车工工艺案例
数控车加工案例分析
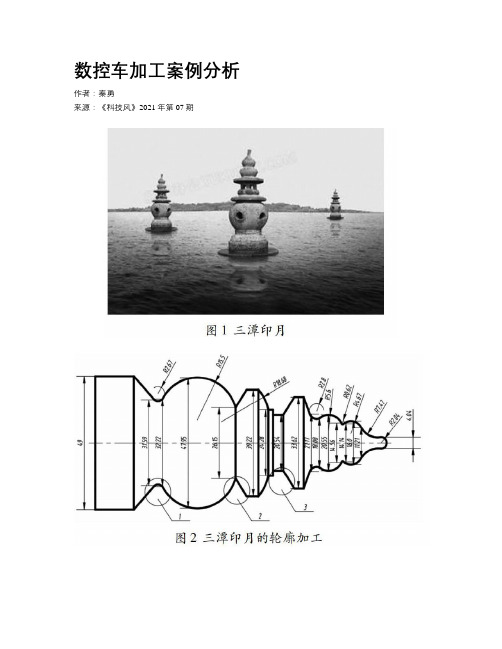
数控车加工案例分析作者:秦勇来源:《科技风》2021年第07期摘要:以三潭印月的数控车削加工为例,分析其加工工艺和步骤,对于其加工过程中可能出现的问题,有针对性地予以解决。
关键词:三潭印月;数控车加工;工艺;分析数控车加工主要是通过对圆形坯料做旋转运动,刀具沿轴向进给,加工出精确的直径和长度,合理的加工工艺满足工件要求,根据零件图和技术要求等,编制加工工艺,编写零件数控加工程序,实现自动进给,控制数控机床按照编制的刀具轨迹进给,从而完成零件的加工。
所以,在数控加工前,根据零件制定加工方案,对零件的工艺过程、刀具的形状、切削用量和走刀路线等都编入程序[1]。
本文以浙江杭州西湖十景之一的三潭印月为例,分析其加工工艺和步骤。
1 数控加工工艺的实例分析三潭印月是西湖中最大的岛屿,岛南湖中建成有三座石塔,由基座、圆形塔身、宝盖、六边小亭、葫芦顶组成。
三座瓶形小石塔鼎足而立,造型别致优美,如图1所示。
如此美丽的石塔,完全可以作为CNC或者3D打印素材。
1.1 工艺分析如图2所示为作了适当调整的三潭印月,去掉了六边小亭和圆形塔身上的孔。
三潭印月为回转体,适合在车床上加工,主要加工轮廓为圆柱面、圆锥面和圆弧面。
根据零件图进行分析,该零件先用G71进行粗加工,选用90度外圆车刀,切除多余余料和端面,再用G73进行精加工,根据零件的形状选定尖刀加工圆弧,先加工大端。
然后夹持住大端,再加工小端。
大端长度刚开始给了10mm,为了装夹强度考虑,可以加长大端长度,增至15mm。
车床装夹原则:尽可能减少零件装夹次数,保证装夹强度,夹大车小[2]。
在夹持时要注意:工件在旋转车削时会产生切削力要与装夹零件的夹紧力相对应。
1.2 加工工序根据零件结构形状选用55mm×150mm的棒料,选用90度外圆车刀(T01)进行粗加工,因用棒料加工三潭印月的轮廓,毛坯料余量较大,为了提高加工效率,根据零件图的外形进行分析,用G71进行粗加工,再选用30度的尖刀(T02)进行精加工,据外形结构用G73进行加工。
车削加工工艺实例

车削加工工艺实例轴类零件是最常见的典型零件之一。
而阶梯轴的车削工艺是一种典型的轴类零件加工工艺,反映了轴类零件加工的大部分内容与基本规律。
结合实训教学实际,我们列举两个实训项目零件来讲解车工工艺。
一、台阶轴车削工艺步骤1.零件图见图5–12.材料:45圆钢图5–1 零件图3.车削加工工艺(1)锯床下料45#钢Φ35×123 卷尺;(2)车床上用三爪卡盘装夹伸出长度L=80;(3)车端面见平,45°车刀, n=800r/min, f=0.15~0.25mm/r,a p≤2 mm;⑷钻中心B2.5/8 B2.5 中心钻Φ1~ Φ16 钻夹头n=1120r/min;⑸车Φ25外圆,L=70 90°车刀0-150游表卡尺;n=800r/min f=0.15~0.25mm/r a p≤2 mm;⑹车18外圆L=70 90°车刀0-150 mm游表卡尺0-25mm千分尺n=800r/min .f=15~0.25mm/r a p≤2 mm;⑺倒角1×45°45°车刀n=800r/min;⑻掉头夹持另一端车Φ25外圆;⑼车端面保证总长L=120 