责和工作要求
流程
职责
工作要求
相关文件 /记录