0-150mm游表卡尺n=800r/min;⑽钻中心B2.5/8 B2.5中心钻1~ 16钻夹头n=1120r/min;⑾夹持Φ18外圆并用活顶尖顶上中心孔;⑿车Φ32外圆,L≥50 90°车刀, 25-50mm千分尺, n=800r/min, f=0.15~0.25mm/r a p≤2 mm;⒀车Φ24外圆,L=20 90°车刀, 0-150mm游表卡尺, 0-25mm千分尺, n=800r/min f=0.15~0.25mm/r a p≤2 mm;⒁倒角1×45°,45°车刀, n=800r/min;⒂打学号印记,四号字头,锤子;⒃检测。
车工工艺教学课件-实训五
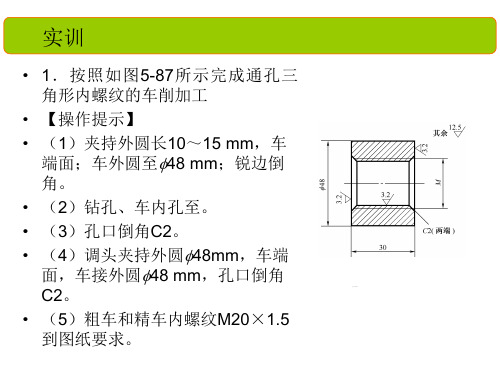
实训
• 1.按照如图5-87所示完成通孔三 角形内螺纹的车削加工
• 【操作提示】
• (1)夹持外圆长10~15 mm,车
端面;车外圆至48 mm;锐边倒
角。
• (2)钻孔、车内孔至。
• (3)孔口倒角C2。
• (4)调头夹持外圆48mm,车端
Hale Waihona Puke 面,车接外圆48 mm,孔口倒角
C2。
通孔三角形内螺纹
• (5)粗车和精车内螺纹M20×1.5 到图纸要求。
制在65 mm。 • (5)两端倒15°角,倒角C1.5。 • (6)粗车梯形螺纹Tr36×6−7h,小径车至,两牙侧留下精车余量
0.2 mm。 • (7)精车梯形螺纹大径至。 • (8)精车两牙侧面,用三针法测量,控制中径尺寸为。 • (9)车断,控制总长为81 mm。 • (10)调头,垫铜皮车端面,控制总长为80 mm,倒角C1.5。
实训
• 2.按照如图5-88所示完成梯形螺纹的车削 加工
梯形螺纹
实训
• 【操作提示】
• (1)夹持外圆长100 mm,车端面;钻中心孔,用一夹一顶装夹工 件。
• (2)粗车或精车梯形螺纹大径至,长度大于65 mm。
• (3)精车或粗车外圆24 mm至尺寸要求,长15 mm。 • (4)粗车或精车退刀槽至24 mm,宽度大于15 mm,长度尺寸控
数控车高级加工案例
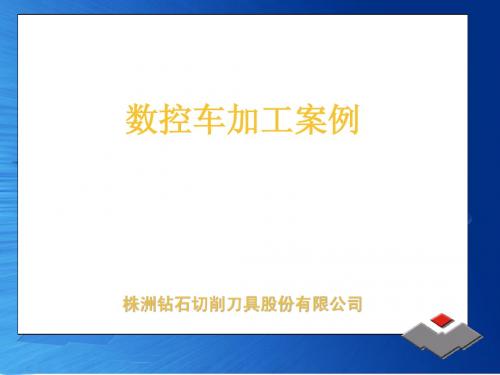
150
2
0.3
13 T03
14
15
16
17
18
QEFD2525R17 YBG302/ZPFD0302 刀片 -MG T03 精车右边外圆、端面 外圆车刀 MCLNR2525M12 YBC151/CNMG1 刀片 20404-DF T09 车螺纹 外螺纹车刀 SWR2525M16B YBG201/RT16.01 刀片 W-1.50GM S16Q粗车内孔(到φ25处) T10 内孔车刀 SCFCR09S25 留余量0.4 YBC251/CCMT09 刀片 T308-HM C20Q-QEDR05T12 内孔车槽 内孔切槽刀 27 YG302/ZTED0250 刀片 3-MG S16Q精车内孔(到φ25 T10 内孔车刀 SCFCR09S25 处) YBC151/CCMT09 刀片 T308-HF
T04 精车左边外圆、端面
外圆车刀 刀片
200
0.2
0.1
5
T05
粗车右端φ60外圆
外圆车刀 刀片
150
2
0.3
6
T06
精车右端φ60外圆
外圆车刀 刀片
200
0.2
0.1
7
T07
粗车圆弧面
外圆车刀 刀片
120
1.5
0.25
8
T08
精车圆弧面
外圆车刀 刀片
200
0.15
0.08
9
T09
粗车内孔(到φ25处) 留余量0.4
数控车加工案例
株洲钻石切削刀具股份有限公司
零件三维图
零件图
毛坯图
工艺分析
1、粗车左边外圆、端面,留余量0.4,圆弧面车 至φ40.5; 2、钻内孔至φ20; 3、车左边两处槽; 4、精车左边外圆、端面; 5、粗车右端φ60外圆; 6、精车右端φ60外圆; 7、粗车圆弧面;
车工工艺与技能练习--钻中心孔、钻孔

(8)在车床上钻孔的教学视频
主要内容: 1、基本操作技术 2、钻孔 3、容易产生的问题及原因
(9)群钻
群钻是利用标准麻花钻头合理刃磨而成的 生产率和加工精度较高、适应性强、寿命 长的新型钻头。 群钻主要用来钻削碳钢和各种合金钢。 群钻是把标准麻花钻的切削部分磨出两条 对称的月牙槽,形成圆弧刃,并在横刃和 钻心处经修磨形成两条内直刃。这样,加 上横刃和原来的两条外直刃,就将标准麻 花钻的“一尖三刃”磨成了“三尖七刃”
(4)中心孔的标注意义
(5)在车床上钻中心孔的教学视频
主要内容: 1、基本操作技术 2、钻中心孔 3、容易产生的问题及原因
2、钻孔
用钻头在实体材料上加工孔的方法叫钻孔。钻孔 属于粗加工,其尺寸精度一般可达IT11~IT12,表 面粗糙度Ra12.5~25mm。
麻花钻是钻孔的常用刀具,材料一般用高速钢制 成,由于高速切削的发展,镶硬质合金的钻头也 得到了广泛的应用。这里介绍高速钢麻花钻及其 钻孔方法。 对于精度要求不高的孔,可用麻花钻直接钻出, 对于精度要求较高的孔,钻孔后还要经过精加工 才能完成(在以后的课程中要涉及到孔的精加 工)。
课题说明
在工件安装中,一夹一顶或两顶都要先预制中心 孔,在钻孔时为了保证同轴度也往往要先钻中心 孔来决定中心位置。 在车床上钻孔加工也是比较常见的工艺,如齿轮、 轴套、带轮、盘盖类等零件的孔,都必须要先进 行钻孔加工。 钻中心孔和钻孔是车工必须要首先掌握的基本技 能。 在传统的教材教学中,这两项内容是在不同的单 元中进行的。本学期在教学改革活动中,我们以 典型零件加工为载体,本着“急用先学”的原则, 对这两项教学内容作了调整性的整合,以满足后 续课的需要,希望能达到预期的效果。
数控车加工案例分析

进行分析该零件先用 :1$ 进行粗加工选用 '% 度外圆车 刀切除多余余料和端面再用 :1( 进行精加工根据零件的 形状选定尖刀加工圆弧先加工大端 然后夹持住大端再 加工小端 大端长度刚开始给了 $%DD为了装夹强度考虑 可以加长大端长度增至 $9DD
5$)% Yg$$%% 5$)$ :1% ;)% `$)% 5$)9 :%% W99&%% 5$(% W$9%&% Y)%%&%% 5$($ b%(%( <3%%% :%% W9%&% Yg$%'% :%$ W% e%&$9% :%% W0%&%% W$9%&% Y$9%&%% 5$(9 @%9% 5$3% @(%% #加工 (&$ 试切 在试切外轮廓加工应注意.)/ 处的夹刀现象"同时要注 意如图所示的 $$( 两个位置# $ 为圆弧"半径较小"在切削时 会出现产生的切屑流出后翻转到半径为 ^$9&9 的圆弧面"划 伤其表面# )$( 的右侧均为锥面"一方面要注意刀具的副后 刀面与工件已车削轮廓表面是否干涉"另外也要注意"在切 削时会出现产生的切屑流出后翻转到锥面上造成划伤# 为 避免干涉也可采用直头刀杆车削"如图 ( 所示# (&) 加工中的问题及解决方法 为了避免上面提到的问题"可采取如下方法予以解决# ($)如在试切时.)/处出项夹刀现象"应改变.)/ 处的外 圆尺寸"进行外圆粗加工"再用 :1( 进行局部精加工# ()) 对整个工件预留不超过 %&$DD的余量"在加工完工 件后"再将预留的 加 工 余 量 切 去" 可 对 划 伤 的 表 面 进 行 修 复 或者 采 取 在 编 程 时" 分 别 对 $$)$( 三 个 位 置 预 留 不 超 过 %E$DD的余量"通过切除余量"修复划伤的表面# 后一种办 法会更为简便一些# 加工效果如图 3 所示#
车工工艺与技能项目七
4.滚花后再进行倒角。
项目七 滚花、车成形面和车偏心工件
三、准备工作
1.工件
毛坯尺寸:φ42 mm×100 mm。材料:45钢。数量:1件/人。
2.工艺装备 90°粗车刀、90°精车刀、45°车刀、0.02 mm/0~150 mm 游标卡尺、25~50 mm千分尺、m0.3双轮滚花刀、钢丝刷。 3.设备 CA6140型卧式车床。
项目七 滚花、车成形面和车偏心工件
本任务是要把φ25 mm×135 mm的毛坯加工成下图所示的
橄榄球手柄。
零件图
橄榄球手柄
实物图
项目七 滚花、车成形面和车偏心工件
一、成形面
成形面——具有曲线特征的表面,也称特形面。
单球手柄
具有成形面的零件
三球手柄
成形面
项目七 滚花、车成形面和车偏心工件
加工方法: 双手控制法 成形法(即样板刀车削法) 仿形法(靠模仿形) 专用工具法
车刀从a点出发至c点,纵向进给速度:快→中→慢;横向 进给速度:慢→中→快
项目七 滚花、车成形面和车偏心工件
4.单球手柄的车削
项目七 滚花、车成形面和车偏心工件
三、表面抛光
抛光——用砂布或砂纸磨光工件表面的过程。 在车床上抛光通常采用锉刀修光和砂布抛光两种方法。 1.锉刀修光
锉刀
握锉方法
项目七 滚花、车成形面和车偏心工件
项目七 滚花、车成形面和车偏心工件
四、操作步骤
滚花销加工的具体操作步骤: 找正并夹紧毛坯 车端面
粗车
30
0 -0.084
mm
外圆
掉头装夹
粗定总长,车外圆
滚花
倒角
保证总长
车工工艺案例
项目三:车削加工阶梯轴教学目标:终极目标:掌握轴类零件的车削加工方法促成目标:1、掌握加工轴类零件车刀的种类和要求。
2、掌握车削加工中常用的工件装夹方式。
3、能够按照图纸完成轴类工件的车削加工。
模块一:车阶梯轴用的车刀教学目标:终极目标:能够正确选择轴类零件加工时需用的车刀促成目标:(1)掌握车轴类零件常用的车刀(2)掌握车轴类零件在不同工况下车刀的选用原则工作任务选择轴类工件车削用的车刀相关理论知识车轴类工件时,一般可分为粗车和精车两个阶段。
粗车时除留一定的精车余量外,不要求工件达到图样要求的尺寸精度和表面粗糙度,为提高劳动生产率,应尽快地将毛坯上的粗车余量车去。
精车时必须使工件达到图样或工艺上规定的尺寸精度、形位精度和表面粗糙度。
由于粗车和精车的目的不同,因此对所用的车刀要求也不一样。
粗车刀必须适应粗车时切削深、进给快的特点,主要要求车刀有足够的强度,能一次进给车去较多的余量。
选择粗车刀几何参数的一般原则是:1、粗车刀(1)为了增加刀头强度,前角和后角应小一些。
但必须注意,前角过小会使切削力增大。
(2)主偏角不宜太小,否则容易引起车削时振动。
当工件外圆形状许可时,最好选用75°左右,因为这样刀尖角较大,能承受较大的切削力,而且有利于切削刃散热。
(3)一般粗车时采用0°~3°的刃倾角以增加刀头强度。
(4)为了增加切削刃强度,主切削刃上应磨有倒棱,其宽度b r1=(0.5~0.8)f,倒棱前角γ01=-(5°~10°)。
(5)为了增加刀尖强度,改善散热条件,使车刀耐用,刀尖处应磨有过渡刃。
(6)粗车塑性金属(如钢类)时,为了保证切削顺利进行,切屑能自行折断,应在前刀面上磨有断屑槽。
断屑槽常用的有直线型和圆弧型两种。
断屑槽的尺寸主要取决于进给量和切削深度。
2、精车刀精车时要求达到工件的尺寸精度和较小的表面粗糙度,并且切去的金属较少,因此要求车刀锋利,切削刃平直光洁,刀尖处必要时还可磨修光刃。
车床加工工艺案例
车床加工工艺案例一、零件分析本次车床加工的零件为轴类零件,主要结构包括圆柱面、圆锥面、螺纹等。
零件的尺寸精度和表面质量要求较高,需要进行精细加工。
二、材料选择根据零件的加工要求和性能要求,选择合适的材料是关键。
本次加工选用45号钢作为原材料,该材料具有较好的切削性能和机械性能,适合用于轴类零件的加工。
三、刀具准备在车床加工中,刀具的选择和使用对加工质量和效率具有重要影响。
根据零件的结构和材料特性,准备以下刀具:外圆车刀:用于加工圆柱面和端面;圆锥车刀:用于加工圆锥面;螺纹车刀:用于加工螺纹;切槽刀:用于加工槽。
四、切削参数设定切削参数的合理设定对加工质量和效率具有重要影响。
根据零件的材料特性和刀具特性,设定以下切削参数:主轴转速:根据所使用的刀具和材料确定合理的转速;进给速度:根据加工表面的粗糙度和刀具寿命确定合理的进给速度;切削深度:根据加工余量和刀具刚度确定合理的切削深度。
五、加工流程设计加工流程的合理设计能够提高加工效率和质量。
本次加工流程如下:将原材料固定在车床工作台上;使用外圆车刀加工圆柱面和端面;使用圆锥车刀加工圆锥面;使用螺纹车刀加工螺纹;使用切槽刀加工槽;对加工完成的零件进行质量检测和成品检验。
六、冷却液使用在车床加工过程中,冷却液的使用能够有效降低切削温度,减少刀具磨损和热变形,提高加工质量和效率。
根据使用的刀具和切削参数,选择合适的冷却液并控制使用量。
七、质量检测在每道工序完成后,应对零件进行质量检测。
检测内容包括:尺寸精度、表面粗糙度、形状精度等。
检测方法可采用千分尺、表面粗糙度仪等测量工具进行测量和评估。
如发现不合格品,应及时进行调整和返工。
八、成品检验成品检验是确保最终产品质量的重要环节。
检验内容应包括:尺寸精度、表面质量、形状精度等。
检验方法与质量检测相同,可使用相同的测量工具进行测量和评估。
如发现不合格品,应进行追溯和整改。
九、优化与改进在实际生产过程中,应根据实际情况对加工工艺进行优化和改进。
数控车削加工案例分析(二)
数控车削加工案例分析(二)
一图样分析:
1 材料与毛坯:材料的属性和毛坯的大小直接影响编程时的切削用量的选择和坐标尺寸的计算,因此,我们要给与足够的重视。
2练习加工的项目:①外轮廓加工(包括圆弧的加工);
②沟槽的加工
③螺纹的加工
3 加工所用的刀具:1#刀外轮廓粗车刀
2#刀外轮廓精车刀
3#刀4mm宽切槽刀
4#刀600螺纹车刀
4 技术要求:注意未注倒角、未注公差、未注表面粗糙度的要求
5 加工工序卡
二手工编写程序:
要求:1外轮廓的粗精加工使用G71\G70指令;
2 编制倒角程序;
3计算牙型高度并使用G92螺纹固定循环指令
三程序的输入与修改:
把编写好的程序输入到机床中,熟练掌握用操作面板输入程序。
四程序的校验:
利用机床上的图形模拟功能校验程序,掌握定义毛坯、判断图形。
五对刀操作:
对刀操作是数控机床学习中的重点,将重点讲述。
六零件的加工:
1 空运行、
2 单段运行、
3 自动运行
七工件的检验:
尺寸精度的控制方法:
1修改程序、2偏移坐标系、3 修改刀补值。
- 1、下载文档前请自行甄别文档内容的完整性,平台不提供额外的编辑、内容补充、找答案等附加服务。
- 2、"仅部分预览"的文档,不可在线预览部分如存在完整性等问题,可反馈申请退款(可完整预览的文档不适用该条件!)。
- 3、如文档侵犯您的权益,请联系客服反馈,我们会尽快为您处理(人工客服工作时间:9:00-18:30)。
项目三:车削加工阶梯轴
教学目标:终极目标:掌握轴类零件的车削加工方法
促成目标:1、掌握加工轴类零件车刀的种类和要求。
2、掌握车削加工中常用的工件装夹方式。
3、能够按照图纸完成轴类工件的车削加工。
模块一:车阶梯轴用的车刀
教学目标:
终极目标:能够正确选择轴类零件加工时需用的车刀
促成目标:(1)掌握车轴类零件常用的车刀
(2)掌握车轴类零件在不同工况下车刀的选用原则
工作任务
选择轴类工件车削用的车刀
相关理论知识
车轴类工件时,一般可分为粗车和精车两个阶段。
粗车时除留一定的精车余量外,不要求工件达到图样要求的尺寸精度和表面粗糙度,为提高劳动生产率,应尽快地将毛坯上的粗车余量车去。
精车时必须使工件达到图样或工艺上规定的尺寸精度、形位精度和表面粗糙度。
由于粗车和精车的目的不同,因此对所用的车刀要求也不一样。
粗车刀必须适应粗车时切削深、进给快的特点,主要要求车刀有足够的强度,能一次进给车去较多的余量。
选择粗车刀几何参数的一般原则是:
1、粗车刀
(1)为了增加刀头强度,前角和后角应小一些。
但必须注意,前角过小会使切削力增大。
(2)主偏角不宜太小,否则容易引起车削时振动。
当工件外圆形状许可时,最好选用75°左右,因为这样刀尖角较大,能承受较大的切削力,而且有利于切削刃散热。
(3)一般粗车时采用0°~3°的刃倾角以增加刀头强度。
(4)为了增加切削刃强度,主切削刃上应磨有倒棱,其宽度b r1=(0.5~0.8)f,倒棱前角γ01=-(5°~10°)。
(5)为了增加刀尖强度,改善散热条件,使车刀耐用,刀尖处应磨有过渡刃。
(6)粗车塑性金属(如钢类)时,为了保证切削顺利进行,切屑能自行折断,应在前刀面上磨有断屑槽。
断屑槽常用的有直线型和圆弧型两种。
断屑槽的尺寸主要取决于进给量和切削深度。
2、精车刀
精车时要求达到工件的尺寸精度和较小的表面粗糙度,并且切去的金属较少,因此要求车刀锋利,切削刃平直光洁,刀尖处必要时还可磨修光刃。
切削时必须使切屑排向工件待加工表面。
选择精车刀几何参数的一般原则是:
(1)前角一般应大些,使车刀锋利,切削轻快。
(2)后角也应大些,以减少车刀和工件之间的摩擦。
精车时对车刀强度要求并不高,也允许取较大的后角。
(3)为了减小工件表面粗糙度,应取较小的副偏角或在刀尖处磨修光刃。
修光刃长度一般为(1.2~1.5)f。
(4)为了控制切削排向工件待加工表面,应选择正确的刃倾角(3°~8°)。
(5)精车塑性金属时,前刀面应磨相应宽度的断屑槽。
相关实践知识
一.45º和90º外圆车刀的安装和使用 (1)、45º外圆车刀的使用:
45º车刀又两个刀尖,前端一个刀尖通常用于车削工件的外圆。
左侧另一个刀尖通常用来车削平面。
主、副切削刃,在需要的时候可用来左右倒角。
(见下图)
车刀安装时,左侧的刀尖必须严格对准工件的旋转中心。
否则在车削平面至中心时会留有凸头或造成车刀刀尖碎裂,刀头伸出的长度约为刀杆厚度的1~1.5倍,伸出过长、刚性变差,车削时容易引起振动。
图3.1 45°车刀的使用
(2)90º车刀又称偏刀,按进给方向
分右偏刀和左偏刀,下面主要介绍常用的右偏刀。
右偏刀一般用来车削工件的外圆、端面和右向台阶,因为它的主偏角较大,车外圆时,用于工件的半径方向上的径向切削力较小,不易将工件顶弯。
车刀安装时,应使刀尖对准工件中心,主切削刃与工件中心线垂直。
如果主切削刃与工件中心线不垂直,将会导致车刀的
工作角度发生变化,主要影响车刀主偏角
和副偏角。
图3.2
右偏刀也可以用来车削平面,但因车削使用副切削刃切削,如果由工件外缘向工件中心进给。
当切削深度较大时,切削力会使车刀扎入工件,而形成凹面,为了防止产生凹面,可改由中心向外进给,用主切削刃切削,但切削深度较小。
二、切断刀和车槽刀
偏刀
1、切断刀在车床上把较长的工件切断成短料或将车削完成的工件从原材料上切下这种加工方法叫切断。
切断刀的种类
(1)高速钢切断刀
刀头和刀杆是同一种材料锻造而成,每到切断刀损坏以后,可以通过锻打后再使用,因此比较经济,目前应用较为广泛。
(2)硬质合金切断刀
刀头用硬质合金焊接而成,因此适宜高速切削。
(3)弹性切断刀
为节省高速钢材料,切刀作成片状,再夹在弹簧刀杆内,这种切断刀即节省刀具材料又富有弹性,当进给过快时刀头在弹性刀杆的作用下会自动产生让刀,这样就不容易产生扎刀而折断车刀
2、车槽刀
车一般外槽的车槽刀的角度和形状与切断刀基本相同。
车狭窄的外槽时,车槽刀的主切削刃宽度应和槽宽相等,但刀头长度只要稍大于槽深即可。
图3.3 切断刀的使用
3、切断刀的安装
切断刀装夹是否正确对切断工件能否顺利进行切断的工件平面是否平直有直接的关系所以切断刀的安装要求严格
(1)切断实心工件时切断刀的主刀刃必须严格对准工件中心刀头中心线与轴线垂直。
(2)为了增加切断刀的强度刀杆不易伸出过长以防震动。
图3.4 切断刀的安装
图3.5 切断方法
4、切断方法
(1)用直进法切断工件:所谓直进法是指垂直于工件轴线方向切断,这种切断方法切断效率高,但对车床刀具刃磨装夹有较高的要求,否则容易造成切断刀的折断。
(2)左右借刀法切断工件:在切削系统(刀具、工件、车床)刚性等不足的情况下可采用左右借刀法切断工件,这种方法是指切断刀在径向进给的同时,车刀在轴线方向反复的往返移动直至工件切断。
(3)反切法切断工件
反切法是指工件反转车刀反装这种切断方法易用于较大直径工件其优点
A:反转切断时作用在工件上的切削力于主轴重力方向一直向下因此主轴不容易产生
上下跳动所以切断工件比较平稳
B:切削从下面流出不会堵塞在切削槽中因此能比较顺利的切削
但必须指出在采用反切法时卡盘与主轴的连接部分必须由保险装置否则卡盘会因倒车而脱离主轴产生事故
5、切断刀和切槽刀几何角度
图3.6 切断刀和切槽刀几何角度
前角切断中碳钢,у0 =200-300切断铸铁у0 = 0-100
主后角α0=6-8
主偏角切断刀以横向进给为主k=900
副偏角k/=10-1.30
副后角α0/=10-30
刀头宽度刀头不能磨的太宽,不但浪费工件材料而且会使刀具强度降低引起
刀头宽度与工件直径有关,一般按经验公式计算
a=(0.5-0.6)√D
a 为刀头宽度单位毫米
D 工件直径单位毫米
刀头长度刀头长度L不宜过长易引振动和刀头折断,刀头长度L可按下式计
L=H+(2+3)
L 刀头长度单位毫米
H 切入深度切断实心工件时,切入深度等于工件的半径
切断空心工件时,切入深度等于工件的壁厚
5、容易产生的问题和注意事项
1 被切工件的平面产生凹凸其原因是
(1)切断刀两侧的刀尖刃磨或磨损不一致造成让刀,因而使工件平面产生凹凸。
(2)窄切断刀的主刀刃与工件轴心线有较大的夹角,左侧刀尖有磨损现象进给时在侧向切削力的作用下刀头易产生偏斜,势必产生工件平面内凹。
(3)主轴轴向串动。
(4)车刀安装歪斜或副刀刃没磨直。
2 切断时产生震动
(1)主轴和轴承之间间隙过大。
(2)切断的棒料过大在离心力的作用下产生震动。
(3)切断刀远离支撑点。
(4)工件细长切断刀刃口太宽。
(5)切断是转速过高进给量过小。
(6)切断刀伸出过长。
3 切断刀折断的原因
图3.7 切断刀折断的原因
(1)工件装夹不牢靠切割点远离卡盘在切削力作用下工件抬起造成刀头折断。
(2)切断时排屑不良铁屑堵塞造成刀头载荷过大时刀头折断。
(3)切断刀的副偏角副后角磨的太大削弱了刀头强度使刀头折断。
(4)切断刀装夹跟工件轴心线不垂直主刀刃与轴线不等高。
(5)进给量过大切断刀前角过大。
(6)床鞍中小滑板松动切削时产生扎刀致使切断刀折断。
4 切割前应调整中小滑板的松紧一般以紧为好。
5 用高速钢刀切断工件时应浇注切削液,这样可以延长切断刀的使用寿命;用硬质合金切断工件时,中途不准停车否则刀刃易碎裂。
6 一夹一顶或两顶尖安装工件是不能把工件直接切断的,以防切断时工件飞出伤人。
7 用左右借刀法切断工件时,借刀速度应均匀,借刀距离要一致。
设备、工具、材料配置表
练习
车外圆时粗车和精车的刀具有什么不同,它们可以互换使用么?
项目教学评价考核点
1、掌握45°外圆刀的使用。
2、掌握90°车刀的使用。
3、掌握切断刀的使用。
4、掌握切槽刀的使用。